数控铣工教程.docx
《数控铣工教程.docx》由会员分享,可在线阅读,更多相关《数控铣工教程.docx(35页珍藏版)》请在冰豆网上搜索。
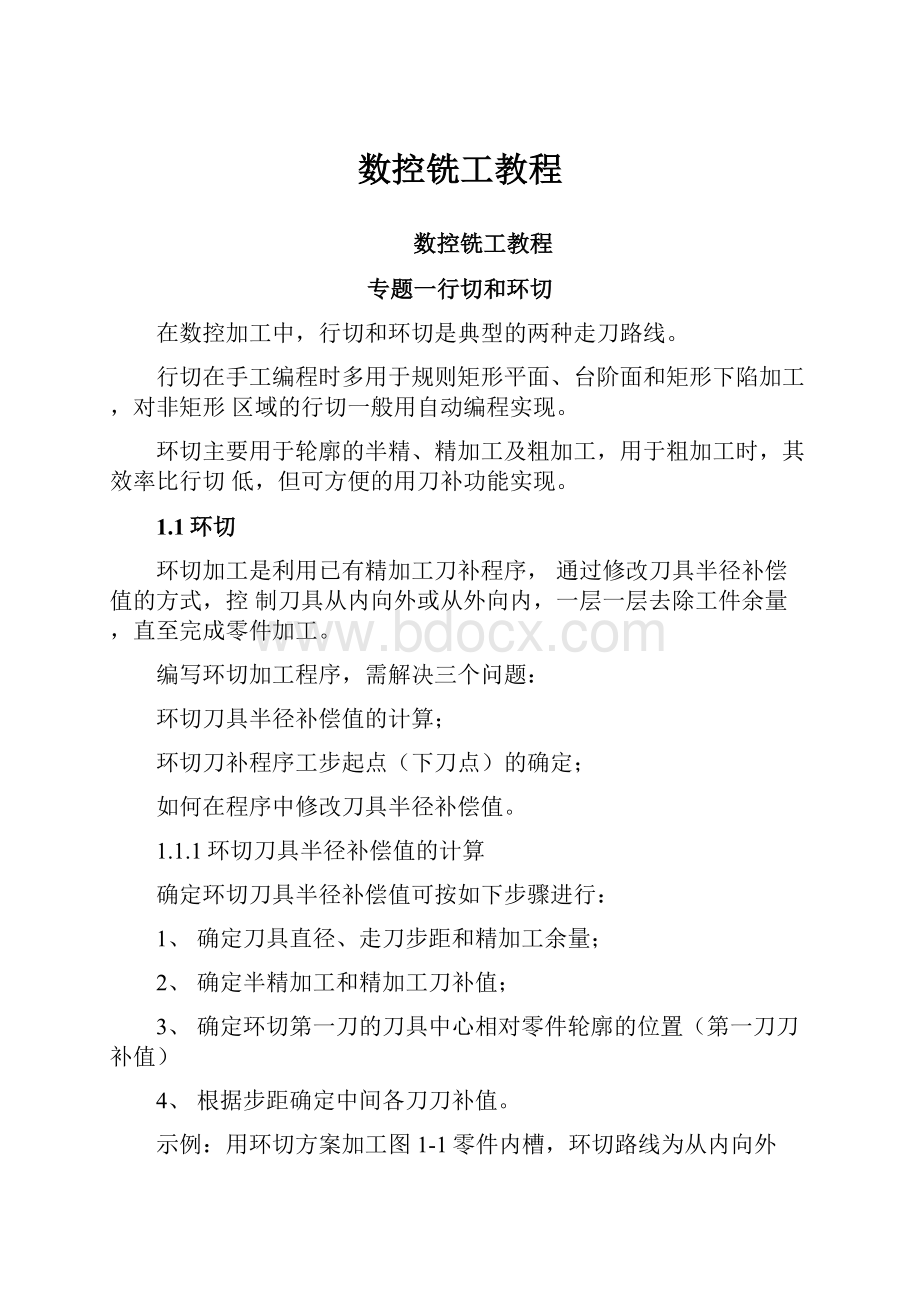
数控铣工教程
数控铣工教程
专题一行切和环切
在数控加工中,行切和环切是典型的两种走刀路线。
行切在手工编程时多用于规则矩形平面、台阶面和矩形下陷加工,对非矩形区域的行切一般用自动编程实现。
环切主要用于轮廓的半精、精加工及粗加工,用于粗加工时,其效率比行切低,但可方便的用刀补功能实现。
1.1环切
环切加工是利用已有精加工刀补程序,通过修改刀具半径补偿值的方式,控制刀具从内向外或从外向内,一层一层去除工件余量,直至完成零件加工。
编写环切加工程序,需解决三个问题:
环切刀具半径补偿值的计算;
环切刀补程序工步起点(下刀点)的确定;
如何在程序中修改刀具半径补偿值。
1.1.1环切刀具半径补偿值的计算
确定环切刀具半径补偿值可按如下步骤进行:
1、确定刀具直径、走刀步距和精加工余量;
2、确定半精加工和精加工刀补值;
3、确定环切第一刀的刀具中心相对零件轮廓的位置(第一刀刀补值)
4、根据步距确定中间各刀刀补值。
示例:
用环切方案加工图1-1零件内槽,环切路线为从内向外
环切刀补值确定过程如下:
1、根据内槽圆角半径R6,选取©12键槽铣刀,精加工余量为0.5mm走刀步距取10mm
2、由刀具半径6,可知精加工和半精加工的刀补半径分别为6和6.5mm
3、如图所示,为保证第一刀的左右两条轨迹按步距要求重叠,则两轨迹间距离等于步距,则该刀刀补值=30-10/2=25mm
4、根据步距确定中间各刀刀补值,
第二刀刀补值=25-10=15mm
第三刀刀补值=15-10=5,该值小于半精加工刀补值,说明此刀不需要。
由上述过程,可知,环切共需4刀,
刀补值分别为25、15、6.5、6mm
1.1.2环切刀补程序工步起点(下刀点)的确定
对于封闭轮廓的刀补加工程序来说,一般选择轮廓上凸出的角作为切削起点,对内轮廓,如没有这样的点,也可以选取圆弧与直线的相切点,以避免在轮廓上
留下接刀痕。
在确定切削起点后,再在该点附近确定一个合适的点,来完成刀补的建立与撤消,这个专用于刀补建立与撤消的点就是刀补程序的工步起点,一般情况下也是刀补程序的下刀点。
一般而言,当选择轮廓上凸出的角作为切削起点时,刀补程序的下刀点应在该角的角平分线上(45°方向),当选取圆弧与直线的相切点或某水平/垂直直线上的点作为切削起点时,刀补程序的下刀点与切削起点的连线应与直线部分垂直。
在一般的刀补程序中,为缩短空刀距离,下刀点与切削起点的距离比刀具半径略大一点,下刀时刀具与工件不发生干涉即可。
但在环切刀补程序中,下刀点与切削起点的距离应大于在上一步骤中确定的最大刀具半径补偿值,以避免产生刀具
干涉报警。
如对图1-1零件,取R30圆弧圆心为编程零点,取R30圆弧右侧端点作为切削起点,如刀补程序仅用于精加工,下刀点取在(22,0)即可,该点至
切削起点距离=8mm但在环切时,由于前两刀的刀具半径补偿值大于8mm建立刀补时,刀具实际运动方向是向左,而程序中指定的运动方向是向右,撤消刀补时与此类似,此时数控系统就会产生刀具干涉报警。
因此合理的下刀点应在编程零点(0,0)。
1.1.3在程序中修改刀具半径补偿值
在程序中修改刀具半径补偿值可采用如下方法
