砂型铸造课程设计.docx
《砂型铸造课程设计.docx》由会员分享,可在线阅读,更多相关《砂型铸造课程设计.docx(25页珍藏版)》请在冰豆网上搜索。
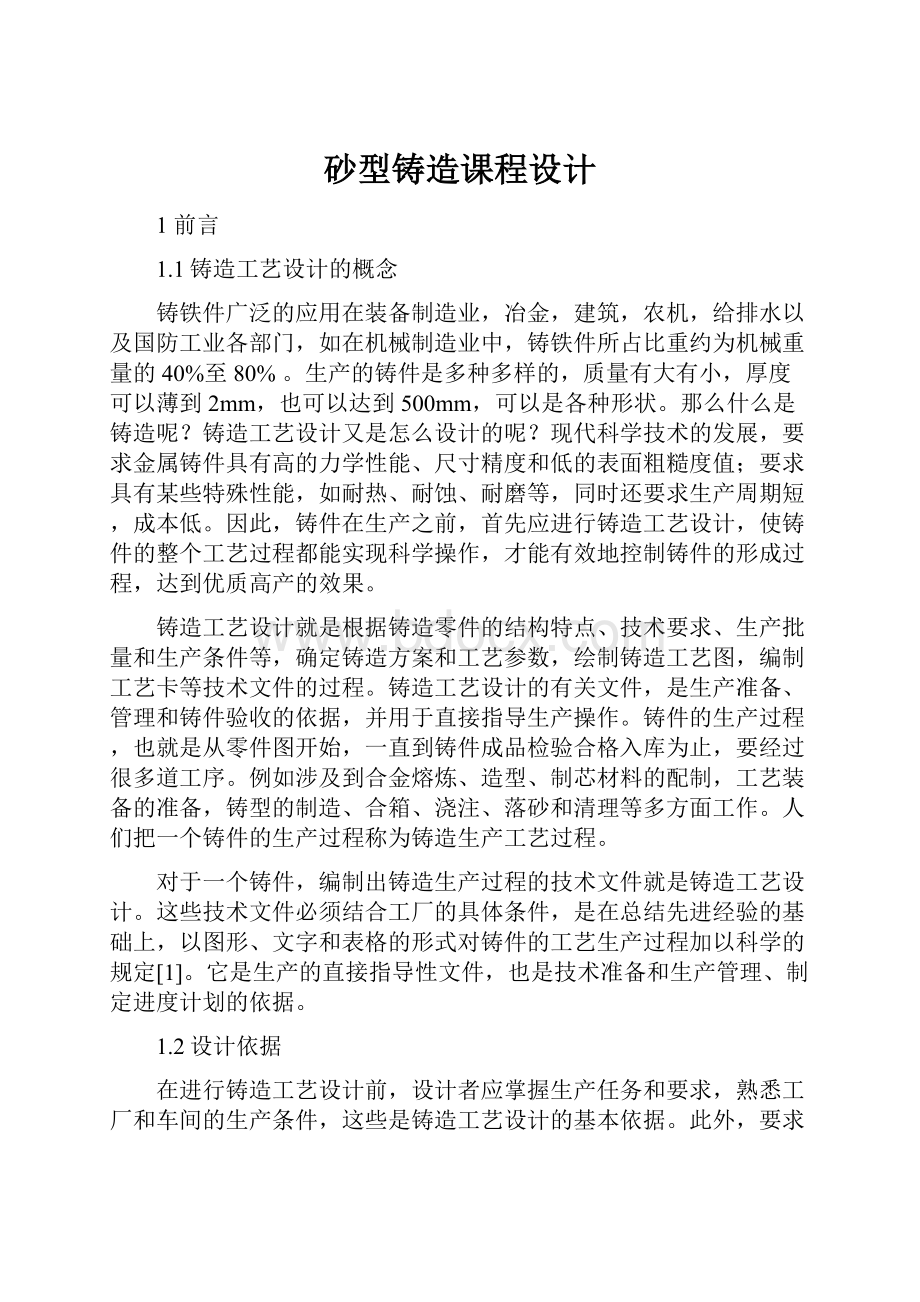
砂型铸造课程设计
1前言
1.1铸造工艺设计的概念
铸铁件广泛的应用在装备制造业,冶金,建筑,农机,给排水以及国防工业各部门,如在机械制造业中,铸铁件所占比重约为机械重量的40%至80%。
生产的铸件是多种多样的,质量有大有小,厚度可以薄到2mm,也可以达到500mm,可以是各种形状。
那么什么是铸造呢?
