FMEA作业程序.docx
《FMEA作业程序.docx》由会员分享,可在线阅读,更多相关《FMEA作业程序.docx(18页珍藏版)》请在冰豆网上搜索。
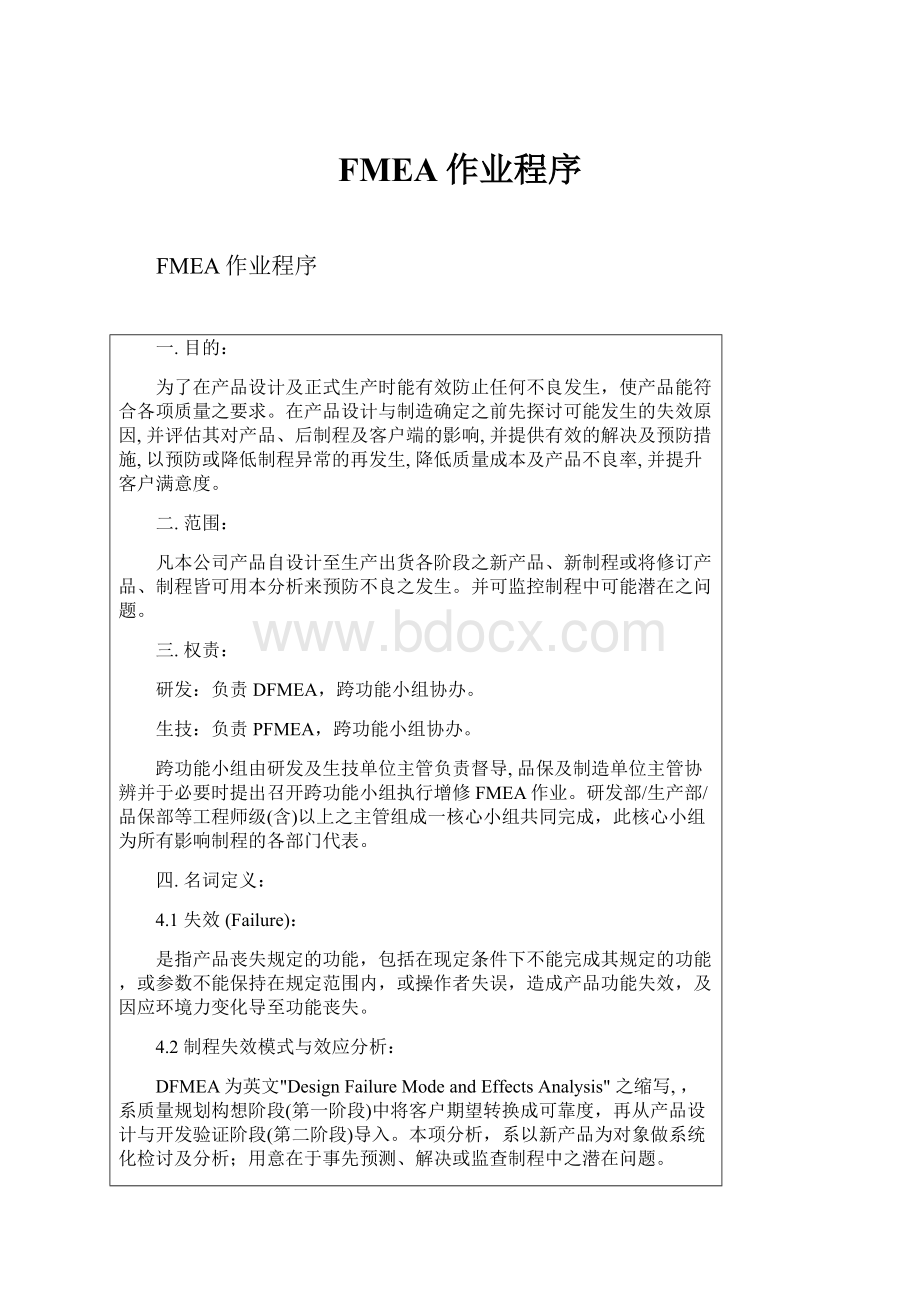
FMEA作业程序
FMEA作业程序
一.目的:
为了在产品设计及正式生产时能有效防止任何不良发生,使产品能符合各项质量之要求。
在产品设计与制造确定之前先探讨可能发生的失效原因,并评估其对产品、后制程及客户端的影响,并提供有效的解决及预防措施,以预防或降低制程异常的再发生,降低质量成本及产品不良率,并提升客户满意度。
二.范围:
凡本公司产品自设计至生产出货各阶段之新产品、新制程或将修订产品、制程皆可用本分析来预防不良之发生。
并可监控制程中可能潜在之问题。
三.权责:
研发:
负责DFMEA,跨功能小组协办。
生技:
负责PFMEA,跨功能小组协办。
跨功能小组由研发及生技单位主管负责督导,品保及制造单位主管协辨并于必要时提出召开跨功能小组执行增修FMEA作业。
研发部/生产部/品保部等工程师级(含)以上之主管组成一核心小组共同完成,此核心小组为所有影响制程的各部门代表。
四.名词定义:
4.1失效(Failure):
是指产品丧失规定的功能,包括在现定条件下不能完成其规定的功能,或参数不能保持在规定范围内,或操作者失误,造成产品功能失效,及因应环境力变化导至功能丧失。
4.2制程失效模式与效应分析:
DFMEA为英文"DesignFailureModeandEffectsAnalysis"之缩写,,系质量规划构想阶段(第一阶段)中将客户期望转换成可靠度,再从产品设计与开发验证阶段(第二阶段)导入。
本项分析,系以新产品为对象做系统化检讨及分析;用意在于事先预测、解决或监查制程中之潜在问题。
PFMEA为英文"ProcessFailureModeandEffectsAnalysis"之缩写,其功能为事前鉴别出制程中可能发生之失效模式,并且加以文件化及数量化之评估,主要采用归纳法。
4.3客户(Customer):
后制程、销售对象、或使用者均属之。
4.4制程功能/要求:
所分析制程功能。
4.5潜在失效模式:
制程不能满足设计或规格需求时之现象。
4.6失效的潜在效果:
失效模式对客户之影响。
4.7严重性(Severity):
失效模式发生时,对客户之影响的严重性之评估指标。
4.8失效的潜在原因与结构:
失效如何发生之原因。
4.9发生性(Occurrence):
为失效原因发生频率之评估指针。
4.10现行制程管制:
为目前已经使用之措施,以预防失效发生或当失效发生时能被检出。
文件编号
页版本
1
文件名称
失效模式与效应分析作业程序
页 次
2/10
4.11侦测性(Detection):
为在半成品流向后制程前,检出失效原因或失效模式之能力评估指针。
4.12风险优先数(RPN):
原文为〞RiskPriorityNumber":
由严重性、发生性、侦测性三指数相乘所得,为是否实施对策改善之总评估指标。
五.FMEA内容:
5.1作业流程:
流 程 权责单位 相关说明 表 单
────── ─────── ──────────── ─────────
┌────┐ DFMEA:
研发 失效模式与效应分析作业程序 异常处理单QA-AQA26
│资料准备│ PFMEA:
生技 QP-AFA15
└────┘ 制程管制程序QP-AFA04 质量改善会议记录
│ (制造.品保等其
↓ 他有关单位协办)
↓
┌────┐ 跨功能小组 1.列出该产品应有之功
│召开会议│ 能及不应有之功能 会议记录
└────┘ 2.列出制程特性
│ 3.对每一作业可能出
↓ 错之处加以明定
/\
/ \
/是否 \
\增修 / 跨功能专业小组
\ / (参考“内容”5.5)
\/
│
↓
┌─────┐
│执行FMEA│ FMEA
└─────┘
│
↓
┌────┐
│是否采取│ 跨功能专业小组 FMEARPN评估
│对 策│
└────┘
│
↓©
文件编号
页版本
1
文件名称
失效模式与效应分析作业程序
页 次
3/10
│©
↓
┌────┐
│对策拟定│ 权责单位 制程管制程序QP-AFA04 FMEA推荐措施
│执 行│
└────┘
│
↓
┌────┐ DFMEA:
研发
│效果确认│ 失效模式与效应分析作业程序 FMEA改正后结果
└────┘ PFMEA:
品保 QP-AFA15
│ 统计.分析及改善程序
│ QP-AQA11
↓
┌────┐
│标准化│ 制造单位 文件与数据管制 文件修订.废止申请表