1、在刀补表中设好环切每一刀的刀具半径补偿值,然后在刀补程序中修改刀具补偿号。
示例1.1直接在G41/G42程序段修改刀具补偿号
主程序
%1000
G54G90G0G17G40;
Z50M03S1000;
X0Y0;
Z5M08;
G1Z-10F60;
G41X30D1F100;
M98P0010;
G41X30D2F100;
M98P0010;
G41X30D3F100;
M98P0010;
G41X30D4F100;
M98P0010;
M05M09:
子程序
%0010G90G1Y60;
X-30;
Y0;
G3X30R30;G0G40X0;M99;
补偿号
刀具补偿半径
1
25
2
15
3
6.5
4
6
利用循环修改刀具补偿号
示例1.2用宏变量表示刀具补偿号,
%100
Y60;
G54G90GOG17G40;
X-30;
Z50M03S1000;
Y0;
X0Y0;
G3X30R30;
Z5M08;
G0G40X0;
G1Z-10F60;
#仁#1+1;
#1=1;刀补号变量
End1;
WHILE#1LE4D01;
Z50;
G41X30D#1F100;
5
2、使用G10修改刀具补偿半径
示例1.3,使用G10和子程序完成环切
主程序
M98P0010;
%100
M05M09;
G54G90G0G17G40;
G0Z50;
Z50M03S1000;
M30;
X0Y0;
Z5M08;
子程序
G1Z-10F60;
%0010
G10L10P1R25;
G90G41X30D1F100;
M98P0010;
Y60;
G10L10P1R15;
X-30;
M98P0010;
Y0;
G10L10P1R6.5;
G3X30R30;
M98P0010;
G0G40X0;
示例1.4使用G10和循环完成环切
%1000
G41X30D1F100;
G54G90G0G17G40;
Y60;
Z50M03S1000;
X-30;
X0Y0;
Y0;
Z5M08;
G3X30R30;
G1Z-10F60;
G0G40X0;
#10=25;粗加工起始刀补值
#10=#10-#11;
#11=10;步距
END2;
#12=6;精加工刀补值
#10=#12+0.5:
半精加工刀补值
#仁2;粗、精加工控制
#11=0.5;
WHILE[#1GE1]DO1;
#仁#1-1;
WHILE#10GE#12DO2;
END1;
G10L10P1R#10:
Z50;
3、直接用宏变量对刀补值赋值
示例1.5直接用宏变量对刀补值赋值,利用循环完成环切
%1000
G54G90GOG17G40;
Z50M03S1000;
X0Y0;
Z5M08;
G1Z-10F60;
#10=25;粗加工起始刀补值
#11=9.25;步距
#12=6;精加工刀补值
#仁2;粗、精加工控制
WHILE]#1GE1]DO1;
WHILE]#10GE#12]DO2;
G41X30D[#10]F100;
Y60;
X-30;
Y0;
G3X30R30;
G0G40X0;#10=#10-#11;
END2;
#10=#12;半精加工刀补值
#1=#1-1;
END1;
Z50;
说明:
在G41X30d#10中,#10表示刀具补偿号,而在G41X30d[#10]中,#10表示刀具半径补偿值,此用法在FANU(说明书中没有,但实际使用的结果确实如此,如所用系统不支持此用法,就只用示例1.4用法。
