冶金建筑钢结构管道涂装工程监理质量控制要点.docx
《冶金建筑钢结构管道涂装工程监理质量控制要点.docx》由会员分享,可在线阅读,更多相关《冶金建筑钢结构管道涂装工程监理质量控制要点.docx(42页珍藏版)》请在冰豆网上搜索。
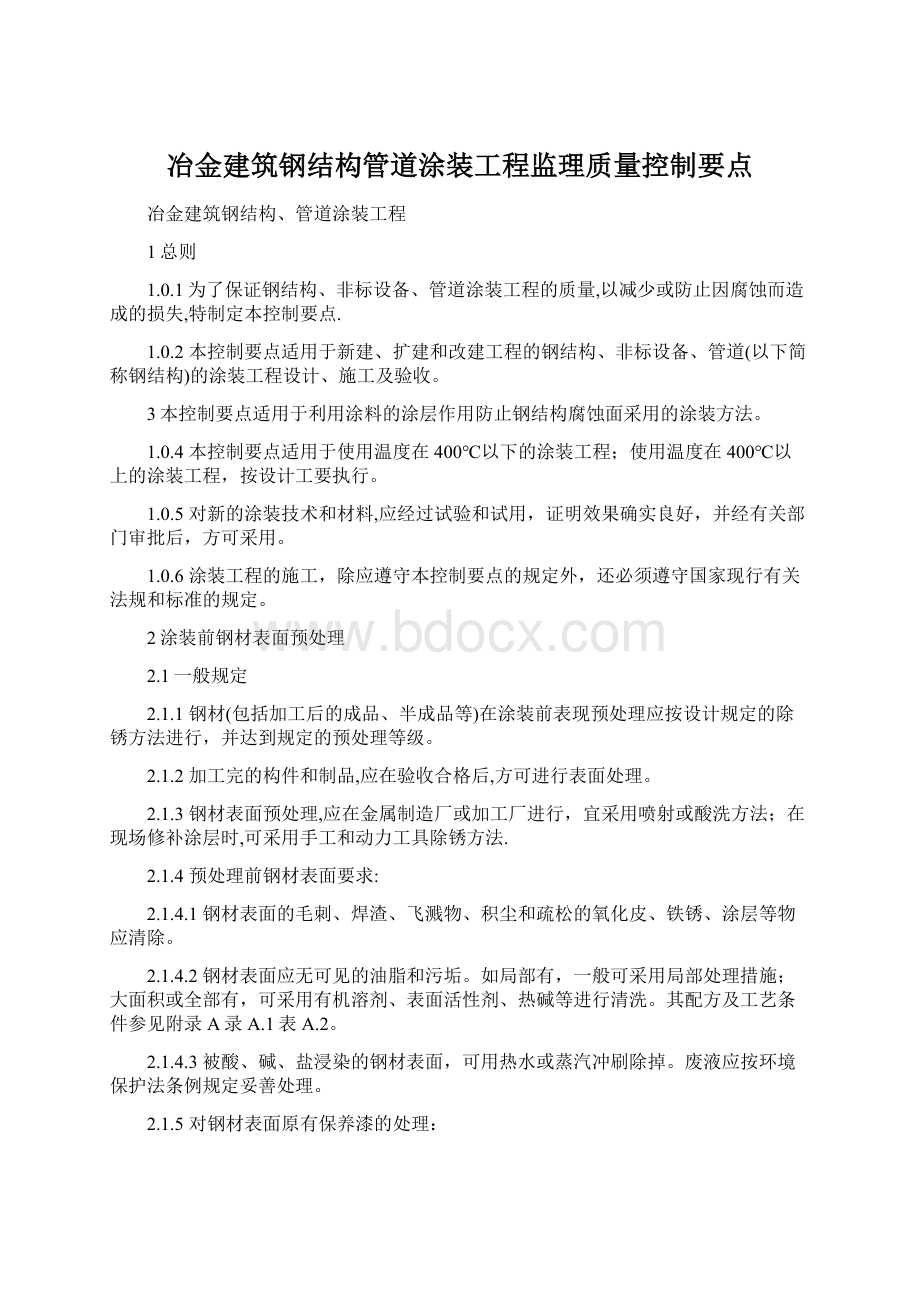
冶金建筑钢结构管道涂装工程监理质量控制要点
冶金建筑钢结构、管道涂装工程
1总则
1.0.1为了保证钢结构、非标设备、管道涂装工程的质量,以减少或防止因腐蚀而造成的损失,特制定本控制要点.
1.0.2本控制要点适用于新建、扩建和改建工程的钢结构、非标设备、管道(以下简称钢结构)的涂装工程设计、施工及验收。
3本控制要点适用于利用涂料的涂层作用防止钢结构腐蚀面采用的涂装方法。
1.0.4本控制要点适用于使用温度在400℃以下的涂装工程;使用温度在400℃以上的涂装工程,按设计工要执行。
1.0.5对新的涂装技术和材料,应经过试验和试用,证明效果确实良好,并经有关部门审批后,方可采用。
1.0.6涂装工程的施工,除应遵守本控制要点的规定外,还必须遵守国家现行有关法规和标准的规定。
2涂装前钢材表面预处理
2.1一般规定
2.1.1钢材(包括加工后的成品、半成品等)在涂装前表现预处理应按设计规定的除锈方法进行,并达到规定的预处理等级。
2.1.2加工完的构件和制品,应在验收合格后,方可进行表面处理。
2.1.3钢材表面预处理,应在金属制造厂或加工厂进行,宜采用喷射或酸洗方法;在现场修补涂层时,可采用手工和动力工具除锈方法.
2.1.4预处理前钢材表面要求:
2.1.4.1钢材表面的毛刺、焊渣、飞溅物、积尘和疏松的氧化皮、铁锈、涂层等物应清除。
2.1.4.2钢材表面应无可见的油脂和污垢。
如局部有,一般可采用局部处理措施;大面积或全部有,可采用有机溶剂、表面活性剂、热碱等进行清洗。
其配方及工艺条件参见附录A录A.1表A.2。
2.1.4.3被酸、碱、盐浸染的钢材表面,可用热水或蒸汽冲刷除掉。
废液应按环境保护法条例规定妥善处理。
2.1.5对钢材表面原有保养漆的处理:
2.1.5.1是否保留用车间底漆或一般底漆的涂层,可根据涂的破坏程度、与下道底漆是否配套等具体情况而定。
凡与清除残留的污物后方可进行下道工序。
2.1.5.2用固化剂固化工厂双组分涂料的涂层,基本完好的可保留,但应用砂纸、钢丝绒或轻度喷射方法进行打毛,并应在清除残留的污物后方可进行下道工序。
2.1.6钢结构涂装,不宜使用带锈涂料,更不得用带锈涂料代替除锈.
2.2喷射除锈
2.2.1本控制要点适用于干喷射方法除锈。
除锈时应在有防尘措施的场地进行,以防止粉尘飞扬。
2.2.2喷射使用的空气压缩机,应设有油水分离装置,确保压缩空气中不含水分和油污。
空气过滤器中的填料应定期更换,空气缓冲罐内的积液应及时排放。
2.2.3喷射用磨料应符合的要求。
2.2.3.1密度大,韧性强,有一定粒度要求的粒状物。
2.2.3.2使用过程中应不易碎裂,散释粉尘量少。
2.2.3.3表面不得有油污,含水率小于1%。
2.2.4喷射使用的磨料种类及其喷射工艺指标,应符合表2.2.4的规定。
2.2.5磨料重复使用时,必须符合本控制要点2.2.3和2.2.4的有关规定。
2.2.6喷射除锈时,施工现场环境湿度大于80%,或钢材表面温度低于空气露点温度3℃时,时禁止施工露点温度,可按表2.2..6查对。
表2.2.4磨料种类及其喷射工艺指标
磨料名称
磨料粒径/
压缩空气
压力/MPa
喷嘴最小
直径/mm
喷射角/(0)
喷距/mm
石英砂
3.2~0.63,0.8筛余量大于40%
0.50~0.60
6~8
35~70
100~200
金刚石
2.0~0.63,0.8筛余量大于40%
0.35~0.45
4~5
35~75
100~200
钢线粒
线粒直径1.0长度等于直径,其
偏差小于直径的40%
0.50~0.60
4~5
35~75
100~200
铁丸或钢丸
1.6~0.63,0.8筛余量大于40%
0.50~0.60
4~5
35~75
100~200
表2.2.6露点温度查对表
环境温度/℃
相对湿度/%
55
60
65
70
75
80
85
90
95
0
-7.90
-6.80
-5.80
-4.80
-4.00
-3.00
-2.20
-1.40
-0.70
5
-3.30
-2.10
-1.00
0.00
0.90
1.80
2.70
3.40
4.30
10
1.4
2.60
3.70
4.80
5.80
6.70
7.60
8.40
9.30
15
6.10
7.40
8.60
9.70
10.70
11.50
12.50
13.40
14.20
20
10.70
12.00
13.20
14.40
15.40
16.40
17.40
18.30
19.20
25
15.60
16.90
18.20
19.30
20.40
21.30
22.30
23.30
24.10
30
19.90
21.40
22.70
23.90
25.10
26.20
27.20
28.20
29.10
35
24.80
26.30
27.50
28.70
29.90
31.10
32.10
33.10
34.10
40
29.10
30.70
32.20
33.50
34.70
35.90
37.00
38.00
38.90
15
6.10
7.40
8.60
9.70
10.70
11.50
12.50
13.40
14.20
2.2.7喷射除锈合格后的钢材,在厂房内存放进,应在16h风涂完底漆完底漆;在露天存放时,应在当班涂完底漆。
如在涂漆前已返锈,需重新除锈。
2.2.8喷射除锈后,用毛刷等式具清扫,或有干净无油、水的压缩空气吹净钢材表面上的锈尘和残余磨料后,方可涂底漆。
2.2.9喷射降锈后的钢材表面粗糙度,宜小于涂层总厚度的1/3~1/2。
2.3化学除锈
2.3.1钢材化学酸洗除锈,应选有硫酸、盐酸或磷酸配制成的酸洗液进行。
酸洗方法可采用浸渍法、喷淋法或循环法。
2.3.2酸洗液的配制,应按规定的比例和配制程序配制其配比及工艺条件,参见附录A附表A.3。
2.3.3酸洗过程中,各道工序必须连续进行,中途不行停顿,并应定期检查酸洗液浓度的变化情况,及时补充各种成分。
2.3.5酸洗后能在短时间内涂上底溱时,应进行中和和钝化处理(磷酸酸洗可不进行)。
根据具体条件,可选用下列方法处理和存放。
2.3.5.1钢材酸洗后,立即用水清洗,继之用5%碳酸钠水溶液处理,再用水冲洗碱液,最后进行钝化处理。
2.3.5.2钢材酸洗后,立即用热水冲洗至中性(ph用试纸检查),然后钝化处理。
钝化液的配方及钝化工艺条件,参见附录A附表A.4。
2.3.5.3钝化处理后的钢材,应在空气流通的地方凉干或用无油、水的压缩空气吹干。
2.3.5.4钝化后听钢材厂房内存放时,应在48h内涂完底漆;在露天存放进,应24h内涂完底漆。
涂底漆之前,如已返锈,则应重新进行酸洗和钝化。
2.3.6酸洗后不能在短时间涂上底漆时,应进行中和和磷化处理,其工艺如下:
酸洗———水洗——中和——水洗——磷化
2.4手工和动力工具除锈
2.4.1手工除锈,主要是用刮刀、手、手钢丝刷和砂布等工具除锈。
动力工具除锈,主要是用风动或电动砂轮、刷轮和除锈机等动力工具除锈。
2.4.2钢材除锈后,应用刷子或无油、水的压缩空气清理,除去锈尘等污物,并应在当班涂完底漆。
2.5火焰除锈
2.5.1火焰除锈是利用氧乙炔焰及喷嘴除锈的一种方法。
喷嘴的开关与大小要适合待除锈的钢材表面状况。
2.5.2火焰除锈适用于厚度5mm以上、未有涂层或要完全去掉旧涂层的钢材。
对厚度近于5mm的钢材进行除锈时,应注意火焰的温度。
2.5.3火焰除锈前,应将钢材表面残留疏松锈层、氧化皮及污物除掉。
2.5.4火焰除锈后,应用动力钢丝刷清除钢材表面上的附着物。
2.6钢材表面锈蚀等级和除锈等级
2.6.1钢材表面锈蚀等级和除锈等级,是以文字叙述和典型的样板照片共同确定的.样板照片,参见现行国家标准《涂装前钢材表面锈等级和除锈等级》(GB8923)
2.6.2钢材表面锈蚀等级,按锈蚀程度分4个选通,分别以A、B、C、D表示,其文字部分叙述如下:
A钢材表面全面覆盖着氧化皮而几乎没有锈蚀;
B钢材表面已发生锈蚀,并且部分氧化皮不锈蚀;
C钢材表面氧化皮已因锈蚀而剥落,或者可以刮除,并有少量的点蚀;
D钢材表面氧化皮已翼面锈蚀而全面剥离,并且普遍发生点蚀.
2.6.3钢材表面除锈等级
2.6.3.1喷射除锈,以字母“Sa”表示,按除锈质量程度分4个等级,其文字部分叙述如下:
Sa1钢材表面上应无可油脂和污垢,并且没有附着不牢的氧化皮、铁锈、油漆涂层等附着物.参见BSa1、CSa1、DSa1样板照片.
Sa2钢材表面应无可见油脂和污垢,并且氧化皮、铁锈、涂层和附着物已基本清除,其残留物应是牢固附着的(牢固附着是氧化皮和锈等物不能以金属腻子刀从钢材表面上剥离下来).参见BSa2、CSa2、DSa2样板照片.
Sa2
钢材表面应无可见的油脂、污垢、氧化皮、铁锈、涂层和附着物,任何残留的痕迹应仅是点状或条纹状的轻微色斑.参见ASa2
、BSa2
、CSa2
、DSa2
样板照片.
Sa3钢材表面应无可见的油脂、污垢、氧化皮、铁锈、涂层等附着物,该表面应显示均匀的金属光泽.参见ASa3、BSa3、CSa3、DSa3样板照片.
2.6.3.2手工和动力工具除锈,以字母“St”表示,分两个等级,其文字部分叙述如下:
St2钢材表面应无可见的油脂和污垢,并且没有附着不牢的氧化皮、铁锈、涂层和附着物.参见BSt2、CSt2、DSt3样板照片.
St3钢材表面应无可见的油脂和污垢,并且没有附着不牢的氧化皮、铁锈、涂层和附着物.除锈应比更彻底,钢材的显露部分的表面应具有金属光泽.参见样板照片.
2.6.3.3酸洗除锈,以字母“Be”表示,其文字部分叙述如下:
Be钢材表面应无可见的氧化皮、铁锈、涂层和附着物,个别残留点允许用手工或机械方法除掉.
2.6.3.4火焰除锈,以字母“F1”表示,其文字部分叙述如下
F1钢材表面应无氧化皮、铁锈、涂层和附着物,任何残留的痕迹应仅为表面变色(不同颜色的暗影).参见AF1、BF1、CF1、DF1样板照片.
2.6.4评定钢材表面锈蚀等级和除锈等级时,应在良好的散射日光下或在照度相当的人工照明条件下进行,检查人员应具有正常的视力,并以目视为准.
2.6.5待检的钢材表面与照片比较时,照片靠近钢材表面,并以最近似标示的照片确定等级.
3涂料
3.0.1钢结构涂料防腐涂料,宜选用醇酸树脂、氯化橡胶、氯碳化聚乙烯、环氯树脂、聚氨酯、有机硅等品种
3.0.2选用涂料时,首先应选已国家或行业标准的品种,其次选用已有企业标准的品种,无标准的产品不得选用.
3.0.3涂料进场应有产品出厂合格证,并应取样复验,符合产品质量标准后,方可使用.取样方法应符合现行国家标准的规定,取样数目和取样量按下列目录规定执行:
3.0.3.1取样数目
涂料使用前,应按交货验收的桶数,对同一生产厂生产的相同包装的产品进行随机取样,取样数目应大于
(n——交货产品桶数),也可按表3.0.3.1规定的取样数抽取。
表3.03.1涂料检验取样数目
交货的桶数
取样数目
交货的桶数
取样数目
2~10
2
71~90
7
11~20
3
91~125
8
21~35
4
126~160
9
36~50
5
161~200
10
51~70
6
此后每增加50桶取样数增加1
3.0.3.2取样量
取样时,应同时取两份0.25kg其中一份做检验,另一份密封贮存备查。
3.0.4涂料应配套使用,涂膜应由漆、中间漆和面漆构成。
不得用单一品种作为防护涂膜。
3.0.5用于钢结构涂装的底漆、中间漆和面漆,所具有的主要性能为:
3.0.5.1底漆,应具有较好的防锈性能和较强的附着力。
3.0.5.2中间漆,除应具有一定的底漆性能外,还应兼有一定的面漆性能,每道漆膜厚度应比底漆或可漆厚。
3.0.5.3面漆直接与腐蚀环境接触,应具有较强的防腐蚀能力和耐候、抗老化性能。
3.0.6选用耐400℃以下的高温涂料,应能在常温条件相自干成膜,在投产使用前构件不能返锈。
3.0.7钢结构涂装常用的主要涂料品种及施工性能指标要求,应符合表3.0.7的规定。
表3.0.7常用涂料品种及施工性能指标
涂料型号及名称
主要施工方法
施工粘度(涂-4杯)/s
稀释剂
使用量/
(g/m2)
涂层厚度/
((μm/道)
涂漆间隔时间
最短/h
最长/d
X06-1乙烯磷化底漆
喷涂或刷涂
30~50
专用稀释剂
60~80
8~12
2
1
Y53-31红丹油性防锈漆
刷涂
40~60
200号溶剂油
100~130
30~35
48
4
Y53-31红丹醇酸防锈漆
刷涂
40~60
X-6稀释剂
120~150
30~35
24
4
C06-1铁红醇酸底漆
刷涂或喷涂
50~80
X-6稀释剂
100~120
20~25
24
4
X53-1云铁高氯化聚乙烯防锈
刷涂或喷涂
90~140
专用稀释剂
180~220
30~35
8
4
J52-81氯磺化聚乙烯防锈漆
刷涂或喷涂
60~80
专用稀释剂
100~120
20~25
8
4
G06-4锌黄铁红过氯乙烯漆
刷涂或喷涂
30~50
X-3稀释剂
70~80
18~20
4
4
H06-4环氧富锌底漆
刷涂
25~40
X-7稀释剂
170~200
20~25
24
4
H06-13环氧沥青底漆
刷涂或喷涂
70~100
X-32稀释剂
120~160
50~70
48
4
S06-4铁红聚氨脂底漆
刷涂或喷涂
40~60
X-11稀释剂
100~120
25~30
8
4
E06-28无机硅富锌底漆
刷涂或喷涂
20~30
专有稀释剂
140~180
20~25
8
4
C53-34云铁醇酸防锈漆
刷涂或喷涂
70~120
X-6稀释剂
120~160
30~40
24
4
G52-31各色过氯乙烯防腐漆
刷涂或喷涂
25~30
X-3稀释剂
80~100
18~22
4
3
X53-4高氯化聚乙烯中间漆
刷涂或喷涂
60~80
专用稀释剂
200~250
35~40
8
4
J53-13云铁氯化橡胶防锈漆
刷涂或喷涂
60~100
X-4稀释剂
130~160
30~40
8
4
J52-氯磺化聚乙烯中间漆
刷涂或喷涂
80~140
专用稀释剂
200~250
40~45
8
4
S53-云铁聚氨脂中间漆
刷涂或喷涂
70~90
X-11稀释剂
130~160
40~50
8
4
C04-2各色醇酸磁漆
刷涂或喷涂
60~90
X-6稀释剂
100~120
20~25
48
4
C04-42各色醇酸磁漆
刷涂或喷涂
60~90
X-6稀释剂
100~120
20~25
48
7
G52-2过氯乙烯防腐漆
刷涂或喷涂
20~25
X-3稀释剂
60~80
16~20
8
7
X52-1各色高氯化聚乙烯磁漆
刷涂或喷涂
80~120
专用稀释剂
150~180
30~35
8
7
J52-61氯磺化聚乙烯防腐漆
刷涂或喷涂
60~80
专用稀释剂
100~120
20~25
8
7
S04-9各色聚氨脂磁漆
刷涂或喷涂
30~40
X-11稀释剂
100~120
20~25
8
7
J52-11各色氯化橡胶防腐漆
刷涂或喷涂
60~90
X-14稀释剂
100~120
30~35
8
7
W61-64有机硅高温防腐漆
刷涂或喷涂
30~60
专用稀释剂
100~120
20~25
24
7
注:
“喷涂”指高压无气喷涂方法。
4涂装设计
4.1腐蚀环境的分类
4.1.1城市大气环境工业不密集区域,大气中含有少量的二氧化硫和其他腐蚀性物质。
4.1.2工业大气环境工业密集区域,大气中含有一定量的二氧化硫和其他腐蚀性物质。
4.1.3化工大气环境化工工业区域,大气中除含有一定量的二氧化硫和其他腐蚀性物质外,还含有化工生产过程中产生的腐蚀气体物质。
4.1.4海洋大气环境海面上和海岸狭窄的地带,大气中主要含有氯化物和二氧化硫等腐蚀物质。
4.1.5水下环境受淡水、混合水、污水或咸水等腐蚀作用的环境。
4.1.6地下环境主要受土壤腐蚀作用的地下环境。
4.1.7高温环境构件表面温度或环境温度在120℃上的环境。
4.1.8特殊环境除上述规定以外的特殊腐蚀环境。
4.2涂装防护体系
4.2.1涂装防护体系的内容包括钢材表面预处理、涂层体系和工程色彩。
涂层体系内容包括涂料品种、涂层结构和涂层厚度。
4.2.2钢材表面预处理方法与除锈等级确定所考虑的因素。
4.2.2.1环境腐蚀程度。
4.2.2.1钢材表面原始锈蚀程度。
4.2.2.3选用的涂层体系和底漆要求最低的除锈等级见表4.2.2
表4.2.2各种底漆或防锈漆要求最低的除锈等级
涂料品种
除锈等级
油性酚醛、醇酸等底漆或防锈漆
Bt3或Be
高氯化聚乙烯、氯化橡胶、氯磺
化聚、聚环氯树脂、聚氨酯等底
漆或防锈漆
Sa2或Be
无机富锌、有机硅、过氯乙烯等
底漆
Sa2
注:
:
选用富锌底漆进,不宜采用酸洗除锈。
4.2.2.4经济合理。
4.2.3涂料品种的选择应符合下列要求:
4.2.3.1涂料的性能应与腐蚀环境相适应,见表4.2.3。
表4.2.3各种腐蚀环境与相适应的涂料和种类
腐蚀环境
相适应的涂料种类
城市大气环境
醇酸树脂
工业大气环境
醇酸树脂、高氯化聚化橡胶、氯碳化
聚乙烯
化工大气环境
高氯化聚乙烯、氯磺化聚乙烯、过氯乙烯、聚
氨酯、环氧树脂
海洋大气环境
氯化橡胶、聚氨酯
水上环境
氯化橡胶、聚氨酯
水下环境
环氧树脂、聚氨酯
高温环境
环氧改性酚醛耐热漆、有机硅耐热漆、聚氨酯
耐热漆
4.2.3.2涂层应由底漆、中间漆和面漆构成,并且配套使用。
4.2.3.3选用的漆应与规定的钢材除锈等级相适应。
4.2.3.4经济合理。
4.2.4涂层厚度应符合下列要求:
4.2.4.1与环境腐蚀程度相适应。
4.2.4.3根据选用涂料品种的特性与使用环境,保证涂层能起防护作用的最低厚度。
4.2.4.4需要加重防腐蚀部队建设位和涂装维修困难部位,宜增加适应的厚度。
