高精度冷轧窄带钢轧机的技术发展.docx
《高精度冷轧窄带钢轧机的技术发展.docx》由会员分享,可在线阅读,更多相关《高精度冷轧窄带钢轧机的技术发展.docx(14页珍藏版)》请在冰豆网上搜索。
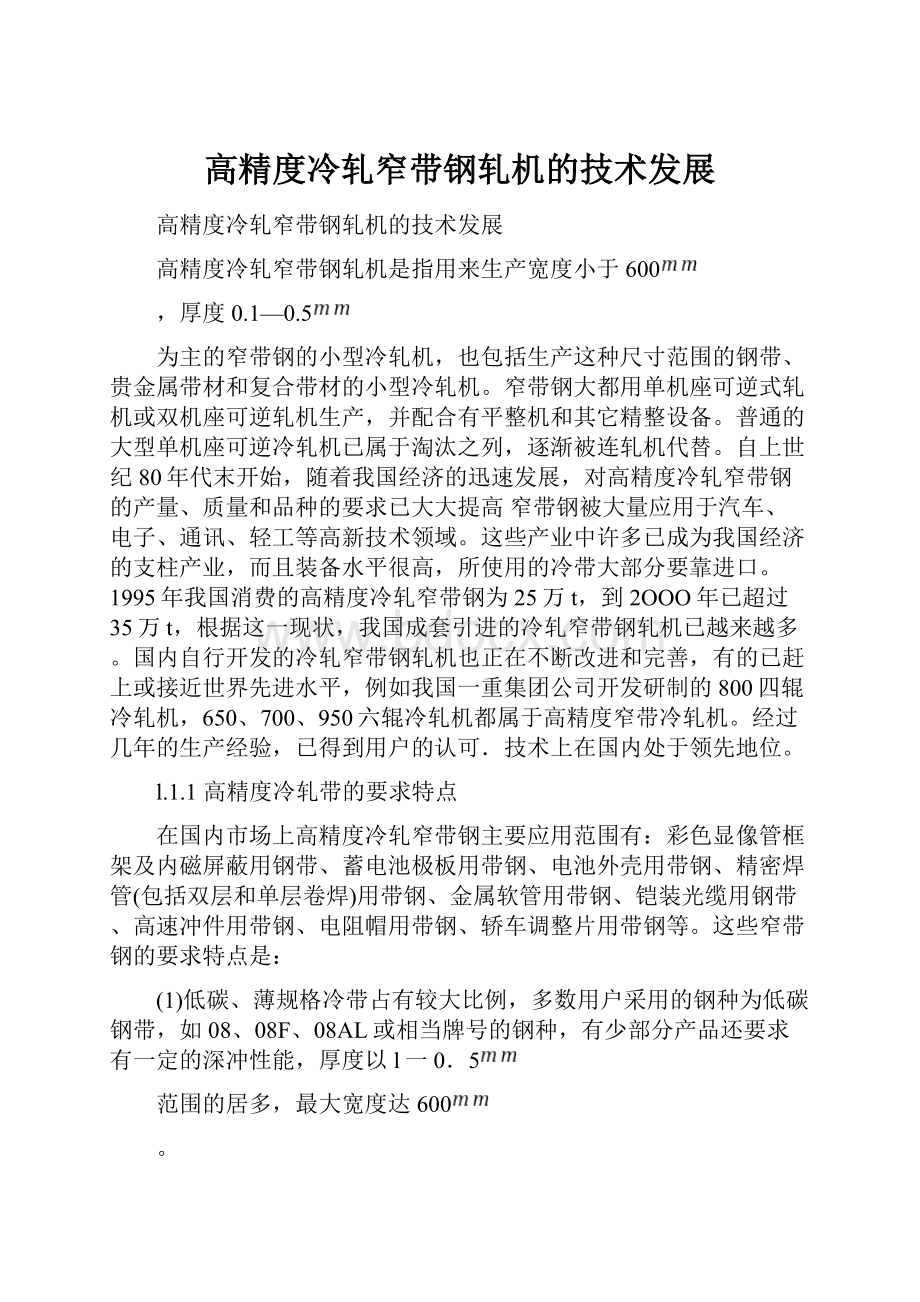
高精度冷轧窄带钢轧机的技术发展
高精度冷轧窄带钢轧机的技术发展
高精度冷轧窄带钢轧机是指用来生产宽度小于600
,厚度0.1—0.5
为主的窄带钢的小型冷轧机,也包括生产这种尺寸范围的钢带、贵金属带材和复合带材的小型冷轧机。
窄带钢大都用单机座可逆式轧机或双机座可逆轧机生产,并配合有平整机和其它精整设备。
普通的大型单机座可逆冷轧机已属于淘汰之列,逐渐被连轧机代替。
自上世纪80年代末开始,随着我国经济的迅速发展,对高精度冷轧窄带钢的产量、质量和品种的要求已大大提高窄带钢被大量应用于汽车、电子、通讯、轻工等高新技术领域。
这些产业中许多已成为我国经济的支柱产业,而且装备水平很高,所使用的冷带大部分要靠进口。
1995年我国消费的高精度冷轧窄带钢为25万t,到2OOO年已超过35万t,根据这一现状,我国成套引进的冷轧窄带钢轧机已越来越多。
国内自行开发的冷轧窄带钢轧机也正在不断改进和完善,有的已赶上或接近世界先进水平,例如我国一重集团公司开发研制的800四辊冷轧机,650、700、950六辊冷轧机都属于高精度窄带冷轧机。
经过几年的生产经验,已得到用户的认可.技术上在国内处于领先地位。
l.1.1高精度冷轧带的要求特点
在国内市场上高精度冷轧窄带钢主要应用范围有:
彩色显像管框架及内磁屏蔽用钢带、蓄电池极板用带钢、电池外壳用带钢、精密焊管(包括双层和单层卷焊)用带钢、金属软管用带钢、铠装光缆用钢带、高速冲件用带钢、电阻帽用带钢、轿车调整片用带钢等。
这些窄带钢的要求特点是:
(1)低碳、薄规格冷带占有较大比例,多数用户采用的钢种为低碳钢带,如08、08F、08AL或相当牌号的钢种,有少部分产品还要求有一定的深冲性能,厚度以l一0.5
范围的居多,最大宽度达600
。
(2)产品规格多且组距较密,有些产品甚至要求厚度按0.01
进级。
(3)交货状态复杂。
软态.半软、硬态三种状态均有。
(4)产品精度要求严格.多数产品厚度公差要求在±(2%~6%)之间.少部分产品厚差要≤±2%
(5)用户多且分散,每次订货量又比较少,有些用户年消费冷带几百吨。
每次订货量仅几十吨,这也是一些大企业或大型冷连轧机不愿意供货的原因。
1.1.2冷轧窄带钢轧机的技术特点
高精度冷带钢由于要求厚差小、板形良好和表面光洁等特点,并且有很多是变形抗力大难轧制的材料,所以轧机需要有一系列相应的高技术措施来保证。
这些高技术措施主要包括:
合理的机型选择、高精度的机械设备、先进的带材纵向公差和横向公差控制技术和精密的检测仪表等等。
(1)合理的机型选择
目前国内外高精度冷轧窄带钢生产用的机型主要有三种:
二十辊轧机、六辊轧机、四辊轧机。
