石油焦煅烧.docx
《石油焦煅烧.docx》由会员分享,可在线阅读,更多相关《石油焦煅烧.docx(38页珍藏版)》请在冰豆网上搜索。
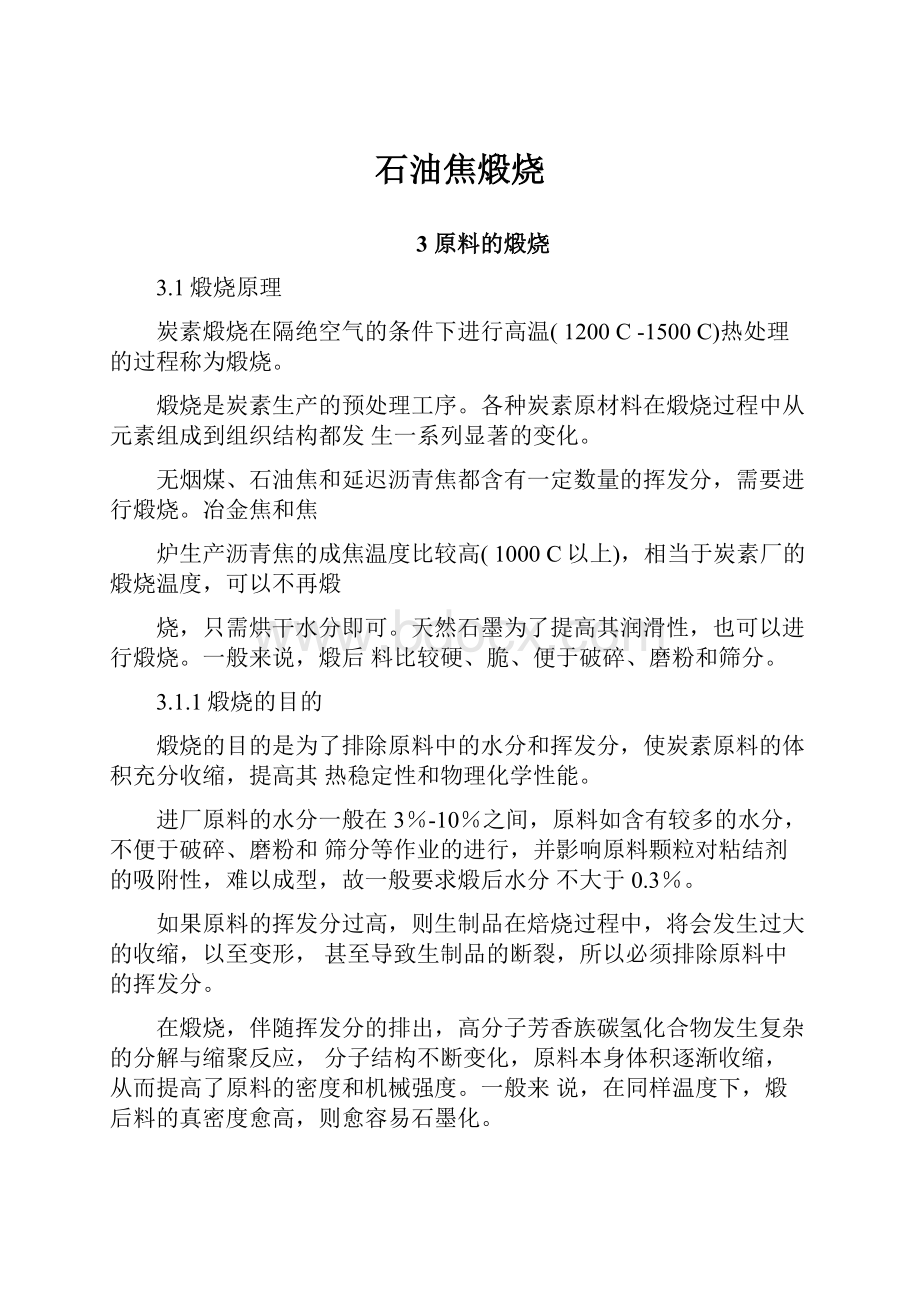
石油焦煅烧
3原料的煅烧
3.1煅烧原理
炭素煅烧在隔绝空气的条件下进行高温(1200C-1500C)热处理的过程称为煅烧。
煅烧是炭素生产的预处理工序。
各种炭素原材料在煅烧过程中从元素组成到组织结构都发生一系列显著的变化。
无烟煤、石油焦和延迟沥青焦都含有一定数量的挥发分,需要进行煅烧。
冶金焦和焦
炉生产沥青焦的成焦温度比较高(1000C以上),相当于炭素厂的煅烧温度,可以不再煅
烧,只需烘干水分即可。
天然石墨为了提高其润滑性,也可以进行煅烧。
一般来说,煅后料比较硬、脆、便于破碎、磨粉和筛分。
3.1.1煅烧的目的
煅烧的目的是为了排除原料中的水分和挥发分,使炭素原料的体积充分收缩,提高其热稳定性和物理化学性能。
进厂原料的水分一般在3%-10%之间,原料如含有较多的水分,不便于破碎、磨粉和筛分等作业的进行,并影响原料颗粒对粘结剂的吸附性,难以成型,故一般要求煅后水分不大于0.3%。
如果原料的挥发分过高,则生制品在焙烧过程中,将会发生过大的收缩,以至变形,甚至导致生制品的断裂,所以必须排除原料中的挥发分。
在煅烧,伴随挥发分的排出,高分子芳香族碳氢化合物发生复杂的分解与缩聚反应,分子结构不断变化,原料本身体积逐渐收缩,从而提高了原料的密度和机械强度。
一般来说,在同样温度下,煅后料的真密度愈高,则愈容易石墨化。
炭素原料煅烧过程中导电性能的提高也是挥发分逸出和分子结构重排的综合结果。
经
过同样温度煅烧后,石油焦的电阻率最低,沥青焦的电阻率略高于石油焦,冶金焦的电阻率又高于沥青焦,无烟煤的电阻率最高。