4.2.5涂装防护体系的设计,根据4.2.2、4.2.3和4.2.4的要求,宜按附录B附表B1的规定选用。
4.2.5.1对大气(城市、工业和化工大气)腐蚀的涂装工程,宜根据环境空气相对湿度确涂层的厚度,湿度低于60%~75%时,选用规定厚度的中限;湿度大于75%时,选用规定厚度的上限。
4.2.5.2对户内,外涂装工程涂层厚度的上限。
4.2.5.2对户内、外涂装工程涂层厚度的确定,宜符合附录B附表B.1的规定,户内选用规定厚度的下、中限,户外选用规定厚度的中、上限。
4.3涂装工程色彩
4.3.1钢结构及管道等涂装工程的颜色和标志.宜按本控制要点的规定采用。
4.3.2本控制要点规定的颜色,应以附录B附表B.2色卡的色标为基准。
采用时以色标的编号及颜色名称共同表示。
4.3.3建筑厂房的颜色,宜按表4.3.3的规定采用。
表中未述及的单元工程厂房,其颜色应与所在区域的厂房颜色相同。
铝合金压型板、镀锌压型钢板、彩色涂层板等按原色使用。
4.3.4电气室、操作室的颜色,宜按表4.3.4的规定采用。
表4.3.3建筑厂房的颜色
建筑区域
外部
内墙和天花板
钢结构
门窗类
屋顶
外墙
炼铁区(包括焦化厂、炼铁厂、码头
栈桥、港口建筑)
610
(深绿色)
606
(中灰)
402
(浅灰蓝)
407
(青蓝)
403(灰蓝)
407(青蓝)
炼钢区(包括炼钢厂、过铸厂、制气
厂房)
705
(铜棕)
701
(浅灰棕)
402
(浅灰蓝)
407
(青蓝)
403(灰蓝)
407(青蓝)
热轧区(包括热轧厂、初轧厂、无缝
钢管厂、机修厂等)
531
(阔叶绿)
505
(浅青绿)
501
(浅绿)
503
(豆绿)
403
(灰蓝)
冷轧区(包括冷轧厂、建钢厂、成品
码头栈桥和建筑物)
405
(浅蓝)
401
(浅青蓝)
401
(浅青蓝)
404
(天蓝)
403(灰蓝)
407(青蓝)
独立厂房、中心试验室等
302
(朱红)
103
(浅米黄)
601
(浅灰)
506
(中青绿)
403
(灰蓝)
表4.3.4电气室、操作室的颜色
建筑物
外部钢结构
内部钢结构
门窗
脚板
厂内电气室、操作室及其他建筑物
(包括地下室)
101(浅象牙黄)
502(浅豆绿)
601
(浅灰)
407(青蓝)
704(深赭石棕)
304
(深蓝)
厂外气室、操作室及其他附属建
筑物
103(浅米黄)
401(浅青蓝)
502(浅豆绿)
601
(浅灰)
407(青蓝)
704(深赭石棕)
304
(深蓝)
4.3.5一般机械、移动机械,构筑物的颜色,宜按表4.3.5的规定采用。
表4.3.5机械、构筑物的颜色
设备名称
色标号
一般机械
507
(灰绿)
电动机
室内
吊车
本体
102(奶油黄)
控制室内部
503(豆绿)
扶手
108(金黄)
室外吊车
507①
(灰绿)
码头吊车
移动机械
507设备名称
色标号
礁料机、取料机
507①
(灰绿)
堆焦机、装煤机、其他
烟囱②
除尘设备
702(中灰棕)
喷煤粉专业设备
608(浅绿灰)
管道支架、运输机械架、其他
屋外构筑物
702(中灰棕)
气
柜
本体
602(铂灰)
走台、踏梯
702(中灰棕)
扶手
102(奶油黄)
油罐
602(铂灰)
氢气罐
804(银粉色)
氨气罐
水罐
锅炉
安装在设备上的扶手③
高炉等高温设备
507(灰绿)
1室外吊车、码头吊车、移动机械、堆取料机等的操作室内部及扶手、应与室内吊车的控制室内部及扶手的颜色相同。
2混凝土烟囱为原色.对100mm以上的烟囱应设航空标志,从标高50m起刷5~10m高的白色圈,相互交替直至顶端。
3安装在设备上的扶手工,一般为金黄色,色标号为108号。
4.3.6电器设备的颜色,宜按表4.