钢结构加工制作方案Word格式.doc
《钢结构加工制作方案Word格式.doc》由会员分享,可在线阅读,更多相关《钢结构加工制作方案Word格式.doc(27页珍藏版)》请在冰豆网上搜索。
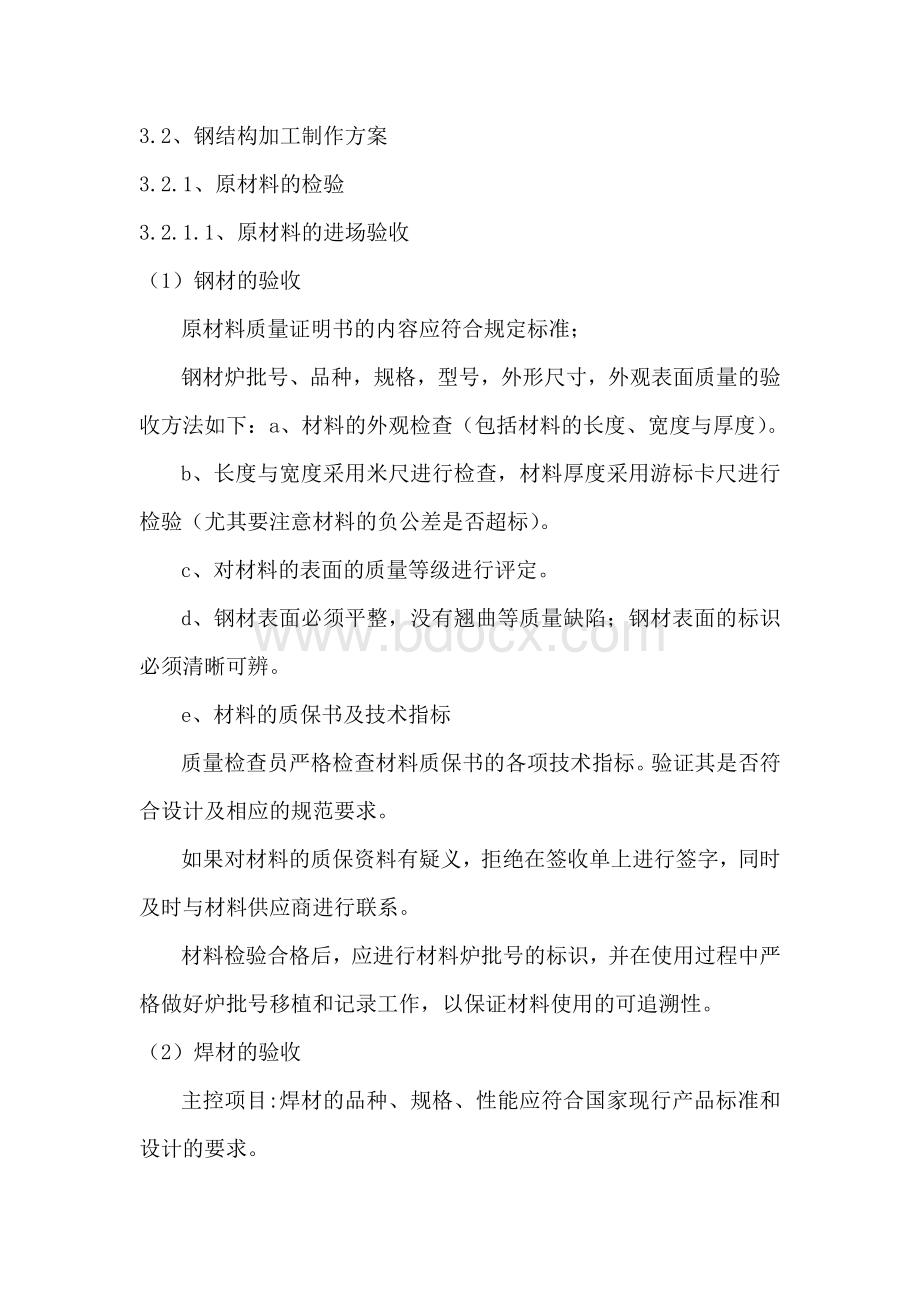
主控项目:
焊材的品种、规格、性能应符合国家现行产品标准和设计的要求。
适用范围:
进厂焊材。
检查数量:
全数检查。
检验方法:
检查质量合格证明文件、中文标志及检验报告等。
焊条外观不应有药皮脱落、焊芯生锈的缺陷;
焊剂不应受潮结块。
按量抽查1%,且不应少于10包。
检查方法:
观察检查。
(3)油漆的验收
钢结构防腐涂料、稀释剂和固化剂等材料的品种、规格、性能等应符合现行国家产品标准和设计要求。
一般项目:
防腐涂料的型号、名称、颜色及有效期应与其质量证明文件相符。
开启后,不应存在结皮、结块、凝胶等现象。
按桶数抽查5%,且不应少于3桶。
2.2.1.2、原材料的复验
根据《钢结构工程施工质量验收规范》GB50205-2001等规定,分别对以下材料进行复检:
对于厚度大于等于40mm,且设计有Z向性能要求的钢板;
建筑结构安全等级为一级,大跨度钢结构中重要受力构件的钢材应按规定进行探伤及化学性能、力学性能复检。
钢材在入厂外观检验合格的基础上,仍需要复验分化学分析和力学性能。
试验材料取样及试验时,要有见证人在场。
除我公司专业质量检验人员外,还应有业主代表或监理见证。
a、钢材的化学成分分析:
主要采用试样取样法。
按国家标准《钢的化学分析用试样取样法及成品化学成分允许偏差》(GB222-84)规定,复验属于成品分析(相对于钢材的产品质保书上规定的是熔炼分析),成品分析的试样必须在钢材具有代表性的部位采取。
试样应均匀一致,能代表每批钢材的化学成分,并应具有足够的数量,以满足全部分析要求。
b、钢材的力学性能试验及试样取样:
包括拉伸试验、夏比缺口冲击试验和弯曲试验几部分。
各种试验的试样取样,应遵循国家标准《钢材力学及工艺性能试验取样规定》(GB2975)。
标准规定样坯应在外观及尺寸合格的钢材上切取,切取时应防止因受热、加工硬化及变形而影响其力学及工艺性能。
用烧割法切取样坯时,必须留有足够的加工余量,一般应不小于钢材的厚度,也不得少于20mm。
3.2.2、主要生产工艺流程
(1)原材料检验流程
(2)焊接工艺流程
(3)构件涂装工艺流程
(4)质量检验流程
3.2.3、主要钢构件的制造工艺方案
本工程主要构件形式主要为箱形柱、箱形梁,而箱形梁中大部分是变截面箱梁。
其加工方案如下面所述。
2.2.3.1、箱形柱、梁的加工方案
