钢包双透气砖底吹氩工艺水模研究.docx
《钢包双透气砖底吹氩工艺水模研究.docx》由会员分享,可在线阅读,更多相关《钢包双透气砖底吹氩工艺水模研究.docx(39页珍藏版)》请在冰豆网上搜索。
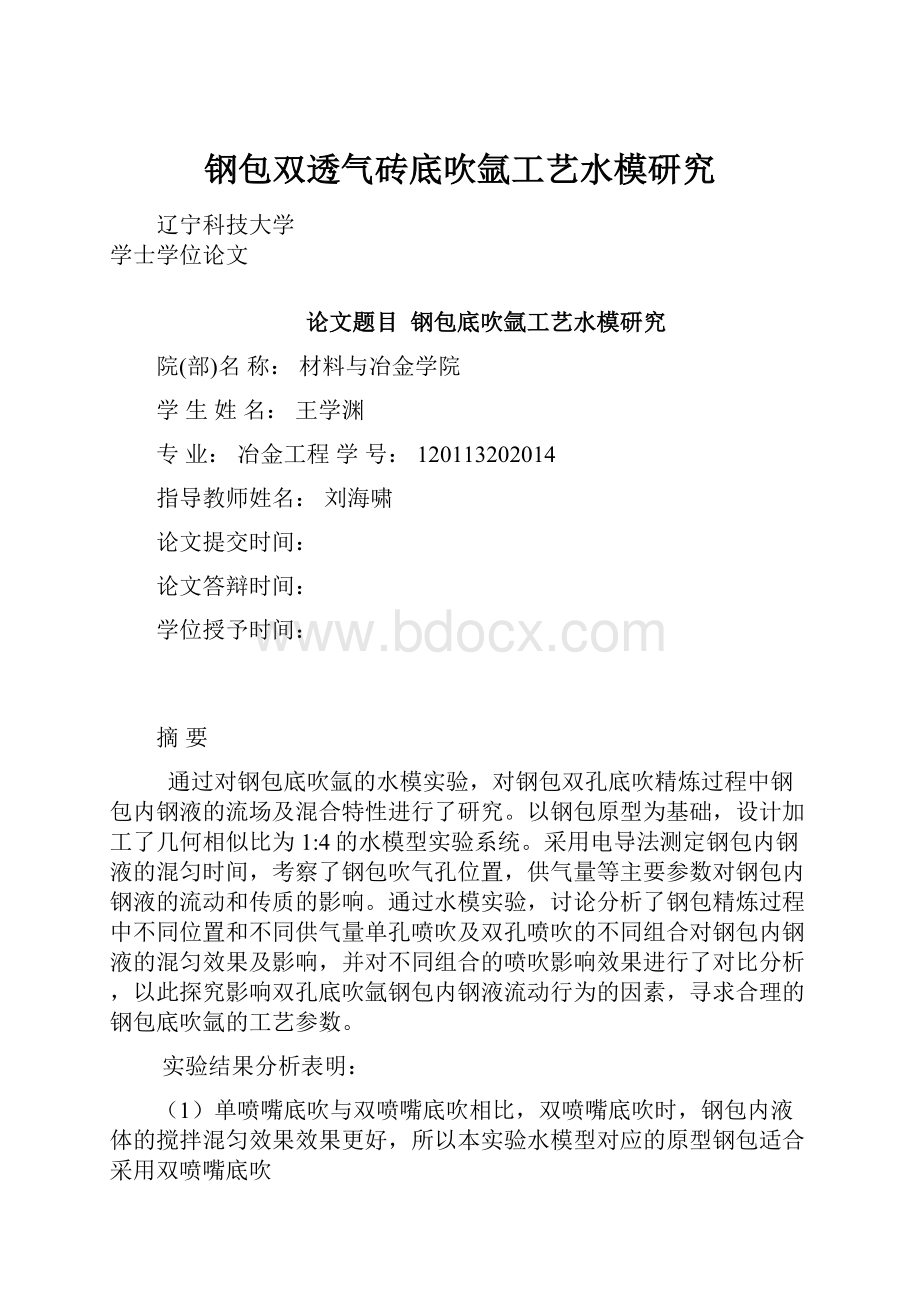
钢包双透气砖底吹氩工艺水模研究
辽宁科技大学
学士学位论文
论文题目钢包底吹氩工艺水模研究
院(部)名称:
材料与冶金学院
学生姓名:
王学渊
专业:
冶金工程学号:
120113202014
指导教师姓名:
刘海啸
论文提交时间:
论文答辩时间:
学位授予时间:
摘要
通过对钢包底吹氩的水模实验,对钢包双孔底吹精炼过程中钢包内钢液的流场及混合特性进行了研究。
以钢包原型为基础,设计加工了几何相似比为1:
4的水模型实验系统。
采用电导法测定钢包内钢液的混匀时间,考察了钢包吹气孔位置,供气量等主要参数对钢包内钢液的流动和传质的影响。
通过水模实验,讨论分析了钢包精炼过程中不同位置和不同供气量单孔喷吹及双孔喷吹的不同组合对钢包内钢液的混匀效果及影响,并对不同组合的喷吹影响效果进行了对比分析,以此探究影响双孔底吹氩钢包内钢液流动行为的因素,寻求合理的钢包底吹氩的工艺参数。
实验结果分析表明:
(1)单喷嘴底吹与双喷嘴底吹相比,双喷嘴底吹时,钢包内液体的搅拌混匀效果效果更好,所以本实验水模型对应的原型钢包适合采用双喷嘴底吹
(2)单喷嘴底吹的最佳位置是距包底中心0.6R处,双喷嘴底吹的最佳位置为距包底中心0.6R,夹角135°。
(3)对于单喷嘴和双喷嘴底吹时,都从在一临界供气量。
钢包底吹超过此临界供气量,混匀时间变化不大,但会造成卷渣等一些问题。
关键词:
钢包吹氩;水模型;混匀时间;双孔底吹
Abstract
Throughwatermodelexperimentofargonblowinginladlebottom,ofladledoublebottomblowingrefiningprocessofmoltensteelinladleandtundishflowfieldandmixingpropertieswerestudied.Basedontheladleprototype,thewatermodelexperimentsystemofthegeometricsimilarityratioof1:
