延迟焦化事故案例分析.docx
《延迟焦化事故案例分析.docx》由会员分享,可在线阅读,更多相关《延迟焦化事故案例分析.docx(21页珍藏版)》请在冰豆网上搜索。
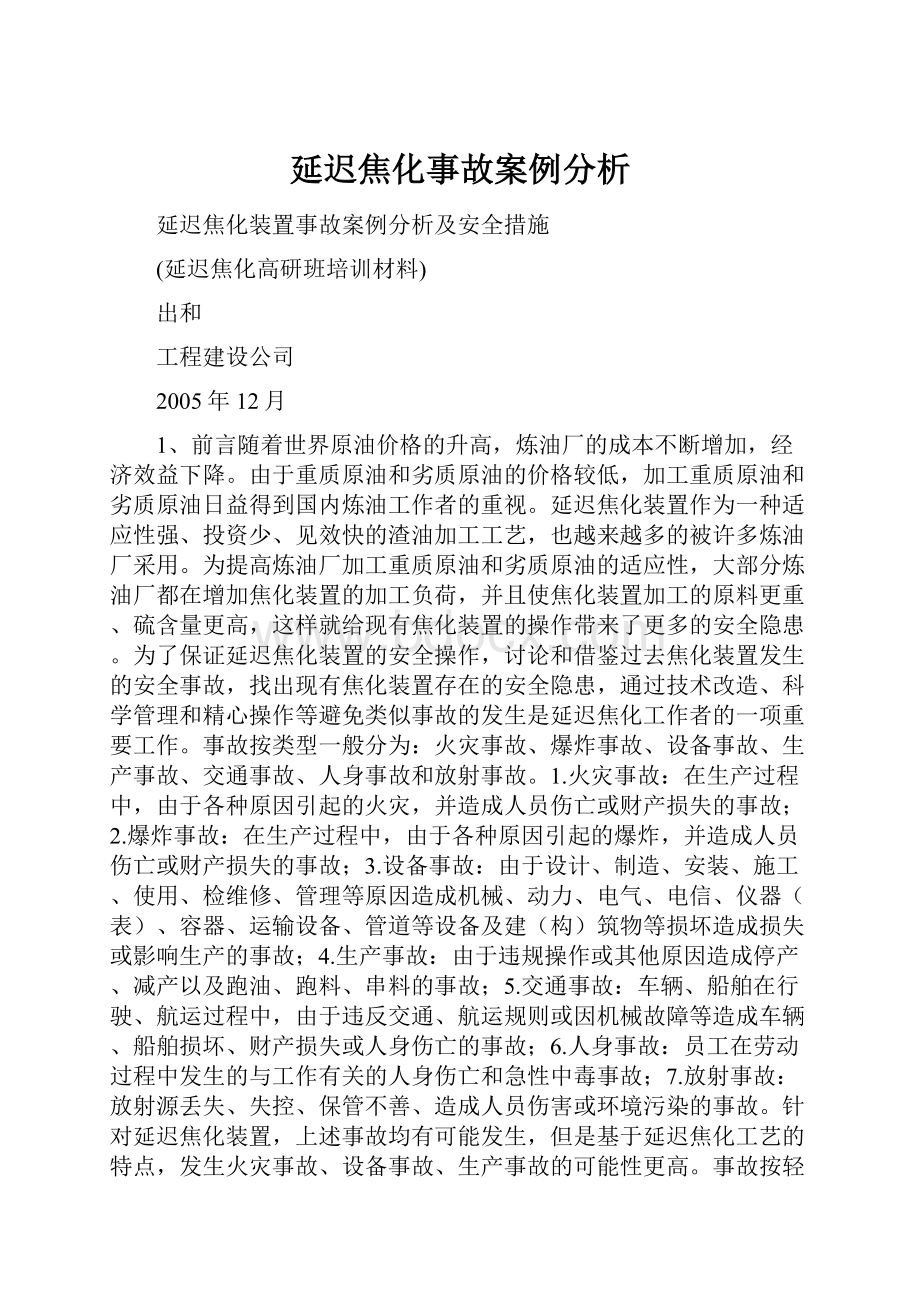
延迟焦化事故案例分析
延迟焦化装置事故案例分析及安全措施
(延迟焦化高研班培训材料)
出和
工程建设公司
2005年12月
1、前言随着世界原油价格的升高,炼油厂的成本不断增加,经济效益下降。
由于重质原油和劣质原油的价格较低,加工重质原油和劣质原油日益得到国内炼油工作者的重视。
延迟焦化装置作为一种适应性强、投资少、见效快的渣油加工工艺,也越来越多的被许多炼油厂采用。
为提高炼油厂加工重质原油和劣质原油的适应性,大部分炼油厂都在增加焦化装置的加工负荷,并且使焦化装置加工的原料更重、硫含量更高,这样就给现有焦化装置的操作带来了更多的安全隐患。
为了保证延迟焦化装置的安全操作,讨论和借鉴过去焦化装置发生的安全事故,找出现有焦化装置存在的安全隐患,通过技术改造、科学管理和精心操作等避免类似事故的发生是延迟焦化工作者的一项重要工作。
事故按类型一般分为:
火灾事故、爆炸事故、设备事故、生产事故、交通事故、人身事故和放射事故。
1.火灾事故:
在生产过程中,由于各种原因引起的火灾,并造成人员伤亡或财产损失的事故;2.爆炸事故:
在生产过程中,由于各种原因引起的爆炸,并造成人员伤亡或财产损失的事故;3.设备事故:
由于设计、制造、安装、施工、使用、检维修、管理等原因造成机械、动力、电气、电信、仪器(表)、容器、运输设备、管道等设备及建(构)筑物等损坏造成损失或影响生产的事故;4.生产事故:
由于违规操作或其他原因造成停产、减产以及跑油、跑料、串料的事故;5.交通事故:
车辆、船舶在行驶、航运过程中,由于违反交通、航运规则或因机械故障等造成车辆、船舶损坏、财产损失或人身伤亡的事故;6.人身事故:
员工在劳动过程中发生的与工作有关的人身伤亡和急性中毒事故;7.放射事故:
放射源丢失、失控、保管不善、造成人员伤害或环境污染的事故。
针对延迟焦化装置,上述事故均有可能发生,但是基于延迟焦化工艺的特点,发生火灾事故、设备事故、生产事故的可能性更高。
事故按轻重一般分为:
一般事故、重大事故、特大事故。
一般事故:
(1)一次造成1~9人重伤;
(2)或一次造成1~2人死亡;(3)或一次直接经济损失在10万元及以上、100万元以下(不含100万元);(4)或炼化、销售企业一次跑、冒、漏油(料)及油品变质在10t及以上;油田企业一次跑油在30t及以上;管道储运企业一次跑油在100t及以上;海上发生一次跑油在1t及以上;销售企业一次混油混入量100t及以上;(5)或炼化企业一次造成3套及以上生产装置或全厂停产,影响日产量50%及以上。
重大事故:
(1)一次事故造成10人及以上重伤;
(2)或一次事故造成3~9人死亡;(3)或一次事故造成直接经济损失100万元及以上,500万元以下(不含500万元)。
特大事故:
(1)一次事故造成10人及以上死亡;
(2)或一次事故直接经济损失500万元及以上;目前焦化装置发生的事故大部分是一般性事故,也有重大事故和特大事故。
延迟焦化装置是炼油厂比较危险的装置之一,国内的每套延迟焦化装置或多或少都发生过安全事故,从安全事故的发生及处理中得到了许多宝贵的经验,也促进了国内焦化技术的发展,本文仅列举了部分延迟焦化装置发生的安全事故案例,供大家进行讨论、分析和参考。
2、国内部分延迟焦化装置安全事故案例及分析2.1、加热炉进料泵抽空导致装置停工(辐射泵进料温度不能太低,否则因为原料油的组分太轻,会导致辐射泵抽空;原料中的轻组分含量小于500度的不能大于6%)
(1)现象:
南方某炼厂的焦化装置,某天18:
00加热炉进料量突然由165t/h降至122t/h,检查泵入口过滤器,运行正常,切换备用泵后,进料量继续下降,18:
30降至联锁值使加热炉熄火,后开蒸汽泵维持,18:
45开1号辐射泵密封泄漏着火,切换到2号辐射泵流量波动,点火慢慢恢复生产,第二天23:
15,2号辐射泵又抽空,1号辐射泵正在维修,导致装置紧急停工。
(2)检查:
泵入口过滤器未堵,渣油换热器未漏,分馏塔底无焦粉,液位计无异常,辐射泵无机械故障。
(3)原因:
常减压装置改变原油,减压塔操作不平稳,渣油性质变化较大,未通知焦化装置及时调整操作。
辐射泵抽空前渣油性质:
比重0.9945,粘度236mm2/s,残炭17.6wt%,<500℃含量5%。
辐射泵抽空时渣油性质:
比重0.9800,粘度214mm2/s,残炭15.2wt%,<500℃含量10.2%。
(4)措施:
控制焦化原料渣油性质的变化X围,开好减压塔,适当提高分馏塔的压力,控制分馏塔底温度不低于330℃,使分馏塔底渣油中轻组分充分闪蒸。
2.2、辐射进料泵入口管线设计不合理,泵抽空导致装置不能开工
(1)现象:
中原某炼厂一焦化装置,开工过程中,柴油循环升温脱水到200℃,蜡油循环升温到440℃,在循环过程中分馏塔底泵一直采用蒸汽往复泵,切换渣油后,开国外引进的辐射进料泵,发现辐射泵抽空,认为脱水不干净,切换蒸汽往复泵继续循环脱水,后分析分馏塔底油含水合格,切换离心泵,辐射泵仍然抽空。
反复几次未解决泵的抽空问题,被迫退油停工。
(2)检查:
原料性质符合设计要求,<500℃含量3.5%,水含量0.05%;泵用封油含水量及馏程X围合格,封油注入管限流孔板完好,分馏塔底及过滤器无杂物,辐射泵无机械故障。
(3)原因:
分馏塔底过滤器安装在地面上,辐射泵入口管线太长,并且存在两个较大的袋型,泵入口阻力大,导致辐射泵抽空。
(4)措施:
装置退油,把泵入口过滤器重新安装到分馏塔底的平台上,保证了辐射泵入口管线无袋型且步步降低。
重新进油开工,辐射泵不再抽空,装置开车成功。
2.3、焦化炉出口憋压,注汽单向阀法兰垫片外圈吹掉,高温渣油泄漏着火,装置停工
(1)现象:
沿海某炼厂焦化装置,某日21:
50加热炉对流室外突然着火,立即切断加热炉进料,迅速报警,出动消防车辆数十辆,23:
