SiC与汽车教学内容.docx
《SiC与汽车教学内容.docx》由会员分享,可在线阅读,更多相关《SiC与汽车教学内容.docx(9页珍藏版)》请在冰豆网上搜索。
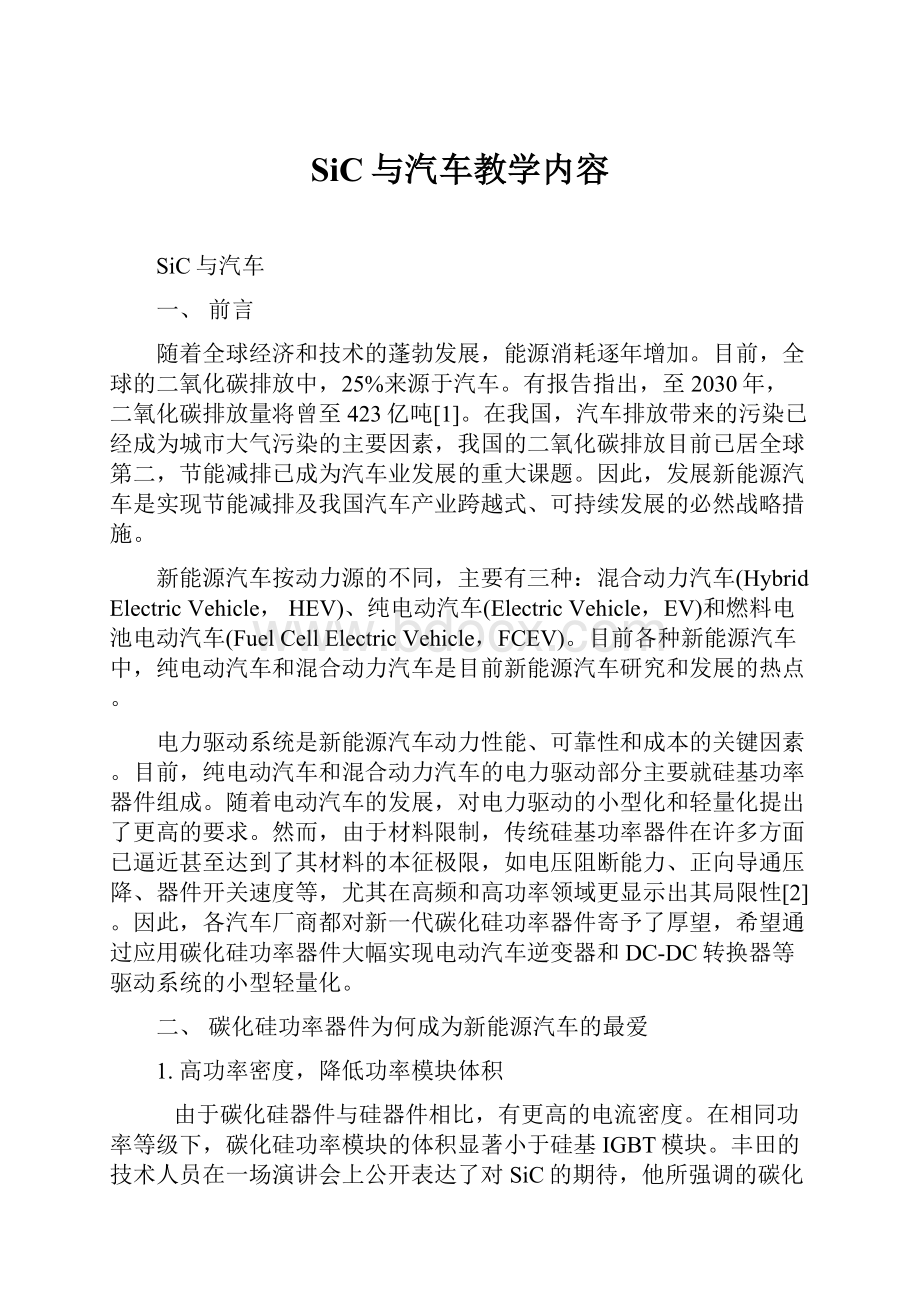
SiC与汽车教学内容
SiC与汽车
一、前言
随着全球经济和技术的蓬勃发展,能源消耗逐年增加。
目前,全球的二氧化碳排放中,25%来源于汽车。
有报告指出,至2030年,二氧化碳排放量将曾至423亿吨[1]。
在我国,汽车排放带来的污染已经成为城市大气污染的主要因素,我国的二氧化碳排放目前已居全球第二,节能减排已成为汽车业发展的重大课题。
因此,发展新能源汽车是实现节能减排及我国汽车产业跨越式、可持续发展的必然战略措施。
新能源汽车按动力源的不同,主要有三种:
混合动力汽车(HybridElectricVehicle, HEV)、纯电动汽车(ElectricVehicle,EV)和燃料电池电动汽车(FuelCellElectricVehicle,FCEV)。
目前各种新能源汽车中,纯电动汽车和混合动力汽车是目前新能源汽车研究和发展的热点。
电力驱动系统是新能源汽车动力性能、可靠性和成本的关键因素。
目前,纯电动汽车和混合动力汽车的电力驱动部分主要就硅基功率器件组成。
随着电动汽车的发展,对电力驱动的小型化和轻量化提出了更高的要求。
然而,由于材料限制,传统硅基功率器件在许多方面已逼近甚至达到了其材料的本征极限,如电压阻断能力、正向导通压降、器件开关速度等,尤其在高频和高功率领域更显示出其局限性[2]。
因此,各汽车厂商都对新一代碳化硅功率器件寄予了厚望,希望通过应用碳化硅功率器件大幅实现电动汽车逆变器和DC-DC转换器等驱动系统的小型轻量化。
二、碳化硅功率器件为何成为新能源汽车的最爱
1. 高功率密度,降低功率模块体积
由于碳化硅器件与硅器件相比,有更高的电流密度。
在相同功率等级下,碳化硅功率模块的体积显著小于硅基IGBT模块。
丰田的技术人员在一场演讲会上公开表达了对SiC的期待,他所强调的碳化硅功率器件的优点之一就是能实现功率模块的小型化。
以IPM(IntelligentPowerModule)为例,估计利用碳化硅功率模块,体积可缩小至硅功率模块的2/3-1/3。
(如图一所示)
图一. 碳化硅IPM与硅IGBT功率模块的体积比较
2. 低功率损耗,提高系统效率或工作频率
提高能源利用效率对许多厂商来说是令人头疼的难题。
而碳化硅器件具有大幅提高设备的能源利用效率的特质。
碳化硅功率模块与采用硅基IGBT的功率模块相比,可将开关损失降低85%(如图二所示)。
