冷冲压模具设计毕业论文.docx
《冷冲压模具设计毕业论文.docx》由会员分享,可在线阅读,更多相关《冷冲压模具设计毕业论文.docx(27页珍藏版)》请在冰豆网上搜索。
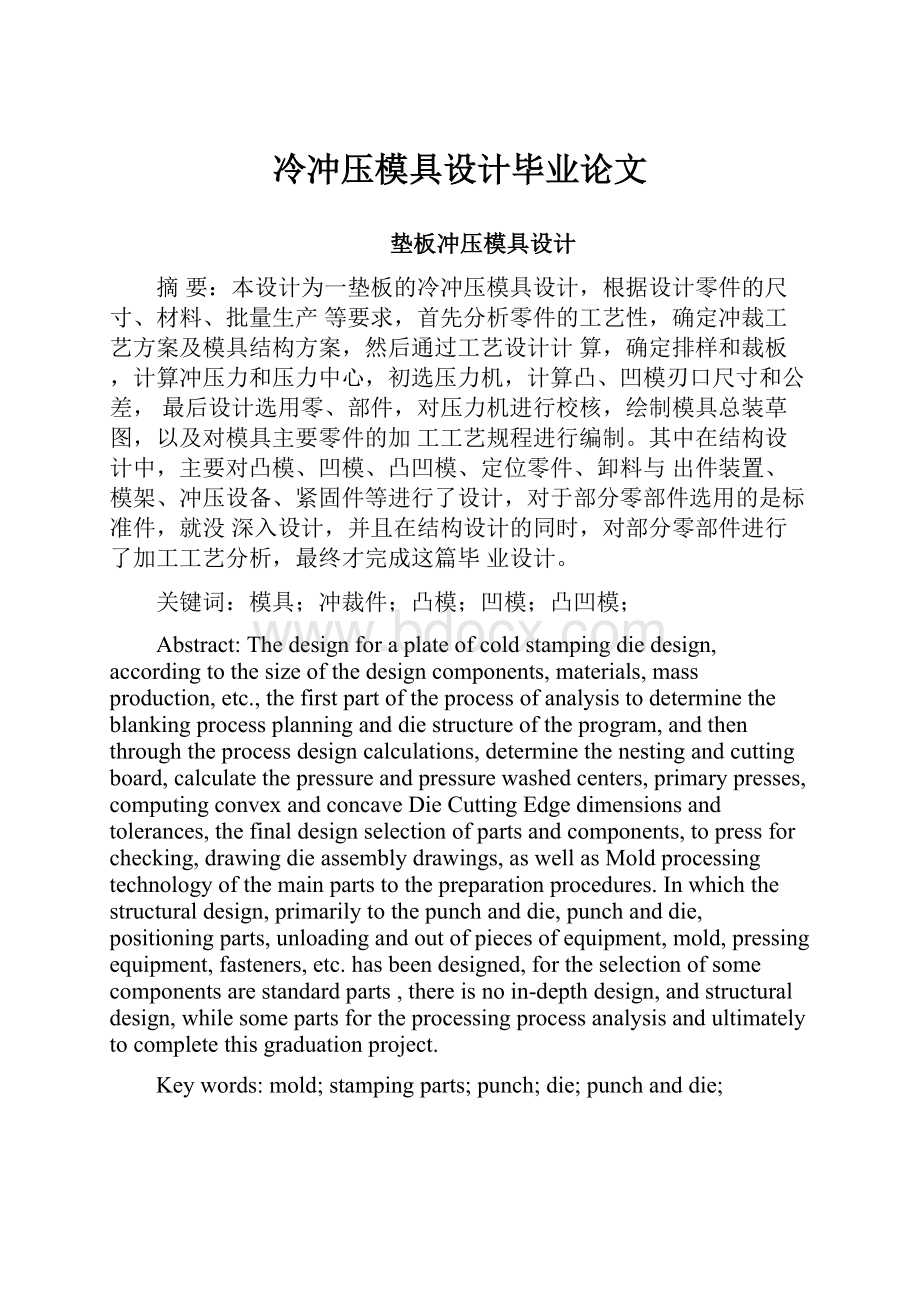
冷冲压模具设计毕业论文
垫板冲压模具设计
摘要:
本设计为一垫板的冷冲压模具设计,根据设计零件的尺寸、材料、批量生产等要求,首先分析零件的工艺性,确定冲裁工艺方案及模具结构方案,然后通过工艺设计计算,确定排样和裁板,计算冲压力和压力中心,初选压力机,计算凸、凹模刃口尺寸和公差,最后设计选用零、部件,对压力机进行校核,绘制模具总装草图,以及对模具主要零件的加工工艺规程进行编制。
其中在结构设计中,主要对凸模、凹模、凸凹模、定位零件、卸料与出件装置、模架、冲压设备、紧固件等进行了设计,对于部分零部件选用的是标准件,就没深入设计,并且在结构设计的同时,对部分零部件进行了加工工艺分析,最终才完成这篇毕业设计。
关键词:
模具;冲裁件;凸模;凹模;凸凹模;
Abstract:
Thedesignforaplateofcoldstampingdiedesign,accordingtothesizeofthedesigncomponents,materials,massproduction,etc.,thefirstpartoftheprocessofanalysistodeterminetheblankingprocessplanninganddiestructureoftheprogram,andthenthroughtheprocessdesigncalculations,determinethenestingandcuttingboard,calculatethepressureandpressurewashedcenters,primarypresses,computingconvexandconcaveDieCuttingEdgedimensionsandtolerances,thefinaldesignselectionofpartsandcomponents,topressforchecking,drawingdieassemblydrawings,aswellasMoldprocessingtechnologyofthemainpartstothepreparationprocedures.Inwhichthestructuraldesign,primarilytothepunchanddie,punchanddie,positioningparts,unloadingandoutofpiecesofequipment,mold,pressingequipment,fasteners,etc.hasbeendesigned,fortheselectionofsomecomponentsarestandardparts,thereisnoin-depthdesign,andstructuraldesign,whilesomepartsfortheprocessingprocessanalysisandultimatelytocompletethisgraduationproject.