二十辊轧机的显著特点是轧机结构紧凑度大、工作辊直径小,最适合轧制难变形金属,如不锈钢.高合精钢及厚度小于0l
的极薄带钢。
这种轧机的缺点是投资大、备品备件费用高、维修复杂。
六辊轧机是在四辊轧机的支承辊和工作辊之间安装有一个中间辊,可轴向移动,通过消除支承辊和工作辊之间有害的接触应力以改善板形,这种轧机比较适合生产较宽而难轧的带钢。
四辊轧机目前仍然是国内应用最为广泛的一种机型,由于采用小直径的工作辊和大直径的支承辊,既可减小变形抗力,也可提高轧机刚度和变形效率当代新型的四辊轧机与传统的四辊轧机在概念上已有本质的区别,由于采用了液压AGC、液压弯辊等新技术,可显著地提高产品精度和板形质量.生产的产品最薄达0.1
,厚度公差达±2
。
与二十辊轧机、六辊轧机相比,四辊轧机投资最少。
根据当前国内市场要求,冷轧窄带钢轧机的建设应以六辊和四辊轧机为主.对一些极薄带钢和有特珠性能要求的带钢,也可考虑建二十辊轧机。
(2)高精度的机械设备
高精度的机械设备对于机架、轴承座、轧辊、卷筒以及主轧机和卷取机的传动齿轮、接轴等关键设备,都要有精良的设计和加工要求。
轧机的两片机架在设计时对其强度和刚度均要经过计算机进行有限元计算,在机架的铸造过程中要把传统的内冷铁改为外冷铁,以提高机架材质的均匀性,并经超声波探伤保证内部质量。
机架窗口的宽度尺寸和对底脚板面的垂直度均应控制在每米0.05
以内,对轴承座的外形和内孔对称度和椭圆度要求控制在0.03
内。
必要时应采用三座标镗床加工。
对轧辊辊颈和辊身的不同轴度应达到±2
。
锻钢工作辊的表面硬度要求达到HS95—100,硬度均匀性控制在HS3以内,对于辊径在
250
以下的工作辊淬硬层深度至少应达到15
(半径),对于中间辊和支承辊也都有相应较高的精度和硬度要求。
轧辊两端一般都采双列或四列短圆拄滚动轴承,精度等级为D级少数也采用C级精度轴承,并配有油雾或油气润滑装置。
卷取机的卷简也是高标准要求的部件。
无论是卷筒的芯轴、扇形板、涨缩楔.涨缩液压缸还是供高压油的旋转密封,都要求有良好的材质和很高的加工精度,以保证有足够的强度、刚度和工作可靠性。
随着传动功率的增大和轧制速度的提高,对主轧机和卷取机的传动齿轮精度也越来越高。
当前多数冷带轧机的传动齿轮要求达到一级精度.并采用硬齿面、经过精磨的高速齿轮。
对于冷轧机的主传动接轴,已从过去的滑块式改为弧齿式或十字头形式。
由于轧薄带时要求采用小直径工作辊,对接轴头部的外径控制很严,所以接轴的结构形式和强度要求已成为带钢冷轧机的关键难题之一。
(3)先进的带材纵向和横向公差控制技术
全液压压下(AGC)技术:
是控制带材纵向公差的主要手段。
与传统的蜗轮、蜗杆结构相比,全液压压下具有控制厚度公差能力强、精度高、反馈速度快的特点。
现代AGC系统包括位置AGC、压力AGC、监控AGC和张力AGC等环节,并有轧辊偏心补偿和油膜补偿等功能,可按工艺要求将轧机调节成超硬特性、硬特性、自然特性和软特性等四种轧机刚度,使轧机既可进行恒辊缝轧制,又可进行恒压力轧制。
