铜尾渣在水泥中的应用综述要点.docx
《铜尾渣在水泥中的应用综述要点.docx》由会员分享,可在线阅读,更多相关《铜尾渣在水泥中的应用综述要点.docx(14页珍藏版)》请在冰豆网上搜索。
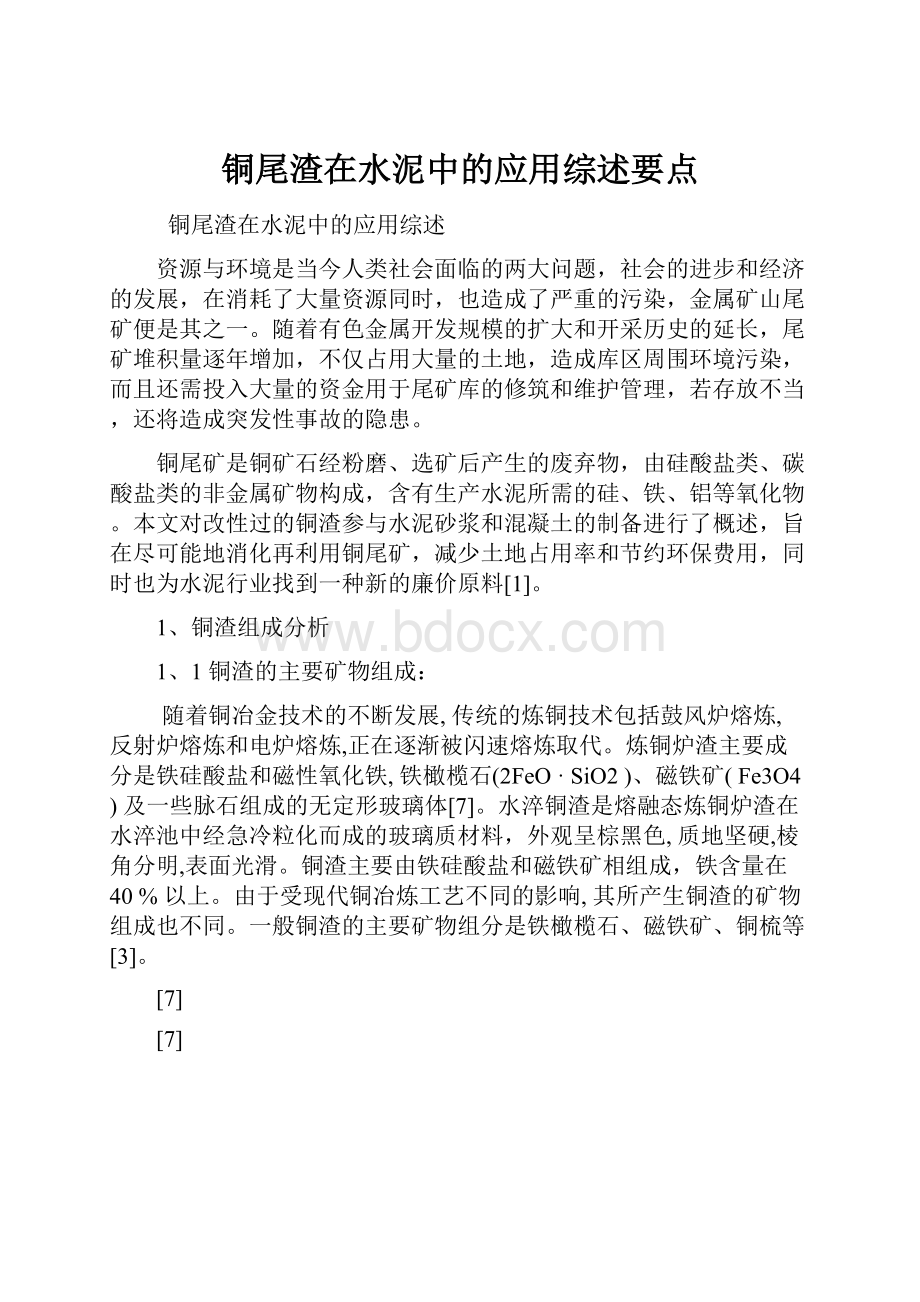
铜尾渣在水泥中的应用综述要点
铜尾渣在水泥中的应用综述
资源与环境是当今人类社会面临的两大问题,社会的进步和经济的发展,在消耗了大量资源同时,也造成了严重的污染,金属矿山尾矿便是其之一。
随着有色金属开发规模的扩大和开采历史的延长,尾矿堆积量逐年增加,不仅占用大量的土地,造成库区周围环境污染,而且还需投入大量的资金用于尾矿库的修筑和维护管理,若存放不当,还将造成突发性事故的隐患。
铜尾矿是铜矿石经粉磨、选矿后产生的废弃物,由硅酸盐类、碳酸盐类的非金属矿物构成,含有生产水泥所需的硅、铁、铝等氧化物。
本文对改性过的铜渣参与水泥砂浆和混凝土的制备进行了概述,旨在尽可能地消化再利用铜尾矿,减少土地占用率和节约环保费用,同时也为水泥行业找到一种新的廉价原料[1]。
1、铜渣组成分析
1、1铜渣的主要矿物组成:
随着铜冶金技术的不断发展,传统的炼铜技术包括鼓风炉熔炼,反射炉熔炼和电炉熔炼,正在逐渐被闪速熔炼取代。
炼铜炉渣主要成分是铁硅酸盐和磁性氧化铁,铁橄榄石(2FeO·SiO2)、磁铁矿(Fe3O4)及一些脉石组成的无定形玻璃体[7]。
水淬铜渣是熔融态炼铜炉渣在水淬池中经急冷粒化而成的玻璃质材料,外观呈棕黑色,质地坚硬,棱角分明,表面光滑。
铜渣主要由铁硅酸盐和磁铁矿相组成,铁含量在40%以上。
由于受现代铜冶炼工艺不同的影响,其所产生铜渣的矿物组成也不同。
一般铜渣的主要矿物组分是铁橄榄石、磁铁矿、铜梳等[3]。
[7]
[7]
1.2铜渣的主要化学成分
铜的冶炼由于工艺不同所产生铜渣的化学组成也不同。
下面是不同冶炼方法产生的铜渣常见的化学成分。
1.3铜渣的物理指标
云南某冶炼厂铜渣的颗粒组成和物理指标见下表。
2、尾矿作水泥混合材使用的可行性分析
水泥混合材长期使用活性材料(如高炉矿渣、粉煤灰、火山灰质材料),由于活性混合材能参与水泥的水化反应,其添加对水泥强度影响较小。
[2]
2.1尾矿作非活性材料的应用试验:
试验选取海螺水泥厂熟料、湖南岳阳石膏、海螺水泥厂石子及煤矸石、铜陵某矿2003年年度平均尾矿样为混合材粉磨制成水泥样进行试验。
混合材配比(%)试验方案见表1表1
检测结果见表2表2
结果分析:
从上表检测结果看:
T1-T5五组试验安定性和凝结时间均正常。
T1空白试验28天的抗压强度59.5MPa,T228天抗压强度41.5MPa,T328天抗压强度
50MPa.T2/T1为69.7%,T3/T1为84%。
根据GB12958-1999国家标准附录A中规定,水泥胶砂28天抗压强度比大于或等于75%的为活性材料,小于75%的为非活性材料,故粉煤灰为活性材料,所取铜尾矿为非活性材料。
从T4和T5两组实验比较也能发现,掺尾矿样28天抗压强度为35.2MPa,能满足国标PC32.5R水泥要求。
因此铜尾矿可以作为非活性混合材生产复合硅酸盐水泥。
2.2尾矿作活性材料的应用研究
从地质成矿条件分析,铜矿属热成矿,其矿物物性应与火山灰质材料相似。
其活性不能表现是因为某种抑制。
据此探索有关激发剂对铜尾矿进行改性试验。
试验结果:
试验结果分析:
从检测报告的检测结果看:
T1-T9九组试验安定性和凝结时间均正常。
T1空白试验28天抗压强度55.8MPa,T2试验28天抗压强度45.1MPa,T5试验28天抗压强度41.1MPa.T2/T1为81.36%,T5/T1为73.65%。
如按火山灰质硅酸盐水泥生产,根据GB/T2847-1996国家标准水泥胶砂28天抗压强度比
62%的为火山灰质活性材料,
62%的为非活性材料,因此,所取尾矿样为火山灰质活性材料。
有待按该标准附录A中规定进行火山灰性试验。
试验结果评价:
通过本次试验分析,所选外加剂(激发剂)的掺入能对尾矿进行物理、化学激发改性,可使尾矿活性大为提高,使其具备很好的水化活性,性能类似于高炉矿渣和粉煤灰,且品质稳定,与其它火山灰质材料有一定的相容性,并能吸收游离氧化钙,并改善水泥安定性。
且T5、T7、T8、T928天抗压强度(MPa)达41.1、48.3、44.5、41.3,比国标火山灰质硅酸盐水泥32.5#水泥28天抗压强度32.5Mpa的指标尚高9、15.8、12、8.8MPa。
。
因此尾矿作火山灰质活性混合材使用掺量可超过30%。
但尾矿作火山灰质活性混合材使用必须按GB/T2847-1996标准附录中规定进行火山灰性试验且合格,并作为水泥新型混合材报省级建材主管部门审批[2]。
3、铜渣活性激发
3.1热激发
将铜渣分别于850,900,950,1000,1050℃进行了煅烧,探讨铜渣在不同温度和不同煅烧时间下的晶体变化,为铜渣的综合利用提供可靠的基础数据。
采用XRD法和SEM/EDX法表征了铜渣在不同煅烧温度和不同煅烧时间下的晶相结构和显微结构。
实验结果表明:
随着煅烧温度的提高和煅烧时间的延长,铜渣中组分晶相发生如下转变过程:
2FeO·SiO2+0.5O2→α-Fe2O3+SiO2和Fe3O4→γFe2O3→αFe2O3.氧化煅烧处理可以实现铜渣中主要晶相铁橄榄石离解,氧化铁的富集和析出[8]。
3.1机械激发
铜渣虽然含有C2S、C3S活性体,具有胶凝活性,但相比于水泥活性很低,在水泥中应用通常通过机械或化学的方式对铜渣的活性进行激发。
机械激发是指通过机械粉磨以增加铜渣的细度提高比表面积,破坏铜渣中的玻璃体,将包裹在里面的硅酸盐和铝酸盐等活性矿物暴露出来,增加与水的接触面积。
铜渣的细度越大,活性越大,当比表面积达到400-550m2/kg时,活性被充分激发出来,之后活性增加不再明显,并且粉磨难度增大,存在破碎一团聚平衡,成本增加[3]。
3.2微波激发
矿石中有用矿物(不含卤化物)主要分为两大类:
硫化矿和氧化矿。
前人的研究结果表明,大多数硫化矿物和部分氧化矿物在微波场中的升温速率很快,而二氧化硅等脉石矿物在微波场中的升温速率均较慢,甚至不升温。
根据微波的选择性加热和快速加热的特点,对矿石进行微波处理,由于加热的不均匀,使矿石内部的应力状况发生改变,达到一定程度,矿石上就出现微裂纹,这不仅使有用矿物暴露出来,同时也降低了矿石的硬度。
这对于硬度较大的矿石的破碎、研磨和低品位复杂多金属矿石的矿物解离意义重大[9]。
SWKingman等人还在2004年研究了微波预处理对铅锌矿石破碎程度的影响。
预先进行了铅锌矿石经微波处理的硬度试验。
矿石硬度的变化由矿石在微波场中的停留时间决定,并且进行了经微波处理的样品与未经微波处理的样品的硬度变化比较。
利用一台多模式谐振腔微波加热器进行试验,结果发
现,当所用微波功率为15kW、辐射时间为0.5s时,矿石硬度明显降低,对于粒度14.53mm的矿石,矿石硬度降低40%以上。
在该类型加热器腔体中,利用低功率进行试验,辐射效果不明显。
单模腔体初步试验在微波功率为10kW、停留时间0.1s下进行,矿石硬度降低50%。
试验结果表明,高电场强度对矿石的破坏有重要意义。
初级能量平衡试验表明,单模加热对矿石硬度降低更有好处。
3.3铜渣冷却方式与活性的关系
铜渣的冷却速度对铜渣的活性起着决定性作用。
目前,铜渣冷却方式有自然冷却、水淬、保温冷却加水淬三种冷却方式。
铜渣中铜矿物结晶粒度大小和铜渣的冷却速度密切相关铜渣缓慢冷却有利于铜相粒子迁移聚集长大和改善渣的可磨性
这是铜渣浮选的关键。
在铜渣的缓冷过程中,铜渣熔体的初析微晶可通过溶解一沉淀形式成长,形成结晶良好的自形晶或半自形晶,同时有用矿物扩散迁移、聚集并长大成相对集中的独立相,易于磨矿单体解离和分别回收。
急速冷却会使铜渣形成非晶质构造,这种非晶质构造会阻止微晶粒析出和迁移聚集,进而阻止析出的铜相粒子的长大,使铜渣中的铜粒子晶粒细而分散,既使细磨也很难使其达到单体解离,致使铜渣中的铜难以浮选回收。
研究表明,1000℃以上的铜渣冷却,其冷却速度以不大于1一3℃/min为宜,此时铜渣中基本上没有相变发生,即采用缓慢冷却;1000℃以下采用自然冷却或喷水冷却不会对铜渣的可磨性和浮选性能产生太大影响。
对于建筑材料中选用的铜渣,最好选1000℃以下喷水冷却的铜渣,这样既可保证铜渣的可磨性,也可保证铜渣的活性[3]。
4、生料的易烧性
4.1水泥生料易烧性
在理论上是指该生料组分是容易转变成水泥熟料相物质的数量,而实际上通常用生料按一定制度煅烧后,熟料中f一CaO含量来衡量。
因此,为了研究铜尾矿全代铁粉配料的生料易烧性,将率值相同的两组配料在相同煅烧条件下进行煅烧,用甘油酒精法测f一Cao含量,试验结果见表4