Keywords:
mold;stampingparts;punch;die;punchanddie;
1前言
冲压是利用安装在冲压设备(主要是压力机)上的模具对材料施加压力,使其产生分离或塑性变形,从而获得所需零件(俗称冲压或冲压件)的一种压力加工方法。
冲压通常是在常温下对材料进行变形加工,且主要采用板料来加工成所需零件,所以也叫冷冲压或板料冲压。
冲压是材料压力加工或塑性加工的主要方法之一,隶属于材料成型工程。
冲压所使用的模具称为冲压模具,简称冲模。
冲模是将材料(金属或非金属)批量加工成所需冲件的专用工具。
冲模在冲压中至关重要,没有符合要求的冲模,批量冲压生产就难以进行;没有先进的冲模,先进的冲压工艺就无法实现。
冲压工艺与模具、冲压设备和冲压材料构成冲压加工的三要素,只有它们相互结合才能得出冲压件。
与机械加工及塑性加工的其它方法相比,冲压加工无论在技术方面还是经济方面都具有许多独特的优点。
主要表现如下。
(1)冲压加工的生产效率高,且操作方便,易于实现机械化与自动化。
(2)冲压时由于模具保证了冲压件的尺寸与形状精度,且一般不破坏冲压件的表面质量,而模具的寿命一般较长,所以冲压的质量稳定,互换性好,具有“一模一样”的特征。
(3)冲压可加工出尺寸范围较大、形状较复杂的零件,如小到钟表的秒表,大到汽车纵梁、覆盖件等,加上冲压时材料的冷变形硬化效应,冲压的强度和刚度均较高。
(4)冲压一般没有切屑碎料生成,材料的消耗较少,且不需其它加热设备,因而是一种省料,节能的加工方法,冲压件的成本较低。
由于冲压加工的零件种类繁多,各类零件的形状、尺寸和精度要求又各不相同,因而生产中采用的冲压工艺方法也是多种多样的。
概括起来,可分为分离工序和成形工序两大类;分离工序是指使坯料沿一定的轮廓线分离而获得一定形状、尺寸和断面质量的冲压(俗称冲裁件)的工序;成形工序是指使坯料在不破裂的条件下产生塑性变形而获得一定形状和尺寸的冲压件的工序。
上述两类工序,按基本变形方式不同又可分为冲裁、弯曲、拉深和成形四种基本工序,每种基本工序还包含有多种单一工序。
在实际生产中,当冲压件的生产批量较大、尺寸较少而公差要求较小时,若用分散的单一工序来冲压是不经济甚至难于达到要求。
这时在工艺上多采用集中的方案,即把两种或两种以上的单一工序集中在一副模具内完成,称为组合的方法不同,又可将其分为复合-级进和复合-级进三种组合方式。
复合冲压——在压力机的一次工作行程中,在模具的同一工位上同时完成两种或两种以上不同单一工序的一种组合方法式。
级进冲压——在压力机上的一次工作行程中,按照一定的顺序在同一模具的不同工位上完成两种或两种以上不同单一工序的一种组合方式。
复合-级进——在一副冲模上包含复合和级进两种方式的组合工序。
冲模的结构类型也很多。
通常按工序性质可分为冲裁模、弯曲模、拉深模和成形模等;按工序的组合方式可分为单工序模、复合模和级进模等。
