基于并行工程汽车保险杠热流道模具设计.docx
《基于并行工程汽车保险杠热流道模具设计.docx》由会员分享,可在线阅读,更多相关《基于并行工程汽车保险杠热流道模具设计.docx(53页珍藏版)》请在冰豆网上搜索。
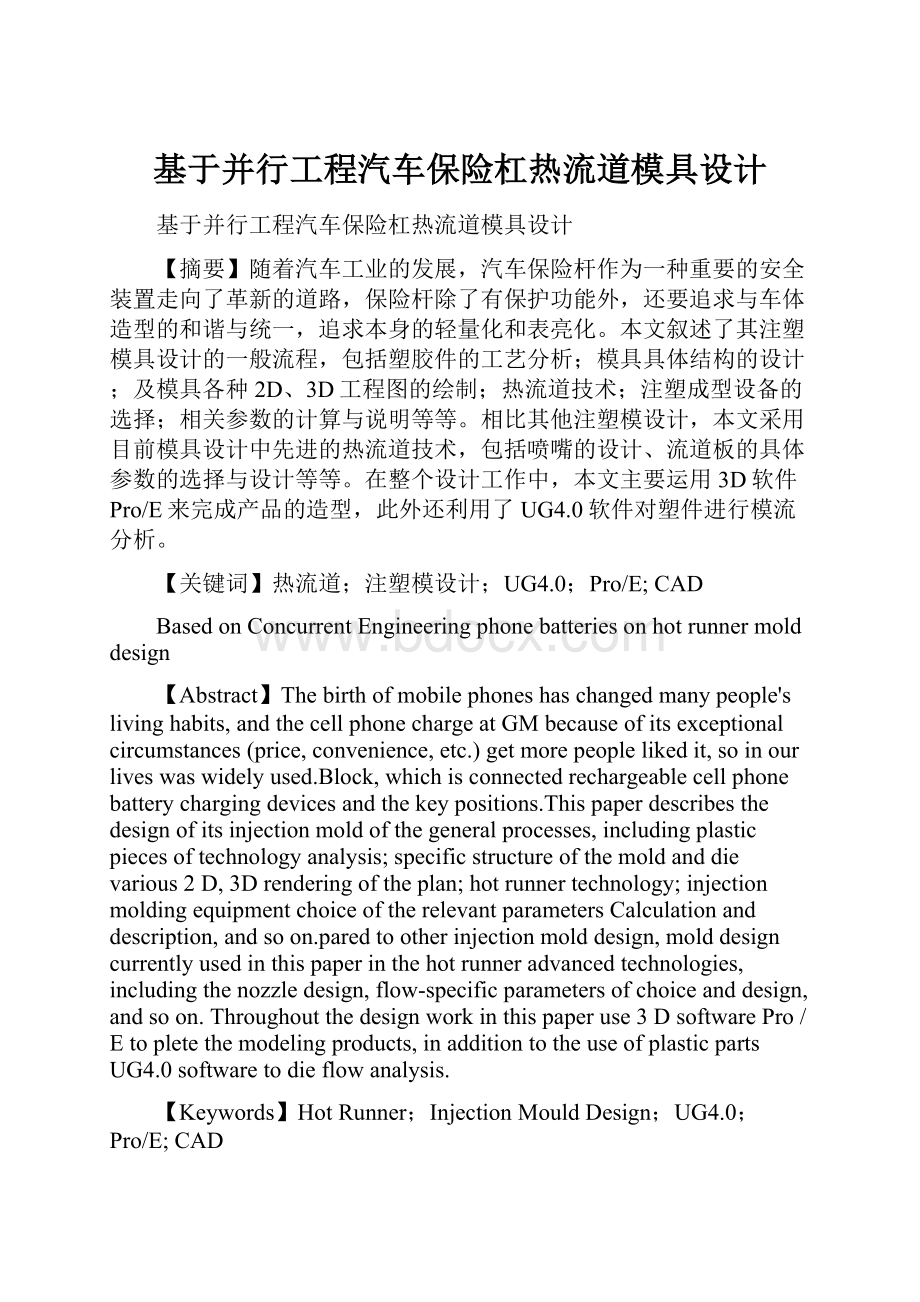
基于并行工程汽车保险杠热流道模具设计
基于并行工程汽车保险杠热流道模具设计
【摘要】随着汽车工业的发展,汽车保险杆作为一种重要的安全装置走向了革新的道路,保险杆除了有保护功能外,还要追求与车体造型的和谐与统一,追求本身的轻量化和表亮化。
本文叙述了其注塑模具设计的一般流程,包括塑胶件的工艺分析;模具具体结构的设计;及模具各种2D、3D工程图的绘制;热流道技术;注塑成型设备的选择;相关参数的计算与说明等等。
相比其他注塑模设计,本文采用目前模具设计中先进的热流道技术,包括喷嘴的设计、流道板的具体参数的选择与设计等等。
在整个设计工作中,本文主要运用3D软件Pro/E来完成产品的造型,此外还利用了UG4.0软件对塑件进行模流分析。
【关键词】热流道;注塑模设计;UG4.0;Pro/E;CAD
BasedonConcurrentEngineeringphonebatteriesonhotrunnermolddesign
【Abstract】Thebirthofmobilephoneshaschangedmanypeople'slivinghabits,andthecellphonechargeatGMbecauseofitsexceptionalcircumstances(price,convenience,etc.)getmorepeoplelikedit,soinourliveswaswidelyused.Block,whichisconnectedrechargeablecellphonebatterychargingdevicesandthekeypositions.Thispaperdescribesthedesignofitsinjectionmoldofthegeneralprocesses,includingplasticpiecesoftechnologyanalysis;specificstructureofthemoldanddievarious2D,3Drenderingoftheplan;hotrunnertechnology;injectionmoldingequipmentchoiceoftherelevantparametersCalculationanddescription,andsoon.paredtootherinjectionmolddesign,molddesigncurrentlyusedinthispaperinthehotrunneradvancedtechnologies,includingthenozzledesign,flow-specificparametersofchoiceanddesign,andsoon.Throughoutthedesignworkinthispaperuse3DsoftwarePro/Etopletethemodelingproducts,inadditiontotheuseofplasticpartsUG4.0softwaretodieflowanalysis.
