灵江大桥#0块施工工艺.docx
《灵江大桥#0块施工工艺.docx》由会员分享,可在线阅读,更多相关《灵江大桥#0块施工工艺.docx(25页珍藏版)》请在冰豆网上搜索。
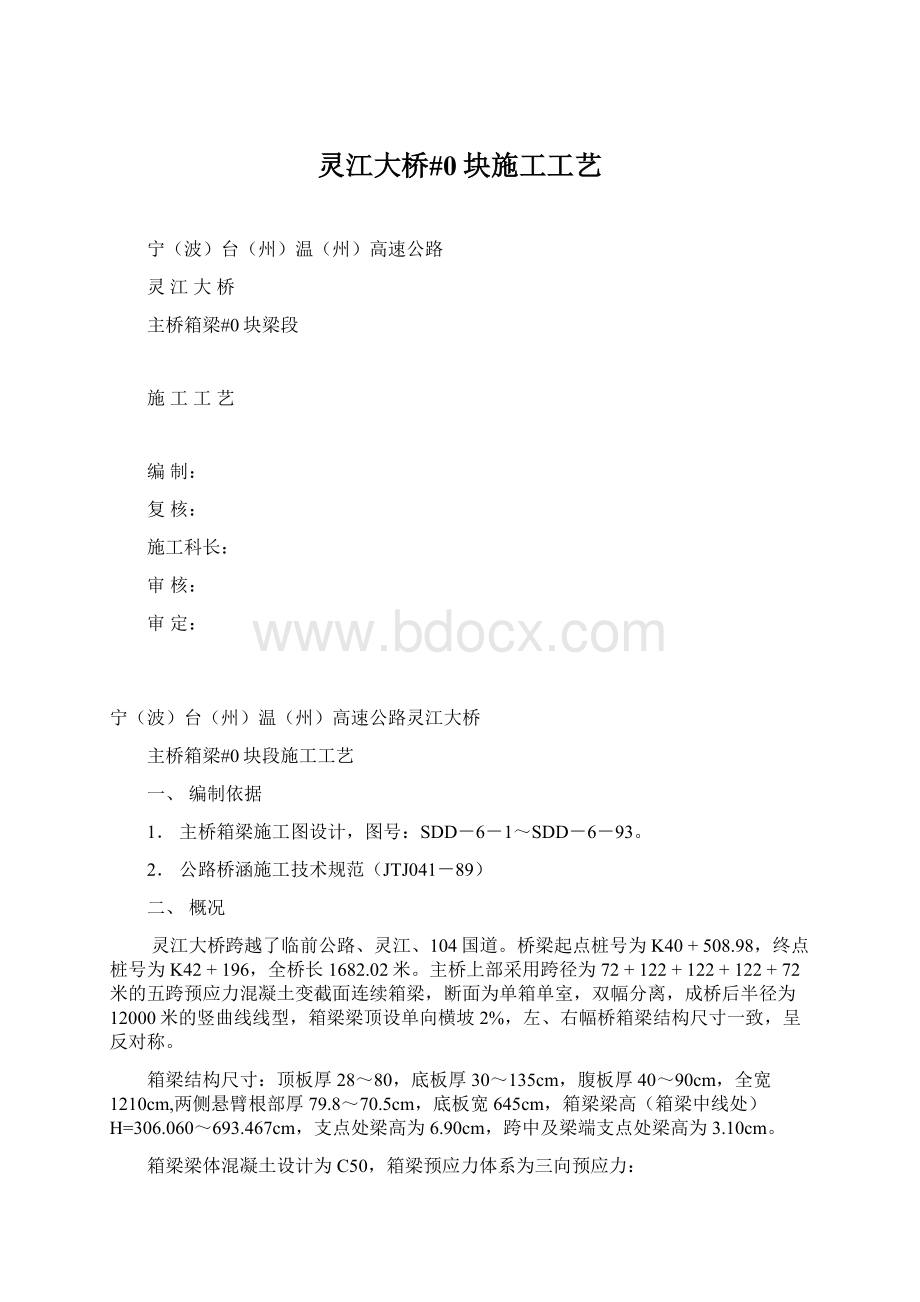
灵江大桥#0块施工工艺
宁(波)台(州)温(州)高速公路
灵江大桥
主桥箱梁#0块梁段
施工工艺
编制:
复核:
施工科长:
审核:
审定:
宁(波)台(州)温(州)高速公路灵江大桥
主桥箱梁#0块段施工工艺
一、编制依据
1.主桥箱梁施工图设计,图号:
SDD-6-1~SDD-6-93。
2.公路桥涵施工技术规范(JTJ041-89)
二、概况
灵江大桥跨越了临前公路、灵江、104国道。
桥梁起点桩号为K40+508.98,终点桩号为K42+196,全桥长1682.02米。
主桥上部采用跨径为72+122+122+122+72米的五跨预应力混凝土变截面连续箱梁,断面为单箱单室,双幅分离,成桥后半径为12000米的竖曲线线型,箱梁梁顶设单向横坡2%,左、右幅桥箱梁结构尺寸一致,呈反对称。
箱梁结构尺寸:
顶板厚28~80,底板厚30~135cm,腹板厚40~90cm,全宽1210cm,两侧悬臂根部厚79.8~70.5cm,底板宽645cm,箱梁梁高(箱梁中线处)H=306.060~693.467cm,支点处梁高为6.90cm,跨中及梁端支点处梁高为3.10cm。
箱梁梁体混凝土设计为C50,箱梁预应力体系为三向预应力:
纵向OVM-12群锚钢绞线束,单副桥束(全桥之半)共528根,其中顶板(负弯矩)束378根,底板(正弯矩)束120根,预留束24+6根。
最长顶板束H1为121.8741米,最长底板束MD10为85.4191米。
张拉控制应力分别为1350Mpa和1302Mpa二种。
横向:
桥面板为YBM15-3钢绞线束锚具(扁锚),单头张拉,间距58~92厘米,单付桥束共665根,单根钢绞线张拉控制力为195.3kN。
横隔板及底板处为OVM15-3群锚钢绞线束,单付桥束共92根,张拉控制力为585.9kN。
钢绞线设计为ASTM-A416-87a标准270K级高强度低松驰钢绞线,直径φ15.24mm,标准强度R
=1860Mpa。
竖向采用YGM精轧螺纹钢锚具,沿全桥箱梁腹板内布设,间距为0.3~0.8米,32精轧螺纹钢筋设计强度R
=750Mpa,张拉控制力为542.9kN,单付桥束共1832根。
主桥箱梁施工方法:
0号块和1号块在主桥#8、#9墩上和托架上立模浇筑,0号块先浇筑并张拉顶板束后,再立模浇筑1号块,其余块段采用挂篮悬臂浇筑,先形成#9墩“T”构,与边跨直线段合拢,再形成#8墩“T”构,合拢次边跨,最后中跨合拢,完成体系转换。
