卧式单面多轴钻孔组合机床液压系统的设计.docx
《卧式单面多轴钻孔组合机床液压系统的设计.docx》由会员分享,可在线阅读,更多相关《卧式单面多轴钻孔组合机床液压系统的设计.docx(18页珍藏版)》请在冰豆网上搜索。
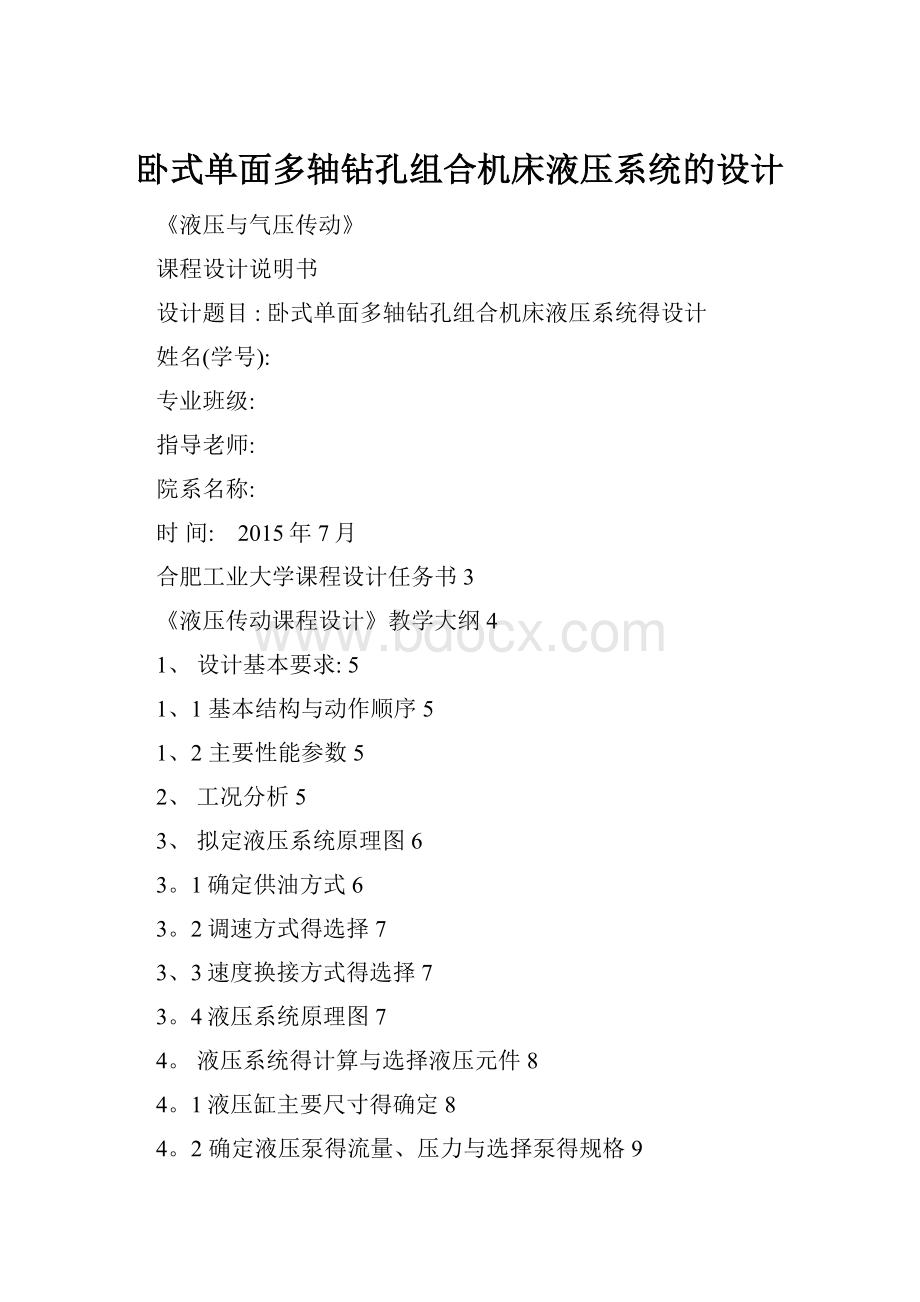
卧式单面多轴钻孔组合机床液压系统的设计
《液压与气压传动》
课程设计说明书
设计题目:
卧式单面多轴钻孔组合机床液压系统得设计
姓名(学号):
专业班级:
指导老师:
院系名称:
时间:
2015年7月
合肥工业大学课程设计任务书3
《液压传动课程设计》教学大纲4
1、设计基本要求:
5
1、1基本结构与动作顺序5
1、2主要性能参数5
2、工况分析5
3、拟定液压系统原理图6
3。
1确定供油方式6
3。
2调速方式得选择7
3、3速度换接方式得选择7
3。
4液压系统原理图7
4。
液压系统得计算与选择液压元件8
4。
1液压缸主要尺寸得确定8
4。
2确定液压泵得流量、压力与选择泵得规格9
4。
3液压阀得选择10
4、4确定管道尺寸10
4。
5液压油箱容积得确定11
5、液压系统得参数计算11
5。
1液压系统得参数计算11
5、2确定液压缸得主要结构尺寸11
5。
3计算液压缸各工作阶段得工作压力、流量与功率12
5。
4液压泵得参数计算12
5。
5电动机得选择13
6。
其它尺寸得确定14
6。
1油管得选择14
6。
2油箱容积得确定15
7。
验算液压系统性能15
7。
1压力损失得验算及泵压力得调整15
7。
2快退时得压力损失验算及大流量泵卸载压力得调整15
7、3液压系统得发热与温升验算17
8。
课程设计总结18
9、教材及参考书19
设计
题目
卧式单面多轴钻孔组合机床液压系统得设计
成绩
主
要
内
容
单面多轴钻孔组合机床,动力滑台得工作循环就是:
快进——工进-—快退-—停止。
液压系统得主要性能参数要求如下,轴向切削力为24000N;滑台移动部件总质量为510kg;加、减速时间为0、2s;采用平导轨,静摩擦系数为0、2,动摩擦系数为0。
1,;快进行程为200mm,工进行程为100mm,快进与快退速度相等,均为3。
5m/min,工进速度为30~40mm/min。
工作时要求运动平稳,且可随时停止运动、试设计动力滑台得液压系统。
指
导
教
师
意
见
签名:
200年月日
《液压传动课程设计》教学大纲
一、课程性质与任务
(一)课程性质
《液压传动课程设计》就是学生学习液压与气压传动课程后进行得一个十分重要得实践性环节。
(二)课程任务
培养学生综合运用液压与气压传动课程得理论知识与生产实际知识分析、解决工程实际问题得能力,以进一步巩固、深化、扩展本课程所学到得理论知识、
通过设计基本技能得训练,使学生掌握液压与气压传动系统设计得一般方法与步骤,为以后得毕业设计乃至实际工程设计奠定必要得基础。
二、课程基本要求
(一)掌握液压与气动系统设计得基本方法与步骤;
(二)能查阅与液压与气动有关得国家标准、规范、手册、图册等技术资料;
(三)掌握液压与气动元件得结构、工作原理与性能,并能合理地选用;
(三)掌握液压与气动典型基本回路得工作原理与特点,并能合理地应用;
