万向节.docx
《万向节.docx》由会员分享,可在线阅读,更多相关《万向节.docx(49页珍藏版)》请在冰豆网上搜索。
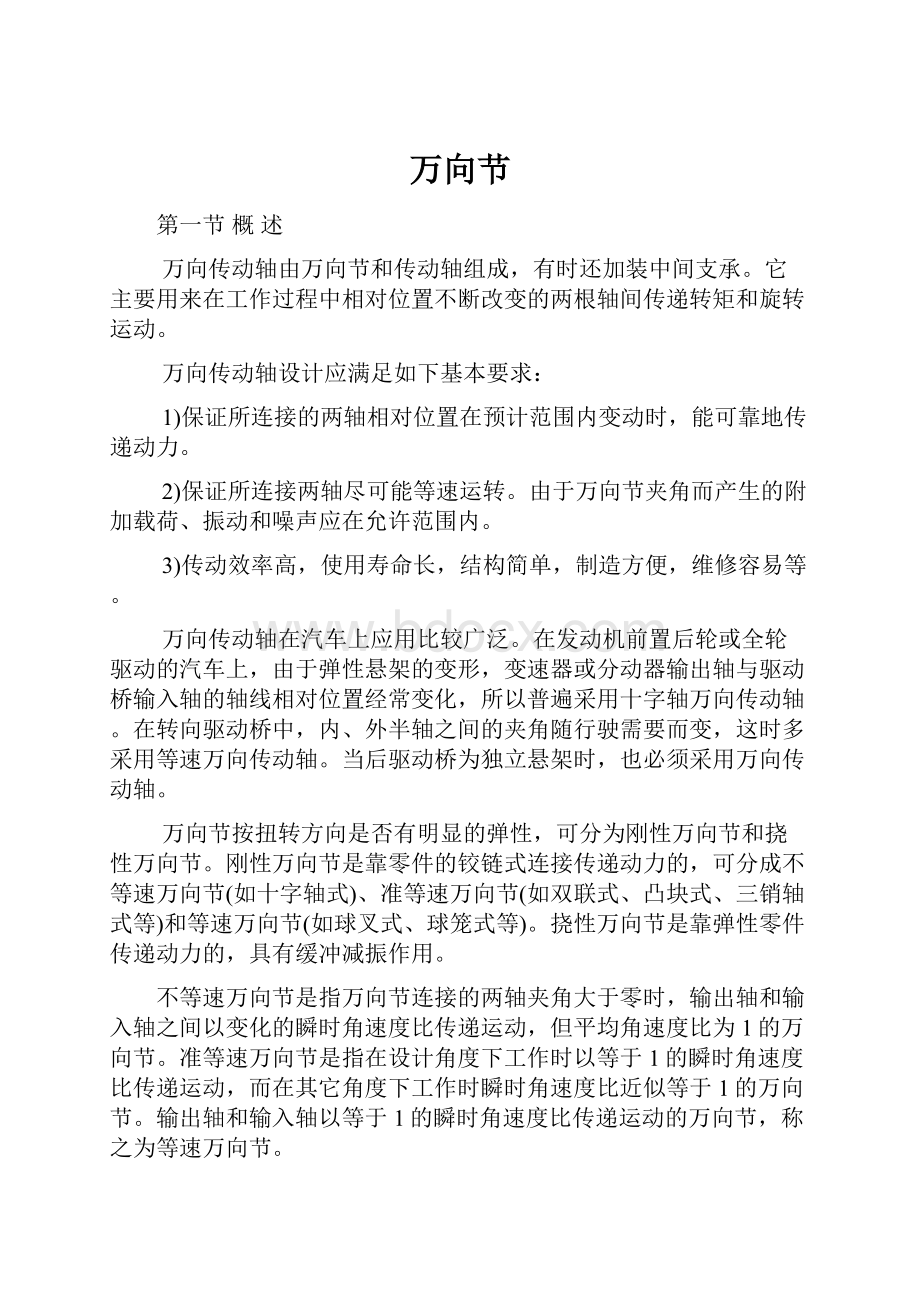
万向节
第一节概述
万向传动轴由万向节和传动轴组成,有时还加装中间支承。
它主要用来在工作过程中相对位置不断改变的两根轴间传递转矩和旋转运动。
万向传动轴设计应满足如下基本要求:
1)保证所连接的两轴相对位置在预计范围内变动时,能可靠地传递动力。
2)保证所连接两轴尽可能等速运转。
由于万向节夹角而产生的附加载荷、振动和噪声应在允许范围内。
3)传动效率高,使用寿命长,结构简单,制造方便,维修容易等。
万向传动轴在汽车上应用比较广泛。
在发动机前置后轮或全轮驱动的汽车上,由于弹性悬架的变形,变速器或分动器输出轴与驱动桥输入轴的轴线相对位置经常变化,所以普遍采用十字轴万向传动轴。
在转向驱动桥中,内、外半轴之间的夹角随行驶需要而变,这时多采用等速万向传动轴。
当后驱动桥为独立悬架时,也必须采用万向传动轴。
万向节按扭转方向是否有明显的弹性,可分为刚性万向节和挠性万向节。
刚性万向节是靠零件的铰链式连接传递动力的,可分成不等速万向节(如十字轴式)、准等速万向节(如双联式、凸块式、三销轴式等)和等速万向节(如球叉式、球笼式等)。
挠性万向节是靠弹性零件传递动力的,具有缓冲减振作用。
不等速万向节是指万向节连接的两轴夹角大于零时,输出轴和输入轴之间以变化的瞬时角速度比传递运动,但平均角速度比为1的万向节。
准等速万向节是指在设计角度下工作时以等于1的瞬时角速度比传递运动,而在其它角度下工作时瞬时角速度比近似等于1的万向节。
输出轴和输入轴以等于1的瞬时角速度比传递运动的万向节,称之为等速万向节。
第二节万向节结构方案分析
一、十字轴万向节
典型的十字轴万向节主要由主动叉、从动叉、十字轴、滚针轴承及其轴向定位件和橡胶密封件等组成。
目前常见的滚针轴承轴向定位方式有盖板式(图4—1a、b)、卡环式(图4—1c、d)、瓦盖固定式(图4—1e)和塑料环定位式(图4—1f)等。
盖板式轴承轴向定位方式的一般结构(图4—1a)是用螺栓1和盖板3将套筒5固定在万向节叉4上,并用锁片2将螺栓锁紧。
它工作可靠、拆装方便,但零件数目较多。
有时将弹性盖板6点焊于轴承座7底部(图4—1b),装配后,弹性盖板对轴承座底部有一定的预压力,以免高速转动时由于离心力作用,在十字轴端面与轴承座底之间出现间隙而引起十字轴轴向窜动,从而避免了由于这种窜动造成的传动轴动平衡状态的破坏。
卡环式可分为外卡式(图4—1c)和内卡式(图4—1d)两种。
它们具有结构简单、工作可靠、零件少和质量小的优点。
瓦盖固定式结构(图4—1e)中的万向节叉与十字轴轴颈配合的圆孔不是一个整体,而是分成两半用螺钉联接起来。
这种结构具有拆装方便、使用可靠的优点,但加工工艺较复杂。
塑料环定位结构(图4—1f)是在轴承碗外圆和万向节叉的轴承孔中部开一环形槽,当滚针轴承动配合装入万向节叉到正确位置时,将塑料经万向节叉上的小孔压注到环槽中,待万向节叉上另一与环槽垂直的小孔有塑料溢出时,表明塑料已充满环槽。
这种结构轴向定位可靠,十字轴轴向窜动小,但拆装不方便。
