双相钢DP600的显微组织和性能.docx
《双相钢DP600的显微组织和性能.docx》由会员分享,可在线阅读,更多相关《双相钢DP600的显微组织和性能.docx(18页珍藏版)》请在冰豆网上搜索。
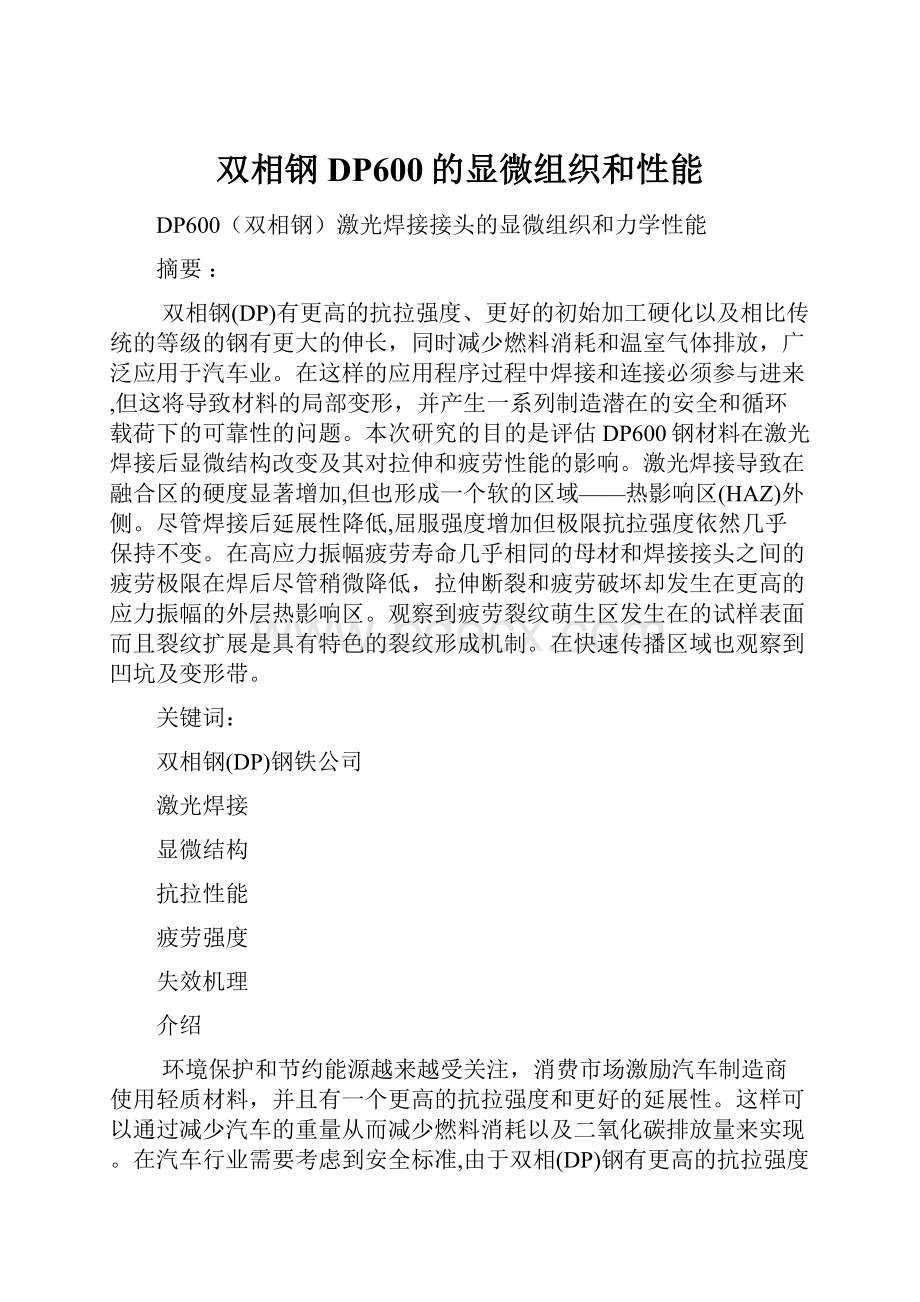
双相钢DP600的显微组织和性能
DP600(双相钢)激光焊接接头的显微组织和力学性能
摘要:
双相钢(DP)有更高的抗拉强度、更好的初始加工硬化以及相比传统的等级的钢有更大的伸长,同时减少燃料消耗和温室气体排放,广泛应用于汽车业。
在这样的应用程序过程中焊接和连接必须参与进来,但这将导致材料的局部变形,并产生一系列制造潜在的安全和循环载荷下的可靠性的问题。
本次研究的目的是评估DP600钢材料在激光焊接后显微结构改变及其对拉伸和疲劳性能的影响。
激光焊接导致在融合区的硬度显著增加,但也形成一个软的区域——热影响区(HAZ)外侧。
尽管焊接后延展性降低,屈服强度增加但极限抗拉强度依然几乎保持不变。
在高应力振幅疲劳寿命几乎相同的母材和焊接接头之间的疲劳极限在焊后尽管稍微降低,拉伸断裂和疲劳破坏却发生在更高的应力振幅的外层热影响区。
观察到疲劳裂纹萌生区发生在的试样表面而且裂纹扩展是具有特色的裂纹形成机制。
在快速传播区域也观察到凹坑及变形带。
关键词:
双相钢(DP)钢铁公司
激光焊接
显微结构
抗拉性能
疲劳强度
失效机理
介绍
环境保护和节约能源越来越受关注,消费市场激励汽车制造商使用轻质材料,并且有一个更高的抗拉强度和更好的延展性。
这样可以通过减少汽车的重量从而减少燃料消耗以及二氧化碳排放量来实现。
在汽车行业需要考虑到安全标准,由于双相(DP)钢有更高的抗拉强度结合高伸长率,比类似的屈服强度钢的更好的成绩,从而获得了很好的口碑。
双相钢的显微组织的基体是具有良好塑性和韧性的铁素体,并且由马氏体相和可能存在的贝氏体相与极少数的残余奥氏体[2-6]结合从而加强了硬度。
钢的延展性源自铁氧体,强度源自于马氏体。
而高强度低合金钢(低合金高强度钢)、双相钢显示出较低的屈服强度但连续移动检测中双相钢的结果有较大且更加统一的总伸长和更高的初始加工硬化率,伴随着相当高的极限抗拉强度,所有这些令人满意的机械特性使双相(DP)钢引起了汽车的制造商的兴趣。
人们常说超过一个国家的国内生产总值50%的产品与焊接存在这样或那样的关联,就车身结构来说焊接是主要的操作过程。
在以前的车身设计中,最典型的材料是低碳钢,这些汽车部件通过电阻点焊(RSW)组装,来的实现汽车制造商的需求过程中高速度和高产量的场景。
但由于改变材料的方案,行业中其他焊接方法也越来越流行了。
其中易于自动化和灵活性的激光焊接在金属链接已经获得了名气。
由于焊接DP钢加入了其他焊接过程,如电阻点焊(RSW)[11]、激光点焊[12]、气体金属电弧焊接(GMAW)[13],搅拌摩擦焊[14]。
所以必须分析它的机械性能。
在双相钢的激光焊接性已经做了部分研究,例如:
钢的拉伸性能的焊接效果和非常有限的疲劳性能的研究。