图二. 碳化硅功率模块和硅IGBT功率模块电力损耗比较
另外,可实现100kHz以上的高速开关,开关频率可高达硅基IGBT模块的10倍以上。
提高开关频率将显著的减小电感器、电容器等周边部件的体积和成本。
3. 良好的高温稳定性,显著减小散热器体积和成本
由于碳化硅器件的能量损耗只有硅器件的一半,发热量也只有硅器件的一半;另外,碳化硅器件还有非常优异高温稳定性,因此,散热处理也更加容易进行,不但散热器可以显著减小,还可以实现逆变器与马达的一体化。
图三. 采用碳化硅器件和硅器件需要的散热器对比
图3 为采用SiCSBDs的小功率EV 车载逆变器散热片体积和采用传统Si基半导体器件散热片体积的对比,可看出,采用SiCSBDs 器件散热片的体积大大减小[3]。
目前电动汽车一般包含两套水冷系统,一套是马达冷却系统,另一套是逆变器等电子设备的冷却系统。
通过采用碳化硅器件实现逆变器、马达一体化不但可以缩短逆变器与马达之间的布线距离,还能整合以往逆变器和马达需要分别配置的水冷却系统,重量和体积大为降低。
基于上述原因,SiC器件也被美寓为“重环保时代的关键元件”。
SiC功率半导体已成为节能、高效、环保的代名词。
为此,汽车业界对SiC的期待十分迫切,丰田汽车表示“SiC具有与汽油发动机同等的重要性”。
三、企业开发实例[4]
为满足汽车厂商的需求,多家企业已进行了相应的开发。
1. 电装在汽车技术展会上展出了输出功率密度高达60kW/L的逆变器。
这是电装与丰田共同研发的成果。
电装试制的逆变器在功率器件方面选用了碳化硅器件,同时采用自主开发的新型器件结构降低了电阻,从而抑制了电力损失。
另外,通过改进逆变器模块的内部布线,减小了模块整体电阻,发热量较原产品降低了68%。
试制的逆变器体积为0.5L,输出密度为60kW/L是在输出功率为30kW时得到的数据。
此时功率元件的温度约为180℃。
构成逆变器的器件出了碳化硅功率模块外,还包括驱动碳化硅功率器件的控制电路、散热片、冷却风扇及电容器等。
2. 罗姆和安川电极也共同试制了面向电动汽车的行驶系统。
该系统由马达及其驱动部分构成。
特点是,通过在驱动部分采用罗姆的碳化硅功率元件,使驱动部分和马达实现了一体化。
线圈切换部分、逆变器及其配备的栅极驱动IC和MCU等的控制器部分与马达部分组合在了一起。
通过实现一体化。
另外,通过采用碳化硅功率器件,逆变器的损失较硅功率器件的产品减少了一半。
四、国内量产碳化硅功率器件的厂家
国内碳化硅功率器件的研发工作始于20世纪末,经过十几年的摸索,已经积累了一定的材料与器件制作经验。
但与国外最高水平相比还有很大差距。