└────┘ 程序QP-ARD01 QF-ARD03
文件修订纪录书
QF-ARD01
5.2使用时机:
当生产线导入新产品或新设备、新材料、制程变更、规格变更、制程不稳定、制程能力不足,均需进行或重新研拟制程FMEA作业。
5.3跨功能专业小组之编成:
须以技术支持能力及产品特性为考虑,人数不限,但至少包括品保、工程、制程各一员,其余材料、服务和供货商等部门视需要加入。
5.4FMEA分析表作成:
5.4.1DFMEA序号:
填入DF-□□□可用于追查。
PFMEA序号:
填入PF-□□□可用于追查。
5.4.2项目:
填入系统、子系统或零组件的名称和号码(型号)。
5.4.3制程责任;填入生产部门和组织,OEM部门和组织,也包括供货商姓名。
5.4.4编制人:
填入负责准备FMEA之工程师的姓名。
5.4.5车型/年份:
填入分析零件所装附于客户的型号及年份(将利用和正被分析的设计或制程所影响)。
5.4.6工程放行日期/主要生产日期:
填入最初工程放行日期与不超过预定的生产开始日期。
5.4.7FMEA日期:
填入原版FMEA制订的日期及最近的修改日期。
文件编号
页版本
1
文件名称
失效模式与效应分析作业程序
页 次
4/10
5.4.8核心(跨功能)小组:
列出负责的个人和有权去确认和从事这项任务的部门的名单。
5.4.9DFMEA零件功能与要求:
填入对正被分析零件的简单描述。
5.4.10PFMEA制程功能/要求:
描述工程目的,使用之设备。
填入对正被分析制程的简单描述
(如:
冲压、塑行、组装)尽可能简单地指出正被分析的制程的目的,在制程中有
许多带有不同潜在失效模式的流程,按单独流程列出工序也许是可取的。
5.4.11 潜在失效模式:
DFMEA潜在的失效模式被定义为一种方式,以这种方式,零件可能潜在地无法满足设
计意图。
破裂的
黏着
变形的
短路的
松开的
生锈的
渗透的
断裂的
PFMEA假设前工程之半成品零件都是好的,列出本制程中所有可能发生的潜在失效模
式,即使它不一定会发生。
温 度
压 力
孔位错
毛 边
变 形
短 路
装卸受损
弄 脏
漏 焊
不适当的结构
工具磨损
5.4.12 失效的潜在效果:
当上述失效发生时,客户会感觉到什么?
后制程性能上会有什么影响?