在应用程序的结构激光焊接接头在循环荷载下的条件是容易失效,因此表征焊接接头的抗疲劳强度是必要的。
先前的研究表明在DP钢焊接导致了在热影响区域(HAZ)外侧形成软带,焊接接头的机械性能在这个地区有显著影响(17、18)。
通过形成这种软化区(17-20)焊接接头的拉伸性能和成形性的严重受阻。
在这个研究进行了拉伸试验也得到这样的结果。
然后问题在于软带是否将会导致还原抗疲劳强度。
详细研究表明关于疲劳性能的影响,以及软带的失效的行为是双相钢焊接接头不足之处。
一个全面的研究发现:
为有效应用DP钢,了解他们的断裂特点和机制在两个单调和循环负载是至关重要的。
因此,本研究的目的是在评估在两个单调和交变载荷强调失效的DP钢激光焊接接头的机制的力学性能。
2材料和实验过程
2.1材料
这个DP600钢拥有一个1.2毫米厚度与镀锌扩散(GA)涂层(46克/平方米顶部和47g/m2在底部)选择适当的区域研究。
母材的化学成分金属是表1中给出。
表格1
在目前的研究选定的DP600钢中的化学成分(wt%)
C
Mn
Si
Al
Mo
Cr
Cu
S
0.09
1.84
0.36
0.05
0.01
0.02
0.03
0.005
2.2激光焊接
激光焊接是通过使用一个二极管激光器,在目前的研究中焊接使用的参数如表2所示。
这个型号为NuvonyxISL4000L二极管激光器头部被安装在松下VR6机器人手臂处。
光束矩形尺寸为12毫米×0.9毫米,焦距为90mm。
同时,由于二极管激光的功率密度导致其局限于焊接传导模式。
以一个流速14.2l/分钟的超高纯度氩作为保护气体在试样表面上焊接。
在金属模版上焊接形成一个熔透焊道,焊接速度为1米/分钟。
表格2
Lasermachine
Lasersource
Laserpower(kW)
Weldingspeed(m/min)
Focallength(cm)
Beamdimension(mm2)
NuvonyxISL-4000
Diode
4
1
9
12×0.9
2.3显微组织和显微硬度测试
母材为DP600钢在三个不同的方向被切割。
即在纵向、横向和短横方向。
然后这些标本是对金相镶嵌、研磨、抛光和有2%硝酸浸蚀液溶液腐蚀之后做成的。
再检查焊接试样横截面的显微结构。
一种结合Clemex图像分析系统光学显微镜被用来观察在焊缝的显微结构的变化。
未侵蚀样本进行了维氏显微硬度测试。
测试期间使用的负载为500gm,保压时间为15s。
所有的值都取的是三个方向系列试样的平均值。
用显微镜仔细观察这个融合区的中心,确定了焊缝的几何规格,所有的几何凹痕是充分地为了避免任何潜在的通过邻近的缺口应变场引起的影响。
图1:
用于目前的研究的拉伸和疲劳试验标本的几何形状和尺寸。
2.4抗拉试验
ASTM-E8M代替试样标本用于拉力测试。
拉伸试样的几何形状由图1中给出。
焊接样品的加工垂直于焊接方向。
所有的测试样本沿着加载方向的仪表测试是小幅度的晃动,最后定格的数字是600。
