ca6140 手柄座 机械制造技术基础课程设计说明书.docx
《ca6140 手柄座 机械制造技术基础课程设计说明书.docx》由会员分享,可在线阅读,更多相关《ca6140 手柄座 机械制造技术基础课程设计说明书.docx(22页珍藏版)》请在冰豆网上搜索。
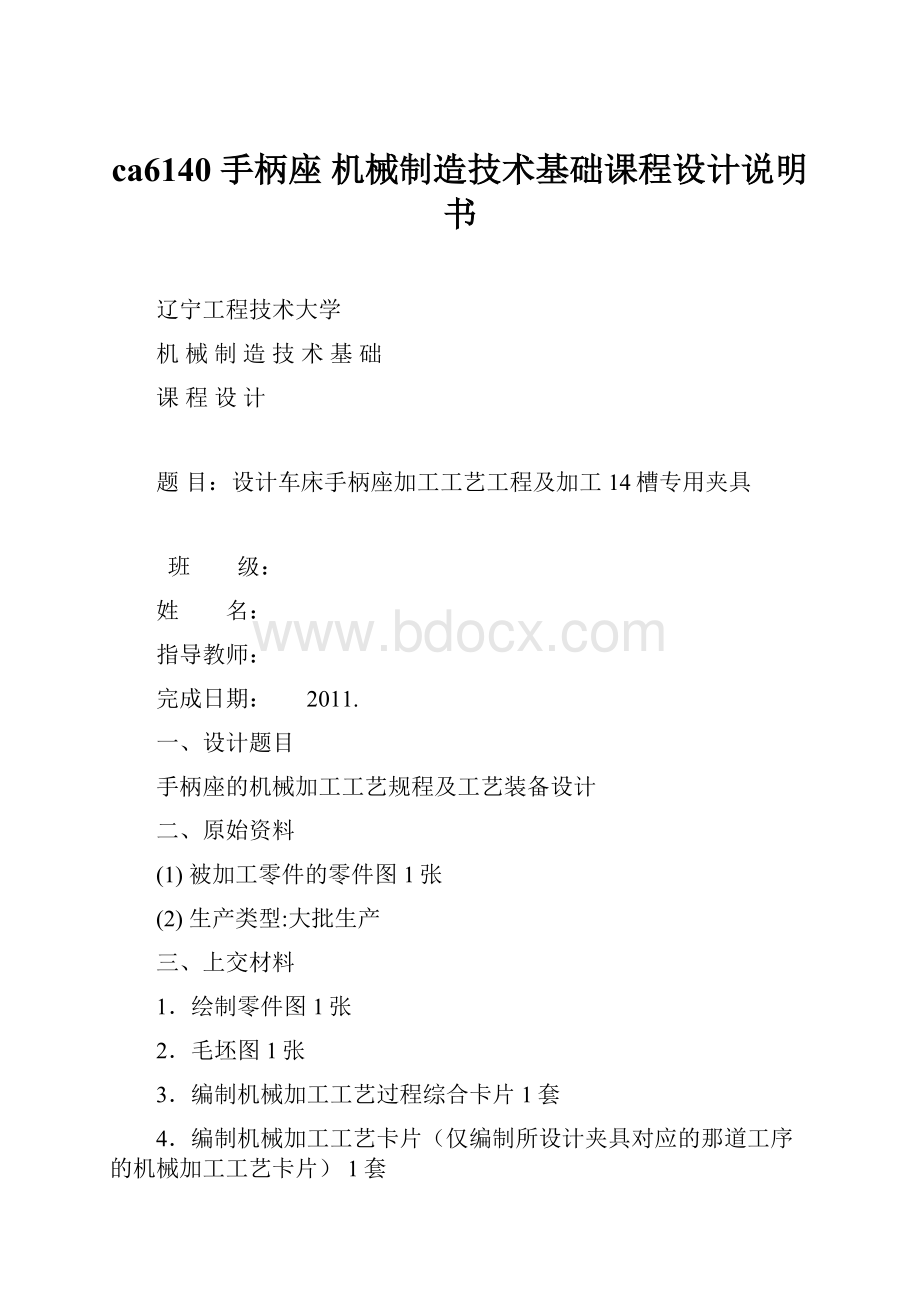
ca6140手柄座机械制造技术基础课程设计说明书
辽宁工程技术大学
机械制造技术基础
课程设计
题目:
设计车床手柄座加工工艺工程及加工14槽专用夹具
班 级:
姓 名:
指导教师:
完成日期:
2011.