砼采用工地自产,用吊斗或用砼泵输送灌注。
由租用的50t水上吊船来完成施工。
主桥箱梁施工特点:
1.箱梁截面高,#0块高6.90米,砼灌注要采取相应措施。
2.箱梁跨度最大为122m,因此顶板和底板束最长可达121.9米和85.4米。
下料、编束、穿束和张拉均有一定的难度。
3.两个单位施工,以中跨合拢段分界,#8、#9墩以后为我处的施工任务,要加强与友邻单位的联系,调整好块段的施工标高,使其顺利合拢。
#0块梁段相关数据表
墩号
#8
#9
梁块号
#1
#0
#1
#1
#0
#1
梁块长(m)
2.50
2×4.50
2.50
2.50
2×4.50
2.50
梁块砼数量(m)
50.8
258.4
50.8
50.8
258.4
50.8
梁块砼重量(t)
132.1
671.9
132.1
132.1
671.9
132.1
段面(束段面)
97
(30)
98
(29)
98
(29)
99
100
(27)
101
102
(29)
102
(29)
103
(30)
137
(30)
138
(29)
138
(29)
139
140
(27)
141
142
(25)
142
(25)
143
(24)
箱梁顶标高(m)
29.098
29.087
29.087
29.077
29.067
29.055
29.044
29.044
29.031
27.960
27.923
27.923
27.890
27.857
27.823
27.788
27.788
27.750
箱梁厚(cm)
631
661.5
661.5
691.066
690
688.891
661.5
661.5
631
631
661.5
661.5
693.354
690
686.604
661.5
661.5
631
顶板厚(cm)
47.26
66.52
66.52
80
80
80
66.52
66.52
47.26
47.26
66.52
66.52
80
80
80
66.52
66.52
47.26
腹板厚(cm)
75
90
90
90
90
90
90
90
75
75
90
90
90
90
90
90
90
75
底板厚(cm)
87.3
90
90
136.066
135
133.066
90
90
87.3
87.3
90
90
138.354
135
131.604
90
90
87.3
顶板预埋孔道数(孔)
锚固束(m)
6
6
6
6
6
6
6
6
通过束(t)
78
84
90
84
78
78
84
90
84
78
备用束(YL)
6
6
6
6
6
6
6
6
6
6
二、#0块梁段施工工艺流程