无烟煤的电阻率不仅与煅烧程度有关,而且与其灰分大小有关。
同一种无烟煤,灰分愈大,煅后电阻率愈高。
随着煅烧温度的提高,炭素原料所含杂质逐渐排除,降低了原料的化学活性。
同时,在煅烧过程中,原料热解逸出的碳氢化合物在原料粒颗粒表面和孔壁沉积一层致密有光泽的热解炭膜,其化学性能稳定,从而提高了煅后料的抗氧化性能。
3.1.2煅烧前后焦炭结构及物理化学能力的变化
3.1.2.1煅烧前后焦炭结构的变化
未煅烧石油焦微晶的层面堆积厚度只Lc和层面直径La有几个纳米,,它们随煅烧温度
的升高不断变化,其变化趋势如图3-1所示。
在700C以前,Lc和La有所缩小。
700C以
上则不断增大。
这种变化趋势与侧链的断裂和结构重排有关,在接近700C时,Lc和La的
缩小说明焦炭内微晶层面结构在这一温度区间内移动和断裂,变得更杂乱和细化,此时挥发分的排出最为剧烈。
图3-2表示了煅烧无烟煤时排出气体总量及其组成。
由此可见,在700C-750C间气体的排出量最大。
各种炭素原料在煅烧过程中,先后进行了热分解和热缩聚以及碳结构的重排,其变化如图3-3所示。
随着缩合反应的进行,发生了晶粒互相接近,导致原料因收缩而致密化。
这种收缩(致密化)直到挥发分排尽才结束。
煅烧过程中,加热制度对煅烧料的晶体尺寸也有影响。
表3-1所示为加热制度对石油
焦晶体尺寸的影响。
由表可见,当加热到700C保温1h后,再升温到1000C,将使煅后
焦的晶粒小。
这也说明,在700C附近,焦炭层面结构正经历断裂和重排。
由于断裂,产
生大量自由基,在此间内保温,促使焦炭中交叉键增多,抑制了焦炭层面间的有序排列。
哥3-3度卩务丁平面两样的变化
4D0T・(叭・(町ISM%?