00火被扑灭,无人伤亡.
熄火停泵又致使炉管凝死结焦,导致装置停工,炉管抽出清焦,检修时间延长。
(2)原因:
操作工切换四通阀,由B塔切入A塔后,应该关闭去B塔的切断球阀BV-2,却误操作为关闭去A塔的切断球阀BV-1,导致炉出口憋压,加热炉入口压力升高,因泵出口压力最高可达5.0Mpa,最终导致加热炉对流室A组入口DN40注汽管线单向阀上法兰金属缠绕垫片外圈吹掉.350℃的渣油泄漏着火。
(3)措施:
四通阀加联锁:
四通阀通油一侧的切断球阀不能关闭;切断球阀不打开,四通阀不能向该侧切换;加热炉进料调节阀加联锁:
当加热炉憋压时,流量低低,应切断燃料气、切断进料、炉管通蒸汽。
提高加热炉出口管线、阀门、法兰及垫片的等级和质量。
降低加热炉进料泵的扬程,加强操作工培训,切换四通阀要两人确认。
2.4、焦化开工时放空塔憋压,导致放空塔爆炸
(1)现象:
沿海某炼厂焦化装置,开工过程中,放空塔的压力突然升高,安全阀起跳未起作用,导致放空塔底部爆炸,爆炸开口约一米多长,装置被迫退油,幸好未造成人员伤亡。
(2)原因:
开工过程中甩油罐带水,低温状态下油在上水在下,当温度升高到水汽化温度时,大量的水突然汽化,蒸汽及油气汽化到放空塔,致使放空塔压力突然升高,放空塔顶安全阀起跳后路不畅,使压力超过放空塔的设计压力导致爆炸。
(3)措施:
放空塔顶安全阀放空由去空冷器后放空开为去焦池敞开放空,保证放空塔的压力不超压,开工循环时及时切除甩油罐的存水,或用甩油泵抽含水油送至系统。
精心操作,密切注意所有设备的压力变化,做到及时处理。
2.5、焦炭塔进料温度低产生沥青导致无法除焦,停工处理(防止炉出口温度过低,导致无法产焦,而生成沥青)。
(1)现象:
北方某炼厂焦化装置,开工已基本成功,后辐射室出口温度降低到450℃,仍进焦炭塔约6小时,后来发现不对紧急停炉,此时焦炭塔内的油已成沥青,无法冷焦,自然冷却后又无法出焦,最终采用人工挖焦,花费近一个月的时间才把焦炭清除出塔。
(2)原因:
渣油已进加热炉并切换四通阀生焦4小时,加热炉对流渣油加热段两路偏流,其中一路出口温度超高(约400℃),操作工经验不足,紧急降低炉火,使对流出口温度降低到工艺卡片要求的360℃以下,但是辐射室出口温度也随之降低到约450℃,致使在焦炭塔内未产生结焦反应而产生软沥青。
(3)措施:
加热炉对流渣油加热段两路改为一路,防止偏流。
采用人工挖焦后,重新开工。
把辐射室出口温度作为最主要的控制指标,要求497±1℃。
对流出口温度高时要适当降低入口温度,适当降低过剩空气系数。
2.6、高温硫腐蚀或选材不合理导致管线或法兰泄漏着火,迫使装置停工。
(1)沿江某炼油厂60万吨/年延迟焦化装置,高温蜡油管线材质为Cr5Mo,而蒸汽吹扫线材质为碳钢,异种钢焊接,开工几天后焊缝开裂,蜡油外喷着火,装置紧急停工。
(2)某炼油厂50万吨/年延迟焦化装置,辐射泵出口高温渣油管线设计为Cr5Mo,而实际安装的为15CrMo,在加工高硫渣油一年后,管线腐蚀穿孔,高温渣油外喷着火,装置紧急停工。
