轮轴损伤形式与检修.docx
《轮轴损伤形式与检修.docx》由会员分享,可在线阅读,更多相关《轮轴损伤形式与检修.docx(32页珍藏版)》请在冰豆网上搜索。
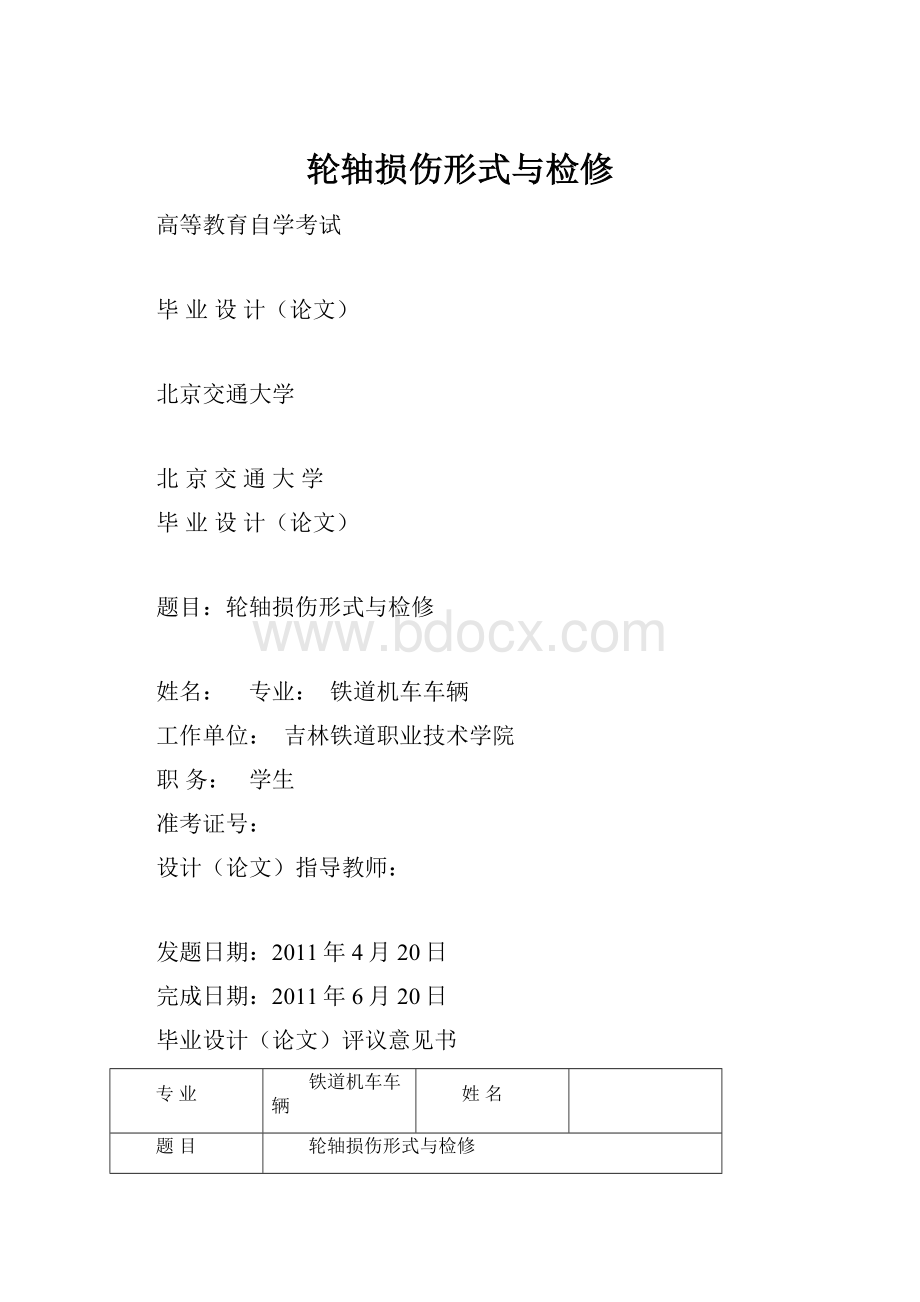
轮轴损伤形式与检修
高等教育自学考试
毕业设计(论文)
北京交通大学
北京交通大学
毕业设计(论文)
题目:
轮轴损伤形式与检修
姓名:
专业:
铁道机车车辆
工作单位:
吉林铁道职业技术学院
职务:
学生
准考证号:
设计(论文)指导教师:
发题日期:
2011年4月20日
完成日期:
2011年6月20日
毕业设计(论文)评议意见书
专业
铁道机车车辆
姓名
题目
轮轴损伤形式与检修
指
导
教
师
评
阅
意
见
成绩评定:
指导教师:
年月日
答
辨
组
意
见
答辩组负责人:
年月日
备
注
毕业设计(论文)任务书
毕业设计(论文)题目:
轮轴损伤形式与检修
毕业设计(论文)内容:
本文主要论述铁道车辆轮对车轮与车轴的损伤形式与检修限度。
主要内容有轮轴的各部分组成与结构简述,重点侧重于车轴的损伤形式与损伤原因;车轮的损伤形式与损伤原因;轮轴的测量,包括踏面圆周磨耗、轮缘厚度、轮缘高度、轮缘垂直磨耗、轮辋厚度、轮辋外侧碾宽、轮辋宽度、踏面擦伤及局部凹陷、踏面擦伤剥离深度、踏面擦伤、剥离长度等的测量以及损伤限度,轮轴修程的判定。
毕业设计(论文)基本要求:
1.论文选题一定要结合实际选择自己较熟悉的专业方向。
通过论文的写作解决工作中所遇到的实际问题,达到提高学员业务水平的要求
2.毕业论文选题避免假、大、空,要具体并有针对性。
3.论文写作不得抄袭,可以借鉴别人的观点,资料运用可以运用站细,要符合论文主题的要求。
一、重点研究的问题
车轴的损伤形式与损伤原因;车轮的损伤形式与损伤原因;轮轴的测量,包括踏面圆周磨耗、轮缘厚度、轮缘高度、轮缘垂直磨耗、轮辋厚度、轮辋外侧碾宽、轮辋宽度、踏面擦伤及局部凹陷、踏面擦伤剥离深度、踏面擦伤、剥离长度等的测量以及损伤限度,轮轴修程的判定。
主要技术指标
1.《铁路货车检修技术规程》
2.《铁路运营管理维修规程》
3.《铁路货车运用维修规程》
二、进度计划
序号
论文内容
日期
完成情况(%)
1
确定论文设计题目,领取设计说明书
4.20
25
2
调研搜集资料
5.10
25
3
论文初稿
5.15
25
4
初稿审核、修改
6.20
15
5
定稿、编排、打印
6.20
10
下达任务日期:
2011年4月20日
要求完成日期:
2011年6月20日
指导教师:
王颜明
开题报告
铁路货车轮轴时货车的重要部件之一,由车轴、车轮和滚动轴承采用过盈配合组装在一起。
