贮油盖塑模.docx
《贮油盖塑模.docx》由会员分享,可在线阅读,更多相关《贮油盖塑模.docx(20页珍藏版)》请在冰豆网上搜索。
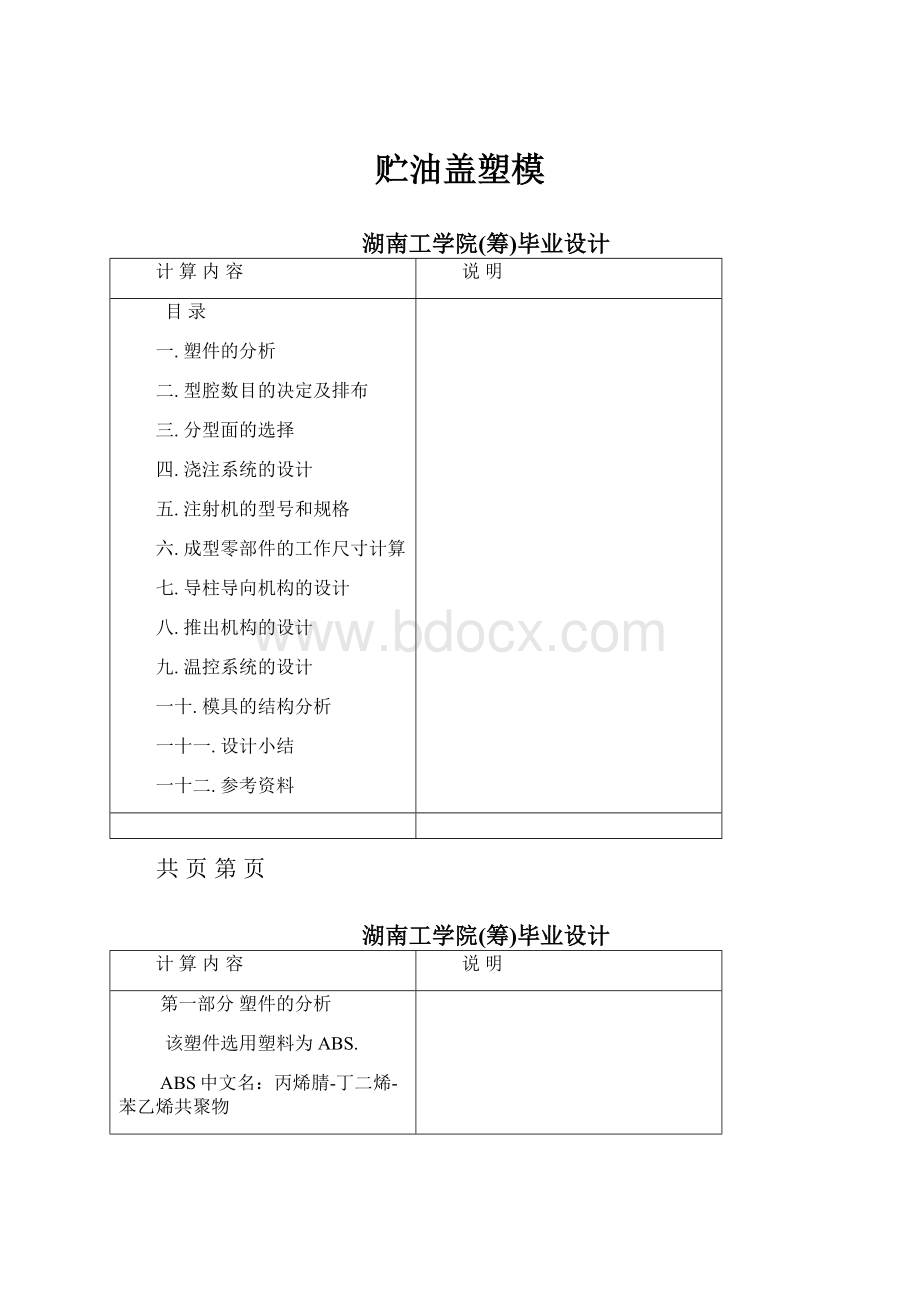
贮油盖塑模
湖南工学院(筹)毕业设计
计算内容
说明
目录
一.塑件的分析
二.型腔数目的决定及排布
三.分型面的选择
四.浇注系统的设计
五.注射机的型号和规格
六.成型零部件的工作尺寸计算
七.导柱导向机构的设计
八.推出机构的设计
九.温控系统的设计
一十.模具的结构分析
一十一.设计小结
一十二.参考资料
共页第页
湖南工学院(筹)毕业设计
计算内容
说明
第一部分塑件的分析
该塑件选用塑料为ABS.