4isdesignedandprocessed.Theeffectofthemainparameterssuchasthegasflowandthemasstransferofthesteelintheladlewasinvestigatedbyusingtheconductancemethod..Throughwatermodelexperiment,discussandanalysistheladlerefiningprocessindifferentpositionanddifferentsupplyquantityofsingleholeblowinganddoubleholeinjectionofdifferentcombinationsinsidetheladleliquidsteelmixedmixingeffectandinfluence,andcombinationofdifferentsprayblowingeffectareanalyzedandcompared,inordertostudytheeffectofthedoublebottomblowingargonladleliquidsteelflowbehaviorfactors,toseekareasonableladlebottomblowingargonprocessparameters.Experimentalresultsshowthat:
(1)singlenozzlebottomblowingandthebottomofthedoublenozzleblowingcomparedtobottomblowingdoublenozzleandladleliquidmixinguniformityeffectbetter,socorrespondingtothewatermodelprototypeladleforthedoublenozzleblowing.
(2)singlenozzleblowingthebestpositioniscenter0.6Rfromthebottomofthebaganddoublenozzleblowingthebestpositionisfromthebottomofthepackagecenter0.6R,theangleof135.
(3)forasinglenozzleandadoublenozzlebottomblowing,bothfromacriticalgassupply.Thebottomblowingofladleismorethanthiscriticalgassupply,butthemixingtimeisnotbig,butitcancausesomeproblemssuchasslag.