铸造工艺设计又是怎么设计的呢?
现代科学技术的发展,要求金属铸件具有高的力学性能、尺寸精度和低的表面粗糙度值;要求具有某些特殊性能,如耐热、耐蚀、耐磨等,同时还要求生产周期短,成本低。
因此,铸件在生产之前,首先应进行铸造工艺设计,使铸件的整个工艺过程都能实现科学操作,才能有效地控制铸件的形成过程,达到优质高产的效果。
铸造工艺设计就是根据铸造零件的结构特点、技术要求、生产批量和生产条件等,确定铸造方案和工艺参数,绘制铸造工艺图,编制工艺卡等技术文件的过程。
铸造工艺设计的有关文件,是生产准备、管理和铸件验收的依据,并用于直接指导生产操作。
铸件的生产过程,也就是从零件图开始,一直到铸件成品检验合格入库为止,要经过很多道工序。
例如涉及到合金熔炼、造型、制芯材料的配制,工艺装备的准备,铸型的制造、合箱、浇注、落砂和清理等多方面工作。
人们把一个铸件的生产过程称为铸造生产工艺过程。
对于一个铸件,编制出铸造生产过程的技术文件就是铸造工艺设计。
这些技术文件必须结合工厂的具体条件,是在总结先进经验的基础上,以图形、文字和表格的形式对铸件的工艺生产过程加以科学的规定[1]。
它是生产的直接指导性文件,也是技术准备和生产管理、制定进度计划的依据。
1.2设计依据
在进行铸造工艺设计前,设计者应掌握生产任务和要求,熟悉工厂和车间的生产条件,这些是铸造工艺设计的基本依据。
此外,要求设计者有一定的生产经验和设计经验,并应对铸造先进技术有所了解,具有经济观点和发展观点。
1.2.1生产任务
1)铸造零件图样。
提供的图样必须清晰无误,有完整的尺寸和各种标记。
设计者应仔细审查图样。
注意零件的结构是否符合铸造工艺性,若认为有必要修改图样时,需与原设计单位或订货单位共同研究,取得一致意见后以修改后的图样作为设计依据。
2)零件的技术要求。
金属材质牌号、金相组织、力学性能要求、铸件尺寸及重量公差及其他特殊性能要求,如是否经水压、气压试验、零件在机器上的工作条件等。
在铸造工艺设计时应注意满足这些要求。
3)产品数量及生产期限。
产品数量是指批量大小。
生产期限是指交货日期的长短。
对于批量大的产品,应尽可能采用先进技术。
对于应急的单件产品,则应考虑使工艺装备尽可能简单,以便缩短生产周期,并获得较大的经济效益。
1.2.2生产条件
1)设备能力。
包括起重运输机的吨位和最大起重高度、熔炉的形式、吨位和生产率、造型和制芯机种类、机械化程度、烘干炉和热处理炉的能力、地坑尺寸、厂房高度和大门尺寸等。
2)车间原材料的应用情况和供应情况。
3)工人技术水平和生产经验。
4)模具等工艺装备制造车间的加工能力和生产经验。
1.2.3考虑经济性
对各种原材料、炉料等的价格、每吨金属液的成本、各级工种工时费用、设备每小时费用等,都应有所了解,以便考核该项工艺的经济性。
1.3铸造工艺及工装设计内容
由于每个铸件的生产任务和要求不同,生产条件不同,因此,铸造工艺及工装设计的内容也不同。
一般情况下,铸造工艺设计包括以下几种技术文件:
铸造工艺图,铸造工艺卡,铸型装配图,铸件图,模样图,芯盒图,砂箱图,模板图。
1.4铸造工艺及工装设计的过程
(1)对零件图纸进行审查和进行铸造工艺性分析
(2)选择铸造方法,确定铸造工艺方法
(3)绘制铸造工艺图
(4)绘制铸件图
(5)绘制铸型装配图
(6)绘制各种铸造工艺装配图纸
各种工装图要以铸造工艺图为主要设计依据。
在大量生产中,一般都有试生产阶段。
在这个阶段中,我们可以用木模或是木芯盒进行反复调试和修改,直到符合要求,在此基础上,我们才可以得到我们需要的铸件。
2铸造工艺方案的确定
铸造工艺方案概括地说明了铸件生产的基本过程和方法。
它包括了造型和造芯的方法、铸型类型、浇注位置和分型面等的方案确定。
确定合理而先进的铸造工艺方案,对获得优质铸件,简化工艺过程,提高生产率,改善劳动条件,以及降低生产成本等起着决定性的作用。
2.1零件结构的铸造工艺性
生产铸件不仅需要采用先进的合理的铸造工艺和设备,而且还要使零件的结构本身符合铸造生产的要求。
每一种铸造合金的铸件,都有其合适的壁厚范围,如果选择适当,既能保证铸件的机械性能要求,又方便铸造生产。
参照【1】中表1-3铸件尺寸在200*200~500*500范围时灰铸铁最小允许壁厚为6~10mm,本设计铸件最小壁厚为6mm,平均壁厚为7mm,符合设计要求。
参照【1】中表1-5,表1-6知本次设计铸件满足铸件壁的连接和圆角要求。
结合图纸,零件是变速箱盖,整体基本上对称,用砂型进行铸造,可以保证圆筒、肋、底座整体外轮廓相似成型。
综合分析知本铸件可以使用砂型铸造工艺进行铸造生产。
2.2浇注位置和分型面的确定
浇注位置是指浇注时,铸件所处的位置。
分型面是指两半个铸型相互接触的表面。
一般先从保证铸件的质量出发来确定浇注位置,然后从工艺操作方便出发确定分型面。
一些质量要求不高或者外形复杂,生产批量又不大,为了简化工艺操作,也可以优先考虑分型面。
2.2.1铸件浇注位置的确定原则
铸件浇注位置要符合铸件的凝固方式,保证铸型的充填,注意以下几个原则:
1)一般情况下铸件浇注位置的上面比下面缺陷多,所以应将铸件的重要加工面或者主要受力使用面等要求较高的部位放在下面,若有困难则可放在侧面或斜面。
2)浇注位置的选择应有利于铸型的充填和型腔中气体的排除,所以,薄壁铸件应将大的平面放在下面或者侧立、倾斜,以防出现浇不足和冷隔等缺陷。
3)当铸件壁厚不均,需要补缩时,应从顺序凝固的原则出发,将厚大部分放在上面或者侧面,以便于安放冒口和冷铁。
对于收缩较小的灰铸铁件,当壁厚差别不大时,也可以将厚部分放在下面靠自身上部的铁水补缩而不用冒口。
4)确定浇注位置时应尽量减少砂芯的数量,同时有利于砂芯的定位、稳定、排气和检验方便。
因此,较大的砂芯应尽可能使芯头朝下,尽可能避免砂芯吊在上箱或仅靠芯撑来固定[5]。
可采用多个铸件共用一个砂芯。
根据以上的浇注位置的选择原则,本铸件的浇注位置选在铸件的侧面,如工艺图所表示的位置。
2.2.2分型面的确定原则
分型面确立的基本原则是:
1)为了起模方便,分型面一般选在铸件的最大截面处,但是注意不要使模样在一箱内过高。
2)尽量将铸件的重要加工面或大部分加工面和加工基准面放在同一个砂箱内,而且尽可能放在下箱。
以保证铸件尺寸的精确,减少铸件的飞边毛刺。
3)为了简化操作过程,保证铸件尺寸精度应尽量减少分型面的数目,减少活块的数目。
4)为了便于生产,减少制造工艺装备的费用,分型面应尽量采用平直面。
5)分型面的选择应尽量减少砂芯的数目。
6)分型面的确定尽可能考虑到内浇口的引入位置,并使合箱后与浇注位置一致,以避免盒箱后再翻动铸型。
综合上述,在本次设计中,铸件是对称的结构,但是在对称的部分有加强筋如果以此来分型的话,不方便取模,故考虑到分型面选在最大截面处,将之间整体放在下箱。
如工艺图所示。
2.2.3砂箱中铸件数目的确定
当铸件的造型方法、浇注位置和分型面确定后,应当初步确定一箱中放几个铸件,作为进行浇冒口设计的依据。
一箱中的铸件数目,应该是在保证铸件质量的前提下越多越好。
本铸件高约137mm,长约212mm,宽约201mm,重约4.5Kg。
铸件的最小吃砂量a=30mm,b=50mm,c=60mm。
这里选用一箱一件,根据本铸件分型面的确定,我们可以先确定下箱的尺寸。
通过查表可以知道模型的最小吃砂量,根据最小吃砂量,可以先确定下箱的尺寸。
由表格我们可以查出最小的吃砂量,在根据表格我们可以选择标准的砂箱。
我们可以选用顶箱起模的震实式造型机Z146,砂箱最大内尺寸(长×宽×高)为350mm×300mm×200mm。
根据本铸件的大概尺寸,在本次设计中采用一箱一件。
因为铸件整个都埋在下箱,所以上砂箱的高度我们还要考虑到浇注系统才可以确定。
2.3工艺参数的选择
铸件的工艺设计,除了根据铸件的特点和具体的生产条件正确地选择铸造方法和确定铸造工艺方案以外,还应该正确地选择合适的工艺参数。
例如:
由于铸件浇注后要收缩,因此在做模样和芯盒时必须在尺寸上放出收缩率;铸件有的表面需要机械加工,在模样和芯盒上要考虑铸件的机械加工余量;为了便于起模和取芯,模样和芯盒上应有拔模斜度;以及最小铸出孔的尺寸等。
这些在进行铸造工艺设计时需要确定的工艺数据叫铸造工艺参数。
2.3.1铸造收缩率的确定
铸件在冷却和凝固过程中,体积一般都要收缩。
金属在液态和凝固过程中的收缩量以体积的改变量表示,称为体收缩。
在固态下的收缩量常用长度表示,称为线收缩。
由于铸件的固态收缩(线收缩)将使铸件各部分的尺寸小于模样原来的尺寸,因此,为了使铸件冷却后的尺寸与铸件图示尺寸一致,则需要在模样或者芯盒上加上其收缩的尺寸。
增加的这部分尺寸为铸件的收缩量,一般用铸造收缩率表示,可以用下式列出:
铸造收缩率k=(L模样—L铸件)/L铸件×100%
式中:
L模样——模样尺寸;L铸件——铸件尺寸
铸造收缩率主要和铸造合金的种类及成分有关,同时还取决于铸件在收缩时受到阻碍的大小等因素。
在决定铸件的收缩率时,应该充分考虑到各种因素的影响,力求比较正确的确定铸造收缩率的大小。
通过查得,在本次设计中材料为灰铸铁,其采用的铸造收缩率选为1%。