在产业化方面,国内主要仅有少数几家公司从事碳化硅材料的相关工作。
而从事碳化硅功率器件研发与生产的企业只有北京泰科天润半导体科技(北京)有限公司一家。
其技术团队具有多年的碳化硅功率器件研发生产经验,经过两年攻关,泰科天润研发的碳化硅肖特基二极管产品已成功量产,产品涵盖600V—3300V等中高压范围,其产品成品率达到国际先进水平。
碳化硅功率器件的量产,打破了欧、美、日长期以来的技术垄断,迈开了我国碳化硅功率器件产业化发展的第一步。
图四.泰科天润产品与国内公司产品实测对比
图五.泰科天润产品与国外公司产品实测对比
五. 结语
碳化硅功率器件以其优异的高耐压、低损耗、高导热率等优异性能,可以有效的实现电力电子系统的高效率、小型化和轻量化,被普遍认为是替代硅基功率器件最理想的新型半导体器件。
随着碳化硅材料及其功率器件制备技术的不断成熟,成本和可靠性的不断优化,我们相信碳化硅功率器件将在新能源等领域有着广泛的应用前景。
东京-丰田汽车公司,旨在扩大其在混合动力领域的领先技术,开发了一种新型半导体组件,进一步提高燃油效率,例如,通过此项技术可以提高普锐斯10%的燃油效率。
SIC功率半导体
作为世界最大的油电混合汽车制造商丰田表示,在测试车辆上已经取得了5%的燃油效率的提高,预计在和2020年左右商业化此项技术。
这种进步来自于新型的半导体功率控制单元,集成了混合动力汽车的电池、电机和发电机的管理。
这种新型的半导体组件只消耗现在常规组件十分之一的电能,并且可以使PCU的体积减小80%,丰田的工程师在新闻发布会上如是说。
左边是SI功率半导体 右边是SIC功率半导体
此种技术之所以有提高10%燃油效率的潜力,是因为在电池驱动马达时或再生制动向电池充电时,能达到更小的能量损失。
“提高燃料效率的关键之一是提高功率半导体组件的效率”,项目总经理丰田汽车电子产品开发部门KimimoriHamada说。
在竞争对手窃取分享以丰田普锐斯为先驱的混合动力车市场时,丰田正在加大力度研究新技术,挤出更好的英里/加仑。
更好的发动机,电池和空气动力学是未来一代混合动力汽车发展的丰田公式,包括下一代普锐斯。
丰田也打算通过提高耗电的PCU性能方面节约能量。
“我们的目标是在燃油经济性和小型化取得巨大的进步,”他说。
“这是一个非常具有挑战性的目标。
”
丰田公司12月在丰田市广濑开设了一个庞大的半导体开发工厂来研发引领新技术。
该工厂已经在生产应用于丰田现有的混合动力系统的半导体组件。
丰田历来是自主研发,从第一代普锐斯在1997年首次亮相开始。
丰田的新的技术是使用碳化硅制备器件,取代简单的硅,Hamada说。
碳化硅晶片有几个优点。