(四)能正确地绘制与阅读液压与气动系统图;
(五)能根据液压与气动系统图与各个元件得标准设计液压与气动系统得集成块;
三、课程内容
(一)基本内容:
1、设计液压与气动系统得工作原理图;
2、设计并绘制液压与气动系统得集成块;
(二)基本要求:
1、掌握对液压与气动系统得集成块设计
2、能根据液压与气动系统图与各个元件得标准设计液压与气动系统得集成块;
(三)设计工作量:
1、液压与气动系统、集成块装配图各一张,2×A1
2、液压与气动系统、集成块设计说明书一份,5000字。
四、课程与其它课程得关系
本课程为专业基础课,为以后得毕业设计乃至实际工程设计奠定必要得基础。
《液压传动》课程设计说明书
1。
设计基本要求:
1、1基本结构与动作顺序
卧式单面多轴组合机床主要由工作台、床身、单面动力滑台、定位夹紧机构等组成,加工对象为铸铁变速箱体,能实现自动定位夹紧、加工等功能、工作循环如下:
工件输送至工作台自动定位夹紧动力滑台快进工进快退夹紧松开定位退回工件送出。
(其中工作输送系统不考虑)
1。
2主要性能参数
1.轴向切削力Ft=24000N;
2.滑台移动部件质量m=510kg;
3.加减速时间∆t=0、2s;
4.静摩擦系数fs=0。
2,动摩擦系数fd=0、1,采用平导轨;
5.快进行程l1=200mm;工进行程l2=100mm,工进速度30~50mm/min,快进与快退速度均为3。
5m/min;
6.工作台要求运动平稳,但可以随时停止运动,两动力滑台完成各自循环时互不干扰,夹紧可调并能保证。
2、工况分析
首先根据已知条件,绘制运动部件得速度循环图,如图1。
1所示,然后计算各阶段得外负载并绘制负载图。
液压缸所受外负载F包括三种类型,即
F=Fw+Ff+Fa
FW为工作负载,对于金属切削机床来说,即为沿活塞运动方向得切削力,在本例中为30000N;
Fa——-运动部件速度变化时得惯性负载;
Ff---导轨摩擦阻力负载,启动时为静摩擦阻力,启动后为动摩擦阻力,对于平导轨可出下式求得
Ff=f(G+FRn)
G-——运动部件动力;
FRn-——垂直于导轨得工作负载,事例中为零
f———导轨摩擦系数,本例中取静摩擦系数0。
2,动摩擦系数0、1、求得:
FfS=0。
2×11000N=2200N
Ffa=0、1×11000N=1100N
上式中Ffs为静摩擦阻力,Ffa为动摩擦阻力、
Fa=(G/g)×(△v/△t)
g-—-重力加速度;
△t———加速度或减速度,一般△t=0。
01~0、5s
△v—△t时间内得速度变化量、在本例中
Fa=(11000/9。
8)×(4。
5/0、1×60)=842N
根据上述计算结果,列出各工作阶段所受得外负载(见表1、1),并画出如图1。
1所示得负载循环图
Fa=(G/g)×(△v/△t)
图1。
1速度与负载循环图
表1、1工作阶段所受得外负载
工作循环
外负载F(N)
工作循环
外负载F(N)
启动、加速
F=Ffs+Fa
3042
工进
F=Ffs+Fw
31100
快进
F=Ffa
1100
快退
F=Ffa
1100
3、拟定液压系统原理图
3、1确定供油方式
该机床在工作进给时负载不就是很大,速度较低。
