曲轴的机加工艺和夹具设计.docx
《曲轴的机加工艺和夹具设计.docx》由会员分享,可在线阅读,更多相关《曲轴的机加工艺和夹具设计.docx(51页珍藏版)》请在冰豆网上搜索。
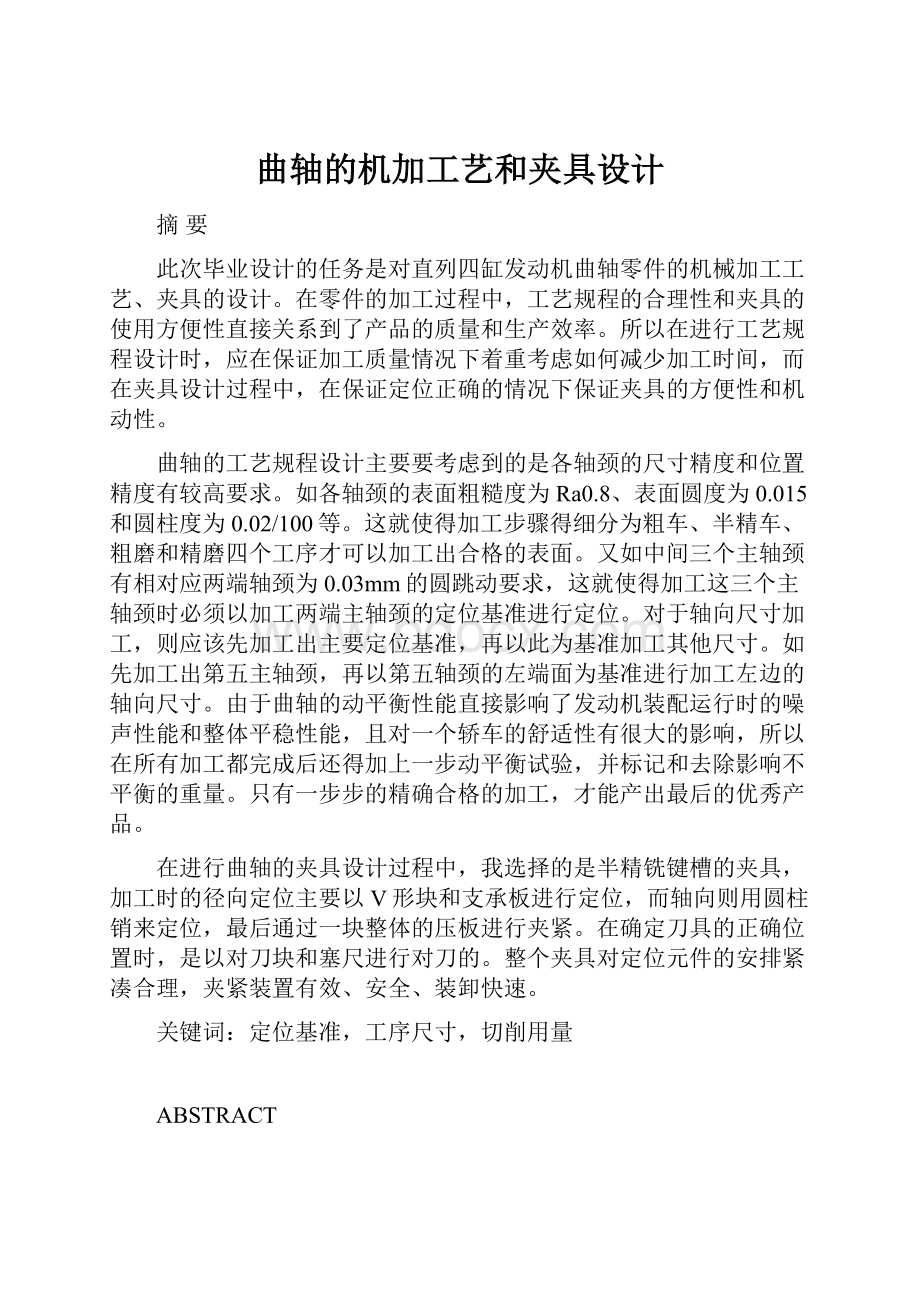
曲轴的机加工艺和夹具设计
摘要
此次毕业设计的任务是对直列四缸发动机曲轴零件的机械加工工艺、夹具的设计。
在零件的加工过程中,工艺规程的合理性和夹具的使用方便性直接关系到了产品的质量和生产效率。
所以在进行工艺规程设计时,应在保证加工质量情况下着重考虑如何减少加工时间,而在夹具设计过程中,在保证定位正确的情况下保证夹具的方便性和机动性。
曲轴的工艺规程设计主要要考虑到的是各轴颈的尺寸精度和位置精度有较高要求。
如各轴颈的表面粗糙度为Ra0.8、表面圆度为0.015和圆柱度为0.02/100等。
这就使得加工步骤得细分为粗车、半精车、粗磨和精磨四个工序才可以加工出合格的表面。
又如中间三个主轴颈有相对应两端轴颈为0.03mm的圆跳动要求,这就使得加工这三个主轴颈时必须以加工两端主轴颈的定位基准进行定位。
对于轴向尺寸加工,则应该先加工出主要定位基准,再以此为基准加工其他尺寸。
如先加工出第五主轴颈,再以第五轴颈的左端面为基准进行加工左边的轴向尺寸。
由于曲轴的动平衡性能直接影响了发动机装配运行时的噪声性能和整体平稳性能,且对一个轿车的舒适性有很大的影响,所以在所有加工都完成后还得加上一步动平衡试验,并标记和去除影响不平衡的重量。
只有一步步的精确合格的加工,才能产出最后的优秀产品。
在进行曲轴的夹具设计过程中,我选择的是半精铣键槽的夹具,加工时的径向定位主要以V形块和支承板进行定位,而轴向则用圆柱销来定位,最后通过一块整体的压板进行夹紧。
在确定刀具的正确位置时,是以对刀块和塞尺进行对刀的。
整个夹具对定位元件的安排紧凑合理,夹紧装置有效、安全、装卸快速。
关键词:
定位基准,工序尺寸,切削用量
ABSTRACT
Thistackofthegraduateddesignistodesignthemachiningprocessandthefixtureofinlinefour-cylinderenginecrankshaff.Duringtheprocessofpart,,thetechnologicalprocedurerationalityandfixtureseaseofusi-ngisdirectlyrelatedtoproductqualityandproductionefficiency.Soduringprocessplanning,wehavetocon-siderhowtoreduceprocessingtimewhenthequalityisundercontrolling.Whenthefixtureisincorrectposit-ion,mustensuretheconvenienceandfiexibilityofthefixtureinthefixturedesignprocess.