拉伸实验在室温下用一个完全自动万能拉力试验机。
目前的拉伸测试的应变率是0.01s−1,0.001s−−1,0.0001秒——1和0.00001s−1。
进行的测量应变测试是用一个长度为25毫米伸长计来测量的。
进行了在每个应变速率至少两个样品的测试。
来评测0.2%的补偿屈服强度,极限抗拉强度和韧性(百分比伸长)。
2.5疲劳试验和金相
疲劳研究采用是一个完全计算机化、在负载控制和在超过6应力振幅的8801电服液压测试系统。
那些拉伸试验样品在每个应力水平进行了两个或更多相同的几何形状和尺寸样品测试,应力比的
等于0.1。
所有的测试正弦波形、频率选择为50Hz。
疲劳试验后的母材和焊接接头通过JSM-6380-lv扫描电子显微镜配备牛津能量色散x射线光谱学系统和3d显微镜观察的分析检查,来确定疲劳裂纹萌生部位和传播机制。
3结果与讨论
3.1显微硬度配置文件及显微组织变化
图2显示了DP600钢激光焊接接头微压痕硬度配置文件。
观察到在融合区(FZ)硬度值明显高于母材,大约1.5倍。
扫描电镜检查该阶段明显融合区(FZ)表明这个地区包括主要马氏体(M)结合一些侧板铁素体和贝氏体(图3(a))。
在融合区(FZ)形成的马氏体使得激光焊接过程中快速冷却的焊缝池在热影响区硬度值变化,由于马氏体的形成该熔化区附近有较高的硬度比该地区接近母材。
相似的结果在[21]提出了。
该区附近观察到具有比母材低的硬度值的金属外热影响区,称为软区在图2显示。
存在软带主要是由于预先存在的回火马氏体[3,18、19],在图3(b)可以看到,回火马氏体(TM)和贝氏体铁素体基体,再加上一些预先存在的残留奥氏体。
类似的结果也在其他等级的焊接DP钢(17、18、20]出现。
这种软区域会有激光焊接DP600钢关节力学性能的不利影响,这在后面的截面将会看到。
在母材观察几乎整个材料常数硬度值,对应母材的显微结构包含马氏体、铁素体基体加上一些残留奥氏体(图3(c))。
图2:
典型DP600钢激光焊接接头剖面的显微硬度
图3:
SEM显微图显示了一个DP600钢关节激光焊接的显微结构的变化,(a)融合区,(b)外热影响区(软带),(c)基本金属,在M,F,B,和TM分别代表马氏体、贝氏体铁素体、,回火马氏体。
图4.DP600钢在不同应变利率的工程应力-应变曲线测试,(a)母材(b)焊接接头
图5.DP600钢激光焊接接头拉伸测试样品的典型的故障位置
3.2拉伸性能
图4显示了母材和焊接接头的两个工程应力-应变曲线。
有意思的是发现DP600母材的应力-应变曲线是光滑的,并且所有的应变率(图4(a))是连续的,而焊接DP600关节在所有的应变率都显示屈服点现象,见图4(b)。
在外层HAZ所有焊接样本失败,在图5显示一个例子,垂直的线标志焊接。
在拉伸试验仔细观察表明,在软化区发生屈服现象,然后在那个区域(即。
在外面的热影响区)累积的是大部分塑性变形,直到最终失败。
焊接关节比母材有更高的屈服强度但焊接标本的拉伸强度,略低于母材(图6)。