停工后对存在高温硫腐蚀的所有管道进行检查和更换。
(3)某炼油厂80万吨/年延迟焦化装置,辐射泵出口高温渣油管线设计为Cr5Mo,在加工高硫渣油一段时间后,管线腐蚀减薄,在切换备用辐射泵时,高温渣油外喷着大火,导致人员伤亡和财产重大损失,装置紧急停工。
(4)某炼油厂100万吨/年延迟焦化装置,急冷油阀门泄漏,油滴到下部的高温阀门上,自然着火,烧毁焦炭塔附近的仪表电缆和电工电缆,装置停工检修。
最近还有一炼油厂,塔顶循环回流管线泄漏,油滴到下部的高温阀门上,自然着火,灭火及时未造成重大损失,但致使装置停工。
(5)某炼油厂100万吨/年延迟焦化装置,加热炉入口仪表法兰螺栓材质较差,开工一段时间后强度减弱断开,导致高温渣油外泄着火,后检查所有高温部位仪表法兰螺栓材质,并进行更换。
(6)沿海某炼油厂60万吨/年延迟焦化装置,加热炉入口管道腐蚀减薄,泄漏着火,导致人员伤亡,装置停工。
2.7、操作不当导致油品泄漏着火,迫使装置停工。
(1)东北某炼油厂160万吨/年延迟焦化装置,开工进油时蜡油渣油换热器未及时热紧,夜间升温时泄漏着火,导致装置停工退油。
(2)某炼油厂120万吨/年延迟焦化装置中的一台焦化炉炉管烧穿导致着火,主要是流量偏流,其中一路偏流结焦,炉管表面温度升高,操作工未及时发现,长时间超过Cr9Mo的允许温度操作,导致炉管烧穿。
处理措施是紧急停炉更换烧穿的炉管,增加炉管表面温度计及炉内火燃检测器。
(3)东北某炼油厂40万吨/年延迟焦化装置,汽油切水带油并排污水沟,使污水沟含轻油太多,汽车通过时点火引着并爆炸,导致仪表室内仪表烧毁,装置停工检修。
(4)某炼油厂焦化装置冷切焦时急冷油未关,冷焦后卸完底盖,高温油品流出自然并导致焦炭着火,装置停工,损失严重。
整改后重新开工。
2.8、操作及设备运转不当导致的事故或装置停工。
(1)早期沿江某炼油厂的60万吨/年带堵焦阀的延迟焦化装置,预热焦炭塔的凝缩油未甩净,切换四通阀时导致焦炭塔突沸冲塔,引起分馏塔冲塔,重油进入火炬放空管线,迫使炼油厂内的部分装置紧急停工,清除气体管道内的污油花费大量的人力和物力,停工损失严重。
(2)沿海某炼油厂100万吨/年延迟焦化装置,生焦时间延长,泡沫层超高冒顶,导致焦炭塔冲塔,引起分馏塔底过滤器堵死,停塔底循环线清除焦粉。
(3)东北某炼油厂100万吨/年延迟焦化装置,四通阀进焊渣,开工进油时无法灵活使用,硬性开关导致阀门损坏,影响开工。
(4)东北某炼油厂100万吨/年延迟焦化装置,焦炭塔底着火引起保温材料着火,迫使装置紧急停工,更换阻燃保温材料。
(5)东北某炼油厂100万吨/年延迟焦化装置,开工进渣油切换四通阀时,四通阀两侧的隔断阀卡死未及时打开,加热炉憋压炉管结焦,导致装置停工退油。
(6)某炼油厂延迟焦化装置,除焦开底盖时,热水流出烫伤除焦人员,造成经济损失。
(7)某炼油厂100万吨/年延迟焦化装置,提高装置处理量,超负荷操作,焦炭塔料位超高,焦炭塔出口管线结焦严重,焦炭塔憋压安全阀起跳,影响安全生产。