(1)箱形构件的加工示意图如下:
(2)关键加工工序
a、采用专用箱形构件组装机进行自动组装,及用箱形构件翻转机进行构件翻转。
b、焊接采用CO2自动打底焊和双弧双丝埋弧焊,采用对称施焊法和约束施焊法等控制焊接变形和扭转变形。
c、采用电渣焊机对内隔板进行熔透焊接,端面铣床对箱体两端面进行机加工,保证构件的几何长度尺寸,从而提供钻孔基准面,有效地保证钻孔精度。
d、柱连接板、节点板的装焊
以柱的两端面的中心为基准,定出柱腹板和面板的中心线并以这个中心线为基准,确定连接板、节点板的水平位置,从而消除安装位置误差。
以柱上端面为基准,定出连接板、节点板的垂直线位置。
组装并焊接连接板、节点板。
2.2.3.2、变截面箱梁的加工方案
(1)变截面箱梁的结构形式如下:
(2)异形翼缘板在下料时可由数控直接切割成形。
(3)组装箱形梁内的隔板时,应首先在翼缘板上划出各个筋板的定位线,见下图:
(4)组装焊接翼缘板和内隔板。
(5)箱形梁组U。
组U前,内隔板两侧的腹板应首先折弯成型,待组装时进行折弯精度的微调,组装时保证腹板的定位尺寸及其与隔板、翼板间的组装间隙,然后焊接腹板与隔板间的焊缝。
(6)箱形梁封闭装配,然后进行四条主焊缝的焊接,为防止变形,应尽量采用对称焊接。
3.2.4、工厂预拼装
(1)预拼装的基本要求
a、在找平的场地上按图纸尺寸1:
1用校核后的卷尺放出预组装构件的大样,然后在大样上搭置胎架,胎架的水平位置采用水准仪进行测量定位,其偏差应符合构件装配的精度要求,并具有足够的强度和刚度,经QC、作业部门主管检查验收后报监理确认后才能使用。
b、大节点及各预组装杆件在预装就位前需按图纸划出几何线,以利正确定位。
c、预装时先将大节点在大样上就位,然后依次将各杆件就位,按水平标高调整各构件的高度。
d、构件预装后的检测,应在结构形成空间刚度单元并连接固定后进行。
e、预装后的允许偏差符合国家《钢结构工程施工质量验收规范》GB50205-2001及设计要求的相关规定,并经监理、以及安装单位确认后方可出厂。
(2)预拼装精度的控制措施
a、严格执行预拼装工艺、确保拼装构件尺寸的正确性
所有需在现场拼装的构件,采取在工厂内先进行预拼装的工艺,以便将现场拼装时可能发生的问题暴露出来,并消灭在工厂内,从而确保现场拼装杆件的外形尺寸、截面、坡口的正确性,并且标明各个接口处的对合标志,可极大地提高现场拼装质量和拼装进度,所以采取预拼装工艺是保证现场拼装质量的关键措施。
b、保证现场拼装胎架精度,确保拼装质量
拼装胎架精度的好坏,将直接关系到构件的拼装质量,所以现场拼装胎架必须严格按工艺要求进行设置,胎架必须有一定的强度,且胎架不得有明显的晃动;
