FMEA教材1.docx
《FMEA教材1.docx》由会员分享,可在线阅读,更多相关《FMEA教材1.docx(24页珍藏版)》请在冰豆网上搜索。
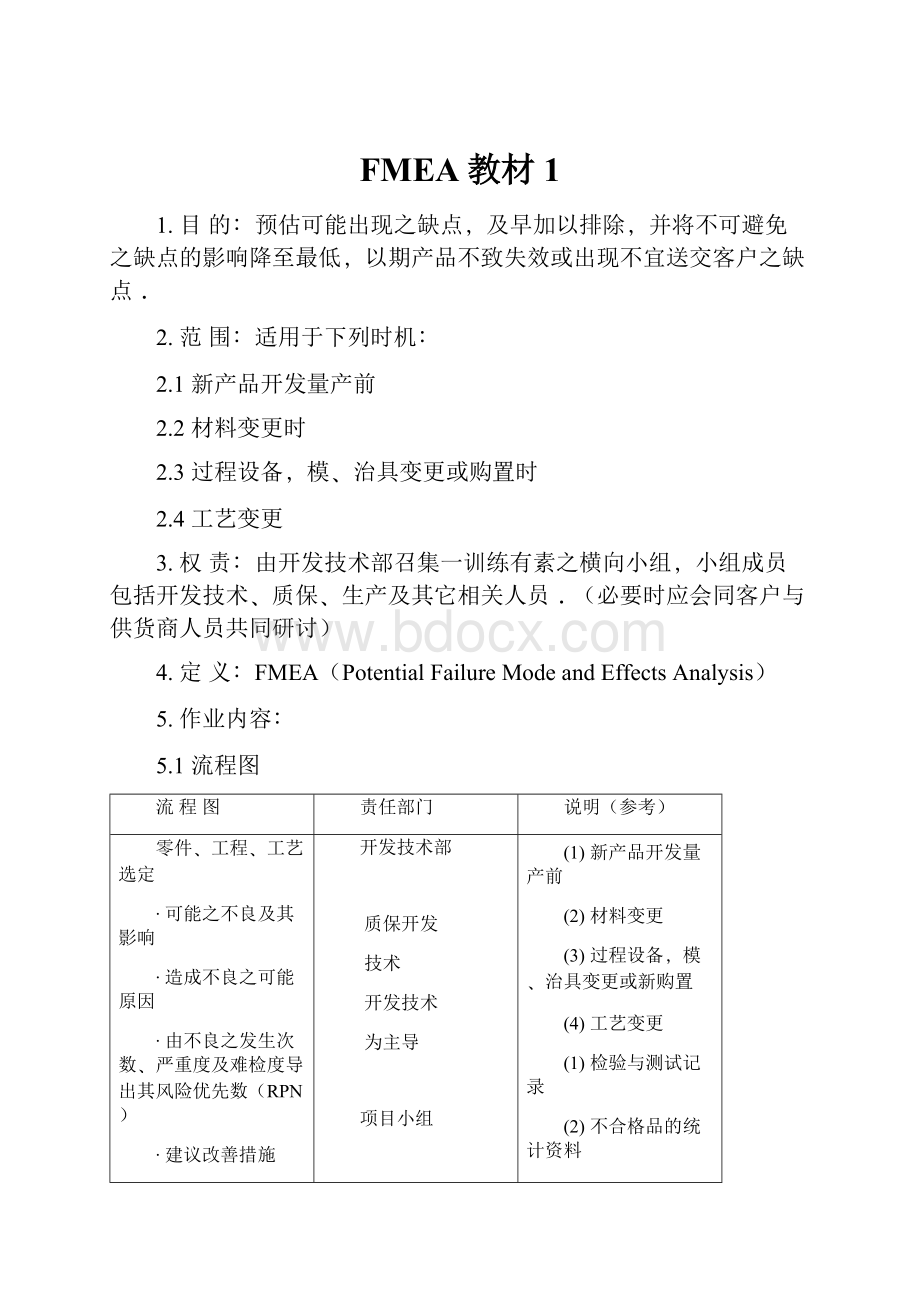
FMEA教材1
1.目的﹕预估可能出现之缺点﹐及早加以排除﹐并将不可避免之缺点的影响降至最低﹐以期产品不致失效或出现不宜送交客户之缺点﹒
2.范围﹕适用于下列时机﹕
2.1新产品开发量产前
2.2材料变更时
2.3过程设备﹐模﹑治具变更或购置时
2.4工艺变更
3.权责﹕由开发技术部召集一训练有素之横向小组﹐小组成员包括开发技术﹑质保﹑生产及其它相关人员﹒(必要时应会同客户与供货商人员共同研讨)
4.定义﹕FMEA(PotentialFailureModeandEffectsAnalysis)
5.作业内容﹕
5.1流程图
流程图
责任部门
说明(参考)
零件﹑工程﹑工艺选定
‧可能之不良及其影响
‧造成不良之可能原因
‧由不良之发生次数﹑严重度及难检度导出其风险优先数(RPN)
‧建议改善措施
‧评估及采行改善措施
‧继续降低RPN
下次开发类似产品之经验
(KNOWHOW)
预防并减少量产时之不良
过去客户抱怨
产品/制程设计
客户提供图样
过去累积经验
降低成本客户满意
FMEA
持续改善
开发技术部
质保开发
技术
开发技术
为主导
项目小组
开发技术质保
市场质保开发技术
(1)新产品开发量产前
(2)材料变更
(3)过程设备﹐模﹑治具变更或新购置
(4)工艺变更
(1)检验与测试记录
(2)不合格品的统计资料
(3)纠正预防措施
(4)过去客户抱怨
(5)图样﹑规范
(6)过程流程图﹑特殊特性清单
(7)现有类似的FMEA资料
(8)其它
接受准则
(1)RPN>100必须有对策
(2)严重度>7且RPN>60者必须有对策
5.2设计/过程FMEA表格说明
Design
Process
项次
设计(D)
过程(P)
项目
说明
项目
说明
1
FMEA编号
填入FMEA文件编号﹐以便查询﹒
FMEA编号
填入FMEA文件编号﹐以便查询
2
项目
填入所分析系统﹑子系统或零部件的名称﹑编号﹒
项目
填入所分析系统﹑子系统或零件的过程名称﹑编号
3
设计责任
填入整车厂(OEM)﹑部门和小组﹒如果知道﹐还应包括供方的名称
过程责任
填入整车厂(OEM)﹑部门和小组﹒如果知道﹐还应包括供方的名称﹒
4
编制者
填入负责FMEA准备工作的工程师的姓名﹑电话和所在公司的名称﹒
编制者
填入负责FMEA准备工作的工程师的姓名﹑电话和所在公司的名称
5
年型/车型
填入将使用和/或正被分析的“设计”所影响的预期的年型及车型(如果已知)﹒
年型/车型
填入将使用和/或正被分析的“过程”所影响的预期的年型及车型(如果已知)
6
关键日期
填入FMEA初次预定完成的日期﹐该日期不应超过计划的“生产设计”发布的日期