轮轴指已压装滚动轴承的轮对,承担着货车承载、走行的功能,起着不可或缺的作用。
由于轮轴承载着铁路货车的载重,受力的作用较大,而且在货车运行时由于车轴与滚子之间的摩擦、踏面与钢轨之间的摩擦等,使车轴与车轮经常损伤。
本文是在对轮轴的相关知识学习,并且通过实践观察学习,参考大量文献资料之后,对车轴的损伤形式与损伤原因;车轮的损伤形式与损伤原因;轮轴的测量,包括踏面圆周磨耗、轮缘厚度、轮缘高度、轮缘垂直磨耗、轮辋厚度、轮辋外侧碾宽、轮辋宽度、踏面擦伤及局部凹陷、踏面擦伤剥离深度、踏面擦伤、剥离长度等的测量以及损伤限度进行研究论述。
摘要
本文主要论述总结铁道车辆车轮与车轴的损伤形式与检修限度。
主要内容有轮轴的各部分组成与结构简述,侧重于车轴的损伤形式与损伤原因;车轮的损伤形式与损伤原因;轮轴的测量,包括踏面圆周磨耗、轮缘厚度、轮缘高度、轮缘垂直磨耗、轮辋厚度、轮辋外侧碾宽、轮辋宽度、踏面擦伤及局部凹陷、踏面擦伤剥离深度、踏面擦伤、剥离长度等的测量以及损伤限度,轮轴修程的判定。
关键词:
车轮;车轴;损伤检修
第1章轮轴组成
1.1车轴
车轴是轮对的主要配件,它除了与车轮组成轮对外,两端还要与轴承装置配合,保证货车安全运行。
按其使用轴承的不同,车轴分为滑动轴承车轴和滚动轴承车轴。
目前,我国铁路货车轮对绝大部分都采用滚动轴承及滚动轴承车轴,但也有极少数货车还在使用滑动轴承车轴及滑动轴承。
1.1.1车轴发展概述
铁路货车车轴最初装用滑动轴承,有A型、B型、C型和D型及其他类型车轴。
B型、C型、D型和E型车轴,轴身为变截面的纺锤形,材质为碳素结构钢。
随着铁路货车由滑动轴承向滚动轴承转化,20世纪70年代在4种滑动轴承的基础上增加了使用滚动轴承的RB2型、RC2型、RD2型、RE2型、RC3型、RD3型、RC4和RD4型等8种车轴,轴身为等截面的平直形,材质为专用优质碳素结构钢。
针对40钢车轴技术性能的不足,从80年代初开始,我国铁路开展了含碳量0.5%的50钢车轴的研究,以期提高车轴疲劳强度,延长车轴的使用寿命,研发了LZ50车轴钢。
2002年取消了C型、RC2型,增加了RE2A型、RD3A型、RD4A型、RD3B型车轴,车轴材质为LZ40钢和LZ50钢。
由于铁路货车滚动轴承采用冷压装方式安装和退缷,车轴轴颈表面发生损伤的数量逐步增加,为做到物尽其用,1993年RD2型车轴开始生产K1、K2等级,K1等级的车轴轴颈直径比原型减少了0.5mm,K2等级的车轴轴颈直径比原型减少了1mm。
随着载重的增加及速度的提高,带有卸荷槽的车轴在轴颈卸荷槽部位发生了多起冷切事故,2003年3月起停止车轴K1、K2等级修并报废正在使用的等级修车轴。
