金属工艺及机制基础实验指导书.docx
《金属工艺及机制基础实验指导书.docx》由会员分享,可在线阅读,更多相关《金属工艺及机制基础实验指导书.docx(18页珍藏版)》请在冰豆网上搜索。
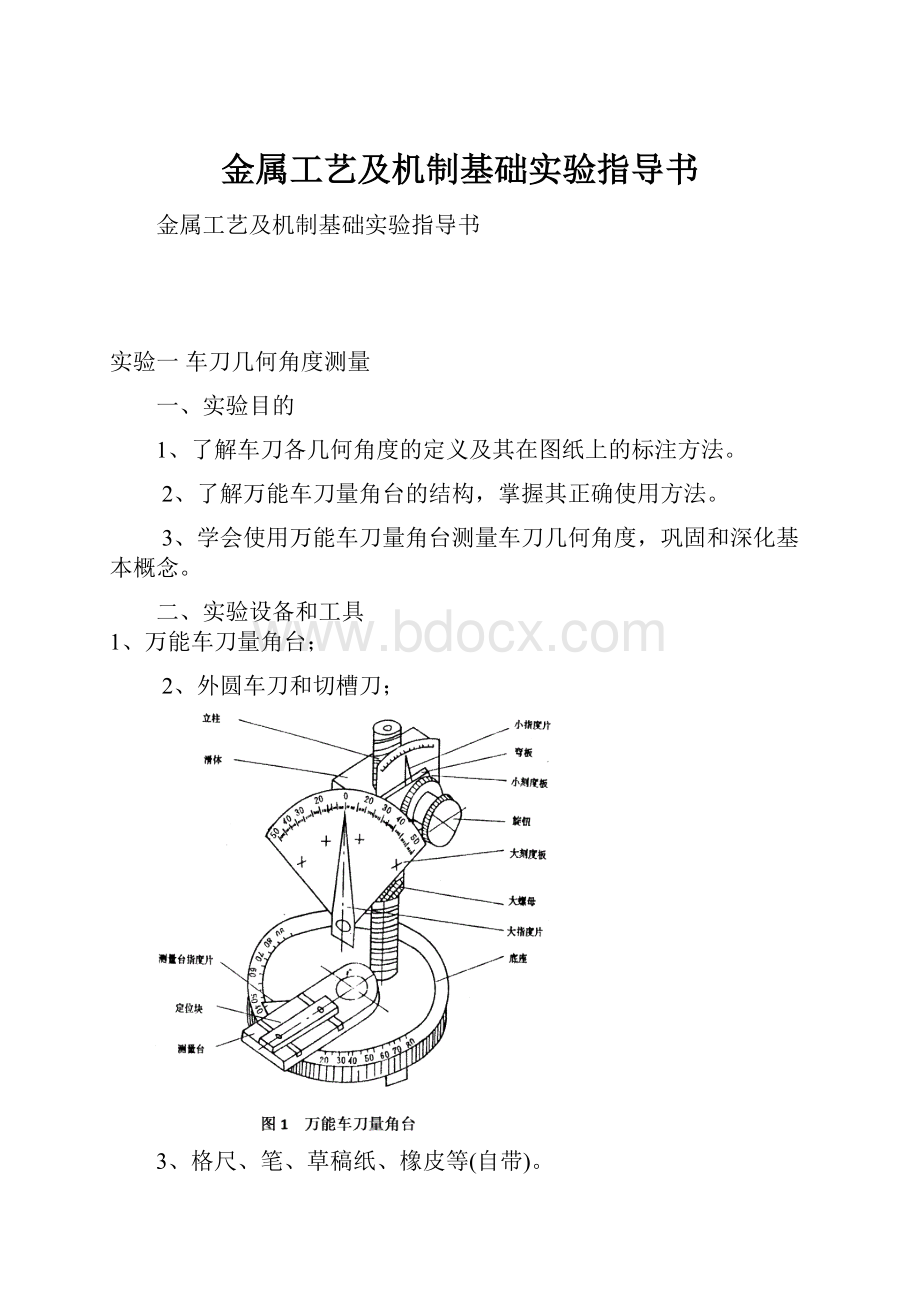
金属工艺及机制基础实验指导书
金属工艺及机制基础实验指导书
实验一车刀几何角度测量
一、实验目的
1、了解车刀各几何角度的定义及其在图纸上的标注方法。
2、了解万能车刀量角台的结构,掌握其正确使用方法。
3、学会使用万能车刀量角台测量车刀几何角度,巩固和深化基本概念。
二、实验设备和工具
1、万能车刀量角台;
2、外圆车刀和切槽刀;
3、格尺、笔、草稿纸、橡皮等(自带)。
三、仪器简介
万能车刀量角台是测量车刀标注角度的专用仪器,其型式很多,常用的车刀量角台如图1所示。
它不仅能测量主剖面参考系的基本角度,而且也能很容易地测量
主法剖面参考系的角度。
它主要由底座、立柱、测量台、定位块、大小刻度盘、大小指度片、螺母等组成。
在圆形底盘的周边上刻有从0º向左、右各100º的刻度,其中底座和立柱是支撑整个仪器的主体。
测量时,刀具放在测量台上,靠紧定位块,
可随测量台一起顺时针或逆时针方向旋转,并能在测量台上沿定位块前后移动和随
定位块左右移动。
旋转大螺母可使滑体上下移动,从而使两刻度盘及指度片达到需要的高度。
使用时,可通过旋转测量台或大指度片,使大指度片的前面或底面或侧面与刀具被测要素紧密贴合,即可从底座或刻度盘上读出被测角度数值。
四、实验步骤
(1)原始位置调整:
将量角台的大小指度片及测量台指度片全部调到零位,并把刀具放在测量台上,使车刀贴紧定位块、刀尖贴紧大指度片的大面。
此时,大指度片的底面与基面平行,刀杆的轴线与大指度片的大面垂直,如图2所示。
(2)在基面Pr内测量主偏角Kr、副偏角Kr′:
旋转测量台,使主刀刃与大指度片的大面贴合,如图3所示,根据主偏角定义,即可直接在底座上读出主偏角Kr的数值。
同理,旋转测量台,使副刀刃与大指度片的大面贴合,即可直接在底座上读出副偏角Kr′的数值。
(3)在切削平面Ps内测量刃倾角入s:
旋转测量台,使主刀刃与大指度片的大面贴合,此时,大指度片与车刀主刀刃的切削平面重合。
再根据刃倾角的定义,使大指度片底面与主刀刃贴合,如图4所示,即可在大刻度盘上读出刃倾角入s的数值(注意入s的正负)。
(4)在主剖面Po内测量前角γo、后角αo:
将测量台从原始位置逆时针旋转(90º-Kr),此时大指度片所在的平面即为车刀主切削刃上的主剖面。
根据前角的定义,
图4在切削平面Ps内测量刃倾角入s图5在主剖面Po内测量前角γo
调节大螺母,使大指度片底面与前刀面贴合,如图5所示,即可在大刻度盘上读出
前角γo的数值。