关键日期
填入FMEA初次预定完成的日期﹐该日期不应超过计划的“开始生产”发布的日期﹒
7
核心小组
填入编制FMEA原始稿的日期及最新修订的日期
核心小组
填入编制FMEA原始稿的日期及最新修订的日期
8
核心小组
列出执行任务的个人姓名
核心小组
列出执行任务的个人姓名
9
项目/功能
被分析项目的名称和编号
过程功能
/要求
简单描述被分析的过程或工序
10
潜在失效模式
预估缺点项目见附件5
潜在失效模式
预估缺点项目见附件5
11
潜在失效后果
缺点之预估影响见附件5
潜在失效后果
缺点之预估影响见附件5
12
严重度Severity
严重度分为1-10级
见附件3
严重度Severity
严重度分为1-10级
见附件4
13
分级(重要度)
产品特性分级(关键﹑主要﹑重要…)标明字母或符号
分级(重要度)
产品特性分级(关键﹑主要﹑重要…)标明字母或符号
14
潜在失效原因
潜在不良原因﹐将一切可能之原因尽量列出见附件5
潜在失效原因
潜在不良原因﹐将一切可能之原因尽量列出见附件5
15
频度Occurrence
发生不良之机率﹐分为
1-10级见附件3
频度Occurrence
发生不良之机率﹐分为
1-10级见附件3
Design
Process
项次
设计(D)
过程(P)
项目
说明
项目
说明
16
现行控制办法(现行设计控制)
‧列出预防措施﹐设计确认/验证﹐Validation/Verification或其它活动﹒
‧现行控制方法指的是那些已经用于或正在用于相同或相似设计中的那些方法(如道路试验﹑设计评审﹑台架/试验室试验﹑可行性评审﹑样件试验和使用试验)﹒
‧三种设计控制方法
(1)防止起因或失效模式出﹐或减少出现率﹔
(2)查明起因并找到纠正措施﹔
(3)查明失效模式﹒
优先运用
(1)﹐次
(2)﹐后(3)
现行控制办法(现行设计控制)
‧可以为防错夹具﹑SPC﹑过程评价等控制方法﹒
‧三种设计控制方法﹕
(1)防止起因或失效模式出﹐或减少出现率﹔
(2)查明起因并找到纠正措施﹔
(3)查明失效模式﹒
优先运用
(1)﹐次
(2)﹐后(3)
17
不易探测度(Detection)
‧指零部件﹑子系统或系统投产前﹐能否探测出其已发生之缺点﹐分为1-10级见附件3
不易探测度(Detection)
‧零部件离开制造工序或装配工位之前﹐能否探测出其已发生之缺点﹐分为1-10级见附件4
18
风险顺序(RPN)
RiskPriorityNumber
风险度=严重度×频度×探测度
风险顺序(RPN)
RiskPriorityNumber
风险度=严重度×频度×探测度
19
建议措施
‧RPN大者先采取纠正措施﹒
‧无建议措施﹐须填写“无”﹒
‧设计确认/验证工作只影响不易探测度﹐只有修改设计严重度减少
‧可考虑但不局限于下列措施﹕
