齿轮泵设计步骤教学资料.docx
《齿轮泵设计步骤教学资料.docx》由会员分享,可在线阅读,更多相关《齿轮泵设计步骤教学资料.docx(13页珍藏版)》请在冰豆网上搜索。
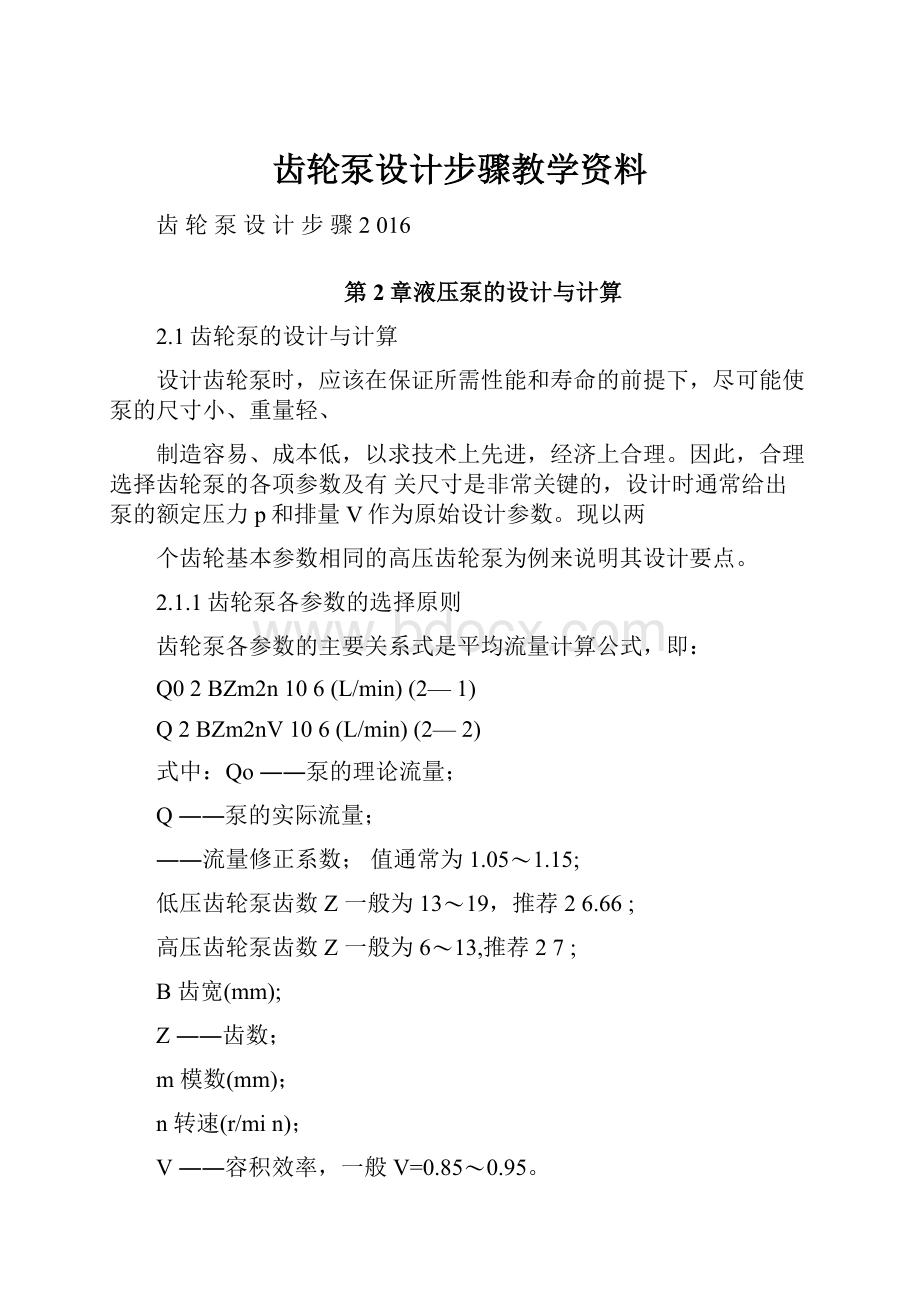
齿轮泵设计步骤教学资料
齿轮泵设计步骤2016
第2章液压泵的设计与计算
2.1齿轮泵的设计与计算
设计齿轮泵时,应该在保证所需性能和寿命的前提下,尽可能使泵的尺寸小、重量轻、
制造容易、成本低,以求技术上先进,经济上合理。
因此,合理选择齿轮泵的各项参数及有关尺寸是非常关键的,设计时通常给出泵的额定压力p和排量V作为原始设计参数。
现以两
个齿轮基本参数相同的高压齿轮泵为例来说明其设计要点。
2.1.1齿轮泵各参数的选择原则
齿轮泵各参数的主要关系式是平均流量计算公式,即:
Q02BZm2n106(L/min)(2—1)
Q2BZm2nV106(L/min)(2—2)
式中:
Qo――泵的理论流量;
Q――泵的实际流量;
――流量修正系数;值通常为1.05〜1.15;
低压齿轮泵齿数Z一般为13〜19,推荐26.66;
高压齿轮泵齿数Z一般为6〜13,推荐27;
B齿宽(mm);
Z――齿数;
m模数(mm);
n转速(r/min);
V――容积效率,一般V=0.85〜0.95。
流量Q是设计参数,只要确定B、Z、mn后泵的结构尺寸就大体确定了,然后参考有
关结构进行设计,最后进行强度校验。
下面来讨论如何确定B、Z、m、n这些参数。
1•确定转速n从流量公式可知,齿轮泵的流量Q与转速n成正比,转速越高,则流量越大。
但转速不能太高,因为转速太高时,油液在离心力的作用下,不能填满吸油腔的工作容积,并且对吸油腔的吸油也造成阻力,这时很容易产生气蚀现象,使泵的容积效率降低,特别是当油液粘度高时,齿轮节圆的线速度就受一定限制。
在各种油液粘度下,允许最大节圆线速度见表2-1。
此外,液压泵的转速也不能太低,因为当工作压力一定时,液压泵的泄漏量也接近于一定值,它与转速的关系不大;但转速越低,流量越小,则液压泵的泄漏量与输油量的相对比值将越大,也就是液压泵的容积效率越低。
