CFRP板与钢梁粘接的疲劳性能研究中文翻译.docx
《CFRP板与钢梁粘接的疲劳性能研究中文翻译.docx》由会员分享,可在线阅读,更多相关《CFRP板与钢梁粘接的疲劳性能研究中文翻译.docx(19页珍藏版)》请在冰豆网上搜索。
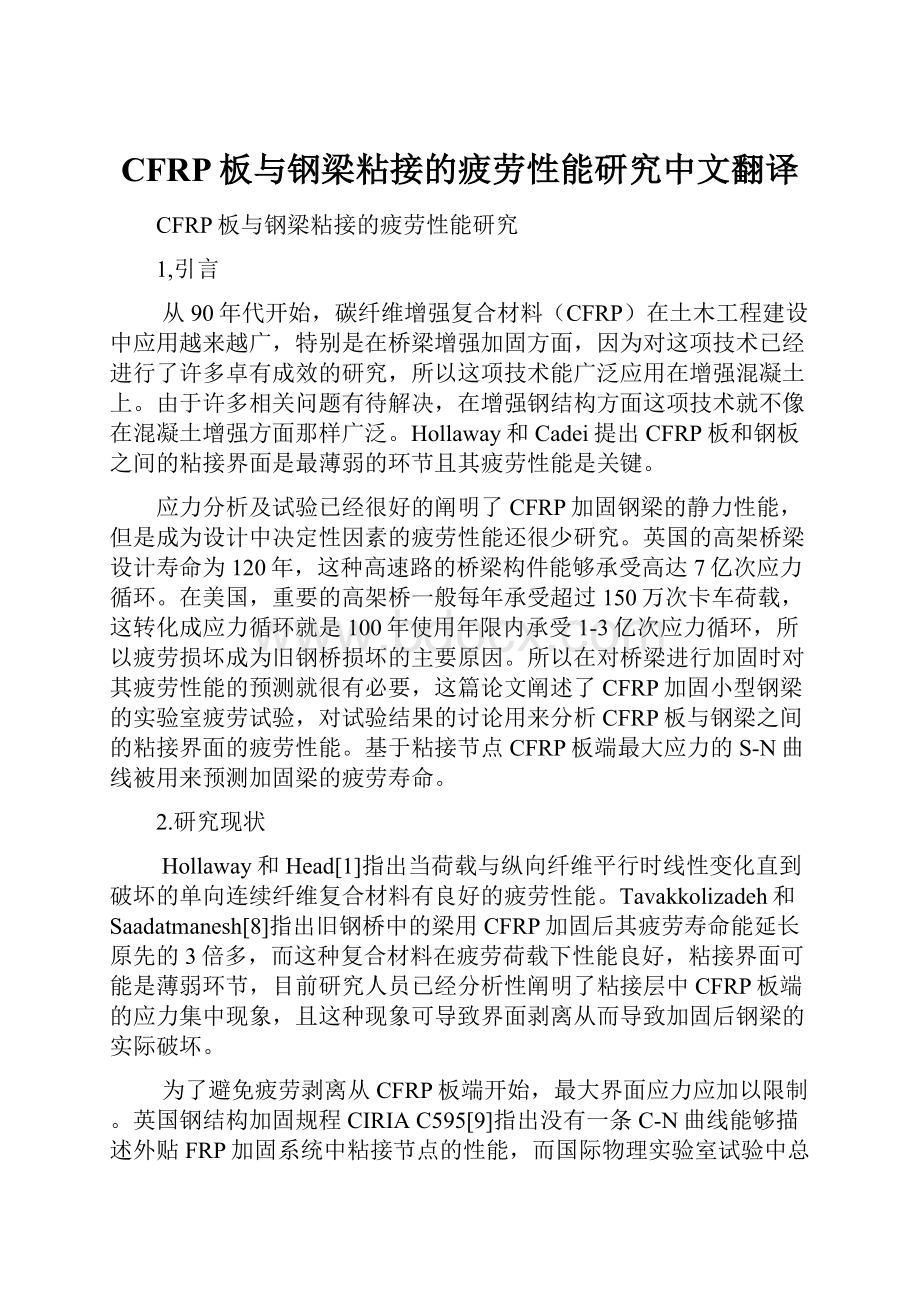
CFRP板与钢梁粘接的疲劳性能研究中文翻译
CFRP板与钢梁粘接的疲劳性能研究
1,引言
从90年代开始,碳纤维增强复合材料(CFRP)在土木工程建设中应用越来越广,特别是在桥梁增强加固方面,因为对这项技术已经进行了许多卓有成效的研究,所以这项技术能广泛应用在增强混凝土上。
由于许多相关问题有待解决,在增强钢结构方面这项技术就不像在混凝土增强方面那样广泛。
Hollaway和Cadei提出CFRP板和钢板之间的粘接界面是最薄弱的环节且其疲劳性能是关键。
应力分析及试验已经很好的阐明了CFRP加固钢梁的静力性能,但是成为设计中决定性因素的疲劳性能还很少研究。
英国的高架桥梁设计寿命为120年,这种高速路的桥梁构件能够承受高达7亿次应力循环。
在美国,重要的高架桥一般每年承受超过150万次卡车荷载,这转化成应力循环就是100年使用年限内承受1-3亿次应力循环,所以疲劳损坏成为旧钢桥损坏的主要原因。
所以在对桥梁进行加固时对其疲劳性能的预测就很有必要,这篇论文阐述了CFRP加固小型钢梁的实验室疲劳试验,对试验结果的讨论用来分析CFRP板与钢梁之间的粘接界面的疲劳性能。
基于粘接节点CFRP板端最大应力的S-N曲线被用来预测加固梁的疲劳寿命。
2.研究现状
Hollaway和Head[1]指出当荷载与纵向纤维平行时线性变化直到破坏的单向连续纤维复合材料有良好的疲劳性能。
Tavakkolizadeh和Saadatmanesh[8]指出旧钢桥中的梁用CFRP加固后其疲劳寿命能延长原先的3倍多,而这种复合材料在疲劳荷载下性能良好,粘接界面可能是薄弱环节,目前研究人员已经分析性阐明了粘接层中CFRP板端的应力集中现象,且这种现象可导致界面剥离从而导致加固后钢梁的实际破坏。
为了避免疲劳剥离从CFRP板端开始,最大界面应力应加以限制。
英国钢结构加固规程CIRIAC595[9]指出没有一条C-N曲线能够描述外贴FRP加固系统中粘接节点的性能,而国际物理实验室试验中总结的S-N曲线能够替代。
在这条曲线中最大剪应力在疲劳加载中建议不超过极限静力疲劳强度的20%-30%。
为了评估CFRP加固钢桥梁粘接界面的疲劳承受能力Miller等人进行了两组试验。
首先他们取7个小型试件两面加固,在82.7Mpa的幅度下进行235万次应力循环。
试验结束后所有CFRP板都完好粘接于钢梁上没有破坏,基于试验前后的应力数据。
接着两个实际尺寸的用CFRP加固的桥梁构件在100万次的34Mpa的应力幅度下发生疲劳破坏。
CFRP板检测处剥离,但是没有任何破坏,加固因此被认为有良好的疲劳抵抗力。