DFMEA:
失效模式功能上所产生的效果
噪音
粗糙
不稳定动作
需要过份努力
不起作用
令人不愉快的气味
不稳定
动作受损
通风
间歇性动作
外观不佳
控制受损
PFMEA:
失效模式对顾客所产生的效果,在本文中的顾客是指下一个工程、随后的工程或场所、交易商和(或)最终使用者、当评估一个失效的潜在效果时,每一个都必需被考虑到。
不能装配
尺寸不符合规格
不能加工
不密合
毛 边
压伤
模具磨损
损坏设备
伤害操作员
端子下陷/上翘
共面度不合格
不保膜
挟持力不足
胶芯/后盖卡勾断裂
文件编号
页版本
1
文件名称
失效模式与效应分析作业程序
页 次
5/10
5.4.13 严重性Severity(S):
严重性系失效对产品功能所造成影响而言,其程度评估必须会同后制程、工程及品保人员一同决定。
严重性只有透过设计更改才可修改严重性等级。
严重性依程度评估由1至10分。
严重性评估标准
效 果
标准:
效果的严重性
等 级
危险-
无警告
伤害机器或装配操作员,当一个潜在失效模式影响安全和(或)涉及政府规定不符时,非常高的严重性等级,失效会在无警告的情况下发生。
10
危险-
有警告
可能会伤害机器或装配操作员,当一个潜在失效模式影响安全和(或)涉及与政府规定不符时,很高的严重性等级,失效会在有警告的情况下发生。
9
甚高
造成生产线重大损坏,产品不得不100%报废,功能无法运作,丧失基本功能,顾客很不满意。
8
高
造成生产线小损坏,产品经分类后部份(少于100%)报废,功能能运作,但功能下降,顾客不满意。
7
中等
造成生产线小损坏,部份产品(少于100%)不得不报废(需要挑拣),功能能运作,但某些舒适/方便性不能动作,顾客有些不舒服。
6
低
造成生产线有一点损坏,100%产品要重新加工,功能能运作,但某些舒适/方便性功能下降,顾客有点不满。
5
甚低
生产线有一点损坏,产品挑拣后,部份要重新加工,合配性、亮度与异音这一项不合要求,大多数顾客注意到了缺陷(多于75%)。
4
很小
生产线有一点损坏,部份产品不得不地重新加工,合配性、亮度与异音这一项不合要求,一般顾客注意到的缺陷(50%)。
3
微乎其微
生产线有一点损坏,部份产品不得不在生产中重新加工,但在站内(in-station)合配性、亮度与异音这一项不合要求,敏锐的顾客注意到的缺陷(少于25%)。
2
无
顾客无法发现的缺陷。
1
文件编号
页版本
1
文件名称
失效模式与效应分析作业程序
页 次
6/10
5.4.14级别:
本栏用于对产品之尺寸特性或保安特殊等级做明确区别。
5.4.15失效的潜在原因与结构:
失效的潜在原因定义为失效会如何发生(设计弱点)。
按照能被矫正或控制的事情来描述,失效原因必须是可管制或是能改善的。
典型失效原因可以包括,但不限于:
DFMEA
塑性
蜕变
疲劳
磨损
材料不稳定
腐蚀
PFMEA
锯带钝化
模具设计不良
零组件遗失或错位
温控器的故障
气压不足
供料不及
涂模剂不剥落
只有特定过失或功能障碍(如:
操作员过失、机器功能障碍)不应该被使用。
5.4.16发生性Occurrence(O):
用1至10分来估计失效原因发生之频率,不要考虑失效模式是否能被检测出,
依据现有数据或以往相关产品之质量记录来决定发生性等级。
可能性
可能的失效率
CPK
等级
甚高:
失效几不可避免的。
≧1/2
1/3
<0.33
≧0.33
10
9
高:
一般与经常发生性失效的前制程相似的制程联系在一起。
1/8
1/20
≧0.51
≧0.67
8
7
中等:
一般同与曾经历过偶然失效但比例高的前制程相似之制程相联系的。
1/80
1/400
1/2000
≧0.83
≧1.0
≧1.17
6
5
4
低:
与相似制程相联的孤立的失效。
1/15000
1/150000
≧1.33
≧1.50
3
2
甚低:
只有与几乎相同制程相联系的单独的失效。
极低:
失效不可能,没有曾与几乎相同制程相联系的失效。
≦1/1500000
≧1.67
1
文件编号
IP-AQA01
页版本
1
文件名称
失效模式与效应分析作业程序
页 次
7/10
5.4.17现行设计&制程管制:
分为预防&侦测。
现行管制是对要在一定程序上阻止了失效模式出现,如果它出现就测出该失效模式的管制的措述,这些管制的可能是诸如装置器差错防止或制程管制之类的制程管制,或者可能是后制程评估。
这评估可以在目标制程发生后或在随后的制程上发生。
期优先次序:
5.4.17.1防止原因/机构或失效模式/效应的发生,或降低他们的发生性。
5.4.17.2侦测出原因/机制并导致矫正行动。
5.4.17.3.侦测出失效模式。
5.4.18侦测性Detection(D):
假设失效发生,上述5.4.17.2与5.4.17.3两类型现行管制措施在零组件流入下工程之前,
检测出潜在失效原因或失效模式之可能机率,用1至10分来代表检出能力之高低。
注意!