每当电流通过PCU组件时,功率就会损失产生热量。
事实上,丰田说,半导体组件的功率损失占混合系统中的所有功率损失的20%左右。
但是碳化硅半导体组件能量损失只有现行使用的硅基组件的十分之一。
此外,碳化硅半导体可以在更高的频率导通和关断。
这使得它们更高率,并且减轻了和减小了PCU中暂时储存电力的线圈和电容器。
在一个典型的PCU中,电容器和线圈占40%的体积。
因为需要的部件减少,使得PCU的整体尺寸可以减小80%。
在今天的发布会上,丰田展示在其目前的混合动力用的笨重的PCU,而旁边的新型PCU只有鞋盒大小。
丰田的目标是大约在2020年商业化碳化硅半导体组件,Hamada说。
但成本仍然是最大的障碍。
左为使用SIC功率半导体的PCU较右边使用SI功率半导体的PCU小很多
目前,碳化硅半导体的成本要比硅基半导体高“一个数量级”以上。
并且因为碳化硅是世界上最坚硬的材料之一,加工成晶片是困难和昂贵的,滨田说。
“仍有巨大的技术障碍,”他补充说,在2020年实现节能和小型化目标的70%,他就会非常满意。
丰田表示,碳化硅半导体将适用于混合动力或纯电动传动系统,可以将其连接到锂离子电池或镍氢电池。
在丰田中央研发实验室公司和丰田集团最大的零部件供应商—日本电装公司的协助下,丰田内部正在开发新的半导体技术。
丰田2014年5月20日宣布,该公司与电装和丰田中央研究所合作开发出了由SiC(碳化硅)材料制成的功率半导体。
计划在今后一年内开始利用配备开发品的试制车进行公路实验。
丰田表示,“希望到2020年能使采用SiC功率半导体的汽车投入量产”。
将来,计划使用这种半导体器件将混合动力车的燃效提高10%,并将动力控制单元(PCU)的体积降至原来的1/5。
左为MOSFET,右为二极管
丰田从2013年秋季开始,在以“普锐斯”为原型的试制车上配备采用SiC功率半导体的PCU开展实验。
PCU通过DC-DC转换器将电池输出的200V直流电压升压至650V,再通过逆变器转化为交流电提供给马达。
目前已确认可使燃效(JC08模式)提高5%以上。
今后还将继续改进,争取将燃效提高10%。
丰田此次展示的SiC功率半导体是二极管和MOSFET(金属氧化物半导体电场效应晶体管)。
二极管方面,展出了在4英寸基板上排列6mm见方器件的试制品,电流为200A。
MOSFET方面,展出了在相同尺寸的基板上排列5mm见方器件的试制品。
试制品为沟道型,耐压为1200V,电流为70A。
丰田打算在今后自己生产SiC功率半导体。
2013年12月,丰田已在从事电子控制装置及半导体等研发和生产的广濑工厂内建成了专门开发SiC半导体的清洁车间。