表3-1加热制度对石油焦微晶尺寸的影响
加热制度
焦种
La,10-6•m
Lc,10-6•m
层间距d002,
10-6•m
50C/h,加热至1000C并在1000C保温1h
执裂焦
八、、^八\、
51
20
3.46
热解焦
51
20
3.49
50C/h,加热至700C并在
700C保温1h,连续升温至
1000C保温1h
执裂焦
八、、^八\、
32
18
3.54
热解焦
35
19
3.53
3.1.1.2煅烧前后焦炭物理化学性质的变化
在煅烧过程中,焦炭的物理化学性质发生了明显的变化。
表3-2列出了我国各种原料
在煅烧前后的理化性质指标。
图3-4表示了一种热裂石油焦随煅烧温度提高,其理化性质
的变化。
(1)煅烧前后焦炭氢含量的变化表3-3表示了热裂焦的真密度、氢含量与煅烧温度
的关系,可以看到在1000C-1300C温度范围内,焦炭的氢含量几乎减少了十分之九。
日本角田三尚等人在实验室条件下,对两种石油焦在煅烧阶段(950C-1400C)进行
元素分析,焦炭A的氮含量为0.6%,焦炭B的氮含量为0.4%,随热处理温度的提高,没有发现有变化。
焦炭A煅烧前的氢含量为3.4%,经1100C热处理后为0.3%,经1400C热处理后为0.1%;焦炭B煅烧前的氢含量为3.3%,经1100C热处理后为0.2%,经1400C热处理后为痕量。
由此可见,随热处理的进行,焦炭发生脱氢反应。
近年来,世界上一些工业发达国家逐渐以氢含量来判断煅烧质量。
对大部分炭素原料来说,氢含量降低到0.05
的温度为最佳煅烧温度。
(2)煅烧前后焦炭硫含量的变化最现实而有效的脱硫方法是高温煅烧,因为高温
表3-2我国各种原料煅烧前后的理化指标
指标名称
石油焦
I
石油焦
n
石油焦
m
石油焦
IV
石油焦
V
沥青焦
无烟煤
I
无烟煤
n
灰分,%煅前
0.11
0.15
0.2
0.17
0.14
0.38
6.47
5.06
煅后
0.35
0.41
0.35
0.54
0.21
0.44
10.04
9.11
真密度,g/cm3煅前
1.61
1.46
1.42
1.37
1.30
1.98
煅后
2.09
2.09
2.08
2.05
2.08
2.06
1.77
1.85
体积密度,g/cm3煅前
0.9
0.82
0.93
0.99
0.94
0.8
1.35
1.35
煅后
0.97
0.99
1.11
1.13
1.15
0.8
1.61
1.59
机械强度,Mpa煅前
3.63
3.00
2.24
6.02
8.72
1.14
13.00
煅后
5.13
4.08
5.72
7.63
7.94
16.8
3.19
硫分,%煅前
0.51
0.40
0.17
1.09
0.38
0.27
0.73
0.41
煅后
0.58
0.57
0.19
1.26
0.42
0.25
0.84
0.73
挥发物,%煅前
2.23
3.23
5.79
11.71
14.95
0.55
7.43
6.31
水分,%煅前
0.95
1.97
0.28
0.34
6.5
0.06
0.49
0.33
煅后粉末电阻率mx10-6
511
493
487
480
523
791
1074
1022
圧3-4热裂石油焦性费蓝躱烧濫度的变比
】一押蚩團痒出量「丁一电殂寧.彳一相对住嵋]I—黑老左
表3-3热裂焦的真密度、氢含量与煅烧温度的关系
煅烧温度,’C
真密度,g/cm3
氢含量,%
煅烧温度,C
真密度,g/cm3
氢含量,%
1000
1.956
0.332
1200
2.096
0.085
1100
2.037
0.188
1300
2.136
0.031
®s-5五柚黑吉鸭■与博烧整崖的关柬s3-a苗商臀議糧魂时的收if
