冲三垫圈复合模设计.docx
《冲三垫圈复合模设计.docx》由会员分享,可在线阅读,更多相关《冲三垫圈复合模设计.docx(26页珍藏版)》请在冰豆网上搜索。
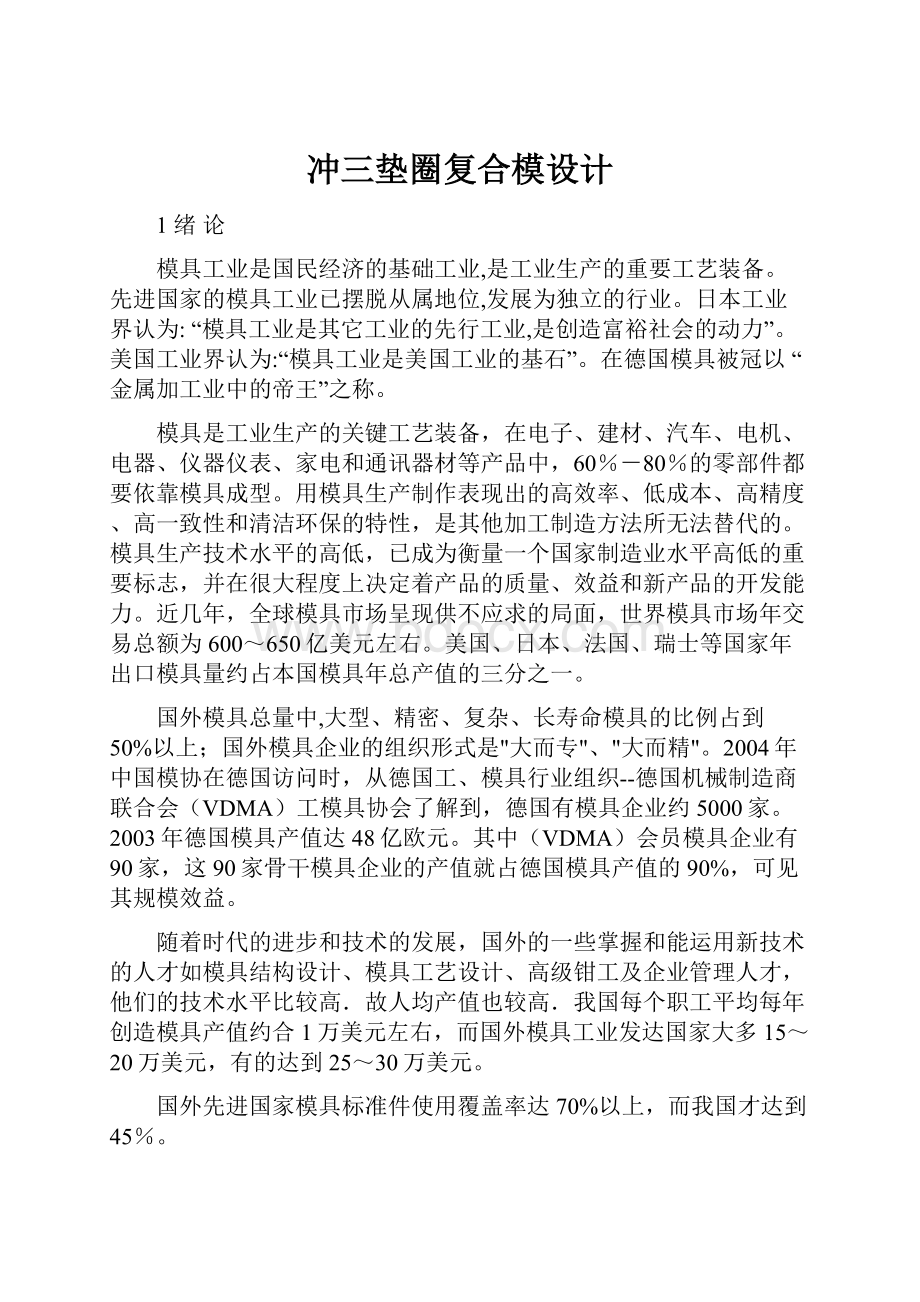
冲三垫圈复合模设计
1绪论
模具工业是国民经济的基础工业,是工业生产的重要工艺装备。
先进国家的模具工业已摆脱从属地位,发展为独立的行业。
日本工业界认为:
“模具工业是其它工业的先行工业,是创造富裕社会的动力”。
美国工业界认为:
“模具工业是美国工业的基石”。
在德国模具被冠以“金属加工业中的帝王”之称。
模具是工业生产的关键工艺装备,在电子、建材、汽车、电机、电器、仪器仪表、家电和通讯器材等产品中,60%-80%的零部件都要依靠模具成型。
用模具生产制作表现出的高效率、低成本、高精度、高一致性和清洁环保的特性,是其他加工制造方法所无法替代的。
模具生产技术水平的高低,已成为衡量一个国家制造业水平高低的重要标志,并在很大程度上决定着产品的质量、效益和新产品的开发能力。
近几年,全球模具市场呈现供不应求的局面,世界模具市场年交易总额为600~650亿美元左右。
美国、日本、法国、瑞士等国家年出口模具量约占本国模具年总产值的三分之一。
国外模具总量中,大型、精密、复杂、长寿命模具的比例占到50%以上;国外模具企业的组织形式是"大而专"、"大而精"。
2004年中国模协在德国访问时,从德国工、模具行业组织--德国机械制造商联合会(VDMA)工模具协会了解到,德国有模具企业约5000家。
2003年德国模具产值达48亿欧元。
其中(VDMA)会员模具企业有90家,这90家骨干模具企业的产值就占德国模具产值的90%,可见其规模效益。
随着时代的进步和技术的发展,国外的一些掌握和能运用新技术的人才如模具结构设计、模具工艺设计、高级钳工及企业管理人才,他们的技术水平比较高.故人均产值也较高.我国每个职工平均每年创造模具产值约合1万美元左右,而国外模具工业发达国家大多15~20万美元,有的达到25~30万美元。
国外先进国家模具标准件使用覆盖率达70%以上,而我国才达到45%。
目前,我国冲压技术与工业发达国家相比还相当的落后,主要原因是我国在冲压基础理论及成形工艺、模具标准化、模具设计、模具制造工艺及设备等方面与工业发达的国家尚有相当大的差距,导致我国模具在寿命、效率、加工精度、生产周期等方面与工业发达国家的模具相比差距相当大。
冲压是一种先进的少无切削加工方法,具有节能省材,效率高,产品质量好,重量轻,加工成本低等一系列优点,在汽车,航空航天,仪器仪表,家电,电子,通讯,军工,日用品等产品的生产中得到了广泛的应用。
据统计,薄板成型后,制造了相当于原材料的12倍的附加值,在国民经济生产总值中,与其相关的产品占四分之一,在现代汽车工业中,冲压件的产值占总产值的59%。
随着我国经济的迅速发展,采用模具的生产技术得到愈来愈广泛的应用。
我国模具业发展尚存在以下几方面的不足:
第一,体制不顺,基础薄弱。
“三资”企业虽然已经对中国模具工业的发展起了积极的推动作用,私营企业近年来发展较快,国企改革也在进行之中,但总体来看,体制和机制尚不适应市场经济,再加上国内模具工业基础薄弱,因此,行业发展还不尽如人意,特别是总体水平和高新技术方面。