Tavakkolizadeh和Saadatmanesh[8]报告中有关于CFRP加固钢梁的疲劳试验。
他们测试了21根用CFRP加固的在中度疲劳荷载下的钢梁。
未加固的梁作为对照试件同样也测试了。
每根钢梁的跨度是1.22m,中点部分用300mm长CFRP板粘接加固,进行四点弯曲试验,中间两个加荷点距离200mm,,此CFRP板是由弹性模量为144.0Gpa的单向编织纤维碳纤维片材制成。
钢梁在持续的从69-379Mpa的不同应力幅度下以5-10Hz的频率下测试。
结果显示CFRP板不仅延长其疲劳寿命达3倍多,而且显著减少了裂缝扩展速度。
如果在CFRP加固桥梁的48小时过程中,桥梁节点附近行驶车辆是不经济的,在这段时间粘性受交通荷载影响下减少,混凝土协会[2]建议:
加固期间由疲劳荷载引起的粘性性能的变化可能很小,与CFRP加固梁完全不受影响的相比强度大概减少10%,Nikouka[10]等人调查发现与早期加固粘接时的疲劳荷载有关。
5组127×76UB13的钢梁,每根长1.2m且用0.98m长的单片碳纤维板加固,与下翼缘连接,CFRP板由超高弹性模量达310Gpa的K13710碳纤维制成,只有7.6mm厚,76mm宽。
一个正弦波状荷载以0.25HZ频率施加于5件试件上,且持续了长达48小时。
这个试验证明了加固期间的疲劳荷载将对最终刚度有影响。
,且加固梁的破坏荷载大于42KN,如果界面中剪应变过大粘性难以发展。
他们还说要谨防粘接界面中剪应力超过1Mpa上限。
在CFRP加固钢结构疲劳性能方面的有限信息意味着如果这项新颖的增强技术得到广泛推广需要做更多的研究工作。
尽管研究现状展示了CFRP加固对于疲劳性能已有改善作用,或者说是粘接处有良好的疲劳抵抗力,但是还未建立起疲劳寿命、界面应力和试件特征之间的良好联系所以试验结果不能应用于实际。
本文的主旨是要研究CFRP加固钢结构粘接界面的疲劳性能,特别是CFRP板破坏的区域。
可以通过机械性交变荷载下的CFRP加固钢梁疲劳试验进行。
3.实验准备
此项试验要达到下列目标:
●观察裂缝开始和开展,建立粘接界面的开裂模式
●估计加固梁在裂纹开展下的刚度变化
●分析粘接节点板端溢胶效应对疲劳性能的影响
●归纳出一条能够设计疲劳寿命简易的S-N曲线
3.1试件
9个用预浸的碳纤维板加固的小型钢梁用来做试验,钢梁都采用1.2m长的127×76UB13,钢材的设计强度为275Mpa,弹性模量为205Gpa,贴CFRP板的基材表面依据工业标准经过喷砂处理至SA21/2,使用的CFRP板3mm厚,400mm长,由0.3mm厚单向环氧树脂坯料制成,胶剂用得三分之二触变环氧树脂。
环氧胶剂通常是Sikadur-13,其弹性模量为9Gpa,剪切模量为2.6Gpa,拉伸强度为29.7Mpa(数据由制造商提供),其中混有占重量为1%的直径1mm路标玻璃珠确保粘接厚度均匀。