尽管两屈服强度、极限抗拉强度略有增加而增加应变速率,就应变率而言(图7)延展性并没有表现出任何细微的改变。
然而进行了所有的拉伸试验样本韧性类型的断裂模式观察,焊接导致减少伸长率(图7)。
图6.DP600钢激光焊接接头在不同应变率的影响下的屈服强度和拉伸强度极限的测试.
在焊接样本存在屈服点现象可能是因为间质扩散,可能发生在激光焊接过程。
高温产生的激光把碳(或氮气)铁原子扩散到别的位置的能量略低于另一个真实的刃型位错的平面原子。
弹性交互如此强劲,杂质原子气团变得完全饱和并沿核心的位错凝聚成一排原子。
当这样一个示例与固定插入的位错(即在这项研究的焊接样品)被加载,启动位错运动需要更高的应力来开始的塑性变形。
结果,经过激光焊接的屈服强度变得更高,如图6所示。
位错线可能是在一个较低的压力挣脱了溶质原子的影响,发生滑移,表现出屈服点现象,见图4(b)。
这屈服点是负载下降之后发生的屈服,在文献[22-24]可以看到一些详细描述。
图7.DP600钢激光焊接接头在不同应变利率的影响延展性的测试。
焊接接头和母材在断裂表面特征上两个显示基本相似。
杯状凹地破裂是断口的主要特征,代表韧性类型断裂的模式。
图8可以看到典型的焊接断口SEM显微图的示例。
断裂表面的中心(图8(a))主要包含晶粒凹坑显示简单拉伸加载引起的典型的断裂。
这个接近边缘的断裂表面(图8(b))表现两个等轴和剪切凹坑的结合,因为它有一个的印象晶粒外表的等轴凹坑这种凹坑有一个细长的抛物线形。
这意味着这个地区随着拉伸载荷发生剪切运动。
图8.典型焊接接头在应变率为1×10−−3s1的拉伸测试试样断口SEM显微图表面(a)在中心和(b)表面附近。
3.3疲劳性能
控制负荷的疲劳试验表明,当焊接关节的疲劳极限比母材稍低,在高应力幅值观察到母材和焊接接头之间有几乎相同的疲劳寿命,见图9。
这个结果表明外热影响区轻微下降硬度(图2)在更高应力振幅下不是足够大来减少疲劳强度。
这是因为高应力振幅破坏了潜在的负面效应的软带。
这两类材料获得的疲劳极限和计算疲劳比如表3所示。
焊接接头的疲劳极限低于母材12.5%,然后一个疲劳率为0.28相比与0.32的母材得到了该焊接接头。
这个焊接样本的外热影响区出现隐含的负面效应软带使疲劳极限或疲劳比率轻微的减少,不能忽视在的疲劳极限区域附近降低压力振幅。
以下Basquin-type方程是用来符合疲劳数据,
是交变应力振幅,
是压力拦截在2N=1的疲劳强度系数。
N是疲劳破坏周期数,2N是逆向负载破坏系数,b是疲劳强度指数。
表4给出了母材的
和b的值和焊接样本。
这是看到焊接接头较高的疲劳强度系数,但疲劳强度指数的绝对值上升将会得到一个稍短疲劳寿命(因为一个小的b值对应一个更长疲劳寿命[24])。
结果,这是同样难以使用
和b的值来区分焊接接头和母材的疲劳寿命之间的区别,在图9证明了这一点。
图9.DP600钢母材和焊接接头进行的在R=0.1、50Hz、室温下的s-n曲线,那里的数据点箭头标志指样本跳动。
3.4疲劳断裂位置和机制
