激光再制造现场粉末输送系统的研究状况综述.docx
《激光再制造现场粉末输送系统的研究状况综述.docx》由会员分享,可在线阅读,更多相关《激光再制造现场粉末输送系统的研究状况综述.docx(13页珍藏版)》请在冰豆网上搜索。
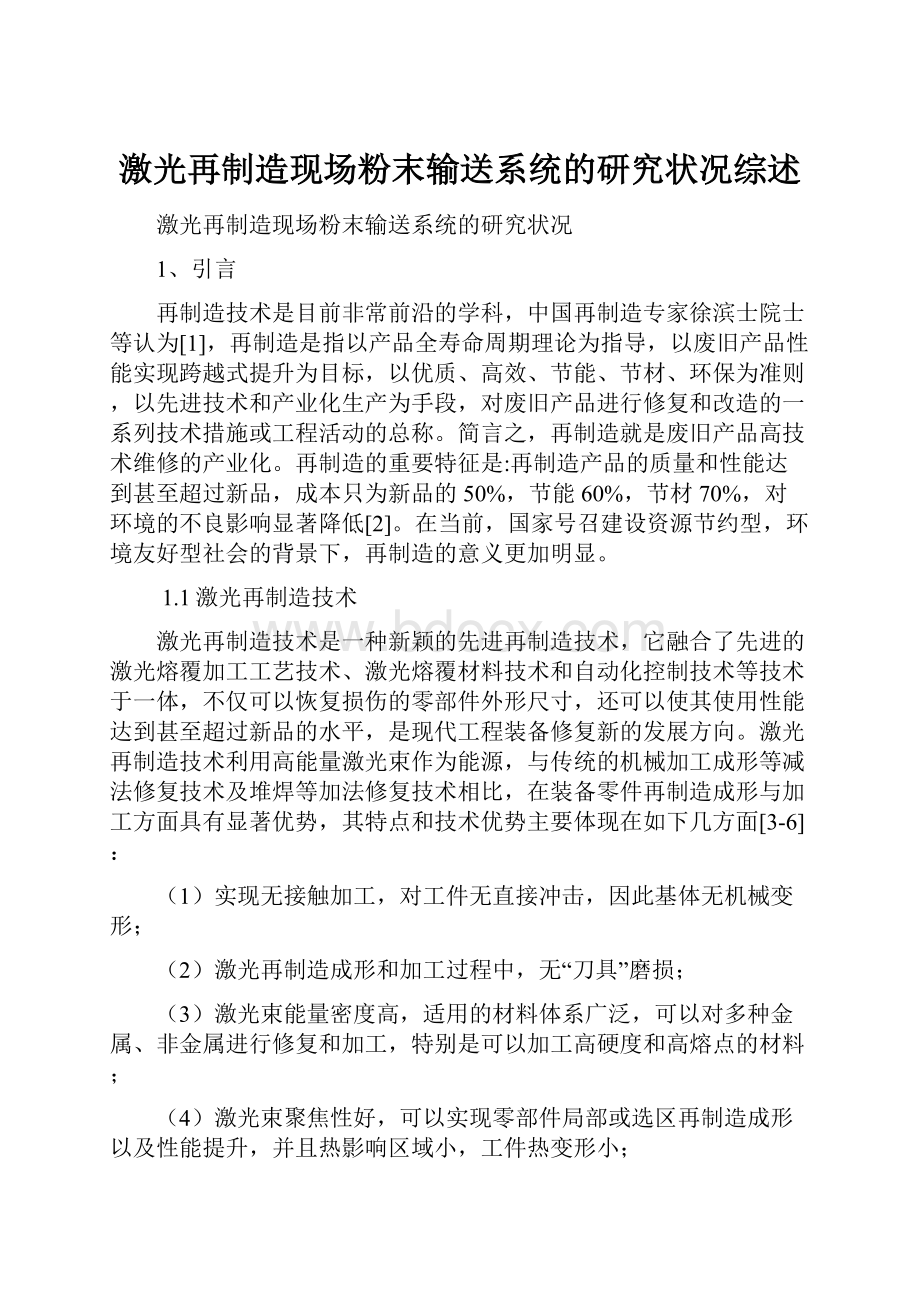
激光再制造现场粉末输送系统的研究状况综述
激光再制造现场粉末输送系统的研究状况
1、引言
再制造技术是目前非常前沿的学科,中国再制造专家徐滨士院士等认为[1],再制造是指以产品全寿命周期理论为指导,以废旧产品性能实现跨越式提升为目标,以优质、高效、节能、节材、环保为准则,以先进技术和产业化生产为手段,对废旧产品进行修复和改造的一系列技术措施或工程活动的总称。
简言之,再制造就是废旧产品高技术维修的产业化。
再制造的重要特征是:
再制造产品的质量和性能达到甚至超过新品,成本只为新品的50%,节能60%,节材70%,对环境的不良影响显著降低[2]。
在当前,国家号召建设资源节约型,环境友好型社会的背景下,再制造的意义更加明显。
1.1激光再制造技术
激光再制造技术是一种新颖的先进再制造技术,它融合了先进的激光熔覆加工工艺技术、激光熔覆材料技术和自动化控制技术等技术于一体,不仅可以恢复损伤的零部件外形尺寸,还可以使其使用性能达到甚至超过新品的水平,是现代工程装备修复新的发展方向。
激光再制造技术利用高能量激光束作为能源,与传统的机械加工成形等减法修复技术及堆焊等加法修复技术相比,在装备零件再制造成形与加工方面具有显著优势,其特点和技术优势主要体现在如下几方面[3-6]:
(1)实现无接触加工,对工件无直接冲击,因此基体无机械变形;
(2)激光再制造成形和加工过程中,无“刀具”磨损;
(3)激光束能量密度高,适用的材料体系广泛,可以对多种金属、非金属进行修复和加工,特别是可以加工高硬度和高熔点的材料;
(4)激光束聚焦性好,可以实现零部件局部或选区再制造成形以及性能提升,并且热影响区域小,工件热变形小;
(5)易于实现多种激光技术手段的复合应用,根据零件形状和性能特点实现激光复合再制造;
(6)可以实现缺损零件选定区域的“近净成形”再制造,后续加工余量小;
(7)激光束易于导向、聚焦、实现方向变换,易与数控系统和工业机器人配合,对复杂工件进行再制造和加工,因此,其工艺柔性好,是极为灵活的加工和修复方法;
(8)是绿色环保型的先进技术,再制造产品质量稳定、性能可靠,经济效益和社会效益好。
鉴于激光再制造技术显著的技术优势和特点,近年来,激光再制造技术方面的研究不断深入,应用领域不断扩大。
在国外,英国P.R航空发动机公司已将它用于涡轮发动机叶片的修复[7],美国海军实验室用于修复舰船螺旋桨叶[8],美国和日本在汽缸、活塞等汽车发动机零件上也有很多应用[9]。
在我国,以沈阳大陆激光技术有限公司作为龙头企业的一批激光再制造专业化公司不断涌现,有许多激光再制造技术成功应用的实例,如:
石化行业的烟气轮机、风机和电机;电力行业的汽轮机和电机;冶金行业的热卷板连轧线、棒材连轧线、高速线材连轧线;铁路行业的货车车轮、道岔、铁路机车曲轴;航空发动机热端部件和大型船舶内燃发动机热端部件等等。
1.2激光再制造系统
先进的激光再制造技术需要先进的设备系统作为支撑。
激光再制造系统主要设备一般包含激光器、送粉系统、运动执行机构(例如数控系统、工装卡具工作台等),还可配备成形过程监测和控制系统等[10],如图1.1所示。
它的基本原理就是通过激光发出平行激光束,然后通过反射或者折射进行聚焦,根据实际情况,选择合理的工艺参数,将激光作用在材料上,完成材料在基体表面的熔覆,实现再制造过程。
1.1激光再制造系统示意图
送粉系统作为激光再制造设备系统的重要组成部分,送料装置、送料方法及其控制技术成为激光再制造过程中关键及核心的技术,也是目前激光再制造研究的重点方向之一。
激光再制造过程中,对送料装置性能要求是能够提供高度连续、均匀、稳定、可控的送料速度,将材料准确地送达熔池,形成高质量熔覆轨迹,并很好地适应扫描方向的变化。
送料装置的性能直接影响零件的成形质量,是系统中极为重要的一部分。
目前用于熔覆的金属形状既有粉末,又有丝状或带状,相应的送料方式称为送粉法和送丝法[11]。
送粉法的主要优点在于材料来源广、易于合金化、易于加工、成形精度高,但也存在着粉末利用率低、生产效率低及粉尘对工作环境有污染的问题。
如何保证几何成形精度情况下实现粉末材料利用率高且提高生产效率,成为本领域研究热点与难点之一。
2激光再制造粉末输送装置的研究
在激光熔覆、再制造过程中,根据材料的供应方式不同分为两大类[12]:
预置法和同步送粉法。
同步送粉法具有工艺过程简单,合金材料利用率高,可控性好,容易实现自动化,使其成为激光熔覆技术的首选方法,国内外实际生产中采用较多。
激光再制造同步送粉装置主要由送粉器和喷嘴组成。
送粉器的主要作用是将粉斗中的粉末变成均匀连续的粉流;喷嘴是将送粉器输送的粉流转变为不同的形状并送入熔池。
在激光同步送粉熔覆工艺中,加工质量主要依赖的参数有[13]:
加工速度、粉末单位时间输送率、激光功率密度分布、光斑直径、粉末的输送速度、稳定性以及粉末束质量等;其中粉末单位时间输送率和粉末的输送速度,稳定性是由送粉器的输送特性决定的,粉末束的输出质量由送粉喷嘴决定。
所以对送粉装置的研究对提高激光熔覆、再制造加工质量具有重要意义。
2.2送粉器的种类及发展
送粉器是激光熔覆技术中的核心元件之一,它按照加工工艺,向激光熔池输送设定好的粉末。
送粉器性能的好坏,直接影响熔覆层的质量和加工零件尺寸等。
所以开发高性能的送粉器,对激光熔覆加工、激光再制造显得尤为重要。
随着激光熔覆、再制造技术的快速发展,以及对熔覆层的加工精度和质量要求的提高,国内外相继研发了基于不同原理的送粉器[14]。
根据工作原理的不同,可以分为:
基于气体动力学的送粉原理,如刮吸式送粉器:
基于机械力学的送粉原理,如螺旋式送粉器:
基于超声振动的送粉原理,如毛细管式送粉器:
基于电磁振动力学的送粉原理,如磁珠激励振动式送粉器:
基于转动碎团的送粉原理,如研磨转针式送粉器;基于转动研磨的送粉原理,如转动刷式送粉器;基于流化床原理,如沸腾式送粉器等。
沸腾式送粉器的工作原理是:
沸腾进气l与沸腾进气2将粉末流化或者使粉末达到临界流化状态,而粉末输送管中间有一孔洞与送粉器内腔相通,当粉末流化或处于临界流化状态时,送粉进气通过粉末输送管,便可将粉末连续地输送出。
其中,为使粉末能够顺利通过小孔洞进入粉末输送管中,腔内的沸腾气压应大于送粉进气的气压。
对于沸腾式送粉器,使气体与粉末混合均匀,不易发生堵塞;调节气体流量的大小便可以实现对粉末输送速率的调节,可靠方便;而且不像刮吸式与螺旋式等机械式送粉器,粉末输送过程中与送粉器内部发生机械挤压和摩擦容易发生粉末堵塞现象,造成送粉量的不稳定;而对于不同的粉末或者是合金粉末,沸腾式送粉器也可以进行输送,对粉末的粒度和形状有较宽的适用范围。
沸腾式送粉器,是基于气固两相流原理设计的,工作时,载流气体在气体流化区域直接将粉末吹出送至激光熔池。
但是,同样要求所送粉末干燥;沸腾式送粉器对于粉末的流化和吹送都是通过气体来完成的,需要单独的供气装置。
(5)其他类型送粉器
华中科技大学邹海平等人为了满足功能梯度材料零件快速成形和制备的需要,开发了高精度数字化功能梯度送粉系统[19]。
该系统采用同步送粉带结构、优化的落粉调节装置和全程封闭负压式载气系统,实现了实时精确配比的多粉末梯度变比例送粉,送粉单元的原理图如图2.6所示。
图2.6送粉单元原理图
该送粉单元采用同步送粉带结构,包括储粉桶、振动装置、落粉调节装置、同步送粉带及送粉气体加速装置、送粉电机及其控制装置等。
在送粉过程中,粉末在振动装置和重力的作用下由储粉桶中落到同步送粉带上,振动装置用于增强超精细粉末的输送能力。
落粉调节装置用于消除落粉管下端的导粉槽与同步送粉带的间隙,使落粉量只由导粉槽口半径尺寸决定,保证了落粉量的准确性。
同步送粉带将落入的粉末连续地送入出粉通道,最终粉末由经过加速的送粉气体从出粉口送出,送粉气体能够增长粉末的输送距离,减少送粉管道布置的影响。
整个送粉器采用封闭式载气系统,,工作时送粉腔内充满平衡气体,全部通道由氩气保护,以避免粉末氧化。
该送粉系统在常速和低速送粉率下,具有送粉量精度高、线性度好、送粉稳定和均匀等特点,送粉误差小于1.5%,送粉重复误差在1%以下,最小送粉速率为0.005g/s,能顺畅输送纳米陶瓷粉末。
北京工业大学武强等设计了一种送粉量可连续变化的四路联动系统[20],可实现多粉末送粉量实时变化控制,来满足成分及性能连续变化功能梯度材料(以及功能零件)激光成形制造工艺的需要。
该送粉系统的送粉装置采用负压吸附正压输送混合气力输送方式的工作原理,如图2.7所示。
图2.7粉末输送原理图
该送粉过程主要包括粉末铺展与输送、送粉气体的输入与输出、送粉气体输送金属粉末3个部分。