当转速低至液压泵的理论流量和泄漏量相等时,则液压泵就不能出油。
最低节圆圆周速度Vmin可按下列经验公式确定:
Vmin0.1^E_(m/s)(2—3)
E50
式中:
p液压泵的工作压力(bar);
E50――油液在50C时的恩氏粘度。
当齿轮泵的转速低于200〜300r/min时,泵已不能正常工作了。
若齿轮泵采用交流电动机拖动,转速一般为:
750r/min、1000r/min、1500r/min,在航空上用到3000r/min或更
表2-1齿轮泵齿轮节圆极限速度和油的粘度关系
油的运动粘度
(mm2/s)
12
45
75
152
300
530
760
齿轮节圆极限线速度
Vmax(m/S)
5
4
3.7
3
2.2
1.6
1.25
2.确定齿数Z:
齿数Z的确定,应根据液压泵的设计要求从流量、压力脉动、机械效率等方面综合考虑。
从泵的流量方面来看,在齿轮分度圆直径不变的条件下,齿数越少,模数越大,泵的流量就越大。
从泵的性能来看,齿数减少后,对改善困油及提高机械效率有利,但使泵的流量及压力脉动增加。
目前齿轮泵的齿数Z一般为6〜19。
对于低压齿轮泵,由于应用在机床方面较多,要求流量脉动小,因此低压齿轮泵齿数Z一般为13〜19。
齿数14〜17的低压齿轮泵,由于根切较小,一般不进行修正。
对于高压齿轮泵,要求有较大的齿根强度。
此外为了减小轴承的受力,要减小齿顶圆直径,这样势必要增大模数,减少齿数,因此高压齿轮泵的齿数较少,一般取Z=6〜14。
为了防止根切,削弱了齿根强度,齿形均须进行修正。
3•确定齿宽B:
齿轮泵的流量与齿宽成正比。
增加齿宽可以相应地增加流量。
而齿轮与泵体及盖板间的摩擦损失及容积损失的总和与齿宽并不成比例地增加,因此,齿宽较大时,液压泵的总效率较高。
但对高压齿轮泵,齿宽不宜过大,否则将使齿轮轴及轴承上的载荷过大,使轴及轴承设计困难。
一般对于高压齿轮泵,B(3~6)m。
对于低压齿轮泵,
B(6~10)m。
这里m为齿轮模数。
泵的工作压力越高,上述系数应取得越小。
4•确定齿轮模数:
对于低压齿轮泵来说,确定模数m主要不是从强度方面着眼,而是从