必须确保胎架模板上口标高尺寸的正确,在构件上胎架拼装前,胎架应由专职检查员进行验收,并提交监理复验,以确保拼装胎架的制作精度,从而来保证构件的拼装质量。
c、加强质量管理
在拼装过程中,严格按质量管理条例进行质量跟踪测量检查,对于不合格的工序不得进入下道工序进行施工,坚持预防为主,以关键部位、薄弱环节,应精心施工,一丝不苟,防止质量事故的发生。
明确检验项目,检验标准、检验方案和检验方法,对保证项目、基本项目和允许偏差项目,认真做好原始记录、操作时间、条件、操作人等,对不合格品做好标记,分别堆放,按规定处理。
d、确保测量工具合格
拼装测量检测过程中必须确保测量工具计量检测单位检测合格,并附有检测公差表,在实际测量过程中,应与该公差表一起进行测量换算,以保证测量的正确性。
3.2.5、钢构件检验
3.2.5.1、制作装配检验外形、尺寸检验
钢结构构件自切割下料开始,就需要对尺寸和加工过程进行全面检验,通过“工序流转卡”的形式,保证构件在车间流转时各工序之间交接的合理控制。
工序流转卡需要分别由上道工序加工班组、质量检查员和下道工序加工班组三方确认方可流入下道工序,保证制作质量的过程控制。
在构件最终加工装配完成后,需要向质量部门进行最终质量报检。
由专检员对构件的整体外形尺寸、外观质量等进行综合检查,并开具构件出车间放行单(检验合格通知单),同时填写尺寸检验记录。
(1)号料划线检验
a、号料前确认其钢号材质,尺寸规格,外形及表面质量。
b、号料用的样杆、样板的尺寸、上面的定位标记,须检验合格方可使用。
c、按照图纸、下料加工单、草图及排版图划线,划中心线,基准线,弧度切割线,加放的加工余量和焊接收缩余量。
d、标注的构件号、零件号、外形尺寸,材质标记的移植应符合下料加工单、零件草图和排版图的规定。
e、如需拼接,应按工艺要求错开拼接位置,不允许采用短料拼接。
f、所有划线检验应记入检查记录中。
(2)切割、锯割与铣削检验
a、切割前应确认钢材表面的清洁度,平整度。
b、按图检验切割尺寸,按标准检验切割断面的粗糙度、垂直度及缺口深度。
c、坡口角度,钝边尺寸,坡口面等应符合规范。
d、督促毛刺、熔渣的清除,超标处的修补及表面处理。
e、切割后的变形矫正及矫正温度应符合技术规范。
f、锯割铣削精度:
垂直度,粗糙度,平面度,直线度,尺寸都应按照技术标准。
(3)制孔检验
a、划线精度:
孔距,孔径,定位基准,数量,孔心孔周的冲印检验。
b、钻孔精度:
孔的偏心,孔距的偏移,孔距,圆度及垂直度的检验。
c、钻孔用的钻模板,钻孔后的节点板,连接板上的基准线及其本体上位置检验。
d、督促孔边缘、孔边距的表面毛刺清除。
e、所有划线检验、孔径、孔距检验都记入检查记录中。