DuringtheprocessplanningofCrankshaft,wetakeintoaccounttherequirementsofahigherdimensionalaccuracyandpositionalaccuracyofthejournal,suchasthesurfaceroughnessofeachjournalforRa0.8mm,surfaceroundness0.015mmandcylindricity0.02/100,etc.Forprocessedsurfaceofqualified,theprocessingstepshavetobebrokendownforroughing,semi-finishturning,roughgrindingandfinegrindingfourprocess-es.Anotherexampleisthemiddlethethreemainjournalscorrespondingtobothendsofthejournalsrequirem-entsfor0.03mmofroundbeating.Whichmakestheprocessingofthethreemainjournals,mustbeprocesssedatbothendsofthespindlesnecklocatingdatumforpositioning.Fortheaxialdimensionprocessed,shouldbeprocessedmainlylocalizedbasis,andthenasabenchmarkprocessotherdimensions.Forexample,weprocessthefifthspindleneckfist,thenprocesstheleftoftheaxialdimensionasabenchmarkwiththeleftsideofthefifthjournal.Asthecrankshaftbalancingperformancedirectlyaffectsthenoiseperformanceoftheengineass-emblyoperationandtheoverallsmoothperformance,andhasagreatinfluencetothecomfortofasedan.Somustbeabalancingtestafterallprocessingiscompletedandremovetheweightoftheimpactoftheimbalan-ce.Onlyastep-by-stepprocessingoftheexactqualifiedcanoutputthefinaloutstandingproducts.
Duringthefixturedesignprocessofthecrankshaft,Ichoseasemi-finemillingkeywayfixture.TheradialpositioninglocateswithaV-shapedblockandbearingplateswhenprocessing.Theaxiallocateswithacylind-erical.Finally,clampwithawholeplate.Determiningthecorrectpositionofthetoolisbasedontheknifeblo-ckandfeeler.Theentirefixtureiscompactandreasonablearrangementofthepositioningelements,clampingdeviceiseffective,safe,fastloadingandunloading.