2.3.2机械加工余量的确定
机械加工余量是指在铸件加工表面上留下的、准备用机械加工方法切去的金属层的厚度,目的是获得精确的尺寸和光洁的表面,以符合设计的要求。
铸件加工余量的大小,要根据铸件的合金种类,生产方法,尺寸大小和复杂程度,以及加工面的要求和所处的浇注位置等因素来确定。
铸件加工面在浇注时的位置,一般上面比下面和侧面的加工余量要大些,铸面内表面则要比铸件外表面的加工余量大些。
该零件采用的材料是灰铸铁,选用时应考虑各厂的实际生产情况,对于机械化的大量生产,其加工余量可比表中数值小些,对于批量生产的重型机械铸件,则加工余量应比表中的数值大些,经分析综合选用以下数值作为本设计的的机械加工余量。
表4-1机械加工余量(mm)
铸件最大尺寸
浇注时位置
公称尺寸
≤100
>101~200
>200~301
>201~500
顶面
6.0
7.0
7.0
侧面
4.0
4.0
4.0
底面
3.0
3.0
4.0
由上表我们可以确定加工余量,本铸件的最大尺寸为212mm,由公称尺寸可以知道铸件的机械加工余量:
顶面7.0mm,侧面4.0mm,底面3.0mm。
2.3.3拔模斜度的确定
为了在造型和制芯时便于起模而不致损坏砂型和砂芯,应该在模样或芯盒的出模方向带有一定的斜度。
如果零件本身没有设计出相应的结构斜度时,就要在铸型工艺设计时给出拔模斜度。
拔模斜度的大小应根据模样的高度,模样的尺寸和表面光洁度以及造型方法来确定,见表4-2
表4-2拔模斜度
测量面高度(毫米)
金属模
a
α。
<20
0.5~1.0
1.30~3。
20~50
0.5~1.2
0.45。
~2。
50~100
1.0~1.5
0.45。
~1。
100~200
1.5~2.0
0.30。
~0.45。
根据上表所显示的数据,该铸件所需要的拔模斜度为:
测量面高度(毫米)
金属模
a
α。
50~100
1.0~1.5
0。
45~1。
2.3.4最小铸出孔
最小铸出孔的尺寸和铸件的生产批量、合金种类、铸件大小、孔处铸件壁厚、孔的长度以及孔的直径有关。
1.加工圆孔(结合参考书【1】中表3-24最小铸出孔为12~15mm)
灰铸铁铸件的最小铸出孔(mm)
铸件厚度
<50
50-100
100-200
>200
应铸最小孔径
30
35
40
另行规定
2.不加工孔
一般情况下应尽量铸出。
若孔径﹤30毫米(小批生产)或15毫米(大量生产),或孔的长度和孔的直径之比大于4时,则不便铸出。
3.参照以上标准,本设计中前后的两个通孔、底板上的圆孔和所有螺栓连接孔不用铸出,待铸造完成后再由机械加工钻孔。
在工艺图上有说明。
2.4砂芯设计
砂芯设计是铸造工艺设计过程中的一个重要环节,砂芯主要用于形成铸件的内腔和孔。
它对铸件的质量,铸造工艺过程以及铸造工艺装备都有直接的影响。
2.4.1砂芯数量的确定
一个铸件所需要的砂芯数量,主要取决于铸件的结构和铸造工艺方案。
由于制造砂芯时材料要求高,工艺装备比较复杂,因此,应该尽可能的少用砂芯。