工作辊正负弯辊技术:
在上下工作辊两端轴承痤内设有8个弯辊液压缸,通以高压油可对工作辊进行正弯曲或负弯曲,以改变板材横向公差控制板形。
中间辊轴向移动技术:
中间辊轴向移动是六辊轧机控制板形的关键技术,通过轴向移动量的设定与弯辊力的最佳组合可有效地控制中浪、边浪和两肋浪。
板形仪开环控制板形技术:
在机组的出口侧配置了板形测量辊、通过带材横向张力的分布不均检测板形,曲线彩屏输出,操作者可根据带材的板形输出状况调节轧辊横移量、弯辊力或轧辊分段冷却状态,以达到理想的板形。
(4)精密的检测仪表
检测仪表的精度,不仅显示出带材的最终厚度和板形指标、而且是轧机自动控制的关键所在。
这些检测仪表包括轧制压力测量仪,辊缝测量仪、X射线(或其它射线)测厚仪、接触式测厚仪、板形测量仪、张力计和液压压下用的位移传感器、压力传感器等等。
(5)其它先进枝术
为适应薄带轧制对小张力控制稳定的需要.还配合有卷取机齿轮换档技术和卷取机双电机电磁离合技术。
现代化轧机还普遍配有自动上卸卷、自动对中、在线矫直、紧急事故处理、乳化液挤干及抽吸、快速换辊等装置,并采用两级计算机控制,轧制过程基本上是在一个密闭的环境下进行的。
1.1.3新技术的应用原则
冷轧技术发展十分迅速,设计一套冷轧机,在满足工艺条件的基础上,如何选择、应用新技木,使设计的机组起点较高,经济实用并留有发展空间,也是用户要充分考虑的:
其一、新技术的应用必须同主导产品方案(用途和质量标准)、产品规模、资金投资等情况综合考虑,首先要满足产品的质量要求。
在此基础上提高机组速度,满足规模产量要求;
其二.应用的新技术必须是发展成熟、工艺先进并经实践验证可行的新技术;
其三、充分论证新技术的实用性、针对性、可操作条件和性能价格比,平衡好追求高起点、高标准、功能全和经济实用的关系;
其四、从生产工艺、机、电、液等方面充分考虑未来的技术发展方向并预留发展空间和接口;
除此之外.还要考虑技术、工艺水平的匹配合理、管理水平.操作人员素质、设备维护、备件供应等诸方面因素。
1.1.4结语
高精度冷轧窄带钢轧机,无论是在设计技术、生产技术,还是在工艺装备、技术经济指标上,还在不断发展和提高之中。
要缩小与国外的差距,提高装备水平与产品质量,参与国内外的市场竞争,还有许多工作要做。
第一、加强对引进技术装备的消化、吸收和创新,积极开发国产技术和装备,加速国产化与成果商品化的进程;
第二、设计人员要与生产单位相结合,充分了解生产工艺和现场操作特性,提高整体设计水平;
第三、提高机械加工装备水平质量和基础元器件质量,加强质量控制确保零件加工精度;
第四、加强行业宏观控制,不断完善企业机制和管理机制。
1.2四辊板带轧机的发展概况
四辊可逆式冷轧机是生产冷轧板带典型的传统轧机。
据1979年5月统计资料,世界上当时共有这种可逆式冷轧机159台(森吉米尔轧机除外)。
其中,美国39台,日本25台,西德16台,意大利8台,法国10台,英国6台。