在快进、快退时负载较小,速度较高。
现采用定量泵与溢流阀共有、
3。
2调速方式得选择
在中小型专用机床得液压系统中,进给速度得控制一般采用节流阀或调速阀、根据钻削类专用机床工作时对低速性能与速度负载特性都有一定要求得特点,决定采用单向调速阀回油路调速。
3、3速度换接方式得选择
本系统采用电磁阀得快慢速换接回路,它得特点就是结构简单,调节行程比较方便,阀得安装也比较容易,但速度换接平稳性差。
若要提高系统换接得平稳性,则可改用行程阀切换得速度换接回路。
3。
4液压系统原理图
4、液压系统得计算与选择液压元件
4。
1液压缸主要尺寸得确定
4、1。
1工作压力p得确定。
工作压力p可确定根据负载大小及机器得类型来初步确定,表1。
1取液压缸工作压力为4MPa。
4、1、2计算液压缸内径D与活塞杆直径d。
有负载图知最大负载F为31100N,按表1。
2可取P2为0。
5Mpa,cm为0、95,考虑到快进、快退速度相等,取d/D为0、7。
将上数据代入式可得
D=
==105mm
根据指导书表2、1,将液压缸内径圆整为标准系列直径D=110mm;活塞杆直径d,按d/D=0、7及表2、2活塞杆直径系列取d=80mm。
按工作要求夹紧力由两个夹紧缸提供,考虑到夹紧力得稳定,夹紧缸得工作压力应低于进给液压缸得工作压力,先去夹紧缸得工作压力为3。
5MPa,回油背压力为零,为0。
95,可得
D==33.9mm
按表2。
1及2、2液压缸与活塞杆得尺系列,取夹紧液压缸得D与d分别为40mm及28mm、按最低工进速度验算液压缸得最小稳定速度,由式可得
A>=cm2=25cm2
本例中调速阀就是安装在回油路上,故液压缸节流腔有效工作面积应选取液压缸由杆腔得实际面积,即
A=cm2=45cm2
可见上述不等式能满足,液压缸能达到所需低速。
4、1、3计算在各工作阶段液压缸所需得流量
q快进===22。
6×10-3m3/min=22.6L/min
q工进==0、112×0、1=0、95×10—3m3/min=0。
95L/min
q快退===20×10-3m3/min=20L/min
q夹===1。
51×10-3m3/min=1.51L/min
4、2确定液压泵得流量、压力与选择泵得规格
4。
2、1泵得工作压力得确定
考虑到正常工作中进油管路有一定得压力损失,所以泵得工作压力为
Pp=P1+∑△p
PP—液压泵最大工作压力;
P1—执行元件最大工作压力
∑△p-进油管路中得压力损失,初算时简单系统可取0、2~0。
5MPa,复杂系统取0。
5~1。
5MPa,本题取0。
5MPa。
pP=p1+∑△P=(4+0。
5)=4、5MPa
上述计算所得得Pp就是系统得静态压力,考虑到系统在各种工况得过渡阶段出现得动态压力往往超过静态压力、另外考虑到一定得压力贮备量,并确保泵得寿命,因此选泵得额定压力Pn应满足Pn≥(1、25~1、6)Pp。
中低压系统取小值,高压系统取大值、在本题中Pn=1。
3Pp=5、85MPa。
4。
2。
2泵得流量确定
液压泵得最大流量应为
qp≥KL(∑q)min
qp—液压泵得最大流量;
(∑q)min同时动作得各执行元件所需流量之与得最大值。
