CO装置试车方案.docx
《CO装置试车方案.docx》由会员分享,可在线阅读,更多相关《CO装置试车方案.docx(29页珍藏版)》请在冰豆网上搜索。
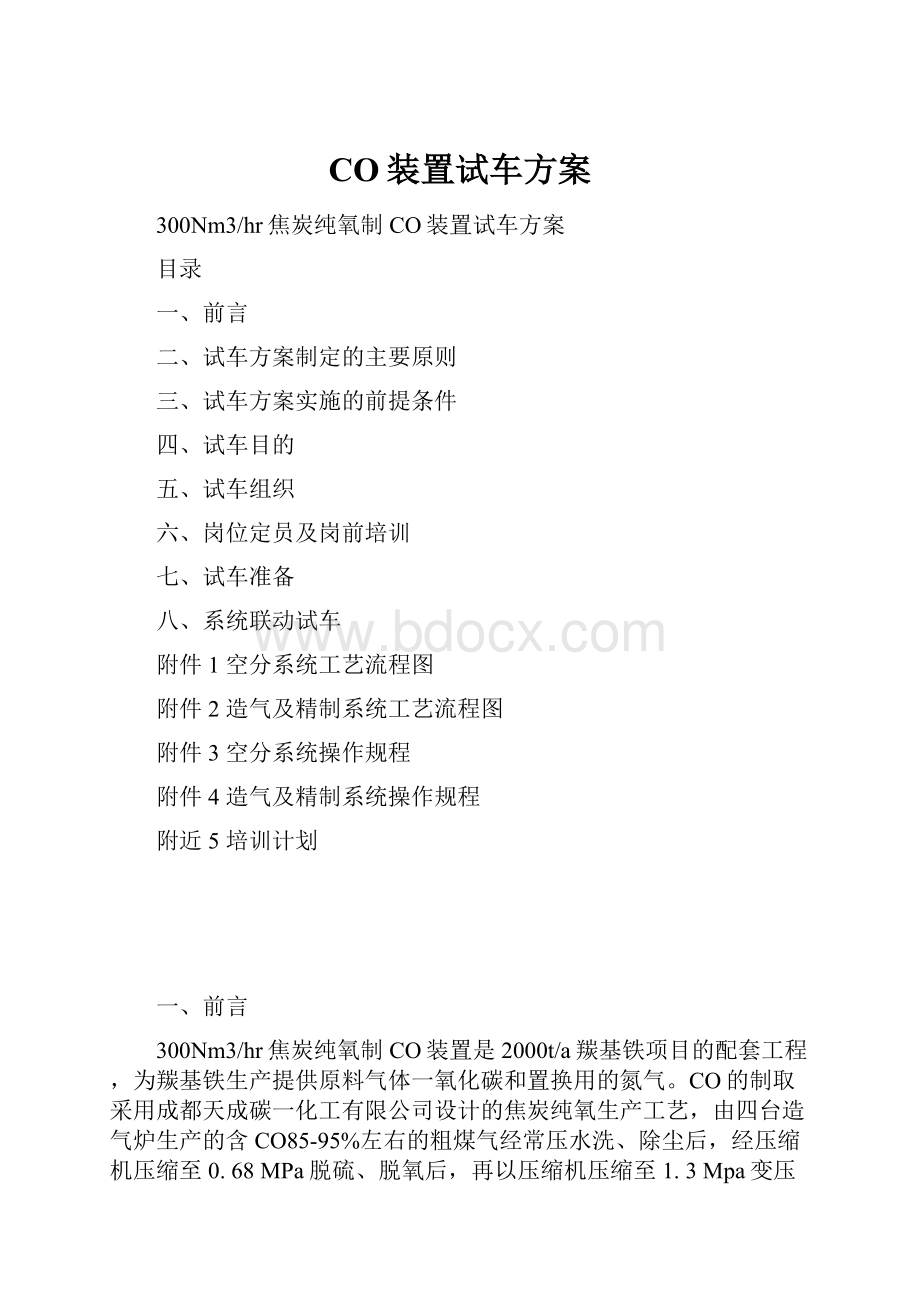
CO装置试车方案
300Nm3/hr焦炭纯氧制CO装置试车方案
目录
一、前言
二、试车方案制定的主要原则
三、试车方案实施的前提条件
四、试车目的
五、试车组织
六、岗位定员及岗前培训
七、试车准备
八、系统联动试车
附件1空分系统工艺流程图
附件2造气及精制系统工艺流程图
附件3空分系统操作规程
附件4造气及精制系统操作规程
附近5培训计划
一、前言
300Nm3/hr焦炭纯氧制CO装置是2000t/a羰基铁项目的配套工程,为羰基铁生产提供原料气体一氧化碳和置换用的氮气。
CO的制取采用成都天成碳一化工有限公司设计的焦炭纯氧生产工艺,由四台造气炉生产的含CO85-95%左右的粗煤气经常压水洗、除尘后,经压缩机压缩至0.68MPa脱硫、脱氧后,再以压缩机压缩至1.3Mpa变压吸附脱碳提纯后得到98.5%的成品一氧化碳送出界区。
本装置采用的焦炭纯氧制一氧化碳技术,为成熟可靠技术,变压吸附气体分离技术具有产品纯度高、工艺简单、操作方便、能耗低等特点,并有多套类似装置成功开发的经验,因此本设计采用的技术是成熟、先进可靠的。
工艺中所用的氧气是采用哈尔滨制氧机有限公司提供的KDON-(150-250)/(300-600)变工况深冷空分装置,能够产出纯度为99.6%的氧气和99.99%的氮气。
因此,气体站的试车主要分四个工序进行:
深冷空分工序,二是造气炉工序,三是提纯工序,四是污水处理工序,本次试车是以这四部分为核心实现全系统拉通,产出合格的一氧化碳气体供100t/a羰基铁试车所需的原料气。
预计试车时间为15天。
二、试车方案制定的主要原则
2.1、力求最小的原辅材料准备量。
2.2、在不增设临时开车设备和临时管线的情况下,力求最小的工艺管线改动量。
2.3、尽可能地减轻工人的劳动强度,提高装置的自动化程度。
三、试车方案实施的前提条件
3.1、系统设备、工艺管线已经安装完毕。
3.2、外部达到供电、供水、供汽条件。
3.3、电气和自动控制系统已经安装连接完毕,具备试车条件。
3.4、老气体站已经具备连续向新气体站供应仪表空气和呼吸空气的条件。
3.5、400m3消防水池已注满工业用水,循环水泵正常运转,给排水管线畅通无阻。
3.6、试车人员经技术、安全培训后进入现场。
四、试车目的
4.1.实现深冷空分系统、造气炉系统、粗煤气提纯系统、污水处理系统联动带料试车的目的;
4.2.获得整个试车过程中各个工序的工艺参数,为下一步正常生产优化和调整工艺参数奠定基础;
4.3.根据试车结果进行物料衡算,根据原辅材料消耗计算生产成本;
4.4.测试DCS系统的反应和对系统工艺参数的控制水平;
4.5.测试和平价系统所有仪表和设备的可操作性和完整性;
4.6、测试系统的安全防火保障措施;