泵的流量、压力脉动、噪声以及结构尺寸大小等方面考虑。
从流量公式(2—1)可以看出,模数m越大,泵的流量就越大。
并且当齿轮节圆直径一定时,对流量来讲,增大模数比增加齿数有利。
因此为了减小泵的体积,希望在可能的条件下尽量增大模数,减少齿数。
但齿数太少将使液压泵的流量及压力脉动增加,因此模数选择要适当。
模数m的粗略估算可用下面的经验公式:
m(0.4~0.6)Q(mm)(2—4)
式中:
Q――泵的实际流量(L/min)。
上述计算公式中,假定B(6~10)m;容积效率v0.85;当这些参数不在此范围内时,系数值也要变化。
目前中低压齿轮泵所用的模数值如表2-2所示。
表2-2中低压齿轮泵的模数值
Q(L/min)
m(mm)
4610
1.5〜2
122532
2.5〜3
405063
3.5〜4
80100125
4.5〜5
当工作压力大于10MPa时,应考虑到齿轮强度须适当增大模数。
齿轮泵精确流量计算公式为(见式(2—5))
22
Q02Bn(ReRh
6(L/min)(2—5)
当齿顶高等于模数m
(即齿顶高系数ho1)的标准齿轮,其
Re,Rh
2
mZ
式中:
Re——齿顶圆半径;
t°齿轮基节;
将上式代入流量公式得
式中:
Q。
一一泵的理论流量,
(L/min);
令B=Km,经整理后得
n泵的转速,(r/min);
K――齿宽系数,对于低压齿轮泵K=6〜10,对于高压齿轮泵K=3〜6;
Z——齿数,Z=6〜19。
对于齿数Z<13的齿轮泵,齿形须修正,其模数的精确计算公式为:
Qo106
m讣——0(mm(2—8)
\2nK(Z1.27)
2.1.2齿轮泵的设计步骤
齿轮泵的流量Q、压力p为已知的设计参数。
1.确定泵的理论流量Qo为
QoQ/v(2—9)
式中:
V――泵的容积效率,一般V=0.85〜0.95。
2.选定转速:
由原动机直接驱动,原动机的转速即为泵的转速,或将原动机减速后作泵
的转速。
若采用交流电动机驱动,一般转速为750、1000、1500、3000r/min。
3.选取齿宽系数K:
对于低压齿轮泵K=6〜10,对于高压齿轮泵K=3〜6。
压力高取小值,压力低取大值。
4.