3.2试验仪器设备
疲劳试验在一台液压伺服Dennison测试仪上进行,其最大压力达到200KN,使用三点弯曲设备,净跨为1.1m,加荷点位于中间,如图一所示,试件置于两个滚轴上,这样让试件处于简直状态,但是约束其侧向运动,加载块由2块钢板组成,每块都有一个传动轴,中间有个滚轴。
这九根梁中的第一根梁(参照试件F135),首先在静荷载下测试,以0.5mm/s的速度的位移控制来测出其破坏荷载,这样能够控制施加到别的8根试件上的最大荷载。
由这根梁得到的破坏荷载是135KN。
由这个值可得出CFRP板端的最大主应力
为80.4Mpa.
是由最大剪应力
和最大正应力
由以下公式计算出来的。
公式中
和
可由作者提出的分析性方法计算出来。
由CFRP板端的不连续性产生的应力集中意味着
就能控制疲劳应力。
其余8根梁在40-125KN之间的最大点荷载P的疲劳荷载下进行试验。
这些荷载转换成23.8-74.4Mpa的
如表1所示。
图一疲劳试验装置示意图
图二所示,三个位置的挠度用分压计测出,如T1,T2,T3所示。
为了得出裂纹开始和发展的现象,隐面应变技术已经应用在试件F55上。
5个2mm长应变片沿着纵向中心线贴于CFRP板的表面。
如图二的G1-G5所示。
此外两个5mm长的应变片贴于梁凸缘内表面,未测试裂纹开展的效应。
所有试件都安置了板端应变片G1和G2用来测试裂纹出现。
包括由液压系统传感器测量的荷载值等所有数据由数据自动记录系统自动记录。
3.3试验过程
除F70*试件外的施加到所有疲劳测试梁上的最小荷载是5KN。
这样能保证梁与支撑之间能紧密接触。
荷载是以正弦波形式1(F125、F90)-2HZ(F55F50F40试件)的频率施加的。
这个频率是根据Emberson和Mays的研究[11]而选择的。
在他们的研究中超过2HZ的频率许多梁在卸荷后不能完全恢复。
Mays和Tilly[6]也推断高度路上的车辆荷载的速率可以代表性的等效为1HZ的频率。
在交变疲劳荷载加载中,实验间断停顿几次,或当裂纹已经检测出来然后试件再加三个轮回的从0-最大值的加载和卸载。
这样做是为了测量荷载、CFRP板端应力值及在加载中的挠度。
因为这些数据不能在疲劳加载中精确记录。
除了用应变片监测裂纹出现和开展,同时用放大镜肉眼监测并记录裂纹长度和相关加荷次数。
当开裂达到梁的跨中后或者裂纹停止开展,停止加载。
这就意味着CFRP板已经失去了加固作用,试件破坏。
为了分析在疲劳试验后无剥离的梁的性能,一直置于以0.05mm/s控制位移的静力荷载下的F40-2试件经历400万次疲劳荷载后破坏。
Notes:
说明:
1.在对照试件中,梁上数字说明了最大荷载(KN)A和B是同一个加固梁的粘接节点的两端。
2.F135是在静力荷载下的试件F135
3.P是最大施加荷载P
4.Pu是极限静力荷载
5.施加的最小荷载是5Kn,而F70*最好荷载是20kN.