4.7.发现系统缺陷和影响系统完整性的关键性因素,为下一步系统整改奠定基础;
4.8考察脱硫剂脱硫效果,为以后的降低生产成本作好准备;
4.9考察造气炉中粗煤气中带出的粉尘量,污水处理系统污水中粉尘的絮凝效果,以及最佳的絮凝剂;
五、试车组织机构
为了保障试车顺利进行,成立试车组织机构,参与试车的有吉恩镍业和管理人员,技术人员和操作人员,负责整个试车过程的顺利完成;设计方代表,负责指导开车和技术支撑;设备供应商,保障提供的设备能够正常运转;安装单位,处理试车过程中发生的设备、管线、仪表和控制系统的安装缺陷。
试车组织机构如下:
试车总指挥:
吉恩镍业总工程师朴东鹤;
试车现场总指挥:
第三精炼厂厂长雷福伟、设备工程管理部牛铁钢;
试车现场副总指挥:
第三精炼厂厂长助理唐思琪、孟庆伟;
工艺负责人:
冯启东、于得明、刘文星、设计方代表;
设备负责人:
杨春芳、宋宏亮、张贵臣,设备供应商;
电气、仪表和自控制负责人:
杨春芳、黄振梅、商伟光、费立新、供应商;
维修负责人:
王金哲、王淑霞;
安全防火负责人:
谢贵明、包录,保卫部和安全生产部协助;
现场操作负责人:
刘洪波、王家龙、王宗波;
后勤保障负责人:
姜宁。
六、岗位定员及岗前培训
气体站的操作实行四班三运转制,岗位定员是根据设计方提供的建议以及结合我公司人力资源的实际情况制定的,总人数为42人。
定员见表1。
工厂定员表1
岗位
每班定员
总定员
车间主任
1
技术主管
1
班长
1
4
DCS操作员
1
4
空分岗位
3
12
造气炉岗位
2
8
污水处理岗位
1
4
气体精制岗位
1
4
压缩机岗位
1
4
操作人员的培训在上岗位前进行严格的安全培训和技术培训,在考试合格后方可上岗,具体培训内容见培训计划中的安全规程、安全应急预案和技术操作规程。
七、试车前准备
7.1试车范围内的装置已经过机械竣工验收。
按设计文件规定的内容和施工及验收规范的标准全部完成。
7.2试车范围内的机器,除必须留待投料试车阶段进行试车的以外,单机试车已经全部合格。
7.3试车范围内的设备内填料已按设计要求装填完毕,设备和管道系统的内部处理及耐压试验、严密性实验已经全部合格。
7.4试车范围内的电气系统和仪表装置的检测系统、自动控制系统、联锁及报警系统等调试已经全部合格。
7.5试车方案和操作法已经批准。
7.6公司管理机构已经建立,各级岗位责任制已经执行。
7.7试车领导组织及各级试车组织已经建立,参加试车的人员已经考试合格。
7.8试车所需燃料、物料、水、电、汽、工艺空气和仪表空气等可以确保稳定供应,各种物资和测试仪表、工具皆已齐备。
装置所需要的原辅材料及公用工程预期条件见表2。
原辅材料、公用工程条件表2
序号
名称
规格
单位
消耗
备注
1
冶金焦
碳含量≥85%(W%)水份≤5%(W%),灰份≤10%(W%)粒度3~8cm
t/hr
0.33
冶金焦按15天试车时间准备,计划进100吨。
2
氧气
≥99.6%
Nm3/hr
60
3
循环水
≥0.2MPa,≤350C
t/hr
180
4