此后一段时间内,世界主要产钢国家仅对原有四辊可逆式冷轧机进行改造,很少再建这种冷轧机,新建轧机主要在第3世界内进行。
80年代末以来,随着世界小钢厂的发展,尤其是薄板坯连铸连轧技术的发展及对热带深加工的需要,四辊可逆式冷轧机成为板带小钢厂热带深加工的主要生产设备。
其装置技术水平不断发展提高。
现代串列式冷轧机及全连续冷轧机上的现代化技术,也用于可逆式冷轧机上。
并且,双机架四辊可逆式冷轧机也得到发展。
现代四辊可逆式冷轧机的生产及装备技术水平远远超过传统的四辊可逆式冷轧机。
1.2.1生产技术发展及装备技术特点
现代四辊可逆式冷轧机的生产技术发展,以提高生产力、扩大产品品种规格、提高产品质量和提高自动化装备水平为中心。
1、高生产力
目前世界小钢厂建设的现代单机架四辊可逆式冷轧机,年产量一般为30~40万t,最高达80~90万t。
如分别为1997、1999年投产的伯克利、希克曼单机架四辊可逆式冷轧机,设计年产量均为80万t;1997年底投产的戴拉米克双机架可逆冷轧机,设计年产量为90万t;计划2000年投产的哈特勒得双机架可逆式冷轧机,设计年产量为100万t。
这比60年代前建设的单机架四辊可逆式冷轧机产量高出数倍至数十倍。
那时有的冷轧机设计年产量只有1万t左右,最高设计年产量只有20万t左右。
要提高冷轧机的生产能力,主要应提高轧制速度,增大带卷重量,减少轧制道次
和提高轧机作业率。
(1)提高轧制速度。
60年代美国单机可逆冷轧机的设计速度为240~360m/min,最高为600m/min。
而今,希克曼单机可逆冷轧机的最大设计速度为1220m/min;戴拉米克双机架可逆冷轧机最大设计速度为1490m/min。
轧机速度的提高,为提高轧机产量创造了有利条件。
而轧机速度的提高建立在稳定的速度调节、压力调节和张力调节等电气自动控制的基础上,建立在设备的强度、刚度及强大功率的基础上。
现代化冷轧机具有高度自动化功能和强大的主传动功率。
如希克曼单机可逆冷轧机主传动功率达16443
,戴拉米克双机架可逆冷轧机的主传动功率为18900
,大大超过传统四辊可逆冷轧机的主传动功率。
(2)增大卷重,减少轧制道次。
轧机速度的提高,为增大带卷重量创造了条件,从而有利于提高轧机产量。
60年代前美国单机可逆式冷轧机的带卷重量一般为5~10t左右,个别为15t左右。
现代四辊可逆冷轧机的卷重普遍加大到30t左右。
日本个别厂单机可逆冷轧机的最大卷重达42t,单位宽度卷重达22.3kg/mm。
增大卷重,不仅有利于酸洗操作,也有利于轧制操作,因而提高了轧机的操作速度,缩短了带卷的纯轧时间;并相对缩短了轧制周期中的辅助时间,提高了机时产量。
同时,相对减少了穿带次数和因穿带而发生的事故,因而有利于提高轧机作业率。
另外,卷重增加,相对减少了穿带和抛尾次数,增加了稳定轧制时间,也利于提高产品质量。
为了提高机时产量,现代四辊可逆式冷轧机注意选择适宜的原料厚度,以减少不必要的轧制道次。