选取齿数Z:
选取不同的K值及Z代入上式可以得到不同的m值,这样可以获得许多组齿轮泵的参数,可以从其中选择一组比较理想方案,作为所要设计的齿轮泵的参数,并把计算模数圆整为标准模数。
6•校验齿轮泵的流量。
该流量与设计理论流量相差5%以内为合格
当为标准齿轮时:
22
2COS6
Qo2Bnm(Z1)10(L/min)(2—12)
12
当为修正齿轮时:
22
2COS6
Q02Bnm(Z2)10(L/min)(2—13)
12
当泵流量与设计理论流量相差很小时,可以修改齿宽系数来调整流量,当相差大时,则需重新修改选定的参数
7•校核齿轮节圆线速度Vh
式中:
Dh——节圆直径,(mm)
n——转速,(r/min)
[Vh]――齿轮节圆许用线速度,其值见表2-1
若轮周速度太大,须减少节圆直径,办法是减少齿数或增加齿宽,有时也可以修改转速
n。
8•确定困油卸荷槽尺寸。
(1)两卸荷槽之间的距离a
2,
mZ2acos
A
式中:
t0齿轮基节(mm)
齿轮啮合角(°)
——分度圆压力角(°)
A两齿轮实际中心距(mm)
m模数(mm)
Z――齿数
⑵卸荷槽宽度:
Cmin
式中:
——重叠系数
(3)卸荷槽深度h:
卸荷槽深度的大小,影响困油排出的速度,一般取h0.8m
式中:
m齿轮模数(mm)。
图2-1困油卸荷槽尺寸计算图
9.计算齿轮各部分尺寸:
De、Di、D、B等,对于修正齿轮,则还须计算中心距移距系数、啮合角h等。
修正后的实际中心距A为标准值:
Am(Z1)(2—15)
修正后的齿顶圆直径De为标准值:
Dem(Z3)(2—16)
啮合角h由下式决定:
hcos^—Jcos)(2—17)
Z1
式中:
m齿轮模数(mm)
Z――齿数
mZ(mm);
D——齿轮分度圆直径,D
Di――齿根圆直径;
H齿轮啮合角
——齿轮压力角
可以通过下式计算:
保证齿侧间隙为0.08m的移距系数
(2—18)
Z(invHinv)0.04/cos
2tg
式中:
invh,inv渐开线函数。
上述修正方法称为“增一齿修正”,采用此种修正方法所求得的值是大于为消除根切所
需的最小移距系数min值。
按值可以求出加工时刀具的切削深度,即全齿高
h2.25m(0.5)m。
经修正后的齿形不仅消除了根切现象,增加了齿根的强度,而且使齿面接触更紧密,减
小了齿面的滑移,提高了泵的机械效率和容积效率。
10.参考有关结构对齿轮泵进行结构设计,边计算、边绘图、边修改。
例如根据工作压力的高低确定是否需要采用径向液压平衡及轴向间隙的自动补偿;采用何种径向力平衡措施;当压力p10MPa时,一般采用轴向间隙的自动补偿。
是采用三片式结构(由前泵盖、泵体、后泵盖)还是采用两片式结构(由壳体和前盖组成)。
三片式结构有以下优点:
(1)毛坯制造容易,甚至可用型材切料;
(2)便于机械加工;
(3)便于布置双向端面间隙自动补偿,从而改善补偿性能和提高寿命;
(4)便于双出轴布置,根据需要可以串接另一个齿轮泵。
11.确定液压泵的驱动功率
pQ
N—(kW)(2—19)
6010
式中:
p齿轮泵压力,(N/m2);
Q――齿轮泵输出流量,(L/min);
――齿轮泵总效率,一般取=0.75〜0.90。
12.强度校核和轴的刚度计算。
对低压齿轮泵,齿轮强度不必验算,一般均能满足要求;对高压齿轮泵,必须进行齿轮强度校验。
采用滚动轴承时,精确地计算轴颈的挠度非常重要。
因为即使轴的挠曲并不显著,也会引起滚针或滚柱滚道边缘接触应力剧烈增加,导致这些表面很快就会损坏。
采用滑动轴承时,轴的挠曲也会使局部接触应力剧烈增加并破坏润滑油膜,造成轴承的烧伤。
为了防止这种破坏,必须尽可能采取措施减少轴的挠度。
13.轴承的设计与选择。