ABS中文名:
丙烯腈-丁二烯-苯乙烯共聚物
英文名:
Acrylinitrile-Butadiene-Styrene。
基本特性:
无毒无味,呈微黄色,成型的塑件有较好的光泽,密度在1.02~1.05g/cm3,其收缩率为0.3~0.8%。
ABS吸湿性很强,成型前需要充分干燥,要求含水量小于0.3%。
流动性一般,溢料间隙约在0.04mm。
ABS有极好的抗冲击强度,且在低温下也不迅速下降。
有良好的机械强度和一定的耐磨性、耐寒性、耐油性、耐水性、化学稳定性和电气性能。
成型特点:
ABS在升温时粘度增高,所以成型压力较高,塑料上的脱模斜度宜稍大;易产生熔接痕,模具设计时应注意尽量减小浇注系统对料流的阴力;在正常的成型条件下,壁厚、熔料温度及收缩率影响极小。
要求塑件精度高时,模具温度可控制在50~60oC,要求塑件光泽和耐热时,应控制在60~80oC。
主要技术指标:
共页第页
湖南工学院(筹)毕业设计
计算内容
说明
比重:
1.02~1.16g/cm3。
比容:
0.86~0.98cm3/g
吸水性:
0.2~0.4%(24h)。
熔点:
130~160oC。
热变形温度:
4.6×105Pa----130~160oC。
18.5×105Pa----90~108oC。
抗拉屈服强度(105Pa):
500
拉伸强度模量:
1.8×104Mpa
弯曲强度:
800×105Pa
ABS的注射工艺参数:
注射机类型:
螺杆式
螺杆转速:
30~60r/min
喷嘴形式:
直通式
喷嘴温度:
190~200oC
料筒温度:
前200~210oC
中210~230oC
后180~200oC
模温:
50~80oC
注射压力:
70~120Mpa
保压力:
50~70Mpa
共页第页
湖南工学院(筹)毕业设计
计算内容
说明
注射时间(s):
3~5
保压时间(s):
15~30
冷却时间(s):
15~30
成型周期(s):
40~70
塑件图如下页所示:
塑件的工作条件对精度要求较低,根据ABS的性能可选择其塑件的精度等级为5级精度(查阅《塑料成型工艺与模具设计》P66表3-9)。
经计算得塑件的面积为:
S塑1=138.16mm2
S塑2=489.84mm2
得塑件的体积为:
V塑=2.223cm3
塑件的质量为:
W塑=V塑×r塑=2.312(g)。
湖南工学院(筹)毕业设计
计算内容
说明
第二部分型腔数目的决定及排布
已知的体积V塑或质量W塑,又因为此产品属大批量生产的小型塑件,综合考虑生产率和生产成本等各种因素,以及注射机的型号选择,初步确定采用一模四腔对称性排布。
由塑件的外形尺寸和机械加工的因素,确定采用侧浇口。
排布图如下图示:
型腔数目及排布图
第三部分分型面的选择
塑件冷却时会因为收缩作用而包覆在凸模上,故从塑件脱模的角度考虑,应有利于塑件滞留在动模一侧,以便于脱模。
而且不影响塑件的质量和外观形状,以及尺寸精度。
其图如下所示:
湖南工学院(筹)毕业设计
计算内容
说明
第四部分浇注系统的初步估计
浇注系统一般由主流道、分流道、浇口和冷料穴等四部分组成。
浇注系统的设计应保证塑件熔体的流动平稳、流程应尽量短、防止型芯变形、整修应方便、防止制品变形和翘曲、应与塑件材料品种相适用、冷料穴设计
合理、尽量减少塑料的消耗。
塑件的截面厚度较小,且为圆筒形,因此采用托盘推杆推出,需开设冷料穴,拉料杆采用Z形式。
分流道采用半圆形截面,并且开设
共页第页
湖南工学院(筹)毕业设计
计算内容
说明
