钢结构制作质量管理制度.docx
《钢结构制作质量管理制度.docx》由会员分享,可在线阅读,更多相关《钢结构制作质量管理制度.docx(11页珍藏版)》请在冰豆网上搜索。
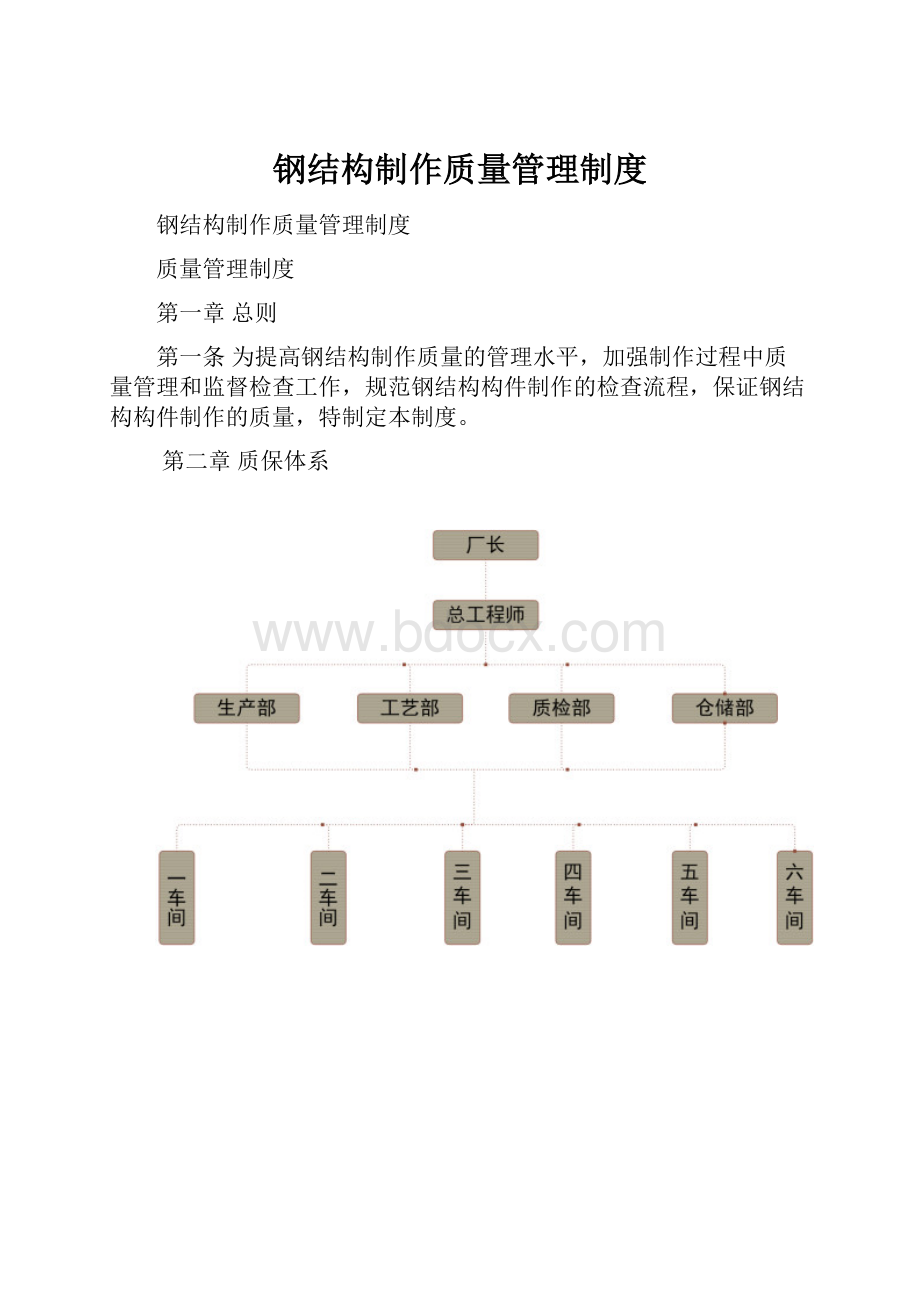
钢结构制作质量管理制度
钢结构制作质量管理制度
质量管理制度
第一章总则
第一条为提高钢结构制作质量的管理水平,加强制作过程中质量管理和监督检查工作,规范钢结构构件制作的检查流程,保证钢结构构件制作的质量,特制定本制度。
第二章质保体系
5.组织编制、修改、管理质量管理文件,负责质量文件的有效性评定;
6.支持上级单位的质量工作;
7.完成领导交办的其他工作。
第五条部门经理助理职责
1.协助部门经理制订质量管理的规章制度,负责归口管理、监督、检查执行情况;
2.进行质量监控,对生产工艺进行监督,处理生产过程中的质量问题,及时反馈至部门经理;
3.协助部门经理开展原材料检验,生产成品检验工作,做好相应质量检验记录;
4.按规定进行产品质量检查,协调生产过程中的质量问题;
5.组织各类质量方面的数据统计、汇总和上报;
6.完成领导交办的其他工作。
第六条材料检验员岗位职责
1.制定材料送检方案,包括取样主材、辅材的规格与数量、具体时间安排等内容;
2.开展原材料的取样、送检及其他一些试验活动的现场实施,做好取样记录并建立相应台帐;
3.收集、整理、保存检验试验资料,及时编写相关报告,总结成果,及时将结果反馈至部门经理;
4.完成领导交办的其他工作。
第七条质量检验员岗位职责
1.监督、检查车间工艺执行情况,确保过程中工艺文件、质量要求贯彻实施;
2.对产品进行内部检查验收,做到质量控制及时有效;
3.向监理监造报验构件,并向部门经理反馈结果;
4.协助推行检查车间质量管理制度运行情况;
5.完成领导交办的其他工作。
第八条资料员岗位职责
1.负责工程资料的收集、整理、移交及存档工作;
2.负责各类质量报表的上报工作;
3.根据监理、监造的要求上报相关资料,听取意见并将意见及时反馈至部门经理;
4.部门考勤、收发文,资金计划、工作计划总结等综合性事务;
5.完成领导交办的其他工作。
第九条车间自检员工作职责
1.负责车间产品的质量检查工作;
2.负责填写、整理产品过程资料和交接报验资料,并配合质检部资料员做好交工资料的整理工作;
3.针对自身编制切实可行的车间质量管理制度、管理措施和办法,提高车间的质量水平。
第四章编制工程检验计划
第十条在建工程开工前应根据技术主管部门技术交底及工艺、设计蓝图要求编制工程检验计划,并严格按规定权限履行审批手续后方能付诸实施。
第十一条检验计划的内容有:
质量要求、制作要求、过程检查主要控制点、验收标准等主要内容。
第十二条检验计划交底:
由编制部门负责向车间、班组及外协交底。
第五章原材料质量管理
第十三条各工程制作所需原材料按《材料管理制度》执行。
第十四条物资主管部门在进行工程所需的各种材料的采购前,应审查生产厂家是否满足业主及工程所需材料要求,并要求提供相关证明。
必要时应进行材料产地或生产厂家的质量调查,确保工程材料的质量保证。
第十五条材料进场后,质量主管部门与物资主管部门负责按照材料质量标准进行外观质量和几何尺寸的检验,并做好相关记录。
第十六条质量主管部门在外观质量检查合格的原材料、半成品中按照业主、监理及国家标准的规定进行取样,抽取的样品由质量主管部门材料检验员负责送检,检测单位应具有规定的资质并在当地建设行政主管部门备案认可。
第十七条只有经过验收、检验被确认为合格的原材料、半成品、零部件才能被允许使用。
第十八条经检验不合格的材料应进行明显的标识,并及时与供应商联系按照合同协商解决。
严禁在工程上使用不合格材料;
第十九条材料进场验收后,均应做好标识,并按要求进行保管:
编号
阶段
工作内容
1
进货
(1)办理入库验收手续,建立进货记录和物资台帐(台帐中注明进货日期、数量、使用、发放日期、使用部位);
(2)贴标签分类码放,按照不同品种、标号、出厂日期、进场时间分区堆放,并用标牌标识其名称、规格、型号、质量等级及检验和试验状态等。
2
贮存
(1)现场加工好的半成品按不同结构编号整齐码放,并附上标识牌;
(2)妥善保持物资存贮器上的标识、标签;
(3)当存贮器中的物资更换或用尽时,及时更新标识内容。
3
发放
核验领料凭证,并采取“先进先出”的措施。
第二十条本材料质量管理同时适用于甲供料加工工程。
第二十一条取样复验主要表格包括:
工程材料见证取样委托单、材料取样送检试验台帐等。
取样检测流程详见《原材料复检管理流程》。
第六章制作过程的质量控制
第二十二条工程质量检验工作必须严格按照国家和地方政府的法律、法规、规范及规程标准执行。
第二十三条工程开工前,相关部门应对车间及作业班组进行技术、制作工艺和检验计划交底。
第二十四条作业班组应严格按照设计图纸和技术交底、制作工艺以及质量验收规范的要求进行,专职质量检验员应按照检验批的划分随时检查制作质量,发现有不符合验收标准要求的及时进行整改。
第二十五条作业班组在工程生产过程中严格进行“三检制”。
上道工序经检验合格后才能进入下道工序的生产。
第二十六条专职质量检验员及车间应认真做好生产记录,以保持加工质量的可追溯性。
第二十七条对不合格的工序产品、应进行及时整改并跟踪复查。
第二十八条外协加工的半成品,由质量主管部门、生产管理部门和技术管理部门共同检查,负责进行外观质量检查。
外观检查合格的半成品中按质量验收标准的规定进行取样,并应按规定做好养护、送检工作。
第二十九条在制作过程中质量主管部门派专人做好现场的试验检测工作。
第三十条按照工程具体要求检查所需样板。
第三十一条质量主管部门会同各加工单位一起对工程质量数据和质量状况进行汇总分析。
第三十二条制作过程中,外协制作厂应严格按照项目质量计划实施过程质量控制,现场分项分部工程质量必须满足质量计划的要求,严格按签订的外协加工合同执行。
第三十三条各重点工序检查要点和要求见《过程质量监督检查管理制度》。
第七章标识、成品保护管理
第三十四条质量主管部门负责监督、检查车间对构件、物资的标识和可追溯性的管理工作。
第三十五条物资主管部门以及车间负责对原、辅材料及生产过程中所有零部件、构件进行标识,并有可追溯性。
第三十六条标识的范围
1.生产所需的原、辅材料;
2.生产车间的零部件、半成品及成品构件。
第三十七条标识的方法
1.钢构件具体标识方法见技术管理部《钢构件标识管理标准》(GGJSWHC·JS10);
2.主材、辅材由物资主管部门采用立标牌方式并标明材料规格、材质、数量、产地、进场日期等;
3.库内存放物资,物资主管部门宜采用悬挂卡片的方法标识名称、规格、材质、数量、产地等;
4.下料班组在零部件下料完成后,进入下道工序前用油漆标明零件号、材质等信息;
5.每道焊接作业完成后,焊接班组应在焊缝附近标记焊工钢印号;
6.总装班组应在构件组装完成后,用钢印标记出构件编号;
7.油漆班组在构件涂装时,应保证构件标识移植的准确性,并做好相应记录。
第三十八条成品堆场构件的堆放、发运的质量管理
1.进入堆场待发运的构件,必须是检验后的合格品;
2.构件堆放、转运、装车应符合相关要求,并有防变形措施;
3.构件的转运过程中必须采取一切有力措施保证构件油漆不损伤、不污染、不变形等质量问题;
4.构件堆放、装车时应考虑构件的堆放位置,以免构件受压变形,大型构件间应设置捆扎点和吊点,确保构件吊运时不受损伤,堆场要做好成品构件的堆放及保护措施;
5.装车时应垫好枕木,吊运时注意油漆保护,装车完后应用钢丝绳可靠捆扎,并注意钢结构件装车高度。
第三十九条成品保护
1.钢构件涂装后应加以临时围护隔离,防止踏踩,油漆未干透不得任意转运,以防损伤涂层;
2.钢构件涂装后,在4h之内如遇有大风或下雨时,应加以覆盖,防止粘染尘土和水气、影响涂层的附着力;
3.涂装后的构件需要运输时,应注意防止磕碰,防止在地面拖拉,防止涂层损坏;
4.涂装后的钢构件勿接触酸类液体,防止咬伤涂层,注意保护构件使用软性材料对构件及构件与包装运输车辆之间进行隔离和衬垫,特别是一些较薄的连接板,应尽量避免与其它构件直接接触;
5.喷涂油漆后的钢构件不得踩踏,转运时轻拿轻放,注意油漆的保护;
6.对油漆好的构件短期内不发货的,应用油布或彩条布遮盖,以保护构件油漆。
第八章不合格构件控制管理
第四十条半成品不合格管理
1.严格控制不合格原、辅材料进入车间制作现场,发现有不合格原、辅材料应立即标识、隔离并移出制作现场,防止误用;
2.车间自检员对制作过程中发现的不合格构件和过程,应按规定进行标识、记录,并自行整改。
第四十一条成品构件不合格管理
1.质量主管部门在收到构件成品报验单后发现不合格构件,视质量情况严重与否,下质量整改单或质量罚款单,车间在规定时间内必须整改完毕,由专职检验员进行跟踪;
2.对返修或返工后的构件,应按规定重新进行报验、检验,并应保存检验记录;
3.当发现产品的不合格能影响工程结构安全和使用功能或重要构件(部件)不合格时,应组织总工程师(副总工程师)及技术管理部门、生产管理部门、车间相关人员共同确定处理方案;
4.严禁不合格工序未经处理转入下道工序;
5.车间自检人员及专职质检员必须按规定保存不合格构件的检查记录;
6.对产生不合格原材料的供方(分包方),重新进行评价考核;
7.质量主管部门应对不合格构件的数据信息要及时进行统计、整理、分析,为制定纠正和预防措施提供依据。
第九章工程质量事故调查和处理
第四十二条质量事故的界定
1.工程质量事故按事故的性质及严重程度划分为一般事故和重大事故分别处理;
2.一般质量事故定义为:
影响使用功能和工程结构安全,造成永久质量缺陷的或工程结构安全、存在重大质量隐患的;
3.重大质量事故定义为:
在工程建设过程中由于责任过失造成工程倒塌或报废。
第四十三条事故处理
1.质量事故发生后,制作车间应马上停止进行质量缺陷部位和与其有关联部位及下道工序生产,并要求制作车间采取必要的措施,防止事故扩大。
同时质量事故发生车间应迅速按性质及严重程度向质量主管部门汇报。
2.由质量主管部门牵头成立由工艺、生产、材料等相关部门组成质量事故调查小组,对质量事故进行全面调查。
各相应部门应积极协助,客观地提供相应证据。
3.质量事故的调查:
(1)查明事故发生的原因、过程、事故严重程度和经济损失情况;
(2)查明事故的性质、责任单位和主要责任人;
(3)组织技术鉴定;
(4)明确事故主要责任单位和次要责任单位,承担经济损失的划分原则;
(5)提出技术处理意见及防止类似事故再次发生应采取的措施;
(6)提出对事故责任单位和责任人的处理建议;
(7)写出事故调查报告。
第四十四条质量事故的处理
1.制定质量事故技术处理方案。
该方案由工艺主管部门提供技术处理方案,并经总工程师(副总工程师)签字同意;
2.技术处理方案批准后,制作车间应严格按此方案实施修补,技术处理过程中的关键部位和关键工序质量主管部门专职质检员及工艺技术人员应进行旁站,并会同各有关单位共同检查认可;
3.车间处理完工自检后报验结果,由质量事故调查组组织有关各方进行检查验收,必要时应进行处理结果鉴定。
并要求事故车间整理编写质量事故处理报告,并审核签认,将有关技术资料归档。
第四十五条质量事故处理报告主要内容
1.质量事故情况、调查情况、原因分析(质量事故调查报告);
2.质量事故处理的依据;
3.质量事故技术处理方案;
4.实施技术处理生产中有关问题和资料;
5.对处理结果的检查鉴定和验收;
6.质量事故处理结论。
第十章质量例会管理
第四十六条质检部每月组织一次全厂范围的质量例会,在开会前由质检部组织厂领导、技术、生产、车间等相关负责人及质检人员对车间构件质量进行检查,检查完毕进行质量例会,在会上对质量问题进行分析、总结,提出解决质量问题的措施。
根据质量检查情况,提交质量检查报告,以《质量检查会议纪要》的形式发给各参检人员。
第十一章附则
第四十七条本制度由质检部负责解释。