【Keywords】HotRunner;InjectionMouldDesign;UG4.0;Pro/E;CAD
1.前言
1.1 汽车保险杠简介
1.1.1概述
汽车保险杠是吸收缓和外界冲击力、防护车身前后部的安全装置。
20年前,轿车前后保险杠是以金属材料为主,用厚度为3毫米以上的钢板冲压成U形槽钢,表面处理镀铬,与车架纵梁铆接或焊接在一起,与车身有一段较大的间隙,好像是一件附加上去的部件。
随着汽车工业的发展,汽车保险杠作为一种重要的安全装置也走向了革新的道路上。
今天的轿车前后保险杠除了保持原有的保护功能外,还要追求与车体造型的和谐与统一,追求本身的轻量化。
为了达到这种目的,目前轿车的前后保险杠采用了塑料,人们称为塑料保险杠。
1.1.2结构组成
塑料保险杠是由外板、缓冲材料和横梁三部分组成。
其中外板和缓冲材料用塑料制成,横梁用厚度为1.5毫米左右的冷轧薄板冲压而成U形槽;外板和缓冲材料附着在横梁上,横梁与车架纵梁螺丝连接,可以随时拆卸下来。
这种塑料保险杠使用的塑料,大体上使用聚酯系和聚丙烯系两种材料,采用注射成型法制成。
例如标致405轿车的保险杠,采用了聚酯系材料并用反应注射模成型法做成。
而大众的奥迪100、高尔夫、XX的桑塔纳、XX的夏利等型号轿车的保险杠,采用了聚丙烯系材料用注射成型法制成。
国外还有一种称为聚碳酯系的塑料,渗进合金成分,采用合金注射成型的方法,加工出来的保险杠不但具有高强度的刚性,还具有可以焊接的优点,而且涂装性能好,在轿车上的用量越来越多。
1.1.3作用
塑料保险杠具有强度、刚性和装饰性,从安全上看,汽车发生碰撞事故时能起到缓冲作用,保护前后车体;从外观上看,可以很自然的与车体结合在一块,浑然成一体,具有很好的装饰性,成为装饰轿车外型的重要部件。
另外,为了减少轿车在发生侧撞事故时对乘员的伤害,在轿车上通常安装有车门保险杠,以增强车门的防撞冲击力。
这种方法实用、简单,对车身结构的改动不大,已经普遍推广使用。
早在’93XX国际汽车展览会上,参展的本田雅阁将一扇车门剖开一部分,专门露出车门保险杠给观众看,以示其良好的安全性能。
安装车门保险杠就是在每扇车门的门板内横置或斜置数条高强度的钢梁,起到车前车后保险杠的作用,做到整部轿车前后左右都有保险杠“护驾”,形成一个“铜墙铁壁”,使得轿车乘员有一个最大限度的安全区域。
当然,安装这种车门保险杠对于汽车制造商来讲,无疑会增加一些成本,但对于轿车的乘员来讲,安全性和安全感都会增加了许多。
1.2塑料注塑模技术
1.2.1塑料及其应用
从制件的实物分析,并结合市场上普遍采用的材料分析,可以知道本次设计的塑胶支撑件所用材料是塑料PP,化学名称是聚丙烯,英文名称是Polypropylene。
PP为结晶型高聚物,常用塑料中PP最轻,密度仅为0.91g/cm3(比水小)。
通用塑料中,PP的耐热性最好,其热变形温度为80-100℃,能在沸水中煮。
PP有良好的耐应力开裂性,有很高的弯曲疲劳寿命,俗称“百折胶”。
PP的综合性能优于PE料。
PP产品质轻、韧性好、耐化学性好。
PP的缺点:
尺寸精度低、刚性不足、耐候性差、易产生“铜害”,它具有后收缩现象,脱模后,易老化、变脆、易变形。
