北汽福田模具生产作业规范.docx
《北汽福田模具生产作业规范.docx》由会员分享,可在线阅读,更多相关《北汽福田模具生产作业规范.docx(64页珍藏版)》请在冰豆网上搜索。
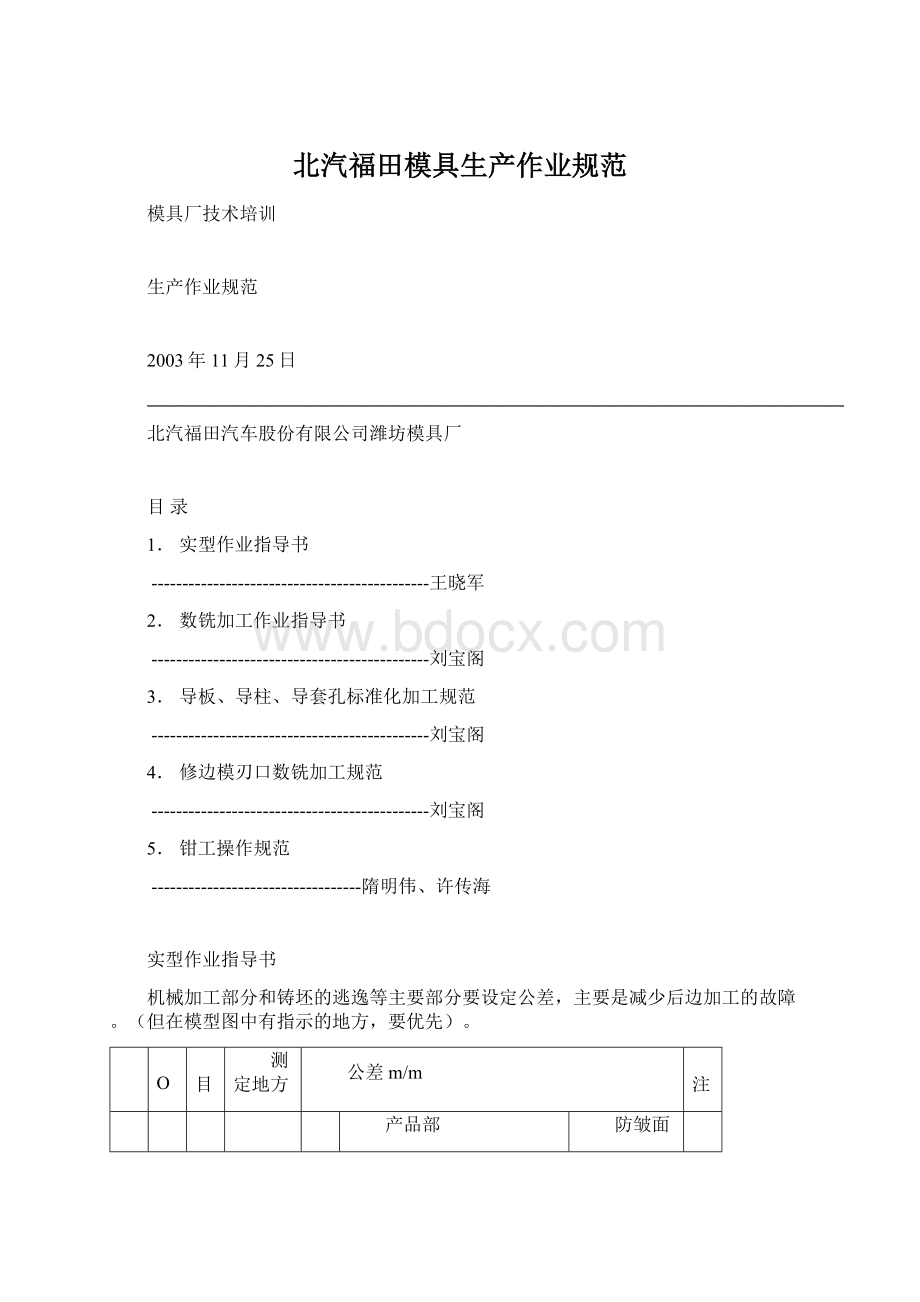
北汽福田模具生产作业规范
模具厂技术培训
生产作业规范
2003年11月25日
北汽福田汽车股份有限公司潍坊模具厂
目录
1.实型作业指导书
---------------------------------------------王晓军
2.数铣加工作业指导书
---------------------------------------------刘宝阁
3.导板、导柱、导套孔标准化加工规范
---------------------------------------------刘宝阁
4.修边模刃口数铣加工规范
---------------------------------------------刘宝阁
5.钳工操作规范
----------------------------------隋明伟、许传海
实型作业指导书
机械加工部分和铸坯的逃逸等主要部分要设定公差,主要是减少后边加工的故障。
(但在模型图中有指示的地方,要优先)。
NO
项目
测定地方
公差m/m
备注
1
产品面的高度
区分
长度
产品部
防皱面
制件部要标有长度,防皱部要标出零件着手尺寸
简单形状
复杂形状
1000以下
+3
+3
+3
-0
-0
-0
1000-2000
+3
+3
+3
-1
-1
-1
2000以上
±3
±3
±3
2
轮廓的大小
区分
长度
曲线轮廓
长度就是标出从模具中心过来的尺寸,不包括缺陷等凹处显著的情况()表示凹侧
简单
复杂
1500以下
-1(+1)
-1(+1)
+3(-3)
+3(-3)
1501以上
±3(±3)
±3(±3)
3
区分
长度
L
H
标出模具长边的尺寸
600以下
+0
-0
-3
+3
601以上
±3
±3
4
区分
长度
L
W、H
所谓逃逸形状包括升降器,键槽气缸,导销导向等
1500以下
±2
-0
+3
1501以上
±3
-0
+4
5
区分
长度
L
D
D
D0
并以导套为基准
1500以下
±2
±3
80
60
100
80
1501以上
±3
±3
120
100
侧销安装面
l
S
顶出器侧位置的大小也以此为基准,但逃逸部分要以四项为基准
±2
±2
导板面(顶出器凸起部分,斜楔等)
l
S
有关滑板安装侧也以此为基准
±2
±2
U型槽,底座
其他未加工面
模具大小,筋与筋的间隔,
配管,配线废料处理,
型芯孔等
位置和大小都在±5以下插座盒和上吊装置也以此为基准
倒角
贴面
贴面
倒角
倒角后
要领参照实型制作-倒角标准
C5
C10
+5,-0
±3