但不论何种类型的冲模,都可看成是由上模和下模两部分
组成,上模被固定在压力机工作台或垫板上,是冲模的固定部分。
工作时,坯料在下模面上通过定位零件定位,压力机滑块带动上模下压,在模具工作零件(即凸模、凹模)的作用下坯料便产生分离或塑性变形,从而获得所需形状与尺寸的冲件。
上模回升时,模具的卸料与出件装置将冲件或废料从凸、凹模上卸下或推、顶出来,以便进行下一次冲压循环。
此设计针对所给的零件进行了一套冷冲压模具的设计,其中设计内容为分析零件的冲裁工艺性(材料、工件结构形状、尺寸精度),拟定零件的冲压工艺方案及模具结构,排样,裁板,计算冲压工序压力,选用压力机及确定压力中心,计算凸凹模刃口尺寸,主要零、部件的结构设计和加工工艺编制,压力机的校核。
冲裁模设计题目
如图1所示零件:
垫扳
生产批量:
大批量
材料:
08Ft=2mm设计该零件的冲压工艺与模具
2零件的工艺分析
2.1结构与尺寸
该零件结构简单,形状对称。
硬钢材料被自由凸模冲圆形孔,查《冷冲压工艺及模具设计》表3-8,可知该工件冲孔的最小尺寸为1.3t,该工件的孔径为:
Φ6>1.3t=1.3×2=2.6。
由于该冲裁件的冲孔边缘与工件的外形的边缘不平行,故最小孔边距不应小于材料厚度t,该工件的空边距(20)>t=2,(10)>t=2,均适宜于冲裁加工。
2.2精度
零件内、外形尺寸均未标注公差,属自由尺寸,可按IT14级确定工件尺寸的公差,经查表得,各尺寸公差分别为:
0000
零件外形:
580,38-0.62,30-0.52,16-0.43,8-0.36
+0.30
零件内形:
60孔心距:
18±0.215,利用普通冲裁方式可以达到零件图样要求。
2.3材料
08F,属于碳素结构钢,查《冷冲压工艺及模具设计》附表1可知抗剪强度τ=260MPa,断后伸长率=32%。
此材料具有良好的塑性和较高的弹性,其冲裁加工性能好。
根据以上分析,该零件的工艺性较好,可以进行冲裁加工。
3确定冲裁工艺方案
该零件包括落料、冲孔两个基本工序,可以采用以下几种工艺方案:
(a)先落料,再冲孔,采用单工序模生产;
(b)采用落料——冲孔复合冲压,采用复合模生产;
(c)用冲孔——落料连续冲压,采用级进模生产。
方案(a)模具结构简单,但需要两道工序,两套模具才能完成零件的加工,生产效率低,难以满足零件大批量生产的要求。
由于零件结构简单,为了提高生产效率,主要采用复合冲裁或级进冲裁方式。
采用复合冲裁时,冲出的零件精度和平直度好,生产效率高,操作方便,通过设计合理的模具结构和排样方案可以达到较好的零件质量。
根据以上分析,该零件采用复合冲裁工艺方案。
4确定模具总体结构方案
4.1模具类型根据零件的冲裁工艺方案,采用复合冲裁模。
复合模的主要结构特点是存在有双重作用的结构零件——凸凹模,凸凹模装在下模称为倒装式复合模。
采用倒装式复合模省去了顶出装置,结构简单,便于操作,因此采用倒装式复合冲裁模。
4.2操作与定位方式虽然零件的生产批量较大,但合理安排生产,可用手工送料方式能够达到批量要求,且能降低模具成本,因此采用手工送料方式。
