吊耳冲压模具设计.docx
《吊耳冲压模具设计.docx》由会员分享,可在线阅读,更多相关《吊耳冲压模具设计.docx(51页珍藏版)》请在冰豆网上搜索。
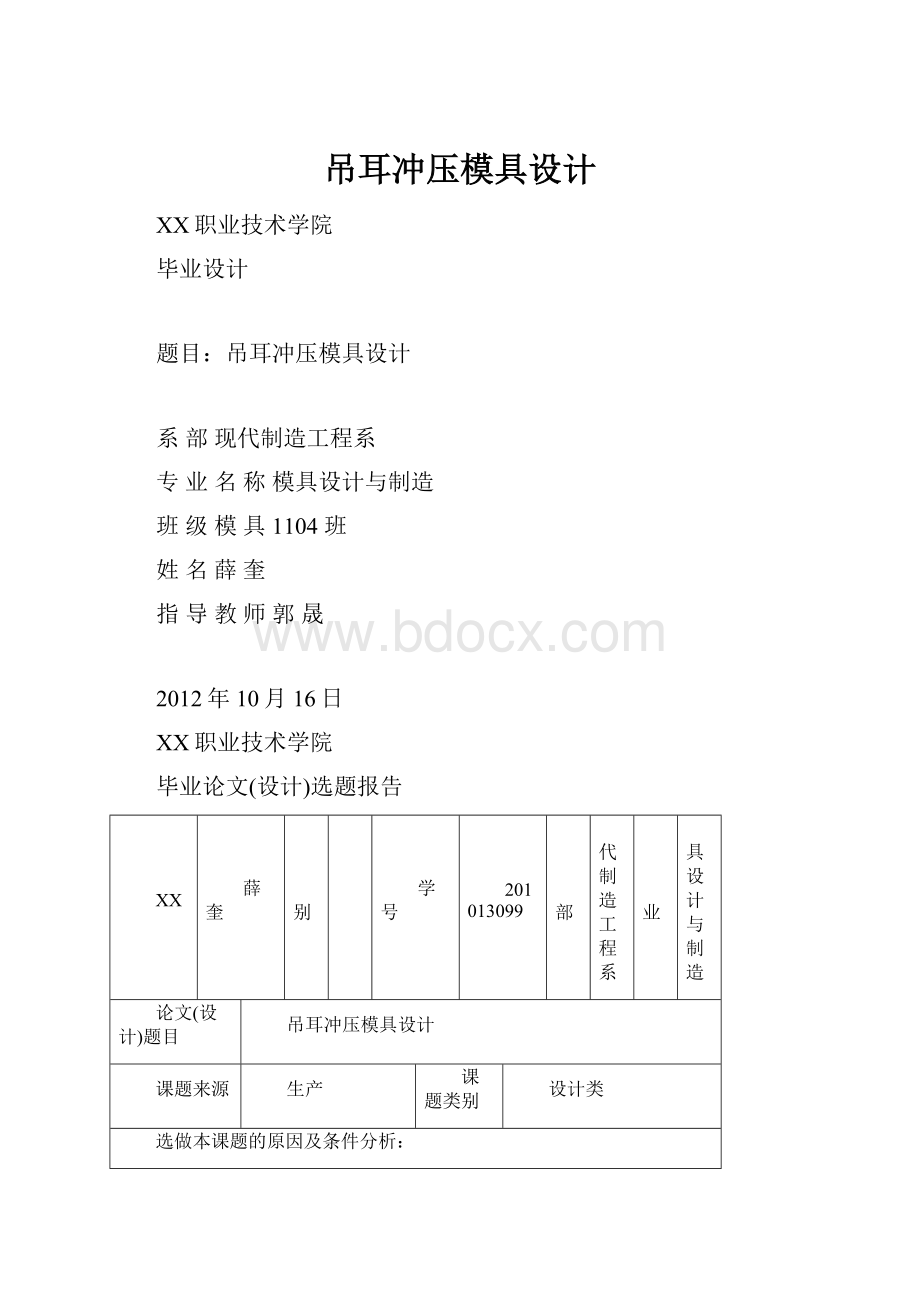
吊耳冲压模具设计
XX职业技术学院
毕业设计
题目:
吊耳冲压模具设计
系部现代制造工程系
专业名称模具设计与制造
班级模具1104班
姓名薛奎
指导教师郭晟
2012年10月16日
XX职业技术学院
毕业论文(设计)选题报告
XX
薛奎
性别
男
学号
201013099
系部
现代制造工程系
专业
模具设计与制造
论文(设计)题目
吊耳冲压模具设计
课题来源
生产
课题类别
设计类
选做本课题的原因及条件分析:
原因:
吊耳模具设计运用到大学几年所学到的相关知识,主要涉及到模具总体设计,主要部件计算,模具总装图,模具辅助零件设计,模具的装配等;通过本次设计能加深并巩固已学的专业知识和技能能提高分析和解决问题的能力;同时也能检验我专业知识和实践能力。
条件:
本人通过这三年的专业学习,具有较扎实的冲压模具知识和技能;能运用AutoCAD、UG等工具进行设计;同时还有模具模型可供我们使用并且有好的网络及图书资源,更有经验丰富的指导老师。
我相信在指导教师的辅导下我一定能顺利完成本课题。
因此,我们申请此课题,望指导老师及系领导批准。
内容和要求
内容:
收集相关资料,对吊耳零件进行分析,确定吊耳冲压模具设计方案;对落料、冲孔成型零件(凸模、凹模)进行结构设计;对落料、冲孔成型零件相关参数进行设计计算;绘制成型零件的零件图和模具辅助零件图;编写设计说明书、绘制模具装配图。
要求:
毕业设计做到结构合理、参数准确、图纸符合国家标准,冷冲压机构设计符合《国家标准GB/2875》规定。
设计做到立论正确,论述充分,结构严谨合理,文字通顺,专业用语准确,书写工整规X
指导教师意见
签名:
年月日
系部毕业论文(设计)领导小组意见:
(签章)
年月日
附表2
XX职业技术学院
毕业论文(设计)指导教师成绩评定表
学生
XX
薛奎
学生
学号
201013099
班级
模具1104
题目
吊耳冲压模具设计
评价内容
具体要求
分值
评分
调查论证
能独立查阅文献和从事其他调研;有收集、加工各种信息及获取新知识的能力。
10
分析及实践能力
理论分析与计算正确,有较强的实际动手能力、分析能力和计算机应用能力。
20
基础理论与专业知识
能运用所学知识和技能去发现与解决实际问题;能对课题进行理论分析,得出有价值的结论。
20
论文(设计)写作质量
立论正确,论述充分,结论严谨合理;分析处理科学;文字通顺,技术用语准确,符号统一,编号齐全,书写工整规X,图表完备、整洁、正确;论文有应用价值、设计结果达到要求。
30
学习态度与
工作质量
按期圆满完成规定的任务,工作量饱满,难度较大;工作努力,遵守纪律;工作作风严谨务实。
10
创新
有创新意识;对前人工作有改进或突破,或有独特见解。
10
总分
指导
教师
评语
是否可以提交答辩