1.1.4环切宏程序
当使用刀具半径补偿来完成环切时,不管我们采用何种方式修改刀具半径补偿值,由于受刀补建、撤的限制,它们都存在走刀路线不够简洁,空刀距离较长的问题。
对于象图1-1所示的轮廓,其刀具中心轨迹很好计算,此时如用宏程序直接计算中心轨迹路线,则可简化走刀路线,缩短空刀距离。
示例1.6完全使用宏程序的环切加工
如图1-2所示,用#1、#2表示轮廓左右和上边界尺寸,编程零点在R30圆心,
加工起始点放在轮廓右上角(可削除接刀痕)
%1000
G54G90GOG17G40;
Z50M03S100;
#4=30;左右边界
#5=60;上边界
#10=25粗加工刀具中心相对轮廓偏移量(相当于刀补程序中的刀补值)
#11=9.25步距
#12=6;精加工刀具中心相对轮廓偏移量(刀具真实半径)
G0X[#4-#10-2]Y[#5-#10-2];
Z5;
G1Z-10F60;
#20=2;
WHILE[#20GE2]DO1;
WHILE[#10GE#12]DO2;
#仁#4-#10;左右实际边界#2=#5-#10;上边实际边界
G1X[#1-2]Y[#2-2]F200;
G3X#1Y#2R2;圆弧切入到切削起点
G1X[-#1];
Y0;
G3X#1R#1;
G1Y#2;
G3X[#1-2]Y[#2-2]R2#10=#10-#11
END2
#10=#12
#20=#20-1
END1
G0Z50
M30
1.2行切
一般来说,行切主要用于粗加工,在手工编程时多用于规则矩形平面、台阶面和矩形下陷加工,对非矩形区域的行切一般用自动编程实现。
1.2.1矩形区域的行切计算
1矩形平面的行切区域计算
如图所示,矩形平面一般采用图示直刀路线加工,在主切削方向,刀具中心需切削至零件轮廓边,在进刀方向,在起始和终止位置,刀具边沿需伸出工件一距离,以避免欠切。
假定工件尺寸如图所示,采用①60面铣刀加工,步距50mm上、下边界刀具各伸出10mm则行切区域尺寸为800X560(600+10*2-60)。
2、矩形下陷的行切区域计算
对矩形下陷而言,由于行切只用于去除中间部分余量,下陷的轮廓是采用环切获得的,因此其行切区域为半精加工形成的矩形区域,计算方法与矩形平面类似。
假定下陷尺寸100*80,由圆角R6选①12铣刀,精加工余量0.5mm步距10mm则半精加工形成的矩形为
(100-12*2-
0.5*2)*(80-12*2-0.5*2)=75*55。
如行切上、下边界刀具各伸出1mm则实际切削区域尺寸=75*(55+2-12)=75*45。
1.2.2行切的子程序实现
对于行切走刀路线而言,每来回切削一次,其切削动作形成一种重复,如果将来回切削一次做成增量子程序,则利用子程序的重复可完成行切加工。
1、切削次数与子程序重复次数计算
进刀次数n=总进刀距离/步距=47/10=4.5,实际需切削6刀,进刀5次。
子程序重复次数m=n/2=5/2=2,剩余一刀进行补刀。
步距的调整:
步距=总进刀距离/切削次数。
说明:
当实际切削次数约为偶数刀时,应对步距进行调整,以方便程序编写;
当实际切削次数约为奇数刀时,可加1成偶数刀,再对步距进行调整,或直接将剩下的一刀放在行切后的补刀中,此时不需调整步距。
由于行切最后一刀总是进刀动作,故行切后一般需补刀。
2、示例1.7
对图1-4零件,编程零点设在工件中央,下刀点选在左下角点,加工程序如下:
子程序
%0020