Keywords:
TheLocatingDatum,ProcessDimension,CuttingAmuout
第一章绪论1
第二章零件分析2
2.1零件的作用2
2.2零件的工艺分析2
第三章工艺规程设计3
3.1确定毛坯的制造形式3
3.2基面的选择3
3.3工艺路线的拟定3
3.3.1两个工艺方案的比较与分析6
3.4机械加工余量、工序尺寸及毛坯尺寸的确定6
3.5确定切削用量10
第四章专用夹具设计36
4.1铣床夹具设计36
4.1.1定位基准的选择36
4.1.2铣削力与夹紧力计算37
4.1.3夹紧元件及动力装置确定37
4.1.4夹具精度分析37
4.1.5定位元件的设计38
4.1.6对刀块和塞尺设计39
第五章结束语………………………………………………………...40
致谢
参考文献
附录
第一章绪论
夹具结构设计在加深我们对课程基本理论的理解和加强对解决工程实际问题能力的培养方面发挥着及其重要的作用。
选择曲轴的夹具设计能很好的综合考查我们大学四年来所学的知识。
本次所选设计内容主要包括:
对零件的结构及尺寸和位置精度的分析,工艺路线的确定,定位基准的选择,切削用量的确定,夹具的设计,各种图纸的绘制和设计说明书的编写等。
机械加工工艺是规定产品或零件机械加工工艺过程和操作方法,是指导生产的重要的技术性文件。
它直接关系到产品的质量、生产率及其加工产品的经济效益,生产规模的大小、工艺水平的高低以及解决各种工艺问题的方法和手段都要通过机械加工工艺来体现。
因此,工艺规程编制的好坏是成产该产品的质量的重要保证和重要依据。
利用更好的夹具可以保证加工质量,机床夹具的首要任务是保证加工精度,特别是保证被加工工件是加工面与定位面以及被加工表面相互之间的位置精度,提高生产率,降低成本,使用夹具后可以减少划线、找正等辅助时间,且易于实现多工位加工,扩大机床工艺范围,减轻工人劳动强度,保证生产安全。
为了让夹具有更好的发展,夹具行业应加强产、学、研协作的力度。
加快用高新技术改造和提升夹具技术水平的步法,创建夹具专业技术网站,充分利用现代信息和网络技术,与时俱进地创新和发展夹具技术。
第二章零件分析
2.1零件的作用
题目所给定的零件是直列四缸发动机曲轴,它是发动机的核心零件之一,其功用是承受连杆传来的力,并由此造成绕其本身轴线的力矩,并对外输出转矩。
在发动机工作中,曲轴受到旋转质量的离心力、周期性变化的气体压力和往复惯性力的共同作用,使曲轴承受弯曲与扭转载荷。
2.2零件的工艺分析
由直列四缸发动机曲轴零件图可知,其形状不规则,尺寸精度、形位精度要求均较高,现对零件的主要技术要求分析如下:
(1)各主轴颈和连杆轴颈的表面粗糙度要求都为Ra0.8,且为滑动的配合面,对表面精度要求较高,需经过粗车、半精车、粗磨和精磨来达到要求。
而大小头的圆柱表面粗糙度为Ra1.6,用粗车—半精车—精车即可达到要求。
(2)四个连杆轴颈都有圆度为0.015mm、圆柱度为0.02/100mm的要求。
四个连杆轴颈对Ⅰ、Ⅴ主轴颈的公共轴线B-D有平行度为0.02/100mm的要求。
第Ⅱ、Ⅲ、Ⅳ连杆颈对第Ⅰ、Ⅴ主轴颈的公共轴线和第Ⅰ连杆轴颈轴线的公共平面C有位置度为1mm的要求。
第Ⅱ连杆颈对第Ⅲ连杆颈有同轴度为Ø1mm的要求。
第Ⅳ连杆颈对第Ⅰ连杆颈有同轴度为Ø1mm的要求。
(3)四个连杆轴颈都有圆度为0.015mm、圆柱度为0.02/100mm的要求。
第Ⅱ、Ⅲ、Ⅳ主轴颈对Ⅰ、Ⅴ主轴颈的公共轴线B-D有圆跳动为0.03mm的要求。
(4)大端Ø16.5的螺栓孔轴线对大端外圆的轴线M和Ø16的螺栓孔轴线N有位置度为Ø0.1mm的要求。
直径为Ø16的螺栓孔对大端外圆的轴线M有位置度为0.05mm的要求。