考虑到零件尺寸大小,材料厚度,为了便于操作和保证零件的精度,宜采用导料板导向,固定挡料销挡料,并与导正销配合使用以保证送料位置的准确性,进而保证零件精度。
为了保证首件冲裁的正确定距,采用始用挡料销,采用使用挡料销的目的是为了提高材料利用率。
4.3卸料与出件方式采用弹性卸料的方式卸料,弹性卸料装配依靠橡皮的弹力来卸料,卸料力不大,但冲压时可兼起压料作用,可以保证冲裁件表面的平面度。
为了方便操作,提高零件生产率,冲件和废料采用由凸模直接从凹模洞口推下的下出件方式。
4.4模架类型及精度
考虑到送料与操作的方便性,模架采用后侧式导柱的模架,用导柱导套导向。
由于零件精度要求不是很高,但冲裁间隙较小,因此采用I级模架精度。
4.5凸模设计凸模的结构形式与固定方法:
落料凸模刃口部分为非圆形,为便于凸模与固定板的加工,可设计成固定台阶式,中间台阶和凸模固定板以H7/m6过渡配合,凸模顶端的最大台阶是用其台肩挡住凸模,在卸料时不至于凸模固定板中拉出。
并将安装部分设计成便于加工的长圆形,通过接方式与凸模固定板固定。
5工艺设计计算
5.1
排样设计与计算零件外形近似矩形,轮廓尺寸为58×30。
考虑操作方便并为了保证零件精度,采用直排有废料排样。
如图1所示:
查《冷冲压工艺及模具设计》表3-13,工件的搭边值a=2,沿边的搭边值a1=2.2。
级进模送料步距为S=30+2=32mm
条料宽度按表3-14中公式计算:
B-0△=(Dmax+2a1)-△0查表3-15得:
△=0.6
B=(58+2×2.2)0=62.40(㎜)
由零件图近似算得一个零件的面积为1354.8㎜2,一个进距内的坏料面积B×S=62.4×32=1996.8㎜2。
因此一个进距内的材料利用率为:
=(A/BS)×100﹪=67.8﹪
查《冷冲压工艺及模具设计》附表3选用板料规格为710×2000×2。
采用横裁时,剪切条料尺寸为62.4。
一块板可裁的条料为32,每间条可冲零件个数22个零件。
则一块板材的材料利用率为:
=(n×A0/A)×100﹪
=(22×32×1354.8/710×2000)×100﹪=67.2﹪采用纵裁时,剪切条料尺寸为62.4。
一块板可裁的条料为11,每条可冲零件个数62个零件,则一块板材的材料利用率为:
=(n×A0/A)×100﹪
=(11×62×1354.8/710×2000)×100﹪=59.2﹪根据以上分析,横裁时比纵裁时的板材的材料利用率高,因此采用横裁。
5.2计算冲压力与压力中心,初选压力机
冲裁力:
根据零件图可算得一个零件外周边长度:
L1=16π+8+28+38×2
=162.27
内周边长度之和:
L=2π×3=18.84㎜查《冷冲压工艺及模具设计》附表1可知:
=260MPa;查《冷冲压工艺及模具设计》附表3可知:
Kx=0.05,KT=0.055.落料力:
F落=KL1tT
=1.3×162.27×2×260
=109.69KN冲孔力:
F孔=KL2tT
=1.3×6×2×260
=12.74
KN
卸料力:
Fx=KxF落
=0.05×109.69
=5.48KN
推件力:
根据材料厚度取凹模刃口直壁高度h=6,