2004年对RD2型车轴轴颈卸荷槽部位进行了研究改进(采用无卸荷槽结构成型磨加工工艺;有卸荷槽的RD2型车轴,轴颈根部圆弧半径由R20改为R25,卸荷槽深度尺寸由0.20
改为0.1,采用车削加滚压加工工艺),当车轴轴颈等级修后定型D1等级轴。
为满足铁路70t级铁路货车的使用需求,2005年又设计了25t周中的RE2B型车轴,其轴颈根部和防尘板座根部采用无卸荷槽形式,并缩短了轴颈载荷中心到根部的距离,材质为LZ50车轴钢。
1.1.2车轴各部分名称及功用
一、滚动轴承车轴
1.中心孔:
加工车轴和组装、加工轮对时机床顶针孔支点,并可以作为校对轴颈。
车轮圆度的中心。
2.轴端螺栓孔:
安装轴承前盖或压板,防止滚动轴承外移窜出。
3.轴颈:
安防轴承,承受垂直载荷。
4.卸荷槽:
为磨削轴颈时便于砂轮退刀,其退刀槽的作用,可以减少轴承内圈组装后与此处相互间的接触应力,有利于提高此处的疲劳强度。
5.轴颈厚肩:
轴颈与防尘板座间的过渡圆弧,可防止应力集中。
6.防尘板座:
安装轴承后档并限制滚动轴承后移。
7.轮座前肩:
防尘板座与轮座之间的过渡圆弧,可防止应力集中。
8.轮座:
固定车轮,时车轴的最大受力部分。
9.轮座后肩:
轮座与轴身之间的过渡圆弧,可防止应力集中。
10.轴身:
车轴中间连接部分。
11.轴端倒角:
轴端部设有1:
10的倒角,其作用时在压装滚动轴承时起引导作用。
二、滑动轴承车轴
滑动轴承车轴与滚动轴承车轴各部分与功用基本相同,所不同的有以下几点:
1.增设轴领:
主要是防止轴瓦外移。
2.轴颈:
安装滑动轴承的轴瓦。
3.没有轴端螺栓孔。
4.没有卸荷槽。
1.2车轮
车轮是铁道车辆所有零件中最基本的零件。
它不仅要承受轮轨之间的垂向、横向动作用力和摩擦力,而且还要承受踏面制动时的热负荷。
它具有载重、导向、传递制动力和牵引力的功能。
它的运用条件十分恶劣,经常发生擦伤、剥离、掉块、热裂和疲劳损坏等损伤。
其性能的好坏,对行车安全具有十分重大的影响。
1.2.1车轮发展概述
1988年1月正式颁布的我国第一个车轮产品标准GB8610—1988国家碾钢车轮标准,把车轮分为A、B两级,铁路货车车轮型号ф840B、ф840C、ф840D、ф840E,碾钢车轮为斜辐板形式,辐板上没有两个直径为45mm的工艺孔,车轮材质为CL60。
1984年以前铁路货车碾钢车轮踏面一直采用锥形轮缘踏面外形,该形式的缺点是轮缘磨耗比较严重,为了减轻轮缘磨耗,1984年研制了LM型磨耗形轮缘踏面外形。
1991年,研制了S形辐板车轮,对于车轮的结构做出了重大修改,强度高,耐热性能良好。