Keywords:
Argonblowing;Watermodel;Mixingtime;Doublebottomblowing
目录
第一章绪论1
1.1本课题研究意义1
1.2本课题研究方向、内容和方法1
第二章文献综述3
2.1炉外精炼技术的发展现状3
2.1.1炉外精炼的方式5
2.1.2钢包底吹的主要炉外精炼工艺7
2.2钢包吹氩10
2.2.1钢包吹氩工艺概述11
2.2.2钢包底吹氩的工作原理11
2.3吹氩精炼的影响因素12
2.3.1吹氩量12
2.3.2氩气压力12
2.3.3吹氩时间13
2.4钢包底吹氩钢液流动行为的研究意义和方法13
2.4.1钢包内钢液流动行为的物理模拟13
2.5改善钢包内钢液流动状况的研究15
2.6课题背景及本文的主要工作15
第三章钢包底吹氩喷嘴的合理布置方式的水模研究16
3.1实验原理16
3.1.1几何相似16
3.1.2动力学相似16
3.2实验参数确定17
3.2.1水模型的建立17
3.2.2喷吹气体流量计算17
3.3实验方案设计18
3.3.1工艺参数的影响18
3.3.2实验方案19
3.3.3实验装置及相关设备21
3.3.5实验方法22
第四章实验结果分析23
4.1供气量、吹气位置对单嘴底吹钢液混匀时间的影响23
4.2双喷嘴底吹供气量、吹气位置对混匀时间的影响26
4.3单喷嘴底吹与双喷嘴底吹的对比29
结 论30
参考文献31
致谢33
第一章绪论
1.1本课题研究意义
目前,科技的不断进步和发展引起社会对优质钢的需求量的不断增加,面对用户对钢高度纯净、品种多样的需求,传统的钢铁冶炼技术已不能满足,所以必须探寻更好更便利的冶炼优质纯净钢的技术方法。
高炉炼铁—铁水预处理—转炉炼钢—钢水炉外精炼—连铸;电炉熔炼—钢水炉外精炼—连铸,是现代炼钢的两大主要流程。
钢水炉外精炼是用钢包或者其他容器作为精炼容器,把从初炼炉内出来的钢水在在容器中精炼,精炼的目的为对钢液进行脱碳、脱氧、脱硫、调温、均匀成分、有害气体(N、H)及夹杂物的去除等。
作为上世纪世界炼钢技术的两大革新,氧气转炉炼钢和连续铸钢提高了炼钢生产率。
而钢水炉外精炼技术的出现,一方面衔接炼钢炉和连铸生产,缩短冶炼时间,提高生产率;另一方面可以提高钢的质量和扩大品种,降低生产成本,提高经济效益。
因此,炉外精炼技术是衡量目前钢铁产品质量和钢铁生产流程水平高低的标准。
然而,钢包炉外精炼作为生产优质钢铁的中间环节,必须被得到高度重视。
1.2本课题研究方向、内容和方法
1.2.1研究的方向
为了获得较好的精炼效果,最大限度的净化钢液,许多学者采用水模型实验和数学模型的方法,对如何改善钢包钢液流动特性做出了大量的工作。
综合国内外研究结果可以看到,钢包喷气搅拌操作的关键是在最佳的气流量条件下达到最短的混合时间和最大的外加合金利用率。
当前解决一系列问题的主要措施集中在合理的透气元件布置方式及最佳吹气量的确定两个方面。
面对未来的需求,本次课题选择了钢包炉外精炼为方向,通过相关研究来探寻冶炼优质纯净钢的方法。
本课题在总结前学者大量工作的基础上,以某钢厂70t钢包为原型,对钢包底吹氩精炼中钢包底吹原件的布置及钢包底吹氩精炼过程中的供气量进行实验研究,探究适合原型钢包合理的吹起元件布置方式及合理的供气量。
1.2.2研究的方法
本课题通过物理模拟的研究方法,通过制作与原钢包比例为1:
4的模型,运用相似原理,用水模拟钢液,空气模拟底吹的氩气,设置与钢包精炼过程相似的实验来模拟钢包的炉外精炼。