G91G1X75F150;Y10;
X-75;
Y10.;
G90M99;
主程序
%1000
G54G90GOG17G40;
Z50M03S800;
G0X-43.5Y-33.5;定位到下刀点
Z5;
G1Z-10F100;
M98P0010;环切加工,
该程序省略
G1X-37.5Y-22.5;行切起点
M98P0020L2;行切加工
G1X37.5;补刀
Y22.5
X-37.5
G0Z50;
M30r
1.2.3行切宏程序实现
对图1-4零件,编程零点设在工件中央,下刀点选在左下角点,加工宏程序如下:
示例1.8(本程序未考虑分层下刀问题)
主程序
%1000
G54G90G0G17G40
Z50M03S800
G65P9010A100B80C0D6Q0.5K10X0Y0Z-10F150G0Z50
M30
宏程序调用参数说明:
A倂1)B(#2)——矩形下陷的长与宽
C(#3)粗精加工标志,C=0,完成粗精加工,C=1,只完成精加
工。
D(#7)刀具半径
Q(#17)精加工余量
K(#6)步距
X(#24)Y(#25)----下陷中心坐标
Z(#26)下陷深度
F(#9)走刀速度
宏程序
G0Z5;N200M99;
专题二相同轮廓的重复加工
在实际加工中,相同轮廓的重复加工主要有两种情况:
1同一零件上相同轮廓在不同位置出现多次;
2、在连续板料上加工多个零件。
实现相同轮廓重复加工的方法
1用增量方式定制轮廓加工子程序,在主程序中用绝对方式对轮廓进行定位,再调用子程序完成加工。
2用绝对方式定制轮廓加工子程序,并解决坐标系平移的问题来完成加工。
3、用宏程序来完成加工。
2.1用增量方式完成相同轮廓的重复加工
示例2-1,加工图2-1所示工件,取零件中心为编程零点,选用©12键槽铣刀加工。
子程序用中心轨迹编程。
主程序
%1000
G54G90G0G17G40M03;Z50S2000;
X-150Y-50;
Z5;
M98P0010;
G0X-150Y50;
M98P0010;
G0X0Y50;
M98P0010;
G0X0Y-50;
M98P0010;
G0X-150Y-50;
M98P0010;
G0X-150Y50;
M98P0010;
G0Z100;
M30;
子程序
%0010
G91GOX24;G1Z-27F60;
G3I-24F200;
G0Z12;
G1X10;
G31-34;
2.2用坐标系平移完成相同轮廓的重复加工
坐标系平移有两种方式
G54+G52用于重复次数不多,且轮廓分布无规律情况。
G54+G92用于轮廓分布有规律且重复次数很多的情况。
示例2-2用局部坐标系G52完成相同轮廓的重复加工,G54零点设在零件中心,局部坐标系零点在需加工孔的孔心。
主程序
%1000
G54G90G0G17G40;
Z50M03M07S1000;
G52X-150Y-50;
M98P0020;
G52X-150Y50;
M98P0020;
G52X0Y50;
M98P0020;
G52X0Y-50;
M98P0020;
G52X150Y-50;
M98P0020;
G52X0Y0;恢复G54GOZ100;
M30;
子程序
%0020
G90G0X24;
Z5;
G1Z-22F100;
G3I-24;
G0Z-10;
G1X34;
G3I-34;
G0Z5;
2.3用宏程序完成相同轮廓的重复加工
示例2-4,用G65调用完成加工,宏程序用绝对编程