(5)大端大头孔中的Ø62员有径向圆跳动为0.05mm的要求。
大端外圆Ø160有径向圆跳动为0.04mm的要求。
大头Ø85轴段有径向圆跳动为0.04mm的要求。
大端面有平面度为0.05(-)/25的要求,且其对Ⅰ、Ⅴ主轴颈的公共轴线B-D有端面圆跳动为0.04mm的要求。
(6)小头处,键槽对Ø45的轴线基准G有对称度为0.1mm的要求。
Ø45轴线对Ⅰ、Ⅴ主轴颈的公共轴线B-D有圆跳动为0.003mm的要求。
Ø38轴线对Ⅰ、Ⅴ主轴颈的公共轴线B-D有圆跳动为0.08mm的要求。
(7)各轴颈和曲柄的距离不是很大,只有0.8mm的距离,在加工时应注意。
第三章工艺规程设计
3.1确定毛坯的制造形式
直列四缸曲轴零件材料为球墨铸铁,牌号为QT700-02,硬度为231304HB,生产类型为大批量生产,采用砂型机器造型的毛坯铸件。
3.2基准面的选择
基准面选择是工艺规程设计中的重要工作之一,基准面选择的正确与合理,可以使加工质量得到保证,生产率得以提高,不盲目的选择基准面。
否则,加工工艺过程中会问题百出,更有甚者,还会造成零件的大批报废,使生产无法正常进行。
(1)粗基准的选择按照粗基准的选择原则,为保证不加工表面和加工表面的位置要求,应选择不加工表面为粗基准,所以选择毛坯的Ⅰ、Ⅴ主轴颈为粗基准,加工两端的中心孔。
而加工连杆轴颈的粗基准则是以半精加工后的主轴颈和定位面作为粗基准。
(2)精基准的选择在两端中心孔加工完以后,粗车和半精车的工序均以两端中心孔做基准。
而加工连杆轴颈的精基准则是以精磨加工后的主轴颈和定位面作为粗基准。
3.3工艺路线的拟定
为保证达到零件的几何形状、尺寸精度、位置精度及各项技术要求,必须制定合理的工艺路线。
由生产纲领为成批生产,所以采用通用机床和部分专用机床,并配以专用的工、夹、量具,并考虑工序集中,以提高生产率和减少机床数量,使生产成本下降。
工艺路线方案
(一):
工序00按零件毛坯尺寸铸造出合格毛坯。
工序05正火处理。
工序10粗车两端面和大端外圆。
工序15半精车大端面和大端外圆,钻两端中心孔。
工序20粗车第三主轴颈和两侧面及圆角。
工序25半精车第三主轴颈和两侧面及圆角。
工序30粗车剩余4个主轴颈及大小头和他们的侧面和圆角。
工序35半精车4个主轴颈及大小头并倒角。
工序40在曲柄上铣出定位面。
工序45粗车4个连杆轴颈及其侧面和圆角。
工序50半精车4个连杆轴颈及其侧面和圆角。
工序55中间检查,检查各轴颈尺寸是否合格。
工序60调质处理。
工序65精车大端面及大端外圆。
工序70钻、扩、铰大头孔并钻大头中心孔。
工序75钻小头直径Ø14.5深60的孔,钻中心孔,攻M16×.5-6H螺纹。
工序80精车大头和小头。
工序85粗磨各主轴颈及其侧面和圆角。
工序90粗磨各连杆轴颈及其侧面和圆角。
工序95精磨各主轴颈及其侧面和圆角。
工序100精磨各连杆轴颈及其侧面和圆角。
工序105中间检查,检查各轴颈尺寸。
工序110粗铣键槽。
工序115半精铣键槽
工序120钻Ø8各轴颈油孔并锪孔。
工序125钻四个直径为Ø8的连杆轴颈的斜油孔。
工序130钻Ø16、Ø16.5孔,扩Ø16孔。
工序135进行动平衡试验,标记不平衡处。
工序140去除不平衡标记处重量。
工序145清洗零件上的油污。
工序150终检,进行表面粗糙度、尺寸精度和相互位置精度的测量。
工艺路线方案
(二):
工序00按零件毛坯尺寸铸造出合格毛坯。
工序05正火处理。
工序10粗车两端面和大端外圆。
工序15半精车大端面和大端外圆,钻两端中心孔。
工序20粗车第三主轴颈和两侧面及圆角。
工序25半精车第三主轴颈和两侧面及圆角。
工序30粗车剩余4个主轴颈及大小头和他们的侧面和圆角。