(1)试验设计(特别在多种因素或相互作用时)﹔
(2)修改试验计划﹔
(3)修改设计﹔
(4)修改材料性能要求﹒
建议措施
‧RPN大者先采取纠正措施﹒
‧无建议措施﹐须填写“无”﹒
‧零组件之设计修改才能降低严重度﹒
增加探测缺点的可能性﹐增加品管检验不一定有效﹐需要修改过程和/或设计﹒
20
责任及目标完成日期
填入组织部门及个人﹐预计完成日期
责任及目标完成日期
填入组织部门及个人﹐预计完成日期
21
采取措施
简要记载执行状况﹐并记下生效日期
采取措施
简要记载执行状况﹐并记下生效日期
22
纠正后的RPN
将新的RPN值填入
纠正后的RPN
将新的RPN值填入
6.相关文件/使用窗体
6.1DFMEA范例附件1
6.2DFMEA范例附件2
6.3DFMEA之S.O.D评价准则附件3
6.4PFMEA之S.O.D评价准则附件4
6.5失效模式﹑失效影响及失效原因附件5
附件1
潜在失效模式及后果分析
(设计FMEA)
系统
FMEA编号:
1234①
×子系统
页码:
共1页第1页
零部件:
01、03车身密封②
设计责任:
车身工程部③
编制人:
泰特-X6412-车身工程师④
车型年/车辆类型:
199×/狮牌4门旅行车⑤
关键日期:
9×0301⑥
FMEA日期:
(编制)8×0322(修订)8×0714⑦
主要参加人:
T.Fender—汽车产品部、C.切利得斯—生产部、J.福特—总装部(Dalton.Fraser.Henley总装厂)⑧
项目
功能
潜在
失效模式
潜在
失效的后果
严重
度数
(S)
级
别
潜在失效的
起因/机理
频
度
数
现行设
计控制
不易
探测
度数
(D)
风险
顺序
数
RPN
建议
措施
责任和目标
完成日期
措施结果
采取的措施
严
重
度
数
频
度
数
不易
探测
度数
R.P.N
左前车门
H8HX-0000
-A
·上、下车
·保护乘员
·免受天气、噪声、侧碰撞的影响
·车门附件,如后视镜、门锁、门铰链及门窗升降器等的固定支撑
·为外观装饰项目提供适当的表面
·喷漆和软内饰
车门内板下部腐蚀
车门寿命降低,导致:
·因漆面生锈,使用户对外观不满
·使车门内附件功能降低
车门内板保护蜡的上限太低
6
整车耐久性试验
T—118
T—109
T—301
7
294
增加试验室强化腐蚀试验
A.泰特—车身工程
8×0903
根据试验结果(1481号试验)上边界技术条件提高125㎜
7
2
2
28
蜡层厚度规定不足
4
整车耐久性试验
T—118
T—109
T—301
7
196
增加试验室强化腐蚀试验,并就蜡层厚度进行试验设计
结合观察和试验验证蜡的上边界,A.泰特—车身工程
9×0115
试验结果(试验号1481)表明要求的厚度是合适的。
试验设计表明要求的厚度在25%范围内变化可以接受
7
2
2
28
蜡的配方不当
2
理化试验室
试验—报告