为了防止十字轴轴向窜动和发热,保证在任何工况下十字轴的端隙始终为零,有的结构在十字轴轴端与轴承碗之间加装端面止推滚针或滚柱轴承。
滚针轴承的润滑和密封好坏直接影响着十字轴万向节的使用寿命。
毛毡油封由于漏油多,防尘、防水效果差,在加注润滑油时,在个别滚针轴承中可能出现空气阻塞而造成缺
油,已不能满足越来越高的使用要求。
结构较复杂的双刃口复合油封(图4—2a),其中反装的单刃口橡胶油封用作径向密封,另一双刃口橡胶油封用作端面密封。
当向十字轴内腔注入润滑油时,陈油、磨损产物及多余的润滑油便从橡胶油封内圆表面与十字轴轴颈接触处溢出,
不需安装安全阀,防尘、防水效果良好。
在灰尘较多的条件下使用时,万向节寿命可显著提高。
图4—2b为一轿车上采用的多刃口油封,安装在无润滑油流通系统且一次润滑的万向
节上。
十字轴万向节结构简单,强度高,耐久性好,传动效率高,生产成本低。
但所连接的两轴夹角不宜过大,当夹角由4°增至16°时,十字轴万向节滚针轴承寿命约下降至原来的
1/4。
二、准等速万向节
1.双联式万向节
双联式万向节(图4—3)是由两个十字轴万向节组合而成。
为了保证两万向节连接的轴工作转速趋于相等,可设有分度机构。
偏心十字轴双联式万向节取消了分度机构,也可确保输出轴与输入轴接近等速。
五分度杆的双联式万向节,在军用越野车的转向驱动桥中用得
相当广泛。
此时采用主销中心偏离万向节中心1.0~3.5mm的方法,使两万向节的工作转速接近相等。
双联式万向节的主要优点是允许两轴间的夹角较大(一般可达50°,偏心十字轴双联式万向节可达60°),轴承密封性好,效率高,工作可靠,制造方便。
缺点是结构较复杂,外形尺寸较大,零件数目较多。
当应用于转向驱动桥时,由于双联式万向节轴向尺寸较大,为使主销轴线的延长线与地面交点到轮胎的接地印迹中心偏离不大,就必须用较大的主销内倾角。
2.凸块式万向节
对于凸块式万向节(图4—4),就运动副来看也是一种双联式万向节。
它主要由两个万向节叉1和4以及两个特殊形状的凸块2和3组成。
两凸块相当于双联万向节装置中两端带有位于同一平面上的两万向节叉的中间轴及两十字销,因此可以保证输入轴与输出轴近似等速。
这种结构工作可靠,加工简单,允许的万向节夹角较大(可达50°)。
但是由于工作面全为滑动摩擦,所以效率低,摩擦表面易磨损,且对密封和润滑要求较高。
它主要用于中型以上越野车的转向驱动桥。
3.三销轴式万向节三销轴式万向节
(图4—5)是由双联式万向节演变而来。
它主要由两个偏心轴叉、两个三销轴和六个滚针轴承组成。
三销轴式万向节允许所连接的两轴最大夹角为45°,易于密封。
但其外形尺寸较大,零件形状较复杂,毛坯需要精确模锻。
由于在工作中三销轴间有相对轴向滑动,万向节的两轴受有附加弯矩和轴向力,所以主动轴一侧需装轴向推力轴承。
这种结构目前用于个别中、重型越野车的转向驱动桥。
三、等速万向节
1.球叉式万向节
球叉式万向节按其钢球滚道形状不同可分为圆弧槽和直槽两种形式。
圆弧槽滚道型的球叉式万向节(图4—6a)由两个万向节叉、四个传力钢球和一个定心钢球组成。
两球叉上的圆弧槽中心线是以O1和O2为圆心而半径相等的圆,O1和O2到万向节中心O的距离相等。
当万向节两轴绕定心钢球中心O转动任何角度时,传力钢球中心始终在滚道中心两圆的交点上,从而保证输出轴与输入轴等速转动。