由表4及表5结果发现,无论是在相同煅烧温度下,还是在相同保温条件下,率值相同时,用铜尾矿全代铁粉缎烧的B组熟料的f一CaO含量都低于铁粉配料的A组熟料,这说明用铜尾矿配料的生料易烧性较好。
众所周知,熟料的最低共熔温度与液相粘度决定于系统组分的性质和数量。
由于铜尾矿中有FeO的加入,使熟料液相组成发生变化,而FeO的熔点低于Fe2O3,使熟料最低共熔物的熔点降低,液相提前出现,液相粘度降低,从而促进固相反应,加速熟料的生成,降低了f一CaO的含量;另外,铜尾矿中还含有丰富的微量元素,因其本身的熔点很低,于1000℃左右即开始熔融,所以对水泥熟料的低温锻烧将产生积极作用。
此外,铜尾矿全代铁粉配料,KH=0.88时f-CaO含量较相同煅烧条件下KH=0.92的低。
这是由于KH值减小,相应生料中CaO含量减少,SiO2含量
相对提高,阿利特形成过程中有更多的SiO2与CaO饱和,使f一CaO含量较低[4]。
4.2熟料游离钙与铜尾矿掺入量的关系[5]
熟料f-CaO>3.5%,会造成水泥安定性不良,要使其小于3.5%,就必须找出铜尾矿掺量与熟料f-CaO之间的定量关系。
我们选用了两种游离钙不同的熟料,分别按一定比例掺入铜尾矿,进行游离钙的测定,其结果见表4。
从以上试验看,铜尾矿掺入量每增加5%,熟料中的f-CaoO可降低0.2%左右。
当掺量增加到15%-20%,两组熟料f-CaO可降至3.5%以下。
当然,此关系也并非固定不变。
5、铜尾渣对水泥砂浆和混凝土强度及耐久性影响[6]
一项实验调查研究了铜渣作为细骨料对水泥砂浆和混凝土的性能的影响。
用不同比例的铜渣从0%(用于控制混合物)到100%作为细骨料替换,制备了各种砂浆和混凝土混合物。
水泥砂浆混合物用抗压强度评估,而混凝土混合物用和易性、密度、抗压强度、抗拉强度、弯曲强度和耐久性来评估。
水泥砂浆的结果显示所有混合了不同比例的铜渣的混合物取得了比参照物可比或更高的抗压强度。
同时,在铜渣的替代量达到50%时,砂浆的抗压强度与参照物相比改善了超过70%。
混凝土的实验结果显示,随着铜渣含量的增加,混凝土的密度以将近5%的速率轻微增加,然而与参照物相比其和易性随着铜渣比例的增加而显著提高。
铜渣作为砂子的替代物,当替代量达到40-50%时,其混合物与参照物相比显出了可比的强度。
然而,添加更多的铜渣会导致混合物的强度降低,因为混合物中自由水含量的增加。
同时,结果已被证实,随着铜渣含量增加,其替代量达到50%前,混合物对表面水的吸收量不断降低。
超过50%后,吸收速率会迅速增加,体积的渗透空隙率与参照物的不相上下。
因此,建议40-50%(重量的砂)的铜渣作为细骨料的替代品以获得一个具有良好强度和耐久性的混凝土的需求。
5.1铜渣替代对水泥砂浆强度的效应
不同比例的混合物实测抗压强度值展示在表4。
试验结果表明所有样品产生更高的抗压强度分别比规范要求的为水泥砂浆的3和7天养护之后的15和23MPa,。