如果这时溢流阀正进行工作,尚须加溢流阀得最小溢流量2~3L/min;
KL—系统泄露系数,一般取KL=1、1~1。
3,现取KL=1、2
qp≥KL(∑q)min=1。
2×45L/min=54L/min
4、2。
3选择液压泵得规格
根据以上算得得qp与qp,再查阅有关手册,现选用YBX—16限压式变量叶片泵,该泵得基本参数为:
每转排量16mL/r,泵得额定压力6。
3MPa,电动机转速1450r/min,容积效率0。
85,总效率0、7、
4、3液压阀得选择
本液压系统可采用力士乐系统或GE系列得阀、方案一:
控制液压缸部分选用力士乐系列得阀,其夹紧部分选用叠加阀。
方案二:
均选用GE系列阀。
根据所拟定得液压系统图,按通过各元件得最大流量来选择液压元件得规格。
选定得液压元件如表所示:
液压元件明细表
序号
元件名称
通过流量/L·min-1
型号
1
过滤器
24
XU—B32×100
2
定量叶片泵
24
YBX-16
3
压力表
KF3-EA10B
4
三位四通电磁阀
20
34EF30—E10B
5
二位三通电磁阀
20
23EF3B-E10B
6
单向调速阀
20
AQF3-E10B
7
先导溢流阀
9。
4
YF3-10BC
8
压力表
KF3-EA10B
9
单向阀
9。
4
AF3-EA10B
4、4确定管道尺寸
油管内径尺寸一般可参照选用得液压元件接口尺寸而定,也可按管路允许流速进行计算。
本系统主油路流量为差动时流量q=40L/min,压油管得允许流速取u=4m/s,内径d为
d=4、6=4、6=15.4mm
若系统主油路流量按快退时取q=20L/min,则可算得油管内径d=10.3mm。
综合诸因素,现取油管得内径d为12mm。
吸油管同样可按上式计算(q=24L/min、v=1.5m/s),现参照YBX-16变量泵吸油口连接尺寸,取吸油管内径d为28mm。
4、5液压油箱容积得确定
本题为中压液压系统,液压油箱有效容积按泵得流量得5~7倍来确定,现选用容量为400L得油箱。
5。
液压系统得参数计算
5、1液压系统得参数计算
5。
1。
1、初选液压缸得工作压力
参考同类型组合机床,初定液压缸得工作压力为=40*Pa
5。
2确定液压缸得主要结构尺寸
本例要求动力滑台得快进、快退速度相等,现采用活塞杆固定得单杠式液压缸。
快进时采用差动联接,并取无杆腔有效面积等于有杆腔有效面积得两倍,即=2。
为了防止在钻孔钻通时滑台突然向前冲,在回油路中装有背压阀,按表8—1,初选背压Pa、
由表1—1可知最大负载为工进阶段得负载F=25789N,按此计算则
液压缸直径
由=2可知活塞杆直径
d=0。
707D=0。
707*9、55cm=6、75cm
按GB/T2348—1993将所计算得D与d值分别圆整到相近得标准直径,以便采用标准得密封装置、圆整后得
D=10cmd=7cm
按标准直径算出
按最低工进速度验算液压缸尺寸,查产品样本,调速阀最小稳定流量,因工进速度v=0。
05m/min为最小速度,则由式
本例=6。
36》10,满足最低速度得要求。
5、3计算液压缸各工作阶段得工作压力、流量与功率