1996年GB8601—1988碾钢车轮标准已经不能适应我国铁路的发展对车轮使用性能的要求,为此制定了使用于时速120km及以下碾钢货车车轮的TB/T2817—1997铁道部行业标准,采用了S形辐板取代了货车车轮的斜辐板结构形式,取消了辐板孔,轮辋厚度为65mm,型号HDS。
为满足减轻簧下质量的要求,设计了轮辋厚度为50mm的S形辐板车轮,21t轴重的为HDSA型,25t轴重的为HESA型,这两种车轮于2001年投入运用。
1999年制定了TB/T1013—1999《碳素钢铸钢车轮技术条件》,铸钢车轮材质为ZL-B,车轮型号为840HDZ。
根据减轻车轮质量的要求,2000年8月,设计出新产品840HDZA型铸钢车轮;2001年3月新型薄轮辋840HDZB型铸钢车轮;2003年1月,设计了第一种铸钢车轮为轴重25t的840HEZB型车轮;新设计了840HDZC型薄轮辋铸钢车轮。
1.2.2车轮结构设计
车轮结构由车轮直径,轮辋、轮毂尺寸,毂辋距,辐板形状,轮缘踏面外形所决定。
每个尺寸和每部位形状都有其特殊意义。
车轮设计时需要对这些尺寸和形状进行研究确定。
一、车轮直径
车轮直径对其本身及整个货车都由较大影响。
一方面车轮直径越大,货车重心越高,货车动力学性能越差。
另一方面,增大车轮直径,可以降低轮轨的接触应力,降低车轮磨耗率,增加车轮的热容量,提高踏面制动热负荷的承受能力,因此车轮直径大小应根据货车情况综合确定。
但总的来说,货车轴重越大,车轮直径应越大,以提高车轮的热容量和增加轮轨接触面积,减少踏面损伤和磨耗。
另外,车轮直径的取值还应注意规格的标准化系列化问题,以利于车轮制造和检修。
目前铁路货车车轮直径大多为840mm,特殊铁路货车车轮直径为915mm。
二、轮辋
轮辋宽度尺寸主要取决于轮轨的搭载量。
当轮对运行在曲线上时,外侧车轮轮缘靠近钢轨,内侧轮缘远离钢轨。
只有内侧车轮踏面在钢轨上的搭载量足够,才能不使轮对脱轨。
《铁路技术管理规程》规定,当曲线半径在300m以下时,规矩应加宽15mm。
因此,最大规矩1435+15+6=1456mm。
轮对最小内侧距为1354mm;
轮缘最小厚度为23mm;
车轮踏面外侧倒角5mm;
钢轨头部圆弧半径R13mm;
钢轨内侧磨耗2mm;
轨枕玩去。
道钉松动等引起轨距扩大8mm;
重车时车轴微弯引起轮对内侧距离减少2mm;
轮轨安全搭载量按7mm考虑。
根据上述数据算的轮辋最小宽度应为120mm,考虑到货车过驼峰时实施的制动,车轮外侧面磨耗5mm,则轮辋最小宽度应为125mm。
目前铁路货车车轮轮辋宽度为135~140.