其中,送粉气体通过进气部件进入到粉末输送装置内的密封腔内,经过出粉部件与粉末输出部件之间的缝隙后,通过粉末输出部件流出。
由于送粉气体的流动,在粉末输出部件通道末端和出粉部件之间形成一个负压区,粉末输出部件末端的通道相当于负压气力输送系统的吸嘴,而出粉部件孔道则相当于负压气力输送系统的料斗,出粉部件孔道内的金属粉末在送粉气体负压吸附的作用下,被吸入到粉末输出部件的通道内,此过程为负压输送过程;在粉末输出部件通道内形成的粉气两相流则是在密封腔内正压送粉气的作用下,沿着送粉管路输送至送粉喷嘴,此过程为正压输送过程。
在送粉过程中,送粉块和出粉块同粉末承载盘之间发生摩擦运动,所以三者之间的配合间隙及相关尺寸直接影响粉末输送精度和稳定性。
2.3现有送粉装置的不足及未来发展
在实际应用加工中,不同的送粉器表现出各自的优缺点。
随着激光技术的发展,经过多种尝试,国内外已经研制出很多类型的送粉器。
一般情况下,较大尺寸的粉末(颗粒直径>100μm)流动性较好,易于传送,而颗粒直径较小的粉末(颗粒直径(1μm)容易聚团和粘滞,流动性较差,通常传送这样尺寸的粉末是非常困难的[21],所以,在同步送粉器中,流动性差是超细粉末输送的难点,由于细粉末的聚团和粘滞,而导致送粉不连续和送粉量不均匀,得到的熔覆层厚度不均匀、表面质量差、严重精密熔覆和微成型的质量。
比如对于纳米相粉这类超细粉末在输送中容易发生团聚,目前的送粉器还没有得到很好的解决。
所以,对于超细粉末的输送和实现微量输送将是以后送粉器研究的重点。
并且对于送粉器综合化的研究,将更有利于实现激光熔覆加工成套设备的集成化和一体化。
随着激光熔覆、再制造技术的快速发展,送粉器作为核心元件之一,得到了广泛的研究和不断发展。
目前,国内外对送粉器的研制目标是将送粉器工作时的连续性、均匀性、稳定性和可控性提高到一个更科学,更先进的水平。
对国内外文献资料的整理和分析可以看出送粉器发展的特点:
(1)多功能化。
现有的送粉器基本都能够对单一的粉末进行连续送粉,以后送粉器的发展向着混合送粉、多方式送粉和高精度方向发展,目前已先后研制出多料仓混合的送粉器,熔覆材料组成及配比连续可调的送粉器以及高度集成带有信息反馈附件的送粉器等。
(2)微量化。
现有的送粉器都是连续送粉,送粉量都比较大,仅适合大面积熔覆应用和三维快速制造。
目前的激光熔覆技术已经开始应用于精密熔覆和微成形,在这种加工过程中,需要对激光熔覆加工区域进行微量输送,这对送粉器的性能要求很高。
当进行零件的激光熔覆精密修复时,大送粉量的送粉器根本无法满足工作的要求。
(3)超细化。
现在的送粉器能够对较大尺寸粉末,进行连续稳定的送粉,因为其流动性好,易于传输。
然而,对于尺寸在毫米级以下的微细熔覆粉末,现有送粉器的输送粉末颗粒比较大,特别是对于有些工件表面的缺陷特别微小(如小的磨损坑、裂痕、小孔洞和腐蚀坑等)无法满足加工的要求。
(4)小型化、模块化。