6.r1max是最大施加荷载下板端最大界面应力
7.Ni1,Ni2和Nf分别是应变片在裂纹出现时加载次数、肉眼可见裂纹时加载次数、试件破坏加载次数。
图二试件上的仪器
4.试验结果分析
4.1隐面应变技术
在前面已提及应变片贴于CFRP板来监测裂纹出现和发展。
在静力加载下相同的试件的类似研究中,笔者已经在3点弯曲试验中给试件跨中粘贴了400mm长CFRP板,如图3中所示,一般试件中的G1、G2处的CFRP板端测试出的应变是负的也就是受压的。
这个试件板端溢出的胶完全清除干净。
这个发现证实了由笔者[12]提出的理论分析。
这个等式里,
(
﹤﹤tp板厚度)处的板端纵向应变为
给出如下:
其中
是溢胶里的力,Ep和Ap分别是弹性模量和板面积,
和
分别为板端剥离应力和剪应力。
公式里的第一项是由板端的溢胶产生的拉(正)力,第二项是由来源于剥离应力(负),第三项来源于剪应力。
因为
﹤﹤tp,第三项可以经常比第二项大,没有溢胶作用,板端纵向应变就是负的(受压)。
板端压应变一般比较小,且很大程度上受溢胶尺寸影响。
当有溢胶时,板端就会出现正的(拉)力,且量级与溢胶尺寸成比例,足够大面积的溢胶因此能将板端压力变成拉力。
在一般疲劳试验中,CFRP板端由G1和G2(用A、B端表示)两个试件在三次以2KN/S的加载和卸载下,在疲劳试验前已出现,如图4所示。
应变(
)
荷载(KN)
图三静力荷载下板端无溢胶试件板端测量的应变
图四三个应力循环下板端测出的应变(a)试件F70(b)F50
由于准备好的试件有已经成形的溢胶,这就不能精确地获得溢胶实际大小。
但是,由应变片G1和G2量出来的应变说明了溢胶的大小。
溢胶在加固后疲劳性能中的作用可通过应变测量研究。
每个梁板两端溢胶可相应得到比较,如表二所示。
由应变-荷载曲线可看出,梁F125,F90和F70的曲线(如图4a)。
不再呈线性。
梁
溢胶尺寸对比
对比
对比
F125
A
-
A
F90
A>B
A>B
A>B
F70
A
A
A
F55
A
A
A
F50
A
A
A
表二加固梁板端溢胶尺寸和加载次数的对比
说明已超过板端胶的弹性极限,所以呈现非线性。
在第三次加载时,F125A的应变降至0,说明裂纹已开展,板端的曲线有了压应变。
除了F90B,F70A,F50A,F50B(如图4b所示)F40-1A和F40-1B,这些试件似乎比那些测出有拉应变的更为正常和呈线性,这表明溢胶的作用不稳定
图5所示疲劳测试中应变幅度(FRP板一端的由G1测出的同次加荷中最小至最大应变)用应力中幅度而不是绝对应变来减少温度波动引起的影响。
试件F125没有考虑这一点因为它疲劳寿命很短,除
图五A端测得的应变幅度
图六F70中测得的应变幅度
了F40-1A和F40-2A的其他曲线在最后减至0之前都有最大压应变。
从公式
(2)可以看出,如果溢胶作用减小,剥离应力减小,应变会趋向受压,但如果剪应力减小,将会减少受压状态。
开裂或剥离会首先发生在溢胶处,溢胶的作用会减小,在粘结层的剥离应力和剪应力减小之前发生。
May和Hutchinson[13]与Pereira和Morais[14]指出模式I是各向同性材料的最低能量破坏模式。
Cheuk等人[15]指出在疲劳荷载下。
模式I中的裂纹及出现比模式II中合金两面节点的更早。
所以剥离应力将比剪应力更早破坏粘结层。
在这个背景下,代表每个试件的曲线将划分成4个截然不同的阶段进入疲劳破坏。
如图6所示的构件F70B,I阶段从开始至
。
在5KN-70KNF20的(最小、最大荷载)静力荷载下无溢胶的相似试件的应变幅度。
如图3[12]所示。
在这一阶段溢胶是起作用的,但逐渐失去强度。
第II阶段从
至最大压应变。
