城轨车辆司控器故障处理.docx
《城轨车辆司控器故障处理.docx》由会员分享,可在线阅读,更多相关《城轨车辆司控器故障处理.docx(17页珍藏版)》请在冰豆网上搜索。
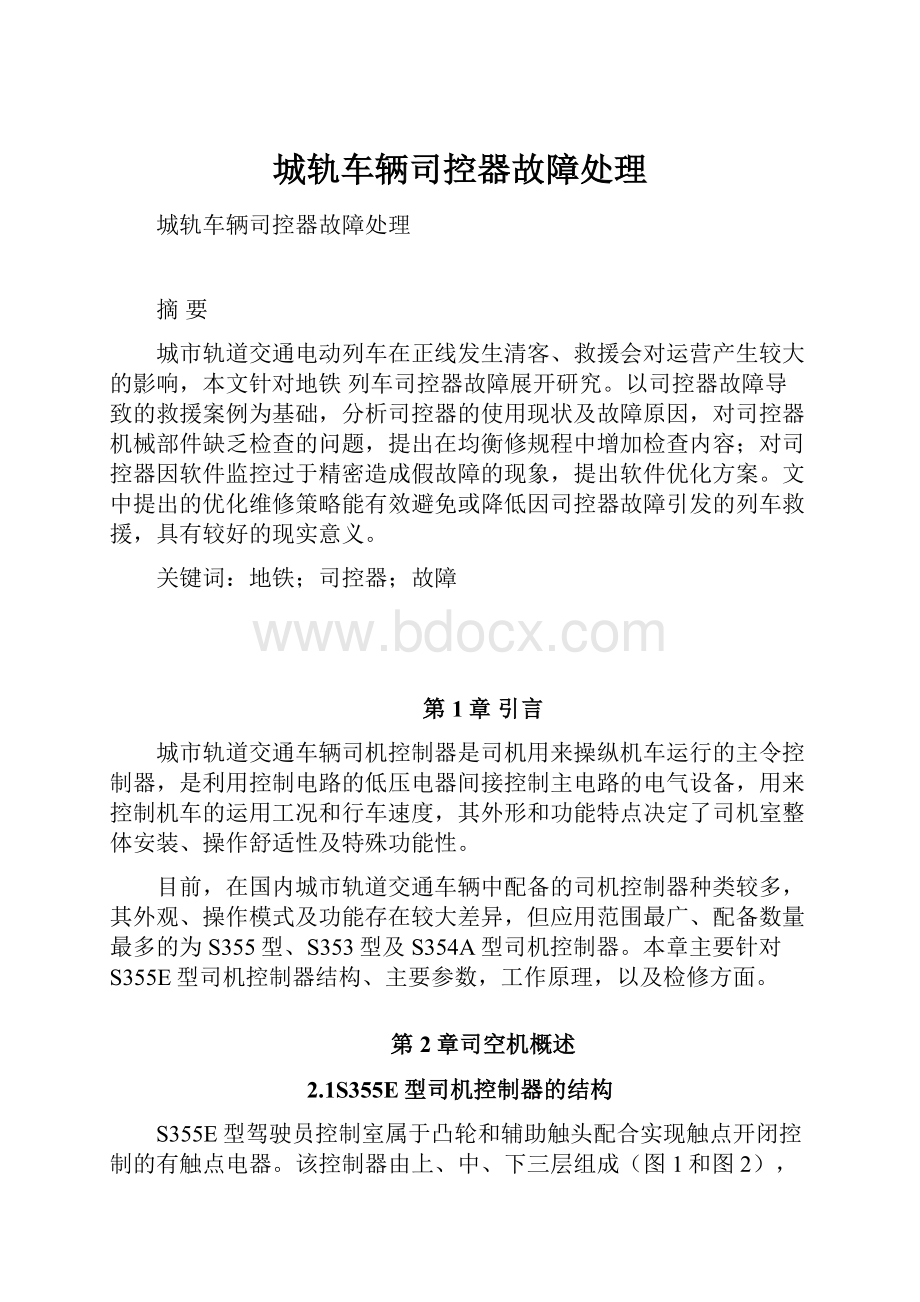
城轨车辆司控器故障处理
城轨车辆司控器故障处理
摘要
城市轨道交通电动列车在正线发生清客、救援会对运营产生较大的影响,本文针对地铁列车司控器故障展开研究。
以司控器故障导致的救援案例为基础,分析司控器的使用现状及故障原因,对司控器机械部件缺乏检查的问题,提出在均衡修规程中增加检查内容;对司控器因软件监控过于精密造成假故障的现象,提出软件优化方案。
文中提出的优化维修策略能有效避免或降低因司控器故障引发的列车救援,具有较好的现实意义。
关键词:
地铁;司控器;故障
第1章引言
城市轨道交通车辆司机控制器是司机用来操纵机车运行的主令控制器,是利用控制电路的低压电器间接控制主电路的电气设备,用来控制机车的运用工况和行车速度,其外形和功能特点决定了司机室整体安装、操作舒适性及特殊功能性。
目前,在国内城市轨道交通车辆中配备的司机控制器种类较多,其外观、操作模式及功能存在较大差异,但应用范围最广、配备数量最多的为S355型、S353型及S354A型司机控制器。
本章主要针对S355E型司机控制器结构、主要参数,工作原理,以及检修方面。
第2章司空机概述
2.1S355E型司机控制器的结构
S355E型驾驶员控制室属于凸轮和辅助触头配合实现触点开闭控制的有触点电器。
该控制器由上、中、下三层组成(图1和图2),上层(面板上)由钥匙开关1、推拉式控制手柄3、方向手柄5、紧急制动按钮4和位置标牌等组成。
中层由安装面板组成。
下层主要由连锁结构、转轴凸轮结构、辅助触头盒、调速电位器和电连接器等组成。
图1驾驶员控制器结构(尺寸单元:
mm)
1-钥匙开关;2-钢丝绳;3-控制手柄;4-警惕开关;5-方向手柄;6-换向轴;7-换向凸轮;8-控制轴;9-控制凸轮;10-控制辅助触头组;11-换向辅助触头组;12-电连接器;13-钥匙开关辅助触头组
图2司机控制器左视图和右视图
(a)方向手柄;(b)控制手柄
控制手柄和方向手柄各配置一套转轴、凸轮和辅助触头装置,分别称它们为控制轴机构和方向轴机构。
控制轴机构包括与控制手柄连接的控制轴8及其安装在该轴上的控制凸轮9、控制辅助触头组10等。
方向轴机构包括与方向手柄连接的换向轴6及其安装在该轴上的换向凸轮7、换向辅助触头组11等。
其中控制轴是一个实心细长轴,作内轴;换向轴是一根空心粗短轴,套在实心轴的外层,其配套凸轮分别套在两根轴上,手柄的转动便可带动相应的轴及凸轮转动,从而带动辅助触头开闭状态的变换。
2.2S355E型司机控制器的工作原理
1.控制功能及机械连锁关系
图3司机控制器手柄位置图
如图3所示,控制手柄有“牵引”区、“0”位、“制动”区、“快速制动”位四个区域,用于调节列车的速度。