(8)南方某炼油厂100万吨/年延迟焦化装置,除焦开顶盖(闸阀式顶盖)时,误开正在生焦的焦炭塔的顶盖,高温油气泄漏,造成附近居民疏散,装置停工处理。
(9)某炼油厂焦化装置采用的水涡轮不好用,又没有风动马达做备用,造成切一塔焦换一次水涡轮,使开工十分不顺利,影响正常生产。
(10)某炼油厂焦化装置的甩油阀采用国产球阀,执行机构到位,而阀门关闭不到位,切换四通阀后,导致高温渣油去甩油罐生焦,装置被迫停工清焦。
(11)某炼油厂焦化装置的冷焦水罐由于进入空气,使硫化亚铁自然发生爆炸。
(12)某炼油厂焦化装置切焦器安装不好,风动马达反转,造成切焦器掉入塔内,更换备用切焦器,影响切焦操作;有的焦化装置切焦器掉入塔内,无备用切焦器,只能派潜水员进塔打捞;还有的焦化装置切焦时焦炭塌方卡钻,强行提钻导致钢丝绳断裂,影响装置的正常操作。
2.9、弹丸焦的产生将影响装置的安全生产
(1)产生弹丸焦对装置的长周期和安全生产十分不利,焦炭塔振动严重,出焦容易塌方卡钻,卸底盖容易塌方伤人,冷焦困难并且放水线容易堵塞,吹汽时带到放空系统的弹丸焦容易损坏机泵,弹丸焦在地面上容易使工人滑倒摔伤,弹丸焦较硬不易破碎。
(2)某炼油厂焦化装置产生了弹丸焦,冷焦放水管道堵塞,操作工人卸法兰疏通,由于热水喷出,工人自绞手架上摔倒而受重伤。
另外,除焦工人在塔底平台上操作时经常滑倒摔伤。
(3)
根据国外资料报道和国内经验:
原料的API小于7及原料的残炭/沥青质小于1.4~1.6会产生弹丸焦,当API大于10及原料的残炭/沥青质大于2.0才不会产生弹丸焦,另外原料中的金属含量、操作温度、循环比、空塔气速等对产生弹丸焦也有一定的影响。
因此在设计和生产当中应尽可能避免生成弹丸焦,保证装置长期安全操作。
3、国外部分延迟焦化装置安全事故案例及分析3.1、美国一焦化装置分馏塔充压时发生爆炸
(1)事故发生过程:
1959年的冬天,美国一套还用钢丝绳拉焦的焦化装置,在开工前需要向整个系统用重柴油和渣油的混合油充油,目的是排除空气、检测法兰和堵头的泄漏、校验安全阀定压,充油是自原料罐用泵抽出经加热炉到焦炭塔再由焦炭塔顶出口线到分馏塔,分馏塔顶放空线打开,用油把空气赶出,由于天气寒冷,夜班工人没有打开放空阀。
由于后部系统憋压,充油速度较慢,充油泵发热,操作人员认为,天气冷油的粘度大,压降大,泵入口过滤器堵塞,为此,拆修过滤器,加热炉点火升温,4:
30炉前压力0.63Mpa,5:
30炉前压力0.91Mpa,炉出口温度232℃,操作人员认为加热炉压降增加,当焦炭塔顶压力升高到1.4Mpa时引起操作工注意,此时炉前压力1.76Mpa,判断分馏塔顶放空线未打开,派操作工去开塔顶放空阀,发现阀门打不开,找到扳手后,炉前压力已达到2.1Mpa,为时已晚,6:
00一声猛烈爆炸,分馏塔炸开。
(2)事故损失:
找到扳手的操作工死亡,操作室的三名操作工由于窗户塌陷受伤,部分管线损伤,附近居民由于爆炸的冲击波人员受轻伤,财产有轻微损失。
当地矿务局估计此次爆炸相当于363公斤固体**。