轮辋厚度通常指心轮辋厚度。
对正常服役的车轮的判废依据是轮辋剩余厚度,新轮辋厚度与轮辋报废限度之差为轮辋有限磨耗厚度。
轮辋越厚,有效磨耗厚度就越大,但车轮自重也大。
有效磨耗厚度越厚,车轮使用寿命越长,新旧车轮直径差就越大。
货车检修时,为了满足货车之间悬挂要求,经常需要在心盘旁撑等位置增加调平垫板。
如果新旧车轮直径差过大,所需增加的垫板厚度相应的厚,这样心盘螺栓越容易折断,同时也将增加检修工作量。
轮辋质量占车轮质量较大的比例,即轮辋质量在很大程度上决定了车轮质量。
特别是铸钢车轮,由于浇铸工艺原因,轮辋质量越大,就要求辐板越厚,车轮质量将更大。
车轮质量为簧下质量,其质量的增加对轮轨垂向动作用力有较大的影响。
为了提高轮辋硬度以提高其使用寿命,生产中要对车轮踏面进行淬火处理。
由于淬火工艺特性,淬硬深度受到限制。
轮辋越厚,内部硬度越低,耐磨性能越差。
虽然车轮使用寿命随着轮辋厚度的增加而延长,但延长的比例越来越小。
从车轮使用寿命的角度来考虑,轮辋应越厚越好。
但从车轮质量和新旧车轮直径差的角度来考虑,轮辋厚度应越小越好。
轮辋厚度尺寸各有利弊,应根据货车具体使用条件及上述各种影响因素综合确定。
目前铁路货车车轮轮辋厚度主要有50mm和65mm两种。
三、轮毂
车轮和车轴考过盈配合组装在一起,轮毂的主要作用是将车轮牢牢地固定到车轴上,其尺寸主要由轮轴配合所需要的紧固力所决定。
铁路货车车轮轮毂长度名义尺寸均为178mm,轮毂厚度随轴重的不同而变化。
在轮毂长度尺寸和轮轴间配合过盈量一定的情况下,轮毂厚度越厚,车轮质量就越大、轮轴间的紧固力也越大。
合理的轮毂厚度应该是:
在满足轮轴紧固力要求的前提下,厚度尽可能地校,以减轻车轮质量。
四、毂辋距
毂辋距是指轮辋内侧面与轮毂内侧面间的轴向距离,该值与轮对内侧距、车轴两轮座之间的距离有关,因此在选取毂辋距时不能仅从车轮的角度考虑,应根据轮对内侧距与车轴协调考虑。
目前铁路货车车轮该值为68mm。
五、辐板形状
辐板的强度直接关系到行车安全,因此车轮辐板应有足够的强度。
辐板形状对车轮的结构强度和刚度有较大的影响。
较小的径向刚度可使车轮具有较大的弹性,可以改善制动热负荷作用下车轮的应力状态和降低轮轨动作用力,因此辐板的径向刚度应适当地小。
辐板的轴向刚度应尽量大,否则车轮将产生较大的轴向变形。
轴向变形过大会改变轮轨正常接触位置和轮缘角度,影响车辆运行性能,增加爬轨的可能性。
一个好的辐板形状,可以在不增加自重的条件下大幅度地提高车轮的结构强度,改善车轮的刚度。
辐板形状有:
直辐板、S形辐板、波浪形辐板、盆型辐板。
六、轮缘踏面外形
轮缘踏面外形设计时应考虑与轨头外形的配合,理想的轮轨型面配合状态能有效地降低接触应力和磨耗,有助于改善列车通过曲线性能,有效地提高列车失稳的临界速度。
同时设计的新踏面应尽量与磨耗后的形状接近,以降低修正踏面时金属切削量。
轮缘要有一定高度,过低易发生脱轨,若轮缘设计的过高,当踏面磨耗深度较大时轮缘顶部可能触碰钢轨鱼尾板螺栓或鱼尾板肩部。
轮缘高度一般在26~30mm之间。
考虑通过道岔安全,车轮轮径越小,轮缘应越高。