(4)装配检验
a、组装前应先检验零部件的材质、编号、尺寸、数量及加工精度是否符合图纸和工艺要求。
b、组装用的工作平台与胎架应符合构件装配的精度要求,并具有足够的强度和刚度。
c、复杂节点的装配次序及方法、矫正、端铣、加放的焊接收缩及加工余量,全部应符合工艺的要求。
d、按图纸、草图检验零部件的坡口、角度、钝边、间隙及接头的错位。
e、为了防止柱、梁构件的扭曲变形,装配胎架要水平,工艺隔板和临时撑杆的对角线也要同步。
f、各种规格的构件,它们的定位焊尺寸、长度、间距、位置及表面质量须100%目视检测。
g、各种构件在封闭前的检验,并作好隐蔽检验记录。
h、各种规格的构件,拼制好送自动焊前,必须标注工作令、构件号。
3.2.5.2、焊接检验
(1)焊接前检验
a、焊接工艺评定、工艺卡、焊工资质。
b、环境温度、湿度、风速等,需预热的温度范围及防风装置。
c、各构件焊接区域的打磨清洁度。
d、坡口角度、坡口面、间隙钝边、钢衬垫的密贴。
e、定位焊的初检和预热后的复检。
f、引﹑熄弧板的尺寸及装置。
g、领会焊接工艺总则中焊缝质量检测的要求。
h、焊材的烘培、保温、选用、发放及回收。
(2)焊接中检验
a、遵照焊接工艺中的焊接规范、顺序、位置、方法。
b、焊缝应连续施焊,遇有中断焊接时,应注意焊后缓冷且重新焊接前的预热。
c、焊接顺序、层间温度应严格按规范及焊接工艺要求执行。
d、监督焊道的清理,碳刨的实施。
e、引弧、熄弧、弧坑及端部焊的处理要规范。
(3)焊接后检验
a、焊缝外形尺寸,后热温度,后热时间,消应处理及焊缝其邻近部位表面质量。
b、变形矫正的温度,矫正后焊缝与邻近母材的表面质量。
c、焊缝探伤的时机、方法、范围、比例、标准、级别。
d、焊缝的返修复探,探伤比例和范围的扩大。
e、隐蔽焊缝在封闭前的检验。
f、督促并检查重要焊缝处的焊工钢印号。
3.2.5.3、除锈、涂装检验
(1)环境
施工环境的温度控制,对施工质量尤为重要。
露天涂装作业在晴天进行。
雨、雾、露、风等天气时,涂装作业应在工棚内进行,相对湿度应按涂装说明要求进行严格控制,且应为自动温湿记录仪或温湿仪为准,温湿度控制要求为:
喷砂时相对湿度≤60%;
涂装时相对湿度≤80%
(2)涂料配比控制
防腐蚀涂料的配制,要根据配方严格按比例配制。
特设专人负责配料,并由专人进行复检。
(3)间隔时间
一道漆涂装完毕后,在进行下道漆涂装之前,一定要确认是否已达到规定的涂装间隔时间,否则就不能进行涂装。
如果在过了最长涂装间隔时间以后再进行涂装,则应该用细砂纸将前道漆打毛后,并清除尘土、杂质以后再进行涂装。
(4)涂层膜厚的检测
施工各道油漆时