是
否
指导教师签字
年月日
附表3
XX职业技术学院
毕业论文(设计)评阅教师成绩评定表
学生XX
薛奎
学生学号
201013099
班级
模具1104
题目
吊耳冲压模具设计
评价内容
具体要求
分值
评分
文献综述
综述简练完整,有见解;有收集、加工各种信息及获取新知识的能力。
10
论文(设计)
写作质量
立论正确,论述充分,结论严谨合理;实验正确,分析处理科学;文字通顺,技术用语准确,符号统一,编号齐全,书写工整规X,图表完备、整洁、正确;论文结果有应用价值、设计结果达到要求。
70
工作量及
难度
工作量饱满,难度较大。
10
创新
有创新意识;对前人工作有改进或突破,或有独特见解。
10
总分
评阅
教师
评语
是否可以提交答辩
是
否
评阅教师签字
年月日
附表4
XX职业技术学院
毕业论文(设计)答辩记录表
学生XX
薛奎
学生学号
201013099
班级
模具1104
题目
吊耳冲压模具设计
答辩小组成员
姓名
职称
工作单位
备注
曾欣
讲师
XX职业技术学院
唐永艳
副教授
XX职业技术学院
X咸超
助教
XX职业技术学院
董振森
高级技师
XX812厂
X宗义
工程师
普什模具公司
答辩中提出的主要问题及学生回答问题的简要情况:
答辩小组代表签字:
年月日
附表5
XX职业技术学院
毕业论文(设计)答辩成绩评定表
学生XX
薛奎
学生学号
201013099
班级
模具1104
题目
吊耳冲压模具设计
答辩小组
成员
XX
曾欣
唐永艳
X咸超
董振森
X宗义
职称
讲师
副教授
助教
高级技师
工程师
评价内容
具体要求
分值
评分
报告内容
思路清晰;语言表达准确,概念清楚,论点正确;实验方法科学,分析归纳合理;结论严谨;论文(设计)结果有应用价值。
40
答辩
回答问题有理论根据,基本概念清楚。
主要问题回答准确、有深度。
30
创新
对前人工作有改进或突破,或有独特见解。
10
综合素质
能合理运用挂图、幻灯、投影或计算机多媒体等辅助手段,用普通话答辩。
10
报告时间
报告时间控制在要求的时间X围之内。
10
答辩成绩
答辩小组代表签字:
年月日
附表6
XX职业技术学院
毕业论文(设计)综合成绩评定表
学生XX
薛奎
学生学号
201013099
班级
模具1104
题目
吊耳冲压模具设计
成绩
权重
得分
指导教师评定成绩
30%
评阅教师评定成绩
30%
答辩成绩
40%
毕业论文(设计)综合成绩
(百分制)
毕业论文(设计)答辩委员会
审定意见
主任签字
年月日
学院意见
年月日
注:
综合成绩=指导教师评定成绩(×30%)+评阅人评定成绩(×30%)+答辩成绩×40%
吊耳冲压模具设计
摘要
本文针对吊耳零件设计了复合模。
该模具设计的难点主要是如何解决好零件中的孔冲裁、确定模具结构、如何进行模具的制造及冲裁方案选定等。
本文结合吊耳零件的特点,具体解决了压力机的选择与校核、凸模和凹模刃口尺寸计算及结构设计、定位方案设计、卸料方式的设计、主要模具零件的加工工艺、标准零件的选用等一系列的设计工作,这些设计可为类似的零件模具设计提供现实的指导意义。