这种球叉式万向节结构较简单,可以在夹角不大于32°~33°的条件下正常工作。
由于四个钢球在单向传动中只有两个传递动力,故单位压力较大,磨损较快。
另外,这种万向节只有在传力钢球与滚道之间具有一定的预紧力时,才能保证等角速传动。
预紧力用选择不同尺寸级别的传力钢球来保证。
在使用中,随着磨损的增加,预紧力逐渐减小以至消失,这时两球叉之间便发生轴向窜动,从而破坏了传动的等速性,严重时会造成钢球脱落。
直槽滚道型球叉式万向节(图4—6b),两个球叉上的直槽与轴的中心线倾斜相同的角度,彼此对称。
在两球叉间的槽中装有四个钢球。
由于两球叉中的槽所处的位置是对称的,这便保证了四个钢球的中心处于两轴夹角的平分面上。
这种万向节加工比较容易,允许的轴间夹角不超过20°,在两叉间允许有一定量的轴间滑动。
圆弧槽型球叉式万向节主要应用于轻、中型越野车的转向驱动桥中。
直槽型球叉式万向节主要应用于断开式驱动桥中,当半轴摆动时,用它可补偿半轴的长度变化而省去滑动花键。
圆弧槽型球叉式万向节作为转向驱动桥的传力构件时,万向节旋转轴线应与车桥的轴线相重合,以避免发生万向节的摆动现象。
为了不至于在万向节转角接近最大值时,放置传力
钢球的主、从动叉的交叉槽趋于平行位置导致钢球无法约束而自动散开,造成万向节装配关系的破坏,在设计时应使两叉的最大夹角大于车轮的最大转角,同时万向节中心应位于转向主销轴线上。
另外,应保证在万向节处于最大转角时,各传力钢球与定心钢球之间不接触,至少使传力钢球与定心钢球在此情况下的间隙不小于5mm,且使各钢球与万向节轴头均匀地预紧在一起,使得在任意方向旋转时能通过万向节的两个传力钢球来传递转矩,避免靠一个钢球来传递,从而防止产生过载现象。
2.球笼式万向节
球笼式万向节是目前应用最为广泛的等速万向节。
早期的Rzeppa型球笼式万向节(图4—7a)是带分度杆的,球形壳1的内表面和星形套3的球表面上各有沿圆周均匀分布的六条同心的圆弧滚道,在它们之间装有六个传力钢球2,这些钢球由球笼4保持在同一平面内。
当万向节两轴之间的夹角变化时,靠比例合适的分度杆6拨动导向盘5,并带动球笼4使六个钢球2处于轴间夹角的平分面上。
经验表明,当轴间夹角较小时,分度杆是必要的;当轴间夹角大于11°时,仅靠球形壳和星形套上的子午滚道的交叉也可将钢球定在正确位置。
这种等速万向节无论转动方向如何,六个钢球全都传递转矩,它可在两轴之间的夹角达35°~37°的情况下工作。
目前结构较为简单、应用较为广泛的是Birfield型球笼式万向节(图4—7b)。
它取消了分度杆,球形壳和星形套的滚道做得不同心,令其圆心对称地偏离万向节中心。
这样,即使轴间夹角为0°,靠内、外子午滚道的交叉也能将钢球定在正确位置。
当轴间夹角为0’时,内、外滚道决定的钢球中心轨迹的夹角稍大于11°,这是能可靠地确定钢球正确位置的最小角度。
滚道的横断面为椭圆形,接触点和球心的连线与过球心的径向线成45‘角,椭圆在接触点处的曲率半径选为钢球半径的1.03~1.05倍。
当受载时,钢球与滚道的接触点实际上为椭圆形接触区。
由于工作时球的每个方向都有机会传递转矩,且由于球和球笼的配合是球形的,因此对这种万向节的润滑应给予足够的重视。
润滑剂的使用主要取决于传动的转速和角度。
在转速高达1500r/min时,一般使用防锈油脂。
若转速和角度都较大时,则使用润滑油。
比较好的方法是采用油浴和循环油润滑。
另外,万向节的密封装置应保证润滑剂不漏出,根据传动角度的大小采取不同形式的密封装置。
这种万向节允许的工作角可达42°。
由于传递转矩时六个钢球均同时参加工作,其承载能力和耐冲击能力强,效率高,结构紧凑,安装方便。
但是滚道的制造精度高,成本较高。
伸缩型球笼式万向节(图4—7c)结构与一般球笼式相近,仅仅外滚道为直槽。
在传递
转矩时,星形套与筒形壳可以沿轴向相对移动,故可省去其它万向传动装置中的滑动花键。
这不仅使结构简单,而且由于轴向相对移动是通过钢球沿内、外滚道滚动实现的,所以与滑
动花键相比,其滚动阻力小,传动效率高。
这种万向节允许的工作最大夹角为20°。
Rzeppa型球笼式万向节以前主要应用于转向驱动桥中,目前应用较少。
Birfield型球笼式万向节和伸缩型球笼式万向节被广泛地应用在具有独立悬架的转向驱动桥中,在靠近转向轮一侧采用Birfield型万向节,靠近差速器一侧则采用伸缩型球笼式万向节,以补偿由于前轮跳动及载荷变化而引起的轮距变化。
伸缩型万向节还被广泛地应用到断开式驱动桥中。
四、挠性万向节
挠性万向节依靠其中弹性元件的弹性变形来保证在相交两轴间传动时不发生干涉。
弹性
元件可以是橡胶盘、·橡胶金属套筒、铰接块、六角环形橡胶圈等多种形状。
盘式挠性万向节的弹性元件通常是4~12层的橡胶纤维或橡胶帘布片结构,并用金属零
件加固。
在挠性万向节装配时,通常使纤维层依次错开,以便于当挠性盘变形时,保证纤维帘布层承受最小的力。
六角环形橡胶挠性万向节的橡胶与用钢或铝合金制成的金属骨架硫化在一起。
为了使橡胶与金属可靠地结合,在硫化之前,骨架镀一层黄铜覆盖层。
使用这种万向节时,为了保证高速转动时传动轴总成有良好的动平衡,常在万向节所连接的两轴端部设专门机构保证对正中心。
图4—8a为具有球面对中机构的环形挠性万向节。
这种结构中装有无需润滑的球形滑动对中轴承,如能正确选择轴承配合,可使其内部在装配后具有适当的预紧力。
为使万向节有必要的寿命,总是设法使其轴向位移引起的轴向力、侧向位移引起的侧向力和万向节工作角引起的力矩尽可能小,使挠性万向节主要传递工作转矩。
有的结构允许有一定的轴向变形(图4—8b)。
当这种环形挠性万向节的轴向变形量满足使用要求时,可
省去伸缩花健。
挠性万向节能减小传动系的扭转振动、动载荷和噪声,结构简单,使用中不需润滑,一
般用于两轴间夹角不大(一般为3°~5°)和很小轴向位移的万向传动场合。
如它常在轿车三
万向节传动中,被用来作为靠近变速器的第一万向节,或在重型汽车中用于发动机与变速器之间,越野汽车中用于变速器与分动器之间,以消除制造安装误差和车架变形对传动的影响。
第三节万向传动的运动和受力分析
一、单十字轴万向节传动
当十字轴万向节的主动轴与从动轴存在一定夹角α时,主动轴的角速度ω1与从动轴的角速度ω2之间存在如下关系
(4-1)
式中,φ1为主动轴转角,定义为万向节主动叉所在平面与万向节主、从动轴所在平面的夹角。
由于cosα是周期为2π的周期函数,所以ω2/ω1,也为同周期的周期函数。
当φ1为0、π时,ω2达最大值ω2max。
且为ω1/cosα;当φ1为π/2、3π/2时,ω2有最小值ω2min。
且为ω1cosα。
因此,当主动轴以等角速度转动时,从动轴时快时慢,此即为普通十字轴万向节传动的不等速性。
十字轴万向节传动的不等速性可用转速不均匀系数k来表示
(4-2)
如不计万向节的摩擦损失,主动轴转矩T1和从动轴转矩T2与各自相应的角速度有关系式T1ω1=T2ω2,这样有
(4-3)
显然,当ω2/ω1最小时,从动轴上的转矩为最大T2max=T1/cosα;当ω2/ω1最大时,
从动轴上的转矩为最小T2min=T1cosα。
当Tl与α一定时,T2在其最大值与最小值之间每一转变化两次;
具有夹角α的十字轴万向节,仅在主动轴驱动转矩和从动轴反转矩的作用下是不能平衡的。
这是因为这两个转矩作用在不同的平面内,在不计万向节惯性力矩时,它们的矢量互成一角度而不能自行封闭,此时在万向节上必然还作用有另外的力偶矩。
从万向节叉与十字轴之间的约束关系分析可知,主动叉对十字轴的作用力偶矩,除主动轴驱动转矩Tl,之外,还有作用在主动叉平面的弯曲力偶矩Tl′。
同理,从动叉对十字轴也作用有从动轴反转矩T2和作用在从动叉平面的弯曲力偶矩T2′。
在这四个力矩作用下,使十字轴万向节得以平衡。
下面仅讨论主动叉在两特殊位置时,附加弯曲力偶矩的大小及变化特点。
当主动叉φl处于0和π位置时(图4—9a),由于Tl作用在十字轴平面,Tl′必为零;而T2的作用平面与十字轴不共平面,必有T2′存在,且矢量T2′垂直于矢量T2;合矢量
T2′+T2指向十字轴平面的法线方向,与Tl大小相等、方向相反。
这样,从动叉上的附加弯矩T2′=Tlsina。
当主动叉φl处于π/2和3π/2位置时(图4—9b),同理可知T2′=0,主动叉上的附加弯矩Tl′=Tltana。
分析可知,附加弯矩的大小是在零与上述两最大值之间变化,其变化周期为π,即每一转变化两次。
附加弯矩可引起与万向节相连零部件的弯曲振动,可在万向节主、从动轴支承上引起周期性变化的径向载荷,从而激起支承处的振动。
因此,为了控制附加弯矩,应避免两轴之间的夹角过大。
二、双十字轴万向节传动
当输入轴与输出轴之间存在夹角α时,单个十字轴万向节的输出轴相对于输入轴是不等速旋转的。
为使处于同一平面的输出轴与输入轴等速旋转,可采用双万向节传动,但必须保证同传动轴相连的两万向节叉应布置在同一平面内,且使两万向节夹角α1与α2相等(图4一10)。
在双万向节传动中,直接与输入轴和输出轴相连的万向节叉所受的附加弯矩分别由相应轴的支承反力平衡。
当输入轴与输出轴平行时(图4—10a),直接连接传动轴的两万向节叉所受的附加弯矩彼此平衡,传动轴发生如图4—10b中双点划线所示的弹性弯曲,从而引起传动轴的弯曲振动。
当输入轴与输出轴相交时(图4—10c),传动轴两端万向节叉上所受的附加弯矩方向相同,不能彼此平衡,传动轴发生如图4—10d中双点划线所示的弹性弯曲,从而对两端的十字轴产生大小相等、方向相反的径向力。
此径向力作用在滚针轴承碗的底部,并在输入轴与输出轴的支承上引起反力。
三、多十字轴万向节传动
多万向节传动的从动叉相对主动叉的转角差Δφ的计算公式与单万向节相似,可写成
(4—4)
式中,αe为多万向节传动的当量夹角;θ为主动叉的初相位角;φ1为主动轴转角。
式(4—4)表明,多万向节传动输出轴与输入轴的运动关系,如同具有夹角αe而主动叉具有初相位θ的单万向节传动。
假如多万向节传动的各轴轴线均在同一平面,且各传动轴两端万向节叉平面之间的夹角为0或π/2,则当量夹角αe为
(4—5)
式中,α1、α2、α3…为各万向节的夹角。
式中的正负号这样确定:
当第一万向节的主动叉处在各轴轴线所在的平面内,在其余的万向节中,如果其主动叉平面与此平面重合定义为正,与此平面垂直定义为负。
为使多万向节传动的输出轴与输入轴等速旋转,应使αe=0。
万向节传动输出轴与输入轴的转角差会引起动力总成支承和悬架弹性元件的振动,还能引起与输出轴相连齿轮的冲击和噪声及驾驶室内的谐振噪声。
因此,在设计多万向节传动时,总是希望其当量夹角αe尽可能小,一般设计时应使空载和满载两种工况下的αe不大于3°另外,对多万向节传动输出轴的角加速度幅值
小加以限制。
对于轿车,
≤350rad/s2;对于货车,
≤600rad/s2。
四、等速万向节传动
在此仅分析目前在轿车上广泛采用的Birfield型球笼式等速万向节的运动情况。
其等速传动原理如图4—7b所示,球形壳的内表面有六条凹槽,形成外滚道;星形套外表面有相应的六条凹槽,形成内滚道。
外滚道中心A与内滚道中心B分别位于万向节中心O的两边,且OA=OB。
另外,钢球中心C到A、B两点的距离也相等,保持架的内、外球面也以万向节中心为球心,这样∠COA=∠COB,即两轴相交任意交角α时,传力钢球都位于交角平分面上。
此时钢球中心到主、从动轴的距离α相等,从而保证了从动轴与主动轴以相等的角速度旋转。
第四节万向节设计
一、万向传动的计算载荷
万向传动轴因布置位置不同,计算载荷是不同的。
计算载荷的计算方法主要有三种,见表4—1。
表4—1万向传动轴计算载荷(N·m)
\\\位置
计算方法\\\
用于变速器与驱动桥之间
用于转向驱动桥中
按发动机最大转矩和—挡传动比来确定
按驱动轮打滑来确定
按日常平均使用转矩来确定
表4—1各式中,Temax为发动机最大转矩;n为计算驱动桥数,取法见表4—2;i1为变速器一挡传动比;η为发动机到万向传动轴之间的传动效率;k为液力变矩器变矩系数,k=[(ko—1)/2]十1,ko为最大变矩系数;G2为满载状态下一个驱动桥上的静载荷(N);m2′为汽车最大加速度时的后轴负荷转移系数,轿车:
m2′=1.2~1.4,货车:
m2′=1.1~1.2;φ为轮胎与路面间的附着系数,对于安装一般轮胎的公路用汽车,在良好的混凝土或沥青路面上,φ可取0.85,对于安装防侧滑轮胎的轿车,φ可取1.25,对于越野车,φ值变化较大,一般取1;rr为车轮滚动半径(m);i。
为主减速器传动化;im为主减速器从动齿轮到车轮之间的传动比;ηm为主减速器主动齿轮到车轮之间的传动效率;G1为满载状态下转向驱动桥上的静载荷(N);m1′为汽车最大加速度时的前轴负荷转移系数,轿车:
m1′=0.80~0.85,货车:
m1′=0.75—0.90;F1为日常汽车行驶平均牵引力(N);if为分动器传动比,取法见表4—2:
kd为猛接离介器所产生的动载系数,对于液力自动变速器,kd=1对于具有手动操纵的机械变速器的高性能赛车,kd=3,对于性能系数fi=0的汽车(一般货车、矿用汽车和越野车),kd=1,对于fi>0的汽车,kd=2或由经验选定。
性能系数由下式计算
当
时
fj=
1当
时
式中,ma为汽车满载质量(若有挂车,则要加上挂车质量)(kg)。
表4—2n与if选取表
车型
高挡传动比ifg与低挡传动比ifd关系
if
n
4X4
ifg>ifd/2
ifg
1
ifgifd
2
6X6
ifg/2>ifd/3
ifg
2
ifg/2ifd
3
对万向传动轴进行静强度计算时,计算载荷TS取Tsel和Tssl的最小值,或取Tse2和Tse2的最小值,即TS=min[Tsel,Tssl]或TS=min[Tse2,Tse2],安全系数一般取2.5~3.0。
当对万向传动轴进行疲劳寿命计算时,计算载荷TS取TsFl或TsF2。
二、十字轴万向节设计
十字轴万向节的损坏形式主要有十字轴轴颈和滚针轴承的磨损,十字轴轴颈和滚针轴承碗工作表面出现压痕和剥落。
一般情况下,当磨损或压痕超过0.15mm时,十字轴万向节便应报废。
十字轴的主要失效形式是轴颈根部处的断裂,所以在设计十字轴万向节时,应保证十字轴轴颈有足够的抗弯强度。
设各滚针对十字轴轴颈作用力的合力为F(图4—11),则
(4—6)
式中,TS为万向传动的计算转矩,TS=min[Tse,Tss]min;r为合力F作用线到十字轴中心之间的距离;α为万向传动的最大夹角。
十字轴轴颈根部的弯曲应力σw应满足
(4—7)
式中,d1为十字轴轴颈直径;d2为十字轴油道孔直径;s为合力F作用线到轴颈根部的距离;[σw]为弯曲应力许用值,为250~350MPa。
十字轴轴颈的切应力τ应满足
(4—8)
式中,[τ]为切应力τ许用值,为80~120MPa。
滚针轴承中的滚针直径一般不小于1.6mm,以免压碎,而且差别要小,否则会加重载荷在滚针间分配的不均匀性,一般控制在0.003mm以内。
滚针轴承径向间隙过大时,承受载荷的滚针数减少,有出现滚针卡住的可能性;而间隙过小时,有可能出现受热卡住或因脏物阻滞卡住,合适的间隙为0.009~0.095mm,滚针轴承的周向总间隙以0.08~0.30mm为好。
滚针的长度一般不超过轴颈的长度,使其既有较高的承载能力,又不致因滚针过长发生歪斜而造成应力集中。
滚针在轴向的游隙一般不应超过0.2~0.4mm。
滚针轴承的接触应力为
(4—9)
式中,η0为滚针直径(mm);Lb为滚针工作长度(mm);Fn为在合力F作用下一个滚针所受的最大载荷(N),由式(4—10)确定
(4—10)
式中,i为滚针列数;z为每列中的滚针数。
当滚针和十字轴轴颈表面硬度在58HRC以上时,许用接触应力为3000~3200MPa。
万向节叉与十字轴组成连接支承。
在万向节工作过程中产生支承反力,叉体受到弯曲和剪切,一般在与十字轴轴孔中心线成45°的某一截面上的应力最大,所以也应对此处进行强度校核。
十字轴万向节的传动效率与两轴的轴间夹角α、十字轴支承结构和材料、加工和装配精度以及润滑条件等有关。
当α≤25°时可按下式计算
(4—11)
式中η0为十字轴万向节传动效率;f为轴颈与万向节叉的摩擦因数,滑动轴承:
f=0.15~0.20,滚针轴承:
f=0.05~0.10;其它符号意义同前。
通常情况下,十字轴万向节传动