在这一阶段溢胶不再影响应变。
板端剥离应力逐渐减小,第III阶段从应变达到峰值开始,到快到0时(c点)结束。
板端的剪应力逐渐消失。
第IV阶段是剩余部分,板端附近的胶完全失去强度时开裂就开始了。
F40-1和F40-2这两个较少加荷试件,如图5中所示,压应变曾达到峰值,一直延续到试验结束。
这也说明这两个试件中没有裂纹出现,40KN是疲劳试验的初荷载。
达到峰值压应变时所经历的加载次数的对比,及达到C点是裂纹发生的点,如表2所示,图5清楚说明了当荷载减小时裂纹延迟出现。
在40KN以下,来检测出裂纹。
疲劳试验中在试件F55中测出的应变幅度如图7所示
从中可以看出
G3、G4应变片中的应变随着界面裂缝开展而减小,在大概8万-9万次加载裂纹延伸至应变片位置时接近0.
在板中的G5中的应变从最大值快速降到0,在7万次加载时裂缝从相距50mm的G1开展到G3。
在同样大概7万次下相距150mm的G3、G5也同样发生裂纹开展。
当G5中的应变减小时,钢梁内翼的G6、G7(特别是G7)中的应变增大,这说明荷载已从板端传至梁。
图7.试件F55的应变范围
Fig.7.ThestrainrangesmeasuredinspecimenF55.
4.2.刚度变化
疲劳试验中试件F70用三种电位器测量得出的应变情况如图8所示,从图中可以得出:
●裂纹出现之前梁的刚度保持不变
●应力从T3依次增加到T1,应变随着裂纹的延伸不断变化,直到裂纹扩展到梁的跨中位置。
●相对于钢梁来说贴布的厚度很薄,其应变的增加是很小的。
通过对其他试件的测试也得出了以上结论。
图8.试件F70在疲劳试验下的偏移
Fig.8.DeflectionsofspecimenF70measuredduringthefatiguetest.
4.3.裂纹扩展与断裂
试件F125由于负荷幅度太大,与其他试件的裂纹开裂与和扩展不再相似。
在荷载循环30次后,其一端突然脱胶(如图9):
裂纹最先在板端溢出胶的中心位置出现,呈45°延伸到钢梁与胶层的交界面,并沿交界面一直扩展,最后导致整个板剥离。
这种情况,通常还会有一小段未开裂的胶体将板和梁粘结在一起。
图9.试件F125的脱胶剥离
Fig.9.DebondinginF125.
图10以具有代表性的试件F90得出裂纹的扩展过程,从图中可以看出,裂纹一旦形成,就会从端部迅速延伸,当两端裂纹中的一条延伸到梁的中部时,裂纹基本就会停止扩展。
图10.试件F90的裂纹扩展
Fig.10.CrackgrowthinspecimenF90.
4.4.S-N的曲线
从图11所示的外荷载与循环次数的关系可以看出,最大界面主应力(P)或相对最大荷载主应力(P/Pu)与循环次数(Nf)的对数logNf近似呈线性关系,经线性拟合得出下式(相关系数R2=0.97):
(3)
上式仅由受测试件结果得出,并无实际应用。
图11.呈对数关系的P-N曲线
Fig.11.P–Ncurveinlogarithmicrepresentation.
由于最大主应力随裂纹的扩展而增大,循环次数就不能直接用来形成S-N曲线。
由理论分析[12]知,最大主应力在裂纹开裂之前是常数。
最大界面主应力
及相对最大界面应力
和裂纹开裂时破坏频率
的对数值
的近似线性关系曲线如图12所示,经线性拟合得下式(相关系数R2=0.96):
(4)
上式基于以下假设,即认为金属梁CFRP板与CFRP板之间的黏结强度不受两者尺寸及物理性质的影响[12]。
因而,如果使用的粘接胶相同,上述S-N曲线关系就可以推广应用的。
图12.呈对数关系的S-N曲线
Fig.12.S–Ncurveinlogarithmicrepresentation.