此次模具设计的突出特点是尝试使用复杂的复合模具,解决常规冲压工艺模具套数多、工艺路线长、生产成本高、效率低等缺点,并为以后此类零件冲压模具设计提供了可靠的依据。
关键词:
复合模;冲裁力;冲裁间隙
1绪论
现代模具行业是技术、资金密集型的行业。
现代模具是高技术背景下的工艺密集型工业,是高技术人才密集型行业。
它作为重要的生产装备行业在为各行各业服务的同时,也直接为高新技术产业服务。
冲模技术的水平直接和生产率、产品质量(尺寸公差和表面粗糙度等)、一次刃磨的寿命以及设计和制造模具的周期紧密相关。
提高冲模技术水平有利于获得优质、高效、低耗、廉价的产品,技术经济效果显著,深受制造行业的重视。
冲压—就是在室温下,利用安装在压力机上的模具对材料施加压力,使其产生分离或塑性变形,从而获得所需零件的一种压力加工方法。
吊耳件运用于较多的机械产品和生活用品中,例如:
桶,卷扬机整体起吊用吊耳。
其上的电机、减速器等的起吊用吊环螺钉。
吊耳常设在机架等处,有铸造、锻造或焊、接铆接等形式,不可拆卸,承载能力大且稳定,常用于设备的整体起吊。
吊环螺钉属于可拆卸形式,常用于独立小部套的起吊。
本次设计零件一般是冲裁件,材料是45钢,厚度是根据受力情况而定,精度等级也根据用途而定,一般为IT12~IT14级,大批量生产本设计注重在模具的设计方案、方法上面。
零件简单,但属于金属加工,有较难的模具加工工艺,所以必须采用复合冲裁或级进模冲裁才能冲出工件。
这样冲出的工件才具有更高的精度,且加工速度也可得以提高。
2冲压件工艺分析
图2-1吊耳零件图
工件名称:
吊耳
生产批量:
大量
材料:
45钢
材料厚度:
2mm
此工件只有落料和冲孔两个工序。
材料为45钢具有良好的冲压性能,适合冲裁。
工件相对简单,有2个Ø4的孔1个Ø8的孔孔与孔,孔与边缘之间的距离也满足要求,因该零件在安装时精度要求较高;所以孔之间的精度为IT12级,其余的为自由公差IT14级尺寸精度较高,该工件所有尺寸为自由尺寸,查表《实用冲压技术手册》P469,附录G冲压基准件标准公差数值表,可得各尺寸公差为:
零件轮廓:
30
、11
、9
、R7
、Ø4
、Ø8
孔心距:
20
、17
断面粗糙度:
Ra6.3。
2.1冲压的工艺方案分析与确定
该工件包括落料,冲孔两个工序,可以有以下三种方案:
方案一:
落料——冲孔,采用单工序模生产。
方案二:
落料——冲孔复合冲压,采用复合模生产。
方案三:
冲孔——落料级进冲压,采用级进模生产。
方案一结构模具简单,但需要两道工序两套模具,成本高而生产效率低,制造容易模具寿命长,难以满足大批量生产要求。
方案二只需一副模具,工件的精度及生产效率都较高工序比较集中,占用设备和人员少,适用于大批量生产,但模具结构复杂,成本高,方案三也只需一副模具,生产率高,操作方便,但模具结构复杂,制造周期长,对零件定位复杂。
倒装的凹模在上,凸模在下,正装的凸模在上,凹模在下;其次是卸料方式的不同,倒装卸料是打杆,正装的是推杆!