#0块箱梁高,分两次灌注,第一次灌注为底板、腹板至顶板最下一根波纹管下10cm,第二次为部分腹板和顶板
#1块梁段施工工艺流程(#1块梁段采用二次灌注施工)
三、
墩旁托架及支座
1.托架
(1)本桥托架是#0块梁段和#1块梁段砼灌注过程中的平台及承重结构。
托架在挂篮悬浇砼施工时不参与受力。
(2)本桥#0块梁段长为9.0m(重671.9t),其中4.5m支撑在墩顶上,两端悬臂各4.5m/2支撑在托架上。
#1块梁段长为2.5m(重132.1t),全部支撑在托架上。
(3)本桥托架或称#0块梁段托架结构,由支承在承台上每柱承压约180t四根直径φ1.0m、壁厚10mm的空心钢管柱分置在顺桥向桥墩两侧,每柱布置顺桥方向各2Ⅰ55工字钢纵梁,每侧横桥向6Ⅰ55工字钢底模支撑梁和顺桥向4Ⅰ55工字钢侧模支承梁组成。
桥墩两侧托架间通过穿插越桥墩螺栓,该螺栓为32精轧螺纹YGM锚分设四层,来传递拉、压应力。
支承梁上再布设垫梁及木底模。
详见施工设计图Q4-LH-040图。
(4)压重
托架立柱支承在承台刚性基础上,为检验托架的施工质量及立柱的弹性变形(设计压缩量为4.5mm),宜进行压重试验,以策安全。
压重可以用水箱或类似水箱的设备进行,压重的重量拟用#1块梁段重量加模板重约为180t,压重点宜在托架#1块梁段的位置,应防止托架翘头变形。
2.临时支座设置
(1)临时支座按箱梁悬浇施工中的不平衡弯矩,是通过伸入到#0块箱梁中的墩顶锚固钢筋来实现的,箱梁#0块桥墩中的锚固钢筋是由墩顶的临时支座来传力的,临时支座中间设有锚固钢筋,所以50号砼50号硫磺砂浆均只能在墩顶现浇(按设计要求分层或分三层)施工,即先在墩顶上立模灌注临时支座底层砼(42.3/2cm)块,待强度达10Mpa时再在其上灌注5cm厚50号硫磺砂浆块,因其冷却时体积收缩很大,灌注时要略高一些。
硫磺在浆凝固后,再灌注上层50号砼(42.3/2cm)块,共同组成临时支座。
为保证接触密贴,各层面要求平整,上层砼顶面按梁底底面标高及梁底坡度抹平,并铺设薄膜隔离层。
(2)硫磺砂浆的配方参照我处其他桥施工的资料试验并调整配合比,待试件达到设计强度(C50)后再施工。
甲、配合比(参数):
硫磺
水泥
粉砂
780聚硫橡胶
44
11
44
1
乙、材质要求:
a.硫磺:
纯度97%,含水率1%,不含杂质,成粉状或粒径小于50mm的块状。
b.砂子:
用过30目筛的粉砂,含泥量小,无杂物,含水量<0.5%的干砂,可采用炒干、烘干、晒干等办法脱水。
c.水泥:
合格的525号水泥。
丙、施工注意事项
a.按重量配合比,称取各项原料。
b.将硫磺放入锅中,小火加热,不断的搅拌,加热熔化至130℃。
c.将水泥和干砂均匀的加入熔化了的硫磺内,不停的搅拌,加热至150℃~155℃.
