机电一体化实验报告.docx
《机电一体化实验报告.docx》由会员分享,可在线阅读,更多相关《机电一体化实验报告.docx(12页珍藏版)》请在冰豆网上搜索。
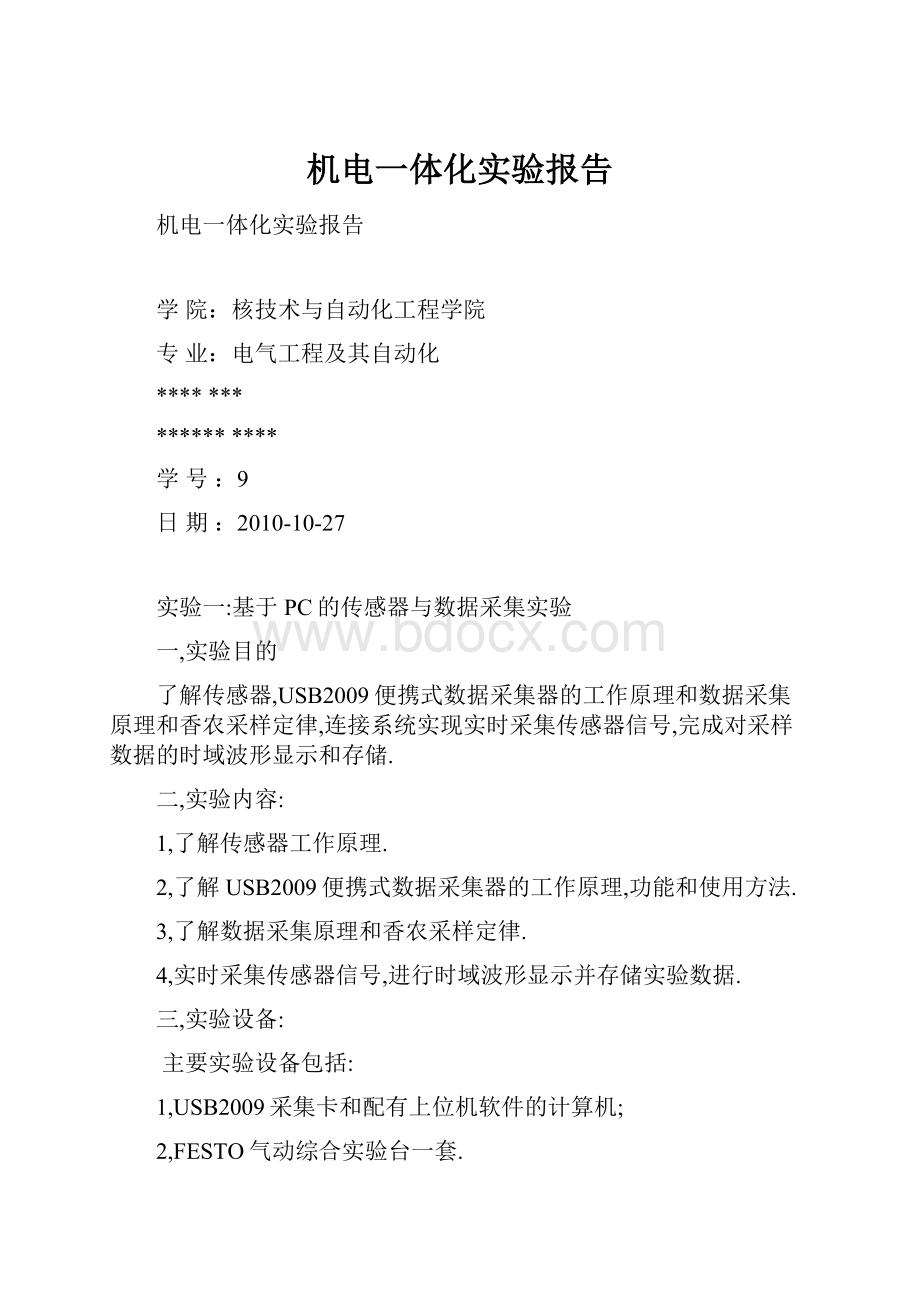
机电一体化实验报告
机电一体化实验报告
学院:
核技术与自动化工程学院
专业:
电气工程及其自动化
*******
**********
学号:
9
日期:
2010-10-27
实验一:
基于PC的传感器与数据采集实验
一,实验目的
了解传感器,USB2009便携式数据采集器的工作原理和数据采集原理和香农采样定律,连接系统实现实时采集传感器信号,完成对采样数据的时域波形显示和存储.