工序35半精车4个主轴颈及大小头并倒角。
工序40在曲柄上铣出定位面。
工序45粗车4个连杆轴颈及其侧面和圆角。
工序50半精车4个连杆轴颈及其侧面和圆角。
工序55中间检查,检查各轴颈尺寸是否合格。
工序60调质处理。
工序65精车大端面及大端外圆。
工序70精车大头和小头。
工序75粗磨各主轴颈及其侧面和圆角。
工序80粗磨各连杆轴颈及其侧面和圆角。
工序85精磨各主轴颈及其侧面和圆角。
工序90精磨各连杆轴颈及其侧面和圆角。
工序95中间检查,检查各轴颈尺寸。
工序100粗铣键槽。
工序105半精铣键槽。
工序110钻、扩、铰大头孔并钻大头中心孔。
工序115钻小头直径Ø14.5深60的孔,钻中心孔,攻M16×.5-6H螺纹。
工序120钻Ø8各轴颈油孔并锪孔。
工序125钻四个直径为Ø8的连杆轴颈的斜油孔。
工序130钻Ø16、Ø16.5孔,扩Ø16孔。
工序135进行动平衡试验,标记不平衡处。
工序140去除不平衡标记处重量。
工序145清洗零件上的油污。
工序150终检,进行表面粗糙度、尺寸精度和相互位置精度的测量。
3.3.1两个工艺方案的比较与分析
经过对两个工艺方案的对比,可知两个工艺方案就是在钻大头孔及中心孔和钻小头孔、中心孔及螺纹这两道工序的安排顺序不同,方案一是将两工序安排在了粗、精磨主轴颈的前面,而方案二是将其安排在了后面。
就方案一来说,其粗、精磨主轴颈的定位中心孔是以两端主轴颈定位加工过的,其精度要比最初以毛坯面的两端主轴颈定位加工的中心孔的精度更好。
所以选取方案一,可以更好的保证零件的加工精度。
根据方案一的工序安排,编出机械加工工艺过程卡及工序卡片。
见附表13:
机械加工工艺过程卡片;附表436:
机械加工工序卡片。
3.4机械加工余量、工序尺寸及毛坯尺寸的确定
直列四缸曲轴零件材料为球墨铸铁,牌号为QT700-02,硬度为231304HB,生产类型为大批量生产,采用砂型机器造型的毛坯铸件。
由《机械加工工艺手册》查得该种铸件的尺寸公差等级CT为810级,现取CT为9级。
(1)曲轴主轴颈和连杆轴颈外圆表面由于这些表面的粗糙度要求较高,粗糙度值都是Ra0.8。
根据工艺设计要求,各轴颈加工分粗、半精车,粗、精磨。
用查表法确定加工余量。
由《机械加工工艺手册》查得:
精磨余量为0.3mm,粗磨余量为0.6mm,半精车余量为2.4mm,机械加工余量为7.0mm。
根据加工总余量定义可得到粗加工余量为3.7mm。
根据“入体原则”确定各工序的加工精度和表面粗糙度。
精磨:
、Ra0.8μm;粗磨:
、Ra1.6μm;半精车:
、Ra3.2μm;粗车:
、Ra12.5μm;各尺寸汇总如下表3-1:
表3-1轴颈处工序尺寸、公差、表面粗糙度及毛坯尺寸的确定
工序名称
工序间余量
/mm
工序
工序基本尺寸
/mm
标注工序尺寸公差/mm
经济精度/mm
表面粗糙度/μm
精磨
0.3
Ra0.8
85
粗磨
0.6
Ra1.6
85+0.3=85.3
半精车
2.4
Ra3.2
85.3+0.6=85.9
粗车
3.7
Ra12.5
85.9+2.4=88.3
毛坯
7.0
±1.5
Ra25
88.3+3.7=92
Ø92±1.5
(2)定时齿轮轴段外圆表面由于该表面的粗糙度要求是Ra1.6,根据工艺设计要求,该轴颈加工分粗车、半精车和精车。
由《机械加工工艺手册》查得:
精车余量为0.8mm,半精车余量为1.5mm,机械加工余量为6.5mm。
根据加工总余量定义可得到粗加工余量为4.2mm。
根据“入体原则”确定各工序的加工精度和表面粗糙度。
精车:
、Ra1.6μm;半精车:
、Ra3.2μm;粗车:
、Ra12.5μm;各尺寸汇总如下表3-2:
表3-2定时齿轮轴段处工序尺寸、公差、表面粗糙度及毛坯尺寸的确定
工序名称
工序间余量
/mm
工序
工序基本尺寸
/mm
标注工序尺寸公差/mm
经济精度/mm
表面粗糙度/μm
精车
0.8
Ra1.6
45
半精车
1.5
Ra3.2
45+0.8=45.8
粗车
4.2
Ra12.5
45.8+1.5=47.3
毛坯
6.5
±1
Ra25
47.3+4.2=51.5
Ø51.5±1
(3)带轮轴段外圆表面由于该表面的粗糙度要求是Ra1.6,根据工艺设计要求,该轴颈加工分粗车、半精车和精车。
由《机械加工工艺手册》查得:
精车余量为0.8mm,半精车余量为1.5mm,机械加工余量为6.5mm。
根据加工总余量定义可得到粗加工余量为4.2mm。
根据“入体原则”确定各工序的加工精度和表面粗糙度。
精车:
、Ra1.6μm;半精车:
、Ra3.2μm;粗车:
、Ra12.5μm;各尺寸汇总如下表3-3:
表3-3定时齿轮轴段处工序尺寸、公差、表面粗糙度及毛坯尺寸的确定
工序名称
工序间余量
/mm
工序
工序基本尺寸
/mm
标注工序尺寸公差/mm
经济精度/mm
表面粗糙度/μm
精车
0.8
Ra1.6
38
精车
半精车
1.5
Ra3.2
38+0.8=38.8
半精车
粗车
4.2
Ra12.5
38.8+1.5=40.3
粗车
毛坯
6.5
±1
Ra25
40.3+4.2=44.5
毛坯
(4)大端外圆表面由于该表面的粗糙度要求是Ra3.2,根据工艺设计要求,该轴颈加工分粗车、半精车和精车。
由《机械加工工艺手册》查得:
精车余量为1.0mm,半精车余量为2.0mm,机械加工余量为7.0mm。
根据加工总余量定义可得到粗加工余量为4.0mm。
根据“入体原则”确定各工序的加工精度和表面粗糙度。
精车:
、Ra3.2μm;半精车:
、Ra6.3μm;粗车:
、Ra12.5μm;各尺寸汇总如下表3-4:
表3-4大端外圆处工序尺寸、公差、表面粗糙度及毛坯尺寸的确定
工序名称
工序间余量
/mm
工序
工序基本尺寸
/mm
标注工序尺寸公差/mm
经济精度/mm
表面粗糙度/μm
精车
1.0
Ra3.2
160
精车
半精车
2.0
Ra6.3
160+1.0=161
半精车
粗车
4.0
Ra12.5
161+2.0=163
粗车
毛坯
7.0
±1.2
Ra25
163+4.0=167
毛坯
(5)大头外圆表面由于该表面的粗糙度要求是Ra3.2,根据工艺设计要求,该轴颈加工分粗车、半精车和精车。
由《机械加工工艺手册》查得:
精车余量为0.9mm,半精车余量为2.4mm,机械加工余量为6.5mm。
根据加工总余量定义可得到粗加工余量为3.2mm。
根据“入体原则”确定各工序的加工精度和表面粗糙度。
精车:
、Ra1.6μm;半精车:
、Ra3.2μm;粗车:
、Ra12.5μm;各尺寸汇总如下表3-5:
表3-5大头外圆处工序尺寸、公差、表面粗糙度及毛坯尺寸的确定
工序名称
工序间余量
/mm
工序
工序基本尺寸
/mm
标注工序尺寸公差/mm
经济精度/mm
表面粗糙度/μm
精车
0.9
Ra3.2
85
精车
半精车
2.4
Ra3.2
85+0.9=85.9
半精车
粗车
3.2
Ra12.5
85.9+2.4=88.3
粗车
毛坯
6.5
±1.5
Ra25
88.3+3.2=91.5
毛坯
(6)各轴颈宽度由于该表面的粗糙度要求也是Ra0.8,根据工艺设计要求,该轴颈加工分粗车、半精车、粗磨和精磨。
由《机械加工工艺手册》查得:
精磨余量为0.1mm,粗磨余量为0.3mm,半精车余量为1.0mm,机械加工余量为5.0mm。
根据加工总余量定义可得到粗加工余量为3.6m