控制手柄在0位、牵引最大位、制动最大位、快速制动位有定位,在这些档位之间为无极调节。
左侧为方向手柄,连接换向轴,用于控制车辆的运行方式及运行方向,共有“ATC”、“向前”、“0”、“向后”四个位置,这四个位置有机械联锁装置定位。
钥匙开关有0、1两个位置,用于激活驾驶员操纵台。
为了防止可能产生的误操作,确保列车设备及运行安全,驾驶员控制室的控制手柄、幻想手柄和机械锁之间有机械联锁。
在使用时,先由钥匙开关打开机械锁,才能对控制手柄和换向手柄进行操作。
当操纵列车时,先将钥匙开关打到“1”位,再由方向手柄选定列车的行车方向,再操作控制手柄来控制列车的速度。
在行车过程中,如需要改变列车的工况时,必须先将控制手柄放回“0”位后,才可进行方向手柄的操作。
如果驾驶员需要进行异端操作时,必须将本端驾驶员控制器的控制手柄置“0”位,换向手柄“0”位,钥匙开关回“0”位,锁闭机械锁,拔出钥匙,方可进行异端操作。
在列车的惰行期间,如果方式方向手柄移动到其他位置,牵引控制单元中牵引指令将失效,将启动紧急制动。
S355E型驾驶员控制器的钥匙开关、控制手柄盒方向手柄之间的联锁关系如下。
(1)钥匙开关在“0”位时,控制手柄和方向手柄均锁定在“0”位不动;反之,只有控制手柄和方向手柄均在“0”位时,钥匙开关才可由“0”位打到“1”位。
(2)钥匙开关在“1”位,控制手柄和方向手柄可进行操作,但控制手柄和方向手柄之间还存在以下互锁关系:
①方向手柄在“0”位,控制手柄被锁在“0”位不动。
②方向手柄在“前”位时,控制手柄可在“牵引”和“制动”区域范围内活动。
③方向手柄在“后”位时,启动列车手动折返模式。
④方向手柄在“ATC”位时,启动列车自动驾驶模式。
⑤控制手柄在“牵引”区、“制动”区或“最大制动”位时,方向手柄不能进行位置转换,只有控制手柄在“0”时,方向手柄才可在“前”位、“后位”和“ATC”位之间转换。
上述机械联锁要求由机械联锁装置来实现。
2.闭合表的实现
电逻辑即闭合表的要求由控制轴、换向轴、辅助触头盒及电连接来实现。
当推动控制手柄时,通过齿轮传动带动控制轴转动,轴上的凸轮随之转动,当凸轮的凸起位置转动到辅助触头盒的杠杆位置时,杠杆受到凸轮凸起部分的挤压而将与其连接的动触头顶开,此时使该触头盒的常开或常闭状态发生变化,从而使与该辅助触头盒相连接的控制线路得失电的状态发生变化;反之当凸轮凸起部分转到无凸起的地方时,由于触头盒自身恢复弹簧的作用,辅助触头盒的触点复原,从而使与该辅助触头盒相连接的控制线路得失电的状态恢复原样。
基于此原理,可根据电路原理图上驾驶员控制器各控制线路得失电的情况,在控制轴和换向轴上布置相应的凸轮凸起部分,如图4所示为某车型的驾驶员控制器方向轴的闭合表,图上ATC、F、O、R为方向手柄的四个位置,S10~S16为受方向轴凸轮控制的7个辅助触头,辅助触头下的长条块表示凸轮的凸起位置。