二,实验内容:
1,了解传感器工作原理.
2,了解USB2009便携式数据采集器的工作原理,功能和使用方法.
3,了解数据采集原理和香农采样定律.
4,实时采集传感器信号,进行时域波形显示并存储实验数据.
三,实验设备:
主要实验设备包括:
1,USB2009采集卡和配有上位机软件的计算机;
2,FESTO气动综合实验台一套.
下图为USB2009采集卡.它包含14Bit分辨率A/D转换器,可以提供16路单端模拟信号输入,8路双端模拟输入通道,4路DA输出功能,1组计数器.提供了内外时钟和内外触发工作方式.A/D转换器输入信号范围为:
±5V(USB2009),±10V(AD7899-1).硬增益范围:
1,2,4,8(N6为PGA203时),1,10,100,10000(N6为PGA202时).
图1.1USB2009采集卡
四,实验原理
将USB2009采集卡与FESTO气动综合实验台上传感器连接在一起,而后通过USB连接到计算机上.利用LabVIEW软件搭建数据采集系统,实时采集传感器信号,进行时域波形显示并存储实验数据.
五,实验步骤
1,由实验教师讲解FESTO气动综合实验台上传感器工作原理;
2,由实验教师讲解USB2009采集卡的工作原理和使用方法;
3,由实验教师讲解数据采集原理和香农采样定律;
4,在实验教师的指导下,由学生完成实验电路连接;
5,在实验电路检查无误后,由学生利用LabVIEW软件搭建数据采集系统;
5,打开设备电源,观察数据采集系统运行状况,纠正错误;
6,利用LabVIEW实时采集传感器信号,进行时域波形显示并存储实验数据;
7,将实验过程中形成的正确的接线方式,数据采集系统的搭建方法以及自己在实验中观察到的现象和思考的问题综合起来,写实验报告.
实验二:
交流伺服电机位置闭环控制实验
一,实验目的
了解交流伺服电机和交流伺服驱动器的工作原理,学习PLC的外部接线和编程方法,掌握PLC编程控制交流伺服电机,完成指定的运动轨迹,并通过调整PID控制参数优化控制效果,并计算位置控制精度.
二,实验内容:
1,针对实物,了解交流伺服电机和交流伺服驱动器的工作原理.
2,弄清PLC的外部接线和编程方法.
3,通过PLC编程控制交流伺服电机,完成指定的运动轨迹,掌握伺服电机闭环控制的编程方法
和控制参数调整方法.
三,实验设备:
MPS模块化生产实验系统的加工单元.
四,实验原理
利用MPS模块化生产实验系统加工单元的现有配置,将PLC与交流伺服电机和交流伺服驱动器连接起来,通过PLC编程,实现交流伺服电机运动的PID控制,调整PID控制参数以优化控制效果,掌握闭环控制系统的编程思路和实现方法.
五,实验步骤
1,由实验教师讲解PLC与交流伺服电机和交流伺服驱动器的连接方法以及其它必要的连线及其原因;
2,由实验教师讲解PLC编程的PID控制算法,说明调整PID控制参数的方法和技巧;
3,在实验教师的指导下,由学生完成实验电路连接;
4,在实验电路检查无误后,由学生读懂实验教师提供的PLC梯形图程序,并作适当的修改;
5,下载PLC梯形图程序到PLC,实际控制系统运行.注意,要修改PID控制参数,并观察交流伺服电机的运动状况.多次修改和观察后记录实验数据,并分析这些数据.
6,分析不同的PID控制参数下,交流伺服电机的运动状况不同的原因;
7,将实验过程中形成的正确的接线方式,PLC梯形图以及自己在实验中观察到的现象,数据和思考的问题综合起来,写实验报告.
实验三:
基于变频器的速度闭环控制实验
一,实验目的
了解变频器的工作原理和接口方式,学习PLC的外部接线和编程方法,掌握PLC编程通过变频器控制单相交流异步电动机,实现传送带的速度闭环控制.
二,实验内容:
1,熟悉变频器并了解其工作原理和接口方式.
2,弄清变频器的外部接线和PLC的编程方法.
3,通过PLC编程控制单相交流异步电动机,完成传送带的速度闭环控制.通过调整PID控制参数优化控制效果.
三,实验设备:
MPS模块化生产实验系统的分类单元.