一次水
≤350C
t/hr
80
5
低压蒸汽
0.6MPa
t
0.3
冬季用量
6
电
220V/380V,50Hz
Kw.h
7
仪表空气
≥0.4MPa
Nm3/hr
80
8
氮气
≥0.4MPa
Nm3/hr
60
置换用
7.9试车方案中规定的工艺指标,报警及联锁整定值已确认并下达。
7.10试车现场有碍安全的机器、设备、场地、走道处的杂物,业已清理干净。
严禁与工作无关的人员进入装置区。
7.11《安全紧急事故处理预案》中的各项准备工作全部落实。
安全设施、消防器具全部准备到位。
防毒面具发放到个人,呼吸式防毒面具发放到控制室,便携式一氧化碳检测报警器发放到生产班组。
车间准备好应急药品,特别是医用氧钢瓶。
联系好安全生产部、保卫部和医院,做到安全应急处理渠道顺畅。
八、系统联动试车
空分系统所使用的原料主要是空气,没有其它物质,所以空分系统的空负荷试车和负荷试车可以同时进行。
造气和精制系统的空负荷试车用氮气作为介质按照正常操作程序测试系统,然后转入正式投料试车,试车采用一级冶金焦炭作为造气炉的原料,生产出来的合格一氧化碳作为100吨级羰基铁系统试车的气体原料。
8.1空分系统试车
8.1.1工艺流程叙述
空气分离的基本原理是利用液化空气中各组分的沸点不同进行精馏,分离氮、氧。
空分系统根据造气炉运行的台数不同,采用KDON-(150-250)/(300-600)变工况操作,当开一至两台造气炉时,采用150/300工况运行,两台空压机、一台氧压机、一台氮压机运行,生产150Nm3氧气和300Nm3氮气,当开三至四台造气炉时,采用250/600工况运行,三台空压机、两台氧压机、两台氮压机运行,生产250Nm3氧气和600Nm3氮气。
原料空气经过过滤器除去灰尘及其它有机杂质后进入压缩机,压缩至0.7Mpa,然后进入空气预冷系统。
在预冷系统中降温至8-10℃,分离水分后进入分子纯化器,除去二氧化碳,碳氢化合物及残留水分。
空气净化后温度在14℃左右。
进入分馏塔冷箱中,空气直接去换热器与返流气体(氧,氮,污氮)换热,换热后空气温度降至-172℃左右,引入下塔,少部分(3.8%左右)空气从换热器中部抽出,进入透平膨胀机,制冷后进入上塔中部(制冷前温度-157℃,制冷后-174℃)。
在下塔中,空气被初步分离成氮和富氧液体,上升气氮在冷凝器中液化,同时冷的低压侧液氧被汽化。
部分液氧作为下塔回流液,另外一部分液态氮经过冷气过冷后送如上塔顶部。
液空经过冷气过冷后进入上塔中部作为回流液。
纯氧从上塔下部引出,并在换热器中换热后,送往界外。
纯氧从上塔顶部引出,经过冷器和换热器复然后送往界外。
部分污氮从上部抽出,经过冷器和换热器换热后,作为分子筛的再生气源。
工艺流程图见附件1
8.1.2工艺过程中的设备及工艺指标
8.1.2.1无油活塞式空气压缩机3套
序号
技术要求
技术参数
单位
备注
1
型号:
LW-11/7
2
排气量:
11
m3/min
(吸入状态)
3
排气压力:
0.7
MPa(G)
4
末级排气温度:
≤40
℃
5
电机功率:
65
KW
6
电压/相位/频率:
380V/三相/50Hz
7
额定转数:
500
r/min
8
主机外型尺寸(L×W×H)
2430×1400×1880
mm
9
机主净重:
3816
KG
10
冷却水用量:
5
m3/hr
11
制造商
哈氧
8.1.2.2空气预冷机组1套
序号
技术要求
技术参数
单位
备注
1
型号:
UF-2000/7
2
处理空气量:
2000
Nm3/hr
3
空气进预冷器压力
0.7
MPa(G)
4
空气进预冷器温度
≤40
℃
5
空气出预冷器温度:
5~8
℃
6
制冷量
10
kW
7
电机功率
13.5
HP
8
冷却水用量
6.8
T/hr
9
冷却水压力
0.4
Mpa
10
外形尺寸
2100×1060×1540
mm
11
机组重量
980
KG
12
制造商
杭州日丰空气处理设备有限公司
8.1.2.3分子筛纯化器系统1套
序号
技术要求
技术参数
单位
备注
1
型号
HXK-2000/7
2
处理气量
2000
Nm3/hr
3
工作压力
0.7
MPa(G)
4
吸附剂种类规格
13X,4×8目球型
5
吸附筒材质
16MnR
6
管路材质
20#
7
切换时间
8
小时
8
切换方式:
手动
9
再生气介质:
富氧空气
10
电加热器容量:
45
KW
分大小组控制(平均15Kw)
11
制造商
哈氧
8.1.2.4分馏塔1套
序号
技术要求
技术参数
单位
备注
1
型号
FON-250/600
2
加工空气量
2000
Nm3/h
3
氧气产量
150-250
Nm3/h
4
氧气纯度
99.6
%O2
5
氮气产量
300-600
Nm3/h
6
氮气纯度
99.99
%N2
7
液氧纯度
99.6
%O2
8
外形尺寸(L×W×H)
2400×2000×15600
mm
9
绝热材料材质
珠光砂保温材料
10
精馏塔探伤处理
X射线100%探伤
11
塔结构材料
铝制筛板塔
12
冷箱外壳材料
Q235-A
13
制造商
哈氧
8.1.2.5气体轴承透平膨胀机2套(一用一备)
序号
技术要求
技术参数
单位
备注
1
轴承气耗量
40
Nm3/h
2
密封气耗量
25
Nm3/h
3
仪表空气过滤器材质
0Cr18Ni9
4
空气质量
-60℃
尘粒1μ
5
轴承气体过滤器材质
铝镍合金
尘粒1μ
6
制造商
哈氧
8.1.2.6氧气压缩系统
1氧气压缩机2套
序号
技术要求
技术参数
单位
备注
1
型号:
ZW-3/8
2
排气量:
180
m3/h
3
排气压力:
0.8
MPa(G)
4
末级排气温度:
≤40
℃
5
电机功率:
25
KW
6
轴功率:
≤19
KW
7
电压/相位/频率:
380V/三相/50Hz
8
额定转数:
495
r/min
9
主机外型尺寸(L×W×H)
2300×1910×2255
mm
10
机主净重:
1700
KG
11
冷却水用量:
5.5
m3/hr
12
制造商
