中厚板卷厂质量方针目标展开终1.docx
《中厚板卷厂质量方针目标展开终1.docx》由会员分享,可在线阅读,更多相关《中厚板卷厂质量方针目标展开终1.docx(38页珍藏版)》请在冰豆网上搜索。
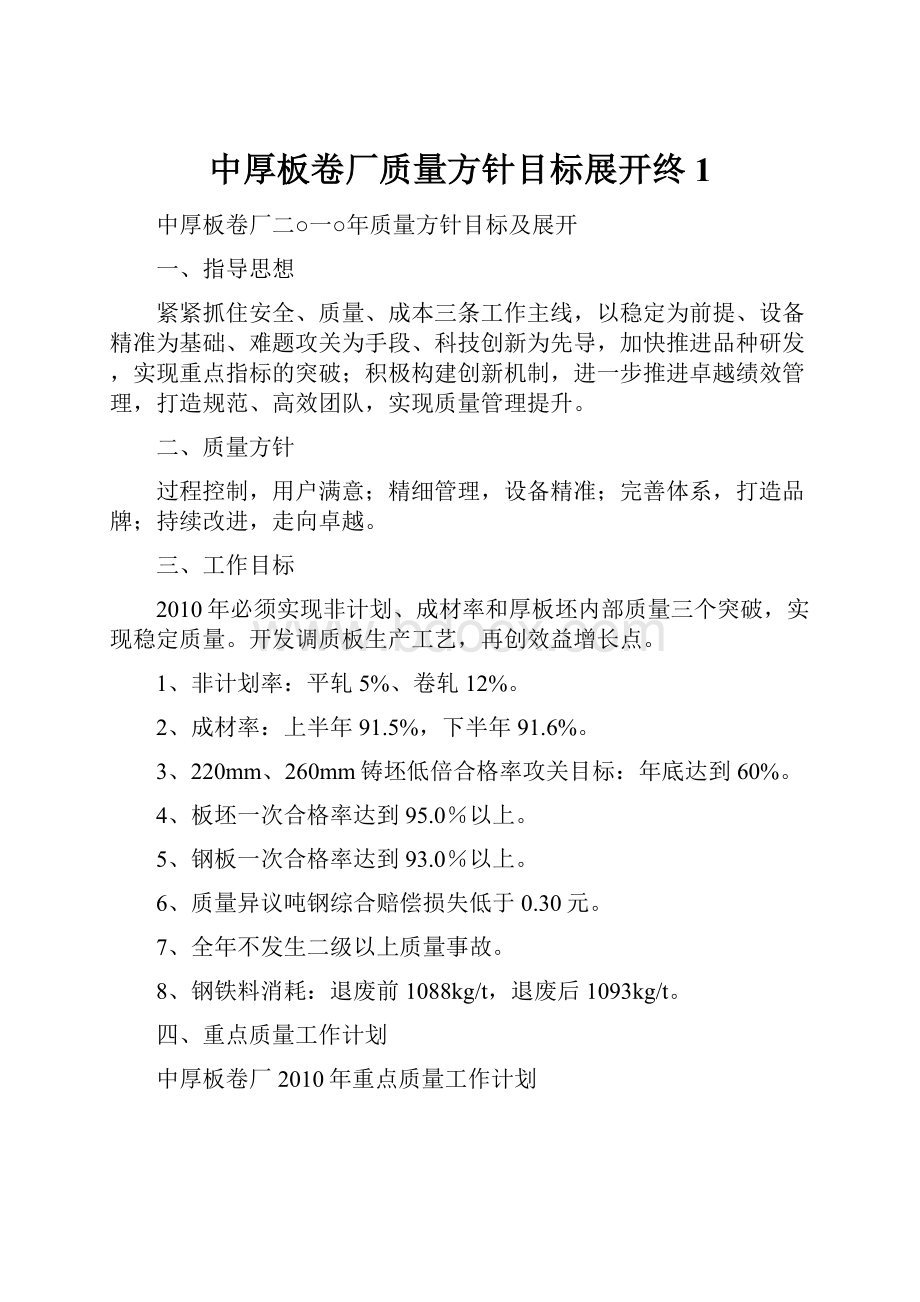
中厚板卷厂质量方针目标展开终1
中厚板卷厂二○一○年质量方针目标及展开
一、指导思想
紧紧抓住安全、质量、成本三条工作主线,以稳定为前提、设备精准为基础、难题攻关为手段、科技创新为先导,加快推进品种研发,实现重点指标的突破;积极构建创新机制,进一步推进卓越绩效管理,打造规范、高效团队,实现质量管理提升。
二、质量方针
过程控制,用户满意;精细管理,设备精准;完善体系,打造品牌;持续改进,走向卓越。
三、工作目标
2010年必须实现非计划、成材率和厚板坯内部质量三个突破,实现稳定质量。
开发调质板生产工艺,再创效益增长点。
1、非计划率:
平轧5%、卷轧12%。
2、成材率:
上半年91.5%,下半年91.6%。
3、220mm、260mm铸坯低倍合格率攻关目标:
年底达到60%。
4、板坯一次合格率达到95.0%以上。
5、钢板一次合格率达到93.0%以上。
6、质量异议吨钢综合赔偿损失低于0.30元。
7、全年不发生二级以上质量事故。
8、钢铁料消耗:
退废前1088kg/t,退废后1093kg/t。
四、重点质量工作计划
中厚板卷厂2010年重点质量工作计划
序号
项目
工作计划及要求
责任单位
配合单位
完成时间
1
梳理关键点,控制轧材非计划
成立非计划攻关队攻关队,制定攻关目标,做好指标分解,责任到人,目标明确,严格按照攻关细则开展工作,分阶段按时完成目标。
技术质量科
各单位
全年
统计好订单附带余材,密切关注新下订单,做好计划附带的余材替代工作。
生产安全科
各单位
全年
通过卷取炉气氛改善、运用高压小流量系统、轧制润滑、转鼓刻槽及修复等措施减少卷轧头尾非计划率;制定卷取炉炉况检查制度,改良炉壳耐材,杜绝卷取炉掉渣改判;尽快恢复加热炉二级走梁,减少在炉时间对除鳞效果的影响。
热轧车间
设备科
自动化科
技术质量科
全年
通过铸坯表面质量及尺寸检查,加强坯料入炉检验,及时清理坯料表面氧化铁皮和异物,确保入炉坯表面质量和规格。
生产安全科
热轧车间
连铸车间
全年
恢复立辊使用,控制好板形,减少由于刮框造成的铁片压入改判。
热轧车间
设备科
3月1日
做好飞剪剪切长度与设定长度的跟踪,逐步将剪切精度提高到±100mm内。
电修车间
热轧车间
5月1日
提高轧制厚度精度控制,确保轧件长度,减少偏差带来的短尺非计划。
热轧车间
设备科
自动化科
4月30日
严格按照抽查制度进行工艺检查,对由于工艺违章造成的性能改判严格考核。
技术质量科
各单位
全年
加强设备维护和点检,发现问题及时处理,降低中间废品,提高设备精准,减少由于设备原因造成的批量改判。
设备科
各单位
全年
利用好我厂热处理设备,做好性能挽救工作。
技术质量科
热处理车间
全年
继续深入开展《钢板表面氧化铁皮控制》项目,降低麻面造成的判废。
技术质量科
各单位
全年
2
努力提高成材率
成立成材率攻关队,制定攻关目标,做好指标分解,责任到人,目标明确,严格按照攻关细则开展工作,分阶段按时完成目标。
技术质量科
各单位
全年
争取毛边及较宽产品的订单,减少切边比重;合理设计坯料,降低定厚系数、压缩切边、切头尾,提高下料成材率。