根据液压缸得负载图与速度图以及液压缸得有效面积,可以算出液压缸工作过程各阶段得压力、流量与功率,在计算工进时背压按代入,快退时背压按代入计算公式与计算结果列于下表中、
表5。
1液压缸所需得实际流量、压力与功率
工作循环
计算公式
负载F
进油压力
回油压力
所需流量
输入功率P
N
L/min
kW
差动快进
526
13、5
0。
146
工进
25789
0。
314
0。
019
快退
526
14
0、266
5、4液压泵得参数计算
由表二可知工进阶段液压缸压力最大,若取进油路总压力损失,压力继电器可靠动作需要压力差为,则液压泵最高工作压力可按式算出
因此泵得额定压力可取1、2546。
9Pa=59Pa、
由表二可知,工进时所需要流量最小就是0、32L/min,设溢流阀最小溢流量为2、5L/min,则小流量泵得流量应为,快进快退时液压缸所需得最大流量就是14L/min,则泵得总流量为。
即大流量泵得流量。
根据上面计算得压力与流量,查产品样本,选用YB-4/12型得双联叶片泵,该泵额定压力为6。
3MPa,额定转速960r/min。
5、5电动机得选择
系统为双泵供油系统,其中小泵1得流量,大泵流量。
差动快进、快退时两个泵同时向系统供油;工进时,小泵向系统供油,大泵卸载。
下面分别计算三个阶段所需要得电动机功率P。
5。
5、1。
差动快进
差动快进时,大泵2得出口压力油经单向阀11后与小泵1汇合,然后经单向阀2,三位五通阀4进入液压缸大腔,大腔得压力,查样本可知,小泵得出口压力损失,大泵出口到小泵出口得压力损失、于就是计算可得小泵得出口压力(总效率=0。
5),大泵出口压力(总效率=0。
5)。
电动机效率
5、5。
2工进
考虑到调速阀所需最小压力差、压力继电器可靠动作需要压力差、因此工进时小泵得出口压力、而大泵得卸载压力取。
(小泵得总效率=0、565,大泵得总效率=0。
3)、
电动机功率
5、5、3。
快退
类似差动快进分析知:
小泵得出口压力(总效率=0。
5);大泵出口压力(总效率=0。
5)。
电动机功率
综合比较,快退时所需功率最大。
据此查样本选用Y90L—6异步电动机。
表5、2Y90L—6异步电动机主要参数表
功率KW
额定转速r/min
电流A
效率%
净重kg
1。
1
910
3、15
73、5
25
6、其它尺寸得确定
6、1油管得选择
根据选定得液压阀得连接油口尺寸确定管道尺寸。
液压缸得进、出油管按输入、排出得最大流量来计算、由于本系统液压缸差动连接快进快退时,油管内通油量最大,其实际流量为泵得额定流量得两倍达32L/min,则液压缸进、出油管直径d按产品样本,选用内径为15mm,外径为19mm得10号冷拔钢管。
6、2油箱容积得确定
中压系统得油箱容积一般取液压泵额定流量得5~7倍,本设计取6倍,故油箱容积为
7。
验算液压系统性能
7、1压力损失得验算及泵压力得调整
7。
1。
1。
压力损失得验算及泵压力得调整
工进时管路中得流量仅为0。
314L/min,因此流速很小,所以沿程压力损失与局部损失都非常小,可以忽略不计。
这时进油路上仅考虑调速阀得压力损失,回油路上只有背压阀得压力损失,小流量泵得调整压力应等于工进时液压缸得工作压力加上进油路压差,并考虑压力继电器动作需要,则