哈氧
2氧气缓冲罐1台
序号
技术要求
技术参数
单位
备注
1
型号:
ZG-5/0.2
2
工作介质:
氧气
3
公称体积:
5
m3
4
储存压力
0.02
MPa(G)
5
储存温度
40
℃
6
外形尺寸(L×W×H)
φ1400×5×4100
mm
7
设备重量
900
kg
8.1.2.7氧气储罐1台
序号
技术要求
技术参数
单位
备注
1
型号:
ZG-30/8
2
工作介质:
氧气
3
储存气量:
30
m3
4
储存压力
0.8
MPa(G)
5
储存温度
40
℃
6
外形尺寸(L×W×H)
φ2200×10×9000
mm
7
设备重量
5400
kg
8
制造商
哈氧
8.1.2.8氮气压缩系统1套
1氮气压缩机2套
序号
技术要求
技术参数
单位
备注
1
型号:
ZW-6/8
2
排气量:
360
m3/h
3
排气压力:
0.8
MPa(G)
4
末级排气温度:
≤40
℃
5
电机功率:
45
KW
6
轴功率:
≤38
KW
7
电压/相位/频率:
380V/三相/50Hz
8
额定转数:
550
r/min
10
机主净重:
1700
KG
11
冷却水用量:
5.5
m3/hr
12
制造商
哈氧
2氮气缓冲罐1台
序号
技术要求
技术参数
单位
备注
1
型号:
ZG-5/0.2
2
工作介质:
氮气
3
公称体积:
5
m3
4
储存压力
0.02
MPa(G)
5
储存温度
40
℃
6
外形尺寸(L×W×H)
φ1400×6×4100
mm
7
设备重量
900
kg
8.1.2.9氮气储罐2台
序号
技术要求
技术参数
单位
备注
1
型号:
ZG-60/8
2
工作介质:
氮气
3
储存气量:
50
m3
4
储存压力
0.8
Mpa(G)
5
储存温度
40
℃
6
外形尺寸(L×W×H)
φ2600×16×12960
mm
7
设备重量
16260
kg
9
制造商
哈氧
8.1.3空分系统开车
空分系统先按150/300工况试车,即两台空压机、一台氧压机、一台氮压机工作,待此工况运转正常后再按250/600工况调整,即三台空压机、两台氧压机、两台氮压机全部工作,也就是系统满负荷运行。
(一)开车前的设备试运转和系统吹扫试漏
在系统启动前,要对每一台动力设备按照设备说明书进行调试,对压缩机的传动部件、转动部件进行检查、加油,保证空压机、氧压机和氮压机运转正常。
系统安装完毕后要对管道和设备进行吹扫,吹除杂物,用工作压力1.2倍的压力对系统进行气密性试验,检查系统的漏点,特别是对分馏塔内部的管线进行仔细检查,保证无漏点。
待所有的漏点消除后启动系统,进行正式开车。
(二):
设备启动
1.空压机启动:
对空压机进行盘车,手摇油泵,对机器供油,待油压达到正常值时,即结束。
开启全部放空阀,启动压缩机。
逐渐关闭排放阀,缓慢升压,在升压过程中,检查压缩机有无异常情况。
待压缩机工作正常时,两台压缩机出口流量达到1320m3/hr,出口压力达到0.7Mpa,温度低于40℃。