故:
n=h/t=3
FT=nKtF孔=3×0.055×25.47
=4.20KN
总冲压力:
FЁ=F落+F孔+Fx+FT
则FЁ=109.69+12.74+5.48+4.20
=132.11KN
应选取的压力机公称压力:
25t.因此可初选压力机型号为J23-25。
当模具结构及尺寸确定之后,可对压力机的闭合高度,模具安装尺寸进行校核,从而最终确定压力机的规格。
确定压力中心:
画出凹模刃口,建立如图所示的坐标系:
由图可知,该形状关于X轴上下对称,关于Y轴左右对称,则压力中心为该图形的几何中心。
即坐标原点O。
该点坐标为(0,0)。
5.3计算凸、凹模刃口尺寸及公差由于模具间隙较小,固凸、凹模采用配作加工为宜,由于凸、凹模之间存在着间隙,使落下的料或冲出的孔都带有锥度。
落料件的尺寸接近于凹模刃口尺寸,而冲孔件的尺寸接近于凸模刃口尺寸。
固计算凸模与凹模刃口尺寸时,应按落料与冲孔两种情况分别进行。
由此,在确定模具刃口尺寸及其制造公差时,需遵循以下原则:
(I)落料时以凹模尺寸为基准,即先确定凹模刃口尺寸;考虑到凹模刃口尺寸在使用过程中因磨损而增大,固落料件的基本尺寸应取工件尺寸公差范围较小尺寸,而落料凸模的基本尺寸则按凹模基本尺寸减最小初始间隙;
(II)冲孔时以凸模尺寸为基准,即先确定凸模刃口尺寸,考虑到凸模尺寸在使用过程中因磨损而减小,固冲孔件的基本尺寸应取工件尺寸公差范围内的较大尺寸,而冲孔凹模的基本尺寸则按凸模基本尺寸加最小初始间隙;
(III)凸模与凹模的制造公差,根据工件的要求而定,一般取比工件精度高2~3级的精度,考虑到凹模比凸模的加工稍难,凹模比凸模低一级。
a):
落料凹模刃口尺寸。
按磨损情况分类计算:
i)凹模磨损后增大的尺寸,按《冷冲压工艺及模具设计》公式:
DA=(Dmax-X
△);计算,取δA=△/4,制件精度为IT14级,故X=0.5
580:
DA1=(58-0.5×0.74)+0.185=57.63+0.185(㎜)
0
38-0.62:
DA2=(38-0.5×0.62)+0.155=37.69+0.155(㎜)
0
30-0.52:
DA3=(30-0.5×0.52)+0.13=29.74+0.13(㎜)
0
16-0.43:
DA4=(16-0.5×0.43)+0.1075=15.785+0.1075(㎜)
0
8-0.36:
DA5=(8-0.5×0.36)+0.09=7.18+0.09(㎜)
ii)凹模磨损后不变的尺寸,按《冷冲压工艺及模具设计》公式:
CA=(Cmin+X
△)±0.5δA:
计算,取δA=△/4,制件精度为IT14级,故X=0.518±0.215:
Cd1=(17.785+0.5×0.43)±0.43/8=18±0.05375(㎜)
冲裁间隙影响冲裁件质量,在正常冲裁情况下,间隙对冲裁力的影响并不大,
但间隙对卸力、推件力的影响却较大。
间隙是影响模具寿命的主要因素。
间隙的大小则直接影响到摩擦的大小,在满足冲裁件质量的前提下,间隙一般取偏大值,这样可以降低冲裁力和提高模具寿命。