一、设计题目
手柄座的机械加工工艺规程及工艺装备设计
二、原始资料
(1)被加工零件的零件图1张
(2)生产类型:
大批生产
三、上交材料
1.绘制零件图1张
2.毛坯图1张
3.编制机械加工工艺过程综合卡片1套
4.编制机械加工工艺卡片(仅编制所设计夹具对应的那道工序的机械加工工艺卡片)1套
5.绘制夹具装配图(A0或A1)1张
6.绘制夹具中1个零件图(A1或A2。
装配图出来后,由指导教师为学生指定需绘制的零件图,一般为夹具体)。
1张
7.编写课程设计说明书(约5000-8000字)。
1份
四、进度安排
本课程设计要求在3周内完成。
1.第l~2天查资料,熟悉题目阶段。
2.第3~7天,完成零件的工艺性分析,确定毛坯的类型、制造方法和机械加工工艺规程的设计并编制出零件的机械加工工艺卡片。
3.第8~10天,完成夹具总体方案设计(画出草图,与指导教师沟通,在其同意的前提下,进行课程设计的下一步)。
4.第11~13天,完成夹具总装图的绘制。
5.第14~15天,零件图的绘制。
6.第16~18天,整理并完成设计说明书的编写。
7.第19天,完成图纸和说明书的输出打印。
8.第20~21天,答辩
五、指导教师评语
成绩:
指导教师
日 期
摘 要
机械制造技术基础课程设计,是以切削理论为基础,制造工艺为主线,兼顾工艺装备知识的机械制造技术基本涉机能力培养的实践课程;是综合运用机械制造技术的基本知识,基本理论和基本技能,分析和解决实际工程问题的一个重要教学环节;是对学生运用掌握的“机械制造”技术基础知识及相关知识的一次全面的应用训练。
机械制造技术基础课程设计,是已机械制造工艺装备为内容进行的设计。
即以给定的一个中等复杂的程度的中小型机械零件为对象,在确定其毛胚制造工艺的基础上,编制其机械加工工艺规程,并对其一工序进行机床专用卡具设计。
由于能力有限,设计尚有许多不足之处,恳请各位老师给予批评指正。
Abstract
Mechanicalmanufacturingtechnologyfoundationcoursedesign,isthecuttingtheoryasafoundation,manufacturingprocessasthemainline,balancingprocessequipmentknowledgeofmechanicalmanufacturingtechnologybasicwademachineofcultivatingtheabilityofpracticalcourses,Isthecomprehensiveuseofmechanicalmanufacturingtechnologyofthebasicknowledge,basictheoryandbasicskill,analyzeandsolvepracticalengineeringproblemsanimportantteachinglink,Forthestudentsusemaster"mechanicalmanufacturingtechnology"basisknowledgeandrelatedknowledgeofacomprehensiveapplicationtraining.Mechanicalmanufacturingtechnologyfoundationcoursedesign,isalreadymachinerymanufacturingtechnologyandequipmentforthedesignofcontent.Namelyinthegivenamedium-sizedcomplexdegreeofsmallandmedium-sizedmachinerypartsastheobject,indeterminingtheblankcastsmanufacturingtechnology,onthebasisofcompilingthemachiningprocessplanning,andoneprocessmachinespecialfixturedesign.