对于所有的混合物,养护期增加了抗压强度,强度的增加在养护的早期更快(3、7和28天)。
表格4还表明,在全部凝期,所有混合物具有相对于控制混合物(100%沙子)更高的抗压强度。
另外,随着铜尾渣的成分增加混凝土砂浆的强度增加,如此一直到铜尾渣替代比例达到50%。
超过50%以后抗压强度会随着铜尾渣增加而减少。
但是,有着100%铜尾渣的7号混合物表现出了比控制混合物更高的强度。
含有50%铜尾渣的4号混合物表现出了最高的28天平均抗压强度47.5N/mm2,几乎74%的样本抗压强度都比控制混合物的高。
对于长时间的养护(比如56天和90天),当掺入铜尾渣时,大多数的样品没有表现出不利影响(比如强度下降)。
虽然所有混合物都表现出了比控制混合物更高的抗压强度,可以这么说50%的铜尾渣替代相对于沙子替代具有更高的抗压强度,在砂浆中的强度增加70%以上。
5.2铜尾渣替代对于混凝土致密度和工作性的影响[6]
表格5表明坍落度值作为一种测定新拌混凝土工作性,以及掺有不同比例铜尾渣混合物的致密度的方法。
测试结果显示,随铜尾渣替代成分增加,混凝土的工作性提升。
控制混合物100%沙子的实测坍落度为65.5mm,而100%铜尾渣替代的混凝土混合物(8号混合物)为200mm。
工作性显著的增加的原因是铜尾渣相对于沙子的少吸水性,因此水化后更多的自由水会留在拌合物中。
但是,发现具有高铜尾渣替代含量的混凝土混合物中存在离析和泌水(混合物7号和8号)。
在其他研究中也有类似的发现,已经发现细渣骨料替代混凝土有一种大量泌水的趋势,因为从测得混凝土坍落度得到他们的致密度太高以及其中含有太多水分。
同时,随着铜尾渣成分增加,混凝土致密度(表格5)轻微增加。
混凝土致密度增加了大约5%(对于8号混合物),从而导致了铜尾渣的高比重。
5.3铜尾渣替代对于普通混凝土的强度影响
铜尾渣作为细骨料替代对于混凝土强度的影响在表格5中已经给出,该表显示了7天和28天立方抗压强度,平均28天抗压强度和抗弯强度。
图2绘制了在7天和28天,用不同比例的钢渣固化混凝土混合物的无侧限抗压强度值。
测试结果显示,对于使用60%铜尾渣替代制得的混合物,该混凝土的抗压强度与100%沙子控制混合物明显不同。
但是,对于80%和100%铜尾渣混合物(7号,8号混合物),其强度低于控制混合物且迅速下降。
具有40%铜尾渣的4号混合物具有最高28天抗压强度48.1N/mm2,相对于控制混合物的45N/mm2。
而且发现具有80%铜尾渣的7号混合物具有最低抗压强度34.8N/mm2。
另外,7号混合物的抗压强度比控制混合物低22%。
具有很高铜尾渣含量的混凝土拌合物抗压强度减少,时因为铜尾渣相对于沙子的吸水性能差导致了自由水含量的增加。
如表格5显示,这致使混凝土工作性大大增加以及强度下降。
同时,图2表明不同混凝土拌合物在7天和28天养护的持续抗压强度,养护7天强度可达到28天强度的80%。