关于疲劳失效的位置,观察到所有焊接样本在一个高于250MPa压力振幅下在外热影响区失效,并且母材样品中的测量部分失效。
然而,在或低于250mpa的压力振幅下所有焊接样品和母材样品的失效远离中间测量部分。
这些结果符合良好,在焊接接头和母材的S-N曲线图中在一个压力振幅约250MPa存在一个转折点,如图9所示。
在焊接样品的缺陷位置可以看到应力幅值两个不同的测试范围如图10。
可能的原因和影响是循环强化机制涉及诱导马氏体转变[25、26、27]变形。
这个DP钢中的微观结构含有一种少量的残余奥氏体;在循环加载下残余奥氏体转化为马氏体从而给了钢额外的加固效果。
这些马氏体粒子被认为促使位错产生和主导循环变形[28]。
在更高的应力振幅下样品测试的LCF区域中位错可以克服马氏体的应力大小的障碍,即超过了由马氏体产生的阻力,在测试样本测量部分产生更多的累积损伤。
在母材和焊接接头两个上的缺陷部分出现的更高层次的应力幅值是这一现象产生的原因。
由于低硬度,焊接样品更具体疲劳失效发生在外层热影响区(图2)。
但在一个较低水平的压力振幅下HCF区域此现象持续了很长一段时间,应力不能与由克服混乱的马氏体的阻塞力相互作用。
由于潜在的应力集中导致的缺口效应使得测量部分附近区域成为最薄弱的地区。
通常,切口效应表明HCF区域相比LCF区域(29)较短的寿命来说更为长期。
图10.典型焊接样品的疲劳断裂位置的压力测试(a)幅度高于250MPa和(b)低于250MPa。
图11:
焊接接头典型的疲劳断口SEM显微图的进行了应力幅225MPa,(a)断裂表面处于低水平的总体视图放大,(b)放大的视图的虚线框(a)显示裂纹萌生区域和裂纹扩展区在中间放大,CP表示裂纹扩展区和箭头说明了裂纹扩展方向,(c)裂纹扩展面积在接近裂纹萌生区域放大,(d)裂纹扩展面积约2毫米的裂纹萌生区域在更高的放大和二次裂纹,(e)表面中心和边缘附近的断裂(f)表面断裂区
这个疲劳断裂表面的显微镜观察表明,裂纹萌生发生标本的表面。
在这母材和焊接接头两者之中,或低于250MPa显示应力幅值样品测试裂缝起始位点和裂纹扩展的断裂表面区域很明显。
一个典型的例子:
图11(a)显示断裂面的总体视图,所示测试样品的焊接应力幅值是在225MPa。
标本表面发生裂纹萌生(图11(b))。
表面晶粒通常比内部的晶粒有更少的压力,以便在试样表面靠近疲劳区域的几个晶粒发生滑动[30]可能相对更容易。
在可以产生刻凹痕或带钢单向皱纹的疲劳表面来回的滑移运动,也被称为作为入侵和挤出[24]。
这种切口与一个原子尺寸根的缺口充当了应力集中器和疲劳裂纹可能的核心[24]。
表面粗糙度和突出物还可以充当一个应力集中点,在此导致疲劳裂纹的萌生。
在表面可以看到疲劳裂纹扩展阶段,图11(b))。
疲劳裂纹II期裂纹扩展的主要特点是疲劳光条纹(图11(c)和(d)),它通常都是垂直的传播方向。
间隔的条纹标志着附近的小裂纹萌生区域反映对裂纹较慢扩展速率(图11(c)),而在随后增加条纹间距、裂纹扩展的阶段(图11(d))代表裂纹在前沿更快的传播。