课程设计的目的和要求
CA6140手柄座课程设计说明书
一、课程设计的目的和要求
(一)课程设计的目的
机械制造工艺学课程设计是在学完机械制造工艺学(或数控加工工艺学),
生产实习后进行的一个教学环节。
要求学生在设计中能初步学会综合运用所学
过的工艺基本理论,在下述几方面得到锻炼
a)巩固、扩大工艺课所学内容;
b)在教师指导下,运用所学知识,独立完成工业设计,并受到工艺技术工作的实际训练
c)学会查阅,准确使用设计资料,图表和手册。
二、零件的分析
(一)零件的作用
该零件是CA6140车床操纵部分的组成零件之一,该手柄座的作用就相当于一个连杆。
车床外部手柄的运动是通过CA6140车床手柄座传递到车床内部实现人为对机床的操纵。
手柄与该零件通过φ25mm孔连接,机床内部零件通过φ10mm孔与手柄座连接,即CA6140车床手柄座的作用是实现运动由外部到内部的传递。
(二)零件的工艺分析
CA6140车床手柄座的加工表面分四种,主要是孔的加工,圆柱端面的加工,槽的加工,螺纹孔的加工,各组加工面之间有严格的尺寸位置度要求和一定的表面加工精度要求,特别是孔的加工,几乎都要保证Ra1.6mm的表面粗糙度,因而需精加工,现将主要加工面分述如下:
a)孔的加工
该零件共有5个孔要加工:
φ25H8mm孔需要精加工;φ14H7mm孔是不通孔,特别注意该孔的加工深度;φ5mm圆锥孔及φ5.5mm孔虽是小孔,但由于表面粗糙度要求高,仍需精铰。
b)面的加工
该零件共有3个端面要加工:
φ45mm圆柱小端面精度要求较高,同时也是配合φ25H8mm孔作为后续工序的精基准面,需精加工;φ45mm圆柱大端面以及φ25H8mm孔端面粗铣既可。
c)槽的加工
该零件仅有2个槽需加工:
φ25H8mm孔上键槽两侧面粗糙度为Ra1.6mm,需精加工,底面加工精度要求不高,但与φ25H8mm孔上表面有尺寸要求,而加工键槽时很难以φ25H8mm孔上表面为定位基准,因而要特别注意尺寸链的推算,保证加工尺寸要求;深槽要注意加工深度,由于表面粗糙度为Ra6.3mm,半精铣即可。
d)螺纹孔的加工
M10mm螺纹孔是重点工序,它与φ25H8mm孔和φ25H8mm孔中心线有角度要求,同时中心线与φ45mm圆柱端面有11mm的尺寸位置要求。
由以上分析可知,该零件的加工应先加工φ45mm圆柱两端面,再以端面为基准加工作为后续工序主要精基准的φ25H8mm孔,进而以该孔为精基准加工出所有的孔,面,槽,螺纹孔等。
三、工艺规程设计
(一)确定生产类型和毛坯的制造形
a)确定生产类型
根据下式计算零件的生产纲领
N(零)=Q×n×(1+a%)(1+b%)
则N(零)=6000×1×(1+12%)(1+3%)
=6000×1×1.12×1.03
=6922(件)
b)毛坯的制造形
零件材料为HT15-33,根据选择毛坯应考虑的因素,该零件体积较小,形状较复杂,外表面采用不去除材料方法获得粗糙度要求,由于零件年产量为6000件,已达到大批生产的水平,而砂型铸造生产成本低,设备简单,故本零件毛坯采用砂型铸造。
由于零件上孔都较小,且都有严格的表面精度要求,故都不铸出,留待后续机械加工反而经济实用。
(二)基面的选择
基面选择是工艺规划设计中的重要工作之一,基准选择的正确与合理,可以使加工质量得到保证,生产率得到提高,否则,不但使加工工艺过程中的问题百出,更有甚者,还会造成零件大批报废,使生产无法正常进行。
a)粗基准的选择