帑華厂篇站縞解健遊,d—戈睛義複阮■厚诒诞化龍損
(3)煅烧前后焦炭的收缩和气孔结构的变化煅烧时焦炭的体积收缩是挥发分排出
所发生的毛细管张力以及结构和化学变化,使焦炭物质致密化而引起的。
图3-6是石油焦和沥青煅烧时的线尺寸变化曲线。
从图中可见,所有曲线都有两个拐点,第一拐点相应于焦炭生成时的温度,显示在该温度下焦炭是受热膨胀的,第二个拐点相应于焦炭的最大收缩期。
它们收缩量的绝对值视焦炭品种和横向交联发展程度而定。
对于气孔结构来说,在700C-1200C之间气孔的总体积大幅度增长,它与700C时气体的大
量析出有关。
由于气体的析出产生了开口气孔。
当温度提高到1200C以上时,气孔的体积由于焦炭收缩而减小,大部分转变为连通的开口气孔。
(4)煅烧前后焦炭导电性的变化焦炭导电性的变化与其结构变化相关,它取决于
共轭n键的形成程度。
煤和焦炭的导电性是碳原子网格中共轭n键体系的离域电子的传导性的反映,它随六角网格层面的增大而增大。
图3-7表示焦炭的电阻率与热处理温度的关系,曲线可分为四个温度区:
500C-700C
时,焦炭的电阻率最大;700C-1200C的范围内,焦炭的电阻率呈直线下降,从107Q・cm
降到10-2cm;1200C-2100C范围内,电阻率变化甚少;2100C以上,电阻率随热处理
高而进一步降低,这与焦炭的石墨化有关。
由此可见,在煅烧过程中,焦炭的电阻率随煅烧温度提高而直线下降,到1200C后转为平缓。
3.1.3煅烧温度与煅烧质量指标
3.1.3.1煅烧温度对焦炭性能的影响
煅烧温度对煅后焦的性能有十分重要的作用。
一般情况下,煅烧温度应高于焙烧温度。
煅烧温度影响到制品焙烧和石墨化时的收缩率。
如煅烧温度过低,炭素原料得不到充分收缩,其热解和聚缩反应不够,使在焙烧和石墨化时收缩率大,引起制品的变形或开裂,
影响产品的成本率;煅烧温度过高(在电煅烧炉中是常见的),则生制品在焙烧和石墨化
时收缩率小,其收缩仅靠粘结剂提供,将使制品结构疏松,制品的体积密度和机械强度低。
为了使煅烧后石油焦收缩更加稳定和晶体排列整齐,适当提高煅烧温度是有重要意义的。
3.1.3.2煅烧温度制定的确定
煅烧温度的确定要视生焦的品种及产品的用途而定。
真密度可以直接反映原料的煅烧程度。
真密度不合格者,需回炉重新煅烧。
根据真密度可以确定煅烧温度。
炭素原料的煅烧温度一般为1250C-1350C。
但对于不同制品所用煅烧温度是不同的。
例如高功率和超高功率电极比普通石墨电极要求原料焦炭的真密度大,所以煅烧温度高,要达到1400C或
更高一些。
而对于炼铝用阳极来说,原料焦炭煅烧温度应尽量接近于焙烧温度1150C左右,
以防止温度过高引起的选择性氧化。
3.1.3.3各种原料煅烧的质量指标
原料的煅烧质量一般用粉末电阻率和真密度两项指标来控制。
原料煅烧程度愈高,煅后料的粉末电阻率愈低,真密度愈大。
各种原料质量控制指标列于表3-4.
3-7若油炊的电阻岸£室滋下韵定〉圻煤趾理禺度的衰基
表3-4原料煅烧质量控制指标
原料种类
粉末电阻率,
mX10-6不大于
真密度,g/cm3不小于
水分,%不大于
石油焦
600
2.04
0.3
沥青焦
650
2.00
0.3
冶金焦
900
1.90
0.3
无烟煤
1300
1.74
0.3
3.2煅烧工艺和设备
焦炭煅烧工艺视所用煅烧设备不同而异,煅烧设备的不同也影响到煅后焦的质量。
煅
烧设备的选型要按照工厂的产品品种、年产量、原料质量、能源供应等情况综合决定。
目前,国内外通用的煅烧炉有以下几种:
1)罐式煅烧炉;2)回转窑;3)电煅烧炉。
3.2.1罐式煅烧炉
罐式炉是将炭素原料放在煅烧罐内,耐火砖火墙传出的热量以辐射方式来间接加热炭素原料的炉子。