该零件精度要求不高正装复合模结构较为简单,成本较低。
综上所述,考虑到该件的批量大,为保证各项技术要求,选用方案二为佳,采用自然落料的倒装式复合模。
2.2定位方式的选择
为保证冲裁出外形完整的合格零件,毛坯在模具中应该有正确的位置,正确位置是依靠定位零件来保证的。
由于毛坯形式和模具结构不同,所以定位零件的种类很多,设计时应根据毛坯形式、模具结构、零件公差大小、生产效率等进行选择。
因为该模具采用的是条料,控制条料的送进方向采用导料销。
因为该零件较小,为倒装复合模,所以控制条料的送进步距采用活动挡料销。
2.3卸料、出件方式的选择
弹压卸料板具有卸料和压料的双重作用,主要用在冲裁料厚在2.5mm以下的板料,由于有压料作用,冲裁件比较平整。
弹压卸料板与弹性元件(弹簧或橡皮)、卸料螺钉组成弹压卸料装置。
卸料板与凸模之间单边间隙选择(0.1~0.2)t,若弹压卸料板还需对凸模起导向作用时,弹性元件的选择,应满足卸料力和冲模结构的要求。
为使卸料可靠,卸料板应高出模具刃口工作面0.3~0.5mm,材料采用45钢,热处理淬火硬度43~48HRC。
因为工件料厚2mm,相对较薄,卸料力不大,由此可知卸料、出件方式的选择可采用弹性卸料装置卸料。
2.4吊耳零件有关工艺与设计
2.4.1排样方式的确定及其计算
方案一:
有废料排样沿冲件外形冲裁,在冲件周边都留有搭边。
冲件尺寸完全由冲模来保证,因此冲件精度高,模具寿命高,但材料利用率低。
方案二:
少废料排样因受剪切条料和定位误差的影响,冲件质量差,模具寿命较方案一低,但材料利用率稍高,冲模结构简单。
方案三:
无废料排样冲件的质量和模具寿命更低一些,但材料利用率最高。
通过上述三种方案的分析比较,综合考虑模具寿命和冲件质量,该冲件的排样方式选择方案一为佳。
考虑模具结构和制造成本有废料排样的具体形式选择直排最佳。
图2-2排样图
排样时零件之间以及零件与条料侧边之间留下的工艺余料,称为搭边。
搭边的作用是补偿定位误差,保持条料有一定的刚度,以保证零件质量和送料方便。
搭边过大,浪费材料。
搭边过小,冲裁时容易翘曲或被拉断,不仅会增大冲件毛刺,有时还有拉入凸、凹模间隙中损坏模具刃口,降低模具寿命。
搭边值通常是由经验值确定,表(2-1)所列搭边值为普通冲裁时经验数据之一。
表2-1搭边a和数a1值
材料厚度
圆形件半径r>2t的工件
矩形工件边长L<50mm
矩形工件边长L>50mm
或r<2t的工件
工件间a1
沿边a
工件间a1
沿边a
工件间a1
沿边a
<0.25
0.25~0.5
0.5~0.8
0.8~1.2
1.2~1.6
1.6~2.0
2.0~2.5
2.5~3.0
1.8
1.2
1.0
0.8
1.0
1.2
1.5
1.8
2.0
1.5
1.2
1.0
1.2
1.5
1.8
2.2
2.2
1.8
1.5
1.2
1.5
1.8
2.0
2.2
2.5
2.0
1.8
1.5
1.8
2.0
2.2
2.5
2.8
2.2
1.8
1.5