生产安全科
各单位
全年
控制炉内气氛,优化加热工艺,减少钢坯在炉内滞留时间,稳定并降低氧化烧损。
热轧车间
技术质量科
全年
不断提高并稳定铸坯尺寸精度,减少火切头尾外形缺陷,保证坯料矩形度。
连铸车间
热轧车间
全年
优化配辊制度,提高厚度控制精度,降低钢板板凸度,降低同板差。
热轧车间
技术质量科
全年
提高板形控制水平,充分发挥矫直机能力,降低因头尾瓢曲造成的切损。
热轧车间
技术质量科
全年
加强层流冷却设备的监控,改进操作,降低强冷板瓢曲判废。
热轧车间
技术质量科
全年
加强设备维护和点检,发现问题及时处理,降低中间废品,提高设备精准,减少由于设备原因造成的批量改判。
设备科
自动化科
热轧车间
电修车间
全年
3
以连铸区域为中心,提升铸坯内部质量
积极与与铸坯内部质量控制较好的同类型厚板坯连铸机厂家如湘钢,进行对标学习,学习其成功经验。
技术质量科
连铸车间
设备科
自动化科
全年
加强二冷喷嘴检查,加大检查维护频次,减少喷嘴堵塞。
优化二冷工艺,结合铸坯表面质量控制,确定适宜的二冷比水量。
连铸车间
设备科
技术质量科
全年
提高离线设备维护精度,加强离线设备的管理,确保正常生产过程中2#机离线弯曲段、弧形段、矫直段合格备件分别有1个、4个、2个,能够满足生产需要;定期检测扇形段的辊缝、对中状况,并及时调整,偏差控制在±0.5mm,不符合要求的段及时更换;加强在线扇形各段的点检、维护,确保铸机精度,在线扇形段辊缝、对弧偏差控制在±0.5mm。
连铸车间
设备科
自动化科
全年
优化调整动态轻压下,如压下速率、压下位置及压下量等,发挥动态轻压下的最佳效果,提高铸坯内部质量。
连铸车间
技术质量科
全年
以提高铸坯内在质量为重点,从全程保护、规范操作、冷却系统的维护、设备精准、二冷制度优化等多方面开展工作,力争快速提高铸坯内部质量并稳定在较高水平,220mm、260mm铸坯低倍合格率攻关目标:
年底达到60%。
连铸车间
设备科
自动化科
技术质量科
全年
以成份、温度、静搅时间为重点,严格控制过热度,以洁净钢为标准开展工作,减少成份出格,作好窄成分控制,提高钢水成分命中率和钢水纯净度。
精炼车间
连铸车间
全年
4
完善质保体系,稳定产品质量
针对2009年存在的主要问题,借ISO9001-2008版换版契机进行全面梳理,如公司下发的质量计划、标准、合同联系单、通知等宣贯不到位问题、关键工艺控制点记录及工艺检查不到位等问题。
技术质量科
各单位
3月31日
不断梳理关键工艺控制点,关键控制参数,使现场数据真实的反馈生产及质量情况,指导现场稳定生产。
技术质量科
各单位
全年
运用好“计划管理系统”,完成技术文件的电子化传递,确保技术文件快速准确地传递到对应岗位,彻底杜绝由于文件版本不符造成的工艺执行问题。
及时将品种开发总结、事故预案、经典拜读、论文、专利等上传到“知识管理系统”,做到技术的不断积累。
技术质量科
各单位
全年
加强质量体系的宣贯与培训,采用看板、专题讲座、横幅、征文等方式,对ISO9001、APIQ1两大体系、技术文件进行针对性的宣贯,做到人人了解体系,人人关心质量,以满足客户要求为工作核心的理念深入人心。
技术质量科
综合科
各单位
全年
完善外包过程的质量管理制度,做好外委加工产品的质量控制。
技术质量科
各单位
全年
严格执行质量事故管理制度,按制度实施和考核,对质量问题“四不放过”,防止重复问题、批量性质量问题的发生,提高体系运行的有效性。