编号:
1265
2
28
无
混入的空气阻止蜡进入边角部分
5
用非功能喷头进行设计辅助调查
8
280
增加集体评价,利用正式生产喷蜡设备和特定的蜡
车身工程和装配部门
8×1115
7
1
3
21
蜡堵塞车门排水孔
3
用最差的蜡和孔尺寸进行试验室试验
1
21
无
根据试验,在有关区域增设3个通气孔
7
1
1
7
车门板之间空间不够,容不下喷关
4
喷头入口的图样评定
示例
4
112
利用辅助设计模型和喷头进行集体评审
车身工程和装配部门
8×1115
评定表明入口合适
7
1
1
7
附件2
潜在失效模式及后果分析
(过程FMEA)
项目名称:
左前门/H8HX—000—A②
FMEA编号:
1450①
过程责任部门:
车身工程部/装配部③
页码:
共1页第1页
车型年/车辆类型:
199×/狮牌4门/旅行车⑤
编制人:
J.福特—X6521—装配部门④
关键日期:
9×03019×0826工位号1⑥
FMEA日期:
(编制)9×0517(修订)9×1106⑦
主要参加人:
A.泰特—车身工程J.史密斯—操作控制R.詹姆斯—生产部J.约翰—维修部⑧
工程功能
要求
潜在的
失效模式
潜在的
失效后果
严重
程度度数
级
别
潜在的失效
原因/机理
频
度
数
现行
过程控制
不可
探测
度数
风险
顺序
数
建议的
措施
责任和目标
完成日期
措施结果
采取的措施
严
重
度
数
频
度
数
不可
探测
度数
风险
顺序数
RPN
车门内部人工涂腊
为覆盖车门内侧,车门下层表面涂以最小厚度的腊,以延缓腐蚀
规定表面涂腊不足
车门寿命下降,导致:
·由于时间长生锈使顾客对外观不满意
·车内门附件功能下降
7
人工插入喷头不够深入
8
每小时进行自测检查,每班检查一次喷膜厚度(深度仪)和范围
5
280
给喷腊器加装深度限位器
制造工程
9×1015
增加限位器,在线上检查喷机
7
2
2
28
制造工程
9×1215
由于同一条线上不同门的复杂程度不同,因此拒绝该项。
7
1
3
21
喷头堵塞
·粘度太高
·温度太低
·压力太低
5
在开始和停机后试验喷雾形状,按照预防维护程序清洗喷头
3
105
使喷腊自动化
制造工程
9×1001
确定了温度和压力限值,安装了限值控制器,控制图显示流程受控。
CPK=1.85
7
1
3
21
因冲击喷头
变形
2
按预防维护程序维护喷头
2
28
无
喷腊时间不足
8
按操作规程进行批量抽样(每班10个门),检查重要部门喷腊范围示例
7
392
安装喷腊定
时器
维修部门
9×0915
安装了自动喷腊定时器,操作者打开喷头,定时器控制关闭,控制图显示流程受控
CPK=2.05
7
1
7
49
附件3
后果
评定准则﹕后果的严重度
严重度
无警告的
严重危害
这是一种非常严重的失效形式﹐它是在没有任何失效预兆的情况下影响到行车安全或违反了政府的有关章程