1.8
2.0
2.2
2.5
3.0
2.5
2.0
1.8
2.0
2.2
2.5
2.8t
据制件厚度与制件的排样方法可查表(2-1)得工件间为1.8沿边为2。
2.4.2条料宽度的确定
排样方式和搭边值确定以后,条料的宽度与进距就可计算出。
计算条料的宽度时须要考虑三种情况:
(1)有侧压装置时条料的宽度;
(2)无侧压装置时条料的宽度;
(3)有定距侧刃时条料的宽度;
图2-3有侧压装置时条料的宽度确定
图2-4无侧压装置时条料的宽度确定
本设计采用的是无侧压装置的模具。
条料宽度公式:
B=[D+2a+c]
(mm)(2-1)
式中:
c—条料与导料板之间的间隙(即条料的可摆动量):
B≤100,c=0.5~1.0;B>100,c=1.0~1.5查表(2-1);
B—条料宽度基本尺寸;
a—侧面搭边,查表(2-1);
D—条料宽度方向零件轮廓的最大尺寸;
—条料下料剪切公差,
B=(D+2a+c)-△0
B=(30+2×2+1)
=350-0.5(mm)
表2-2剪料公差及条料与导料板之间隙(mm)
条料宽度B/mm
材料厚度t/mm
~1
1~2
2~3
3~5
~50
0.4
0.5
0.7
0.9
50~100
0.5
0.6
0.8
1.0
100~150
0.6
0.7
0.9
1.1
150~220
0.7
0.8
1.0
1.2
表2-3条料宽度偏差(mm)
条料宽度B/mm
材料厚度t/mm
~0.5
>0.5~1
>1~2
~20
0.05
0.08
0.10
>20~30
0.08
0.10
0.15
>30~50
0.10
0.15
0.20
2.4.3确定步距
送料步距S:
条料在模具上每次送进的距离称为送料步距,每个步距可冲一个或多个零件。
进距与排样方式有关,是决定挡料销位置的依据。
条料宽度的确定与模具的结构有关。
进距确定的原则是,最小条料宽度要保证冲裁时工件周边有足够的搭边值;最大条料宽度能在冲裁时顺利的在导料板之间送进条料,并有一定的间隙。
复合模送料步距S=零件的长度+搭边值(2-2)
S=23+2.2
=25.2(mm)
2.4.4材料利用率
材料利用率通常是指在一个进距内的制件实际面积与所用毛坯面积的百分比η:
η=F/F0×100%=F/AB×100%(2-3)
式中:
η材料利用率(%);
F—冲裁件的实际面积(mm2);
F0—所用材料面积,包括工件面积与废料面积;
A—送料进距(相邻两个制件对应点的距离);
B—条料宽度(mm)。
η=F/F0×100%=F/AB×100%
=30×11+14×8+(3.14×7²/2)-(3.14×42+3.14×22×2)/25.2×34×100%
=61%
3模具总体设计
3.1冲压力与压力中心计算
冲裁过程中,冲裁力是随凸模进入凹模材料的深度而变化的。
通常说的冲裁力是指冲裁力的最大值,它是选用压力机和设计模具重要依据之一。
表3-1部分常用冲压材料的力学性能
材料名称
牌号
材料状态
抗剪强度
抗拉强度
伸长率
屈服强度
普通碳素钢