轮缘有防止车轮脱线的功能,为防止低速车轮爬轨和高速车轮跳轨,轮缘外侧面与水平面之间应有足够的轮缘角,一般在60°~70°,过小容易爬轨,不能保证安全,过大使修复外形时切削量增加,且当轮对有冲角时轮缘顶部易与钢轨发生接触。
轮缘踏面形状主要取决于线路情况和列车运行速度,而与车轮本身结构无关。
当运行的线路和列车的速度没有较大变化时,即使车轮结构发生了变化,其踏面形状也无需改变。
通常状况下踏面采用标准形状。
目前铁路货车只有一种轮缘踏面外形,即LM型(磨耗形踏面外形),其轮辋宽度为135mm;由车轮内侧面到踏面上70mm处的点叫基准点;由车轮内侧面向外16mm与轮缘外表面的交点为轮缘顶点;踏面采用R100mm和R500mm及R220mm为半径的三段弧线,圆滑连接成的一条曲线和斜度为1:
8的一段直线所组成的几何图形。
轮缘高度是由过基准点且与车轮内侧面的垂直线到轮缘顶点的距离,标准高度为27mm。
轮缘厚度是由过基准点且与车轮内侧面的垂直线向轮缘顶点方向12mm作一水平线交轮缘内外侧两点之间的距离,标准厚度为32mm。
1.2.3车轮各部分的名称及作用
1.踏面:
车轮与钢轨面向接触的外圆周面,具有一定的斜度。
踏面与轨面在一定的摩擦力下完成滚动运行。
2.轮缘:
车轮内侧面的径向圆周突起部分,称为轮缘。
其作用时为防止轮对出轨,保证货车在直线和曲线上安全运行。
3.轮辋:
车轮具有完整踏面的径向厚度部分,以保证踏面内具有足够的强度,同时也便于加修踏面。
4.轮毂:
车轮中心圆周部分,固定在车轴轮座上,为车轮整个结构的主干与支承。
5.轮毂孔:
用于安装车轴,该孔与车轴轮座部分通过过盈配合组装在一起。
6.辐板:
连接轮辋与轮毂的部分,呈板状者称为辐板,辐板呈曲面状,使车轮具有弹性,贼力在传递时较为缓和。
7.辐板孔:
为了便于加工和吊装轮对而设,每个车轮上有两个。
现在由于用途不大且影响车轮的性能,在S形辐板车轮上予以取消。
第2章轮轴损伤形式
2.1车轴损伤形式
车轴的损伤形式主要有车轴裂纹、车轴碰伤、磨伤、车轴弯曲及磨损、打痕、碰伤、电焊打火凹痕、燃轴造成的轴颈碾长等。
这些故障可能导致切轴事故,而造成车辆脱轨、颠覆事故。
2.1.1车轴裂纹
裂纹:
在工艺过程中金属的连续性破坏而形成的缺陷。
磁粉探伤时,其磁痕特征一般为线形锯齿形,两端呈尖角状,磁粉聚集的图像不规则,但清晰、密集。
发纹:
是由原材料中的微小气孔、针孔、金属和非金属夹杂物等,经锻轧而成的原材料缺陷。
磁粉探伤时,其磁痕特征呈直线或微弯的细线状,磁粉聚集的图像规则,呈细长、平直状。
一、车轴裂纹及折损
车轴裂纹及折损一般分为疲劳折损及一次性断裂两种。
车轴的受力情况非常复杂,在运行中除受很大的垂直力外,还要承受来自钢轨接头的刚性冲击。
车站内部则长期经受交变的动载荷作用。
同时车轮与车轴压配合也给车轴以附加应力,沿车轴纵向还有变化着的水平力作用。
因此车轴内部应力状态是多种应力的综合,所以工作一定时间后,易于产生疲劳裂纹。
车轴裂纹分为纵向裂纹与横向裂纹两种,若裂纹与车轴中心线夹角大于45°时,称为横裂纹。
横裂纹的产生将减小车轴的有效横截面积,对车轴强度的影响最大,车轴折损都是由于横裂纹的深度不断扩展,导致应力上升而引起的。