1.2.3研究的内容
研究的内容有:
(1)在不同的底吹供气量下,单喷嘴底吹时喷嘴布置的位置对钢包内钢液搅拌混匀的影响(体现在混匀时间)。
(2)单喷嘴底吹时,供气量与钢包内钢液混匀所需时间的关系。
(3)在不同的底吹供气量下,双喷嘴底吹时喷嘴布置的位置对钢包内钢液搅拌混匀的影响(体现在混匀时间)。
(4)双喷嘴底吹时,供气量与钢包内钢液混匀所需时间的关系。
(5)双喷嘴底吹时,俩喷嘴间距及与包底中心连线的夹角与钢包内钢液混匀所需时间的关系。
(6)单喷嘴底吹与双喷嘴底吹的最优对比,确定最优方案。
(7)确定本此实验对象合理的供气元件布置方式和供气量,并在此基础上进行联系推广。
第二章文献综述
2.1炉外精炼技术的发展现状
随着科学技术高速发展,各行各业对钢材质量和使用性能都提出了更高的要求。
钢的成分控制范围越来越窄,洁净度要求亦越来越高,即尽可能降低钢中氩氩气体含量、硫磷含量、氧化物含量、非金属及有害微量杂质元素含量等。
此外,为了保证连铸工艺顺行和多炉连浇,降低生成成本和提高劳动率,也要求降低钢中硫、氧含量,均匀钢液成分和温度。
过去,特殊钢的精炼任务主要是在电弧炉内进行,由于渣钢间的接触面积小,反应能热力学和动力学条件差、精炼时间长,导致钢液的吸气及炉衬侵蚀严重。
因此造成一些电炉钢的质量问题不能从根本上得到解决,尤其是出钢过程中钢液的进一步吸气和二次氧化让更降低了钢的纯净度。
所以在浇注前对钢液实行一次炉外精炼是十分必要的。
以上契机促使了炉外精炼技术的发展。
相关功能的精炼方法层出不穷。
去气、脱硫、脱磷、脱氧、微合金化、去除夹杂。
调整钢液温度,均可在精炼炉中完成,使得转炉一炉外精炼工艺冶炼高质量钢种成为可能。
从60年代开始至今,随着连铸技术的发展和大量生产纯净钢生产体制的建立,炉外精炼技术一直保持着恒定的增长势头,一种新技术的出现并得到迅速的发展,必然有其技术和经济上的原因,炉外精炼法作为一项新技术也不例外。
从技术上看主要原因有[1]:
对钢材质量日益苛刻的要求主要表现在纯洁度高,各向异性小合金成份范围窄等方面。
如石油管线用钢(N)0.005%,轴承钢中(O)≤0.001%。
如此低的杂质含量,无论如何仔细的操作,传统炼钢方法产品的杂质含量仍将比上述水平高出几倍,甚至几十倍。
要达到如此高的产品质量必须通过炉外精炼来实现,炉外精炼的冶金效果和材质的关系。
(8)世界炼钢生产中连铸比日益增长,炉外精炼在炼钢炉与连铸之间起衔接与缓冲作用。
特别是连铸对钢水成份、温度和纯净度要求极高。
离开炉外精炼很难满足。
(9)超高功率电弧炉快速发展。
没有炉外精炼,超高功率电弧炉无法发挥优势。
在炉外精炼的配合下,超高功率电弧炉熔炼周期缩短到37-60分钟。
另外从经济方面考虑,炉外精炼的出现提高了初炼炉的生产率,缩短了生产周期,提高了产品质量,降低了产品成本。
目前,炉外精炼作为完整、独立的生产工序与炼钢、连铸有机地结合、成为现代钢铁生产的重要组成部分。
在现代化钢铁生产流程中,炉外精炼的作用主要是[4]见图2.1:
(1)承担初炼炉原有的部分精炼功能,在最佳的热力学和动力学条件下完成部分炼钢反应,提高单体设备的生产能力;
(2)均匀钢水,精确控制钢种成分:
(3)精确控制钢水温度,以适应连铸的生产要求;
(4)进一步提高钢水的纯净度,满足成品钢材性能要求;
(5)作为炼钢与连铸间的缓冲,提高炼钢车间整体效率。