10
有警告的
严重危害
这是一种非常严重的失效形式﹐是在具有失效预兆的前提下所发生的﹐并影响到行车安全或违反了政府的有关章程
9
很高
车辆(或系统)不能运行﹐丧失基本功能
8
高
车辆(或系统)能运行﹐但性能下降﹐顾客不满意
7
中等
车辆(或系统)能运行﹐但舒适性或方便性部件不能工作﹐顾客感觉不舒服
6
低
车辆(或系统)能运行﹐但舒适性或方便性项目性能下降﹐顾客感觉有些不舒服
5
很低
配合﹑外观或尖响﹑卡嗒响等项目不符合要求﹐大多数顾客发现有缺陷
4
轻微
配合﹑外观或尖响﹑卡嗒响等项目不符合要求﹐有一半顾客发现有缺陷
3
很轻微
配合﹑外观或尖响﹑卡嗒响等项目不符合要求﹐但很少有顾客发现有缺陷
2
无
无影响
1
失效发生可能性
可能的失效率
频度数
很高﹕失效几乎是不可避免的
10
9
高﹕反复发生的失效
8
7
中等﹕偶尔发生的失效
6
5
4
低﹕相对很少发生的失效
3
2
极低﹕失效不太可能发生
1
探测性
评价准则﹕由设计控制可探测的可能性
不易探测度数
绝对不肯定
设计控制将不能和/或不可能找出潜在的原因/机理及后续的失效模式﹐或根本没有设计控制
10
很级少
设计控制只有很极少的机会能找出潜在原因/机理及后续的失效模式
9
极少
设计控制只有级少的机会能找出潜在原因/机理及后续的失效模式
8
很少
设计控制只有很少的机会能找出潜在原因/机理及后续的失效模式
7
少
设计控制只有较少的机会能找出潜在原因/机理及后续的失效模式
6
中等
设计控制有中等机会能找出潜在原因/机理及后续的失效模式
5
中上
设计控制有中上等多的机会能找出潜在原因/机理及后续的失效模式
4
多
设计控制有较多的机会能找出潜在原因/机理及后续的失效模式
3
很多
设计控制有很多的机会能找出潜在原因/机理及后续的失效模式
2
几乎肯定
设计控制几乎肯定能够找出潜在原因/机理及后续的失效模式
1
附件4
后果
判定准则﹕后果的严重度
严重度数
无警告的
严重危害
可能危害机器或装配操作者﹒潜在失效模式严重影响车辆安全运行和/或包含不符合政府法规项﹐严重程度很高﹒失效发生时无警告﹒
10
有警告的
严重危害
可能危害机器或装配操作者﹒潜在失效模式严重影响车辆安全运行和/或包含不符合政府法规项﹐严重程度很高﹒失效发生时有警告﹒
9
很高
生产线严重破坏﹐可能100%的产品得报废﹐车辆/系统无法运行﹐丧失基本功能﹐顾客非常不满﹒
8
高
生产线破坏不严重﹐产品需筛选部份(低于100%)报废﹐车辆能运行﹐但性能下降﹐顾客不满意﹒
7
中等
生产线破坏不严重﹐部份(低于100%)产品报废(不筛选)﹐车辆/系统能运行﹐但舒适性方便性项目失效﹐顾客有些不满意﹒
6
低
生产线破坏不严重﹐产品需要100%返工﹐车辆或系统能运行﹐但有些舒适性或方便性项目性能下降﹐顾客有些不满意﹒
5
很低