根据后悬架铸模的结构和复杂程度决定使用2个砂芯。
2.4.2芯头的设计
芯头是砂芯的重要组成部分,其作用一般为定位、支撑和排气。
定位主要是通过芯头与芯座的配合,便于将砂芯准确的安放在砂型中;支撑主要是砂芯通过芯头支撑在铸型中,保证砂芯在它本身的重力和金属液的浮力作用下位置不变;排气主要是在浇注凝固过程中,保证砂芯中产生的大量气体能够及时的从芯头排出铸型。
一个砂芯的芯头能否满足砂芯对于定位、支撑和排气这三方面的要求,主要是由芯头的形式、个数、形状和尺寸决定的。
在满足砂芯支撑稳固、定位准确和排气通畅的情况下,芯头的数量越少越好。
2.4.2.1芯头的形式
根据芯头在砂型中的位置,可分为垂直芯头和水平芯头。
考虑到后悬架的内腔和外型较复杂,故将砂芯设计为两个,砂芯1#和2#配合在一起,砂芯2#为内侧的大砂芯。
砂芯1#为垂直芯头。
2.4.2.2芯头尺寸的确定
芯头横截面的尺寸,一般决定于铸件相应部位孔眼的尺寸,为了便于下芯合箱,芯头应有一定的斜度,芯头和芯座之间应留一定的间隙。
经查表得芯头的斜度分别为5°、10°,芯头与芯座的间隙为1mm。
由于本次设计过程中砂芯1#和2#芯头的尺寸较小,作用在芯头上的重力和浮力不大,因此不必验算芯头的尺寸。
2.4.2.3压环、防压环和集砂槽尺寸的确定
在大量的生产中,为了加速下芯合箱及保证铸件质量,在芯头的模样上常常做出压环、防压环和集砂槽。
压环用来阻止金属液钻进砂芯的通气道;防压环用来防止芯头压坏芯座的边缘后,散砂落入型腔;集砂槽用于存放散落的砂粒。
表5-1压环、防压环和集砂槽的尺寸(mm)
芯头直径D
垂直芯头
e
f
g
30—50
1.5
3
1.5
100—200
3
4
3
200—400
4
5
5
>400
5
6
6
2.5浇注系统的设计
浇注系统(gatingsystem,runningsystem)是铸型中液态金属流入型腔的通道之总称。
铸铁件浇注系统的典型结构如图所示,它由浇口杯(外浇口)、直浇道、直浇道窝、横浇道和内浇道等部分组成。
生产中常常因浇注系统设计安排不合理,造成砂眼、夹砂、气孔、粘砂、缩孔、缩松、浇不足、变形、裂纹、偏析等缺陷。
此外,浇注系统的好坏还影响造型和清理工作的繁简,砂型的体积大小和型砂的耗用运输量,非生产性消耗的液态合金用量等等。
所以,浇注系统与获得优质铸件,提高生产效率和降低铸件成本的关系是密不可分的。
2.5.1浇注系统类型及选择
2.5.1.1浇注系统的各组成部分
浇口杯
结构简单,制作方便,容积小,消耗的金属液少,能缓冲股流,撇渣能力小
直浇道
方便起模,金属液能较快充满,在直浇道中呈正压状态流动,减少吸气和卷渣
横浇道
渣粒能在横浇道中浮起,能够滞留渣粒,确保夹杂物不被吸入内浇道
内浇道
造成的吸动区域小,有助于横浇道发挥撇渣作用,模样制造方便,易于从铸件上去除。
2.5.1.2浇注系统类型选择
应采用的考虑本铸件采用湿型铸造且铸件本身较小的特点,以及考虑了浇注系统各组元的断面比关系,内浇道对铸件型腔的引注高度,浇道的结构等,选择封闭式浇注系统,其断面比例关系为F直〉F横〉F内。