±2
±3
浇铸吊钩
浇铸螺帽
孔直径+0浇铸前确认
-1
实型制作倒角规范
技术要求
1.贴倒角的尺寸原则如图所记。
2.在上记的模型图中有尺寸指示时,就按照模型图尺寸。
3.在上记的C5加工后存在的是机械加工留出的指定的倒角尺寸。
4.当导柱及导套的公称直径为63以上时,要预先在导柱和导套打入部标注切削余量,设型芯孔。
模具上铸字要求
1.一般英文字母和尺寸:
宽X高=25X35
2.模具前侧需铸出“F”记号,字母尺寸:
宽X高=35X50
3.铸出文字项目:
零件号、模具号、左或右、模具前后识别标志“F”,上模重量及总重,材料等。
4.铸出文字位置:
如图
5.铸字颜色:
白色
铸件基准所有铸件(刃口镶块除外)
均有铸造基准(二角槽),其位置在铸造四边的侧壁上,位于冲模中心线上,直接铸出,不需加工。
数铣加工作业指导书
1总则
1.1严格按照数控设备的启动顺序启动设备。
1.2经常保持鼻端锥孔的清净,刀体无油泥、灰尘,保持主轴跟刀具的同心度(机床维护保养规程)。
1.3严格按照机床的加工范围、动力、精度等技术指标操作,防止超程、超载、超压、超差现象发生。
1.4加工过程中,要经常密切注意设备运行中的CNCSYS信息反馈,对出现的异常信息和报警,要及时查清原因,及时清除。
1.5要以六点定位原理为基本指导思想进行装夹。
1.6要严格执行工艺,保证工件装夹可靠、稳定和平衡。
1.7加工前要对机床的各项参数进行检查并调整到要求的状态。
1.8要根据加工程序要求选择刀具,要严格按照刀具提供的切削参数加工,尽量发挥出刀具的最大切削效能。
2装夹找正规范
2.1六点定位原理和工艺装夹系统的稳定性是基本依据。
2.2找正时,以毛坯工件背面的3个32×80键槽粗定位,然后以正面2-Φ10孔打表找到工件的加工原点,一般情况下,加工原点跟模具中心一致。
2.3垫铁布置以右图为准(图示为长度约1.5m的工件),长度每增加1mm,增加两块垫铁,呈对称分布。
2.4一般情况下,以四个压板四角呈对称分布,特殊情况下可酌加或酌减。
2.5压板位置要放到工件底部有垫铁的地方,压板不要悬空,防止工件受压变型,压板后端支点要略高于前端1-2mm。
3镗孔
3.1保证同轴度、垂直度、位置度和表面质量。
3.2同一套模具上下模镗孔必须在同一机床上加工且加工顺序合模后必须一致。
3.3镗孔参数表
加工
类别
坯料
进给速度
mm/min
主轴转速
rpm
进刀量
mm
刀具材料
粗
钢
30
600
2-3
合金
铸
35-40
645
3-5
合金
半精
钢
30
645
0.5-1.0
合金
铸
30
645
0.5-1.5
合金
精
钢
28
645
0.4左右
合金
铸
28
600
0.1
合金
4型面加工
4.1型面加工规范