粗基准选择应为后续加工提供精基准,由于该零件毛坯没有铸孔,故只能以3个主要端面为基准,由于φ45mm小端面表面粗糙度为Ra3.2mm,若直接以大端面为粗基准,恐不能一次达到加工精度,故先以φ45mm小端面为粗基准,粗铣φ45mm大端面,再以φ45mm大端面为基准,半精铣小端面,并保证尺寸43mm。
b)精基准的选择
精基准主要考虑如何保证加工精度和装夹方便,前面已多次提过以φ25mm孔为第一精基准,φ45mm圆柱小端面作为基准先加工出φ25mm孔,然后作为辅助基准面配合φ25mm孔加工后续工序中的孔,面,槽,螺纹等。
(三)工艺路线的拟定
拟定工艺路线的内容除选择定位基准外,还要选择各加工表面的加工方法,安排工序的先后顺序,确定加工设备,工艺装备等。
工艺路线的拟定要考虑使工件的几何形状精度,尺寸精度及位置精度等技术要求得到合理保证,成批生产还应考虑采用组合机床,专用夹具,工序集中,以提高效率,还应考虑加工的经济性,以便使生产成本尽量下降。
a)确定加工方法
加工表面
精度
表面
粗糙
可选加工方法
确定加工方法
φ45mm
大端面
IT7~8
3.2
粗刨→精刨
粗铣
粗铣
φ45mm
小端面
IT7
3.2
粗刨→精刨
粗铣→半精铣
粗铣→半精铣
φ25H8mm孔
IT8
1.6
粗镗→半粗镗→拉
钻→扩→铰
钻→扩→铰
键槽
IT9
1.6
粗铣→精铣
粗铣→精铣
φ10H7mm孔
IT8
1.6
粗镗→半粗镗→拉
钻→粗铰→精铰
钻→粗铰→精铰
φ14H7mm孔端面
IT8
1.6
粗刨→精刨
粗铣
粗铣
φ14H7mm孔
IT7
1.6
粗镗→半粗镗→拉
钻→粗铰→精铰
钻→粗铰→精铰
M10mm螺纹孔
钻→攻
钻→攻
φ5.5mm孔
IT7~8
3.2
钻→粗铰→精铰
钻→精铰
钻→精铰
φ5mm圆锥孔
IT7~8
1.6
铰
钻→精铰
钻→精铰
大槽
IT8~11
6.3
粗刨→半精刨
粗铣
粗铣
b)工艺路线方案一
工序Ⅰ.铣φ45mm圆柱小端面;
工序Ⅱ.粗铣φ45mm圆柱大端面,保证尺寸43mm;
工序Ⅲ.钻,扩,铰φ25H8mm孔;
工序Ⅳ.钻,扩,铰φ10H7mm孔;
工序Ⅴ.钻,铰φ14H7mm孔;
工序Ⅵ.钻,攻M10mm螺纹孔;
工序Ⅶ.插键槽,保证尺寸27.3H11mm;
工序Ⅷ.钻,铰φ5mm圆锥孔;
工序Ⅸ.铣槽,保证尺寸14mm,深度30mm;
工序Ⅹ.钻,铰φ5.5mm孔;
工序Ⅺ.去锐边,毛刺;
工序Ⅻ.终检,入库。
c)工艺路线方案二
工序Ⅰ.粗铣φ45mm圆柱大端面;
工序Ⅱ.半精铣φ45mm圆柱小端面,保证尺寸43mm;
工序Ⅲ.钻,扩,铰φ25H8mm孔;
工序Ⅳ.粗铣φ14H7mm孔端面;
工序Ⅴ.钻,铰φ14H7mm孔;
工序Ⅵ.钻,铰φ5mm圆锥孔,钻,扩,铰φ10H7mm孔;
工序Ⅶ.钻,攻M10螺纹孔;
工序Ⅷ.插键槽,保证尺寸27.3H11mm
工序Ⅸ.铣槽,保证尺寸14mm,深度30mm;
工序Ⅹ.钻,铰φ5.5mm孔;
工序Ⅺ.去锐边,毛刺;
工序Ⅻ.终检,入库。
d)工艺方案的比较与分析
上述两个方案区别在两点:
一是方案一先加工有Ra3.2mm表面精度要求的小端面,再加工大端面,而方案二是先粗铣大端面,再加工小端面;二是方案一将φ5mm圆锥孔和φ10mm孔按部就班顺序加工,而方案二显得更灵活聪明,看出这两个孔的定位方式,夹紧方式相同,故而在一台机床上同时加工出来.另外,方案一没有铣φ14mm小端面,但由于φ14mm孔有严格深度要求,故最好还是粗铣一遍.