为完成上述精炼任务,一般要求炉外精炼设备具备以下功能:
(1)熔池搅拌功能,均匀钢水成分和温度,促进夹杂物上浮和钢渣反应;
(2)钢水升温和控温功能,精确控制钢水温度;
(3)精炼功能,包括渣洗,脱气,脱碳,脱硫,去除夹杂和夹杂物变性处理等;
(4)合金化功能,对钢水实现窄成分控制;
(5)生产调节功能,均衡炼钢—连铸生产。
图2.1炉外精炼的冶金效果和材质的关系
钢的连铸比及炉外精炼比可以衡量一个国家的炼钢技术的水平。
近年来,我国钢材生产的连铸比增加速度较快,但在钢的炉外精炼比方面,令人担心。
虽然我国早在五十年代,大连、抚顺、太钢即已建成了钢包真空脱气系统,七十年代以后,从欧洲和日本引进了大批炉外精炼设备,并自行设计研制了DH、LF、VD、VOD、AOD、CAS-OB等精炼炉,但直到目前,我国钢的炉外精炼比仍低于50%,而日本转炉钢和电炉钢的炉外精炼比都高达90%以上。
为了使我国由一个钢铁大国变成一个钢铁强国,面对国际市场严峻的竞争挑战,能处于不败之地,大力发展炉外耩炼技术是当务之急。
2.1.1炉外精炼的方式
钢水炉外精炼方式繁多,目前所采用的被接受、应用最普遍的方式归纳起来有搅拌、加热、真空、喷吹、合成渣洗及喂丝等[2]。
(1)搅拌。
搅拌是最基本的精炼手段。
通常是向熔池中提供一定的动能,使得反应器内的金属液进行流动。
金属液通过对流运动可以加速冶金反应、加快反应器内的传热和传质过程,促进夹杂物的聚集、上浮排除,均匀钢液温度和成分。
在钢铁冶炼过程通常采用气体搅拌、电磁搅拌和循环搅拌方式。
气体搅拌是通过一定方式向熔池中吹入氩气对金属液做功而产生对流运动达到搅拌熔池的效果。
它包括顶吹氩和底吹氩,底吹氩是在钢包底部某一位置安装一个喷嘴将氩气吹入钢包内;而用插入钢液中吹氩枪将氩气从钢包上部吹入钢液中是顶吹氩的喷吹方式。
从工艺布置及搅拌效果来看,底吹氩较顶吹氩操作灵活,设备简单,搅拌效果好而被普遍应用。
电磁搅拌是对钢液非接触搅拌,搅拌力是电磁力,熔体不易被污染。
搅拌方向是通过两相电流相位的变化来调整,电磁力是用电流大小的改变来调整。
其优点是搅拌方便充分,热损小,熔体的温度和成分均匀效果好,对于纯净度要求较高的钢种搅拌效果好。
然而,电磁搅拌脱气效果不明显,其设备复杂,对钢包材质、外形及技术等方面要求较高,投资远高于气体搅拌,因此目前电磁搅拌在钢水炉外精炼中应用不普遍,典型的采用电磁搅拌的精炼法为ASEA-SK法。
然而,结晶器在连续铸钢中发挥着重要的作用,铸坯质量的好坏与结晶器有很大的关系,结晶器电磁搅拌是目前连铸的一种重要冶金技术,它能降低钢液的过热度、改善钢液的流动、减轻铸坯中心缩孔和中心偏析、扩大铸坯等轴晶区域等,因此,电磁搅拌应用到连铸领域使得优质铸坯生产率大幅度提高[3]。
循环搅拌:
RH和DH精炼的搅拌方式就是典型的循环搅拌法。
RH精炼中的搅拌是通过真空室抽真空靠压力差使得钢包中的钢液进入真空室内,同时浸渍管上升管中吹入氩气利用气泡泵原理引导真空室内钢液通过下降管流入钢包产生钢液的循环运动。
此搅拌法搅拌强度大,钢水处理量较大,有利于钢水的脱碳、脱氩、脱氧、去夹杂物及均匀钢水成分和温度。
(2)加热。
钢液温度下降是钢液二次精炼过程中不可避免的。
为了保证钢液正常浇铸和避免高温出钢,通常钢液炉外精炼带有加热升温的功能。
目前常用的加热方法有化学加热法和电加热法。
化学加热法是一种直接又操作简单的加热方法,该法的热量来源主要是化学反应产生的热量。