(3)事故原因:
爆炸是由于分馏塔中油气气体自然着火所引起,在系统充压前,要求用柴油冲洗阀门、排放口、液面计和压力表接头,冲洗油进入系统中去,冲洗油易挥发,232℃约蒸发20%,自然点低。
当向分馏塔充油时,系统的空气及油气全部被顶至分馏塔,分馏塔顶放空线未打开时,该气体被压缩,这种情况的压缩近似绝热压缩,自开始到爆炸时的压缩比约为18,估计热油表面的油气温度为260℃,该温度足以引起自然和爆炸。
(4)几点看法:
爆炸应具备可爆炸介质,浓度在爆炸极限X围内,还应有点火条件,不能只考虑人为点火,高温油品的自然、静电打火更应引起重视;天然气置换空气应直接置换,不应在蒸汽清扫后马上天然气置换空气;热裂化装置不能用循环产生的气体置换空气,避免爆炸,首先应避免油与空气接触的开工过程。
3.2、焦炭塔底进料线DN100的排水线误开,导致焦炭塔底着火。
(1)事故发生过程:
国外一套一炉三塔的焦化装置,1号塔装满焦炭并冷却完成,操作工准备开盖除焦,2号塔正在生焦后期,3号塔正在预热。
两个塔平行进料时,从一个塔切换到另一个塔约需要2小时。
根据操作程序,操作工把塔内的水排净后就交给除焦班,操作工检查时发现排凝阀关闭,操作工误操作打开了2号塔底部的DN100排凝阀,这里面有500℃的渣油,刚开时没发生情况,待渣油及焦炭流出后,遇到空气着火。
(2)事故损失:
及时通知主控室处理,切断相关阀门,没有人员伤亡,该平台上的电缆、仪表、保温、梯子和管线垫片均被烧毁,停工18天。
(3)事故原因:
操作工误操作,把生焦塔当为除焦塔。
(4)几点看法:
经常开关的阀门应设警示标志,排凝阀应加盲板或联锁机构,加强操作工培训,要有机灵清醒的操作工,开阀前要确定内部介质的温度和压力,必要时由两个操作工进行确认,焦炭塔平台应在两侧均设逃生梯子,建议都用斜梯。
3.3、焦化炉管碳化导致破裂
(1)焦化炉管碳化导致破裂,国内外经常发生焦化炉管烧穿引起加热炉内着火,装置停工。
(2)国外某炼油厂焦化装置对炉管碳化的分析:
炉管严重的碳化造成低合金辐射管的毁坏,加热炉运行6年后,碳化是不均匀的,迎火面比背火面要严重,较热的炉壁管比温度底的炉管碳化严重的多,碳化使炉管损失金属并脆化,一次在吹蒸汽时产生裂纹,用锤子一敲另一根也裂了,138根炉管全部更换。
裂纹的断面显示,由焦炭、氧化铁、和铁铬化合物组成的低密度层紧密的附着在炉管内壁,管壁被较厚的多层带铁焦炭沉积物所覆盖,导致高温晶间碳扩散并形成复杂的铬-铁化合物(铬-铁-碳化合物的络合物),此为脆化的基本原因。
(3)建议:
避免管壁超温操作,特别是在烧焦和蒸汽清焦时,控制管壁温度防止高温碳化,碳化后的炉管用超声波测厚较难发现炉管减薄,最好定期金相分析。
3.4、焦炭塔裙座焊缝开裂脱落导致蒸汽管线断裂
(1)现象:
美国一套焦化装置,建成投产11年后,当焦炭塔充水冷焦期间,塔体与裙座的焊缝突然断裂脱落,塔体下沉约356mm,导致两条DN25的蒸汽管线断裂,幸运的是油气管线还没问题,
(2)处理措施:
放净焦炭塔内的水,用缆绳栓住塔顶防止塔体倾斜,底盖不能用小车拆卸,通过人工慢慢卸下来。
水力除焦完成后,检测发现裙座的每个焊逢全部损坏,许多焊逢已开裂许多时间,检查另一个焦炭塔也有开裂现象,停工后,把塔吊起到正常位置,重新安装加强的裙座并对塔进行修复,使塔体与裙座的连接比原来更牢固。
(3)原因:
塔体与裙座的断裂是因为焊接材料的疲劳造成的,金属疲劳是因为其每天都从常温到500℃X围内反复加热和冷却。
(4)建议:
定期检查塔体与裙座的焊缝,降低或放缓加热及冷却速度。
3.5、焦化装置流程考虑不周,焦化操作的失误,导致加氢装置停工(高压和低压相连时,应考虑到串压,要加单向阀,防止出现问题时,高压向低压串压)。
(1)基本流程:
焦化吸收柴油泵出口一路去柴油吸收塔,另一路出装置去柴油加氢装置进料泵入口,经升压加热后去加氢反应器。
(2)事故过程及分析:
焦化吸收柴油泵在切换过程中发生抽空,被迫停泵,贫气自柴油吸收塔返回到柴油线,并串到柴油加氢装置进料泵入口,导致加氢装置进料泵抽空,尽管加氢装置采取了措施,没有进入加氢反应器的这段时间使得催化剂失活,装置停工换剂。
(3)建议:
装置的设计应考虑全厂的情况,应将整个炼油厂操作结合在一起,考虑由于本装置的操作失误而引起的其他装置的操作问题。
操作人员应加强迅速联系,加强对发生事故后处理能力的培训。
设计措施:
去吸收塔的柴油线加单向阀,加氢装置设缓冲罐,柴油出装置泵和吸收柴油泵分开。
3.6、焦炭塔井架断裂,导致装置停工。
(1)基本情况:
美国一个运行20年的焦化装置,建设有两个焦炭塔A、B,这两个塔的井架是靠塔顶上焊接的1/2英寸厚的圆环支撑的,塔的井架是用平台连接,类似国内的半井架,这两个井架发生断裂,导致装置停工检修。
(2)断裂原因:
发生断裂的前两个月,A塔冷却循环阶段曾发生不寻常的振动,造成钻杆在塔底偏离中心,顶部平台摇动,顶部传送设备不对中,两个塔间的通道扭曲变形,测量后发现A塔井架顶部向西倾斜30英寸。
(3)处理措施:
撤掉支撑环的保温发现焊缝全部开裂,塔西侧支撑圈掉到焊缝下3英寸,塔东侧支撑圈抬到焊缝上3英寸,撤掉另一个塔时也发现类似的情况,装置停工,利用千斤顶和铁块把井架调整到正常状态,重新焊接加固。
3.7、分馏塔入口管线弯头漏油着大火,导致装置停工,损失惨重(1)着火过程:
1993年8月,一个10塔的焦化装置着火,火灾是由地面上的DN200的管线弯头漏油引起,渣油被加热到约400℃,带压送到分馏塔,管线弯头漏油闪爆成为一个大火球,大火从地面蔓延到46米的切焦平台,6分钟内大火蔓延成76X15X48米的X围,急冷油管线被烧裂,更加大了火势,导致井架坍塌,给消防人员造成严重威胁,大火持续了5个小时,损失惨重。
(2)经验教训:
加工高硫油后,管线、管件、阀门均应升级更换;加大消防水系统的能力,易着火部位应设置独立的喷淋系统,并能够在主控室远程操作;着火后的逃生道路应至少设计两条,一旦一条被大火堵死,还有其他逃生渠道。
3.8、国外其他事故
(1)1998年11月,由于天气原因造成停电一段时间,迫使装置重新开工,操作工打开了带压焦炭的塔底的盖,看内部是不是产生焦炭,结果热油自塔内流出,遇见空气着火,造成六名操作人员死亡。
(2)美国某炼油厂延迟焦化装置,水力除焦时,发现高压阀门开关不灵,在检修阀门时,高压水管道未泄压,致使高压水喷出把人切伤。
(3)据文献报道,美国某炼油厂延迟焦化装置,在7年的生产过程中,有15名工人死于焦化的火灾中,1998年5次火灾事故,有8名工人伤亡。
4、目前国内延迟焦化装置存在的安全隐患XX现有运行的焦化装置约25套,其中2000年前建成投产的约15套,2000年后建成投产的约10套。
这些装置都不同程度的存在一定的安全隐患。
安全隐患管理规定:
贯彻“安全第一,预防为主”的方针,加强对重大事故隐患的管理,预防重大事故的发生。
安全隐患也分为:
重大事故隐患和特别重大事故隐患。
重大事故隐患是指可能导致重大人身伤亡或者重大经济损失的事故隐患,是指可能造成死亡10人以上,或直接经济损失500万元以上的事故隐。
特别重大事故隐患是指可能造成死亡50人以上,或直接经济损失1000万元以上的事故隐患。
针对延迟焦化装置,目前存在的安全事故隐患估计有:
(1)
基础理论、设计软件、材料研究的可靠性对延迟焦化装置应用的基础理论主要有:
热裂化反应机理、反应动力学-由于研究不深,对焦化过程了解不够,只有一些定性的概念,不同原料的定量分析研究数据缺乏,按此分析问题或处理问题难免产生误导。
设计软件的开发也涉及到应用许多理论知识,如传热理论、精馏原理、传质理论、流体力学等,虽然上述理论都是一些经典的基础知识,但是不同人研究的定量表达式却不同,这说明不同设计软件设计出的结果是不同的,采用不可靠的软件设计出的装置就存在一定的安全隐患。
金属材料金相分析的准确性,不同材料在不同条件下的使用寿命研究的准确性,不同材料在不同条件下的强度研究的准确性,都影响到材料的使用,根据基础研究使用材料只是符合相关标准规X,但不一定万无一失,随着基础理论的研究和发展,会发现过去的基础理论指导下的工程装置也存在一定的隐患。
(2)
设计及操作的时空性焦化装置的安全隐患之一是人们的经验主义,如认为某炼油厂延迟焦化装置的某一个单元是如何操作,我厂也可以这样操作;某炼油厂延迟焦化装置的某一个事故是如何处理,我厂发生类似事故也可以这样处理;某炼油厂延迟焦化装置某设备材质采用碳钢,我厂相应设备材质采用碳钢也没问题;加工原料相同,设计选材也可一样;今年装置安全操作,明年也不会有大问题等等的现象比较普遍。
设计有针对性、地域性以及原料的适应性,所有设备都有其使用寿命与生产制造的特殊性。
(3)
设备及管道材质不适合高硫原料的加工,腐蚀严重,特别是早期设计的焦化装置,许多高温管道及阀门仍然是碳钢材质,虽然现在没有发生事故,但是存在安全隐患;设备及管道的使用条件发生变化,设备及管道的使用寿命到期,但仍超期使用,存在安全隐患;
(4)
早期设计规X要求较低,安全设计考虑不周全,自动化水平较低,安全联锁配置少;焦炭塔及加热炉区的逃生平台较少,易着火部位消