疲劳光条纹的形成基本上是被认为是由于在塑性带重复塑性变钝刃磨过程中由于要么错位或成对滑动[31][32,33]形成疲劳裂纹。
在II期裂纹扩展观察二次裂纹,同时,见图11(d)。
在断口中心的更快的裂纹扩展的典型的韧性断裂模式主要特征是杯状波纹断裂,(图11(e))。
边缘断裂表面主要的特征是由于剪切运动的伸长的椭圆形的凹坑,(图11(f))显示最终的快速失败的示例。
母材和焊接样本两者都有基本相似断裂表面特征。
然而,在或低于一个应力幅250MPa样品测试显示一些变形带位于远离裂纹萌生的区域,如图12(a)和(b)所示。
主要是由于不均匀变形形成了变形带,从而引起在轧制钢板存在的晶体结构(34,35)。
进一步研究了DP600钢焊接接头的疲劳断裂纹理的影响机制是必要的。
图12:
焊接样品表面疲劳断裂测试压力振幅250MPa(a)两试样表面附近变形带,(b)一个放大了视图的方形区域(a)。
4.总结
1.由于焊接时快速冷却时导致在溶合区(FZ)形成大量的马氏体结构,导致一硬度增加相当大。
然而,由于预先存在的回火马氏体,在DP600钢外热影响区发现一个软带。
2.尽管在某种程度上热影响区(HAZ)外侧软化减少了延展性,激光焊接后极限抗拉强度几乎没有改变。
另一方面,DP600钢焊接接头相比母材具有更高的屈服强度和稍显屈服点现象,。
3.观察到依赖拉伸性能的应变速率是很弱,因为屈服强度、极限拉伸强度增加在母材和焊接关节仅略微增加应变率(从1×10−5s−1到1×10−2s−1)。
4.尽管焊接接头的疲劳极限和疲劳率略低于母材,母材和焊接接头存在的软带之间实验性的散播使得疲劳寿命和更高层次的应力振幅几乎相同的。
5.在所有焊接样品在不同应变利率测试情况下的拉伸断口发生在软区,但拉伸断裂表面仍然表现出凹坑、韧性断裂特性。
在在母材和焊接接头这两个试样表面观察到疲劳裂纹,断裂表面是以疲劳光条纹为特征。
在快速传播地区也观察到凹坑和一些变形带。
鸣谢
作者要感谢加拿大自然科学和工程研究委员会(NSERC),和汽车创新行动(安大略省卓越研究基金会)提供金融支持。
谢谢瑞尔森学校的研究生SGS奖学金。
也感激总理的杰出研究奖(PREA)、加拿大创新基金会(CFI),和瑞尔盛研究椅(RRC)项目的金融支持。
作者还想谢谢各位先生(A.Machin,Q.Li,j.Amankrah,d.奥斯特罗姆和r.Churaman)在实验中的帮助,S.D-Bhole教授提供有用的讨论。
个人总结
双相钢(DP)有更高的抗拉强度、更好的初始加工硬化以及相比传统的等级的钢有更大的伸长,同时减少燃料消耗和温室气体排放,广泛应用于汽车业。
本次研究的目的是评估DP600钢材料在激光焊接后显微结构改变及其对拉伸和疲劳性能的影响。
由于焊接DP钢加入了其他焊接过程,如电阻点焊(RSW)、激光点焊、气体金属电弧焊接(GMAW),搅拌摩擦焊。
所以必须分析它的机械性能。
在双相钢的激光焊接性已经做了部分研究,例如:
钢的拉伸性能的焊接效果和非常有限的疲劳性能的研究。