如希克曼厂全部产品安排3道次轧制,并在第1道次就采用高速轧制,使生产率大为提高。
(3)提高轧机作业率
现代四辊可逆式冷轧机采用快速换辊装置,使换工作辊时间缩短到5~10min;而传统四辊可逆冷轧机采用C型钩或平衡锤换工作辊,换辊时间近1h。
现代四辊可逆式冷轧机实现了自动控制,提高了设备和操作的可靠性,减少了停工时间,从而提高了作业率。
此外,现代四辊可逆冷轧机与串列式和连续式冷轧机比较,操作灵活,相互影响小,因而轧机作业率比串列式和连续式冷轧机提高4%~10%。
1.2.2、扩大品种规格范围,提高产品质量
由于四辊可逆式冷轧机操作灵活,因而适合生产多品种、多规格产品,除生产普通冷带外,更适于生产优质钢带或合金钢带,并可满足某些产品特殊工艺性能的要求,在产品规格上更具有灵活性。
现代四辊可逆冷轧机生产的产品品种,可以满足汽车、家电、轻工仪表、建筑、交通、农业等方面的要求。
其产品规格范围进一步扩大,厚度为0.25~2.0
。
如伯克利厂最薄带钢厚为0.25
;希克曼及戴拉米克厂最薄带钢厚0.38
;我国海南冷轧厂生产最薄带钢规格为0.22~0.25
,其0.5
以下的薄规格比例曾高达80%以上。
带钢宽度一般为900~1700
。
现代四辊可逆冷轧机轧制的产品质量(尺寸公差、板形及表面质量)达到的水平如表1.1所示。
表1.1现代四辊可逆冷轧机的产品质量
厚度公差
厚度范围/mm
稳态公差
/%
加、减速公差
/%
整卷长度公差
/%
0.2~0.5
0.005(mm)
0.01(mm)
95以上
>0.5
±1
±2
95以上
平直度公差
宽度范围
/mm
稳态公差
/I
加、减速
公差/I
整卷长度
公差/%
609~914
10
20
95以上
914~1549
12
24
95以上
带钢表面质量
最大残油量/mg.m-2
最大铁粒残量/mg.m-2
<100
<50
1.2.3技术装备特点
现代四辊可逆式冷轧机的技术装备如下:
液压压下和AGC控制。
现代四辊可逆式冷轧机采用液压压下和AGC控制。
因此整个带钢长度上的尺寸精度大大提高。
并且,轧机的驱动系统采用可控硅(SCR)控制,有效地改善了响应速度的稳定性,使板厚控制精度大大提高。
AGC控制方式设有位置环、压力环、张力环、监控环、预控环、加减速动态补偿、轧辊偏心补偿系统等。
正负弯辊装置。
正负弯辊装置用来增加或减少轧辊凸度,二者均能迅速调整轧辊凸度,以控制带钢板形。
分段冷却装置。
在轧机入、出口两侧设有乳化液喷射装置,一般工作辊喷射系统分为5段,支撑辊喷射系统分为3段。
各段乳化液冷却剂流量按抛物线进行分配,最大喷嘴设在中央。
流量可自动或人工调节。
分段冷却装置与正负弯辊装置配合使用,可控制带钢板形。
采用快速换辊装置。
换辊时间仅为套筒、C型钩的1/6~1/12。
轧机前后配有测厚仪。
以检测带钢入、出口厚度,供前馈和反馈AGC控制或自适应前馈AGC控制(秒流量速度控制),并可用测厚仪改善板形特性。
