热加工工艺基础铸造.docx
《热加工工艺基础铸造.docx》由会员分享,可在线阅读,更多相关《热加工工艺基础铸造.docx(13页珍藏版)》请在冰豆网上搜索。
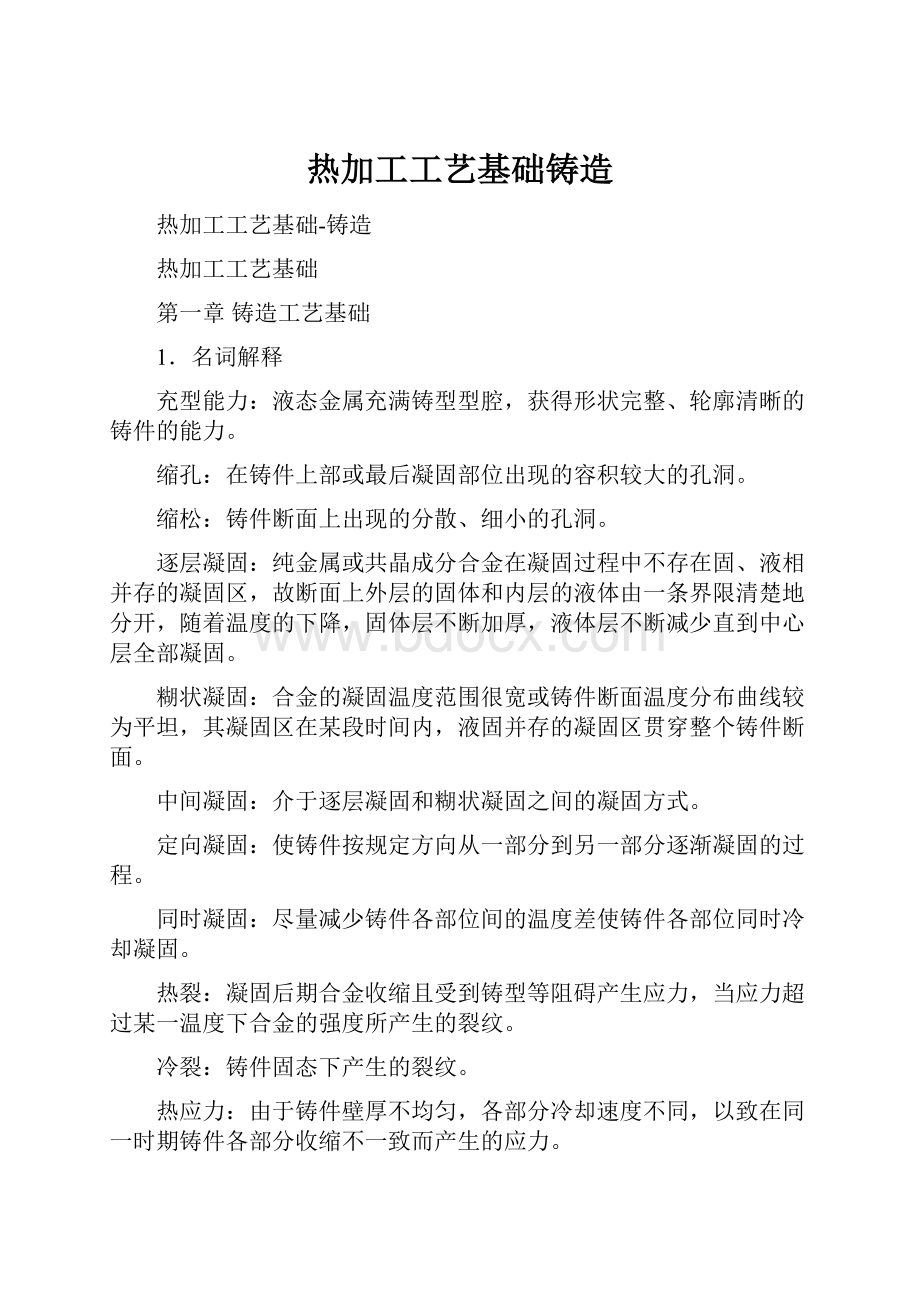
热加工工艺基础铸造
热加工工艺基础-铸造
热加工工艺基础
第一章铸造工艺基础
1.名词解释
充型能力:
液态金属充满铸型型腔,获得形状完整、轮廓清晰的铸件的能力。
缩孔:
在铸件上部或最后凝固部位出现的容积较大的孔洞。
缩松:
铸件断面上出现的分散、细小的孔洞。
逐层凝固:
纯金属或共晶成分合金在凝固过程中不存在固、液相并存的凝固区,故断面上外层的固体和内层的液体由一条界限清楚地分开,随着温度的下降,固体层不断加厚,液体层不断减少直到中心层全部凝固。
糊状凝固:
合金的凝固温度范围很宽或铸件断面温度分布曲线较为平坦,其凝固区在某段时间内,液固并存的凝固区贯穿整个铸件断面。
中间凝固:
介于逐层凝固和糊状凝固之间的凝固方式。
定向凝固:
使铸件按规定方向从一部分到另一部分逐渐凝固的过程。
同时凝固:
尽量减少铸件各部位间的温度差使铸件各部位同时冷却凝固。
热裂:
凝固后期合金收缩且受到铸型等阻碍产生应力,当应力超过某一温度下合金的强度所产生的裂纹。
冷裂:
铸件固态下产生的裂纹。
热应力:
由于铸件壁厚不均匀,各部分冷却速度不同,以致在同一时期铸件各部分收缩不一致而产生的应力。
侵入气孔:
砂型或砂芯受热产生气体侵入金属液内部在凝固前未析出而产生的气孔
反应气孔:
合金液与型砂中的水分、冷铁、芯撑之间或合金内部某些元素、化合物之间发生化学反应产生气体而形成的气孔。
·
析出气孔:
合金在熔炼和浇注过程中接触气体使气体溶解其中,当合金液冷却凝固时,气体来不及析出而形成的气孔。
2.合金的流动性不足易产生哪些缺陷?
浇不足,冷隔,气孔,夹渣,缩孔,缩松。
影响合金流动性的主要因素有哪几个方面?
合金的种类,合金的成分,温度。
在实际生产中常用什么措施防止浇不足和冷隔缺陷?