2.预冷机组启动:
按照预冷机组操作规程启动,在启动过程中,逐渐开启V-101,直至全开。
待预冷机组工作正常后,从压缩机排出的空气进入预冷机组进行预冷,使空气冷却到8-10℃。
3.纯化器启动和分馏塔启动:
纯化器启动与预冷机组同时进行,全开纯化器出口阀门V-1210、V-1219,微开纯化器入口阀V-1205(对应开启V-1201)或V-1206(对应开启V-1202),向吸附筒内导气,进气要慢,导气时间约10分钟左右,直至压力达到要求。
当预冷机组排气温度其达到20以下时使,气体通过电炉缓慢向吸附筒内导气,直至再生气量满足要求后,即可开启电炉。
纯化器需要工作一个周期(8小时),检查吸附后的空气中CO2含量合格后,方可向塔内送气。
缓慢开启去主换热器阀门V-103、在压缩机排压稳定的情况下,但PI-101为0.7Mpa时,微开主换热器后去下塔的阀门V-12,缓慢向下塔送气,直至下塔压力达到要求,即可开启纯氧管线放空阀V-108、纯氮管线放空阀V-109,同时关闭去贮罐阀门V-106、V-107。
全开V-1、V-2、V-9(下塔去上塔阀门),向上塔送气,逐渐开V-8(观察上塔调整V-8),调整V-108、V-109。
使PIS-10的值为0.04Mpa。
4.膨胀机启动:
开启膨胀机放空阀V-409、V-410,开启轴承气管线上的阀门V-5、V-6、V-10、V-7。
适当开启V-3、V-4,打开电阀慢慢开启V-3、V-4,使膨胀机转速平稳升至额定转速为止。
通过调节V-108、V-109,适时调整上塔压力。
随着塔内温度的降低,膨胀机转速将下降,适时调整V-3、V-4直至全开。
V-302、V-13适当开启,到管道结霜为止,将其关闭。
(二):
正常工作
1.设备冷却阶段:
膨胀机启动,即算冷却开始。
让膨胀气主要进入上塔,将上塔尽快冷却,随着塔内温度的降低,塔内进气量增大。
调整主换热器去膨胀机阀门V-11、V-10,调整进气温度,当温度达到要求时,最终关闭V-10,调整V-7使部分空气进入上塔。
适时调整V-8,保证上塔压力随着温度继续下降,逐渐关闭V-8。
2.设备积液阶段:
随着液空、液氮的来临,尽量将液体送入上塔,使上塔慢慢建立精溜工况(即阻力增加液面增长)。
第一次开车液面达到50mm时,液体全部排出,重新积液。
3.调纯阶段:
用V-1、V-2、V-9阀门开、关度调整上塔工况的运行,氮气产量超过400m3/h以上时,可关闭V-9。
当阻力不再增大,说明产品气体纯度基本接近正常,此时可以启动氧压机、氮压机向外送气。
(三):
氧压机、氮压机启动:
在分馏塔加温和冷却阶段,对氧压机、氮压机进行单体试车,氧压机、氮压机试车必须按照氧氮压机操作规程进行。
启动氧氮压机向贮罐送气,置换氧气和氮气贮罐,使贮罐内气体纯度达到使用要求。
至此,空分系统开车完成,进入正常运行阶段。
整个空分系统从启动到产出合格气体,大概需要72小时左右。