四,实验原理
利用MPS模块化生产实验系统的分类单元的标准配置,将PLC,变频器,单相交流异步电动机连
接起来,通过PLC编程,实现传送带的速度闭环PID控制.通过调整PID控制参数优化控制效果.
五,实验步骤
1,由实验教师讲解PLC,变频器,单相交流异步电动机的连接方法以及其它必要的连线及其原因;
2,由实验教师讲解PLC编程的PID控制程序,说明调整PID控制参数的方法和技巧;
3,在实验教师的指导下,由学生完成实验电路连接;
4,在实验电路检查无误后,由学生读懂实验教师提供的PLC梯形图程序,并作适当的修改;
5,下载PLC梯形图程序到PLC,实际控制系统运行.注意,要修改PID控制参数,并观察交流伺服电机的运动状况.多次修改和观察后记录实验数据,并分析这些数据.
6,分析不同的PID控制参数下,单相交流异步电动机的运动状况不同的原因;
7,将实验过程中形成的正确的接线方式,PLC梯形图以及自己在实验中观察到的现象,数据和思考的问题综合起来,写实验报告.
实验四:
机电一体化综合控制实验
一,实验目的
了解机电一体化系统的组成要素,学习并掌握可编程序控制器在机电一体化系统中的具体应用.
二,实验内容:
1,了解机电一体化系统的组成要素.
2,通过操作模块化生产培训系统,选择模拟工件进行操作,搞清楚各站的电气组成与动作要求,掌握可编程序控制器在机电一体化系统中的具体应用.
三,实验设备:
MPS模块化生产实验系统一套(5站).
四,实验原理
利用MPS模块化生产实验系统的各个单元,将它们连接起来,使之组成一个可以在工作中相互通讯,相互配合的机电一体化系统.各站独立工作,工作中通过各自中间数据相互配合,完成一个模拟工件的进料,加工,入仓的完整过程.
五,实验步骤
1,由实验教师讲解各站的PLC系统;
2,由实验教师讲解各站的连接和配合;
3,由实验教师讲解各站中关键工作部件的工作原理和作用;
4,由实验教师讲解各站的PLC控制程序的工作原理;
5,在实验教师的指导下学生观察实验电路连接;
6,在实验教师的指导下学生观察各站的工作;
7,在实验教师的指导下学生观察各站工作中的配合;
8,由实验教师讲解系统组态的工作原理和使用;
9,在实验教师的指导下学生观察系统组态的设计;
10,由实验教师复位系统,依次启动各站,并讲解这样做的原因;
11,由实验教师启动整个系统,并详细讲解系统的工作;
12,在实验教师的指导下学生观察各站启动时产生的现象;
13,在实验教师的指导下学生观察启动整个系统时产生的现象;
14,在实验教师的指导下学生观察系统工作时系统组态发生的变化;
15,在实验教师的指导下学生重新复位,启动整个系统;
16,学生观察系统工作,记录实验现象和实验中出现的问题;
17,分析实验中产生的实验现象和出现的问题的原因;
18,任选一站,修改该站的PLC梯形图程序,使之动作发生变化,但这种改变不影响系统的整体工作性能;
19,综合考虑实验中各站的工作,考虑一个模拟工件的进料,加工,入仓的完整过程所需要的动作和配合,结合实验现象,实验中产生的问题以及系统修改后的梯形图,写实验报告.