激光再制造过程中,许多重大设备不方便拆装,或需要及时抢修,就需要进行现场修复,即进行现场激光再制造,所以要求激光现场再制造系统要方便灵活,粉末输送系统作为激光再制造系统的重要组成部分,实现送粉器小型化、模块化设计将是重要趋势。
(5)集成化。
现有的送粉器大多都是独立的系统体系,其控制单元是专门的独立单元,与上位机的通讯缺失,与激光再制造其它系统集成度差。
随着技术的发展,未来送粉器的控制系统自身优化提升的同时,必将会实现与激光再制造其它系统的集成化与融合,从而实现整个激光再制造系统的集成化,使激光再制造过程更加自动化与智能化。
3、送粉控制策略的研究
3.1早期的控制策略
对于较早前的以电机为驱动元件的送粉器,采用的是直流电机简单的通过旋转电位器调整给定电压,实现电机的转速控制[22],这种控制方法太简单,控制精度不高,送粉量的重复性不好。
随着步进电机的发展,送粉器驱动器件逐渐由步进电机取代。
步进电机是一种将电脉冲信号转换成角位移的运动部件[23],它能直接接受数字信号(电脉冲)并方便地转换为与之严格对应的角位移。
在控制中它的转速只与脉冲串的给定频率有关,不受系统电压、电流以及环境温度变化的影响,而且在一个运行周期中它可以自动消除位置积累误差使之为零。
因而即使用它进行开环位置控制时,也具有较高的位置精度。
以前的步进电机控制系统由步进控制器、功率放大器和步进电机组成,这种步进控制器线路复杂,而且成本高,使用因此受到了限制。
3.2现代控制技术
随着单片微机的发展,对步进电机的控制变得简单方便了。
目前的单片机的系统结构简单,集成度高,可靠性高,处理功能强,有丰富的外围接口芯片,可方便地构成功能强、成本低的步进电机控制器,它不仅简化了线路,降了成本,而且提高了可靠性。
以单片微机作为送粉器的控制器,不仅控制精度高,送粉速率的重复性好,而且能与激光熔覆加工的其它成套设备连为一体,便于实现激光加工控制自动化。
采用单片机系统对步进电机进行控制,有串行控制和并行控制两种方法[24-25]。
这两种方法的一个重要区别是驱动电源中是否含有环形分配器,在串行控制中,单片机只输出脉冲信号、方向信号和方式信号,环形分配器功能在驱动电源中实现,串行控制示意图如图3.1所示。
图3.1串行控制系统结构示意图
在并行控制中,是由单片机的几个I/O端口直接接在驱动器的相应的各相上,其环分功能一般是由计算机编程(即按照步进电机的控制方式给出相应的控制模型直接进行相序的分配)或者是由软硬件相结合的方法来实现。
并行控制示意图如图3.2所示
图3.2并行控制系统结构示意图
3.4粉末流的监测技术研究
现阶段,对激光熔覆再制造过程中的粉末输送技术的研究大多关注送粉器、电机驱动等设计和研究[30-33],上述文献中所采用的送粉装置对粉末输送量的调节主要采用对计量容积(凹槽容积、螺纹沟槽容积)和电机速度的调节来实现,依靠输料装置的稳定运转来实现粉末输送的稳定性。