两套方案显然方案二更简洁更符合要求,但正如前面所分析的,方案二将φ5mm圆锥孔φ10mm孔的加工合并在一道工中,虽然减少了装夹次数,简化了工艺设计,但在一道工序中完成这两个钻孔,由于两孔的加工深度,加工刀具尺寸,加工时产生的轴向力等等都相差较大,且两孔的加工精度要求都较高,显然组合机床不适用。
如果采用摇臂钻床,对于大批量生产,则要频繁更换钻头刀具,大大增加了劳动强度,降低了生产效率,因此,决定还是将两个孔分开加工。
综上所述,零件的最后加工路线如下
工序Ⅰ.粗铣φ45mm圆柱大端面,以φ45mm圆柱小端面为定位基准;
工序Ⅱ.半精铣φ45mm圆柱小端面,以φ45mm大端面为定位基准;
工序Ⅲ.钻,扩,铰φ25H8mm孔,以φ45mm圆柱大端面为定位基准;
工序Ⅳ.钻,扩,铰φ10H7mm,以φ25H8mm孔和φ45mm圆柱小端面为基准;
工序Ⅴ.粗铣φ14mm孔端面,利用φ45mm圆柱小端面,φ25H8mm孔和φ10H7mm孔定位,保证尺寸43mm;
工序Ⅵ.钻,铰φ14H7mm孔,定位与Ⅴ工序相同,保证孔深度25mm;
工序Ⅶ.钻,攻M10mm螺纹孔,定位与Ⅴ工序相同;
工序Ⅷ.钻,铰φ5mm圆锥孔,定位与Ⅴ工序相同;
工序Ⅸ.插键槽,为便于加工,以φ45mm圆柱小端面,φ10H7mm孔和φ14H7mm孔端面定位,同时要保证尺寸27.3H11mm;
工序Ⅹ.铣槽,定位与Ⅴ工序相同,保证尺寸30mm;
工序Ⅺ.钻,铰φ5.5mm孔,定位与Ⅴ工序相同;
工序Ⅻ.去锐边,毛刺,尤其注意φ25H8mm孔表面可能因为钻M10mm螺纹孔以及插槽带来的表面鳞次损伤;
工序ⅩⅢ.终检,入库。
(四)机械加工余量、工序尺寸及毛坯尺寸的确定
CA6140车床手柄座零件材料为HT15-33,毛坯重量约为0.73kg,生产类型为大批生产,采用砂型铸造生产。
由于所有孔均有精度要求,且尺寸小,均不铸出。
故仅确定三个端面的相关尺寸。
查表确定加工余量:
砂型铸造,材料为灰铸铁,机器造型,公差等级为CT8~12,取CT10,加工余量等级E~G,取G
切削余量:
查表,基本尺寸小于100mm,加工余量为1.4mm;
基本尺寸小于63mm,加工余量为0.7mm。
铸件公差等级:
查表,基本尺寸小于100mm,取3.2mm;
基本尺寸小于63mm,取2.8mm。
a)φ45mm圆柱两端面毛坯尺寸及加工余量计算
根据工序要求,φ45mm圆柱两端面经过两道工序,先粗铣φ45mm圆柱大端面,再粗,半精铣φ45mm圆柱小端面,各步余量如下:
粗铣:
由《机械加工工艺手册第一卷》表3.2-23,其余量值规定,对于小端面(≤50mm)为1.0~2.0mm,现取1.8mm。
表3.2-27粗铣平面的厚度偏差(≤30mm)为―0.25~―0.39mm,现取―0.30mm。
半精铣:
由《加工工艺手册》表3.2-25,其余量规定值为1.0mm。
故铸造毛坯的基本尺寸为43+1.2+1.8+1.0=47mm。
又根据前面铸件尺寸公差标准值,取尺寸公差为2.8mm。
故:
毛坯的名义尺寸:
43+1.2+1.8+1.0=47mm;
毛坯的最小尺寸:
47-1.4=45.6mm;