七,系统说明
1,控制面板
各站都可通过一控制面板来控制PLC的控制程序使各站按要求进行工作,一个控制面板上有8个按钮开关,各开关的控制功能定义为:
带灯按钮,绿色开始
带灯按钮,黄色复位
按钮,黄色特殊
两位旋钮,黑色自动/手动
两位旋钮,黑色单站/联网
按钮,红色停止
带灯按钮,红色上电
急停按钮,红色急停
实验一典型机电一体化系统(产品)结构剖析、操作
一、实验要求
巩固和加深对机电一体化技术基本原理的理解;具体了解机电一体化装置的组成及性能特点;
掌握典型机电一体化产品的使用与维护;初步具有机电一体化产品试验研究的能力。
二、实验目的
(1)了解微机数控装置的构成特点及工作原理;
(2)熟悉各构成要素的分布位置与作用;
(3)熟悉各构成要素之间的相互连接;
(4)熟悉数控系统的控制操作。
四、实验教材及参考书
《机电一体化系统设计实验指导书》,西南石油大学
《机电一体化系统设计》,张建民,北京:
高等教育出版社
设备使用说明书
数控机床是典型的机电一体化系统。
PLC工程现场界面涉及光、机、电、气、液等复杂的输入输出信令,加之PLC对于信号的逻辑处理具有的抽象运算特征,使得工业现场故障处理工作通常是相当的复杂困难,PLC机电系统现场故障往往使得缺少工程经验的设备管理者们束手无策,较长时间的故障处理处理可以大幅度降低产能,严重影响生产。
本文以就事论事的方式平铺直叙具体的机电工程现场故障处理案例,保留住故障处理经验中最珍贵的分析判断过程。
2 数控机床故障诊断案例
2.1甄别PLC内外部故障实例
配备820数控系统的某加工中心,产生7035号报警,查阅报警信息为工作台分度盘不回落。
在SINUMERIK
810/820S数控系统中,7字头报警为PLC操作信息或机床厂设定的报警,指示CNC系统外的机床侧状态不正常。
处理方法是,针对故障的信息,调出PLC输入/输出状态与拷贝清单对照。
工作台分度盘的回落是由工作台下面的接近开关SQ25、SQ28来检测的,其中SQ28检测工作台分度盘旋转到位,对应PLC输入接口110.6,SQ25检测工作台分度盘回落到位,对应PLC输入接口110.0。
工作台分度盘的回落是由输出接口Q4.7通过继电器KA32驱动电磁阀YV06动作来完成。
从PLCSTATUS中观察,110.6为“1”,表明工作台分度盘旋转到位,I10.0为“0”,表明工作台分度盘未回落,再观察Q4.7为“0”,KA32继电器不得电,YV06电磁阀不动作,因而工作台分度盘不回落产生报警。
处理方法:
手动YV06电磁阀,观察工作台分度盘是否回落,以区别故障在输出回路还是在PLC内部。
2.2诊断接近开关故障实例
某立式加工中心自动换刀故障。
故障现象:
换刀臂平移到位时,无拔刀动作。
ATC动作的起始状态是:
(1)主轴保持要交换的旧刀具。
(2)换刀臂在B位置。
(3)换刀臂在上部位置。
(4)刀库已将要交换的新刀具定位。
自动换刀的顺序为:
换刀臂左移(B→A)→换刀臂下降(从刀库拔刀)→换刀臂右移(A→B)→换刀臂上升→换刀臂右移(B→C,抓住主轴中刀具)→主轴液压缸下降(松刀)→换刀臂下降(从主轴拔刀)→换刀臂旋转180°(两刀具交换位置)→换刀臂上升(装刀)→主轴液压缸上升(抓刀)→换刀臂左移(C→B)→刀库转动(找出旧刀具位置)→换刀臂左移(B→A,返回旧刀具给刀库)→换刀臂右移(A→B)→刀库转动(找下把刀具)。
换刀臂平移至C位置时,无拔刀动作,分析原因,有几种可能:
(1)SQ2无信号,使松刀电磁阀YV2未激磁,主轴仍处抓刀状态,换刀臂不能下移。
(2)松刀接近开关SQ4无信号,则换刀臂升降电磁阀YV1状态不变,换刀臂不下降。
(3)电磁阀有故障,给予信号也不能动作。
逐步检查,发现SQ4未发信号,进一步对SQ4检查,发现感应间隙过大,导致接近开关无信号输出,产生动作障碍。
2.3诊断压力开关故障实例
配备FANUC0T系统的某数控车床。
故障现象:
当脚踏尾座开关使套筒顶尖顶紧工件时,系统产生报紧。
在系统诊断状态下,调出PLC输入信号,发现脚踏向前开关输入X04.2为“1”,尾座套筒转换开关输入X17.3为“l”,润滑油供给正常使液位开关输入X17.6为“1”。
调出PLC输出信号,当脚踏向前开关时,输出Y49.0为“1”,同时,电磁阀YV4.1也得电,这说明系统PLC输入/输出状态均正常,分析尾座套筒液压系统。
当电磁阀YV4.1通电后,液压油经溢流阀、流量控制阀和单向阀进入尾座套筒液压缸,使其向前顶紧工件。