第二,开发能力较差,经济效益欠佳。
我国模具企业技术人员比例低,水平较低,且不重视产品开发,在市场中经常处于被动地位。
我国每个模具职工平均年创造产值约合1万美元,国外模具工业发达国家大多是15~20万美元,有的高达25~30万美元,与之相对的是我国相当一部分模具企业还沿用过去作坊式管理,真正实现现代化企业管理的企业较少。
第三,工艺装备水平低,且配套性不好,利用率低.虽然国内许多企业采用了先进的加工设备,但总的来看装备水平仍比国外企业落后许多,特别是设备数控化率和CAD/CAM应用覆盖率要比国外企业低得多。
由于体制和资金等原因,引进设备不配套,设备与附配件不配套现象十分普遍,设备利用率低的问题长期得不到较好解决。
装备水平低,带来中国模具企业钳工比例过高等问题。
第四,专业化、标准化、商品化的程度低、协作差.由于长期以来受“大而全”“小而全”影响,许多模具企业观念落后,模具企业专业化生产水平低,专业化分工不细,商品化程度也低。
目前国内每年生产的模具,商品模具只占45%左右,其馀为自产自用。
模具企业之间协作不好,难以完成较大规模的模具成套任务,与国际水平相比要落后许多。
模具标准化水平低,标准件使用覆盖率低也对模具质量、成本有较大影响,对模具制造周期影响尤甚。
第五,模具材料及模具相关技术落后.模具材料性能、质量和品种往往会影响模具质量、寿命及成本,国产模具钢与国外进口钢相比,无论是质量还是品种规格,都有较大差距。
塑料、板材、设备等性能差,也直接影响模具水平的提高。
我国模具业未来发展方向主要包括以下几方面:
①模具日趋大型化;
②在模具设计制造中广泛应用CAD/CAE/CAM技术;
④模具扫描及数字化系统;
⑤在塑料模具中推广应用热流道技术、气辅注射成型和高压注射成型技术;
⑥提高模具标准化水平和模具标准件的使用率;
⑦发展优质模具材料和先进的表面处理技术;
⑧模具的精度将越来越高;
⑨模具研磨抛光将自动化、智能化;
⑩研究和应用模具的高速测量技术与逆向工程;开发新的成形工艺和模具。
1998年3月,《国务院关于当前产业政策要点的决定》中模具被列为机械工业技术改造序列的第一位,生产和基本建设序列第二位,把发展模具工业摆在发展国民经济的重要位置。
目前,我国冲压模具在产值占模具总产值的40%以上,处于主导地位。
在完成大学三年的课程学习和课程、生产实习,我熟练地掌握了机械制图、机械设计、机械原理等专业基础课和专业课方面的知识,对机械制造、加工的工艺有了一个系统、全面的理解,达到了学习的目的。
对于模具设计这个实践性非常强的设计课题,我们进行了大量的实习。
经过在新飞电器有限公司、在洛阳中国一拖、中信重型矿山机械厂的生产实习,我对于冷冲模具、塑料模具的设计步骤有了一个全新的认识,丰富和加深了对各种模具的结构和动作过程方面的知识,而对于模具的制造工艺更是有了全新的理解。
在指导老师的细心指导下和在工厂师傅的讲解下,我们对于模具的设计和制造工艺有了系统而深刻的认识。
同时在实习现场亲手拆装了一些典型的模具实体并查阅了很多相关资料,通过这些实践,我们熟练掌握了模具的一般工作原理、制造、加工工艺。
通过在图书馆借阅相关手册和书籍,更系统而全面了细节问题。
锻炼了缜密的思维和使我们初步具备了设计工作者应有的素质。
设计中,将充分利用和查阅各种资料,并与同学进行充分讨论,尽最大努力搞好本次毕业设计。
在设计的过程中,将有一定的困难,但有指导老师的悉心指导和自己的努力,相信会完满的完成毕业设计任务。
由于学生水平有限,而且缺乏经验,设计中难免有不妥之处,肯请各位老师指正。
第二章工艺分析
工件名称:
垫圈
生产批量:
大批量
材料:
A3
厚度:
1.5mm
工件简图见图1
设计方案:
复合模一次冲压完成
第三章工艺方案的确定
该工件只需要采用冲孔和落料两道工序即可完成,材料为A3钢,A3钢具有良好的冲压性能,适合冲裁。
外形落料的工艺性:
该垫圈料厚为2mm,外形比较简单,尺寸精度要求一般,因此可采用落料工艺获得。
冲孔的工艺性:
φ14.5的孔,尺寸精度要求一般,可采用冲孔。
此工件只有外形落料和冲孔两个工序。
图示零件尺寸均为未注公差的一般尺寸,按惯例取IT14级,符合一般级进冲压的经济精度要求。
由以上分析可知,图示零件具有比较好的冲压工艺性,适合冲压生产。
该工件仅包含落料和冲孔两个基本工序,可以采用以下三种工艺方案:
第一:
先落料,后冲孔。
采用单工序模生产。
第二:
落料—冲孔复合冲压。
采用复合模生产。
第三:
冲孔—落料级进冲压。
采用级进模生产。
方案一:
模具结构简单,成本较低,但需要两道工序两副模具,由于两次定位使得工件的形位误差难以保证,尺寸较小,制件的质量较差,成本高而生产效率低,难以满足大批量生产要求,操作也不安全,故不宜采用。
方案二:
只需一副模具,由于一次成形,减少了多次定位出现的定位误差,并且在模具结构中采用弹性压料装置,使其制件质量较好,工件的精度及生产效率都较高。
方案三:
也只需一副模具,生产效率高,操作较方便,工件精度也能满足要求,但是成本较复合模高。
通过对上述三种方案分析比较,该件的冲压生产采用第二种方案进行冲裁为好。
第四章主要设计计算
4.1排样方式的确定及其毛坯尺寸计算
设计复合模,首先要设计的就是排样方式,该零件形状比较规则,直排可以显著地减少废料,所以采用直排的方式排样,根据零件的结构特点需要冲孔和落料两个工序就可以完成零件的制造。
工序方案如图所示。
4.2条料宽度、导尺间宽度和材料利用率的计算
查表取得搭边值为a1=2mm和a=2.2mm。
条料宽度的计算:
拟采用无侧压装置的送料方式,由
b-Δ=〔D+2a+c1〕-Δ﹝2﹞
D—条料宽度方向冲裁件的最大尺寸
a—侧搭边值
c1—导料板与最宽条料之间的间隙
代入数据计算,取得条料宽度为95.8mm。
导尺间距离的计算:
由s=D+2(a+c1),代入数据计算得导尺间距离为96.3mm。
材料利用率的计算:
由文献﹝2﹞材料利用率通用计算公式
=
式中A—一个冲裁件的面积,mm2;
n—一个进距内的冲裁件数量;
B—条料宽度,mm;
s—进距,mm
得
=
=70.3%
可得下表:
项目
公式
结果
备注
冲裁件的面积A
A=24×65-2×π(8.5/2)×(8.5/2)-(16-4π)+0.5×L×R
6196.6mm
查表2.5.2得最小搭边值a=2.2mm
a1=2.0mm采用导料销导料
条料宽度B
B=90.87+2.2×2+0.1
95.77mm
步距S
S=90+2
92mm
材料的利用率η总
η=6196.595/95.77×92×100%
70.3%
冲裁力公式为
P=P孔+P落
由工件结构和前面所定的冲压方案可知,本工件的冲裁力包括以下部分:
冲φ14.5mm孔的力P1、落外型料的力P2,向下推出φ14.5mm冲孔废料的力P3,向上顶出工件的力P5。
考虑到模具刃部被磨损、凸凹模间隙不均匀和波动、材料力学性能及材料厚度偏差等因素的影响,实际计算冲裁力时按下面公式:
P=KLtτ﹝3﹞
式中P—冲裁力(kN)
L—冲裁件剪切周边长度(mm)
t—冲裁件材料厚度(mm)
τ—被冲材料的抗剪强度(MPa)
K—系数,一般取1.3。
上式中抗剪强度τ与材料种类和坯料的原始状态有关,可在手册中查询。
为方便计算,可取材料的τ=0.8σb,故冲裁力表达式又可表示为:
P=1.3Ltτ≈Ltσb
式中σb—被冲材料抗拉强度(MPa)。
查手册﹝1﹞表8—7得A3的σb=450MP
(1)冲孔冲裁力P孔
P孔=L孔σbt=14.5×3.14×2×450=40977.7N
(2)落料冲裁力P落
P落=L落σbt=(28+50+90)×3.14×450=475008.8N
(3)推件力Pt
Pt=KtP孔n
其中Kt——推件系数,查表取Kt=0.055;
n——同时卡在凹模洞口内的件数,取n=2。
所以Pt=0.055×2×40997.8=4509.8N
(4)卸料力Px。
Px=P落Kx
式中Px——卸料力;
Kx——卸料系数,查表Kx=0.05
所以Px=0.05××40977.8=2049.9N
(5)顶件力Pd。
Pd=Kd(P落+P落)
式中Pd——顶件力
Kd——顶件系数,查表取Kd=0.06
所以Pd=0.06×(40977.8+475008.8)=3096.4N
(6)总冲压力P总冲裁时,压力机的压力值必须大于或等于冲裁各工艺力的总和,即大于总的冲压力。
总的冲压力根据模具结构不同计算公式不同,当采用弹压卸料装置和下出件的模具时,总的压力为
P总=P孔+P落+Px+Pt=40977.7+475008.8+2049.9+4509.8
=522566.2N
初选压力机:
J23-63
所选择压力机的相关参数,见表一。
表一所选择压力机的相关参数
型号
公称压力/kN
滑块行程/mm
最大封闭高度/mm
模柄
直径
/mm
工作台尺寸/mm
可倾斜角/·
封闭高度调节量/mm
JG23-63
630
130
360
50
480×710
30
80
4.3压力中心的确定及相关尺寸的计算
模具的压力中心就是冲压力合力的作用点。
为了保证压力机和模具的正常工作,应使模具的压力中心与压力机的中心滑块中心线重合。
否则,冲压时滑块就会承受偏心载荷,导致滑块导轨与模具的导向部分不正常的磨损,还会使合理的间隙得不着保证,从而影响制件的质量和降低模具的寿命,甚至损坏模具。
该磨具结构的设计与制造压力中心与模柄中心线相重合。
4.4工作零件刃口尺寸的计算
在确定工作零件刃口尺寸之前,首先要考虑到工作零件的加工方法和模具的装配方法,结合该模具的特点,工作零件的形状相对比较简单,适宜采用线切割机床分别加工落料凸凹模、凹模、凹模固定板以及卸料板等,这种加工方法可以保证这些零件各孔的同轴度,使装配工作简化,因此工作零件刃口尺寸计算就按分别加工的方法来计算。
4.4.1冲孔加工工序
同样也是采用自由公差为IT14级精度,单一的冲孔只冲1个Φ14.5mm的孔,还要保证孔与孔的相互位置关系均为IT14级的制造精度,凸、凹模的加工精度同样也取IT6级和IT7级进行加工制造。
当冲该孔的时候,因为IT14级取x=0.5查表2.3.3可得最大、最小冲裁间隙分别为Zmax=0.360mmZmin=0.246mm。
计算如下:
(mm)
(mm)
校核:
|δA| +|δT|≤Zmax-Zmin
0.114≤Zmax-Zmin
满足间隙公差条件
4.4.2落料加工工序
在落料加工工序中要完成的是对直径为28mm、50mm、90mm的圆形进行落料,其尺寸公差均未标注,根据设计的规则取自由公差为IT14级精度,标准公差值由课本表2.3.3查得其公差是0.62mm和0.52mm,然后查课本表2.3.3查得冲模设计时的最大、最小间隙分别Zmax=0.360mmZmin=0.246mm则
Zmax-Zmin=(0.360-0.246)mm=0.114mm
由于制件的精度为IT14级,x取0.52设凸、凹模的加工精度分别为IT6级和IT6级,可以满足落料时的精度要求:
落Φ28的料:
(mm)
(mm)
落Φ50的料:
(mm)
(mm)
落Φ90的料:
(mm)
(mm)
校核:
|δA| +|δT|≤Zmax-Zmin
|δA| +|δT|=0.114mm
0.114mm≤0.114mm,可以满足公差条件。
4.5卸料件的设计
由以上计算可知卸料力为F=2049.9N,这个力相对适中,可采用弹簧卸料装置较为合适
4.5.1弹簧的设计计算:
1)根据分析采用的复合模冲压力适中,相应的卸料力也适中,要求卸料装置的承载能力也适中,所以采用弹簧是合适。
2)根据模具安装位置拟选6个弹簧,每个弹簧的预压力为
F0≧Fx/n=2049.9/6=341.6N
3)查有关弹簧规格,初选弹簧规格为:
22mm×3.5mm×128mm。
其具体参数为:
D=22mm,d=3.5mm,t=12.1mm,F2=478.43N,△H2=33.95mm,H0=128mm,n=10mm,f=3.395mm。
4)计算△H0:
△H0=F0△H2/F2=341.6×33.95/478.43=24.2mm
5)校核:
设△H1=3mm,△H2=5mm
△H=△H0+△H1+△H2=32.2mm
由于33.95﹥32.2,即△H2﹥△H
所以,所选弹簧是合适的。
第五章模具的总体设计
5.1模具类型的选择
由冲压工艺分析可知,采用复合冲压,所以模具类型为复合模,凸凹模在下,落料凹模和冲孔凸模在上,为典型的倒装冲孔落料复合模。
5.2定位方式的选择
因为该模具采用的是条料,控制条料的送进方向采用导料销,控制条料的送进步距采用活动挡料销定距,简单,可靠,定位方便。
5.3卸料、出件方式的选择
因为工件料厚为1.0mm,相对较薄,卸料力也比较小,故可以采用弹性卸料。
又因为是复合模生产,所以采用上出件比较便于操作和提高生产效率。
5.4导向方式的选择
为了提高模具寿命和工件质量,方便安装调整等因素该复合模采用后侧导柱的导向方式。
5.5工作零件的结构设计
根据模具设计的基本形式,可以确定模具的基本结构原理。
5.5.1冲孔凸模的设计
5.5.1.1冲孔凸模长度
根据制件的零件图可以知道,冲孔凸模的结构为圆形,具体结构可以根据具体的设计需要而定。
因为所用的冲孔凸模均为圆形,而且由[1]P38(3)的数据可得,这里所用的圆形凸模都是不需要特殊保护的小凸模,所以冲孔凸模采用台阶式,一方面加工方便,另一方面又便于装配和更换。
其总长L可根据具体设计按如下方式计算,首先其结构形式如下图所示:
由上图得
L=Ht+l自
Ht=(0.6+0.8)Hk
Hk=
l自=Ha
以上各式中Ht——固定凸模部分长度;
Hk——冲孔凸模厚度;
P孔——冲孔冲裁力,P孔=40977.7N;
K——系数,根据L孔=14.5×3.14,查表得K=1;
l自——凸模自由长度;
所以Hk=
=
=16mm
Ht=(0.6+0.8)×16=(10.2~13.6)mm,取Ht=12mm
该凸模可选用标准件BII型式,即如上图所示取D=Φ22mm,l=40mm
5.5.1.2凸模强度——压应力校核。
校核公式为
≦【σ】压
式中P孔——冲孔冲裁力,N,P孔=40997.8N;
Fmin——凸模最小断面积,mm2;Fmin=170.6mm2;
【σ】压——凸模材料的许用压应力,Mpa,凸模材料选用Cr12,《查手册》,
【σ】压=(1000~1600)Mpa,取【σ】压=1000Mpa,
=
=240.3Mpa﹤【σ】压
所以凸模强度符合要求。
5.5.1.3凸模刚度——细长杆失稳校核。
凸模校核公式lmax≦
lmax——凸模最大自由长度,mm;
P——凸模总压力,N,P孔=40997.8N;
E——凸模材料弹性模量,Mpa,一般取E=2.1×105;
Jmin——凸模最小断面积直径,mm,d=14.7mm;
——支承系数,无导板导向取
=2mm;
n——安全系数,钢取2~3mm。
代入公式,得
lmax≦
=107.01mm
实际l自=28mm﹤107.01mm
所以凸模刚度符合要求。
5.5.2落料凹模组件的尺寸确定和示意图
凹模采用整体式凹模,各冲裁的凹模孔均采用线切割加工,安排凹模在模架上的位置时,要依据计算的压力中心的数据,使压力中心与模柄中心重合
因为本例生产批量较大,所以采用刃口较高的圆形凹模,其轮廓尺寸可按公式2.9.3、2.9.4计算:
凹模厚度H=kb≥15mm而0.25×89.57=22.4mm,圆整后取H=23mm
凹模壁厚C=(1.5~2)H(≥30~40mm)=34.5~46mm
取凹模厚度H=22mm凹模壁厚C=35mm
凹模直径B=89.57+2c=89.57+70=159.57mm
式中b----凹模孔的最大宽度,mm但B不小于15mm
C-----凹模壁厚,mm指刃口至凹模外形边缘的距离;
K=系数,取0.25
凹模上螺孔到凹模外缘的距离一般取(1.7~2.0)d,d为螺孔的距离,由于凹模厚度为15mm,所以根据《冲压模具标准件》表5-8查得螺孔选用4×M6的螺钉固定在下模座。
如下图所示:
螺孔到凹模外缘的最小距离a2=1.0d=1.0×7=7mm
a3=1.5d=10.5mm
凹模上螺孔间距由表5-7查得最小间距为5mm。
螺孔到销孔的距离一般取b>2d,所以b应大于14。
根据上述方法确定凹模外形尺寸须选用圆凹模板100×100T10A(JB/T7643.4)
即如下图所示形式:
5.5.3凸凹模的设计
结合工件外形并考虑加工,凸凹模采用整体凸凹模,将落料凸凸模设计成直通式,冲裁的凸凹模外形及孔均采用线切割机床加工,1个M8的螺钉固定在下垫板上,该副模具中共有三个凸凹模,与凸模固定板配合按H6/m5。
其结构简图分别如下所示:
凸凹模1凸凹模2
凸凹模3
5.5.4导料销及挡料销的设计
条料采用两个导料销导料,送进方向上采用一个挡料销进行定位,导料定位都较可靠,方便,将其固定在卸料板上,在凹模板上设置避让孔,其深度稍大于销头部高度。
5.5.5卸料部件的设计
5.5.5.1卸料板的设计
4.5.5.1.1卸料板的形状与尺寸。
卸料板取如下图所示的圆形版,直径视情况而定,厚度Hx=14mm;卸料板材料选A3(45钢),不用热处理淬硬。
5.5.5.1.2卸料板上成形孔的设计。
取弹压卸料板与凸模的双面间隙为0.1~0.3mm。
所以卸料板上与凸模装配的成形孔尺寸为
Dx=Dt+C=89.32+1.3=90.62(mm)
式中Dt——落料凸凹模刃口尺寸;
C——弹压卸料板与凸凹模的双面间隙;
5.5.5.2卸料螺钉的选用
卸料板上设置4个卸料螺钉,公称直径为6mm,螺纹部分为8×8。
卸料钉尾部应留有足够的行程空间。
卸料螺钉拧紧后,应使卸料板超出凸凹模端面1mm,有误差时通过在螺钉与卸料板之间安装垫片来调整。
5.5.6推件块的设计
推件块用来推出卡在凹模里的之间,要有一定的行程空间,材料选用45钢,其具体尺寸设计如下图所示:
5.5.7模架及其它零部件的设计
4.5.7.1该模具采用中后侧导柱模架,这种模架的导柱在模具后侧位置,模具较敞开。
以凹模周界尺寸为依据,选择模架规格。
根据模具周界的具体尺寸,查[2]P273得采用中间导柱模架最适合具体规准是:
上模座100×100×30GB/T2855.5
下模座100×100×40GB/T2855.61的标准模架,材料为HT200。
上模座厚度取30mm,固定板厚度取15mm,下模座厚度取40mm,那么该模具的闭合高度:
H闭=H上模+L+H+H下模-h2
=30+40+15+20+40-1=144
其中:
L为凸模长度,L=40mm;
H为凹模厚度,H=28mm;
h2为冲裁后进入凹模的深度,h2=1.
可见该模具闭合高度小于所选压力机J23-6.3的最大装模高度(150mm),可以使用。
根据设计出来的最大闭合高度设计导柱和导套,有模座上的导柱和导套的尺寸确定选择的尺寸查[2]p280和p284得:
导柱:
B22h5×80×35GB/T2861.2
B25h5×80×35GB/T2861.2
导套:
C22H6×100×33GB/T2861.8
C25H6×100×33GB/T2861.8
5.5.7.2模柄与上模座的联接采用旋入式的结构,如下图所示:
5.5.8模具总装配图
通过以上的设计,可得到如图所示的模具总装图:
模具上模部分主要由上模座、上垫板、凸模、凸模固定板、空心垫板、凸凹模等组成。
卸料方式采用弹性卸料,以弹簧为弹性组件。
下模部分由下模座、凸凹模板、卸料板、弹簧等组成。
冲孔废料由漏料孔漏出,制件由推件块从下模推出。
5.5.9模具零