a.Sф50清根→Sф50粗铣(步距8-10MM)→Sф32清根→Sф32半精铣(step=4mm)→Sф20清根→Sф20精铣(step=0.8-1mm)→Sф16清根→Sф12清根→ф10清根;
b.ф50R6平刀粗铣(等高线)→Sф32清根→Sф32精铣(step=1mm)→Sф25清根→Sф20清根→Sф16清根→Sф10清根(多用于内板2-3序);
c.要求上序加工刀的驱动方向跟下序驱动方向基本一样。
4.2型面加工参数表
类别
刀具
机床
Speed
rpm
Step
mm
Feed
mm
T
质量要求
粗
Sφ50
HARDFORD
1600
8-10
150-2000
5-8
φ50R6
CMG
1100
SORA
1100
1400
1-1.5
半精
Sφ32
HARDFORD
2000
3-4
1500
0.6-0.8
SMG
1400
900
SORA
1400
900
精
Sφ20
RAMSPEED
7-8000
0.5-0.7
4000
0.2-0.3
粗糙度要好
Sφ32
其它数控
1400-2000
0.8-1
1000
0.6-0.8
清根
Sφ25-Sφ16
Sφ10、12、20
RAMSPEED
7-8000
1000
每次1mm
保证内拐角不能有余量
其它机床
1400
800-900
注意:
1.高速铣清根时,只能用Sφ20刀具,切深每次下落0.5mm。
2.合模加工的方法,修边模、翻边模的压件器,应放到模座里进行加工。
3.特深或特殊型面的刀具及切削参数要具体情况,具体对待。
5刃口轮廓加工规范
5.1修边轮廓采用粗铣半精铣清角精铣,不能产生让刀亏料现象。
5.2如遇到轮廓上面有型面的情况应先粗铣轮廓→加工型面→洁角→精铣轮廓。
且铣型面边界设定应以轮廓线为准。
5.3分模轮廓采用粗铣→精铣→不用洁角。
5.4压件器加工时,合模压紧,以上下模体为基准。
5.5刀具尽量以硬合金刀为主,粗铣时要冷却。
5.6刀具的选用及铣削用量表(刃口轮廓)
刀具
刀材质
进刀方向
留量
F
S
粗
ф50-ф30合金铣刀
合金
逆
1
30
150-250
半精
ф30-ф20
合金
逆
0.5
60
150-250
洁角
ф16-ф10
合金
顺
0
调
250以上
精铣
ф30-ф20
合金刀
逆
0
70-90
150-250
5.7铣削用量选择标准表:
HARDFORD
CMG
SORA
RAMSPEED
T
△T×0.8
△T×0.5
0.5△T×
0.2-0.3
Vc
Vc×0.8
Vc×0.6
Vc×0.6
Vc×1.0
Sz
Sz×0.7
Sz×0.5
Sz×0.5
Sz×0.4
F
F×0.9
F×0.7
F×0.7
F×1.0
8刀具选用及铣削用量的选择规范:
8.1据不同的铣削方式选用不同的刀具。
8.2铣削用量的选择要充分考虑切削四要素和他们之间的相互关系和前后次序,其步骤:
a.据刀具的参数值确定深度下,铣削宽度B。