由于两齿轮的轴线距离较小,往往不能安装所需的球轴承,因此在传统齿轮泵中一般采用径向尺寸较小的滚针轴承或滑动轴承。
当采用滑动轴承时,计算出滑动轴承的尺寸d、I。
当采用滚针轴承时,选择合适的滚针轴承并算出轴承寿命。
目前一般齿轮泵轴承的计算寿命不低于1000小时。
滚针轴承的优点:
工作时摩擦系数小,起动摩擦力矩小,机械效率高;承载能力强;既适用低转速也适用于高转速;能在较大温度范围内工作;抗污染能力强。
其缺点是:
工作中噪声大;轴承尺寸较大,结构布置不便;当采用长的滚针轴承时,对制造和装配误差较敏感;在高压齿轮泵中,pv值较大,对滚针精度要求较高以及热处理工艺规程要严格控制。
近来趋向于选取短而粗的滚针。
滑动轴承的优点是:
结构简单;安装方便;工作中噪声低;抗冲击性能好;价格便宜;只要材质和加工精度选择恰当,润滑条件良好,就能承受相当高的负载。
其缺点是:
抗污染能力差;在高温时油膜强度低,易烧坏;起动时摩擦力矩大;当转速很低时不易形成油膜,易烧坏。
复合材料轴承由于结构简单、成本低廉、过载能力强、抗污染能力强等优点,目前在齿轮泵中得到应用。
与金属轴承相比,复合材料轴承的摩擦、磨损性能有以下特点:
(1)工作负荷与摩擦系数之间的关系不像金属那样决定于弹性接触变形或塑性接触变形,而是决定于摩擦对偶材料之间的工作状态;
(2)相对滑动速度和摩擦系数之间的关系决定于聚合物基体材料的蠕变特性、纤维的方位及相对滑动的方向。
因而复合材料轴承对相配的轴颈材料、硬度、表面粗糙度等有相应的要求,与轴颈的配合间隙必须严格按厂家推荐的公差进行设计和制造。
齿轮泵是可逆元件,从原则上来讲,一般的齿轮泵都可以作为齿轮马达来使用,因此齿轮马达的设计方法和步骤与齿轮泵是相同的,但考虑到马达工作的特殊性,如带载起动、正反转,冲击等,齿轮马达在结构上有如下特点:
(1)考虑到马达要正反转,因此马达具有左右对称结构,采用外泄油口。
(2)为了改善起动性能,马达一般不宜采用端面间隙自动补偿装置,并选用滚针轴承。
(3)要求马达尺寸小,输出转矩脉动小,齿轮马达齿数Z取10〜14。
2.1.3齿轮泵的工艺、材料及技术要求
目前使用的齿轮泵中,齿轮和轴通常做成整体。
其优点是结构紧凑,装配方便。
对于尺寸较大的齿轮泵,齿轮和轴可以做成分离式,齿轮和轴之间采用键联接,这样结构工艺性好,加工齿轮侧面较容易,在平面磨床上加工相同的齿宽很容易获得。
齿轮泵通常采用的零件材料是:
泵体和端盖采用铸铁或铝合金,齿轮和轴采用45号
钢、40Cr、18CrMnTi、20Cr、38CrMoAI等材料(前面两种材料用于低压齿轮泵,后面三种材料用于高压齿轮泵),材料经渗碳氮化处理,表面硬度达HRC=60〜62,心部硬度HRC=28〜44。
使齿轮具有较高的耐磨性和冲击韧性。
淬火后的工作表面必须磨光。
轴套一般采用40号钢、40Cr和青铜。
下面给出齿轮泵典型零部件的工艺要求,仅供参考。
齿轮泵的主要零件的技术要求如下:
(1)泵体内孔锥度和椭圆度小于0.01mm;
(2)齿顶圆和泵体配合H7/f7;
泵径向间隙一般为0.02〜0.06mm;
(3)一对齿轮宽度差小于0.005〜0.01mm,—对齿轮同侧轴套宽度差小于0.005〜
0.01mm;
⑷齿轮轴孔和齿顶圆之间的偏心量小于0.0lmm;
(5)用涂色法检查,在齿高方向上,齿轮啮合长度大于65%,在齿宽方向上齿轮啮合长度
大于60%;
(6)齿面粗糙度为0.2m,齿轮两侧面粗糙度为0.2m,轴颈的粗糙度为0.1m,泵的
其它主要密封面(如轴套内孔表面,轴套端面,齿顶圆表面及泵壳内表面等)的粗糙度
一般为0.4m;
(7)轴椭圆度及锥度小于0.005mm;
(8)泵体中心偏心距偏差小于0.03〜0.04mm,中心线平行度小于0.01〜0.02mm。
,t0mcos
2