特点为浇注开始后,液态合金很快充满浇注系统;铸件成品率高,撇渣能力较强,浇注初期也有一定的撇渣能力。
本次设计中采用封闭式。
2.5.2浇注系统断面尺寸的确定
2.5.2.1水力学近似计算公式:
计算浇注系统,主要是确定最小断面积(阻流断面),然后按经验比例确定其他组元的断面积。
封闭式浇注系统的最小断面是内浇道,以伯努利方程为基础的水力学近似计算公式是:
F内=G/(μ·t·0.31·Hp1/2)(cm2)
式中:
F内——内浇道总断面积(cm2);
G——流经内浇道的液态合金重量(Kg);
μ——流量总耗损系数;
t——浇注时间(s);
Hp——平均静压力头(cm)。
2.5.2.2流量系数μ的确定。
μ值的理论计算不仅繁琐,而且难以准确的计算,故多用实验方法或根据经验确定之,通常是查表获得。
本铸件为湿型薄壁复杂件,砂芯多,铸型阻力大,取μ=0.35.修正数值为:
①湿型薄壁复杂件,浇注温度要高+0.05②在铸型上需要安放横截面积大于内浇道总面积的通气孔+0.05③有两个内浇道,阻力加大,μ值取-0.05,所以μ=0.40
2.5.2.3铸件质量m的计算和流经内浇道的液态合金重量G
根据质量计算公式:
m=ρν可知可先计算出铸件的体积ν,然后再乘以灰铸铁密度ρ(ρ=7.2*103㎏/m3)
铸件可分为六部分来计算它的质量:
ν
①底座体积ν1
ν1=[212×(72×2+20)-(34.06+92)×(95+12)]×8=170236.6mm3
②空心圆筒体积ν2
ν2=1/4π×(462-302﹚×50=47728.0mm3
③盖子部分体积ν3
ν3=﹙85×90-50×60﹚×8=37200.0mm3
④薄壁的体积ν4
ν4=ν前后﹢v左右
=﹛[﹙80-46/2﹚﹢﹙22+6﹚×tan30º﹢﹙15-8﹚/sin60º]×6﹢[53.12+﹙15-8﹚]×6﹜×﹙95+2×6﹚﹢﹛1/2×[﹙125.8×sin30º﹚×﹙125.8×sin60º﹚﹢53.12﹢﹙15-8﹚+125.8×sin60º]×86.09﹜×2×8=262021.0mm3
⑤两个凸台体积ν5
ν5=1/4π×282×[﹙94-6-95/2﹚+﹙107-70﹚]=47720.8mm3
⑥肋的体积ν6
ν6=1/2×﹙98.57+81.25﹚×30×8×3+1/2×32×60.12×8×2=64735.2+15390.7
=80125.9mm3
铸件的总体积:
v总=ν1+ν2+ν3+ν4+ν5+ν6
=170236.6+47728.0+37200.0+262021.0+47720.8+80125.9
=645032.3mm3
所以铸件的总质量为:
m=ρν=645032.3×10﹣6×7.2=4.64㎏
流经内浇道的液态合金总重量为铸件重加上浇冒口重量。
而浇冒口质量约占铸件质量的20%到30%,所以G=1.2m至1.3m,所以G=5.5kg.
2.5.2.4浇注时间t.