如图4可知,手柄在“ATC”位时,将使S10、S11、S12、S15、S16辅助触头状态发生变化;当手柄在“F”位时,将使S10、S11、S12、S15辅助触头状态发生变化;当手柄在“R”位时,将使S10、S11、S13、S14辅助触头状态发生变化。
图4S355E型司机控制器方向手柄闭合表
3.电位器的调节
控制手柄的调速主要是通过调节电位器电阻的大小来实现的。
其工作原理参见图5,其中的电阻R代表的是“牵引”区域或“制动”区域的单边电阻,两边的结构以“0”位为中心对称。
两个电位器的公共端接地,另一端经限流电阻接+15V直流电源,滑动端随控制手柄转动而转动,从而改变滑动端和15V电源端之间的电压,如图1-3所示,这三点电位信号由X2-2、X2-3、X2-5输出到控制主机,控制主机根据这一电压信号判断控制手柄的几位设定值。
图5调速点位器原理图
4.主要技术参数
(1)触头S826a/L额定电压
①额定电压(Ue):
DC110V;
②约定发热电流(Ith):
DC10A;
③额定电流(Ie):
DC1.0A
(2)触头特点
①接点位速动型;
②密封式结构;
③接点具有自净功能,可提高用作计算机信号时的可靠性;
(3)电位器特性
①输出电位器型号为:
FSGPW702X1043Ω;
②独立线性度:
1.0%;
③输出平滑性:
≤0.1%;
④绝缘电压:
500VAC,50Hz;
⑤工作温度范围:
—55~+80℃;
⑥额定功耗:
6W(25℃);
⑦电位器输出值。
输出电压:
15VDC;
0位:
3VDC±0.1VDC
牵引最大位:
8.3VDC±0.15VDC
制动最大位:
8VDC±0.1VDC
快速制动:
8.3VDC±0.15VDC
(4)手柄操作力
调速手柄操作力:
不大于35N
换向手柄操作力:
不大于25N
注:
调速手柄从制动最大位转到“快制”位时手柄操作力为40N±10N
(5)防护等级(污染等级3)
整机:
TP00;
触头S826a/:
IP00(接线部分);IP40(触点部分)。
(6)寿命
机械寿命>1×106;
电寿命>1×105。
(7)质量
质量约10kg
第3章司控机常见故障机原因分析
3.1司控机档位混乱
对司控器进行检查,发现在B4档位回B3档位时,手柄回B3但ATI仍显示B4,BC压力仍显示B4档位1.8bar。
B6回B5档位时也偶发该手柄与ATI显示不一致情况。
对司控器行程开关通断状态进行测量,发现手柄在B3和B5时相应点电压无法断开,司控器凸轮无法正常触发行程开关。
向前晃动手柄,可听到行程开关动作,故障消失。
因此判定造成该故障的原因是由于司控器凸轮在B3、B5档位时,凸轮不到位,无法正常触动行程开关,从此导致制动系统无法转换至正确档位。
B7→FB档位混乱现象,P4→P1和B1→B6相邻档位间的转动角度为5.5°,B6→F7及B7→FB的转动角度为7°,电压加载重叠区间为0.65°。