Q195
未退火
260~320
320~400
28~33
200
Q235
未退火
310~380
380~470
21~25
240
Q275
未退火
400~500
500~620
15~19
280
优质碳素结构钢
08F
已退火
220~310
280~390
32
180
08
已退火
260~360
330~450
32
200
10
已退火
260~340
300~440
29
210
20
已退火
280~400
360~410
25
250
45
已退火
440~560
550~700
16
360
65Mn
已退火
600
750
12
400
3.1.1冲压力计算
计算冲裁力是为了选择合适的压力机,设计模具和检验模具的强度,压力机的吨位必须大于所计算的冲裁力,以适宜冲裁的要求,普通平刃冲裁模,其冲裁力Fp一般可以按下式计算:
Fp=KptLτ(3-1)
式中:
τ—材料抗剪强度,;
L—冲裁周边总长(mm);
t—材料厚度(mm);
系数Kp是考虑到冲裁模刃口的磨损,凸模与凹模间隙之波动(数值的变化或分布不均),润滑情况,材料力学性能与厚度公差的变化等因数而设置的安全系数Kp,一般取1~3。
当查不到抗剪强度r时,可以用抗拉强度σb代替τ,而取Kp=1的近似计算法计算。
根据公式3-1可得出详见表(表3-3)。
抗剪强度
按退火45钢板计算,查表(《实用冲压技术手册》P329,表8-49黑色金属的机械性能),得45钢退火τ=440~560;取τ=500MPa。
表3-2卸料力、推件力和顶件力系数
料厚t/mm
Kx
Kt
Kd
钢
≤0.1
>0.1~0.5
>0.5~0.25
>2.5~6.5
>6.5
0.065~0.075
0.045~0.055
0.04~0.05
0.03~0.04
0.02~0.03
0.1
0.063
0.055
0.045
0.025
0.14
0.08
0.06
0.05
0.03
铝、铝合金
纯铜,黄铜
0.025~0.08
0.02~0.06
0.03~0.07
0.03~0.09
对于表中的数据,厚的材料取小直,薄材料取大值。
表3-3冲压力
项目分类
项目
公式
结果
备注
冲压力
落料力F落
F落=1.3ltτ
137800N
τ=500MPa
L=106mm
冲孔力F冲
F冲=1.3ltτ
65312N
L=50.24mm
卸料力F卸
F卸=K卸F冲
3265.6N
查表5得K卸=0.05
推件力F推
F推=nK推F落
9646N
n=h/t=12/2=6
K推=0.07
总冲压力F总
F总=F落+F冲+F卸+F推
216023.6N
3.1.2压力中心计算
模具压力中心是指冲压时诸冲压力合力的作用点位置。
为了确保压力机和模具正常工作,应使模具的压力中心与压力机滑块的中心相重合,否则,会使冲模和力机滑块产生偏心载荷,使滑块和导轨之间产生过大的摩擦,模具导向零件加速磨损,降低模具和压力机的使用寿命。
冲模的压力中心,可以按下述原则来确定:
(1)对称形状的单个冲裁件,冲模的压力中心就是冲裁件的几何中心。
(2)工件形状相同且分布位置对称时,冲模的压力中心与零件的对称中心相重合。
(3)形状复杂的零件、多孔冲模、级进模的压力中心可以用解析计算法求出冲模压力中心。
解析法的计算依据是:
各分力对某坐标轴的力矩之代数和等于诸力的合力对该轴的力矩。
求出合力作用点的坐标位置0,0(x=0,y=0),即为所求模具的压力中心如图(图3-1),根据公式:
(3-2)
(3-3)
先求合力,即使有力矩也要转化成单一的力矢量;然后选取任意点作转动中心根据力矩平衡原理求作用点的坐标。
最后从作用点出发画出合力交与物体表面得到的交点即压力中心。
得出表(表3-4),最后画出压力中心图如图(图3-1)。
表3-4压力中心计算
基本要素长度L/mm
各基本要素压力中心的坐标值
X
Y
L1=30
0
0
L2=11
15
5.5
L3=8
11
11
L4=8
7
15
L5=21.98
0
19
L6=8
-7
15
L7=8
-11
11
L8=11
-15
5.5
L9=25.12
0
19
L10=12.56
-10
5.5
L11=12.56
10
5.5
合计156.12
0
10.1
图3-1压力中心
由以上计算结果可以看出该工件的压力中心在(0,10.1)这一点。
3.1.3冲裁模间隙的确定
冲裁间隙时指冲裁模中凹模刃口横向尺寸DA与凸模刃口横向尺寸dr的差值(如图3-2),是设计模具的重要工艺参数。
图3-2冲裁间隙
(1)间隙对冲裁件尺寸精度的影响
冲裁件的尺寸精度是指冲裁件的实际尺寸与基本尺寸的差值,差值越小,则精度越高,这个差值包括两方面的偏差,一是冲裁件相对于凸模或凹模的偏差,二是模具本身的制造偏差。
(2)间隙对模具寿命的影响
间隙是也许模具寿命诸因数中最主要的因数之一,冲裁过程中,凸模与被冲的孔之间,凹模与落料件之间均有摩擦,而且间隙越小,模具作用的压应力越大,摩擦也越严重,所以过小的间隙对模具寿命极为不利。
设计模具时一定要选择合理的间隙,以保证冲裁件的断面质量、尺寸精度满足产品的要求,所需冲裁力小、模具寿命高,但分别从质量,冲裁力、模具寿命等方面的要求确定的合理间隙并不是同一个数值,只是彼此接近。
考虑到制造中的偏差及使用中的磨损、生产中通常只选择一个适当的X围作为合理间隙,只要间隙在这个X围内,就可以冲出良好的制件,这个X围的最小值称为最小合理间隙Zmin,最大值称为最大合理间隙Zmax。
考虑到模具在使用过程中的磨损使间隙增大,故设计与制造新模具时要采用最小合理间隙值Zmin。
根据始用间隙表(3-5)查得材料45号钢的最小双面间隙Zmin=0.260mm,最大双面间隙Zmax=0.380mm
表3-5冲裁模初始用间隙2c(mm)
材料
厚度
08、10、35、
09Mn、Q235
16Mn
45、50
65Mn
2Cmin
2Cmax
2Cmin
2Cmax
2Cmin
2Cmax
2Cmin
2Cmax
小于0.5
极小间隙
0.5
0.6
0.7
0.8
0.9
1.0
1.2
1.5