常用的有顺流式罐式炉和逆流式罐式炉两种。
罐式煅烧炉车间的生产流程如图3-8所示。
国3-B艺薩程示恋凰
3.2.1.1顺流式罐式煅烧炉的结构和工艺
煅烧物料运动的方向与热气体运动总的流向一致的罐式煅烧炉称为顺流式罐式煅烧炉。
r—WasIgjjid聘空Pt
炉体包括罐式炉的炉膛和加热火道;2)加料、排料和冷却装置;3)煤气管道、挥发分集
合道和控制阀门;4)空气预热室、烟道、排烟机和烟囱。
罐式煅烧炉的炉体(见图3-9)是由若干个用耐火砖砌成的相同结构及垂直配置的煅烧罐所组成。
每个罐体高3-4m罐体内宽为360mm长1.7-1.8m,每四个煅烧罐为一组。
根据产量的需要,每台煅烧炉可配置3-7组,大多数罐式炉由6个组组成,共有24个煅
烧罐。
在每个煅烧罐两侧设有加热火道5-8层,目前多数为6层。
现将6个组的罐式炉的
基本尺寸列于表3-5。
表3-56个组罐式炉的基本尺寸
炉体尺寸(长X宽X高)蓄热室尺寸(长X宽X高)煅烧罐尺寸(长X宽X高)火道尺寸(长X宽X高)火道层数
相邻两蓄热室中心距离
相邻两煅烧罐纵向中心距离(组与组)(同一组)相邻两煅烧罐横向中心距离煅烧罐两侧火道中心距离支承底板表面标咼
15760X9600X9990mm
1240X970X4390mm
1780X360X3400mm
4013X215X479mm
6
1200mm
1330mm
1070mm
2075mm
740mm
5300mm
罐式炉两侧火道的最高温度可达到1300C-1350C。
加热燃料由两部分组成,一部分
是原料煅烧时排出的挥发分,另一部分是外加煤气。
煤气和挥发分在首层火道燃烧,炽热的火焰及燃烧后的高温气流由烟囱及排烟机产生的抽力引导,从首层火道末端向下迂回进入第二层火道,又由第二层火道向下迂回进入第三层火道。
最后,从末层火道进行蓄热室,
在蓄热室通过格子砖的热交换使冷空气加热到400C-500C。
预热后的空气上升到第一层
火道,与挥发份或煤气混合燃烧。
通过蓄热室的烟气,经总烟道和排烟机由烟囱排入大气。
此时,烟气温度还有500C-600C,其余热可以继续利用。
原料在煅烧时排出的挥发分,从煅烧罐上部排出,进入挥发分集合道及分配道,再向下引入第一层火道及第二层火道燃烧。
原料通过炉顶的加料机构间断地或连续地加入罐内,接受罐两侧火道间接加热。
原料在罐内经过预热带排出水汽及一部分挥发分,再往下经过煅烧带(相当于加热火道的1-3
层)。
在此处,火道温度达到1250C-1350C。
原料在煅烧带继续排出挥发分,同时产生体
积收缩,密度、强度不断提高。
最后,原料从煅烧带继续排出挥发分,同时产生体积收缩,密度、强度不断提高。
最后,原料从煅烧罐底部落入带有冷却水套的冷却筒,使灼热的原料迅速冷却下来,再经过密封的排料机构定期或连续排出。
原料在罐内停留时间达18-36h,
每个罐的排料量一般为60-100kg/h。
原料在煅烧罐内停留时间可用(3-1)式计算:
公式(3-1)
式中Z—停留时间,h;
a—煅烧罐的长度,m;
b—煅烧罐的宽度,m;
h—煅烧罐的高度,m
丫一原料平均堆积密度,kg/m3;
Q—每罐每小时排料量,kg/h。
由式(3-1)可知,由于罐体的尺寸是固定的,原料在罐内停留时间,主要受原料的堆积密度及每小时排料量的影响。
当煅烧固定品种时,堆积密度也可视为常数,因此,停留时间直接与每小时排料量呈反比关系,排料量愈多,则原料在罐内停留时间愈短。
(2)顺流式罐式煅烧炉的生产工艺为了保证煅烧物料的挥发分在煅烧过程中能
够均匀地逸出,避免原料在煅烧罐内结焦,对于含挥发分高于12%的石油焦,要加入低挥发分的原料混合煅烧。
混入焦可用沥青焦或回炉重新煅烧的焦炭,其加入量视原料焦的挥发分而定。