在B7→FB转换过程中,主控开关MC11/MC12/MC13与MC14无电压加载重叠区,由于凸轮触头爬坡,可能导致B1至B6中任何一种档位的跳变。
3.2司控器警惕按钮结构
在ATPM模式对标时,主控手柄在B1/B2/B3位时,ATI屏显示“紧急回路动作”。
故障为警惕按钮配线或警惕按钮行程开关存在问题。
将司控器拆下检查发现警惕按钮配线与转动轮用扎带捆绑位置接线断裂,即当在牵引档位及B1、B2档位时,此断裂接线两断头可以接通,故ATI屏不报“警惕按钮回路动作”,但当拉至B3时,此时随着控制手柄的转动,此断裂接线两端分开,此时ATI屏报“警惕按钮回路动作”,当拉至B4至FB位时,此时此接线两端头仍旧断开,但电路设置在B4至FB档位时,警惕回路不依赖此根接线,故在B4至FB档位ATI屏不报“警惕按钮回路动作”故障。
导线不再因手柄转动而磨损,可杜绝因导线磨损造成的故障、无需专门定期检查和更换警惕按钮导线、减小维护工作量及维护材料成本;增加带滚轮架的速动开关,有机械过压保护结构功能,结构更可靠、机械寿命更长,并统一了整机使用的速动开关型号。
3.3级位错乱
通过现场试验,认为级位错乱的原因主要有2类情况:
第一类是在级位切换时由于某些原因导致行程开关滚轮未完全运行至凸轮的凹面或凸面,即行程开关爬坡,最终使行程开关未按照要求充分动作;第二类是由于司控器上相关行程开关动作不同步导致级位错乱。
下面将结合现场实际对上述2种原因引起的司控器级位错乱现象逐项进行分析说明。
1.由于行程开关滚轮爬坡导致的级位错乱
如上所述,司控器级位的转换是通过凸轮的凸面和凹面与行程开关滚轮的接触来控制行程开关的开闭来实现的,但由于某些原因行程开关未按照设计要求充分运行至凸轮的凸面或凹面,即行程开关运行至凸面与凹面的过渡处(爬坡),导致行程开关未按照要求动作,从而出现了主控手柄所处的级位与TCMS屏上显示的级位不一致的情况。
当司控器手柄从B3拉至B4时,此时3个行程开关(MC11/MC12/MC13)中只有MC13动作,即行程开关滚轮从凸轮的凹面滚动至凸轮的凸面,但当MC13滚轮未完全滚动至凸轮的凸面时,此时滚轮停止在凸轮的坡上,MC13未动作,仍旧为“010”,此时虽然控制手柄位置推至B4位,但TCMS屏仍旧显示B3位。
同样,在从B5拉至B6时,此时TCMS屏上显示B5也是此道理。
通过对现场出现行程开关滚轮爬坡的原因进行分析,概括出如下3种情况。
(1)由于凸轮与凸轮轴之间安装松动导致的行程开关滚轮爬坡司控器凸轮套在凸轮轴上,凸轮轴为六棱角形状,同时凸轮轴为金属材料,凸轮为树脂材料,这样要保证凸轮在凸轮轴上安装紧固无松动是比较困难的,并且司控器使用较长时间后,此时凸轮与凸轮轴摩擦、振动,这些都可能导致凸轮在凸轮轴上的安装出现松动,导致凸轮在凸轮轴上有微小转动。
当单个凸轮出现了微小转动就会出现司控器在级位转换时行程开关爬坡,最终出现级位错乱。
(2)由于凸轮齿形异常磨耗使行程开关不能正常动作导致的行程开关滚轮爬坡由于行程开关在凸轮上长时间动作,尤其是当行程开关滚轮出现动作不灵活,在进行级位切换时滚轮与凸轮面之间的滚动摩擦(静摩擦)变成了滑动摩擦(动摩擦),从而使凸轮外形轮廓变形,这样在级位转换时,也会出现行程开关滚轮爬坡的情况。
(3)由于在相邻级位之间行程开关在凸轮圆周方向运行的距离太小导致的行程开关滚轮爬坡。
由于司控器的外形尺寸受司机控制台尺寸的限制,司控器凸轮直径就受到了限制,在这种情况下当司控器级位较多时,就会导致在相邻级位切换时,行程开关滚轮在凸轮上的圆周方向运行的距离变短,这样就容易出现行程开关滚轮爬坡的情况,尤其是当发生上述2种情况时,就更容易出现此问题。
2.由于司控器上各行程开关动作不同步导致的级位混乱
为避免由于行程开关不同步导致级位错乱问题,在进行级位组合时,两相邻级位之间切换时采用循环码,即两相邻级位之间切换时只有一个行程开关动作。
但地铁1、2号线车辆司控器在B1~B7之间采用循环码控制,而B7与FB之间切换时,未采取循环码(由于3根控制线高低电平组合已经用完)。
在B7与FB之间切换时4个行程开关均动作。
同时,为保证故障导向安全,逻辑设计只要MC14行程开关动作,就为FB级位,此时与行程开关MC11、MC12、MC13无关。
这样要保证切换准确,必须保证MC14行程开关提前动作或4个行程开关同时动作。
但实际行程开关动作是个范围值且由于行程开关的安装精度等问题,4个行程开关很难同时动作,只要MC14行程开关后动作,这样都会出现级位错乱的问题。
在控制手柄从B7位到FB位切换时,TCMS屏上可能显示2级、4级或6级制动级位,这样当缓慢拉动控制手柄从B7位到FB位时,此时从双针压力表看出制动缸压力先降低,然后升高,并且每次降低的制动压力不尽相同。
这样就可以解释为何在地铁1、2号线车辆上司控器在从B7向FB拉时双针压力表压力先降后升。
3.4司控器卡滞故障
1.手柄晃动较大
(1)手柄晃动较大的主要表现有:
司机对手柄进行牵引操作或调速操作时,因手柄太松,而造成手柄晃动较大,切换到档位时定位不准,不能正常咬合进行自锁。
(2)手柄晃动较大的的原因分析:
①司机在对机车的控制过程中,对手柄的使用率较高,导致了手柄在长期的使用过程中出现一定的磨损;②联锁杠杆在长时间的投入使用后,会导致零件变形,而出现限位滑块孔出现误差,甚至无法自锁。
2.司控器手柄卡滞
(1)司控器手柄卡滞的主要表现有:
①联锁杠杆过于高的端部高度,阻碍了滑块的滑动轨迹,因此造成的定位凸轮,导致单元手柄转换困难,进而形成手柄卡滞;②司控器与滑块之间发生较为严重的摩擦,导致手柄的转动较为困难,甚至出现卡滞的现象;③当换向手柄处于“0”位时,制动手柄被锁死、卡滞在制动的“0”档位上,无法再继续进行制动或牵引操作。
(2)司控器手柄卡滞的原因分析:
①联锁杠杆的局部抬高,进入到滑块的滑动轨迹里,影响滑块的正常滑动,进而导致了手柄卡滞;②联锁杠杆的转轴摩擦力较大,即便是在弹簧力与自重的双重作用下,其转动灵活性仍然不足,导致底部凹槽无法准确、顺畅的贴合定位轮;③定位弹簧力偏小,因此在控制定位的过程中,由于压迫较大,造成弹簧的弹力不足,不能与联锁杠杆底部凹槽进行准确、顺畅的贴合;④手柄的转动角度不够,导致速度手柄的提升高度不够,造成手柄卡滞;⑤在控制手柄中,设定速度时,滑块与挡片之间相互发生干涉,而导致手柄卡滞。
第4章司控机常见故障处理
4.1档位混乱的处理
控制手柄档位划分较细,当控制手柄在相邻两档间转动时传动至凸轮的转动角度不大,加上零件加工精度、组装调试精度、凸轮松动等原因,进而造成触头“爬坡”现象”。
为增强操作司控器速动开关通断的可靠性,改善凸轮“爬坡”导致相邻档位变换不可靠,对凸轮的设计进行以下改进:
(1)控制手柄至控制凸轮件的传动比由1:
1.5改为1:
2.2,通过对两项角度调整达到改变的结果,具体角度调整方式见表1。
档位
整改前
整改后
手柄位置
凸轮位置
手柄位置
凸轮位置
P4
25°
37.5°
25°
55°
P3
19.5°
29.25°
19.5°
42.9°
P2
14°
21°
14°
30.8°
P1
8.5°
12.75°
8.5°
18.7°
N
0°
0°
0°
0°
B1
8.5°
12.75°
8.5°
18.7°
B2
14°
21°
14°
30.8°
B3
19.5°
29.25°
19.5°
42.9°
B4
25°
37.5°
25°
55°
B5
30.5°
45.75°
30.5°
67.1°
B6
36°
54°
36°
79.2°
B7
43°
64.5°
43°
91.3°
FB
50°
75°
50°
110°
表1整改前后的手柄和凸轮位置
(2)凸轮采用新式的嵌套结构,可有效改善凸轮的松动。
图6新式与原凸轮结构对比
(3)B6→F7转动角度缩小至5.5°,B7→FB转动角度扩大至8.5°电压加载重叠区间扩大至3.95°。
在B7→FB过程中主控开关MC11-MC14应出现同时接通区域,目的是实现MC11/MC12/MC13触头动作之前,MC14触动行程开关,完成B7→FB的档位转换,避免了凸轮爬坡造成的档位混乱。
4.2司控器警惕按钮故障处理
(1)原警惕按钮结构中,警惕按钮开关固定在运动部件上,其导线会随手柄的转动而运动,导线易磨损;新警惕按钮结构中,按钮开关固定在静止的侧板上,不会随手柄的转动而运动,导线不易磨损。
(2)新警惕按钮结构中使用了带滚轮架的速动开关,与其余的钥匙侧、换向侧、控制侧的速动开关型号一致。
(3)结构差异:
原警惕按钮行程约等于4mm,新警惕按钮行程约等于6.4mm。
虽结构有差异、行程范围有差别,两种结构的操作力范围相同,尽量避免出现手感差异。
司控器是地铁车辆换向、调速的主令电器,与牵引和制动系统连接,给变流器提供可识别的电机转向信号及转速信号。
司机控制器利用控制电路的低压电器来间接控制主电路的电气设备,其动作的好坏直接影响到列车的平稳操纵以及各种工况的实现。
根据运营中出现的故障,从设计、生产和管理等各方面进行了改进,降低司控器的故障率。
4.3级位错乱
1.由于凸轮松动导致的级位错乱的整改方案
关于凸轮与凸轮轴之间安装出现的松动问题,通过调研发现,部分城市地铁车辆司控器凸轮与凸轮轴均为金属材质,并且为一体式结构,这样凸轮与凸轮轴就不会出现相对活动的情况,从根本上解决了凸轮松动导致的级位错乱问题,这样整改量太大,并且改造后的司控器需要重新进行设计及试验,供货周期长。
为确保一致性要求,同时又可以解决类似问题的出现,增购车辆的司控器对于凸轮松动问题进行了如下改造。
在凸轮与凸轮轴接触位置增加了凸轮内圈,此内圈材料与凸轮材料相比硬度较差、但韧性好。
这样凸轮外圈硬度好,保证了凸轮与行程开关滚轮之间的耐磨性要求,凸轮内圈的韧性好,保证了凸轮与凸轮轴配合紧固的要求,同时这样可以通过凸轮外圈与凸轮内圈,以及凸轮内圈与凸轮轴之间的缓冲将凸轮轴与凸轮在转动时的冲击进行吸收,解决了凸轮轴在长时间转动时与凸轮出现松动的问题。
2.相邻级位之间行程开关在凸轮圆周方向运行的距离太短导致级位错乱
关于相邻级位之间行程开关在凸轮圆周方向运行的距离太短导致级位错乱问题,根本原因是由于凸轮的周长有限,但司控器级位划分较密集,这样导致了行程开关滚轮在凸轮周向行程太短,容易出现行程开关滚轮爬坡,最终导致行程开关不动作。
为解决此问题,主要有2种方案。
(1)增大凸轮直径
车辆司控器凸轮直径为80mm,当将此凸轮直径变大至100mm或更大,这样在其他设计不变的情况下就可以解决凸轮滚轮爬坡的现象。
但考虑到司机台人体工程学设计,司机台上安装司控器的空间有限,将凸轮变大,直接影响司机台上安装司控器的尺寸,并为确保一致性要求,增大凸轮直径尺寸不可取。
(2)增大控制手柄扇齿与凸轮轴上的圆齿传动比
在其他设计不变的情况下,将控制手柄扇齿与凸轮轴上的圆齿传动比变大,这样在控制手柄转动同样的角度情况下,凸轮的转动角度变大,从而使行程开关滚轮在凸轮上的周向行程变大,这样可以解决由于行程开关滚轮爬坡导致的级位错乱问题。
增大控制手柄至凸轮间的传动比,可在手柄转动角度不变的情况下加大凸轮转动工作角度,减小分布在凸轮上挡位的密度,从而可加大触头在由接通到断开时触头在断开位置的角度裕量,进而可有效降低行程开关触头“爬坡”的可能性,因此需尽量增大手柄至凸轮间的传动比。
由于受司控器结构及尺寸限制,所有控制侧凸轮两侧均装有触头,凸轮单侧最大可工作角度<180°,因此最大传动比必然<180/(50+25)=2.4,由于图中(左侧触头的)FB位和(右侧触头的)P4位间不能交叉且要保持一定角度,因此传动比最大可改为1:
2.2。
将控制手柄扇齿与凸轮轴上的圆齿传动比由1:
1.5变为1:
2.2后行程开关滚轮在凸轮周向方向的滚动距离比较。
3.由于凸轮齿形异常磨耗使行程开关不能正常动作导致的级位错乱的整改措施
为防止此类问题的发生,需要对司控器凸轮材料进行研究,对于新线车辆而言,应选取耐磨性较好的材料或使用金属材料对此凸轮进行加工。
对于既有线路的车辆而言,需要加大司控器凸轮表面清洁以及检查行程开关滚轮动作是否灵活的频次。
4.由于司控器上各行程开关动作不同步导致级位错乱问题的整改方案
车辆上出现司控器级位由B7拉至FB位的过程中TCMS显示各种级位的问题,通过分析制动级位编码表不难看出,此问题是由于在司控器从B7拉至FB位时需要4个行程开关动作,此时只要行程开关MC11、MC12、MC13、MC14动作不同步,并且MC14后动作就会出现级位错乱的问题。
针对此问题,现场提出2种整改方案:
(1)B1级位至FB级位统一进行循环码编码通过上面的分析,1号线车辆上出现司控器级位由B7拉至FB的过程中TCMS显示各种级位的原因为控制手柄从B7(1110)拉至FB(xxx1)时4个行程开关状态均变化,只要此4个行程开关未按照要求先后动作就会出现级位混乱,并且各行程开关先后动作的组合不同,级位显示也就不同,故考虑将FB和B1~B7统一进行循环码编码,如表4所示,即将各制动级位状态由4个行程开关状态组合来决定,这样从B7(1110)至FB(1111),只有1个行程开关(MC14)动作,此问题就可以解决。
通过分析,新方案的确可以解决现场级位混乱的问题,但考虑到制动系统的设计都是故障导向安全的理念,之前的设计方案中FB级位只有1个行程开关(MC14)控制,而整改的方案中需要4个行程开关状态来控制,按照行程开关的故障发生的概率算,后者故障率是前者的4倍。
并且新方案中如果MC11/MC12/MC13中有任何一个误动作或故障,此时FB制动可能会失效(例如MC13故障,此时制动组合为1101,表4中没有此组合),存在安全隐患,故提出第2个方案。
(2)通过改变B7至FB之间的电压加载重叠区间原方案中P4→P1、N、B1→B6相邻级位间的转动角度为5.5°;B6→F7及B7→FB的转动角度为7°,电压加载重叠区间为0.65°。
而提出新方案中B6→F7转动角度缩小至5.5°,B7→FB转动角度扩大至8.5°,电压加载重叠区间扩大至3.95°。
这样控制手柄从B7拉至FB时,控制手柄还没拉到FB位置时MC14行程开关就已动作,此时ATI屏上显示FB。
同样,当控制手柄从FB位推至B7位时,控制手柄还没推至B7位,此时MC14已动作,并当控制手柄推至B7位时,MC11/MC12/MC13均动作,可正常显示B7级位。
这样就解决了现场存在问题,并且司控器的外形机械尺寸以及电气接口都无变化,备件的互换性好。
此方案在2号线增购车上试验,效果良好。
对于运营人员而言,司控器的日常维护也是非常重要的,当检修发现司控器出现不正常情况,应该及时进行分析故障,找出故障真正原因,并对所有司控器进行普查。
当故障是由于检修方法或检修周期设定不合理引起,则须及时修订检修规程并规范司控器检修标准及检