测量后角αo时,量角台处于上述同一位置,根据后角的定义,调节大螺母,使大指度片侧面与后刀面贴合,如图6所示,即可在大刻度盘上读出后角αo的数值。
(5)在副剖面Po′内测量副后角αo′:
将测量台从原始位置顺时针旋转(90º-Kr′),此时大指度片所在的平面即为车刀副切削刃上的副剖面。
根据副后角的定义,调节大螺母,使大指度片侧面与副后刀面贴合,即可在大刻度盘上读出副后角αo′的数值。
(6)在法剖面Pn内测量法向前角γn、法向后角αn:
将测量台逆时针转过(90º-Kr),松开小螺母,使小指度片在刻度盘上转过入s,旋向根据入s值的正负确定。
若入s值为正,则逆时针旋转;若入s值为负,则顺时针旋转。
此时大指度片所在的平面即为法向剖面。
根据法向前角和法向后角的定义,按照测量γo、αo相同方法,即为测出法向前角γn和法向后角αn的数值。
实验二切削用量对加工表面粗糙度的影响
一、实验目的
1、了解加工表面粗糙度的影响因素。
2、了解降低加工表面粗糙度的工艺措施。
3、通过实验测出数据验证切削用量v、f、ap对加工表面粗糙度的影响,达到深化、巩固所学的基本概念和基本理论的目的。
二、实验设备和工具
1、普通车床。
2、光切显微镜。
3、车刀、试件。
4、计算器、格尺、笔。
三、实验原理
1、表面粗糙度及其影响因素
金属切削加工的工件表面微观上表现为间距较小(小于1mm)、高低起伏的微小峰谷。
这些峰谷的一些特征参数即为表面粗糙度,其值反映了零件表面加工痕迹的高低不平程度和峰谷间的某些特征。
它和工件的尺寸精度、几何形状精度、相互位置精度以及零件表层的物理力学性能一样,是度量工件加工质量的重要指标。
影响工件表面粗糙度的因素很多,也很复杂,主要有以下几个方面:
切削刃、刀面、切削崩碎(脆性材料)、加工系统的高频振动、刀具角度、材料性能、切削用量等,我们实验主要研究切削用量对工件表面粗糙度的影响。
1)切削速度v对表面粗糙度的影响:
加工塑性金属时,v值越高,材料的变形越小,粗糙度值也越小。
v小于5m/min或大于100m/min,不宜产生积屑瘤,对减小Ra值有利。
V在20~30m/min时切削塑性材料最易产生积屑瘸,使Ra值增加。
常用低速或高速切削以避免积屑瘤的产生,可以降低表面粗糙度。
2)进给量f对表面粗糙度的影响:
在其它条件不变时,根据公式
当γε=0时,H=f/(ctgKr十ctgKr′)
当γε≠0时,H=f2/8γε
可知,减小进给量f可有效地减小残留面积高度H,故可降低加工表面粗糙度。
3)切削液:
冷却和润滑能减小切削、工件和刀具之间的摩擦,降低切削区的温度,从而减小切削过程的塑性变形,并抑制鳞刺和积屑瘤的生成,降低表面粗糙度。
若在切削液中加入硫、磷和氯等添加剂,则降低表面粗糙度的效果更加显著。
4)切削深度ap对表面粗糙度的影响:
比进给量和切削速度影响都小。
当ap小时,切削力也小,不宜产生振动,对减小Ra值有利。
四、光切显微镜简介
本仪器又称光割显微镜。
它是以光切法测量零件加工表面的微观不平度,一般用于测量微观不平度十点高度Rz,能判定国家标准所规定参数Rz<=80~0.8μm表面粗糙度。
五、实验方法和步骤
1、用双顶尖和拨盘将工件装夹在车床上。
2、观察切削条件对表面粗糙度的影响
1)切削速度v
用选定刀具分别以高、低速分别车削45#钢外圆,试件长度取50~60mm。
然后用光切显微镜测定试件表面粗糙度值,将数据填入实验结果表中,并观察加工表面。
实验条件如下:
切削用量:
ap=O.5mm;f=0.2mm/r;
n1=450r/min;n2=1100r/min。
刀具:
1#
2)进给量f
用选定刀具分别以大、小两种进给量车削45#钢外圆,切削长度取50~60mm。
再用光切显微镜测定试件表面粗糙度值,将数据填入实验结果表中,并观察加工表面。
实验条件如下:
切削用量:
ap=0.4mm;n=1100r/min;
f1=0.1mm/r;f2=0.2mm/r。
刀具:
1#
3)切削深度ap
用选定刀具分别以大、小两种切削深度车削45#钢外圆,切削长度取50~60mm。
再用光切显微镜测定试件表面粗糙度值,将数据填入实验结果表中,并观察加工表面。
实验条件如下:
切削用量:
n=1100r/min;f=0.15mm/r;
ap1=0.15mm;ap2=0.3mm。
刀具:
1#。
3、分析切削用量对表面粗糙度的影响。
实验三安装方法对零件加工精度的影响
一、实验目的
1、了解加工精度的概念。
2、了解安装因素对加工精度的影响形式。
3、熟悉齿轮跳动检查仪的结构与用途。
二、实验设备
1、普通车床
2、齿轮跳动检查仪
3、试件:
阶梯轴2件
三、实验原理
1、加工精度的概念
加工精度就是工件加工后的几何参数与图纸规定的几何参数相符合的程度。
符合程度高,加工精度也高。
工件几何参数包括形状、尺寸和相互位置等三个方面,所以加工精度包括:
(1)几何形状精度
表示加工表面宏观几何形状误差不超过一定范围。
如圆度、圆柱度、平面度、直线度等均属几何形状精度。
(2)尺寸精度
表示加工表面和基准间的尺寸误差不超过一定范围。
(3)相互位置精度
表示加工表面与基准间的相互位置误差不超过一定范围,如平行度、垂直度、同轴度等均属于相互位置精度(误差)。
一般情况下,零件加工精度越高,成本也越高,生产率越低,因此,设计者应在满足使用要求的前提下,合理确定零件的加工精度;工艺人员应该采取有效的工艺手段,在保证工件加工精度的前提下,尽量提高生产率和降低生产成本。
零件加工精度主要取决于工件和刀具在切削过程中相互位置的正确程度。
因此,包括机床、夹具、工件、刀具在内的工艺系统中各个环节误差都会不同程度地反映到工件上来,使之产生加工误差,影响加工精度。
2、影响加工精度的安装因素
(1)工件的定位
工件的定位是指以一定的方法将工件正确地安装在机床夹具中或直接安装在工作台上,使待加工表面相对于刀具处于正确位置的过程。
常用的定位方式有:
1)工件直接找正定位
用划线、百分表等直接在机床上找正工件的某个表面作为安装基准。
如图3—1所示。
加工内孔及端面之前用百分表找正外圆表面来完成工件定位。
该外圆表面称找正面,即定位基准。
一般用百分表找正,内外圆的同轴度可控制在φ0.005~φ
0.02mm之内;若同轴度要求不高,可用划线找正,其同轴度误差在φ0.3mm左右。
图3—1图3—2a)图3—2b)
显然,直接找正定位方法对加工精度的影响取决于工人的技术水平和经验,比较费时,且不稳定,一般只适用于下列情况:
a、工件加工批量小,采用夹具不经济。
b、工件的定位要求特别高(如小于0.01~0.05mm),采用夹具不能保证,只能用精密量具直接找正定位。
2)按划线找正定位
在涂有白粉的毛坯上,用高度游标卡尺、划针等将加工表面的轮廓及中心线、对称线划出来,再用划针找正工件定位。
该法的误差比较大,工件的定位精度一般只能达到0.2~0.5mm,对于形状复杂的工件,有时需要经过几次划线。
所以,划线找正定位方法对加工精度的影响也取
四、实验方法和步骤
1、卡盘安装对加工精度的影响。
(1)将试件用三爪卡盘夹紧。
(2)加工至图4所示要求。
(3)卸下工件测量同轴度误差。
2、中心孔安装对加工精度的要求
(1)利用中心孔将阶梯轴装夹在车床前后顶尖之间。
(2)车削各轴断的外圆至图4所示要求。
(3)测量工件的同轴度误差。
图4
五、齿轮跳动检查仪的结构及原理
(一)结构如图5所示,齿轮跳动检查仪是多用性仪器,可测量有中心孔的圆柱齿轮,圆锥齿轮,蜗杆蜗轮的齿轮齿圈跳动,圆柱表面的圆度、圆柱度、同轴度及各种跳动等。
(二)测量原理及步骤
1、将加工好的阶梯轴安装在顶针架上,使其无轴向移动;同时将千分表安装在千分表架上。
2、松开测量架上的紧固螺钉,转动升降螺母7,升降测量支架10,使测量头在被测表面上。
将千分表压缩1~2圈(用测量支架调),紧固测量支架的螺钉,然后调干分表(转动千分表盘对零即可)。
3、以前后顶尖公共轴线为基准轴线,在被测量表面上选取十个横截面逐一测量,依次读出千分表中的最大变化值a1、a2、a3、a4、a5、a6、a7、a8、a9、a10,将测得数据填入实验报告内。
图5
1、底座2、活动台3纵向移动手轮4、紧固螺钉5、顶尖6、项尖架7、升降螺母8、立柱
9、千分表10、测量支架11、可换测量头:
12、顶尖紧固螺钉13、移动手柄14、顶尖架紧固螺钉
实验四冲压模具的结构分析与拆装
—、实验目的
1、掌握冲压模具的结构、组成及各部分的作用.
2、了解连续模与复合模各自的特点.
二、实验用具
1、落料——冲孔连续模。
2、落料——拉深复合模。
三、实验原理
冷冲压模具是对板材进行压力加工以获得合格工件的工具。
在冲压过程中,模具的凸模和凹模直接接触被加工材料并相互作用,使其产生变形或分离,从而形成预期的工件形状。
图1所示的落料—冲孔连续模可按一定的程序,在冲床滑块的一次行程中,完成两个冲压工序。
工作时,随着条料的连续送进,在模具的两对凸模和凹模的作用下,分别完成冲孔和落料工作。
该模具容易保证零件各部分的相对尺寸,生产效率也较高。
该模具工作时,首先由冲孔凸模和凹模冲出零件的四个孔,然后把条料向前送进一个步距,利用落料凸模和凹模进行落料,即可得到所需要的零件。
在前一个零件落料的同时,冲孔凸模和凹模又冲出下一个零件上的孔。
随着条料的不断送进,连续地冲孔和落料,冲床滑块的一次行程,即能完成整个零件的冲压工序。
连续模中,定位是一个关键问题,本实验所用模具,条料横向由定位器定位,纵向由导板定位,上下方向凸凹模对正由导柱导套进行导向。
图2所示的落料—拉深复合模,制件为有凸缘的拉深件。
落料时,在落料凹模和落料凸模的作用下,冲下拉深时所需的制件毛料,废料由卸料橡皮卸下。
落料完毕后随即进行拉深工作,这时,落料凸模即成为拉探凹模。
拉深凸模固定在下模座上。
顶件器上部的压边圈在顶件器中的橡皮作用下。
通过顶杆产生压力,当落料工作完成后,压边圈就与拉深凹模将毛料压紧,防止制件在拉深过程中产生起皱现象,直到拉深完毕。
当拉深完毕上模上升时,压边圈在顶件器的作用下将制件顶出。
如制件卡在拉深凹模内时,则由卸料杆将制件击落。
四、实验内容和步骤
本实验要求完成拆装落料—冲孔连续模和落料—拉深复合模各一副,对模具的整体作用和各个部分的单独及联合作用进行功能分析。
1、打开上下模,认真观察模具结构及动作过程。
2、分析模具的整体作用。
3、分析各组合结构的特点和作用。
图1
4、分析各个零件的作用。
图1为落料—冲孔连续模的结构图,1模柄,2上模座,3固定板,4冲孔凸模,5落料凸模,6导套,7导柱,8定位器压杆,9卸料板,10导板,11冲孔凹模,12落料凹模,13固定板,14下模座,15定位销,16定位器,17定位器弹簧,18定位器支柱。
图二为落料—拉深复合模的结构图,1卸料板,2模柄,3上模座,4固定板,5凸凹模,6卸料橡皮,7落料凹模,8拉深凸模,9压边圈,10顶杆,11固定板,12下模座,13顶件器。
实验五微机控制线切割机床加工