在应用程序的结构激光焊接接头在循环荷载下的条件是容易失效,因此表征焊接接头的抗疲劳强度是必要的。
先前的研究表明在DP钢焊接导致了在热影响区域(HAZ)外侧形成软带,焊接接头的机械性能在这个地区有显著影响。
通过形成这种软化区焊接接头的拉伸性能和成形性的严重受阻。
一个全面的研究发现:
为有效应用DP钢,了解他们的断裂特点和机制在两个单调和循环负载是至关重要的。
因此,本研究的目的是在评估在两个单调和交变载荷强调失效的DP钢激光焊接接头的机制的力学性能。
母材为DP600钢在三个不同的方向被切割。
即在纵向、横向和短横方向。
然后这些标本是对金相镶嵌、研磨、抛光和有2%硝酸浸蚀液溶液腐蚀之后做成的。
再检查焊接试样横截面的显微结构。
疲劳研究采用是一个完全计算机化、在负载控制和在超过6应力振幅的8801电服液压测试系统。
那些拉伸试验样品在每个应力水平进行了两个或更多相同的几何形状和尺寸样品测试,应力比的
等于0.1。
所有的测试正弦波形、频率选择为50Hz。
疲劳试验后的母材和焊接接头通过JSM-6380-lv扫描电子显微镜配备牛津能量色散x射线光谱学系统和3d显微镜观察的分析检查,来确定疲劳裂纹萌生部位和传播机制。
观察到在融合区(FZ)硬度值明显高于母材,大约1.5倍。
扫描电镜检查该阶段明显融合区(FZ)表明这个地区包括主要马氏体(M)结合一些侧板铁素体和贝氏体。
在融合区(FZ)形成的马氏体使得激光焊接过程中快速冷却的焊缝池在热影响区硬度值变化,由于马氏体的形成该熔化区附近有较高的硬度比该地区接近母材。
在母材观察几乎整个材料常数硬度值,对应母材的显微结构包含马氏体、铁素体基体加上一些残留奥氏体。
在焊接样本存在屈服点现象可能是因为间质扩散,可能发生在激光焊接过程。
高温产生的激光把碳(或氮气)铁原子扩散到别的位置的能量略低于另一个真实的刃型位错的平面原子。
弹性交互如此强劲,杂质原子气团变得完全饱和并沿核心的位错凝聚成一排原子。
当这样一个示例与固定插入的位错(即在这项研究的焊接样品)被加载,启动位错运动需要更高的应力来开始的塑性变形。
结果,经过激光焊接的屈服强度变得更高。
关于疲劳失效的位置,观察到所有焊接样本在一个高于250MPa压力振幅下在外热影响区失效,并且母材样品中的测量部分失效。
然而,在或低于250mpa的压力振幅下所有焊接样品和母材样品的失效远离中间测量部分。
这个疲劳断裂表面的显微镜观察表明,裂纹萌生发生标本的表面。
在这母材和焊接接头两者之中,或低于250MPa显示应力幅值样品测试裂缝起始位点和裂纹扩展的断裂表面区域很明显。
在可以产生刻凹痕或带钢单向皱纹的疲劳表面来回的滑移运动,也被称为作为入侵和挤出。
这种切口与一个原子尺寸根的缺口充当了应力集中器和疲劳裂纹可能的核心。
表面粗糙度和突出物还可以充当一个应力集中点,在此导致疲劳裂纹的萌生。
主要是由于不均匀变形形成了变形带,从而引起在轧制钢板存在的晶体结构(34,35)。
进一步研究了DP600钢焊接接头的疲劳断裂纹理的影响机制是必要的。