b.选定铣削速度Vc。
c.6.2.3先定进给量Fz
d.6.2.4然后确定进给:
F=1000.Vc/ЛD×n×Fz×K
(Vc铣削速度,n刀齿数,Fz每齿进给,K刚性系数)
8.3刀具尽量短。
8.4冷却方式:
粗铣、水冷、油冷;精铣:
雾化冷却。
8.5刀片更换要以准切削参数运行10000行更换一次,以对刀块或对刀仪确定Z轴高度,谨防传递失误(精铣)
导板、导柱、导套孔标准化加工规范
1.为实现导板、导柱、导套孔的标准化加工,特制定此规范,此规范适用于:
西班牙龙门加工中心、台湾数控龙门铣床、卧式加工中心、北京数显龙门铣床。
2.导板标准化加工规范
2.1加工前,一定要准确检测刀具直径及刀具状况。
2.2测量导板的实际加工量,以确定每刀的加工量及粗加工次数。
需要插铣的导板,还要测量导板的宽度,以确定插铣的范围。
2.3切削用量的选择
2.3.1导板粗加工
2.3.1.1选用Ф50、Ф40波纹粗齿立铣刀,单边加工量4-6mm,S70-S120,F30-F80。
2.3.1.2选用φ60、φ50硬质合金铣刀,单边加工量3-4mm,S80-S120,F50-F100。
2.3.2导板半精加工,选用φ60、φ50硬质合金铣刀,单边切削量0.5-1.5mm,S80-S120,F60-F120。
2.3.3导板精加工
2.3.3.1插铣φ32、φ40、φ50插铣刀,间距为0.7mm,单边切削量0.2-0.5mm,S1000-S1200,F1000-F1200.
2.3.3.2立铣φ60、φ50硬质合金立铣刀,单边切削量0.2-0.5mm,S80-S120,F80-F120,单边留量0.15mm.
2.3.3.3加工完成后要求检查导板尺寸及垂直度是否符合标准要求。
3.导柱、导套孔标准化加工规范
3.1加工前,要先检查底孔直径,以确定粗镗孔的首次加工尺寸,镗杆直径及粗镗孔次数,并根据孔的深浅及所处位置,选择合适长度的镗杆。
3.2加工前,还要检测预钻孔的偏心情况,若不够加工,则及时找有关人员协商。
3.3导套孔底部非工作部分的直径,应大于其相应导柱直径5mm以上。
3.4刀具选用
3.4.1粗、半精镗孔,应选用不可调侧固式镗杆,镗刀头为方型刀头,主偏角450,刀头伸出方向与刀杆中心线成450角,刀头为焊接式硬质合金刀头,且切削部分宽度粗镗孔应大于6mm,半精镗孔应大于4mm.
3.4.2精镗孔采用可调式镗杆,刀头为圆柱形可调式刀头,刀片为可转位硬质合金刀片,刀头伸出方向与刀杆中心线成450角。
3.5切削用量的选择
3.5.1粗镗孔,单边切削量为4-5mm,S450-S600,F30-F50,加工后直径为公称直径D
3.5.2半精镗孔:
单边切削量0.5-1.5mm,S400-S600,F30-F50,加工后直径为D
3.5.3精镗孔,单边切削量为0.1-0.3mm,S400-S500,F20-F40.
3.6导柱、导套孔加工完成后,要检测孔径及垂直度等项目是否符合标准要求。
4.各机床的导板加工程序,插铣程序及镗孔程序应建立专用目录,并固定程序
程序号,使用时,只需改动相应数据,以减少操作人员的编程时间
修边模刃口数铣加工规范
为确保修边模刃口的负间隙,保证刃口的加工质量,减少钳工修研工作量,在数铣加工修边模刃口时必须按以下规范进行加工。
1.在加工前,一定要认真测量刀具的直径,以保证加工后尺寸的准确。
2.所有刃口的加工,均采用顺铣加工,若程序是逆铣的,则要求编程人员增加顺铣程序,左右对称件加工刃口的,要求提供顺、逆铣两套刃口的加工程序。
3.在轮廓加工前,一定要测量刃口余量的大小。
若余量大于10mm时,应分两刀以上进行粗加工。
4.刃口加工工艺为粗加工、半精加工、精加工、清角。
5.粗加工后的单边余量为0.5—0.7mm,半精加工后单边余量为0.3—0.4,上模精加工后单边余量为0.15—0.2,下模精加工后单边余量为零.
6.若按以上原则加工刃口,出现刀补过切的,则要求编程人员按实际留量编程,进行加工.
7.有条件的机床,应在切削过程中,适当加冷却,以提高加工质量和刀具的使用寿命.
8.切削参数的选择
8.1粗加工
8.1.1Ф50硬质合金刀,加工Cr12MoV时,单边切5--6mm,S90--S100,F30—F50;加工风冷钢时,单边切削量5--10mm,S100—S120,F40—F70.
8.1.2Φ32硬质合金刀,加工Cr12MoV时,单边切削≤8mm,S160—S200,F40—S80;加工风冷钢时,单边切削≤12mm,S200—S240,F40—F100。
8.2半精加工(单边加工量为0.2-0.4)Φ32(Φ30)硬质合金刀加工Cr12MoV时,S200—S240,F60—120;加工风冷钢时,S240—S300,F80---F160.
8.3精加工(单边加工量为0.15—0.2)Φ32(Φ30)硬质合金刀加工Cr12MoV时,S240—S300,F80---F160;加工风冷钢时,S300—S400,F100---F200.
8.4清角加工
8.4.1ф20整体硬质合金刀,S600—S800,F10—F40
8.4.2ф16整体硬质合金刀,S800—S1000,F10—F40
8.4.3ф12整体硬质合金刀,S1000—S1200,F10—F40
8.4.4ф10整体硬质合金刀,S1200—S1600,F10—F40
8.4.5ф6整体硬质合金刀,S1800—S2000,F10—F40
钳工操作规范
第一章:
钳工应具备的基本技能:
1.划线——工件在加工之前(指毛坯)或在加工过程中(指半成品),用划线工具或三坐标划线机按图纸和加工工艺在工件上划出所需要的线条,用以表示工件上要加工的部位和界限。
2.划线的目的——第一,按照图纸和工艺要求确定各加工面的余量和各孔、槽、凸台、表面等的相互位置,为以后的加工或校正提供参考依据;第二,可以对毛坯进行加工前的检查,并对加工余量进行全面的调整和分配;第三,确定在板材上截取材料的位置,和理安排,做到节约材料。
3.划线前的准备——A.熟悉图纸和工艺文件,仔细分析下几道工序的具体要求;B.对画线对象进行外观的粗略检查,看其是否有明显的缺陷;C.对铸件毛坯,应预先清理型砂,除净毛刺和冒口;D.对锻件毛坯,应将氧化皮去掉;E.对半成品件,要去掉基准面上的毛刺,除净表面污垢和浮锈;E.考虑画线方案、画线基准、划线步骤、划线的内容以及划线工具、吊装工具和安全措施。
4.划线基准的选择——A.划线基准应尽量和设计基准一致。
B.选择已经精加工并且加工精度最高的边、面或有配合要求的边、面、外圆、孔、槽和凸台的对称线。
C.选择较长的边或相对两边的对称线,或是较大的面或相对两面的对称线。
D.较大外圆的中心线。
E.便于支撑的边、面或外圆。
F.补充性划线时,要以原有的线或有关的装夹部位为基准。
第二章:
钻孔及铰孔的基本要素
1.钻孔——在不同的材料上钻孔时,应根据材料的性质将钻头刃磨出相应的角度,以改善钻头的切削性能,延长钻头的寿命,使钻出的孔达到图样的技术要求。
加工钢和铸铁时钻头顶角为116-118°;加工钢锻件时顶角为120-125°;加工锰钢和不锈钢时顶角为135-150°。
2.钻头的刃磨——手工刃磨钻头时,为保证两主切削刃的对称性,在刃磨的每一步骤,应注意磨完一侧翻转180°再磨另一侧时要尽量做到三不变,及手持钻头的部位不变,手的姿势不变,刃磨吃刀情况不变。
必要时,可用量具检验或进行试钻检查。
可在位置半径R=(0.5-0.7)R处测量(R为钻头半径),它能综合反映出钻尖偏心和锋角不对称误差。
3.钻小孔的加工方法———小孔是指直径在3mm以下的孔。
钻小孔的钻头直径小,强度低,螺旋槽又比较小,不易排屑,在钻削过程中,转速高,进给不均匀。
故钻头容易折断。
为此钻小孔时必须掌握以下几点,
(1)选用精度较高的钻床,采用相应的小型钻夹头。
(2)开始进给时,进给力要小,防止钻头弯曲和滑移,以保证钻孔的正确位置。
进给时要注意用力大小和感觉,以防钻头折断。
(3)钻削过程中,需及时提起钻头进行排屑,并借此使孔中输入切削液和使钻头在空气中得到冷却。
(4)钻小孔的转速:
在一般精度不高的钻床上钻小孔:
钻头直径D=2~3mm
n=1500~2000r/minD≤1mmn=2000~3000/min。
在精度很高的钻床上钻小孔时,对上述直径的钻头n均可选3000~10000r/min以上。
4.钻孔时产生孔偏移或歪斜的原因——A.位置偏移的原因是:
(1)工件画线或安装不正确或未装牢,钻孔时移动;
(2)钻头回转时摇摆,进刀过急;
(3)钻头下刀位置不准,导致无法纠正而使孔偏移;
(4)工件表面与钻头不垂直。
尤其是在斜面上钻孔,操作不细心,使孔偏移。
防止的方法是:
正确对工件画线,仔细按线试钻浅孔,待位置正确后,再往下加工。
应将工件正确装夹与夹牢,防止变形。
钻头装夹应正确等。
B.产生孔歪斜的原因是:
(1)工件在钻床工作台上安装不正确或松动;
(2)钻床主轴与工作台不垂直;
(3)斜面上钻孔方法不对;
(4)配钻两种硬度不一致的材料半边孔上,容易产生歪斜。
预防的方法是:
正确的安装工件;注意检查钻床精度是否符合要求;掌握斜面上钻孔和钻半边孔的操作方法;合理刃磨钻头与选择切削速度等。
铰孔——用铰刀在预制孔上切除较小的余量,加工出具有较高精度和粗糙度的孔的过程。
选择铰孔余量时,应考虑到孔径的大小、材料的硬度、铰刀的类型等因素。
一般原则是:
孔径大余量大;孔径小余量小;材料硬余量小;材料软余量大。
A.余量的选择:
圆柱销孔铰孔前的钻孔直径:
(mm)
圆柱销孔直径
6
8
10
12
16
20
25
钻孔直径
5.7
7.5
9.5
11.5
15.5
19.5
24.5
铰孔时,出现孔的扩张和缩小的原因:
A.铰孔时出现孔的扩张主要是由于切削时的振动,工件与刀具的安装偏差和刀瘤等原因造成,
例如:
(1)机铰时钻床主轴震摆,铰刀中心与孔中心不重合;
(2)冷却润滑不良(如铰铸铁时不加煤油),铰刀刃口粘附切屑瘤而把孔铰大;
(3)加工余量过大或过小,余量过大加上进刀量又大,会将金属撕裂下来使孔径变大;余量太小时局部铰不起来,自然孔径就大了。
(4)手铰孔时,两手用力不均匀,铰刀左右晃动,将孔径铰大
(5)切削速度增加会使切削力和变形减小,孔径将由收缩转为大。
B.孔径的缩小主要是由于铰孔过程中被切金属的弹性恢复而成。
例如:
(1)铰刀切削刃磨钝以后,切削能力降低,对一部分加工余量产生挤压作用,当铰刀退出时,金属又恢复起弹性变形,致使孔径缩小。
(2)铰刀校准部分直径已经磨损,铰出的孔自然缩小。
C.铰孔时铰刀为什么不能反转?