查《冷冲压工艺及模具设计》表3-3可知Zmax=0.360㎜,Zmin=0.246㎜相应凸模按凹模实际尺寸配作,保证最小合理间隙为0.246mm冲孔凸模刃口尺寸。
冲孔凸模为圆形,可按《冷冲压工艺及模具设计》公式dT=(dmin+x△)0-计算,取δT=△/4,制件精度为IT14级,故X=0.5
+0.30
120:
dT1=(6+0.5×0.30)0=6.150
6设计选用零件、部件,绘制模具总装草图
6.1凹模设计
凹模的结构形式和固定方法:
凹模采用矩形板状结构和通过用螺钉、销钉固定在凹模固定板内,其螺钉与销钉与凹模孔壁间距不能太小否则会影响模具强度和寿命,其值可查《冷冲压工艺及模具设计》表3-23。
凹模刃口的结构形式:
因冲件的批量较大,考虑凹模有磨损和保证冲件的质量,凹模刃口采用直刃壁结构,刃壁高度取6mm,漏料部分沿刃口轮廓单边扩大0.5mm
凹模轮廓尺寸的确定:
查《冷冲压工艺及模具设计》表3-24,得:
K=0.28;
查《冷冲压工艺及模具设计》表3-25,得:
s2=36;
凹模厚度H=ks=0.28×58=16.24(㎜)
B=s+(2.5~4.0)H
=58+(2.5~4.0)×16.24
=98.6~122.96(㎜)
L=s1+2s2
=30+2×36
=102(㎜)
根据算得的凹模轮廓尺寸,选取与计算值相接近的标准凹模板轮廓尺寸为L×B×H=125×125×28.5(㎜)
凹模材料和技术要求:
凹模的材料选用T10A。
工件部分淬硬至HRC58~62。
外轮廓棱角要倒钝。
如图2所示:
其余
图2落料凹模
6.2凸模设计
6.2.1凸模的结构形式与固定方法冲孔部分的凸模刃口尺寸为圆形,为了便于凸模和固定板的加工,将冲孔凸模设计成台阶式。
为了保证强度、刚度及便于加工与装配,圆形凸模常做成圆滑过渡的阶梯形,小端圆柱部分。
是具有锋利刃口的工作部分,中间圆柱部分是安装部分,它与固定板按H7/m6配合,尾部台肩是为了保证卸料时凸模不致被拉出,圆形凸模采用台肩式固定。
6.2.2凸模长度计算
凸模的长度是依据模具结构而定的。
采用弹性卸料时,凸模长度按公式L=h1+h2+h3计算,
式中L---凸模长度,mm;
h1---凸模固定板厚度,mm;
h2卸料板厚度,mm;
h3卸料弹性元件被预压后的厚度
L=22mm+10mm+18.5mm
=50.5mm
6.2.3凸模的强度与刚度校核一般情况下,凸模强度与刚度足够,由于凸模的截面尺寸较为积适中,估计强度足够,只需对刚度进行校核。
对冲孔凸模进行刚度校核:
凸模的最大自由长度不超过下式:
有导向的凸模Lmax≤1200,其中对于圆形凸模Imin=∏d4/64
则Lmax≤12001.312264260=24.00mm由此可知:
冲孔部分凸模工作长度不能超过24.00mm,根据冲孔标准中的凸
模长度系列,选取凸模的长度:
50.5
6.2.4凸模材料和技术条件
凸模材料采用碳素工具钢T10A,凸模工作端(即刃口)淬硬至HRC56~60,凸模尾端淬火后,硬度为HRC43~48为宜。
如图3所示:
2.刃口淬硬至56~60HRC,尾端淬硬至43~48HRC.