技术质量科
各单位
全年
运用好已建设的ERP系统、检化验系统、计量系统、EMS能源管理系统,配合项目部完成“质量分析系统”,使用现代化分析工具将大量的工业数据有序化。
自动化科
各单位
全年
5
开发高效节能钢板,实现调质板规模化生产
研究各类调质钢板性能的控制机理,研究淬火加热温度及淬火冷速对马氏体组织形态的影响,研究淬火机板形控制技术,主要包括上下水比、水量及淬火速率之间的关系。
技术质量科
热轧车间
热处理车间
全年
通过与高校或科研院所的合作,对技术难题进行专项研究,如回火工艺与力学性能之间的关系,提高性能挽救合格率。
技术质量科
技术质量科
全年
开发调质产品以耐磨钢、高强结构钢、容器用钢等十多个品种为重点,特别是50mm以上厚板的调质产品和6~12mm薄规格耐磨板。
技术质量科
各单位
全年
以9Ni钢为重点进一步开展好品种研发和规模化生产工作,将9Ni钢打造成我厂的拳头产品。
技术质量科
各单位
全年
梳理调质板生产工艺流程,挖掘热处理设备的潜能,保证设备的精准运行。
力争达到年产10万吨调质板的生产能力。
技术质量科
生产安全科
热处理车间
全年
6
做好新产品认证,实施品牌战略
通过各种方式对员工进行品牌意识、市场意识、竞争意识等方面的宣传教育,提高各岗位人员的品牌意识,在全厂营造质量是品牌的核心。
技术质量科
各单位
6月30日
以质量意识和工作质量的提高,来促进产品实物质量的提高,从抓好切边、标识、包装等外观质量着手,打造产品质量品牌。
技术质量科
各单位
全年
完成水电工程用板、Q550级别高强度船板、锅炉及压力容器板、JIS产品、CE产品的认证、扩证及换证工作。
技术质量科
各单位
全年
完成APIQ1年度审核工作,不断完善质保体系,持续提高质量保证能力。
技术质量科
各单位
全年
7
创新质量管理,推广先进质量管理方法
推广运用六西格玛分析问题、解决问题的方法,围绕影响质量、效率与效益的难题开展攻关。
技术质量科
各单位
全年
各单位与各专业互相协作、密切配合,制定详细实施计划,确保完成攻关目标。
技术质量科
各单位
全年
重点做好《提高2#机铸坯低倍合格率》、《降低钢板麻面改判率》等六个项目。
技术质量科
各单位
全年
进一步深化卓越绩效模式管理方法,结合全国质量奖、市长质量奖评审意见,制定卓越绩效管理提升改进方法,分解落实KPI指标,完善自我评价体系,做到持续改进。
技术质量科
各单位
全年
以QC小组等群众性质量管理活动普及创新,将QC活动覆盖到班组,对基础较好班组在内部注册开展QC活动,对班组成员开展QC培训,普及QC质量管理的知识。
技术质量科
各单位
全年
针对性开展先进质量管理方法的培训。
对技术人员开展五大工具(APQP、FMEA、SPC、MSA、PPAP)培训。
技术质量科
各单位
全年
8
精细管理,提高设备精准
做好在线影响产品质量的设备精度的测量,最大程度的减少设备对产品质量的影响。
自动化科
各单位
全年
积极组织开展设备难题攻关,解决影响产品质量的设备问题。
设备科
各单位
全年
扎实推行设备零故障管理,以点检为基础,计划为手段,离线设备维护为保证,细化各项设备管理制度。
设备科
各单位
全年
合理安排和精心组织年度设备大中修,集中处理和解决比较大的设备隐患,更换主要零部件,保持主体设备状态稳定。
设备科
各单位
全年
9
完善用户满意工程,提高顾客满意度