所以车轴上的横裂纹时危险性极大的一种损伤,是不允许存在的。
根据统计,车轴裂纹大多数发生在轮座上,而且多数在离轮座捏、外侧边缘10~20mm处。
但也有一部分发生在轴颈和轴中央部分。
二、车轴裂纹产生的原因
主要的原因是车轴实际的疲劳极限较车轴钢试样的疲劳限度要低得多。
至于在压装车轮后车轴轮座部分,产生疲劳裂纹特别多,显然是由于在该处疲劳极限显著下降而造成的,一般来讲有以下几方面的原因:
1.采用压配合的轮对。
当车轴压入轮毂孔后,使轮对的形状相当于一个截面突然变化的整体轴,因而在车轴与车轮交界的截面突变处产生高度的应力集中。
2.当车轴压入轮毂孔后,在车轴表面产生很大的接触压应力,这种接触压应力的分布是不均匀的,在轮座接触面两侧的压应力最大,轮座两端内向10~30mm处,此处弯矩最大,且轮毂孔上部有空隙,下部轮座受挤压,在运行中承受弯曲交变应力的作用,因此容易产生裂纹。
3.车轴每转动一周,轮座部的纤维在交变应力作用下交变地产生拉伸和压缩,造成车轴轮座部分与轮毂边缘有微小的滑动摩擦,时间久了在摩擦处形成了磨损。
而车轴在实际使用中,在各种腐蚀介质(如空气、水、油脂和杂物等)的作用下产生了摩擦腐蚀,使摩损表面形成了许多微小的腐蚀坑穴,而成为车轴裂纹疲劳源,使车轴疲劳极限下降,致使过早地出现疲劳裂纹。
4.由于材质内部缺陷,或设计、工艺及运用上的不适当所引起的。
5.轴颈表面进行机械加工时,轴颈与防尘板座交界处、防尘板座与轮座交界处的圆弧过渡不良,圆弧半径太小或留有刀痕,会使应力集中情况加重,因而降低车轴的疲劳极限,导致裂纹的产生。
6.违章电焊、碰伤轴身及电焊灯火痕迹等也都会降低车轴疲劳极限,以致先期出现裂纹。
7.滚动轴承车轴由于滚动轴承的损坏,出现轴承内圈崩裂、滚子破碎等故障,就会造成轴承激热,车轴折断。
2.1.2车轴磨损
1.轴颈磨损:
滚动轴承的轴颈,由于滚动轴承故障造成内圈松弛,内圈与车轴轴颈部产生了滑动摩擦造成轴颈磨损。
2.滚动轴承车轴的轴端螺纹部分,经过长时间的运用会因磨耗而失去紧固作用。
防尘板座部分,由于组装防尘轴承后档不当,易于产生擦伤、凹痕及纵向划痕。
3.轴身擦伤:
由于制动拉杆、杠杆等组装不良与车轴接触造成轴身磨伤。
磨伤过甚时,车轴磨伤处会引起应力集中,导致车轴裂纹。
4.车轴磕碰伤:
轮对在运用和运输时轴身有可能被磕碰打击而损伤。
5.电焊打火:
在货车焊修时,有时也会发生因电焊地线接的不当,造成电流通过车轴将轴身打伤。
2.1.3车轴弯曲
车轴弯曲的主要原因是由于货车脱轨时,使车轴受到剧烈的振动,或在组装轮对时操作不当而造成的。
货车脱轨时应退缷轴承,检查轴颈弯曲度,以顶针孔为基准,旋转一周,测量后肩处半径尺寸的变化量,其值小于0.15mm时可以使用。
沿车轮圆周测量轮对内侧距离,如果任意两处相差超过3mm,则车轴弯曲过限,要更换轮对。
车轴加修时,可将弯曲处旋除,旋除后的轴身尺寸允许比原型公称尺寸减少4mm。
2.2车轮损伤形式
车轮的损伤形式有车轮踏面剥离、擦伤、局部凹陷、碾宽、圆周磨耗超限及裂纹、缺损、粘有熔化金属;轮缘厚度超限或轮缘垂直磨耗超限,轮缘缺损、裂纹、碾堆:
车轮裂纹、辐板孔、轮毂裂纹。
2.2.1踏面剥离
一、损伤性质