在150/300工况运转正常后,可以根据生产需要再调整250/600工况,或者在主系统停车过程再调250/600工况,其调整过程与150/300工况基本相同,只是要整个系统全部启动,实现满负荷运转。
空分系统的生产成本主要是电耗,所以在试车过程中主要考核此项指标。
8.2造气及精制系统试车
造气工序共有四台造气炉,本次开车计划逐台启动,即一台炉生产正常后再开第二台,直到四台炉全部启动,使系统达到满负荷生产,按设计合同要求,逐项指标进行考核。
整个工艺流程图见附件2。
8.2.1工艺原理及流程简述
100#造气工序:
参看造气工序管道及仪表流程图(图号:
TC0706-32-101)。
原料焦碳经电动葫芦(L101)送至一氧化碳发生炉(F101A~D),炉底通入氧气,使焦碳燃烧生成二氧化碳,燃烧温度在1500℃左右,当二氧化碳上升时遇到上层红热的焦碳层而还原成一氧化碳,还原温度在1000℃左右,其主要化学反应式为:
C+O2====CO2↑+409.05KJ
C+CO2↑====2CO↑-160.35KJ
一氧化碳从炉中进入水洗塔(T101A~D),由来自循环水站的水洗涤,水洗后的一氧化碳气进入一氧化碳气柜(V102),经气柜后送200#脱硫压缩工序。
一氧化碳发生炉(F101A~D)夹套冷却由软水冷却器(E101)、软水循环泵(P101)、软水高位槽(V101)组成的系统保证。
单台造气炉的粗煤气量约为120Nm3/hr左右。
200#脱硫压缩工序:
参看脱硫压缩工序管道及仪表流程图(图号:
TC0706-32-201)。
来自气柜的粗产品气,进入静电除尘(M201AB)除去其中所含的绝大部分粉尘和焦油杂质,静电除尘(M201AB)可单独使用,也可串联使用。
除尘后气体在氧化铁脱硫罐(T201A,B)中进行脱硫,两脱硫罐可单独使用,也可串联使用,也可并联使用,脱除H2S后气体(H2S含量低于5ppm)经压前缓冲罐(V202)进入压缩机(C201AB)压缩至0.67Mpa去300#脱硫脱氧工序。
300#精制工序
参看精制工序管道及仪表流程图(图号:
TC0706-32-301)。
从200#来粗产品气在水解加热器中加热到150℃左右进行水解转化,之后进行在水解催化剂作用下粗产品气中大部分羰基硫被转化成硫化氢,然后进入氧化铁脱硫罐进行脱硫,共有两级脱硫(R302AB和R304AB),一级和二级脱硫罐均为两个脱硫罐,可单独使用,也可串联使用,也可并联使用。
脱硫后的气体中硫化氢含量为1ppm。
此段工序重点考察脱硫剂的脱硫效果,因为脱硫剂半年左右就要更换一次,总量为33吨,约10万元,如果脱硫效果好,可以大大简化此段工序,为节约生产成本做好准备。
脱硫后气体进行脱氧,脱氧后的气体(氧气含量为0.1%),返回到200#压缩机的三级压缩,压缩至1.3Mpa,进入到400#进行变压吸附脱碳。
400#变压吸附(PSA)脱碳工序
粗产品气中的二氧化碳,采用5-1-2变压吸附工艺技术,变压吸附的操作步骤有:
吸附(A)、均压降(D1、D2、D3)、逆放(D)、抽真空(V)、均压升(R1、R2、R3)、终充(RR)等,各步骤的过程