转变客户服务意识,做到售前服务、售中服务、使用服务和售后服务,提高客户满意度。
生产安全科
各单位
全年
掌握生产动态,完善合同管理,确保合同兑现,做好合同跟踪。
生产安全科
各单位
全年
通过驻厂员及时了解用户对产品的使用情况,针对用户提出的问题和要求,及时进行答复或上门服务。
针对出现的问题,制定切实可行的整改措施,并逐一落实,努力提高客户满意度。
生产安全科
各单位
全年
对内做好精料方针,强化原辅料、关键备件、工艺备件的管理,建立合格供方档案,做好原辅料和关键备件使用情况的工作,及时做好新材料、新备件的使用质量总结和反馈工作。
技术质量科设备科自动化科
各单位
全年
增强过程质量控制意识,牢固树立下道工序就是用户的质量理念,定期与下道工序和用户沟通,把好质量关,杜绝不合格品流向下道工序,严把产品出厂关,严格产品抽查和考核制度。
技术质量科
各单位
全年
10
健全绩效体系,创新培训机制,大力开发人力资源
拓展管理、技术、操作三条通道。
综合科
各单位
全年
完善单位、跨部门组织(工艺牵头的小组等)、个人三类绩效评价机制。
综合科
各单位
全年
制定完善的纯净考核体系,实现薪酬与纯净挂钩。
综合科
各单位
全年
量化培训内容,明确培训对象,落实奖惩措施。
综合科
各单位
全年
要以信息化为手段,制定合理的积分奖惩办法,突破传统培训模式,建立网络多媒体集成培训平台,深入推行跨专业培训。
综合科
自动化科
全年
拟制:
审核:
批准:
中厚板卷厂2010年度质量目标及过程指标测评分解表
记录编号:
JL100202/A
序号
质量目标/过程指标
公司
目标值
中厚板卷厂
目标值
计算方式
测评频次
对应措施
责任部门
1
轧材非计划
-
平轧≤5%
卷轧≤12%
平轧非计划=(非计划总量-卷轧头尾非计划)/(总产量-卷轧头尾非计划)×100%
卷轧非计划=卷轧头尾非计划/卷轧生产总量×100%
月
制定攻关目标,做好指标分解,责任到人,目标明确,严格按照攻关细则开展工作,分阶段按时完成目标。
技术质量科
2
成材率
-
上半年≥
91.5%
下半年≥
91.6%
(合格品+待判+钢卷合格品)/(坯料重量-原料废)×100%
月
成立成材率攻关队,制定攻关目标,做好指标分解,责任到人,目标明确,严格按照攻关细则开展工作,分阶段按时完成目标。
技术质量科
3
220mm、260mm铸坯低倍合格率
-
≥60%
220mm、260mm铸坯低倍合格品数/220mm、260mm铸坯低倍取样总数×100%
月
以提高铸坯内在质量为重点,从全程保护、规范操作、冷却系统的维护、设备精准、二冷制度优化等多方面开展工作,力争快速提高铸坯内部质量并稳定在较高水平。
技术质量科
4
生产计划完成率
≥98%
≥98.5%
实际完成计划产量/生产计划产量×100%
月
1.完善合同执行,强化合同执行每个环节的控制,提高合同命中率。
2.对每一票合同,从接单、合同评审、规程的采用、生产计划的安排、工艺过程的控制、检验和放行的标准、标识等做到一一对应,确保合同高效率完成。
生产安全科
5
坯一次合格率
≥94.85%
≥95.0%
合格产量/检验量
月
1.严格按钢种规程控制成份,减少成份波动。
2.合理调节静搅拌时的氩气流量,尽可能延长静搅拌时间,促进夹杂物充分上浮去除。
3.进一步加强连铸保护浇注操作,避免钢水二次氧化。
技术质量科
6
材一次合格率
≥92.90%
≥93.0%