松开脚踏开关后,电磁换向阀处于中间位置,油路停止供油,由于单向阀的作用,尾座套筒向前时的油压得到保持,该油压使压力继电器常开触点接通,在系统PLC输入信号中X00.2为“l”。
但检查系统PLC输入信号X00.2则为“0”,说明压力继电器有问题,其触点开关损坏。
故障原因:
因压力继电器SP4.1触点开关损坏,油压信号无法接通,从而造成PLC输入信号为“0”,故系统认为尾座套筒未顶紧而产生报警。
解决方法:
更换新的压力继电器,调整触点压力,使其在向前脚踏开关动作后接通并保持到压力取消,故障排除。
2.4诊断中间继电器故障实例
某数控机床出现防护门关不上,自动加工不能进行的故障,而且无故障显示。
该防护门是由气缸来完成开关的,关闭防护门是由PLC输出Q2.0控制电磁阀YV2.0来实现。
检查Q2.0的状态,其状态为“1”,但电磁阀YV2.0却没有得电,由于PLC输出Q2.0是通过中间继电器KA2.0来控制电磁阀YV2.0的,检查发现,中间继电器损坏引起故障,更换继电器,故障被排除。
另外一种简单实用的方法,就是将数控机床的输入/输出状态列表,通过比较通常状态和故障状态,就能迅速诊断出故障的部位。
2.5根据梯形图逻辑诊断DI点故障实例
配备SINUMERIK810数控系统的加工中心,出现分度工作台不分度的故障且无故障报警。
根据工作原理,分度时首先将分度的齿条与齿轮啮合,这个动作是靠液压装置来完成的,由PLC输出Q1.4控制电磁阀YVl4来执行,PLC梯形图如图1所示。
图1 分度工作台PLC梯形图
通过数控系统的DIAGNOSIS能中的“STATUSPLC”软键,实时查看Q1.4的状态,发现其状态为“0”,由PLC梯形图查看F123.0也为“0”,按梯形图逐个检查,发现F105.2为“0”导致F123.0也为“0”,根据梯形图,查看STATUSPLC中的输入信号,发现I10.2为“0”,从而导致F105.2为“0”。
I9.3、I9.4、I10.2和I10.3为四个接近开关的检测信号,以检测齿条和齿轮是否啮合。
分度时,这四个接近开关都应有信号,即I9.3、I9.4、I10.2和I10.3应闭合,现I10.2未闭合,处理方法:
(1)检查机械传动部分。
(2)检查接近开关是否损坏。
2.6根据梯形图逻辑诊断DO点故障实例
配备SINUMERIK810数控系统的双工位、双主轴数控机床。
故障现象:
机床在AUTOMATIC方式下运行,工件在一工位加工完,一工位主轴还没有退到位且旋转工作台正要旋转时,二工位主轴停转,自动循环中断,并出现报警且报警内容表示二工位主轴速度不正常。
两个主轴分别由B1、B2两个传感器来检测转速,通过对主轴传动系统的检查,没发现问题。
用机外编程器观察梯形图的状态。
F112.0为二工位主轴起动标志位,F111.7为二工位主轴起动条件,Q32.0为二工位主轴起动输出,I21.1为二工位主轴刀具卡紧检测输入,F115.1为二工位刀具卡紧标志位。
在编程器上观察梯形图的状态,出现故障时,F112.0和Q32.0状态都为“0”,因此主轴停转,而F112.0为“0”是由于Bl、B2检测主轴速度不正常所致。
动态观察Q32.0的变化,发现故障没有出现时,F112.0和F111.7都闭合,而当出现故障时,F111.7瞬间断开,之后又马上闭合,Q32.0随F111.7瞬间断开其状态变为“0”,在Flll.7闭合的同时,F112.0的状态也变成了“0”,这样Q32.0的状态保持为“0”,主轴停转。
Bl、B2由于Q32.0随F111.7瞬间断开测得速度不正常而使F112.0状态变为“0”。
主轴起动的条件F111.7受多方面因素的制约,从梯形图上观察,发现F111.6的瞬间变“0”引起Flll.7的变化,向下检查梯形图PB8.3,发现刀具卡紧标志F115.1瞬间变“0”,促使Flll.6发生变化,继续跟踪梯形图PB13.7,观察发现,在出故障时,I21.1瞬间断开,使F115.1瞬间变“0”,最后使主轴停转。
I21.1是刀具液压卡紧压力检测开关信号,它的断开指示刀具卡紧力不够。
由此诊断故障的根本原因是刀具液压卡紧力波动,调整液压使之正常,故障排除。
3 结束语
通过典型实例与故障现象对数控系统、立式加工中心自动换刀故障、配备FANUC0T系统的某数控车床、配备SINUMERIK810数控系统的双工位、双主轴数控机床等运行中存在的问题加以分析,并作出相应的故障排除方法。