毛坯的最大尺寸:
47+1.4=48.4mm;
粗铣大端面后的最大尺寸:
43+1.0+1.2=45.2mm;
粗铣大端面后的最小尺寸:
45.2-0.30=44.9mm;
粗铣小端面后的最大尺寸:
:
43+1.0=44mm;
粗铣小端面后的最小尺寸:
:
44-0.30=43.7mm。
精铣后尺寸与零件尺寸相同,但由于设计零件图纸并未给出具体的公差等级,现按《加工工艺手册》表5.29,粗铣→精铣所能达到的经济精度取IT8,按入体原则取值。
故精铣后尺寸为43
mm
b)φ14H7mm孔端面毛坯尺寸及加工余量计算
根据工序要求,φ14H7mm孔端面仅由粗铣得到,故φ14H7mm孔端面距φ25H8mm孔中心线的毛坯基本尺寸为43+1.2=44.2mm,故:
毛坯的名义尺寸:
43+1.2=44.2mm;
毛坯的最大尺寸:
44.2+1.4=45.6mm;
毛坯的最小尺寸:
44.2-1.4=42.8mm。
粗铣后尺寸应于零件图尺寸相同,但由于零件图纸并未给出具体的公差等级,现按前面粗铣平面厚度偏差取-0.28mm。
故粗铣后的尺寸为43
mm
其他毛坯尺寸由于零件图纸未做具体的工序尺寸要求,且对后面诸孔,槽的加工影响不大,仅粗铣即可。
c)其他尺寸极其加工余量的确
其他工序尺寸包括5个孔,2个槽,1个螺纹孔的基本尺寸,现仅分析主要的5个孔的加工余量及尺寸偏差。
5个孔均不铸出,机械加工出来,根据《加工工艺手册》,由于5个孔的表面粗糙度要求均较高,所以都要经过精铰工序,具体工序尺寸和加工余量为:
(1)φ25H8mm孔,Ra=1.6mm;
根据《加工工艺手册》表3.2-10,加工该孔的工艺为:
钻→扩→铰
钻孔:
φ23mm;
扩孔:
φ24.8mm2Z=1.8mm(Z为单边加工余量);
铰孔:
φ25H8mm。
(2)φ10H7mm孔,Ra=1.6mm;
根据《加工工艺手册》表3.2-9,加工该孔的工艺为:
钻→粗铰→精铰
钻孔:
φ9.8mm;
粗铰:
φ9.96mm;
精铰:
φ10H7mm。
(3)φ14H7mm孔,Ra=1.6mm;
根据《加工工艺手册》表3.2-9,加工该孔的工艺为:
钻→粗铰→精铰
钻孔:
φ13.0mm;
粗铰:
φ13.95mm;
精铰:
φ14H7mm。
(4)φ5mm圆锥孔,Ra=1.6mm;
由于零件图纸未给出具体的公差等级,现也按H7公差等级加工,按表3.2-9,加工该孔的工艺为:
钻→精铰
钻孔:
φ4.8mm;
精铰:
φ5H7mm。
(5)φ5.5mm孔,Ra=3.2mm
由于也未给出公差等级,现同样按φ5mm圆锥孔加工方式:
钻→精铰
钻孔:
φ4.8mm;
精铰:
φ5.5H7mm。
(五)确定各工序切削用量及基本工时
a)工序Ⅰ:
粗铣φ45mm圆柱大端面
机床:
X51立式铣床
刀具:
高速钢端铣刀,直径D=50mm,齿数Z=6
根据《加工工艺手册》表2.4-73,取每齿进给量f=0.15mm/Z,根据《切削工艺手册》表3.9,取铣削速度
=20m/min。
则车床主轴转速
=127.4r/min
按机床选取铣刀转数
=160r/min,则实际切削速度
=25.12m/min.