不要因为发生率低就以为侦测能力高。
侦测性
由设计控制所测出的可能性
制程管制减检测出来之可能性
等级
完全不确定性
将不会和(或)不能侦测潜在的原因/机制和随后的失效模式;或者根本没有设计控制。
现在没有已知的控制去检测或检查失效模式。
10
极其微乎其微
几乎不可能侦测出潜在原因/机制和随后的失效模式的机会。
现行的控制将检测出失效模式的可能性极其微乎其微,间接或随机检查。
9
微乎其微
侦测出潜在原因/机制和随后的失效模式的机会.微乎其微。
现行的控制将检测出失效模式的可能性绝少。
目视检查。
8
很低
侦测出潜在原因/机制和随后的失效模式的机会很小。
现行的控制将检测出失效模式的可能性甚低。
双重目视检查。
7
低
侦测出潜在原因/机制和随后的失效模式的机会很小。
现行的控制将检测出失效模式的可能性较低。
SPC管制。
6
文件编号
页版本
1
文件名称
失效模式与效应分析作业程序
页 次
8/10
侦测性
由设计控制所测出的可能性
制程管制减检测出来之可能性
等级
一般
侦测出潜在原因/机制和随后的失效模式的机会有限
现行的控制将检测出失效模式的可能悾中等。
计量值/计数值测定。
5
有点高
有机会侦测出潜在原因/机制和随后的失效模式
现行的控制将检测出失效模式的可能性不低。
后续作业侦测/作业前准备/首件检查。
4
高
将会侦测出潜在原因/机制和随后的失效模式
现行的控制将检测出失效模式的可能性较高。
当场或多重接获准则后续作业侦测。
3
很高
有很高的机会侦测出潜在原因/机制和随后的失效模式
现行的控制几乎可以确定能检测出失效模式。
当场自动化侦测。
2
几乎可以确定
几乎会侦测出潜在原因/机制和随后的失效模式
现行的控制几乎可以确定。
制程/产品设计防误法.无产出缺陷零件。
1
5.4.19风险领先指数(RPN):
风险领先指数是严重性(S),发生性(O)与侦测性(D)的产物RPN=(S)╳(O)╳(D),公司依RPN评估等级采取必要措施:
5.4.19.1严重性:
经评分后为:
9或10分且发生次数>1分者.