车轮是货车的重要走形部件,在使用中其受力状态复杂、服役条件恶劣及其材质或制造上的缺陷等会产生各种损伤,而且多发生在车轮的踏面,最常见的为踏面剥离。
在运用中车轮踏面整个圆周或局部出现不规则网状裂纹、龟纹状裂纹或层状金属剥落,从长期研究和机理分析来看,车轮剥离主要分为制动剥离、接触疲劳剥离、擦伤剥离这三种;从材料失效机理上主要可以归结为两类:
一类是由交变接触应力引起的接触疲劳损伤,另一类是由摩擦热循环引起的热疲劳损伤。
二、产生原因
1.制动剥离时由于在不合适的制动条件下,闸瓦与车轮接触部位产生高热导致车轮表面金属相变等,踏面制动时,轮瓦接触部位的摩擦产生高热使踏面局部瞬间加热到相变点温度以上,随后冷却时形成所谓热机械作用的马氏体白层,脆硬的马氏体白层在轮轨接触应力、热应力和组织应力作用下极易碎裂和薄片状脱落,在随后轮轨接触应力作用下,将发展成为大面积剥落掉块。
车轮踏面制动剥离前所产生的热裂纹起源于热影响层的马氏体白层处。
由制动产生的热影响层和热应力是指踏面局部金属受制动摩擦热作用,引起金相组织和残余应力状态变化的物理现象。
热影响层的深度取决于最恶劣的一次制动热输入的影响,在相同的制动热影响作用下,热影响层的厚度和热应力只取决于摩擦热温度及其持续时间和温度梯度。
钢的化学成分至影响热影响层处马氏体转变的厚度和硬度,不同硬度和厚度的马氏体转变层,在轮轨接触应力和热应力作用下产生裂纹的倾向无明显差别。
马氏体白层硬度很高,时萌生裂纹的主要原因,裂纹的扩展速率和扩展法相与车轮、轮箍的残余应力状态有关。
轮辋经热处理后沿轮辋圆周方向将产生压缩应力,周向残余压应力可以减缓或抑制踏面上疲劳裂纹沿径向扩展。
因此,当车轮踏面出现较浅的热影响层时,轮辋仍为残余压应力状态,产生于马氏体白层处的裂纹的扩展主要受轮轨接触应力控制,疲劳裂纹扩展方向逐渐倾斜和转向到平行于踏面,导致形成剥离掉块损伤。
2.接触疲劳剥离时由于轮轨接触应力累计到应变所致,通常与车轮硬度、强度有关,车轮钢的接触疲劳抗力主要取决于钢的强度和夹杂物的含量和大小。
GB8601—1988车轮标准中,规定了普碳车轮踏面下30mm处的抗拉强度为910~1155N/mm2。
实物车轮踏面接触应力作用部位的抗拉强度一般约为1000N/mm2,轮箍的抗拉强度略高一些,屈服强度ss约为600N/mm2,其剪切应力屈服强度ts约为ss的0.7倍,此时的t45max是位于踏面下3~4mm部位处。
但如列车在小半径曲线上行驶时,将使车轮踏面表层金属产生严重的塑性变形,致使珠光体层片碎裂而形成微孔洞,并由此萌生疲劳裂纹,疲劳裂纹源位于踏面表层并呈多源特征,当应力虚幻达到一定周期后,则裂纹沿与踏面承一倾角(约45°)向轮辋内部扩展,最终会在踏面发展成疲劳掉块形成剥离。
3.擦伤剥离是由于车轮与钢轨之间出现局部摩擦或滑动摩擦,摩擦高热导致车轮表面金属相变,出现硬而脆的马氏体,并在随后轮轨接触作用力下该部位剥落,运行中的车轮当紧急制动或制动力过大时,都将会产生抱闸,由于列车仍具有一定的惯性向前运动,当惯性大于轮轨黏着力时,就会出现轮轨滑行或蠕滑现象,因为产生不同程度的摩擦热,这种摩擦热的温度很高,极易达到相变点以上,即高温奥氏体相,在迅速