Wu和其他人观测到,在进行具有不同铜尾渣含量混凝土样本微结构测试之后,40%替代强度增加主要归咎于铜尾渣的物理性能。
铜尾渣比沙子有更好的抗压能力,如果沙子作为主要细骨料和铜尾渣支撑整个混凝土拌合物,铜尾渣可以部分减少应力集中。
同时,铜尾渣颗粒锋利的粒角边缘,可以提高混凝土集体的凝聚力。
已经知道,由于沙子能可以提高水泥浆和粗骨料之间的粘附性。
然而,沙子随多年的风化导致砂粒的边缘呈圆形,其磨损性能变弱了,是不利于联锁性能的复合材料。
铜渣颗粒锐利的角边缘可以在一定程度上起到补偿砂的作用。
因此,进一步提高混凝土的凝聚力。
另一方面,
玻璃表面纹理的铜渣颗粒对凝聚力有负面影响。
同时,低吸水性能的铜渣会多水分在混凝土中,这可能会导致高铜渣含量,泌水量过多。
结果导致在混凝土中形成内部孔隙和毛细管通道,降低其质量。
因此,当铜渣含量较低,混凝土的强度可以改善,而如果铜渣含量超过40%,混凝土的强度会大大减少伴随凝聚力的降低。
还值得一提的是,有超过70%的砂浆抗压强度的提高发生在铜渣替代量占50%时(表4)。
而混凝土的抗压强度有一个轻微的4.4%的增加,当铜渣替代量为50%时(表5)。
这种强度方面改善的差异在水泥砂浆和混凝土之间,可能因于在水泥粘合中的粒子键的不一样。
此外,粗骨料是混凝土中引入的混合物,这可能导致同样的混合物在砂浆和混凝土有不同的行为。
28天抗拉强度的混凝土也给出了在表5。
结果表明,平均抗拉强度在容许值之内符合设计规范。
为达到设计目的,拉伸强度可以根据经验取0.45pfcu。
28天抗折强度(模量的平均断裂)值展示在表4。
结果表明,所有混凝土混合物的弯曲强度值略高于允许的设计值。
混凝土的抗弯强度通常是0.75pfcu。
这个混凝土的试验抗折强度平均为6.9N/Mm2,传统的计算经验是5N/mm2。
为评估用铜渣作为细骨料的混凝土的耐久性,我们做了两个实验。
第一测试测量混凝土的表面水吸收率,而第二个测试测量混凝土的渗透孔洞的体积百分比。
最初的表面吸收测试结果显示在图3和图4。
图3表明,所有的混合物显示一个类似的趋势,随着时间增加表面水吸收率降低。
该下降一般在第一个30分钟降得最快,,在后来的120分钟内后来缓慢降低。
所有混合物产生的流动率都在指定的范围内,第一个十分钟里为0.05ml/m2s和3.6ml/m2s之间。
同时,图3表明混合物#4,40%的铜渣替代,在整个测试时间显示最低的表面水吸收,而混合物#8,100%铜渣替代,显示最大的表面水吸收。
图4表明,当铜渣替代量在40%之前,增加铜渣替代含量会普遍降低面吸水。
超过40%,吸收随铜渣的含量增加而增加。
这主要是由于增加的自由水含量会导致硬化混凝土创建更多的孔隙。
然而,在120分钟,多达50%替代铜渣的混合物的表面吸水值与100%的混合砂相比。
图5显示了混凝土混合物在28天养护后体积的水渗透空隙的含量。