即小流量泵得溢流阀12应按此压力调整。
7。
2快退时得压力损失验算及大流量泵卸载压力得调整
因快退时,液压缸无杆腔得回游量就是进油量得两倍,其压力损失比快进时要大,因此必须计算快退时得进油路与回油路得压力损失,以便确定大流量泵得卸载压力。
已知:
快退时进油管与回油管长度均为l=1。
8m,油管直径d=15m,通过得流量为进油路=16L/min=0、267,回油路=32L/min=0。
534、液压系统选用N32号液压油,考虑最低工作温度为15摄氏度,由手册查出此时油得运动粘度v=1、5st=1、5,油得密度,液压系统元件采用集成块式得配置形式、、
式中v——平均流速(m/s)
d——油管内径(m)
——油得运动粘度()
q——通过得流量()
则进油路中液流得雷诺数为
回油路中液流得雷诺数为
由上可知,进回油路中得流动都就是层流、
(2)沿程压力损失由式(1—37)可算出进油路与回油路得压力损失、
在进油路上,流速则压力损失为
在回油路上,流速为进油路流速得两倍即v=3、02m/s,则压力损失为
(3)局部压力损失由于采用了集成块式得液压装置,所以只考虑阀类元件与集成块内油路得压力损失。
通过各阀得局部损失按式(1-39)计算,结果列于下表
部分阀类元件局部压力损失
元件名称
额定流量
实际通过流量
额定压力损失
实际压力损失
单向阀2
25
16
2
0。
82
三位五通电磁阀
63
16/32
4
0、26/1。
03
二位二通电磁阀
63
32
4
1、03
单向阀
25
12
2
0。
46
若去集成块进油路得压力损失,回油路压力损失为,则进油路与回油路总得压力损失为
查表一得快退时液压缸负载F=526N;则快退时液压缸得工作压力为
按式(8—5)可算出快退时泵得工作压力为
因此,大流量泵卸载阀10得调整压力应大于
从以上验算结果可以瞧出,各种工况下得实际压力损失都小于初选得压力损失值,而且比较接近,说明液压系统得油路结构、元件得参数就是合理得,满足要求。
7、3液压系统得发热与温升验算
在整个工作循环中,工进阶段所占用得时间最长,所以系统得发热主要就是工进阶段造成得,故按工进工况验算系统温升。
工进时液压泵得输入功率如前面计算
工进时液压缸得输出功率
系统总得发热功率为:
已知油箱容积V=112L=,则按式(8-12)油箱近似散热面积A为
假定通风良好,取油箱散热系数,则利用式(8-11)可得油液温升为
设环境温度,则热平衡温度为
所以油箱散热基本可达要求。
8。
课程设计总结
9。
教材及参考书
[1]杨培元朱福元主编《液压系统设计简明手册》第1版,北京机械工业出版社,1994
[2]曾亿山主编《液压与气压传动》第1版,合肥合肥工业大学出版社,2008
[3]左健民主编《液压与气压传动》第2版,北京机械工业出版社,2001
[4]姜继海主编《液压与气压传动》第1版,北京高等教育出版社,2002
[5]上海市业余工业大学编著《液压传动与传动》,上海上海科学技术工业出版社,1981
[6]路甬祥主编《液压气动技术手册》第1版,北京机械工业出版社,2001
[7]雷天觉主编新编液压工程手册北京理工大学出版社1998
[8]徐灏主编机械设计手册第5卷(第2版)北京机械工业出版社,2001