一般混合焦的平均挥发分控制在5%-7%,粒度以50mm为宜。
用加料和排料来控制煅烧质量,这是在煅烧生产中常采用的一种方法。
在温度正常的情况下,加料和排料需按时、适量,以保证火道内总有一定的挥发分在燃烧。
一般地说,在炉内温度恒定的情况下,排料量应不使罐内料面的允许高度有所改变,并且排出的热料不应有红料为宜。
而在加料时,供给的原料不应含有过高的水分,而且要加得均匀。
提高罐式煅烧炉产量和质量的关键,是适当提高炉温或延长煅烧带。
虽然罐式煅烧炉
的火道温度最高可达1300C左右,但由于煅烧物料与火道温度之间存在着温度差(一般相
差100C-150C),因此,要保证煅烧的质量,煅烧带(主要是1-3层火道)的温度必须控
制在1250C-1350C。
实践证明,罐式煅烧炉内火道温度是受许多因素制约的。
一般说来影响煅烧炉内火道温度的主要因素有以下几方面:
1)燃料燃烧的影响。
在正常生产中,原料在煅烧时所产生的挥发分是热源的主要部分。
因此,对挥发分必须充分利用,但又要严格控制。
如果挥发分不足,就要用煤气及时进行补充,否则煅烧温度就要下降,影响煅烧质量。
如果挥发分过多,要关闭煤气阀门,调整挥发分的拉板,控制挥发分的给入量。
否则,挥发分过量,个别火道温度过高,会烧坏炉体。
因此,在生产中,为了确保煅烧炉火道温度的恒定,对原材料的配比,挥发分和煤气的用量都要严格控制,及时进行调整。
2)空气量的影响。
经预热的空气进入量的大小也是保证煅烧炉温度火道恒定和煅烧
质量的一个重要环节。
因为只有空气量调整适当,燃料才能充分燃烧,煅烧炉的火道才能
达到高温,煅烧的质量才能得到保证。
空气量不足时,燃烧不充分,火道的温度下降,同
时,还会在进入蓄热室或烟道以后继续燃烧,以致烧坏设备;空气量过多时,就会把火道内的热量带走,使火道温度降低,燃烧质量下降。
3)负压的影响。
炉子负压的控制也是极为重要的。
以每组炉室顶部负压在49-98Pa,罐内负压接近零最为理想。
负压过大,火道内空气流量大,热损失大;负压过小,则挥发分难以抽出,预热空气也将供给不足,燃烧不完全。
因此,在煅烧炉生产中,只有很好地掌握煤气、空气和挥发分的供给量与负压大小的相互关系,并且严格执行生产技术操作规程,才能保证恒定的煅烧温度,提高原料的煅烧质量。
各炭素厂的罐式煅烧炉,虽然炉体结构大同小异,但煅烧原料种类不一样,对煅烧质
量要求不一样,工艺操作条件也有所差别。
现将6层火道的罐式煅烧炉的主要工艺操作条件举例如下:
首层火道温度(C)1250-1350
二层火道温度(C)1250-1350
六层火道温度(C),不大于1250
排烟机前废气温度(C)400-500
首层火道负压(Pa)9.8-14.7
六层火道负压(Pa)78.4-98
原料在罐内停留时间(h)34-36
炭质烧损(%)2-5
排料量(kg/罐・h)少灰混合焦65-75
无烟煤70-80
煅烧后少灰混合焦质量指标
3
真密度(g/cm),不小于2.04
电阻率mx10-6),不大于650
煅烧炉的密封和煅后料的冷却也是重要环节。
如果煅烧炉的密封性能不好,将使煅烧原料烧损,火道温度降低或者烧坏炉体。
特别是排料装置要有好的密封性,否则,灼热的煅后料将大量被氧化,也会把排料设备烧坏。
与此同时,煅后料的冷却装置的冷却效果要好,使煅后料能迅速冷却。
由于石油化工厂已经将釜式焦化改为延迟焦化,使顺流式罐式炉在煅烧高挥发分的延迟焦时产生了不少困难,为此把炉体结构改造为上窄下宽罐体的逆流式罐式炉。
321.2逆流式罐式炉的结构和生产工艺
罐内煅烧物料流向与火道内热气流运动总方向相反的罐式炉叫逆流式罐式炉。
(1)逆流式罐式炉的炉体结构和工作原理逆流式罐式炉的炉体是由煅烧罐、火道