PP是所有合成树脂中密度最小的,仅为0.90~0.91g/cm3,是PVC密度的60%左右。
这意味着用同样重量的原料可以生产出数量更多同体积的产品。
PP在熔融温度下有较好的流动性,成型性能好,PP在加工上有两个特点:
其一:
PP熔体的粘度随剪切速度的提高而有明显的下降(受温度影响较小);其二:
分子取向程度高而呈现较大的收缩率。
PP的加工温度在200-300℃左右较好,它有良好的热稳定性(分解温度为310℃),但高温下(270-300℃),长时间停留在炮筒中会有降解的可能。
因PP的粘度随着剪切速度的提高有明显的降低,所以提高注射压力和注射速度会提高其流动性,改善收缩变形和凹陷。
模温宜控制在30-50℃X围内。
PP熔体能穿越很窄的模具缝隙而出现披锋。
PP在熔化过程中,要吸收大量的熔解热(比热较大),产品出模后比较烫。
PP料加工时不需干燥,PP的收缩率和结晶度比PE低。
1.2.2注塑成型工艺简介
塑料在成型加工过程中表现出的一系列特性,也就是塑料的成型工艺特性,与塑料的品种、模具结构等密切相关,设计者必须对塑料的成型工艺有充分的了解,这样才有利于合理地选择设计模具,达到控制产品质量的目的。
塑料模塑成型的方法有很多,它主要的成型方法有注塑成型、吹塑成型、挤压成型、压缩成型、热成型等。
其中注塑成型是塑料加工中被广泛应用的方法之一,主要优点是可以制造各种结构复杂、尺寸精密的成型制件、对各种塑料的成型适应性强、成型周期短、可多腔成型等。
注塑成型又称注射成型,其成型的简单过程为:
利用注塑机将粒状或粉状的塑料原料熔融后,通过喷嘴和模具的浇注系统使其快速进入温度较低的模具内,充满后经过保压和冷却固化,形成与模腔形状一致的塑料制品,然后开启模具取出制件。
注塑成型在塑料制件成型中占有很大比重,约占塑料制品总量的20%~30%,世界上注塑模具产量约占塑料成型模具总产量的50%。
用于注塑成型的通用塑料主要是PS、PE、PP、ABS四种。
其中ABS塑料属于高强度塑料,在注塑成型前需要预先干燥[3][4]。
1.2.3热流道注塑模具技术
热流道注塑成型于20世纪50年代问世,经历了一段较长时间的推广以后,其市场占有率逐年上升,80年代中期,美国的热流道模具占注塑模具总数的15%~17%,欧洲为12%~15%,日本约为10%。
但到了90年代,美国生产的塑料注塑模具中热流道模具占40%以上,在大型制品的注射模具中则占90%以上[5]。
热流道注塑模具是无流道凝料注塑模具中最常见的一种,通常分为绝热流道注塑模具和加热流道注塑模具两种,也可以分为单型腔热流道模具、多型腔热分流道模具(外加热)、阀式浇口热流道模、内加热的热分流道模具等四种。
传统注塑成型中,滞留在浇注系统内的熔体冷却固化后作为废料,增加原材料消耗,降低了材料的利用率,增大注射机的能耗。
热流道注塑成型作为传统注塑成型一个重要发展方向,其最大特点在于浇注系统内的塑料不会凝固,也不会随制件脱模,整个注塑过程可实现自动化,从而大大提高了材料利用率;使长流程流道成为可能,保证多型腔注塑生产的一致性,提高了制件的精度;浇注系统更人性化,通过温度控制可实现充模过程的平衡。
尽管在很多方面,热流道模具与冷流道模具相比有显著的优点,但热流道模具也存在一些缺点与不足。
概括起来有以下几点。
1.模具的总体成本上升。