d.将780聚硫橡胶均匀的加入,加强搅拌,严格控制温度在170℃以内,以免起火燃烧。
e.加热至完全脱水后(即表面无气泡),降温至140℃,浇入模内。
f.硫磺的熔点为96℃,燃点为180℃,遇明火易燃,在熬制过程中严格控制在170℃以内,以免燃烧,燃烧过的硫磺砂浆,强度已降低而脆,所以不得使用。
g.按上述配比的硫磺砂浆性能:
比重2.16~2.28;抗压强度40Mpa;
抗拉强度5Mpa;抗折强度10Mpa。
h.直接购置硫磺胶泥灌浇临时支座,熬制时不必加任何材料,施工更为方便。
(3)临时支座拆除
a.临时支座的拆除,必须在正式支座能够承受正压力后进行,用喷灯烧熔化硫磺砂浆夹层,再割断锚固钢筋。
b.先在硫磺砂浆夹层中预埋电阻丝,拆除时再通电熔化硫磺砂浆层,然后割断锚固筋。
c.拆除临时支座时,须在临时支座与永久支座间采取隔热措施,以防永久支座受热变形及损伤。
3.正式支座
(1)本桥主桥各墩采用GPZ系列盆式橡胶支座,用于#8、#9墩为GPZ30000SX(双向)和GPZ30000DX(单向)活动支座各一套,#10墩GPZ4000SX(双向)和GPZ4000DX(单向)活动支座各一套。
位移量纵向±150mm,横向±15mm。
主墩支座上下盆中心线应重合,边墩支座在大气温度15℃时,上盆中心线偏离下盆中心线25mm(远离河心方向)。
(2)正式支座安装
在#0块梁段和边跨直线段底模铺设前,正式支座须就位,其要点如下:
a.盆式支座安装前应拆箱作全面检查,看零部件有无丢失、损坏,然后进行清洁。
除去油污,特别是不锈钢板与填充四氟乙烯板的相对滑移面应用丙酮或洒精仔细擦洗干净。
如设计需在滑动面间涂抹硅脂时,应按设计要求进行,支座其他各部件也应擦洗干净。
支座内不得涂刷防锈油,擦洗应在低温时室内进行,防止四氟乙烯板和橡胶板因日照膨胀变形后无法入盆安装。
b.支座安装标高必须符合设计要求,保证二个方向平面水平。
c.支座中心线与箱梁中心线应保持平行。
d.支座上下各部件纵、横向必须对中,活动支座纵向上摆设偏量必须与设计计算值相符。
e.一切非工作面(除上顶面和下底面外)均应作防锈处理。
油漆采用红丹一度灰漆二度。
f.支座安装可事先将垫石抹平到设计标高,或预留30mm砼不灌注,用铁楔抄垫,使之符合设计标高。
g.支座安装就位经检查合格后,在顺桥向两侧用4φ20圆钢将支座上下摆底板前后临时点焊联结。
待支座锚固螺栓灌浆后,再解除,并补填防锈油漆。
(3)灌注箱梁时必须用薄膜将支座遮盖严密,不得使砂浆及其它杂物进入支座,影响支座性能。
(4)箱梁合拢后,全桥体系转换前,支座底板预留30mm的空隙内压浆(或干砸砼)填实,支座锚栓孔按设计要求填筑,若设计无要求采用与箱梁同等能砂浆(或球氧树脂砂浆)填筑使全桥体系转换后正式支座受力。
(5)在#0块(含#1块)砼达到设计强度后,拆除支座的铁抄楔,使盆式支座悬空不受力,由临时支座受力支撑。
四、模板
1.为了保证砼的密实、光洁及砼下料顺利,宜在外侧模板上安装附着式震动器,呈梅花形布置。
在外模与底模交接处置以20×20mm三角木条,以保证砼外表线型。
2.内外模安装前均应涂脱模剂,模板棱角及拼接处,用油灰刮平,打光,涂脱模剂。
端模必须保证波纹管孔道位置准确,线形符合设计要求,应保证伸出模板的波纹管完好,以便与下一段波纹管联结。
3.#0、#1块梁段砼分两次灌注,内模分两次安装,位置应准确,内模二次拼接面上应将砼残渣及污损清理修整好后再安装,并塞缝完好防止漏浆。
4.内模下梗肋与底板交接处两侧要增加约30cm宽的底板水平顶模,以增加腹板砼上冒的阻力。
5.模板安装允许误差:
梁段长±5mm梁段宽±10mm
梁段高±10mm支座预埋板±5mm
顶板厚±5mm腹板厚+5mm-0mm
底板厚±5mm腹板垂直度3%
孔道轴线3mm底板底标高±5mm
五、钢筋
1.箱梁所用非预应力钢筋进场时应有材质说明书,且必须符合GB1499-84有关规定,受力钢筋采用Ⅱ级螺纹钢筋,构造钢筋采用Ⅰ级光圆钢筋,凡需焊接的钢筋均应满足可焊性要求。
2.箱梁所用钢板和型钢应符合GB700-79规定的普通碳素结构钢(A3)及45号钢,型钢采用热轧轻型型钢。
3.所用钢筋抽检应合格,使用前将钢筋(钢板、型钢)表面的锈蚀、油渍、泥砂灰尘清除干净,再进行整直加工。
4.钢筋的加工、绑扎、接头等项应符合《公桥施规》有关规定。
5.根据《公桥施规》的规定,钢筋安装允许偏差为:
(1)受力钢筋间距允许偏差±10mm
(2)顺高度方向两排钢筋间距允许偏差±5mm
(3)箍筋间距允许偏差±20mm
(4)两层钢筋间距允许偏差±20mm
(5)整体结构中个别钢筋保护层允许偏差±5mm
(6)同一断面内接头数量应小于50%
6.有预应力钢束处钢筋位置力求准确,当相互干扰时,可适当挪动非预应力筋位置。
7.支座预埋板为20mm(边墩)和30mm钢板,φ20钢筋作为预埋锚固钢筋平行电焊多根。
因局部高温极易使钢板变形。
要采取预防措施:
其一用厚钢板或砼墩作底板,利用支座预埋板螺栓孔固定中间用型钢作扁担预压后电焊。
其二是电焊时先点焊,再跳越式断续焊后再焊满。
并且几块互相轮换电焊使钢板冷却。
8.挂篮在箱梁上顶板、下底板处的预留孔,应避开波纹管位置,所有因预留孔切断的钢筋,预留孔使用完后要恢复原样,挂篮底板后吊孔,局部应力较大,箱梁底板上下面均应增加水平钢筋,以策安全。
六、制孔和冷拉
<一>制孔
1.纵向OVM15-12锚具钢绞线孔道
(1)纵向采用0.3mm外径92波纹管制孔;
(2)波纹管的接头采用外套接方式,将长度为250mm,并大一号(内径增减5mm为一号)规格的波纹管旋在要接的波纹管上,并齐头,将另一根要接的波纹管与之对齐。
再将接头波纹管回旋在对齐的另一根要接的波纹管上,各套上125mm长度,两头均用胶布贴封。
伸出箱梁块段端头的波纹管一般不应少于250mm,为加劲和下次接头,可以先套上大一号的接头波纹管。
如砼端头外露的波纹管损坏,可将波纹管靠砼面切割,只可用小一号波纹管连接,这将减小孔径,穿束困难,张拉增加摩阻,施工中应尽量避免采用内套接法。
如图一
断面锚固孔道的喇叭管支承垫板预埋一定要与按设计线形预埋的管道垂直,不能偏装。
波纹管是直接套入与其直径相配套的喇叭管内,但波纹管头不能越过喇叭管压浆孔的内孔,为了防止渗浆,应在喇叭管内,波纹管口上用棉花或麻棉纱塞实,胶带封固。
(3)波纹管的驼峰处,应设置排气管。
每驼峰处设置一个,以便排气、排水而保证孔道压浆质量,排气管为φ20的普通铁管焊在半圆的薄铁皮背上,套在已开孔的波纹管上而成型。
如图二
(4)波纹管的直径为:
φ内85与OVM15-12钢绞线锚相配套,波纹管的埋置长度按设计要求下料。
2.横向YBM15-3锚和OVM15-3锚钢绞线孔道
(1)YBM15-3锚具其波纹管规格为65×22扁管,该锚为单头张拉,用于桥面板处横向张拉。
(2)OVM15-3锚具其波纹管为φ内50,用于非桥面即横隔墙及其底板处。
上述横向波纹管插入支承板接头管处要采取防止渗浆措施。
3.竖向32精轧螺纹钢筋YGM锚(图三)
(1)采用φ内49mm的铁皮管(如设计人员同意也可用φ内49mm高频管)。
(2)按设计图尺寸进行下料并编号。
(3)铁皮管与支承板的连接,在支承板上先焊上内径稍大(φ内52mm),长度L=50mm钢管,与铁皮管承插连接,接缝用胶布密封。
(4)32精轧螺纹钢筋穿入已连接好的支承板和铁皮管内,并用螺帽上好拧紧,支承板以外粗钢筋长节锚固端不小于 100mm,在张拉端不小于150mm(该尺寸与用于张拉顶的穿心张拉头核对后确定)。
购进的精轧螺纹钢未进行冷拉处理,在工地冷拉处理后,才准装入梁体内。
(5)
竖向YGM锚的压浆管φ24×0.75弯成型直接焊在张拉端铁皮管上,伸出桥面埋设,下端需两根一组,互相贯通,连通管为φ24×0.75直接焊在铁皮管上,使之一端压入一端排气。
如埋入箱梁块段内的锚管根数为奇数,有一组应是三根相联,即一端压入两端排气。
此法压浆方便,浆液可保证压满,不损坏模板,经验证明是可行的。
(6)因砼分二次灌注,第一次砼灌注时尚未绑扎桥面钢筋,YGM锚的上端是自由状态无法固定,只能用与#0块(或#1块)等长木带木一侧锯成符合设计位置的凹槽将YGM锚上端固定在模板上。
4.波纹管压重
(1)本桥箱梁纵向和横向均为波纹管制孔。
波纹管孔道跨度较大,由于波纹管本身自重轻,柔性大,易变形,在液态中易上浮等因素,施工中必须引起重视,除在制孔时按设计线型安装定位网钢筋固定其位置外,尚须防止灌注砼时,波纹管上浮或横向摆动而使管道偏离设计位置改变预应力束受力状态。
因此在灌注砼前须在直孔波纹管内穿入钢管压重,在曲线形波纹管内穿入钢筋或钢束压重,压重物两端支承在模板上。
(2)波纹管每束压重量为:
φ内85-----------6.7公斤
φ内50-----------2.6公斤
(3)波纹管压重在封模前完成,以便对波纹管进行检查。
砼灌注中要分别抽动内衬钢管和压重筋,以防漏浆后凝固。
<二>冷拉
1.竖向预应力采用32高强精轧螺纹钢筋,锚具为YGM锚,使用前应进行冷拉。
2.冷拉有两种做法:
来料钢筋先冷拉后按设计长度下料使用;另一种先按设计长度下料后,再冷拉。
冷拉使用的千斤顶,按规定进行标定,摩阻系数≤1.05,油表≮1.5级精度。
3.冷拉采用双控,以控制应力为主,冷拉应力为75kgf/mm2(拉力60.3t),冷拉延伸率为2~4%,持荷时间不少于2分钟,在持荷时间内由于钢筋伸长,吨位下降,应及时补足吨位,由吨位不再下降时计算持荷时间,若该拉伸率偏低,持荷时间可适当延长。
4.冷拉时速不宜过快,通常以每秒增加50kgf/cm2的钢筋冷拉力为宜。
接近控制应力时,尢应放慢加载速度,冷拉延伸率超过4%一般不宜使用。
若延伸率超标的钢筋数量较大时,经研究后才可继续进行冷拉工作。
5.冷拉后钢筋表面不得有裂纹和局部颈缩等不正常现象,应逐根检查外观。
6.自然时效处理,冷拉后需经48小时后才能进入工地安装,两周后才能进行预施应力。
7.冷拉后的粗钢筋要在室内存放,挂牌分规格张拉批次堆放。
防止锈蚀,按料单发货,先冷拉的先使用,不得混乱。
8.冷拉粗钢筋,施工中不得有施焊行为。
七、砼灌注
<一>砼配料要求
1.水泥、粗细集料、拌和用水、掺用外加剂等均应符合《公路桥涵施工技术规范》有关规定。
2.水泥用量:
箱梁采用C50混凝土,每立方水泥用量不宜大于500公斤。
3.水灰比:
掺用减水剂时,水灰比不得大于0.4。
4.掺用复合减水剂FDN用量不超过水泥用量的7.5‰,掺用木钙用量不超过水泥用量的2.5‰,也可选用其他附加剂(如上海麦斯特厂生产的附加剂)。
附加剂使用前加强检查,确保品种无误,计量准确,经过试验优选。
5.到达作业面的砼陷度:
下翼缘、支座底板、腹板(含隔墙)等部位为14~16cm(支座部位陷度尽量大一点),顶板及底板为12~14cm。
6.初凝时间不少于6小时,亦可按实际灌注砼量进行修正。
7.砼入模温度25℃~10℃。
8.为了加快箱梁块段的生产周期,要求混凝土三天强度大于设计强度的90%以上。
<二>砼灌注原则
1.在支架上灌注的梁块除#0块外还有#1块段共长14m,其组成为2.5m+9.0m+2.5m,分两次进行灌注,首先灌注中间9m段,达到强度并张拉、压浆后,再立模、扎钢筋灌注两侧2.5m块段。
2.梁段砼因其梁身高采用二次灌注法。
第一次先灌注底板及腹板根部和腹板部分(控制在顶板最下一根波纹管下沿10cm处),第二次灌注腹板部分及顶板和翼板。
3.振动体系
施工中采用以内部插入振动为主,外部侧振为辅的原则,在灌注底、顶板砼时采用插入式振动器,灌注腹板砼时,除采用插入式振动器外还利用安装在侧模上附着式振动器加以辅助。
内侧只安装在下半部,外侧全高度范围安装附着式振动器。
<三>砼灌注前检查
1.在砼灌注前,对模板、钢筋、预应力管道、预埋件、支座板及挂篮预留孔位置等按设计要求和施工规范进行检查验收,并办理签证手续后,方可开盘灌注。
2.模板内的杂物和钢筋上的油污应清除干净。
穿好波纹管内的压重筋后波纹管应全部检查一遍。
3.由于箱梁砼的数量较多,灌注的时间较长,要核对试验确定的水泥的初凝时间控制其灌注速度,使重复振动的影响因素减少。
<四>砼灌注顺序
1.灌注的原则是:
采用分段分层法;灌注顺序是:
由下而上,由低向高进行。
2.先灌注底板,由低处向高处进行,首先由支座处开始灌注,灌注中避免砂浆集中,防止收缩裂纹的产生。
3.灌注腹板采用水平分层,每层灌注厚度不大于30厘米。
4.第二次灌注顶板,为避免因顶板悬臂过大,模板支架变形而产生裂纹,顶板宜采用由外向内的灌注顺序。
<五>灌注注意事项
1.灌注砼作业必须保证不间断进行,其上、下层砼间隔时间,不能超过初凝时间。
2.灌注腹板时,砼经振动,易沿下梗肋冒出底板,此时应停止肋板或下梗肋的振动,并在内模下梗肋与底板交接处设置水平模板压住,防止砼大量冒出,超过底板。
其冒出的砼,亦不宜过早铲除,待腹板砼较稳定时再处理,以防腹板砼尚未凝结,因振动流失现象的发生,以腹板区段内出现沟洞(即脱裤)等质量问题。
3.主桥箱梁中跨中间向两边分设3.5%的纵坡,每侧箱梁设有单向2%横坡,在灌注顶板砼前,应严格检验顶板的标高,并保证表面平整度,使其符合设计要求。
4.振捣是灌注砼保证质量的关键工序,应分工明确,定岗定职,分区定人负责,并有专人检查配合,用竹片插捣、排气、检查。
侧模附着式振动器,采用瞬时振捣,均匀长时间振捣不利腹板砼的稳定。
内侧模(含隔墙处)应开窗。
既便于检查腹板砼的质量,又利于腹板区段砼用插棒振捣密实。
振捣以表面泛浆,光洁及气泡消失为度,严防漏振或过振,使砼外光内实。
<六>砼灌注作业的下料方式
1.底板处主要靠两端安装滑槽送入砼,或在桥面板上开洞用漏斗下料;严禁以腹板作溜槽灌注底板砼。
2.腹板及横隔墙可直接下料,但必须均匀,层厚约30cm,及时用插棒振捣,同时补以附着式振捣器侧振。
应采取防止碎石堆集一起,而水泥浆又集中表面的措施。
3.支座部分的下料主要由横隔墙处灌入,同时两端滑槽也送入部分砼,此处钢筋较密集,又是主要受力部位,此处