和挥发分道等组成,每四个罐为一组,每座炉可根据产量配置6-7组。
逆流式罐式炉炉体
结构图示于图3-10。
圈3-10逆涯式it式織饶炉、
I—加Q贮斗》2—QI握百料机,融琳(Ji4^加料址it,
逆流式罐式炉在炉体结构上与顺流式罐式炉的区别:
1)逆流式煅烧罐由厚度为80mm的耐火砖砌筑而成,带有适当的锥度,上部内宽为
260mm下部内宽为360mm由于截面自上而下逐渐扩大,使原料在下移的过程中容易产生相对位移而松动,从而为避免结焦和堵塞炉子创造了有利条件。
2)逆流式罐式炉的水平火道增加到八层,其目的在于加长煅烧带,增加原料在罐内的煅烧时间,以便充分利用挥发分而达到高产优质的目的。
3)逆流式煅烧罐还把挥发分出口设置得高于煅烧料面,并且加大了挥发分出口和分道的截面,以便于挥发分顺利排出。
4)逆流式煅烧罐取消了蓄热室,采用加热火道所传递的热量和煅后料的余热来加热炉底空气预热道,从而把冷空气加热,其目的在于简化炉体结构,并利用余热。
煅烧罐的两侧是加热火道,火道是沿罐体的高度配置的,每层火道是用硅砖和火道盖板砌筑的。
煅料从第八层火道喷嘴喷入(或从第五层火道喷嘴喷入),燃烧后沿火道由下向上迂回流动,最后经集合烟道到余热锅炉或副烟道排出。
由于煅烧料是由上往下移动,而热烟气由下往上迂回流动,就使物料与烟气在炉内形成了逆流,从而提高了热的利用率。
挥发分总通道是设计在煅烧罐的上部,每两个煅烧罐的挥发分通道互相联通,同时还与边墙的挥发分垂直道相连。
挥发分从罐内逸出后,就直接进入挥发分垂直道,然后通过挥发物的拉板调节或分别进入第一、第八和第五层火道,或直接进入余热锅炉。
挥发分垂直道具有清扫容易,减少炉顶散热和改善操作条件等特点。
第八层火道的下部还有两层空气预热道,冷空气从调节风门进入第十层空气预热道,经十、九两层预热后就可进入第八层或第五层火道,与煤气或挥发分混合而燃烧。
预热空气量是由第九层空气预热道末端的空气拉板来调节的。
罐式煅烧炉的喷火嘴是用两种形状简单的异形砖砌成的。
它的结构特点是:
煤气和挥发物分别进入火道,因而煤气和挥发物就可以在该处同时使用。
炉子的总负压是由烟道闸门、锅炉和副烟道闸门来调节的。
而每层火道的负压则是由该层火道的负压拉板来控制的。
(2)逆流式罐式炉的生产工艺逆流式罐式炉在生产工艺上除了与顺流式罐式炉具
有相同之处外,还有以下不同点:
1)在逆流罐式炉的生产过程中,保持低料面操作,可以保证挥发分出口畅通无阻。
适当提高首层火道温度,使延迟焦中的挥发分在短时间内排出,避免结焦堵炉。
2)在逆流罐式炉的生产中,煅烧料料面的高低是由自动探料装置控制的,它能使煅烧料面终保持在一定高度范围内。
当罐内料面低于控制位置的,加料装置自动加料;当料面达到控制位置时,加料装置停止加料。
连续自动加料和连续排料,保证了挥发分均匀排出,使罐内煅烧料不断松动,可防止结焦。
3)逆流罐式炉进行延迟焦这类高挥发分烧时,在操作上要求较高,对负压和空气量必须严加控制,要保持一定负压,使挥发分均匀排出和充分燃烧。
4)煅烧混合焦时,沥青焦应破碎到20mm以下(螺旋加料机的构造限制),并在预碎
时要求配比准确,混合均匀,以避免结焦现象。
3.2.1.3罐式炉的优缺点
罐式炉虽然形式较老,却有它的优点:
1)热利用率高。
这种炉子可以利用原料煅烧时排出的挥发分。
煅烧石油焦的挥发分热值高达5837kJ/m3,几乎与发生炉煤气的热值相当。
如煅前焦的挥发分较高,可以停用煤气。
正常生产时,燃料自给有余,节约燃料费用。
2)煅烧料缓慢地通过炉膛,挥发分在焦炭表面热解,形成热解炭膜,提高了焦炭强度。
而且因煅烧料移动缓慢,耐火砖磨损较小。
3)由于罐式炉煅烧罐是密闭的,在非排料情况下是很少有空