%1000
G54G90G0G17G40M03;
Z50S2000;
Z5;
G65P9010X-150Y-50;
G65P9010X-150Y50;
G65P9010X0Y50;
G65P9010X0Y-50;
G65P9010X150Y-50;
G65P9010X150Y50;
G0Z100;
宏程序
%9010
G90G0X[#24+24]Y#25
Z5
G1Z-20F60
G3I-24F200
G0Z-10
G1X[#24+34]
G3I-34
G0Z5
M99
示例2-5,用G66调用完成加工,宏程序用绝对编程
%1000
%9011
G54G90G0G17G40;
#1=#5001;取当前孔心坐标
Z50M03M07S1000;
#2=#5002;
X-150Y-50;
G90G0X[#1+24]Y#2;
G66P9011;
Z5;
G0X-150Y50;
G1Z-22F100;
X0Y50;
G3I-24;
X0Y-50;
G0Z-10;
X150Y-50;
G1X[#1+34];
X150Y50;
G3I-34;
G67;
G0Z5;
G0Z100;
M99;
示例2-6,使用循环,用一个程序完成加工
%1000
G54G90GOG17G40;
Z50M03M07S1000;
#1=2;行数
#2=3;列数
#3=150;列距
#4=100;行距
#5=-150;左下角孔中心坐标(起始孔)
#6=-50;
#10=1;列变量
WHILE#10LE#2DO1;
#1仁1;行变量
#20=#5+[#10-1]*#3;待加工孔的孔心坐标X
WHILE#11LE#1DO2;
#21=#6+[#11-1]*#4;孔心坐标Y
G0X[#20+24]Y#21;
Z2;
G1Z-22F100;
G31-24;
G0Z-10;
G1X[#20+34];
G3I-34;
G0Z5;
#11=#11+1;
END2;
#10=#10+1;
END1;
专题三简单平面曲线轮廓加工
对简单平面曲线轮廓进行加工,是采用小直线段逼近曲线来完成的。
具体算
法为:
采用某种规律在曲线上取点,然后用小直线段将这些点连接起来完成加工。
示例3-1,椭圆加工,假定椭圆长(X向)、短轴(Y向)半长分别为A和B,则椭圆的极坐标方程为%=*90^,利用此方程可方便地完成在椭圆上取点工作。
y=b.sin日
编程条件:
编程零点在椭圆中心,a=50,b=30,椭圆轮廓为外轮廓,下刀点在椭圆右极限点,刀具直径©18,加工深度10mm程序如下:
%1000
G54G90G0G17G40;
Z50M30S1000;
X60Y-15;
Z5M07;
G1Z-12F800;
G42X50D1F100;
Y0;
#1=0.5;B变量初始值0.5度
WHILE#1LE360DO1;
#2=50*COS[#1];
#3=30*SIN[#1];
G1X#2Y#3;
#仁#1+0.5;
END1;
G1Y15;
G0G40X60;
Z100;
专题四简单立体曲面加工
4.1球面加工
球面加工使用的刀具
粗加工可以使用键槽铣刀或立铣刀,
也可以使用球头铣刀。
精加工应使用球头铣刀。
球面加工的走刀路线
一般使用一系列水平面截球面所形成的同心圆来完成走刀。
在进刀控制上有从上向下进刀和从下向上进刀两种,一般应使用从下向上进刀来完成加工,此时主要利用铣刀侧刃切削,表面质量较好,端刃磨损较小,同时切削力将刀具向欠切方向推,有利于控制加工尺寸。