由于热流道模具的元件价格比较贵,所以热流道模具成本可能会大幅度增高。
如果制件为小批量生产,成本价格贵是影响热流道模具广泛使用的主要问题之一。
2.热流道模具制作工艺要求高。
由于热流道模具需要精密的加工机械作保证,所以热流道系统与模具的配合要求极为严格,否则在生产过程中会出现很多严重问题,如喷嘴与浇口相对位置不好导致制品质量严重下降等。
3.温度控制系统的精确要求很高。
4.热辐射难以控制,热流道系统最大的毛病就是流道的热量损耗,是一个需要解决的重大课题。
5.与冷流道模具相比,热流道模具的生产操作与维修比较复杂,对这方面的技术人员要求较高[6]。
由于快速自动化注塑成型工艺的发展,热流道注塑模具正在我国逐渐推广使用。
在20世纪70年代,我国已经有热流道技术的应用,从20实际90年代开始,已相继创建了不少热流道装备的经营企业。
虽然目前我国的热流道模具技术有了很大的进步,但是在模具设计和模具加工工艺、制造精度、表面粗糙度、加工模具的复杂程度以及模具的制造周期和使用寿命方面等与国外相比差距十分明显。
此外,模具工业的整体设备水平也存在相对落后和利用率低、高素质的模具技术人才缺乏等现象。
针对当前国内热流道模具存在的情况,我国的热流道模具工业主要发展趋势要包括以下几个方面:
热流道元件的小型化、标准化、系列化;提高热流道模具材料的耐磨性和耐热性;开发更精密的温控装置,以便快速安全的启动和操作;提高封合技术,防止模具泄露等等[7]。
1.3我国塑料模具技术现状与发展方向
从20世纪80年代以来,我国模具工业发展迅速,平均每年的增长速度均为13%,在1999年我国模具工业产值为245亿,到2000年我国模具总产值为260~270亿元,其中塑料模具占30%左右。
在未来的模具市场中,塑料模具在模具总量中的比例还将逐步提高。
我国塑料模具工业从起步发展到现在,历经半个多世纪,从总体来说,各个方面都有了很大发展,模具水平有了较大提高。
根据各种显示数据的表明,我国模具市场的总体趋势是稳定提升的,在未来的模具市场中,塑料模具的发展速度将继续高于其它模具,在模具行业中的比例将逐步提高。
在未来的发展中,精密、大型、复杂、长寿命塑料模具将成为主流,这类模具的发展将高于总量发展的速度,其中国产化的占有率也会提高;在塑料模具设计制造中全面推广应用CAD/CAE/CAM技术,先进的CAD/CAE/CAM技术对提高模具生产效率和质量起到了直接的作用;推广和应用热流道技术、气辅注塑成型技术和高压注塑成型技术,随着生产的快速自动化要求,这类先进的成型技术将得到越来越多的关注和应用;开发新的塑料成型工艺和快速经济模具,随着塑料工业的发展和进步,要求模具的生产周期大大缩短和经济实用;提高塑料模具标准化水平和标准件的使用率,由于现代工业的分工越来越细,模具行业也要提高模具的标准化,方便模具各零件的生产加工和使用,缩短模具的生产周期;应用优质模具材料和先进的表面处理技术;研究和应用模具的高速测量技术与逆向工程等[8]。
1.4并行工程的产生及发展
1.4.1并行工程产生的背景
并行工程是近年来新出现的一种产品开发模式,它受到了国内外众多研究单位与制造企业的重视。
并行工程是一种指导新产品开发的朴素的哲理,同时也是一门综合的自动化制造技术。
1.4.2并行工程的四个关键要素
并行工程的核心内容包括四方面:
第一,产品开发队伍重够;第二,过程重够;第三,数字化产品定义;第四,协同工作环境。
针对并行工程的核心内容,并行工程包括组织结构变革、新的用户需求策略、必要的支撑环境、产品开发过程改进这四个关键要素。
1.4.3并行工程关键技术概述
传统的CIMS中的基础技术,如信息集成、STEP、CAD/CAPP/CAM、数据库等,在并行工程中仍然扮演重要角色。
然而在CIMS信息技术的基础上实施并行工程还需要组织管理,过程改进、并行化设计方法学等新信息的关键技术支持。
1.4.4并行工程的组织结构
并行工程要求打破部门间的界限,组成跨部门多专业的集成产品开发团队(IPT)
1.4.5并行工程协调管理
并行工程的大规模协同工作的特点,使得冲突成为并行工程实施过程中的一个重要的现象。
为使产品开发过程顺利进行,使并行工程的效益得以充分体现,必须具有一种协调管理的支持技术、工具及系统,来建立各功能小组及产品元件之间的依赖关系,协调各跨功能小组之间的活动,支持各小组及产品信息的透明访问,以保证把正确的信息和资源,在正确的时刻,以正确的方式,送给正确的小组(小组成员)。
并行工程协调管理应提供有效的冲突仲裁支持信息,妥善而全面地处理并行工程环境下出现的各种冲突,来解决新的开发模式下出现的各种新的问题,使产品开发过程顺利进行,真正实现并行工程的效益。
协调管理问题是并行工程中的一个关键技术问题,它直接影响到并行工程能否顺利地实施以及并行工程的效益能否真正体现的问题。
1.5毕业设计的任务
参考市面上的汽车保险杆,设计保险杆,包括塑件设计、工艺性分析、确定收缩率和分型面、浇道系统的设计、冷却系统的设计与计算、模具结构件设计、干涉分析(动态碰撞检查)、零部件加工工艺方案制订、注塑设备选择、绘制模具设计图纸等。
为满足大批量自动化生产的需要,该制件的设计选用热流道型注塑模具。
完成以上内容后要求打印模具的装配图纸和模具成型部分的零件图纸,并完成符合相关规定、规X的毕业论文和提供完整的模具设计电子图档。
1.6制品资料
1.6.1制品的实物图
这次设计的制件是汽车保险杆,制件的参考实物图如图1所示。
1.6.2制品的市场调查
市场上,不同公司生产的或同一公司生产的不同型号的充电座,制件会存在差异。
经过市场上调查,找到一些充电座的样品,如图2所示,在样品中可以看到有些充电座部件与这次设计的制件的实物图存在差异,主要是由于设计者设计的充电座的外观与功能的不同。
如图1制品的参考实物图
图2市场上的部分汽车保险杠
1.6.3制品三维模型
根据制品的实物几何特征和尺寸,利用Pro/E软件三维模型中心模块进行制件的三维造型,得到的制品3D效果如图3所示,由于经过自己的设计,所以用Pro/E构建出来的效果图与制品的实物图会存在差异。
图3制品的3D视图
1.6.4制品零件图
并利用Pro\E软件的三维模型中心模块,将构建的制品3D模型图转换为2D视图,如图4所示。
图4制品的零件示意图
1.7基于并行工程产品开发过程改进与重组提供指南
1.7.1产品开发过程工程
产品开发过程工程的概念来源于一般意义的“过程工程”的概念,所谓过程工程就是指有关过程的定义、优化和控制的工程活动的总称。
过程工程的研究为人们研究、管理和实施过程乃至过程重组提供们研究、管理和实施过程乃至过程重组提供
1.7.1.1过程重组需求分析