5.4.19.2单项评分发生次数≧7分者
5.4.19.3R.P.N(风险优先数)≧100分者。
5.4.19.4非前述3项但判定仍有改善须要且有能力改善者。
5.4.20推荐措施:
推荐措施须优先针对RPN最高者,若对于其成因机构并不十分了解,可以藉由试验获得适当之对策。
如果失效模式可能造成后制程人员伤害时,就一定要采取措施加以消除或控制,否则要给予操作人员适当保护。
如果没有适当对策就填写「无」。
建议对策应考虑以下方向:
5.4.20.1要求修订制程或设计以降低失效发生性的机率。
另外利用统计法对制程进行的行动导向分析,可凭借适当程序不间断的讯息回馈,以达成持续的改善及缺点预防。
5.4.20.2只有一项制程或设计修订能降低严重性之等级。
5.4.20.3修订制程或设计以提升侦测能力,一般而言,增加检验管制会增加成本而且对质量改善没有帮助,只能作为暂行措施。
总之,预防重于检验,例如统计制程管制要优于随机之质量检验。
文件编号
页版本
1
文件名称
失效模式与效应分析作业程序
页 次
9/10
5.4.21推荐措施之负责单位/人员及完成日期:
负责执行改善之单位及预定完成之日期,如果没有任何需执行改善动作,此栏项"无"。
5.4.22采取的措施:
在一项措施被实施后,请填入一份对该措施的简要描述及有效日期。
5.4.23改正后结果:
于推荐措施执行完成后,将推荐措施中有效之措施纳入采取的措施中,重新评估严重性、发生性、侦测性及RPN值。
如果没有任何措施,则此栏空白,如果有必要采取进一步措施,请重复5.4.20到5.4.21的步骤。
改善措施实施后必须再予评分确认是否改善,如未达改善效果应再检讨并提出对策(或列为管制重点)以PDCA方式持续改善活动。
5.5制程FMEA增修订之程序如下:
5.5.1新产品或重要原料、规格变更时,RD开发单位应于接获通知后召集小组成员重新审查是否须增修订,增修订结果应于量产前评估会议提出。
5.5.2新设备入厂、制程变更,工程或制程单位亦应召集小组成员重新评估之,以达成顾客目标。
5.5.3当原有之失效模式重新评估及改善,或新的失效模式增列评估及改善后,必须将已改正之严重性、发生性、侦测性及RPN值重新填写于「PFMEA」上,(此时"改正后结果"栏空白),并依文件管制程序向文件管制中心提出文件修订。
5.5.4制程FMEA改变时必须适时修订「QC工程表」、「标准作业程序(SOP)」、「作业指导书」。
5.6.风险优先数RPN评比标准:
跨功能专业小组必需一致同意评比标准及等级之区分,即使是因个别制程分析而修改评比标准时。
六.管制特性:
为确保本公司生产之产品及制程之管制特性,均被确实的掌握及适当的管理。
6.1制程管制特性:
该制程的质量变异会造成部品的基本功能丧失或无法使用。
管制特性:
指有关产品的要求(尺寸、性能测试)或制程参数具有『重要性』;符号为『◇』(相对于三大车厂中克赖斯勒之钻石『D』符号)。
6.2产品管制特性:
产品变异的发生对使用者,会造成身体的伤害及他物损毁或引起严重的灾害等之部品。
安全特性:
指有关产品的要求(尺寸、性能测试)或制程参数,可能影响安全性或政 府法令之规定者,必须采取『特别措施』纳入管制计划中;符号为『☆』符号(相对于三大车厂中克赖斯勒之盾牌『S』符号、福特之倒三角▽))。
6.3管制时机:
A.开发单位接获客户所提供的图面中,有管制特性符号标示者。
B.客户代表针对产品特性或以往承制经验所做的特别要求。
C.本公司根据以往对类似部品承制经验认为有必要时。
文件编号
页版本
1
文件名称
失效模式与效应分析作业程序
页 次
10/10
6.4文件标示:
制作管制计划(QC工程表)、检查规格、FMEA、作业指导书等,属管制特性者须加盖”管制特性”,以凸显该工程之重要性。
6.5属制程管制特性作业人员,必须指定作业者,且适当教育训练测试合格者,方可担任。
6.6管制特性产品或制程于生产作业发生异常,必须迅速反应主管处置。
6.7管制特性之设备若故障,宜优先排除;故障排除后,如有必要应请品管做品质项目确认。
6.8管制特性工程作业不得外包,若须外包生产或加工,须经评估合格并经总经理核准,才可外制。
七.参考文件:
失效模式与效应分析参考手册
(PotentialFailureModeandEffectsAnalysis :
FMEA)
八.记录之保存:
FMEA文件依文件管制规定之保存期保存之。