进刀控制算法
进刀点的计算:
先根据允许的加工误差和表面粗糙度,确定合理的Z向进刀量,再根据给定
加工深度Z,计算加工圆的半径,即:
r=sqrt[R2-z2]。
此算法走刀次数较多。
先根据允许的加工误差和表面粗糙度,确定两相邻进刀点相对球心的角度增量,再根据角度计算进刀点的r和Z值,即Z=R*sin9,r=R*cosB。
进刀轨迹的处理
对立铣刀加工,曲面加工是刀尖完成的,当刀尖沿圆弧运动时,其刀具中心运动轨迹也是一行径的圆弧,只是位置相差一个刀具半径。
对球头刀加工,曲面加工是球刃完成的,其刀具中心是球面的同心球面,半径相差一个刀具半径。
4.1.1外球面加工
示例4-1,加工图4-3所示外球面。
为对刀方便,宏程序编程零点在球面最高点处,采用从下向上进刀方式。
立铣刀加工宏程序号为%9013球刀加工宏程
序号%9014
主程序
%1000
G91G28Z0
M06T01
G54G90G0G17G40
G43Z50H1M03S3000
G65P9013X0Y0Z-30D6I40.5Q3F800
G49Z100M05
G28Z105
M06T02
G43Z50H2M03S4000
G65P9014X0Y0Z-30D6I40Q0.5F1000
G49Z100M05
G28Z105
宏程序
宏程序调用参数说明
X(#24)/Y(#25)
Z(#26)
D(#7)
Q(#17)
I(#4)
球心坐标
球高
刀具半径
角度增量,度球径
图4-3
%9013
%9014
#仁#4+#26;进刀点相对球心Z坐标
#1=#4+#26;中间变量
#2=SQRT[#4*#4-#1*#1];切削圆半径
#2=SQRT[#4*#4-#1*#1];中间变量
#3=ATAN#1/#2;角度初值
#3=ATAN#1/#2;角度初值
#2=#2+#7;
#4=#4+#7;处理球径
G90G0X[#24+#2+#7+2]Y#25;
#1=#4*[SIN[#3]-1];Z=-(R-RSIN9)
Z5;
#2=#4*COS[#3];r=RCOS9
G1Z#26F300;
G90G0X[#24+#2+2]Y[#25];
WHILE[#3LT90]DO1;当进刀点
Z5;
相对水平方向夹角小于90度时加工
G1Z#26F300;
G1Z#1F#9;
WHILE]#3LT90]DO1;当角小于90度
X[#24+#2];
时加工
G2I-#2;
G1Z#1F#9;
#3=#3+#17;
X[#24+#2];
#1=#4*[SIN[#3]-1];Z=-(R-RSIN9)
G2I-#2;
#2=#4*COS[#3]+#7;r=RCOS9+r刀
#3=#3+#17;
END1;
#1=#4*[SIN[#3]-1];Z=-(R-RSIN9)
G0Z5;
#2=#4*COS[#3];r=RCOS9
M99;
END1;
G0Z5・
4.1.2内球面加工
示例4-2,加工图4-4所示内球面。
为对刀方便,宏程序编程零点在球面最高处中心,采用从下向上进刀方式。
其主程序与示例4-1类似,宏程序调用参数与示例4-1相同,本例不再给出。
立铣刀加工宏程序号为%9015球刀加工宏程序号%9016
4.2水平圆柱面的加工
水平圆柱面加工可采用行切加工
沿圆柱面轴向走刀,沿圆周方向进刀;走刀路线短,加工效率高,加工后圆柱面直线度好;用于模具加工,脱模力较大;程序可用宏程序