计算机控制及自动化功能。
70年代初,可逆式冷轧机开始引入计算机控制。
现代四辊可逆式冷轧机生产线上的控制系统已全部采用计算机,实现直接数字控制。
海南四辊可逆式冷轧机配置3台自动控制用计算机:
1台用于自动厚度控制系统、轧制表计算和存贮、SPC统计数据系统等;1台用于基础逻辑控制(PLC),完成轧制线上的控制;第3台为兼容计算机,主要用于编程、修改、查找故障等,并可离线开发轧制表。
可控硅(SCR)供电。
60年代中期,轧机驱动系统逐步采用可控硅(SCR)供电,以取代电动-发电机组供电。
现代四辊可逆式冷轧机已全部采用可控硅供电,有效地改善了响应速度的稳定性,从而改善并提高了控制精度。
双机架四辊可逆式冷轧机。
在对单机架四辊可逆式冷轧机不断进行改进、提高、完善的同时,也发展了双机架四辊可逆式冷轧机。
它具有占地少、节省设备的优点,1台双机架紧凑式可逆冷轧机的占地面积几乎与1台单机架冷轧机占地面积相当。
与2台单机架轧机比较,可以减少1台开卷机、2台卷取机及相应的电气设备,并可减少操作人员。
但在操作上,1台双机架轧机不如2台单机架轧机灵活;而且就目前设计产量上看,1台双机架轧机为90~100万t,而1台单机架轧机也高达80~90万t,两者各有其特点。
目前世界上有2台双机架四辊可逆式冷轧机,美国戴拉米克厂及哈特勒得厂各1台。
1.2.4、套机组的技术发展
与四辊可逆冷轧机组工序配套的机组有酸洗机组、退火机组、平整机组、剪切机组等。
(1)推拉式酸洗机组。
从生产规模及经济角度考虑,与四辊可逆式冷轧机工序配套,推拉式酸洗机组是最佳选择之一,且能满足酸洗质量要求。
与连续式酸洗机组比较,推拉式酸洗机组具有设备组成简单、设备重量轻、占地面积小、投资省的特点,并且操作简单,灵活,适合中、低产量的工厂选用。
目前这种机组最大酸洗速度为180~200m/min。
机组最大设计产量为80~90万t。
(2)全氢罩式退火炉。
因连续退火炉一次性投资大、产量高,因此四辊可逆式冷轧机一般选用全氢罩式退火炉,且罩式炉台数量增减较方便。
全氢炉与氮、氢气体混合型罩式炉相比,具有退火产品质量好、能耗低、产量高的优点。
因此,全氢罩式退火炉是现代四辊可逆式冷轧机组的主要退火配套机组。
此外,与现代四辊可逆式冷轧机配套的平整机组及剪切机组,无论设备本身,还是电气自动控制技术,都有很大发展。
1.2.5、现代四辊可逆冷轧机的典型实例介绍
现代四辊可逆式冷轧机的典型介绍见表1.2
表1.2现代四辊可逆式冷轧机典型实例
工艺设备参数
美国伯克利厂
美国希克曼厂
美国印第安纳厂
美国戴拉米克厂
机架数量
单机架
单机架
单机架
双机架
轧机形式
四辊可逆式
四辊可逆式冷轧兼平整机
四辊可逆式(二手)
紧凑式四辊可逆式
投产日期
1997-08-03
1999一季度
1990年左右
1997-12
年设计能力/万t
80
冷轧:
80,平整:
13.6
31.5
90
成品规格/mm