通常采用的方法:
一氧化碳二次燃烧法、Si热法以及Al热法。
通过加入钢包中的发热剂(Al,Si)和CO分别与O₂发生反应放出热量。
利用化学热来加热钢水的优点为:
设备简单、操作灵活、投资低、钢水提高温度的速度快等。
电加热法是利用电能转化为热能的方法以加热钢水。
电弧加热是采用高温电弧使钢液升温。
高温电弧是石墨电极通电后钢液与石墨电极之间产生。
常用的电弧加热精炼炉有电弧加热的真空精炼炉、电弧加热的钢包精炼炉(LF)、真空电弧脱气精炼炉等。
(3)真空。
是目前冶炼纯净度较高的优质钢的精炼手段。
根据化学平衡移动原理,当某气体生成物的分压降低时,则反应向着生成该气体的方向进行。
同样,在钢水炉外精炼过程中,通常有气体产生,为了加强精炼过程,通过抽真空的方式来减小反应器内的压力。
因此,在精炼过程中提高钢水脱碳、脱气和脱氧效果时采用抽真空。
随着真空技术快速发展,发明大型蒸汽喷射泵,相继又研究出各种钢液真空处理方法,如:
VD、VOD、VAD、RH等。
(4)合成渣洗[4]
最简单的精炼手段。
将配置好的满足某种冶金功能的合成炉渣加入钢包,倒入钢包中的钢水通过冲击合成渣,使钢水与渣均混来达到对钢水精炼的目的。
不同钢厂精炼不同钢种所用的合成渣的成分不同,但是基本都属于
渣系。
选择合成渣一般要考虑几点:
具备相应的物化性质是对合成渣的成分要求;合成渣的熔点要低于所渣洗的钢液熔点,即液态渣;合成渣要有良好的流动性来减小乳化渣滴的直径,增加其与钢液的接触面积;合成渣具有还原性,即渣中低
含量。
(5)喂丝和喷吹。
熔体中直接加入精炼剂的精炼方法。
喷吹是先将精炼粉剂用载气流态化后,然后用特殊喷枪将其喷吹到钢液中达到钢液精炼的目的。
对于那些易氧化且比重轻的合金元素直接加入到钢液中会导致合金氧化进入渣中或者熔损,使得这些合金的收得率降低,因此,将这些合金元素放入低碳钢包芯线中用喂丝机加入钢水中的喂丝法解决了很多问题。
喂丝法具有添加合金元素的数量控制准确,合金元素的利用率高,钢液温降小,避免钢液二次氧化,成本低等优点。
喷吹法由于吹入的小粒度的精炼粉剂而增大了与钢液的接触面积,精炼效果显著。
2.1.2钢包底吹的主要炉外精炼工艺
炉外精炼能够提高钢的质量和产量,降低生产成本,改善炼钢劳动条件,已成为现代钢铁冶炼重要工序之一。
目前,国内外大部分钢铁厂采用炉外精炼,炉外精炼比不断提高,炉外精炼比超过百分之九十的国家很多,世界各大钢厂采用钢包底吹搅拌技术比已达到百分之百。
目前为止,存在的炉外精炼装置大约有30多种,国际上广泛应用的有十多种,而且不断地向多功能、高效率、高冶金效果的方向完善和发展,为提供更高质量、更多品种钢提供了良好条件。
图2.2CAS-OB精炼装置示意图
CAS钢包精炼法又称为成分调整密封吹氩法,日本于1975年开发的一种炉外精炼法。
该方法是利用钢包底吹氩吹开钢液面的渣,将浸渍罩插入钢包内,保证罩内钢水在低氧化性气氛下、无渣或者少渣,然后根据所炼钢种的要求将不同合金元素加入罩内,进行合金化。
CAS-OB精炼法是在CAS处理法的基础上,顶部喷吹O₂,同时加入发热剂(FeSi、Al)的一种具有化学加热功能精炼技术。
CAS-OB设备布置如上图2.2所示。
其精炼工艺具有优点:
底吹氩使得夹杂物很好上浮去除,钢水的洁净度有效提高,并且钢水温度和成分较均匀;钢液升温快和准确控制钢水的温度;增加喂丝功能可实现变性处理夹杂物;合金微调使得钢液成分得到准确控制,合金收得率提高;较快的冶炼节奏,与转炉的冶炼与连铸节奏相匹配。