在凹模上,以便于脱模,加工也较容易,在定模固定板上采用浇口套。
根据塑件的外形尺寸和质量等决定影响因素,初步取值如下:
d=4mmD=6.7mmR=20mmt=3mm
r=3mml=45mmL=40~50mm
初步估算浇注系统的体积,V浇=5~6cm3。
其质量约为:
W浇=V浇×r塑=6~7g。
S=(n×W塑+W浇)/0.8=28~30g。
所以,选择用注射机型号为:
XS-Z-30。
第五部分注射机的型号和规格
注射机的技术规格:
型号:
XS-Z-30
额定注射量(cm3):
30g
螺杆直径(mm):
28
注射压力(MPa):
119
注射行程(mm):
130
注射时间(s):
0.7
注射方式:
柱塞式
共页第页
湖南工学院(筹)毕业设计
计算内容
说明
合模力kN:
250
合模方式:
液压-机械
最大注射面积(cm2):
90
最大开(合)模行程(mm):
160
模具最大厚度(mm):
180
模具最小厚度(mm):
60
模板最大距离(mm):
340
最大开模行程(mm):
160
喷嘴圆弧(mm):
12
喷嘴孔径(mm):
2
第六部分成型零部件的工作尺寸计算
1、产生偏差的原因:
①.塑料的成型收缩 成型收缩引起制品产生尺寸偏差的原因
有:
预定收缩率(设计算成型零部件工作尺寸所用的收缩率)与制品实际收缩率之间的误差;成型过程中,收缩率可能在其最大值和最小值之间发生的波动。
共页第页
湖南工学院(筹)毕业设计
计算内容
说明
σs=(Smax-Smin)×制品尺寸
σs 成型收缩率波动引起的制品的尺寸偏差。
Smax、Smin分别是制品的最大收缩率和最小收缩率。
②.成型零部件的制造偏差 工作尺寸的制造偏差包括加工偏差和装配偏差。
③.成型零部件的磨损
2、本产品为抗冲ABS制品,属于大批量生产的小型塑件,预定的收缩率的最大值和最小值分别取0.8%和0.3%。
此产品采用5级精度,属于低精度制品。
因此,凸凹模径向尺寸、高度尺寸及深度尺寸的制造与作用修正系数x取值可在0.5~0.75的范围之间,凸凹模各处工作尺寸的制造公差,因一般机械加工的型腔和型芯的制造公差可达到IT7~IT8级,综合参考,相关计算具体如下:
凹模的计算:
Lm1=[(1+(Smax+Smin)/2>Lsl-Δ/2)Δ/3
=((1+0.55%)×32-1/2×0.28)Δ/3
=32.0360.09mm
共页第页
湖南工学院(筹)毕业设计
计算内容
说明
凹模深度尺寸计算:
Hm1=〔(1+(Smin+Smax)/2)x3-2/3×0.22〕Δ/3
=〔(1+0.55%)×3-2/3×0.22〕0.07
=2.870.07
凸凹模工作尺寸计算图例
凸模径向尺寸计算:
lm1=〔(1+(Smax+Smin)/2>×20+1/2×△)-△/3
=〔(1+0.55%)×20+1/2×0.22〕-0.07
=20.22-0.07
凸模高度:
hm=〔(1+(Smax+Smin)/2>×hs+2/3×△)-△/3
=〔(1+0.55%)×50+2/3×0.22〕-0.07
=50.42-0.07
共页第页
湖南工学院(筹)毕业设计
计算内容
说明
3、成型零件的强度、刚度计算
注射模在其工作过程需要承受多种外力,如注射压力、保压力、合模力和脱模力等。
如果外力过大,注射模及其成型零部件将会产生塑性变形或断裂破坏,或产生较大的弹性弯曲变形,引起成型零部件在它们的对接面或贴合面处出现较大的间隙,由此而发生溢料及飞边现象,从而导致整个模具失效或无法达到技术质量要求。