0.25~1.93×1168~1676
0.38~1.90×915~1625
0.40~1.56×1250~1350
0.38~2.18×914~1625
原料规格/mm
1.02~3.81×1168~1676
1.27~4.00×915~1625
2.80~4.50×1250~1350
1.52~3.96×914~1625
最大卷重/t
36.2
29.0
-
29
工作辊直径/mm
Φ295~Φ360
Φ432~Φ483
Φ380~Φ450×1700
Φ440×1875
支撑辊直径/mm
Φ1320~Φ1435
Φ1280~Φ1425
Φ1250~Φ1350
Φ1250×1625
轧机最高速度/m.min-1
800
1220
700
1490
轧机特点
前馈自动厚度控制;CVC轧辊移动;自动板形控制,多段冷却;轧辊弯辊和板形仪,2台X射线测厚仪;钢卷进出轧机采用6卷位步进梁
长行程液压AGC,长行程工作辊移动;工作辊正负弯辊;闭环板形控制;轧辊热凸度控制
轧机配套机组
1987年由西德购进,SMS将1422mm改成1700mm四辊可逆冷轧机。
1990年投产后进行一系列改造,1996年产量超过70万t,还可轧薄规格产品
.酸洗机组型式
推拉式
推拉式
推拉式
连续式
年设计能力/万t
80
88
-
130(140)
酸洗规格/mm
1.02~6.35×1168~1727
0.889~6.096
-
0.76~4.44×990~1625
机组最高速度/m.min-1
182
-
-
182
.罩式退火炉
全氢式
全氢式
全氢式
全氢式
最大装炉量/t
200(5卷)
-
-
115
最大装料高度/mm
6500
-
-
5664
处理品种
CQ、DQ、SQ、半硬、1/4硬
-
-
-
.平整机型式
四辊
平整剪切线
四辊
平整机最高速度/m.min-1
1094
-
-
1193
.热镀锌线
1条
1条
1条
2条
年设计能力/万t
40
50
-
40(热带为主)、30(冷带为主)
原料/mm
热、冷轧卷 厚:
0.25~2.66
-
-
0.38~4.26×914~1625
宽:
914~1676
-
-
0.38~1.77×914~615
最大卷重/t
22.65
-
-
29
机组速度/m.min-1
182
-
-
-
1.2.6、结语。
四辊可逆式冷轧机是生产冷轧板带典型的传统轧机,60年代美国曾大量建设这种轧机,其它国家在60~70年代也曾建设了一批这种轧机,此后一段时间内建设甚少。
80~90年代,随着世界小钢厂的发展,尤其是薄板坯连铸连轧技术的发展及热带深加工的需要,四辊可逆式冷轧机成了与CSP工艺配套生产高质量冷轧产品的首选机型之一。
机组的装备水平及产品质量远远高于传统的四辊可逆冷轧机。
当前建设100万t规模以下的冷轧厂,选择单机架或双机架四辊可逆冷轧机,配有推拉式酸洗机组、全氢罩式退火炉、平整机组及剪切机组、热镀锌机组,是最经济实用的方案。