铰刀在铰孔时,无论进刀或退刀,都只能顺转,不能反转,原因如下:
(1)铰刀刀刃的切削角是有方向的,在顺转时才起切削作用。
反转时不但不起切削作用,反而会磨损刀齿。
螺纹直径D
螺距p
钻头直径d
铸铁黄铜
钢、可锻铸铁
4
0.7
3.3
3.3
5
0.8
4.1
4.2
6
1
4.9
5
8
1.25
6.6
6.7
10
1.5
8.4
8.5
12
1.75
10.1
10.2
16
2
13.8
14
20
2.5
17.3
17.5
24
3
20.7
21
(2)铰刀在退出时反转,容易使切屑从铰刀后面挤进去,卡在铰刀与孔壁之间,划伤孔壁,降低孔的粗糙度,或使孔径扩张,还可能造成崩齿,严重时会折断铰刀。
5.钳工攻丝的方法和要求:
A.常用丝锥的螺距及底孔钻头直径见下表:
B.手工攻丝时要注意以下几点
(1)工件夹紧要牢靠和正直,丝孔中心线要垂直于水平面。
(2)丝锥要放正开始用力要均匀,保持丝锥与丝孔中心平直下去(可从正面与侧面凭眼力观察丝锥是否与工件平面垂直)。
要求高时可用90°透光尺检查,发现不正,应及时纠正过来。
(3)根据材料性质,选用和经常保持有足够的冷却润滑剂。
(4)板转铰杠,一般每次只旋转1/2转为宜。
丝锥小时旋转更要小于1/2转。
每次旋转后应反转1/4或1/2行程,目的是把铁屑折断,利于排屑,减少切削刃粘屑的现象。
(5)攻丝时,如感觉很费力,不可强行转动,否则将折断丝锥。
而应当退出检查丝锥是否有毛病,或者用二锥攻几扣,再用一锥攻。
(6)用力应均匀,保持平衡,以免将螺纹牙型撕裂或或使螺纹扩大,出现锥度。
(7)攻不通孔螺纹时,应经常退出丝锥或倒出切屑,快攻到底时,不可蛮干,否则将会折断丝锥。
C.机器攻丝时要注意以下几点:
(1)钻床主轴的径向振摆不能太大,一般在0.05mm以内。
(2)工件夹紧要正确,丝孔轴心线应与钻床主轴轴心线重合,不要歪斜太大,一般在0.05/100mm以内。
(3)当丝锥刚进入螺纹底孔时,进刀要轻且慢,以放碰撞,可在钻床进刀柄上均匀加压,协助丝锥进入工作。
当校正部分进入螺孔时,则不要再加压。
(4)攻不通螺纹时,应用攻丝夹头。
(5)选择适当而充足的冷却润滑剂。
(6)选择较合适的主轴转速:
钢材,6~15米/分;调质后或较硬的钢材,5~10米/分;铸铁8~10米/分;在同样条件下,丝锥直径小取较大速度;丝锥直径大、螺距大选低速。
D、断丝锥的取出方法:
在取断丝锥前先清理螺孔中的切屑及丝锥碎屑,以免轧在螺纹与丝锥之间阻碍断丝锥的取出。
(1)丝锥折断部分在孔内时,用钢丝插入攻槽中旋出或用小窄錾轻轻敲击丝锥周围取出。
在断丝锥处适量加点润滑液。
(2)丝锥折断部分露出孔外,用钳子旋出或用窄錾轻轻剔出。
(3)难取出的断丝锥可以用气焊的方法在断口上堆