因此,在模具设计时,成型零部件的强度和刚度计算和较核是必不可少的。
一般来说,凹模型腔的侧壁厚度和底部的厚度可以利用强度计算决定,但凸模和型芯通常都是由制品内形或制品上的孔型决定,设计时只能对它们进行强度校核。
因在设计时采用的是整体式圆形型腔。
因此,计算参考公式如下:
侧壁:
按强度计算:
按刚度计算:
共页第页
湖南工学院(筹)毕业设计
计算内容
说明
底部:
按强度计算:
按刚度计算:
凸模、型芯计算公式:
按强度计算:
按刚度计算:
由公式分别计算出相应的值为:
按强度计算得:
tc=4.93mmth=4.38mmr=8.52mm
按刚度计算得:
tc=0.93mmth=1.91mmr=3.97mm
参数符号的意义和单位:
Pm模腔压力(MPa)
E材料的弹性模量(MPa)查得2.06×105;
材料的许用应力(MPa)查得176.5;
共页第页
湖南工学院(筹)毕业设计
计算内容
说明
u材料的泊松比查表得0.025;
成型零部件的许用变形量(mm)查得0.05;
采用材料为45,调质及表面淬火,≥55HRC。
第七部分导柱导向机构的设计
导柱导向机构是保证动定模或上下模合模时,正确定位和导向的零件。
一、导柱导向机构的作用:
1、定位件用:
模具闭合后,保证动定模或上下模位置正确,保证型腔的形状和尺寸精确,在模具的装配过程中也起定位作用,便于装配和调整。
2、导向作用:
合模时,首先是导向零件接触,引导动定模或上下模准确闭合,避免型芯先进入型腔造成成型零件损坏。
3、承受一定的侧向压力。
二、导柱导套的选择:
导柱导套结约形式及尺寸如下图:
共页第页
湖南工学院(筹)毕业设计
计算内容
说明
其材料采用20钢经渗碳淬火处理,硬度为50~55HRC。
导柱、导套固定部分表面粗糙度Ra为08μm,导向部分表面粗糙度Ra为0.8~0.4μm。
具体尺寸如上图所示。
导柱、导套用H7/r6配合镶入模板。
布局形式如右图示:
为便于导套与导柱配合后工作
时的的排气,在定模固定板的开设通气孔。
第八部分推出机构的设计
1.推出机构的组成
推出机构由推出零件、推出零件固定板和推板、推出机构的导
共页第页
湖南工学院(筹)毕业设计
计算内容
说明
向与复位部件组成。
即推件板、推件板紧固螺钉、推板固定板、推杆垫板、顶板导柱、顶板导套以及推板紧固螺钉。
2.设计原则:
a、推出机构应尽量设在动模一侧;
b、保证塑件不因推出而变形损坏;
c、机构简单动作可靠;
d、合模时的正确复位。
3、脱模力的计算:
根据力平衡原理,列出平衡方程式:
∑Fx=0
Ft+Fbsinα=Fcosα
Fb塑件对型芯的包紧力;
F脱模时型芯所受的摩擦力;
Ft脱模力;
Α型芯的脱模斜度。
又:
F=Fbμ
于是Ft=Fb(μcosα-sinα)
而包紧力为包容型芯的面积与单位面积上包紧力之积,即:
Fb=Ap
由此可得:
Ft=Ap(μcosα-sinα)
共页第页
湖南工学院(筹)毕业设计
计算内容
说明
式中:
μ为塑料对钢的摩擦系数,约为0.1~0.3;
A为塑件包容型芯的总面积;
p为塑件对型芯的单位面积上的包紧力,在一般情况下,模外冷却的塑件p取2.4~3.9×107Pa;模内冷却的塑件p约取0.8~1.2×107Pa。
所以:
经计算,A=475.04mm2,μ取0.25,p取1×107Pa,取α=45,。
Ft=475.04×10-6×1×107(0.25×cos45`-sin45`)
=1125.32N.