产品开发过程重组是通过从根本上对产品开发过程的重新考虑和彻底性的设计,达到产品开发在成本、质量、服务和速度上的巨大的改进,重组意味着对过程的较为彻底的改造。
产品开发过程重组是组织层次的周密的过程改革。
过程工程的每一次大的循环,即组织启动过程重组,是由经营环境变化和新技术驱动,或者是由内部过程度量与评估结果驱动的,从而形成过程重组的需求。
当市场竞争发生变化,如时间成为当前产品开发竞争的焦点,或者当前的产品技术发生较大的突破时,企业必须做出相应的对策,进行产品开发过程重组,以提高其竞争能力。
同样,基于某个或多个项目内部改革的成功经验,或者是在大量的项目实施中发现很多问题,也可能启动过程重组。
1.7.1.2过程体系结构设计
过程的体系结构设计是指从不同角度对过程进行较高抽象层次的设计,包括产品开发过程分解方法、功能模型‘组织模型。
行为模型和信息模型等,对过程的一般体系结构进行设计和扩充,并负责组织各过程构件,定义其接口关系。
过程的体系结构是随着过程工程的进行而不断完善,不断扩大和不断丰富的。
1.7.2产品开发过程建模
1.7.2.1产品开发过程建模目标与需求
产品开发过程建模工作应当满足如下需求,这些需求体现了产品开发过程研究和应该的基本目标。
(1)加强团队成员对过程的理解和团队协作。
(2)支持过程的分析和改进
(3)支持开发过程的实施、监控和管理
(4)支持过程集成开发环境
1.7.2.2过程的层次与过程建模的关系
从过程实施的角度看,产品开发过程具有层次性。
通常将产品开发过程分为四层次:
组织标准化产品开发过程、项目既定过程、项目与团队开发设计划和具体任务层。
1.7.3产品开发过程的规划和管理
1.7.3.1PERT技术和CPM方法
PERT技术和CPM方法都采用活动网络图来描述一个项目,也就是从一个项目的开始到结束,把应当完成的任务用图或表的形式表示出来。
通常用两X来定义网络图。
一X表给出与一特定项目有关的所有任务(称为任务分解结构),另一X表则给出应当按照什么样的次序来完成这些任务(称为限制表)。
1.8并行工程的组织模式----集成产品开发团队
并行工程强调及早考虑下游活动对产品设计的影响,强调各个活动并行交叉进行,强调面向过程和以产品为中心,强调系统集成与整体优化。
这些都离不开高校的组织形式和快捷的信息沟通和交流。
传统的部门制在组织结构变大时,生产效率降低,通信障碍增加,各部分的信息分享成为瓶颈,致使开发周期延长,产品质量下降。
1.9并行工程协同工作环境
1.9.1并行工程协同工作环境
并行工程协同工作环境分为五层,分别为:
活动层、事物层、合作服务层、企业信息模型层和网络层。
1.9.1.1并行工程协同工作环境中的关键技术
一般认为协同工作的七个要素为7C,即协作、信任、交流、折衷、一致、不断提高、协调。
为体现7个基本要素,实现协同工作,必须解决好以下关键技术。
1.通信2.信息建模3.工作流管理4.约束管理5.协商6.历史信息的获取与管理
1.9.2并行工程产品开发过程的协调管理
1.9.2.1并行工程产品开发过程的协调
为得出并行工程产品开发过程协调问题的相关结论,必须将协调对象具体化并行工程开发过程。
并行工程产品开发过程协调的定义:
在集成产品开发团队组织结构下,通过采用有效的问题表示机制和及时地采集过程有关信息,来避免冲突、发现开发过程中已出现的冲突及发现在开发过程下游才可能暴露出的冲突,并通过调整开发小组间及开发小组内的各种相互依赖关系,来化解冲突,从而保证并行工程总目标的实现。
1.9.2.2并行工程产品开发过程的协调模型
本节提出一种并行工程协调模型,以提供一个全面的参考筐架,来系统地深入地解决并行工程产品开发过程的协调问题。
(1)对协调模型的要求
(2)协调模型
(3)关联模型
(4)过程模型和产品模型
(5)知识模型
(6)数据采集
(7)冲突化解
2.热流道注塑模具设计
2.1概述
注塑模具的设计是塑料模具工业中的一个重要的环节,模具的质量直接影响生产制品的优劣。
注塑模具分为动模和定模两大部分,定模部分安装在注塑机的固定座板上,动模部分安装在注塑机的移动座板上。
注塑生产时,定模与动模两大部分闭合,塑料通过喷嘴进入模具的型腔内,开模时,定模与动模两大部分分离,顶出机构讲制件顶出,完成一次制件注塑过程。
注塑模具的设计按其结构特征来分主要包含成型部分的设计、模架的选用、浇注系统的设计、侧向抽芯结构的设计、顶出机构的设计、冷却和加热系统的设计等等。
2.2模具设计环境与工具
2.2.1Pro/E3.0
Pro/ENGINEER是由美国参数技术公司推出的一套博大精深的三维CAD/CAM参数化软件系统,它的内容涵盖了产品从概念设计、工业造型设计、三维模型设计、分析计算、动态模拟与仿真、工程图的输出、生产加工成产品的全过程,其中还包括了大量的电缆和管道布线、模具设计与分析等使用模块。
在整个毕业设计过程中,主要使用Pro/E3.0工业设计模块中的实体造型特征功能完成产品的3D造型。
2.2.2UG5.0
UG是一个全三维、双精度的造型系统,使用户能够比较精确地描述任何几何形体,通过对这些形体的组合,就可以对产品进行设计、分析和制图。
UG可以为机械设计、模具设计以及电器设计提供一套完整的设计、分析、制造方案;UG提供了包括特征造型、曲面造型、实体造型在内的多种造型方法。
而本毕业设计我是运用UG5.0进行模具设计,根据UG5.0开模的优势,进行整副模具的3D设计!
2.2.3AutoCAD2004
AutoCAD是Autodesk公司推出的计算机辅助设计软件,由于其强大的功能,所以该软件广泛应用于建筑、机械、电子等设计领域。
本次毕业设计,运用该软件进行塑胶制件、模具装配及其零件工程图的绘制和修改工作。
AutoCAD2004采用了XP风格的操作界面,所有工具栏的图标都是真彩色的。
相对与Autodesk公司以前推出的AutoCAD版本,AutoCAD2004可以支持无限次地撤消和恢复操作。
在图像管理方面功能也有所加强,如可以实现保存调出图层状态、图层状态的存盘、图层的拷贝和图层的转换等功能。
此外,AutoCAD2004和燕绣还提供了一个非常实用的外挂功能。
2.3注塑模具设计流程
2.3.1注塑模具的传统设计流程
传统的注塑模设计流程如图5所示[10]。
图5传统注塑模具设计流程图
在进行设计之前,设计者应该明确自己要设计的事项,要以设计任务书为依据设计模具。
根据设计书的内容,设计者应熟悉塑件的几何形状、明确使用要求。
然后对塑件进行成型工艺性的检查,以确认塑件各个细节是否符合注塑成型的工艺条件,这可以利用一些塑料CAE分析软件辅