但实际的粉末输送过程中,一方面,由于气压波动、粉末团聚等原因,粉末的输送量未必与电机转速具有确定的对应关系。
另一方面,即使送粉器输出口的粉末输出量稳定,经过管道中的输送,粉料到达输送管道出口处的输送量未必能够准确、稳定。
这是因为粉末在管道中的流动状态实际上很复杂,与气流速度、气流中所含的粉末量、粉末本身料性等相关[34-37]。
粉末在管道中的输送状态可能是依靠高速流的气流动压被输送的悬浮流,也可能是依靠气流的静压推送的栓流,或者是介于两种气流状态之间的输送方式。
粉末在管道中的传送可能是时而停滞时而吹走交替进行的状态,因此,送粉器输出粉末的准确性不能保证通过管道输送后管道出口处粉末输出的稳定。
因此,通过检测装置检测粉末在送粉管里的流量,进而实现粉末的闭环控制对提高表面熔覆质量具有重要意义。
长春理工大学薛菲在基于载气式送粉器的基础上,针对熔覆所需粉末流量的要求,设计了一种通过流量计检测来反馈粉末流量的闭环控制系统[38],即粉末经出粉口出来后,会流经一个流量计。
该控制系统总体有以下几个环节组成,如图3.5所示。
图3.5送粉器控制系统的元器件组成框图
其中,控制部分和被控部分(送粉器)组成了整个闭环系统,控制部分主要是处理指令信号和反馈信号,并对被控部分发出控制信号,而被控部分则是接收控制信号,发出反馈信号,从而实现精确控制送粉器按指定要求的流量输送粉末。
釆用流量检测反馈的闭环控制系统,可以利用输入信息与反馈至输入处的信息两者之间的偏差对送粉器的粉末输出进行控制,使送粉器按所需流量的大小来完成送粉工作。
流量计检测的反馈能够缩小输入信息与反馈信息之间的偏差,从而得到希望的送粉量,实现送粉器定量送粉。
整个送粉器控制系统的目的就是想要控制粉末流量,因此监测流量的多少是否合理是整个控制系统的关键。
当流量监测装置将测到粉末流量反馈回单片机时,流量值会和设定好的值比较。
为了让激光束与经过同轴送粉头的粉末进行较好的耦合输出,同轴送粉工作头不但具有高汇聚性能,还应使输出的粉末流具有良好的粉末形貌,所以对进入熔池前的粉末形貌及相应的性能参数具有一定的观察及测量手段,为此,天津工业大学王非等开发了一款粉末流场实时在线检测系统[39]。
该检测系统检测金属粉末流场主要依据DPIV数字图像检测原理[40]:
如图3.6所示。
图3.6DPIV检测系统原理图
其原理是,由能在空间形成二维光平面的高亮度半导体线光源激光器发出的激光照亮由同轴送粉嘴输出的金属粉末流,在粉末流被照亮的同时,由高速跨帧CMOS相机拍得位于光源平面内被照亮的金属粉末流层的照片,拍得的照片经过数字图像处理卡经由USB数据传输线输入到计算机,再由自己编制的专用粉末流场检测软件进行实时处理和计算并显示相应结果。
该系统由硬件装置及软件系统两部分组成,DPIV检测系统所包含的硬件装置为:
能在空间形成二维光平面的高亮度半导体线光源激光发射器、高速跨帧CMOS相机、计算机系统以及实现产品化时所需要的相应的安装结构等。
软件为在LabVIEW平台下开发出能准确检测出同轴送粉粉末流场实时形貌特征参数及送粉速率的粉末流场实时检测系统专用软件。
该检测系统具备能实时显示同轴送粉粉末流场具体形貌及精确检测相应的粉末流重要参数如焦点直径、焦距及送粉量等;完成了熔覆粉末材料输送及测控系统的整体集成,可实现对激光熔覆粉末的远程同轴输送及实时检测控制的较好结合,从而进一步提高了同轴送粉激光熔覆的加工效率及加工质量。
针对激光熔覆制造过程中粉末输送不均匀的现象,浙江工业大学激光加工技术中心胡晓冬、姚建华、陈智君、张毅等人提出了一种基于光电传感器的粉末流量检测与控制方法[41]。
该技术的关键在于在分析粉末流对光线的吸收特性的基础上,设计了一种新型的光电式粉末流量传感器,该传感器采用红色发光二极管作为光源,二极管所发出的光线经粉末流散射后照射到光电变送器上,通过信号调理可以将传感器输出电压信号与粉末流量相对应。
其原理如图3.7所示。
图3.7光电式气固两相流粉末浓度测量原理图
对该传感器进行测试,试验数据表明:
粉末流量与传感器输出信号具有较好的线性相关度。
为实现粉末流量控制,基于模糊PID控制策略,开发了一套采用PIC单片机作为控制元件的粉末流控制器,对辊轮式送粉器的粉末传输进行流量控制,粉末流量稳定性提高60%以上。
3.5送粉控制技术未来展望
粉末输送控制系统经历了早期的开环控制,简单闭环控制,到现在利用各种传感器测量方法以及更先进的控制算法来实现良好的闭环反馈控制粉末流量,送粉的稳定性和准确性有了较大的提高。
但是,目前送粉稳定性还是主要是依靠通过各种手段增加输料装置的稳定运转来实现粉末输送的稳定性,通过对粉末流量的在线检测与实时反馈控制的方法还在探索阶段,问题在于激光熔覆、再制造过程的粉末流属于气固两相流,而气固两相流动的复杂使得检测技术存在着不少困难,目前还没有哪个理论模型能完整的阐述其流动的规律特性,因此实验成为研究其规律的主要手段之一。
由于人们对气固两相流物理特性的认识仍有局限性,迄今为止仍没有一种较为理想的气固两相流动的测量仪器,虽然在这一方面诸多学者有了一些研究,形成了以DPIV数字图像检测,压电原理、电容式、光电式原理等的粉末流传感器测量技术,但是,在反馈与控制的准确性、稳定性和快速性上有待提高。
所以,
未来控制技术提高粉末输送装置的稳定性的同时,发展更加先进的粉末流传感检测理论与手段,更好的检测粉末输送量,才能更加精确的控制送粉,从而使再制造成形质量达到更高水平。
4、总结
随着国内外学者不断对激光再制造送粉系统的研究,送粉器的类型不断丰富,送粉的稳定性得到较大提升,其发展方向正朝着多功能、微量化、超细化、小型模块化、集成化的方向发展。
送粉喷嘴随着计算流体CFD数值模拟的发展,其结构设计水平提高,粉末的输出质量有了较大提升。
在粉末输送系统的控制方面,已经实现了较好的闭环控制,但是在粉末流测量上还存在短板,随着传感技术的发展,送粉的精确度将进一步提升,激光再制造的水平也会上个新台阶