工作台每分钟进给量f=144mm/min,
铣床工作台进给量f=150mm/min,
按《加工工艺手册》表6.2-5,
基本工时t=0.65min。
b)工序Ⅱ:
半精铣φ45mm圆柱小端面
机床:
X51立式铣
刀具:
高速钢端铣刀,直径D=50mm,齿数Z=6
(1)粗铣φ45mm小端面
铣削余量Z=1.2mm,
同样查表选取确定切削速度
=20m/min,进给量f=0.15mm/Z,则车床主轴转速
=127.4r/min,
同样选取机床铣刀转数
=160r/min,则实际切削速度
=25.12m/min.,工作台每分钟进给量f=144mm/min,铣床工作台进给量f=150mm/min
则基本工时间t=0.43min。
(2)半精铣φ45mm小端面
加工余量Z=1.0mm,
同样查表确定切削速度
=20m/min,进给量f=0.15mm/Z,则车床主轴转速
=127.4r/min,
同样选取机床铣刀转数
=160r/min,则实际切削速度
=25.12m/min.,工作台每分钟进给量f=144mm/min,铣床工作台进给量f=100mm/min,
则基本工时t=0.65min。
c)工序Ⅲ:
钻,扩,铰φ25H8mm孔
机床:
Z535立式钻床
(1)钻孔φ23mm
刀具:
高速钢锥柄标准麻花钻,D=23mm。
根据《切削工艺手册》表2.7,取麻花钻每转进给量f=0.43mm/r,根据表2.15,取V=15m/min,则主轴转速n=208r/min,
按机床选取主轴转速n=195r/min,则实际切削V=14.08m/min.,
则基本工时t=0.64min。
(2)扩孔φ24.8mm
刀具:
高速钢锥柄标准麻花钻,D=24.8mm
双边余量2Z=1.8mm
由《切削工艺手册》表2.10查的扩孔钻扩孔时进给量f=0.7~0.8mm/r,并由《加工工艺手册》表4.2-16取f=0.72mm/r,扩孔钻扩孔时,根据《切削工艺手册》表2.15查得切削速度v=14m/min,故v=7~4.7m/min,则主轴转速n=89~60r/min,
按机床选取主轴转速n=68r/min,则切削速度v=5.29m/min.,
则基本工时t=1.1min。
(3)铰φ25H8mm孔
刀具:
高速钢锥柄机用铰刀,D=25mm
由《切削工艺手册》表2.24查得f=1.0~1.5mm/r,并由《加工工艺手册》表4.2-16选取进给量f=1.22mm/r,取切削深度h=0.15~0.25mm,切削速度v=4~8m/min,则主轴转速度n=51~102r/min,
按机床选取则主轴转速n=68r/min,则切削速度v=5.34m/min.,
则基本工时t=0.65min。
d)工序Ⅳ:
钻,铰φ10H7孔
机床:
Z535立式钻床
(1)钻φ9.8mm孔
刀具:
高速钢锥柄麻花钻,D=9.8mm
由《切削工艺手册》表2.7查得f=0.17mm/r,由表2.15取切削速度v=23m/min,则主轴转速n=747.4r/min
按机床选取主轴转速n=960r/min,则切削速度v=29.54m/min.,
则基本工时t=0.31min。
(2)粗铰φ9.96mm孔
刀具:
高速钢锥柄机用铰刀,D=9.96mm
由《切削工艺手册》表2.24查得f=0.17mm/r,根据表2.15取切削速度v=6m/min,则主轴转速n=191.85r/min
按机床选取主轴转速n=195r/min,则切削速度v=6.1m/min.,
则基本工时t=0.19min。
(3)精铰φ10H7孔
刀具:
高速钢锥柄机用铰刀,D=10mm
由《切削工艺手册》表2.24查得f=0.8mm/r,根据表2.15取切削速度v=6m/min,则主轴转速n=191.85r/min,
按机床选取主轴转速n=195r/min,则切削速度v=6.1m/min.
则基本工时t=0.31min。
工序Ⅴ:
粗铣φ14mm孔端面
机床:
X51立式铣床
刀具:
高速钢端铣刀,D=30mm,Z=6
根据《加工工艺手册》表2.4-73,取f=0.15mm/Z,根据《切削工艺手册》表3.9,取切削速度v=20m/min,则主轴转速n=212.3r/min,
按机床选取主轴转速n=220r/min,则切削速度v=20.72m/min.,工作台进给量f=198mm/min,取f=150mm/min,
则基本工时t=0.33min
e)工序Ⅵ:
钻,铰φ14H7mm孔
机床:
Z535立式钻床
(1)钻孔φ13mm
刀具:
高速钢锥柄麻花钻,D=13mm
由《切削工艺手册》表2.7查得f=0.36mm/r,由表2.15取切削速度v=14