生产线破坏不严重﹐生产经筛选﹐部份(少于100%)需要返工﹐装配和涂装或尖响和卡喀响等项目不符合要求﹐多数顾客发现有缺陷﹒
4
轻微
生产线破坏较轻﹐部份(少于100%)需要在生产线上其它工位返工﹒装配和涂装或尖响和卡喀响等项目不符合要求﹐有一半顾客发现有缺陷﹒
3
很轻微
生产线破坏轻微﹐部份(少于100%)需要在生产线上原工位返工﹐装配和涂装或尖响和卡喀响等项目不符合要求﹐很少顾客发现有缺陷﹒
2
无
没有影响
1
失效发生的可能性
可能的失效率
Cpk
频度数
很高﹕失效几乎是不可避免的
<
10
9
高﹕一般与以前经常发生失效的过程相似的工艺有关
8
7
中等﹕一般与以前时有失效发生﹐但不占主要比例的过程相类似的工艺有关
6
5
4
低﹕很少几次与相似过程有关的失效
3
很低﹕很少几次与几乎完全相同的过程有关的失效
2
极低﹕失效不大可能发生﹒几乎完全相同的过程也未有过失效
1
附件4(续)
探测性
评价准则﹕在下一个或后续工艺前﹐或零部件离开制造或装配工位之前﹐利用过程控制方法找出缺陷存在的可能性
不易探测度数
几乎不可能
没有已知的控制方法能找出失效模式
10
很微小
现行控制方法找出失效模式的可能性很微小
9
微小
现行控制方法找出失效模式的可能性微小
8
很小
现行控制方法找出失效模式的可能性很小
7
小
现行控制方法找出失效模式的可能性小
6
中等
现行控制方法找出失效模式的可能性中等
5
中上
现行控制方法找出失效模式的可能性中等偏上
4
高
现行控制方法找出失效模式的可能性高
3
很高
现行控制方法找出失效模式的可能性很高
2
几乎肯定
现行工艺控制方法几乎肯定能找出失效模式﹐已知相似工艺的可靠的探测控制方法
1
附件5
常见之失效模式﹑失效影响及失效原因
失效模式
(缺点项目)
失效影响
失效原因
弯曲
装配不正
脆性
不平衡
融解
破损
过短
变形磨损
打滑
支撑不足
脱离太快
信号间断
皱
粗糙
不齐
折断
短路
腐蚀
粗糙
褪色
氧化
变形
无支撑
不传输扭矩
翘
松动
漆剥落
漏装
扭曲
过紧
漏泄
裂痕
砂孔
无信号
信号不足
漏气
冷却不够
车辆性能减退
乱挡
臭气
漏水
操作费力
收音机不作用
引擎不起动
噪音
警示灯不灵
电动窗不作用
剎车失灵
驾驶盘不灵
跳动
耗油量偏高
剎车有响声
加力挡不灵
坐椅不定位
燃油有烟
漏机油
装配错误
速度﹑送料不正确
热处理度收缩
不齐
超出规格
量具不准
包装损坏
夹持力不足
通气不足
运搬破损
材料不良
工具装设不当
过热
负荷过大
间隙不良
工具磨耗
零件损坏
工具不当
表面处理不当
漏装
扭力不当
控制系统不良
工具损坏
润滑不足
备注﹕
规定的材料──不对
设计的寿命──估计不当
应力──过大
维修保养说明──不当
计算──错误
扭矩不正确──过大﹑过小
焊接不正确──电流﹑时间﹑压力不对
热处理不正确──时间﹑温度有误
作业人员──操作错误