因此,脱模力的大小随塑件包容型芯的面积增加而增大,随脱模斜度的增加而减小。
由于影响脱模力大小的因素很多,如推出机构本身运动时的摩擦阻力、塑料与钢材间的粘附力、大气压力及成型工艺条件的波动等等,因此要考虑到所有因素的影响较困难,而且也只能是个近似值。
4.用推件板推出机构中,为了减少推件板与型芯的摩擦,在推件板与型芯间留0.20~0.25mm的间隙,并用锥面配合,民防止推件因偏心而溢料。
5.复位零件:
由于推杆端面与推件板接触,可以起到复位杆的作用。
因此,可以不必再另外设置复位杆。
另外,设计顶板导柱可以对顶板起导向
共页第页
湖南工学院(筹)毕业设计
计算内容
说明
作用,防止顶板因受力不均而偏斜,影响正常的顶出和复位。
第九部分温控系统设计
1.注射模冷却系统设计:
基本原则:
熔体热量95%由冷却介质(水)带走,冷却时间占成型周期的2/3。
A、冷却系统从模具中带走热量:
Q=KAΔTt/3600(J)
A冷却介质传热面积(m2):
A=πdL。
d冷却管道直径(m):
d=0.01;
L冷却管长度(m)L=0.16;
K冷却管壁与介质间的传热膜系数〔J/(m2hC)
K=4187f(ρv)0.8/d0.2.
2.与冷却介质温度有关的物理系数;
v冷却介质在管中流速(m/s);
ρ冷却介质在该温度下的密度〔kg/m3〕,水在30℃时取为0.996×103kg/m3。
d.冷却管直径;
△T模温与冷却介质的平均温差(℃);
t冷却时间;
共页第页
湖南工学院(筹)毕业设计
计算内容
说明
第十部分模具结构分析
1.塑料的加热,塑化是在高温料筒内进行,不是在模具内进行,因而模具不设加料腔,而设浇注系统,熔体通过浇注系统充满型腔.
2.塑料熔体进入型腔之前,模具已经闭合.在注塑过程中需根据塑料特性,在模具中设冷却系统.
3.该模具采用单分型面注射模,型腔一部分设在定模,一部分设在动模,其主流道设在定模一侧,分流道设在分型面上,开模后塑料制品连同流道凝料一起留在动模上,动模一侧设有推出机构,用以推出制品及流道凝料.
4.注射模具生产适应性强,生产率高,容易实现自动化.
5.注射模一般是机动的,结构一般较复杂,因而制造周期较长,成本较高.
共页第页
湖南工学院(筹)毕业设计
计算内容
说明
第十一部分设计小结
通过在注射模设计过程中,我有以下几点体会:
1.了解聚合物的物理性能,流动特性,成型过程中的物理,化学变化以及塑料的组成,分类及其性能.
2.了解塑料成型的基本原理和工艺特点,能够正确分析成型工艺对模具的要求;
3.掌握成型设备对各类模具的要求;
4.掌握各类成型模具的结构特点及设计计算方法.
5.具有分析问题的能力,包括分析成型缺陷产生的原因和提出克服办法的能力.
6.攻固了我以前所学的专业知识,
共页第页
湖南工学院(筹)毕业设计
计算内容
说明
第十二部分参考文献
参考资料:
1.屈华昌主编.塑料成型工艺与模具设计.北京:
机械工业出版社,1995
2.黄毅宏、李明辉主编模具制造工艺.北京:
机械工业出版社,1999.6
3.何忠保,陈晓华,王秀英主编.典型零件模具图册.北京:
机械工业出版社,2000.9
4.李绍林,马长福主编.实用模具技术手册.上海:
上海科学技术文献出版社,2000.6
5.王树勋主编.注塑模具设计与制造实用技术.广州:
华南理工大学出版社,1996.1
6.李绍林主编.塑料·橡胶成型模具设计手册.北京:
机械工业出版社,2000.9
共页