章水电制氢控制系统.docx
《章水电制氢控制系统.docx》由会员分享,可在线阅读,更多相关《章水电制氢控制系统.docx(28页珍藏版)》请在冰豆网上搜索。
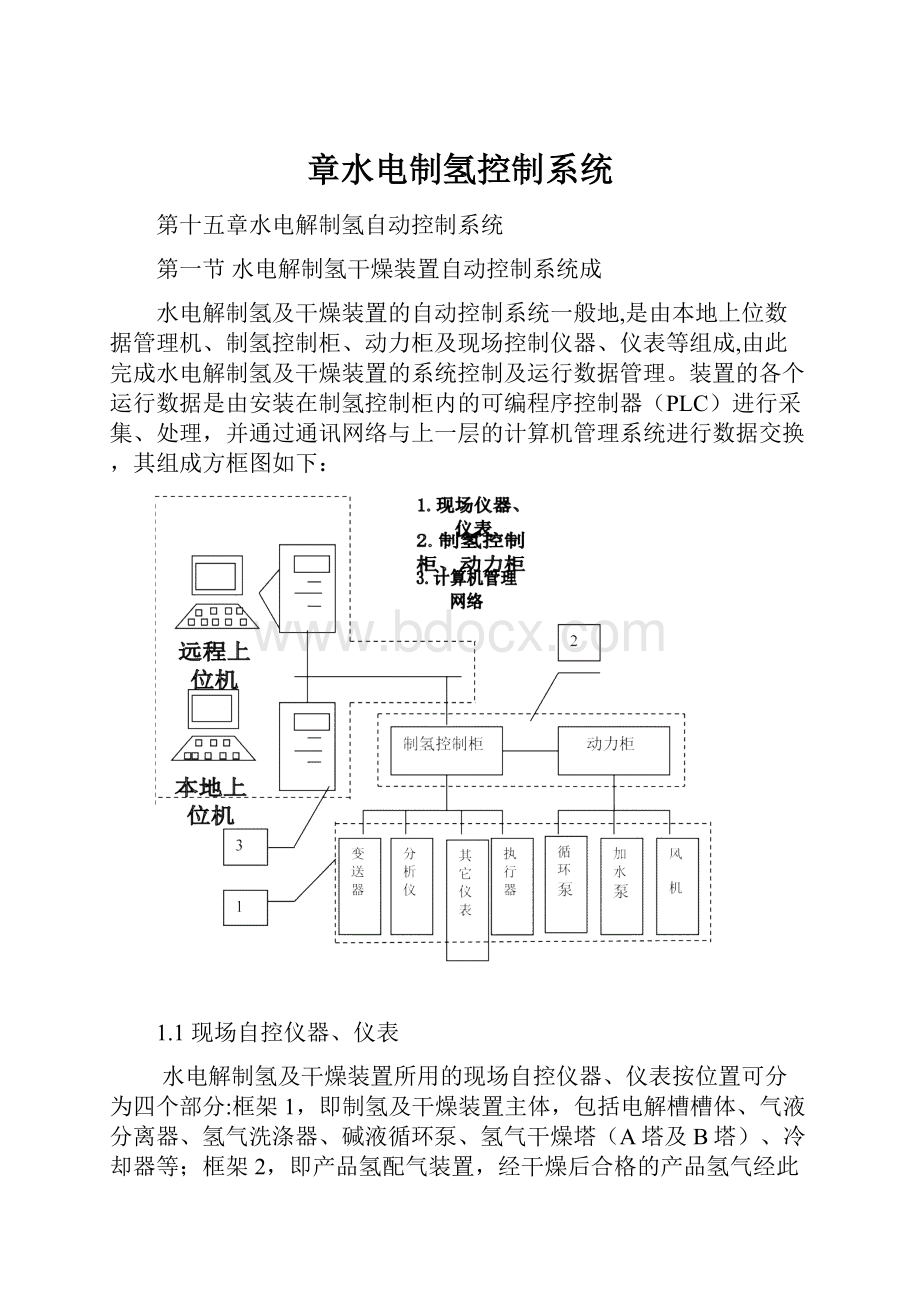
章水电制氢控制系统
第十五章水电解制氢自动控制系统
第一节水电解制氢干燥装置自动控制系统成
水电解制氢及干燥装置的自动控制系统一般地,是由本地上位数据管理机、制氢控制柜、动力柜及现场控制仪器、仪表等组成,由此完成水电解制氢及干燥装置的系统控制及运行数据管理。
装置的各个运行数据是由安装在制氢控制柜内的可编程序控制器(PLC)进行采集、处理,并通过通讯网络与上一层的计算机管理系统进行数据交换,其组成方框图如下:
1.1现场自控仪器、仪表
水电解制氢及干燥装置所用的现场自控仪器、仪表按位置可分为四个部分:
框架1,即制氢及干燥装置主体,包括电解槽槽体、气液分离器、氢气洗涤器、碱液循环泵、氢气干燥塔(A塔及B塔)、冷却器等;框架2,即产品氢配气装置,经干燥后合格的产品氢气经此装置进入氢气储罐或向发电机组补氢;框架3,包括原料水箱、碱液箱及系统加水泵;氢气储罐等。
(1)框架1:
本部分的自控仪器、仪表主要有以下四类:
●变送器:
包括压力变送器、差压变送器(氢液位变送器及氧液位变送器)、铂电阻等。
装置的工作压力经压力变送器后变成4~20mA的电信号传送到制氢控制柜;两套差压变送器分别把氢气液分离器中的氢液位及氧气液中的分离器中的氧液位变换成标准的
4~20mA信号传送到制氢控制柜;铂电阻共有五支,一支用来测量装置运行时循环碱液的温度。
两支分别用来测量干燥A塔和干燥B塔的上部温度,还有两支分别用来测量干燥A塔和干燥B塔的上部温度信号全部送入制氢控制柜。
●执行器:
包括有三个气动薄膜调节阀及七个气动球阀。
●检测仪表:
包括氢中氧分析仪、氧中氢分析仪及氢气露点仪等。
●防爆电接点压力表或压力开关:
一般设置了两块压力表,其中一块用来检测装置运行时的氢阀后压力,当氢阀后压力超过了报警设定值时,氢阀后压力超限报警信号即送入制氢控制柜内;另一块作用是,当自动控制系统失灵时,用来检测装置运行时的系统压力,并由此发出联锁信号直接传送给整流柜,切断整流柜的输出电流,起到二次保护的作用。
(2)框架2:
框架2上的自控仪器、仪表及执行器机构视不同的要求进行的配置:
当要求自动充罐功能且氢气储罐进行选择时,则对应每一个氢气储罐,此框架上安装一个气动球阀及一个压力变送器;当要求具有自动向发电机组自动补氢功能时,则在每一个补氢管路上增加一个气动球阀,补氢母管上安装一套压力变送器。
(3)框架3:
框架3上的自控仪器、仪表及执行机构视不同的要求进行不同的配置:
当要求具有自动对原料水箱进行补水功能时,则在原料水箱的进水管道上安装一个气动球阀或防爆电磁阀用来控制进水;在原料水箱上安装一套差压变送器用来把水箱液位信号变换成标准的4~20mA信号传送给制氢控制柜。
1.2制氢控制柜、动力柜:
制氢控制柜是制氢及干燥装置自动控制系统的核心部分,负责整个装置的安全、稳定、可靠运行,其组成可以分为以下几个部分:
(1)可编程序控制器:
可编程序控制器(PLC)是完成制氢及干燥装置自动控制功能的核心器件,装置的工作压力调节、运行温度的控制及氢位的平衡调节,干燥单元的工作状态选择、系统报警和联锁及相位处理等均由PLC来完成;其主要选型为美国AB公司的SLC500系列、德国Siemens公司的S7—300系列及美国Schneider公司的ModiconQuantun系列,亦可根据用户要求选用其它型号的PLC。
有关不同型号的可编程序控制器的详细说明,请参见各自的使用说明书。
(2)控制监测仪表:
主要包括控制仪表如XMT—7002U型数字显示调节仪和XMT—7602型数字显示调节仪,用于显示和控制干燥A塔和干燥B塔运行情况;显示仪表如氢中氧分析仪、氧中氢分析仪及氢气露点仪等,分别显示制氢装置运行时氢、氧气体纯度及湿度。
其可根据用户要求采用不同的型号。
(3)隔离栅:
由于制氢及干燥装置处于氢气环境下,因而对防爆提出了一定的要求,所有从位于危险区的仪器、仪表送入制氢控制柜的电型号在处理之前先经过隔离栅隔离,然后再进入制氢控制柜内部,这样就能满足相应的防爆要求。
(4)电流传感器:
整流柜输出到电解槽的电解电流在整流柜内经互感器线圈及附属装置变换0~0.5A的电信号后,传送至制氢控制柜内,经电流传感器变送后成为标准的1~5V电信号送入可编程序控制器,由可编程序控制器得输出的整流给定信号4~20
mA经电流传感器变成1~10V的电压信号传送至整流柜,作为整流柜的自动给定信号控制其输出到电解槽的电解电流大小。
(5)电气转换器:
主要采用EPC—1110OG/1的电气转换器,PLC的模拟量输出模块(AO)输出的4~20mA标准信号经电气转换器后变成0.02~0.10Mpa的标准气动信号去驱动现场气动薄膜调节阀。
(6)电磁阀:
用来驱动现场的气动球阀。
(7)空气过滤减压器:
空气过滤减压器主要用来对仪表气源进行过滤和减压,主要包括有QFH—111型的空气过滤器,将气源压力减至0.14Mpa,为三个电气转换器提供合格气源;QFH—261型的空气过滤减压器,将气源压力减至0.35~0.45Mpa,为电磁阀提供合格气源。
(8)固态继电器板:
固态继电器板的主要作用是将PLC数字量输出模块(DO)输出的24VDC开关量信号转换成220VAC开关量信号去驱动电磁阀,或者为其它设备提供无源接点。
(9)其它:
制氢控制柜内的其它低压电器包括信号灯、按钮开关、24VDC稳压线性电源等。
1.3上位数据管理机:
CNDQ系列制氢及干燥装置自动控制系统中的上位数据管理机一般地选用工业用PC机,其基本配置应满足MicrosoftWindowsNT4.0的运行要求,上位机的系统监控软件根据PLC的选型不同可选用不同的开发软件,通常为RSView、FIX或Intouch等。
上位数据管理机的运行参数以及发布系统的操作命令等。
有关上位机的系统监控软件操作说明,、详见有关内容。
第二节水电解制氢及干燥装置自动控制原理
水电解制氢及干燥装置的自动控制系统可以分为两部分:
即水电解制氢单元的自动控制及氢气干燥单元的自动控制,两部分的自动控制既相互独立,又互有关系,组成一个有机的自动控制系统。
2.1水电解制氢单元
水电解制氢单元部分的自动控制任务是在装置运行时,对系统压力,温度进行自动调节及控制,保持系统压力及温度的稳定;使氢,氧液位始终保持平衡;可按照操作人员要求自动进行整流的电流给定;在装置运行时根据一定的条件能对装置加水进行自动控制;能对水电解后产生的氢、氧气体纯度进行在线分析,并根据气体纯度自动判断是否使氢气进入下一工艺流程;当装置进行异常时及时发出报警信号,如果装置运行时的主要受监控参数超出规定的极限值时,自动发出联锁信号切断整流柜输出直流电流,使电解槽停止工作。
本自动控制系统还设置了槽压的二次保护功能,即当自动控制系统失灵时,槽压的超上限信号通过坊爆电接点压力表或压力开关直接输出至整流柜,切断整流柜供电电源,从而保障装置的安全运行。
2.1.1槽压调节控制系统:
装置的槽压调节控制系统如图2所示。
系统压力(0—4Mpa)经压力变送器转换后成4~20mA的标准电信号,送入制氢控制柜,经隔离栅隔离后输入PLC的模拟量输入模块(AI),在PLC中与设定的系统工作压力进行比较,应用PID酸法算法进行运算得出结果,并将此结果通过PLC的模拟量输出模块输出一个标准的4~20mA信号,经电气转换后转换成0.02~0.10Mpa的标准信号,控制调节槽压的气动薄膜调节阀
(氧阀)开度的大小,使系统运行时的槽压稳定在设定值。
例如,当槽压高于设定值时,PID运算的结果将使氧阀的开度增大,致使槽压适当升高并与设定值基本保持一致。
为使装置在非常状况下(如出现停电、停气源异常情况)下使氢、氧液位发生较大、较快的偏差,出于安全考虑,氧阀选用气开式薄膜调节阀。
图2槽压调节及控制系统方框图
当槽压在系统运行时超过了报警上限值(HI)时,PLC发出声光报警,当超过了联锁上限值(HiHi)时,PLC不仅发出声光报警,而且输出联锁信号至整流柜一次联锁回路,切断整流柜输出电流
当自动控制系统失灵时,若槽压上升达到危险值时,由防爆电接点压力表或压力开关输出无源接点信号进入整流柜二次联锁回路切断整流柜供电电源,从而切断整流柜输出电流,这即上槽压的二次保护功能。
槽压调节控制系统中涉及到的参数如下:
1.运行槽压设定值(SP1):
SP1是整个装置的工作压力设定值,一般设定值在装置的额定工作压力,并可在线修改,以满足用户对不同的系统工作压力要求,但不超过装置的额定工作压力。
2.加水启动压力设定值(SP2):
当装置初始启动时,为了避免由于液位较低导致控制系统自动启动加水泵给系统加水,设置了加水启动压力。
当装置启动后,随着水电解的进行,使系统产气量增加,氢、氧液位会逐渐上生,最后达到一个稳定的液位。
如果在装置启动时就开始给系统加水,就有可能造成氢、氧液位随着产气量的增加上升至联锁上限值,发生联锁反应。
当出现这种情况时,可手动操作整流柜使之输出较小的电解电流,装置在此电流下运行一段时间后,系统内的水被消耗一部分,使氢、氧液位降低到正常值,此时可加大电流,使装置继续运行。
3.干燥单元启动压力设定值(SP3):
干燥单元启动的工作条件是:
制氢单元产出的氢气纯度合格且系统工作不低于SP3;若系统工作压力过低,则产出的氢气流量很小,干燥单元不能正常工作。
一般地,干燥单元启动压力设定在制氢装置的额定工作压力。
4.槽压联锁上限值(HiHi):
装置运行时,若运行压力高于HiHi时,控制系统给出联锁信号到整流柜,装置自动停车、泄压,同时系统发出声、光报警。
5.槽压报警上限值(Hi):
装置运行时,若运行压力高于Hi时,控制系统发出声、光报警。
6.槽压调节比例系数(Kc):
控制系统对槽压调节时进行PI运算时的比例系数。
7.槽压调节积分时间(Ti):
控制系统对槽压调节进行PI运算时的积分时间,单位为秒。
2.1.2氢、氧液位平衡调节控制系统
装置的氢、氧液位平衡调节系统如图3所示。
2.1.2.1氢液位(0~600mm)经氢差压变送器转换成4~20mA的标准电信号,送入制氢控制柜,经隔离栅隔离后输入PLC的模拟量输入模块(AI)。
装置在运行过程中原料水由于电解而被消耗,因此需要不时地加水,以补充被消耗的原料水。
自动控制系统是以氢液位的高低来判断是否对装置进行自动加水。
PLC将氢液位加水下限设定值及氢液位加水上限值进行比较,再根据一定的条件(如装置处于开车状态、无联锁且装置的运行系统压力高于一定值等)输出信号至加水控制回路,控制加水泵的启停从而达到自动加水的目的。
氢液位调节控制系统中涉及到的相关参数如下:
1.氢液位加水下限设定值(SP1):
当实际氢液位低于SP1时,若满足一定条件,则加水泵启动,控制系统开始给装置自动加水。
2.氢液位加水上限设定值(SP2):
当实际氢液位高于SP2时,则加水泵停车,控制系统停止给装置自动加水。
3.氢液位下限联锁值(LoLo):
当氢液位低于LoLo时,控制系统发出联锁信号到整流柜,装置自动停车、泻压,同时系统发出声、光报警。
4.氢液位下限报警值(Lo):
当氢液位低于Lo时,系统发出声、光报警。
5.氢液位上限报警值(Hi):
当氢液位高于Hi时,系统发出声、光报警。
6.氢液位上限联锁值(HiHi):
当氢液位高于HiHI时,控制系统发出联锁信号到整流柜,装置自动停车、泄压,同时系统发出声、光报警。
2.1.2.2氧液位平衡调节控制:
氧液位(0~600mm)经氧差压变送器转换成4~20mA的标准电流信号,送入制氢控制柜,经隔离栅隔离后输入PLC的模拟量输入模块(AI)。
装置在运行过程中,保持氢氧液位的平衡是非常重要的。
自动控制系统是这样实现氢氧液位的平衡运行:
PLC在接受到氢、氧液位信号后,利用PID杂接受到氢、氧液位信号后,利用PID控制算法,把氢液位信号作为PID算法的给定值,氧液位信号作为测量值进行运算,将运算结果通过PLC的模拟量输出模块输出一个标准的4~20mA电信号,经电气转换器转换成0.02~0.10Mpa的标准信号,控制调节氢、氧液位平衡的气动薄膜调节阀(氢阀)开度的大小,使系统运行时的氢、氧液位保持平衡。
例如,当氧液位高于氢液位时,PID运算的结果将使氢阀的开度增大,致使氢侧的压力泻放得更快一些,使氢液位适当升高并与氧液位基本保持平衡;反之,当氧液位低于氢液位时,PID运算的结果将使氢阀的开度减少,致使氢侧的压力泄放得更慢一些,使氢液位适当降低并与氧液位基本保持平衡。
为使装置在非常状况下(如出现停电、挺气源等异常情况)不使氢、氧液位发生较大、较快的偏差,出于安全考虑,氢阀选用气开式薄膜调节阀。
氧液位平衡调节控制系统中涉及到的相关参数如下:
1.氧液位平衡PI运算比例参数值(Kc):
控制系统对氧液位平衡调节进行PI运算的比例系数。
2.氧液位平衡PI运算积分时间(Ti):
控制系统对氧液位平衡调节进行PI运算时的积分时间。
3.氧液位下限联锁值(LoLo):
当氧液位低于LoLo时,控制系统发出联锁信号到整流柜,装置自动停车、泄压,同时系统发出声、光报警。
4.氧液位下限报警值(Lo):
当氧液位低于Lo时,系统发出声、光报警。
5.氧液位上限报警值(Hi):
当氧液位高于Hi时,系统发出声、光报警。
6.氧液位上限联锁值(HiHi):
当氧液位高于HiHi时,控制系统发出联锁信号到整流柜,装置自动停车、泻压,同时系统发出声、光报警。
2.1.3槽温调节控制系统
槽温调节控制系统入4所示。
电解槽在运行过程中由于水电解而产生的热量由循环碱液的循环带出,较热的气液混合物在氢、氧气液分离中进行水分离、冷却,被冷却后的碱液又返回电解槽参与水的电解。
因此,只要控制冷却水的流量即可控制循环碱液的温度,从而实现对电解槽的温度的控制。
基于上述,控制系统是如下实现槽温的自动调节控制的:
在电解槽碱液出口安装的PT100热电阻采样循环碱液的温度,将随温度变化的电阻信号传送至制氢控制柜,经隔离栅变送器转换成4~20mA的标准信号,送入PLC的模拟量输入模块。
在PLC中与设定的系统工作温度进行比较,运用PID算法进行运算得出结果,并将此结果通过PLC的模拟量输出模块输出一个标准的4~20mA信号,经电气转换器后转换成0.02~0.10Mpa的标准气信号,控制调节槽温的气动薄膜调节阀(水阀)开度的大小,使系统运行时的槽温稳定在设定值。
例如,当槽温高于设定值时,PID运算的结果将使水阀的开度增大,冷却水流量增大,导致循环碱液的温度降低,从而使槽温降低并与设定值基本保持一致;反之,当槽温低于设定值时,PID运算的结果将使水阀的开度减小,冷却水流量减少,导致循环碱液的温度上升,从而上槽温上升并与设定值基本保持一致。
为上装置在非常状况下(如出现停电、停气源等异常情况)不使槽温较高,即应加大冷却水流量以降低槽温,因此水阀选用气闭式薄膜调节阀。
槽压调节系统中涉及到的参数如下:
1.运行槽温设定值(SP1):
SP1是整个装置的工作温度设定值,一般设定在装置的额定工作温度,并可在线修改,以满足用户对不同的系统工作温度要求,但不超过装置的额定工作温度。
2.槽温联锁上限值(HiHi):
装置运行时,若运行槽温高于HiHi时,控制系统发出联锁信号到整流柜,装置自动发出停车、泻压,同时系统发出声、光报警。
3.槽温报警上限值(Hi):
装置运行时,若运行槽温高于Hi时,控制系统发出声、光报警。
4.槽温调节比例系数(Kc):
控制系统对槽温调节时进行PID运算时的比例系数。
5.槽温调节积分时间(Ti):
控制系统对槽温调节时进行PID运算的积分时间,单位为秒。
6.槽温调节微分时间(TD):
控制系统对槽温调节时进行PID运算的微分时间,单位为分。
2.1.4整流输出电流调节控制
整流输出电流调节控制系统如图5所示
装置在正常运行说需要整流柜提供一个稳定的直流电流,并且这个直流电流可按要求在线修改,使装置可在非额定电流下运行。
整流柜内的电流互感装置将直流电流的采样信号通过电流变送器送入制氢控制柜内的PLC,PLC将此电流采样信号与设定值进行比较,经PID运算,运算结果通过PLC的模拟量输出4~20mA的标准信号,经过电流变送器转换成0~10V的电压信号传送回整流柜内的电流给定回路,调节整流柜内的直流电流的大小。
整流输出电流调节控制
1.整流输出电流设定值(SP1):
整流柜根据要求输出的直流电流值,其可调节范围为额定输出电流的50%~100%;
2.整流输出电流PI调节比例系数(Kc):
控制系统对整流输出电流调节进行PI运算时的比例系数;
3.整流输出电流PI调节积分时间(Ti):
控制系统对整流输出电流调节进行PI运算时的积分时间,单位为秒。
2.2氢气干燥单元的自动控制
氢气干燥单元的自动控制的任务是对氢气干燥单元的工作状态进行选择,保证氢气干燥单元把制氢单元产生的纯度合格的氢气(原料氢)中所含的水份去掉,但产品氢气的露点满足要求之后接可进入下一流程。
氢气干燥单元的工作流程,请参见«CNDQ系列水电解制氢装置安装使用说明书(微机控制)»中附录一。
氢气干燥单元的工作状态可分成如下四个工作状态:
干燥A塔再生状态、干下燥B塔工作状态、干燥B塔再生状态及干燥A塔工作状态,在不同的工作状态下,原料氢气的流动路径上不相同的,其目的就是干燥A塔和干燥B塔能交替工作、再生,整个顺序为:
1.干燥A塔再生状态:
干燥A塔工作24小时后使干燥A塔进入再生状态,干燥A塔处于再生状态的同时使干燥B塔进入工作状态;
2.干燥B塔工作状态:
干燥A塔再生结束后干燥B塔继续保持工作状态,直到工作24小时;
3.干燥B塔再生状态:
干燥B塔工作24小时后使干燥B塔进入再生状态,干燥B塔处于再生状态的同时使干燥A塔进入工作状态;
4.干燥A塔工作状态:
干燥B塔再生结束后干燥A塔继续保持工作状态,直到24小时。
氢气干燥单元的自动控制系统方框如图7所示。
氢气干燥单元的自动控制即使自动选择干燥单元的工作状态。
一般地,当制氢单元产生出的纯度合格的氢气进入干燥单元后,在氢气干燥单元初始投入运行时,按工艺要求应选择A塔再生状态或干燥B塔再生状态,对干燥进行预再生。
工作状态选择完成之后,氢气干燥单元即自动运行。
干燥塔的再生控制分别由XMT—7002U和XMT—7602两块数字显示调节仪来完成,干燥单元的两个干燥塔上分别装有两支铂电阻,用来测量干燥再生时的温度,并将温度信号传送至制氢控制柜内的相应数字显示仪,这些测量温度
分别被称为干燥A塔上部温度、干燥A塔下部温度、干燥B塔上部温度及干燥B塔下部温度。
干燥塔的再生控制温度(干燥A塔下部温度、干燥B塔下部温度)一般设定在250℃,而干燥塔的再生结束温度(干燥A塔上部温度、干燥B塔上部温度)一般设定在180℃。
2.3产品氢配气装置(框架Ⅱ)
由制氢及干燥装置产出的合格氢气经过产品氢配气(框架Ⅱ)根据一定的条件可进入氢气储罐储存。
当发电机组需要补氢时,可由储存在氢气储罐中的氢气经框架Ⅱ向发电机组补氢。
根据不同的控制要求,产品氢配气装置可以有不同的自动控制方案。
当需要自动充罐及自动补氢时,可在相应的管路上增加压力变送器以采样储罐压力和氢管道压力、增加气动球阀以实现管路的自动切断或畅通。
当自动充罐时,采用逐个充满的原则,即在1号储罐充满后进行2号储罐的充氢,以此类推。
所有储罐充满后,制氢装置自动降电流运行、情放空或停机。
当自动补氢时,根据补氢管道压力,从1号储罐开始向发电机组进行补氢,当1号储罐的压力下降到一定值后,自动切换到从2号储罐,以此类推。
2.4其它辅助设备的自动控制
2.4.1原料水箱的自动补水功能
制氢装置的连续运行使原料中的原料不时地由于向制氢装置补充而减少,设置自动补水功能可保证原料水箱中的原料水一直保持,这是保证制氢装置稳定运行的一个重要因数.其自动补水系统方框图如图8所示。
原料水箱中的原料水液位由差压变送器转换成4~20mA的标准电信号送入制氢控制柜内的PLC,PLC将送入的原料水箱液位信号与相应的设定值做比较后确定是否对原料水箱进行补水,即通过补水控制回路控制回路控制安装在原料水箱进水管路上的防爆电磁阀的开启和关闭。
原料水箱自动补水系统中涉及到的相关参数有:
1.原料水箱停止补水液位设定值(SP1):
当原料水箱液位高于SP1时停止补水;
2.原料水箱开始加水液位设定值(SP2):
当原料水箱液位低于SP2时开始补水;
3.原料水箱液位上限报警值(Hi):
当原料水箱液位高于Hi时,自动控制系统发出声、光报警。
4.原料水箱液位下限报警值(Lo):
当原料水箱液位低于L0时,自动控制系统发出声、光报警。
第三节水电解制氢及干燥装置自动控制系统的操作
3.1自动控制系统在装置运行前的准备
3.1.1气动管路在装置运行前的准备:
1.用洁净的压缩空气吹扫仪表气源及自动阀气源罐路;
2.对气源管路及气动讯号管路进行检漏,发现有漏点应及时补漏;
3.接通总气源,检查气源是否无水、无油、无尘,气源压力是否在正常范围内,把气源压力的下限值设定在0.5Mpa左右,把供电气转换器的空气过滤减压器的输出压力设定在0.14Mpa,把供气动阀的空气过滤减压器的输出压力设定在0.4Mpa。
3.1.2PLC及上位数据管理机在装置运行前的准备
当水电解制氢及干燥装置工艺准备就绪时,整套装置可投入运行。
在投入运行之前需要完成下列步骤:
1.接通制氢控制柜总电源:
2.接通制氢控制柜内相应的断路器开关,检查各仪表、电器通电显示情况是否正常;检查PLC电源指使、CPU模块工作是否正常;
3.接通上位数据管理机的工作电源,电源指示灯亮,选择启动WINDOWSNTV4.0,在出现开始登录指示时,操作员同时按下键盘上Ctrl+Alt+Del三键,提示输入等录有效的用户名和密码,用户输入密码后回车。
当用户名为“Administrator”时,操作员以管理员身份等录,当用户名为“User”时,操作员以一般身份等录。
4.进入WIDOWSNT工作桌面后点击“开始”按纽出现提拉菜单,后选择“运行”菜单,出现如下对话框:
点击“确定”按钮后出现如下对话框:
点击:
“Start”按钮后上位机监控程序运行,出现“水电解制氢一体化装置控制流程”画面:
此时,装置相应的参数值直接显示在此控制流程主画面上。
3.2装置运行时自动控制系统的参数整定及操作步骤
当自动控制系统在装置运行前的准备工作完成后,即可进行装置的稀碱试运行。
在稀碱试运行期间,应对自动控制系统的所有参数进行整定。
其具体步骤如下:
1.动力柜或制倾控制柜上选择循环泵的控制方式“手动或自动”;
2.若循环泵控制方式为“自动”方式,则点击控制流程主画面上的“开机”命令(若为“手动”方式,则在控制面板上按下“循环泵启动”按钮):
3.检查碱液循环量,整定碱液流量开关中碱液循环量的下限联锁参数
4.按整流柜使用说明书操作整流柜:
5.在整流电流达到额定值后,即可整定下列运行参
压力调节系统中涉及到的参数:
在控制流程主画面上用鼠标点击“槽压”按钮即弹出“槽压调节设定参数”画面;
设定系统压力后,控制程序通过控制氧侧薄膜调节阀的开度大小即可控制系统工作压力为设定的系统压力,氧侧薄膜调节阀的开度大小变化可通过PID调节控制,当给定合适的“槽压调节KP”参数及“槽压调节TI”参数后,控制程序自动进行PID运算并输出合适的DA信号去控制氧侧薄膜调节阀的开度大小从而实现槽压的自动调节;
加水启动压力的设定,目的是为了避免系统在开始运行不久时由于实际氢液位低于加水下限而启动加水