a.选用黏度小,比热容大,密度大,导热系数小的合金,使合金较长时间保持液态。
b.选用共晶成分或结晶温度范围窄的合金作为铸造合金。
c.选择合理的浇注温度。
3.充型能力与合金的流动性有什么关系?
合金的流动性越好,则其充型能力越好。
不同化学成分的合金为何流动性不同?
合金的化学成分不同,它们的熔点及结晶温度范围不同,其流动性不同。
为什么铸钢的充型能力比铸铁差?
铸铁为共晶成分的合金流动性好,其凝固时从表面逐层向中心凝固,已凝固的硬壳内表面比较光滑,对尚未凝固的流动阻力小,因而定型能力强而铸钢的结晶温度范围大,初生的枝状晶已使凝固的硬壳内表面参差不齐,将阻碍金属液的流动,因而铸钢的充型能力比铸铁差。
4.铸件的凝固方式有哪些?
根据液固相区的宽窄分为:
逐层凝固,糊状凝固,中间凝固。
合金的凝固方式与合金的铸造性能有何关系?
逐层凝固的合金铸造时合金的流动性较好,充型能力强,缩孔、缩松比较集中,便于防止,其铸造性能好。
糊状凝固的合金的流动性较差,易产生浇不到、冷隔等缺陷,而且易产生缩松,难以获得结晶紧实的铸件。
合金的凝固方式受哪些因素影响?
a合金的结晶温度范围合金结晶温度范围愈小,凝固区愈窄,合金趋于逐层凝固。
b凝固时铸件断面上温度分布梯度铸件的温度梯度较小,合金趋于糊状凝固。
5.何谓合金的收缩?
熔融合金注入铸型,凝固,直至冷却到室温的过程中,其体积和尺寸缩小到现象。
合金收缩由哪几个阶段组成?
液态收缩,凝固收缩,固态收缩
各会产生哪些缺陷?
液态收缩和凝固收缩,产生缩孔、缩松。
固态收缩影响铸件尺寸精度,产生裂纹,变形。
6.铸造应力形成的原因有哪几种?
(!
)由于铸件壁厚不均匀,各部分冷却速度不同,以致在同一时期铸件各部分收缩不一致而引起的热应力。
(2)由于合金的线收缩受到铸型或型芯的机械阻碍而产生的内应力。
试分析一下热应力是如何形成的?
固态金属在弹——塑临界温度一下,金属呈弹性状态,在应力作用下发生弹性变形,变形后应力仍然存在。
7.定向凝固后与同时凝固各需采用什么措施来实现?
定向凝固的措施:
厚大部位安放冒口或在远离浇冒部位增设冷铁。
同时凝固的措施:
在铸件厚壁处加冷铁并将内浇道设在薄壁处。
各适用于什么合金及何种结构特点的铸件?
定向凝固适用于纯金属、共晶成分的合金,以及壁厚不均匀,致密性要求高的铸件。
同时凝固适用于凝固收缩小的合金,以及壁厚均匀结晶温度范围宽且对致密性要求不高的铸件。
8.铸件的气孔有哪几种?
侵入气孔,反应气孔,析出气孔。
析出气孔产生的原因是什么?
合金在熔炼和浇注过程中因接触气体使气体溶解在其中且溶解度随温度上升而增加,当达到合金熔点时急剧上升,当合金冷却凝固时气体在合金中的溶解度下降而以气泡形式析出,气泡如不能及时上浮逸出,便会在铸件中形成析出气孔。
下列情况容易产生哪种气孔?
舂砂过紧,(侵入气孔)熔化铝时油污过多,(析出气孔)型撑有锈,(反应气孔)起模时刷水过多.(侵入气孔)
9.试述缩松、缩孔形成机理及防止措施。
缩松的形成机理:
(1)基本原因:
液态收缩、凝固收缩大于固态收缩。
(2)形成条件:
糊状凝固合金形成枝晶,将液体分割成小熔池得不到补缩。
缩孔的形成机理:
(1)基本原因:
液态收缩、凝固收缩大于固态收缩。
(2)形成条件:
a.浇口封闭且无冒口。
b.呈逐层凝固的合金(纯金属、共晶合金)
缩孔的防止措施:
采用定向凝固的方法,在厚大部位安放冒口,增设冷铁。
使缩松转化为缩孔再采用定向凝固的方法。
第二章砂型铸造
1.名词解释
砂型:
砂型铸造选用的铸型。
型砂:
按一定比例配合的造型材料,经过混制成符合造型、造芯要求的混合料。
模样:
模拟铸件形状,形成铸型型腔的工艺装备或易耗件。
型芯头:
为了在铸型中形成支承型芯的空腔,模样比铸件多出的突出部分。
型芯座:
由模样的型芯头在铸型中形成的空腔称为型芯座。
出气口:
在铸型或型芯中为排除浇注形成的气体而设置的沟槽或孔道。
冒口:
在铸型内存储供补缩铸件用熔融金属的空腔。
起模斜度:
为了使模样易从铸型中取出或型芯自芯盒中脱出,在平行于起出模样方向上,模壁上都应留出一定的倾斜度。
结构斜度:
铸件结构所具有的斜度。
机械加工余量:
为进行机械加工铸件比零件增大的一层金属。
收缩余量:
为补偿铸件收缩,模样比铸件图纸尺寸增大的数值。
2.为什么铸件的重要加工面和主要工作面在铸型中应朝下?
因为铸件上部凝固速度慢,晶粒较粗大,易形成缩孔、缩松,而且气体、非金属夹杂物密度小,易在铸件上部形成砂眼、气孔、渣气孔等缺陷。
铸件下部的晶粒细小,组织致密,缺陷少,质量优于上部。
因此,当铸件有几个重要加工面或重要面时应将主要和较大加工面向下。
3.为什么尽量使铸件全部或大部分位于同一砂箱内?
因为这样不仅减少了因错箱造成的误差,而且使铸件的基准面与加工面在同一个砂箱内,保证了铸件的位置精度。
4.为什么大面积的薄壁铸件应放在铸型的下部或放在垂直、倾斜位置?
因为这样可以增加液体的流动性,避免铸件产生浇不足或冷隔缺陷。
5.方案
(1)分模造型水平浇注,铸件沿底板中心线分型,轴孔下芯方便,底板凸台采用活块。
缺点:
分模尺寸精度差,容易产生错箱缺陷,飞边的清理量大。
方案
(2)整模造型,顶部浇注,铸件沿底面分型吗,铸件全部在下箱,即上箱为平面,不会产生错箱缺陷,铸件清理简便,四个凸台不需活块。
缺点:
中间部位需要砂芯,轴孔妨碍起模。
6.如何选择.浇注位置?
(1)铸件的重要加工面和主要工作面应朝下或位于侧面。
(2)铸件的大平面应朝下。
、
(3)铸件上面积较大的薄壁部分应处于铸型的下部或处于垂直、倾斜位置。
(4)易形成缩孔的铸件,应将截面较厚的部分放在分型面附近的上部或侧面。
(5)应尽量减少芯子的数量,便于芯子的安放、固定和排气。
7.如何选择铸型分型面?
(1)应保证顺利起模。
(2)应使铸型的分型面最少。
(3)应尽量使铸型全部或大部分在同一砂箱内
第三章合金铸件的生产
1.何谓孕育铸铁?
与普通灰铸铁有何区别?
其适用范围如何?
孕育铸铁:
经过孕育处理后再进行浇注获得的铸铁。
普通灰铸铁:
不经任何处理,直接进行浇注获得的灰铸铁。
石墨粗大,力学性能差,壁厚敏感性大。
孕育铸铁:
经过孕育处理后再进行浇注获得的铸铁。
强度、硬度高,壁厚敏感性小。
孕育铸铁的适用范围:
高牌号铸铁材质更适宜于生产壁厚铸件,还适用于制造承受较小的动载荷、较大的静载荷、耐磨性好和有一定减震性的铸件,如机床床身。
2.何谓球墨铸铁?
有哪些优越性?
适用于哪些铸件?
球墨铸铁:
将铁液经球化处理,使石墨全部或大部分呈球状而制成的铸铁。
优越性:
与铸铁比,综合力学性能高,与铸钢比,铸造性能好,成本低。
适用于:
承受冲击、振动的零件,强度与塑性中等的零件,载荷大、耐磨、受力复杂的零件,高强度、耐磨、耐疲劳的零件。
3.举例说明碳素铸钢|、灰铸铁、球墨铸铁的牌号表示方法。
铸钢:
ZG230—450:
最低屈服强度230Mpa,最低抗拉强度450Mpa
灰铸铁:
HT—100:
最低抗拉强度100Mpa
球墨铸铁:
QT400—18:
最低抗拉强度400Mpa,最低延伸率为18%
4.灰铸铁、球墨铸铁进行孕育处理的目的是什么?
灰铸铁孕育处理的目的:
细化石墨相,减小壁厚敏感性。
球铁孕育处理的目的:
(1)防白口
(2)有利于使石墨更加细小均匀。
5.试比较铸铁件与铸钢件的铸造工艺特点及铸造性能
铸钢件的铸造工艺特点:
(1)铸件结构设计要合理壁厚适当均匀,圆滑过渡
(2)要合理设计冒口
(3)保证型砂性能要使用优质造型材料
铸铁件的铸造工艺特点:
普通灰铸铁:
铁水不经任何处理,直接浇注。
孕育铸铁:
浇注前铁水需要孕育处理。
球墨铸铁件:
保证有足够的浇注温度,还要求其浇注系统的截面积比灰铸铁大。
多采用半封闭或开放式浇注系统,当内浇道经冒口浇入时,可采用封闭式。
对于厚大热节处,应设冒口、冷铁,以消除缩松、缩孔。
此外,应严格控制型砂的水分以及原铁水的碳、硅含量,并在球化、孕育处理后尽快浇注。
灰铸铁的铸造性能:
流动性好,收缩性小,不易产生缩松、缩孔、裂纹、变形、气孔,壁厚敏感性大。
铸钢的铸造性能:
体收缩和线收缩大,流动性差,裂纹、敏感性较大。
球墨铸铁介于灰铸铁与铸钢之间。
.6.铝合金和铜合金的铸造工艺特点是什么?
铸造性能?
铝合金的铸造工艺特点和铸造性能:
铝硅合金处于共晶成分,铸造性能最好,可浇注薄壁复杂件。
铝铜、铝镁、铝锌合金远离共晶点,铸造性能差,适当提高浇注温度,合理安置冒口,可防止浇不到、缩孔、裂纹等缺陷。
铝合金极易吸气和氧化,必须除气精炼,浇注时,通常采用开放式浇注系统和蛇形浇道避免氧化。
铜合金的铸造工艺特点及铸造性能:
铸造黄铜熔点低,流动性好,可浇注薄壁复杂件,宜用细砂造型,有利于提高铸件表面质量,但容易产生缩孔、缩松,应注意安置冒口、冷铁。
锡青铜的结晶温度范围宽,呈糊状凝固,易产生缩松,对于防渗漏铸件,常采用冷铁提高致密性。
铝青铜的结晶温度范围窄,易获得致密铸件,但收缩大,易产生集中缩孔,要用较大的冒口进行补缩。
铜合金易氧化、吸气,常采用带过滤网的底
注式浇注系统,防止金属飞溅氧化并去除浮渣。
7.何谓孕育处理、球化处理、变质处理?
孕育处理:
向铁水中加入孕育剂增加铸铁结晶形核速度达到细化石墨的目的。
球化处理:
将球化剂加入铁水中在球化剂作用下促使石墨成为球状。
变质处理(铝硅合金的变质处理):
向铝硅合金液中加入变质剂,使粗大的共晶硅变成细小的纤维状或层片状的方法。
第四章特种铸造
1.什么是熔模铸造?
试述其工艺过程。
熔模铸造:
用易熔材料制成模样,然后在模样上涂挂耐火材料,经硬化之后,再将模样排出型外,从而获得无分型面的铸型。
工艺过程:
蜡模制造,结壳,脱蜡,焙烧和浇注,清理。
2.金属型铸造有何优越性?
金属型铸造能完全取代砂型铸造吗?
为什么?
金属型铸造的优越性:
(1)有较高的尺寸精度和较小的表面粗糙度,机械加工余量小。
(2)由于金属型的导热性好,冷却速度快,铸件的晶粒较细,力学性能好。
(3)可实现“一型多铸”提高劳动生产率,且节约造型材料,可减轻环境污染,改善劳动条件。
不能,
(1)因为金属型铸造只能生产简单件,不宜生产大型复杂薄壁件。
a易产生热裂。
b型能力低,产生浇不足、冷隔等缺陷。
(2)金属型铸造只能生产低熔点的合金,温度过高会降低模具的寿命。
3.压力铸造有何优缺点?
它与熔模铸造的范围有何不同?
压力铸造优点:
(1)压铸件尺寸精度高,表面质量好。
(2)可以压铸壁薄、状复杂以及具有很小孔和螺纹的铸件。
(3)压铸件的强度和表面硬度较高。
(4)生产率高,可实现自动化生产。
缺点:
由于充型速度快,型腔中的气体难以排出,在压铸件皮下易产生气孔,故压铸件不能进行热处理,也不宜在高温下工作。
否则,气孔中气体产生膨胀压力,可能使铸件开裂。
金属液凝固快,厚壁处来不及补缩,易产生缩孔、缩松。
设备投资大,铸型制造周期长,造价高,不适宜小批量生产。
压力铸造可用于生产铝合金、锌合金、镁合金和铜合金等有色金属铸件。
熔模铸造主要用来生产形状复杂,精度要求较高或难以切削加工的小型零件。
4.什么是离心铸造?
它在圆筒型或环形铸件生产中有哪些优越性?
离心铸造:
将熔融金属浇入旋转的铸型中,使液体金属在离心力作用下,充满铸型并凝固成型的一种铸造方法。
优越性:
(1)芯即可铸出中空铸件。
(2)液体金属能在铸型中形成中空的自由表面,大大简化了套筒、管类铸件的生产过程。
5.试述熔模铸造、金属型铸造、压力铸造、离心铸造的特点及适用范围。
熔模铸造特点:
(1)可生产形状复杂的铸件及薄壁铸件。
(2)铸型无分型面,铸件尺寸精度高,表面质量好。
(3)工艺过程较复杂,生产周期长,铸型制造费用高,铸件不宜太大。
(4)适应性广,不受合金种类批量的限制。
适用范围:
主要用来生产形状复杂,精度要求较高或难以切削加工的小型零件。
金属型铸造特点:
(1)尺寸精度高,表面光洁。
(2)铸件晶粒较细,力学性能好。
(3)生产率高,可实现“一型多铸”(4)适应性差。
适用范围:
主要用于铜合金、铝合金等有色金属的大批量生产。
压力铸造特点:
(1)尺寸精度高,表面光洁。
(2)可生产薄壁件以及形状复杂的铸件。
(3)强度和表面硬度较高。
(4)生产率高,可实现自动化生产。
(5)压铸件皮下易产生气孔,不能进行热处理。
适用范围:
有色合金的大批量生产。
离心铸造特点:
(1)作中空铸件,工艺简单。
(2)表面光洁。
(3)内部缺陷少(4)金属利用率高。
适用范围:
仅适用于管类料。
第五章铸件结构设计与质量控制
1.简述铸件结构与铸造工艺的关系。
a.铸件的外形应便于取出模型
(1)分型面尽量平直
(2)避免外部侧凹(3)凸台、筋条的设计应便于造型
b.合理设计铸件内腔
(1)简化制造工艺的设计
(2)便于型芯的固定、排气和铸件清理
c.铸件要有结构斜度
2.举例说明铸件外形的结构设计应注意哪些要求?
为什么?
(1)分型面尽量平直。
平直的分型面可避免操作费时的挖砂造型或假箱造型,同时,可使铸件的毛边少,便于清理,因此,尽力避免弯曲的分型面。
(2)避免外部侧凹。
铸件在起模方向若侧凹,必将增加分型面的数量,这不仅使造型费工,而且增加了错箱的可能性,使铸件的尺寸误差增大。
(3)凸台、筋条的设计。
设计铸件上凸台、筋条时,应考虑便于造型。
3.举例说明铸件内腔的结构设计应注意哪些要求?
为什么?
(1)简化制造工艺的设计。
在铸件设计中,尤其是设计批量很小的产品时,应尽量避免或少用型芯。
如悬臂支架,如果采用中空结构,必须以悬臂型芯来形成,这种型芯需用型芯撑加固,下芯费工。
改进:
开式结构,省去了型芯,降低了成本。
(2)便于型芯的固定,排气和铸件的清理。
如轴承架,其内腔采用两个型芯,其中较大的呈悬臂状,须用型撑来加固。
改进:
使型芯为整体型芯,则型芯的稳定性大为提高,且下芯简便易于排气。
4.为什么要规定最小壁厚?
不同铸造合金要求一样吗?
为什么?
保证铸造合金的流动性,避免浇不足、冷隔等缺陷的形成,所以要规定最小壁厚。
不同铸造合金的最小壁厚不同,因为铸造合金的流动性不同,铸件的“最小壁厚”与合金的种类、铸造方法和铸件尺寸等因素有关。
5.铸件的壁厚如不均匀对铸件质量有哪些影响?
厚壁处形成金属集聚的热节,致使厚壁处易产生缩孔、缩松等缺陷,同时还会增大热应力产生变形甚至裂纹。
6.铸钢件对铸造结构有哪些要求?
(1)壁厚应尽量均匀或设计成定向凝固方式以利冒口补缩
(2)铸件壁不能太薄,不宜设计成复杂形状的铸件
(3)在壁的相交处要有比灰铸铁大的过渡圆角
(4)铸件薄弱处多用肋加固
7.铸造方法对铸件结构的影响主要表现在哪些方面?
铸件形状、铸件大小、铸件壁厚、铸件最小壁厚、拔模斜度、最小铸孔及槽。
8.判断下列零件结构是否合理,若不合理,请改正,并说明理由。
不合理,铸件壁间的转角处一般应有结构圆角,铸件壁的直角相交处,承载时将形成应力集中,且因结晶的方向性,形成柱状晶结合脆弱面,再加上该处金属局部集聚形成热节,易产生裂纹、缩孔、缩松等缺陷。
不合理,壁厚不均匀,若铸件各部分的厚度差别过大,则厚壁处形成金属集聚的热节,致使厚壁处易产生缩孔、缩松等缺陷,同时还会增大热应力,产生变形甚至裂纹。
10.试述灰口铸铁、球墨铸铁、铸钢的铸造性能特点与适宜的结构。
灰口铸铁铸造性能特点:
(1)流动性好,收缩小,铸造性能好,减震减磨性能好
(2)综合力学性能低,并随截面增加显著下降(3)抗压强度较高
适宜的结构:
薄壁(但不能过薄,以防产生白口)、形状复杂的铸件。
不宜用于厚大铸件,否则强度过低。
球墨铸铁铸造性能特点:
(1)铸造性能比灰铸铁差
(2)综合力学性能比灰铸铁高很多
适宜的结构:
(1)壁厚均匀
(2)避免厚大截面,对某些厚大件可设计成中空均匀壁厚的截面或带肋结构。
铸钢件铸造性能特点:
(1)铸造性能差,减震性差
(2)体收缩和线收缩大(3)流动性差,熔点高,易氧化(4)裂纹敏感性较大(5)低碳钢焊接性好(6)力学性能高
适宜的结构:
(1)壁厚应尽量均匀或设计成定向凝固方式,以利补缩。
(2)铸件壁不能太薄,不宜设计复杂形状的铸件(3)在壁的相交处要有结构圆角(4)铸件薄弱处多用肋加固(5)可采用铸—焊结构
11.最小壁厚临界壁厚
最小壁厚:
保证铸造合金的流动性,避免浇不到、冷隔等缺陷的壁厚。
临界壁厚:
可以保证晶粒细小且不产生缩松、缩孔、组织粗大等缺陷的壁厚。