试件F40-1和F40-2在四百万个周期作用后依然没有被破坏,其中试件F40-1经过三百万个周期作用后,试件F40-2经过二百万个周期作用后,CFRP板的端部才会出现微小的应力变化(如图5),故可认为两种试件不会发生疲劳破坏。
因此测试试件的疲劳极限荷载可取40kN,相应粘接的疲劳极限应力为23.8Mpa,这一值相对于粘接强度80.4MPa为30%。
4.5.疲劳测试后样品F40-2的强度
如第3节所详述,疲劳试验后试件F40-2在静载试验下会产生破坏。
破坏时的荷载为133kN,很接近没经过疲劳过程的试件F135的强度135kN,从图13这两个试件的载荷-位移曲线对比中可看出,疲劳测试相对于静载作用对粘接强度没有多大影响。
图13.试件在疲劳试验和未经疲劳试验下的载荷-位移曲线对比
Fig.13.Comparisonsofload–deflectioncurvesbetweenspecimenswithfatiguetestandwithoutfatiguetest.
在静荷载作用下试件F40-2的CFRP板端部应力如图3所示,无溢出胶的试件S304s的应力-应变曲线如图14,分别标记为G1,G2。
通过比较上述几条曲线可知,在试件的应力递减阶段,有溢出胶的要比无溢出胶的线性性更好,这表明溢出胶对应力将不再有影响,板端的粘接胶在疲劳试验后塑性会降低。
图14.试件F40-2与试件S304s端部应力对比
Fig.14.Comparisonsofstainattheplateends
betweenspecimensF40-2andS304s.
4.6.疲劳荷载幅度的效应
试件F70*上所加的最小负荷为20kN,因而,和试件F55一样,疲劳荷载幅度为50kN。
图15比较了试件F70A、F70*A及F55A的应变幅度与荷载循环的关系曲线,可以看出梁F70*比F70更接近梁F55曲线。
应变仪记录数据显示,试件F70*破坏循环次数是6400和7400,这比F55(17000和18000)更接近于F70的破坏循环次数3000和4000。
综上所述,疲劳荷载幅度对疲劳特性有一定影响,但这种影响远小于最大疲劳荷载的作用。
图15.试件F70A、F70*A及F55A的应力幅度比较
Fig.15.Comparisonsofthestainrangesobtained
forspecimensF70A,F70*AandF55A.
5.结论
本文通过疲劳试验对小尺寸钢梁在粘贴400mmCFRP板时的性能进行了研究,主要结论有:
●试验中采用隐面应变技术来检测裂纹的开裂和扩展。
检测结果表明,当裂纹开裂时应变仪能及时记录,并可对裂纹在胶层内的延伸路径进行追踪。
由此可见,用隐面应变技术来检测CFRP加固钢梁的性能,既简单又有效。
●应变仪对应变的检测结果表明,裂纹的开裂和扩展在样本I上要早于与梁贴接在一起的样本II,这也证明了双盖板搭接接头的结论是合理的[15]。
●由于外加应力幅度随裂纹扩展而增加,得出的裂纹扩展速度就会同时受观测和迅速发展起来的隐面应变技术两因素的共同影响。
测出的应变值表明板端溢出胶对粘接结合面的抗疲劳性具有一定的加强作用,当这种作用不是很大。
CFRP板加固钢梁的刚度会因裂纹的扩展而降低,但降低的幅度与试验所贴CFRP薄板的厚度并没有多大关系。
●通过试验得到了S–N曲线。
该曲线表示由理论计算的最大界面应力和循环次数之间的关系,故可以用于使用同一结构胶的其他尺寸和材料性能的CFRP加固钢梁。
加固梁粘接层S-N曲线的疲劳极限(或说临界点),大约是静载破坏时最大极限界面应力的30%,这与英国规程CIRIA的推荐值相符[9]。
●CFRP加固钢梁在极限状态下,疲劳荷载的影响作用相比静载作用可忽略不计。
试验显示疲劳荷载幅度对其疲劳寿命有一定的影响,但这种影响远小于最大疲劳荷载的作用。
致谢
第一作者邓军特向南安普敦大学在本次工作中所给予的经费支持表示感谢。