结果表明,在铜渣含量高达40%前,随铜渣的置换量增加,渗透孔隙的比例略微下降。
超过40%,孔隙体积的增加变得与参照物相似。
因此,建议40-50%(按重量计算)的
铜渣部份取代细骨料制作的混凝土将会产生一个良好的耐久性。
1、对于水泥砂浆,混合了不同比例铜渣的混合物与参照物比都产生了类似或更高的抗压强度。
用50%的铜渣替代的砂浆,其抗压强度与参照物相比提高了70%。
2、当铜渣作为砂的替代物,混合物的密度增加了5%,而其和易性却随着铜渣的增加大幅增加。
这是由于低的水吸收率和玻璃表面效应。
3、混凝土用低于50%铜渣替代砂,其抗压、抗拉和抗弯强度与参照物相似,但它们会随铜渣含量的进一步增长而下降。
4、用低于40%的铜渣替代砂的混凝土的表面吸水率都降低了。
5、低于50%的铜渣替代,随其含量增加,混合物的渗透孔隙的体积减少。
6、效益分析
利用铜尾矿作混合材生产水泥,具有显著的经济和社会效益。
水泥安定期的缩短,使原先压库的水泥能按时出厂,缓解了资金周转困难的压力,保证了生产正常运转,其潜在的经济效益十分可观。
同时,铜尾矿又是一种廉价的工业废渣,可用于水泥生产中。
由于铜尾矿是一种粉末状废渣,堆放时占地面积大,且在风沙天,更加剧了当地空气污染。
因此,合理利用铜尾矿,可以减轻对环境的污染,社会效益显著[5]。
参考文献:
[1]饶春如,肖国先,郜志海,周慈.铜尾矿替代粘土煅烧硅酸盐水泥熟料的研究[J].苏州科技学院学报,2009,(4):
37-40.
[2]唐达高.铜尾矿在水泥生产中的应用研究[J].中国资源综合利用,2005,(10):
17-20.
[3]周惠群,李强.铜渣在建筑材料中资源化利用的研究进展.2012国内外水泥粉磨新技术交流大会暨展览会论文集,2012:
277-281.
[4]郑秀华,赵晶,王金忠.铜尾矿对水泥生料及水泥强度的影响1999[J].房材与应用,1999,
(2):
8-15.
[5]许小荣,张月.铜尾矿作混合材在水泥生产中的应用[J].研究与开发,青海科技,2001,(4):
36-37.
[6]KhalifaS.Al-Jabri*,AbdullahH.Al-Saidy,RamziTaha.Effectofcopperslagasafineaggregateonthepropertiesofcementmortarsandconcrete.ConstructionandBuildingMaterials25(2011)933–938.
[7]张林楠,张力,王明玉,隋智通.铜渣的处理与资源化[J].矿产综合利用,2005,(5):
22-26.
[8]胡建杭,王华,刘慧利,李磊.铜渣在不同煅烧温度的晶相结构[J].湖南科技大学学报(自然科学版),2011,26
(2):
97-100.
[9]赵俊蔚,赵国惠,郑 晔,邢志军,马金瑞.微波加热在矿冶方面的应用研究现状[J].选矿与冶炼,2008,12(29):
39-43.