图3冲孔凸模
6.3凸凹模的设计
6.3.1凸凹模的结构形式与固定方法
凸凹模的结构简图如图4所示:
技术要求:
1.上下面无毛刺,平行度为0.02.
2.材料为T10A,热处理56-60HRC.
3.带*号的尺寸按凹模实际尺寸配作,保证Zmin=0.246.
4.带**号的尺寸按凸模实际尺寸配作,
保证Zmin=0.246.
图4凸凹模
凸凹模与凸凹模固定板的采用H7/m6配合。
6.3.2校核凸凹模的强度冲孔边缘与工件外开边缘不平行时,凸凹模的最小壁厚不应小于材料厚度
t=2mm,而实际最小壁厚为5mm,故符合强度要求。
6.3.3凸凹模尺寸的确定
凸凹模的外刃口尺寸按凹模尺寸配作并保证最小间隙为Zmin=0.246mm,内形刃口尺寸按凸模尺寸配做并保证最小间隙为Zmin=0.246mm。
6.3.4凸凹模材料和技术条件凸凹模材料采用碳素工具钢T10A,淬硬至56~60HRC。
6.4定位零件定位零件的作用是使坯料或工序件在模具上相对凸、凹模有正确的位置。
选用固定挡料销一个。
挡料销的作用是挡住条料搭边或冲件轮廓以限定条料送进的距离,固定挡料销固定在位于下模的凸凹模上,规格为GB/T7694.10-94,材料45号钢,硬度为43~48HRC
选用导料销两个。
导料销的作用是保证条料沿正确的方向送进,位于条料的后侧(条料从右向左送进)尺寸规格为6X2,如图5所示:
图5导料销
6.5卸料与出件装置出件方式是采用凸模直接顶出的下出料方式。
由于卸料采用弹性卸料的方式,弹性卸料装置由卸料板、卸料螺钉和弹性元件组成。
卸料板:
弹性卸料板的平面尺寸等于或稍大于凹模板的尺寸,厚度取凹模厚度的0.6~0.8倍,卸料板与凸模的单边间隙按《冷冲压工艺及模具设计》表3-32选取,t>1mm时,单边间隙为0.15mm。
为了便于可靠卸料,在模具开启状态时,卸料板工作平面应高出凸模刃口尺寸端面0.3~0.5,卸料板的尺寸规格为:
125mmX125mmX10mm,材料为:
45#钢。
如图6所示:
卸料螺钉:
卸料螺钉采用标准的阶梯形螺钉,根据卸料板的尺寸选择4个卸料螺钉,规格为,JB/T7650.5-94。
如图7所示:
卸料装置:
由于橡皮允许承受的负荷较大,安装调整方便,因此选用橡皮作为弹性元件,卸料橡皮的选择原则:
为了保证卸料正常工作,应使橡皮工作时的弹力大于或等于卸料力FX
FXY=AP≥FX=5.48KN
式中FXY—橡皮工作时的弹力,A—橡皮的横截面积,P—与橡橡皮压缩量有关的单位压力,一般预压时压缩量为10%~15%。
由《冷冲压工艺及模具设计》图3-64知,取P=0.6MPa,求得A=91.3cm2,由《冷冲压工艺及模具设计》表3-33中的公式求得橡皮尺寸规格为35×26×24
根据工件材料厚度为2mm,冲裁时凸模进如凹模的深度为1mm,模具维修时刃磨留量为2mm,开启时卸料板高于凸模1mm,则求得总工作行程:
h工件=6mm,
使用橡皮时,不应使最大压缩量超过橡皮自由高度的35%~45%否则是皮的自由高度应为:
H=h/(0.25~0.30)
=6/(0.25~0.30)
=20~24mm
模具组装时的预压缩量为:
H预=(10%~15%)H
=2.4~3.6mm
取H预=3mm由此可知:
安装橡皮高度尺寸为21mm,式中的H———所需的工作行程。
由上式所得的