合格产量/检验量
月
1.控制加热温度,提高温度均匀性。
2.提高板形控制水平,减少待判量。
3.优化板坯长度和生产计划;优化钢卷工艺,提高钢卷卷形质量、减少氧化皮产生,提高钢卷性能合格率。
3.提高矫直操作水平,减少轧件撞辊,定期检查矫直机工作辊,防止粘氧化铁皮,减少钢板压痕发生率。
技术质量科
7
吨钢赔偿额
≤0.40元/吨
≤0.30元/吨
异议赔偿额/钢产量
月
1.强化各环节的控制,特别关注夜班工艺执行和产品的检验判定,严格之行评审制度,减少临界缺陷品出厂风险。
2.对板坯入炉质量、修磨质量、上下表检验频次、切割质量、喷识质量、矫直质量等进行严格检查和考核。
3.严格执行公司制定的内控标准管理办法,配合公司完成内控标准升级,强化质量控制,并按要求进行生产组织、检验和考核。
技术质量科
8
顾客投诉抱怨的次数
≤70次
≤5次
责任异议发生次数
月
1.通过专职驻厂员及时掌握和了解用户使用对产品的使用情况,针对用户提出的问题和要求,及时进行答复或上门服务;针对出现的问题,制定切实可行的整改措施,并逐一落实,提高客户满意度。
2.增强车间过程质量控制意识,严把产品出厂关,确保合格产品出厂,严格抽查和考核制度。
技术质量科
9
更改的错漏次数
≤1次
0次
统计更改错漏次数
年
严格按照TS16949体系关于文件管理方面的要求进行规程、质量计划、作业指导书的拟制、审阅、审批手续;严格按照工艺文件更改评审制度,减少出现错漏的几率。
技术质量科
10
不符合项整改完成率
100%
100%
已完成不符合整改项数/总不符合项数×100%
年
严格按照要求时间完成整改,并按照《2010年中厚板卷厂经济责任制》相关条款进行考核。
技术质量科
11
产品审核质量特征值(QKZ)
≥90%
≥92%
QKZ=100–(缺陷点数/样品数量)
按审核计划
按定产品标准要求进行严格控制,提高产品的质量特性。
技术质量科
12
过程审核符合率
≥80%
≥85%
各相关问题实际得分的总和/各相关问题满分的总和×100%
按审核计划
严严格执行各过程工艺技术和管理文件,提高过程的符合性,并按照《2010年中厚板卷厂经济责任制》相关条款进行考核。
技术质量科
13
六西格玛项目、质量攻关项目计划完成率
≥70%
≥85%
项目目标完成项数/总项目数×100%
年
组织六西格玛项目按DMAI步骤培训、开展活动。
组织攻关小组制定攻关措施进行难题攻关,对达到目标的予以奖励。
技术质量科
14
重大技术难题攻关项目完成率
≥70%
≥70%
攻关目标完成项数/总重大攻关项数×100%
年
积极按技术难题攻关项目开展相关工作。
首席工程师室
15
QC小组成果率
≥65%
≥75%
取得成果的课题数/QC课题注册数×100%
年
积极宣传质量意识,鼓励班组基层员工参与QC小组,组织培训,检查指导QC小组活动,提高成果率。
技术质量科
16
纠正预防措施完成率
100%
100%
已纠正的不符合数或改进数/发生的不符合总数或需改进数
月
严格按照要求时间完成,并按照《2010年中厚板卷厂经济责任制》相关条款进行考核。
技术质量科
17
外部顾客满意度
≥85分
≥85分
满意度调查评分×40%+客观指标评分×60%
季度
严格按照要求时间完成,并按照《2010年中厚板卷厂经济责任制》相关条款进行考核。
技术质量科
18
员工满意度
≥80分
≥85分
回收问卷总得分/回收问卷份数