低合金钢、普碳钢及低碳铝镇静钢等是该精炼工艺适合冶炼的钢种[5]。
VAD法,即真空电弧脱气精炼法,可以实现去气(w[H]达0.0001%~0.0002%,w[N]将至0.008%)、脱氧(w[O]可到0.001%)、脱硫(w[S]达0.009%~0.0015%)、脱碳(w[C]达0.005%)、去夹杂、调整成分等许多功能;有效防止炉渣回磷。
它与ASEA-SKF法的区别在于采用底吹氩搅拌,搅拌剧烈,处理时间较ASEA-SKF法短,脱氧彻底[6]。
用于生产轴承钢、不锈钢、合金钢等。
VAD设备布置如图2.3所示。
1-真空室;2-氩气;3-钢包;4-电极;5-合金加料装置;6-抽气系统
图2.3VAD精炼装置示意图
LF法,即电弧加热的钢包吹氩法,于1971年在日本开发并投入使用。
由于LF炉操作灵活、设备简单以及精炼效果好等特点,成为国内外普及程度最高的钢水精炼法。
LF炉的冶金功能:
炉内还原性气氛,进一步脱硫、脱氧、去夹杂物等;底吹氩能均匀钢液成分和温度,加速渣-钢间化学反应,有利于脱S、脱O;高碱度合成渣洗,脱硫效果好;利用石墨电极在常压下插入渣中进行埋弧加热,石墨中的碳能还原渣中的一些合金元素使得合金收得率有所提高,埋弧能减少散热量而提高热效率以及合金微调[6]。
其优点为多功能精炼,易于生产超低S、低O钢;电弧埋弧加热,温度升高快,高热效率,温度易于精确控制;合金化和底吹搅拌,控制成分波动在较小的区域内,产品的性能不产生大的波动;简单的设备,较低的成本。
为了提高脱气率,没有脱气功能的LF炉配合VD炉,形成LF(V)具有脱气功能的精炼炉。
除超低碳、氩钢外,几乎所有的钢种,尤其是合金钢、工具钢、轴承钢等可以采用LF法精炼。
设备布置如图2.4所示。
1-石墨电极;2-合金加料装置;3-底吹孔;4-出钢口
图2.4LF精炼装置示意图
1-惰性气体;2-真空室;3-合金加料装置;4-氧枪装置;
5-测量和取样装置;6-保护装置;7-钢包
图2.5VOD精炼装置示意图
钢的主要精炼法之一。
它是采用真空法,降低系统内CO分压来达到降碳保铬来冶炼不锈钢的目的,通过顶吹氧枪向真空室内钢液吹氧,达到脱碳的目的;同时利用熔池内碳、氧反应的氧化热来加热钢水保证钢液温度的稳定;精炼过程中始终保持底吹氩搅拌,加快钢液的传热和传质,加快反应速率,均匀钢水成分和温度,为连铸提供的合格钢水,保证连铸工序的顺利进行。
VOD设备布置如图2.5所示。
AOD法,即氩氧脱碳法,AOD法是冶炼不锈钢最主要的精炼方法,全球75%的不锈钢都是由AOD法生产的。
它采用稀释法,通过气体喷嘴从炉底侧面向炉内吹入稀释气体(惰性气体Ar、O₂),使炉内碳氧反应生成的CO分压降低,使反应平衡从铬(Cr)的氧化转移到C的氧化,达到降碳保铬的目的。
AOD法的优点:
大量吹入气体,脱碳快,炉内搅拌强度大;对炉料的要求不严格,成本低;生产率高,热效率好;设备简单,投资少;精炼过程容易控制,易于实现自动化。
生产钢种:
不锈钢、耐候钢、耐热钢、高温合金、工具钢、结构钢等。
AOD设备布置如图2.6所示。
1-倾动出钢;2-活动炉壳;3-倾动耳轴套圈;4-气体喷嘴;
图2.6AOD精炼装置示意图
2.2钢包吹氩
二十世纪炼钢技术的不断革新,顶吹转炉炼钢法和连续铸钢法等工艺的广泛应用,使摄炼钢生产率飞速提高。
在炼钢法中,炉外精炼是设置在转炉和连续铸钢