查表可知S=1.85,所以t=4.34s
2.5.2.5确定平均压头Hp
浇注系统为底注式浇注系统,铸件浇注位置高度C=137mm,C=P自由液面至内浇道的高度H0=200mm,故:
Hp=H0-C/8=18.3cm
2.5.2.6验算型腔内铁水液面上升速度u
验算液面上升速度:
Vs=C/t,C为铸件浇注位置高度,C=137mm,求得Vs=31.6>20~30
满足要求。
2.5.2.7确定其他组元的横截面积
由公式F内=G/(μ·t·0.31·Hp1/2)得内浇道总截面积Fn=5.5/(0.40×4.34×0.31×18.31/2)=2.4cm2由于有两个内浇道,故单个内浇道最小截面积为1.2cm2。
由于采用的是封闭式浇注系统,取截面比为:
Fz:
ΣFD:
ΣFn=1.2:
1.4:
1
可知:
内浇道总截面积2.4cm²横浇道总截面积3.4cm²直浇道截面积2.9cm²
验算内浇道截面积(经验公式):
∑Fn=
=2.45㎝2,计算结果相同于水力学公式计算。
2.5.3各浇道尺寸
直浇道
横浇道
内浇道
3模样及模板的设计
模样和模板是机器造型中使用的主要工艺装备。
模样在造型中主要形成铸件外表面的型腔。
模板是模底版、模样和浇冒口模等的总称。
模底板用于安装模样、浇冒口模等,造型后形成铸型的分型面。
3.1模样的设计
模样设计的主要内容:
选择模样材料,确定模样的尺寸和结构,以及模样在模底板的定位和紧固的安装方式等。
3.1.1模样材料的选择
目前制造模样的材料有:
木材、塑料、铝合金、铜合金、铸铁、球墨铸铁、铸钢、菱苦土以及泡沫塑料等。
金属模样是成批大量流水生产中目前采用最广泛的一种模样,本设计中采用的就是金属模样,金属模样一般是由铸造毛坯或钢材坯料经机械加工制成,从而保证模样表面粗糙度和尺寸精度。
金属模样材料有很多种,比如铸造铝合金,铸造黄铜,灰铸铁,钢材等,但我们选择材料,不仅仅要考虑其力学性能,我们还要考虑到生产批量、价格等,综合分析后,我选择铸造铝合金。
在本次设计中设计的是下模样,采用的模样材料铝合金,主要优点是轻便,不宜生锈,加工性好,表面光滑但是其强度较低,耐磨性差,硬度50~60HBS。
能够满足本铸件的工艺装备要求,铝合金的规格牌号选为ZL105,其收缩率为1%[9]。
3.1.2模样尺寸的设计
3.1.2.1模样尺寸的确定
模样的设计质量和制造质量,直接关系着铸件的几何形状、尺寸精度和表面质量,模样的设计和选择还直接影响着模样制造的工艺性和经济性,也直接影响着模样的使用要求和寿命,因此,在满足产品质量、满足工艺要求的前提下,正确的选择和设计模样是很重要的。
设计金属模样的尺寸除了考虑产品的零件尺寸外,还要考虑零件的铸造工艺尺寸,以及零件的铸造收缩率。
零件尺寸由产品零件图上查得,零件的铸造工艺尺寸包括各种工艺参数,芯头尺寸,浇冒口系统。
模样的尺寸=铸件尺寸×(1+K);式中K为铸件收缩率,查表为1%。
铸件尺寸=零件尺寸+加工余量+拔模斜度及其它加工余量。
对于芯头及冒口尺寸按原工艺图计算。
为了模样和底板的定位和紧固,在没有现成凸缘或凸耳不够用时,在模样内侧专门设计凸耳,并设置定位销孔,紧固螺钉孔。
尺寸如模样模板装配图上所示。
3.1.2.2模样类型的选择
金属模样的结构设计必须在保证产品质量满足铸造工艺要求的前提下,使模样由足够的强度和刚度,其坯料结构必须同时满足铸造工艺和加工工艺多方面的要求,以便于制造和使用,以及安装和维修。
金属模样的结构分为两类,即机器造型用金属模样和手工造型用金属模样。
本次设计采用机器造型用金属模样。
3.1.2.3模样技术要求
金属模样用于成批大量的生产时,对其表面光洁度和尺寸偏差应严格控制。
模样工作表面光洁度的确定:
模样工作表面为▽6,模样分型面为▽5,模样定位销孔为▽6。
模样装配凸耳采取内凸耳。
3.1.3模样的壁厚和加强筋
在保证模样使用要求的前提下,壁厚越小越好,以减轻重量和节省金属。
铝合金模样常用壁厚可参考表6-2选用。
高压造型中,为了防止模样的变形和压坏常将选取的壁厚50%到100%增加。
模样中加强筋的厚度可按壁厚的80%到100%选取,加强筋排列要力求均匀规则,尽可能使筋条错开以利于铸造。
筋条的高度对于高度小于的模样,可以减小,即不与分模面取平,