年
严格按照要求时间完成,并按照《2010年中厚板卷厂经济责任制》相关条款进行考核。
技术质量科
19
质量损失率
≤0.22%
≤0.20%
(内部损失成本+外部损失成本)/工业总产值*100%
月
严格按照要求时间完成,并按照《2010年中厚板卷厂经济责任制》相关条款进行考核。
技术质量科
20
记录保存时限
满足法规及顾客要求
满足法规及顾客要求
查阅记录保存满足法规及顾客要求的情况
年
内审
严格按照要求时间完成,技术质量科不定期进行核查,并按照《2010年中厚板卷厂经济责任制》相关条款进行考核。
技术质量科
21
培训计划完成率
≥95%
≥98%
实际培训班级数/计划培训完成数×100%
季度
严格按照要求时间完成,并按照《2010年中厚板卷厂经济责任制》相关条款进行考核。
综合科
22
不合格品评审时限
≤72小时
≤48小时
统计不合格品评审情况
月
严格按照要求时间完成,并按照《2010年中厚板卷厂经济责任制》相关条款进行考核。
技术质量科
23
重大设备事故次
0
0
统计出现重大设备事故的次数
月
1.加强对设备隐蔽部位的检查,发现问题,及时想出对策,避免重大设备事故的发生。
2.提高计划检修的质量,保证检修项目按质按量完成。
3.加强对设备润滑的监护,保证设备的润滑充足。
设备科
24
设备故障停机率
<3‰
<3‰
产线故障停机时间/日历时间*主机台数)×1000‰
月
1.加强设备点检,保证信息的畅通,发现问题,快速处理。
2.提高计划检修的质量,保证检修项目按质按量完成,避免重复事故的发生。
3.利用生产间隙,合理安排设备小修。
4.提高备件的实物质量,杜绝因备件质量而产生的停机。
设备科
25
检修计划按时执行率
日常100%
日常100%
实际完成数/计划完成数×100%
月
计划
1.合理安排计划检修项目,做好检修工器具的准备及重要项目的检修方案。
2.加强对设备检修过程的跟踪,保证设备的检修参数符合技术要求。
设备科
大中修98%
大中修98%
计划
1.做好检修的四图一表及安全管理工作;落实好人员的安排及待查技术资料的准备。
2.加强检修的安全教育工作,提高员工的安全意识。
3.加强对重要项目的跟踪管理,保证检修项目的参数符合技术要求;做好检修期间的协调工作,保证检修项目按节点完成。
4.落实好检修后项目验收及试车工作,保证设备检修达到检修前预期目的。
设备科
26
现场管理评分
≥92分
≥95分
统计各单位现场检查得分
月
1.推行现场标准化管理,在制定现场标准的过程中加强了员工保持现场环境的意识,同时也为现场检查提供依据。
2.实行科室、车间6S督导员联合交叉检查的检查模式,让各车间督导员在检查中相互交流学习,取长补短,相互促进。
3.推行“红单管理”,有效减少了现场备件摆放数量,使现场备件摆放整齐有序,备件管理严格合理。
综合科
27
工亡事故次数
0
0
统计因工伤亡事故次数
年
1、制定厂部安全工作文件,下达2010年安全工作计划,各单位严格执行。
2、修改完善《安全管理考核办法》3、加强安全培训,提高员工安全意识。
4、加大现场安全违章考核力度,确保安全隐患按期整改率100%。
生产安全科
28
千人重伤率
≤0.3‰
≤0.2‰
负重伤的人数/总人数×1000‰
年
生产安全科
29
月千人负伤率
≤0.3‰
≤0.2‰
出安全事故负伤的人数/总人数×1000‰
月
生产安全科
编制:
审核:
批准: