钒钛矿冶炼培训资料.docx
《钒钛矿冶炼培训资料.docx》由会员分享,可在线阅读,更多相关《钒钛矿冶炼培训资料.docx(25页珍藏版)》请在冰豆网上搜索。
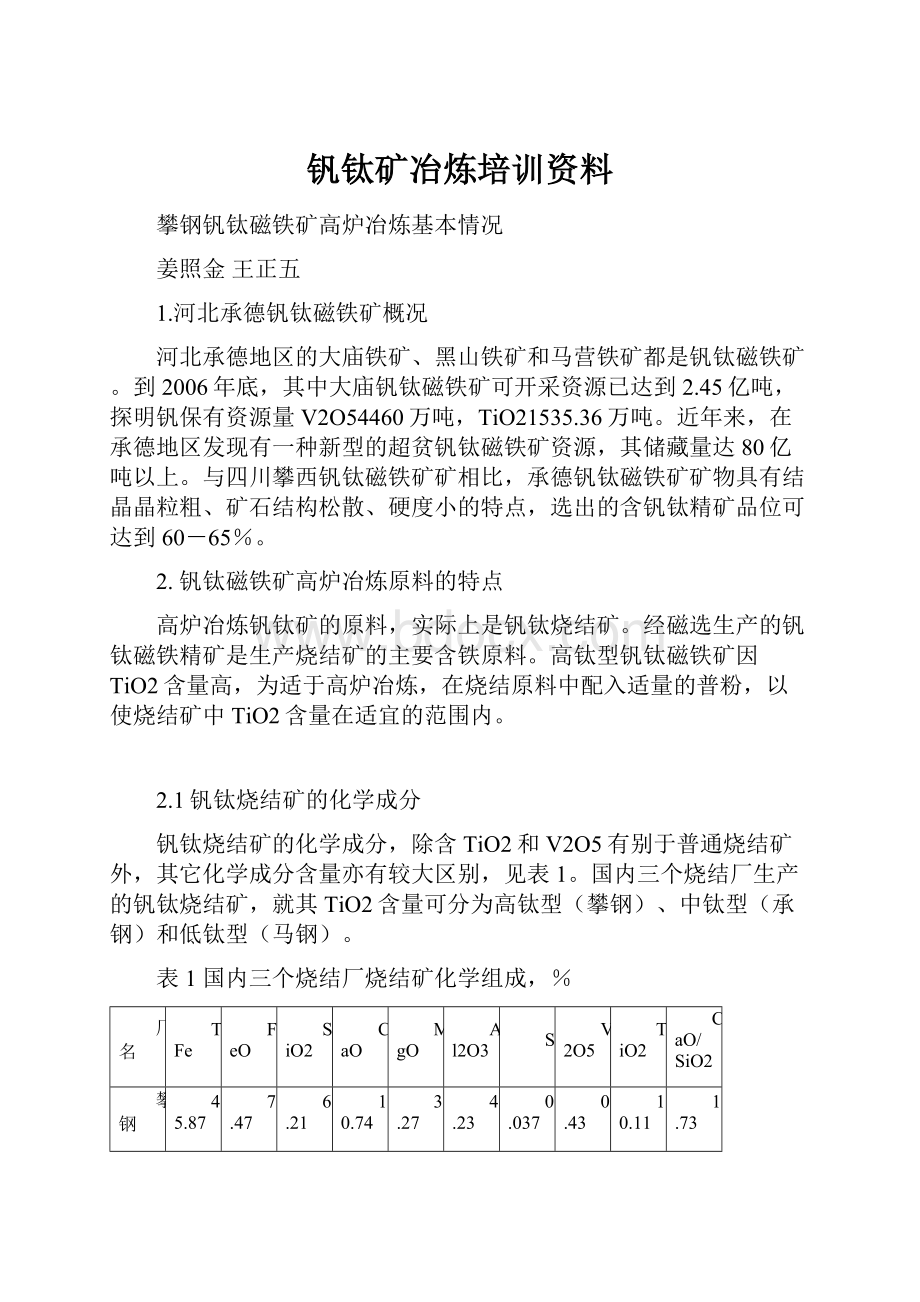
钒钛矿冶炼培训资料
攀钢钒钛磁铁矿高炉冶炼基本情况
姜照金王正五
1.河北承德钒钛磁铁矿概况
河北承德地区的大庙铁矿、黑山铁矿和马营铁矿都是钒钛磁铁矿。
到2006年底,其中大庙钒钛磁铁矿可开采资源已达到2.45亿吨,探明钒保有资源量V2O54460万吨,TiO21535.36万吨。
近年来,在承德地区发现有一种新型的超贫钒钛磁铁矿资源,其储藏量达80亿吨以上。
与四川攀西钒钛磁铁矿矿相比,承德钒钛磁铁矿矿物具有结晶晶粒粗、矿石结构松散、硬度小的特点,选出的含钒钛精矿品位可达到60-65%。
2.钒钛磁铁矿高炉冶炼原料的特点
高炉冶炼钒钛矿的原料,实际上是钒钛烧结矿。
经磁选生产的钒钛磁铁精矿是生产烧结矿的主要含铁原料。
高钛型钒钛磁铁矿因TiO2含量高,为适于高炉冶炼,在烧结原料中配入适量的普粉,以使烧结矿中TiO2含量在适宜的范围内。
2.1钒钛烧结矿的化学成分
钒钛烧结矿的化学成分,除含TiO2和V2O5有别于普通烧结矿外,其它化学成分含量亦有较大区别,见表1。
国内三个烧结厂生产的钒钛烧结矿,就其TiO2含量可分为高钛型(攀钢)、中钛型(承钢)和低钛型(马钢)。
表1国内三个烧结厂烧结矿化学组成,%
厂名
TFe
FeO
SiO2
CaO
MgO
Al2O3
S
V2O5
TiO2
CaO/SiO2
攀钢
45.87
7.47
6.21
10.74
3.27
4.23
0.037
0.43
10.11
1.73
承钢
55.09
12.15
3.32
6.43
2.63
2.89
0.051
0.75
7.40
1.95
马钢
53.28
16.54
12.78
11.63
3.08
2.00
0.078
0.42
1.32
1.87
高钛型钒钛烧结矿的化学成分与普通烧结矿相比,具有“三低”、“三高”的特点。
其中“三低”是指烧结矿含铁分低、FeO含量低和SiO2低;“三高”是指烧结矿含TiO2高、MgO和Al2O3高和V2O5高,其中TiO2决定了烧结过程和高炉冶炼的特殊规律。
2.2钒钛烧结矿的冶金性能
1.钒钛烧结矿的转鼓强度
钒钛烧结矿的强度一般比普通烧结矿强度低,其转鼓指数一般为81~82%,而普通烧结矿转鼓指数可达83~85%。
钒钛烧结矿冷却后的转鼓指数比冷却前提高6~7%,说明钒钛烧结矿在热状态下脆性大,强度不如普通烧结矿好。
2.烧结矿贮存性能
钒钛烧结矿有较好的贮存性能,其自然粉化率比普通烧结矿低得多。
普通烧结矿贮存一天粉化率达20%以上,五天中每天粉化率递增3%;而钒钛烧结矿自然粉化率很低,且随贮存时间增加,粉化率无明显增加,尤其是水浸后的钒钛烧结矿自然粉化率亦无明显变化,这表明钒钛烧结矿具有较好的贮存性能。
普通烧结矿配加生石灰或消石灰时,烧结矿的贮存性能变差,而钒钛烧结矿烧结生产配加生石灰或消石灰时,对钒钛烧结矿自然粉化率无明显变化。
此外,烧结钒钛烧结矿时配加50%或100%消石灰或生石灰,不因烧结矿的FeO或碱度的变化而影响钒钛烧结矿自然粉化率的变化。
3.烧结矿的软化性能
钒钛烧结矿的软化性能,由于矿物组成的特点而与普通烧结矿显著不同。
钒钛烧结矿的开始软化和终了温度比普通烧结矿约高120℃,软化区间稍宽。
生产用的高钛型钒钛矿,由于配入部分普粉,SiO2含量有所升高,TiO2含量有所降低,因此软化开始和终了温度都有所降低,但仍比普通烧结矿高,其软化区间变宽。
4.钒钛烧结矿的还原性能
高钛型钒钛烧结矿由于FeO含量低、氧化度高,还原性能一般比普通烧结矿好。
5.钒钛烧结矿的低温还原粉化性能
钒钛烧结矿的低温还原粉化率比普通烧结矿高得多,一般大于60%,高的达80~85%。
6.钒钛烧结矿的熔滴性能
钒钛烧结矿的熔滴性能通常表现为开始软熔温度低、熔化滴落温度高,熔-滴温度区间宽,且钒钛烧结矿熔化滴落过程中渣铁分离差,渣中带铁多。
2.3高炉冶炼钒钛矿时的炉料要求及合理的炉料结构
1.炉料要求
由于钒钛磁铁矿冶炼的特殊性,要维持高炉长期顺行,对“精料”的要求比普通矿冶炼时要更加严格,同时要加强对料槽的管理,首先不要混料,其次不要空槽,并提高筛分效率,降低入炉烧结矿的粉末量,改善高炉料柱的透气性。
2.合理的炉料结构
高炉冶炼钒钛磁铁矿的入炉原料结构包括熟料率、FeO、m(TiO2)/m(TFe)值三个方面。
合理的炉料结构为:
1)钒钛精矿配加部分普通富矿粉的高碱度烧结矿配加经过充分中和混匀并筛除粉末的普通块矿入炉。
2)钒钛精矿配加12~15%经破碎后的普通富矿粉烧结矿入炉而不加普通块矿入炉。
3)钒钛精矿配加部分普通富矿粉的烧结矿配入渣量的1~3%的萤石和经过充分中和混匀并筛除粉末的普通块矿入炉并尽量减少块矿配比。
4)钒钛精矿加部分贫锰矿粉的烧结矿,配加充分中和混匀并筛除粉末的普通块矿入炉。
5)高碱度钒钛烧结矿配加酸性钒钛烧结矿入炉。
3.钒钛磁铁矿高炉冶炼过程
3.1钒钛矿冶炼过程的基本反应
钒钛烧结矿的矿物组成是钛赤铁矿、钛磁铁矿、钙钛矿和含钛硅酸盐,以及少量的铁酸钙、铁板钛矿和残存的钛铁矿。
原燃料从高炉炉顶装入后,烧结矿从炉喉下降到炉腹过程中,经过温度不断升高的温度场和上升煤气流的作用,烧结矿经历了还原、软化熔融到渣铁形成熔化滴落的过程。
在这个过程中,钒钛烧结矿经过不同温度区间。
经煤气流传热传质的作用所发生的基本反应和物相组成的变化特点如下:
1)块状带大致分三个温度区间进行化学反应和相变过程。
从炉喉到炉身上部的650~900℃区间,钒钛烧结矿原有的钛赤铁矿、钛磁铁矿、铁酸钙、铁板钛矿被还原失氧,反应后的物相是钛磁铁矿、钛铁晶石、浮士体及少量的细小铁粒;炉身中部约900~1150℃,钛磁铁矿被还原,反应生成浮士体和钛铁晶石固熔体以及部分浮士体被还原为金属铁;炉身下部的1150~1250℃是钛铁晶石还原分解阶段,反应生成的物相有金属铁、钛铁晶石、少量浮士体、钛铁矿、板钛矿固熔体出现,钙钛矿增加。
2)软熔带是从炉身下部到炉腹的1250~1350℃区间,直接还原发展,烧结矿软熔形成以粘结物为特征的软熔带。
软熔带下部,初渣形成,铁粒聚合。
3)滴落带是从炉腹到风口区的大于1350℃区间,金属铁渗碳和初渣形成,熔化性温度下降,渣铁开始熔化滴落,滴落的熔渣为钛辉石、巴依石、钙钛矿和金属铁等。
钒钛矿冶炼在滴落带的反应特点是钛氧化物和钒氧化物被碳还原。
3.2含钛矿物中氧化物的还原
1.含钛矿物中铁氧化物的还原
钒钛磁铁矿中以固熔体存在的Fe2O3、Fe3O4和球团矿中Fe2O3的还原与普通矿相同,即按Fe2O3Fe3O4FeOFe逐级还原顺序进行。
而不同的是钛铁氧化物按照Fe2O3·TiO2Fe2TiO4FeTiO3FeTi2O5的途径还原。
2.含钛矿物中钒氧化物的还原
钒钛磁铁矿中钒以V3+的形态固熔于磁铁矿晶格内,形成钒尖晶石[FeO·(Fe·V)2O3]。
研究表明,烧结矿中铁的还原度达90%以上时,铁中方出现钒。
铁相中钒与铁水含钒相近,表明含钒氧化物的还原在铁氧化物之后方开始还原,且高炉内钒的还原主要发生在风口以上软熔带,改善这一区域的还原条件,将是提高钒收率的主要途径。
钒钛烧结矿经深度还原且有铁相产生后,可以认为在软熔带中,钒以FeO·V2O3形式进行还原。
3.高炉内含钛矿物中铁、钛、钒、硅元素的选择还原
铁、钛、钒、硅氧化物的稳定性按FeOV2O3SiO2TiO2的顺序递增,即V2O3、SiO2、TiO2都是较难还原的氧化物。
3.3钒钛矿冶炼的造渣过程
高炉冶炼的炉渣,主要成分来源于原燃料所带入的脉石成分。
冶炼普通矿形成四元(CaO-MgO-SiO2-Al2O3)渣系;而冶炼钒钛矿则为五元(CaO-MgO-SiO2-Al2O3-TiO2)渣系。
按照五元炉渣中TiO2含量不同可划分为高钛渣(>20%TiO2)、中钛渣(10~20%TiO2)和低钛渣(<10%TiO2),其SiO2/TiO2的比值分别为接近1.0、>1.40、>3.0。
3.3.1含钛炉渣的熔化性温度及其影响因素
1.炉渣熔化性温度
炉渣熔化性温度主要取决于炉渣化学组成和矿物组成。
低钛渣的熔化性温度与普通四元渣相近,中钛渣的熔化性温度高于四元渣50~60℃,而高钛渣则高出100℃左右。
高钛型炉渣的熔化性温度一般为1380~1450℃,高温时炉渣粘度较低,但由流动性较好至完全失去流动的温度区间极窄,只有20~30℃。
2.影响高钛型炉渣熔化性温度的因素
1)碱度的影响
相同TiO2含量的炉渣,其熔化性温度随碱度增加而升高;不同含量TiO2的炉渣,随碱度的变化都有一个低熔区,且渣中TiO2含量越高其低熔区对应的碱度越高,低熔区的熔化性温度也随之越高。
2)TiO2含量的影响
在一定碱度下,随TiO2含量增加,熔化性温度升高。
特别是TiO2含量差别大的炉渣,熔化性温度有明显的差异。
3)低价钛氧化物含量的影响
随着低价钛氧化物含量的增加,炉渣熔化性温度逐渐降低。
4)TiC和TiN含量的影响
随着TiC或TiN含量的增加,炉渣熔化性温度迅速提高。
5)MgO含量的影响
在CaO/SiO2比值不变的情况下,随渣中MgO含量的增加,炉渣熔化性温度升高。
渣中MgO含量由8%增加到12%时,适当降低CaO/SiO2比值,可以适当降低熔化性温度。
6)Al2O3含量的影响
Al2O3含量增加或降低都使炉渣熔化性温度升高。
3.改善钛渣熔化性温度的措施
1)MnO:
对实际冶炼的高钛型炉渣和中钛渣,添加0~6%的MnO,随添加量增加,熔化性温度逐渐降低,无回升现象。
若添加1.5%MnO,对于高钛型炉渣,其熔化性温度降低约30℃,而对中钛渣则降10℃左右。
2)CaF2:
添加0~3%时,熔化性温度随CaF2含量的增加而下降。
3.3.2含钛炉渣变稠的特性
含钛炉渣在还原气氛并有炽热焦炭存在的高炉冶炼条件下,随高温和还原时间延长,其粘度增加,这是与四元炉渣冶炼最本质的区别。
根据实际冶炼的表现,低钛渣的变稠速度缓慢,而高钛型炉渣变稠速度最快,中钛渣则介于两者之间。
1.含钛炉渣变稠的因素
1)TiO2含量的影响
当TiO2含量增加时,变稠速度大大加快。
低于20%TiO2的炉渣随着还原时间的延长,炉渣粘度增加很小,而大于20%TiO2的炉渣随着还原时间的延长,变稠急剧加快,特别是达到30%或更高时,其变稠速度更快。
2)温度的影响
随着温度升高,TiO2还原反应速度加快,反应产物TiC增加,致使含钛炉渣变稠速度加快。
3)碱度影响
不同TiO2含量的炉渣,随着碱度升高,其开始变稠的时间都相应增加。
TiO2含量增加,变稠愈快。
但是高钛型炉渣因碱度升高而使其熔化性温度升高,所以实际冶炼不能用提高碱度的办法来抑制钛的还原,而应在选择适于冶炼的熔化性温度下,确定稍高的碱度以抑制炉渣变稠。
4)MgO的影响
在一定碱度下,随MgO含量的增加,炉渣变稠程度减小。
低碱度下,MgO对抑制变稠的作用更为明显。
适当降低CaO/SiO2比值和提高(CaO+MgO)/SiO2比值,可以使渣系具有适于冶炼的熔化性温度,既有一定的脱硫能力又利于抑制变稠。
3.3.3含钛泡沫渣的特性
高炉冶炼高钛型炉渣,“泡沫渣”的形成会给冶炼行程造成极大危害。
其表现为炉渣流入罐内,产生大量气体,使炉渣成泡沫状上涨外溢,这就是所谓的“泡沫渣”现象。
从渣罐出来的气体成分分析结果表明,气体中主要成分为一氧化碳,占60~80%,与炉缸气体成分不同。
因此,这些气体不是由炉渣所带出,而是在罐内新生成的。
“泡沫渣”的产生破坏了高炉冶炼行程的稳定并限制了冶炼的强化。
1.“泡沫渣”形成机理
随着TiO2等在高温下的还原,气泡不断产生,炉渣中的Ti3+、Ti2+、Ti(C,N)、TiO等增多,因此炉渣性质也不断变化,这种过程作用下的炉渣逐渐变得易于稳定气泡,达到气泡在渣中逐渐积累而形成泡沫渣。
在这过程中,气泡的运动使得铁珠不易合并、沉降而乳化于渣中,造成渣中残碳量增多,分散度增大,也造成Ti(C,N)更进一步地分散于渣中。
2.“泡沫渣”的影响因素
1)温度的影响
随着温度升高,反应速度在1450℃以下有下降趋势,然后逐渐增加。
当温度为1460~1470℃时,气泡产生速率急剧增大。
涨泡高度随温度升高,但在
1420℃以下急剧下降,在1420℃以上先缓慢上升,到1480℃时则急剧升高。
2)TiO2含量的影响
随渣中TiO2含量增加和温度升高,炉渣起泡早且上涨高。
TiO2含量在20~30%之间,涨泡高度变化不大。
当渣中TiO2含量达35%时,涨泡高度急剧升高。
3)碱度的影响
当炉渣中TiO2含量为30%时,提高炉渣碱度,涨泡高度下降;当炉渣中TiO2含量小于27.5%时,提高炉渣碱度,涨泡高度增加。
3.“消泡”措施
1)合理配矿:
用不同矿种配矿后,炉渣中Ti(C,N)含量和涨泡高度皆比100%钒钛烧结矿时降低,特别是配钒钛原矿,尽管渣中TiO2含量升高,但其抑制钛的过还原和“消泡”效果是最好的。
2)高碱度烧结矿配加酸性钒钛烧结矿:
配加酸性钒钛烧结矿有助于抑制“泡沫渣”的形成。
3)配加球团矿:
适当的配加球团矿具有较好的消泡作用。
4)添加CaF2和MnO:
随着CaF2和MnO量增加,熔渣涨泡高度明显降低。
当CaF2含量为3%时,涨泡高度降低到最低值,如继续增加,则涨泡高度无甚变化。
若添加MnO大于3%时,效果更佳。
添加一定量的CaF2或MnO,可使高钛型炉渣的熔化性温度降低,粘度减小,从而改善炉渣流动性,减少渣中带铁,使渣相反应产生的气泡易于逸出。
此外,MnO可提高渣中氧位,利于抑制TiO2还原,因此,随MnO量的增加,效果愈明显。
3.4钒钛矿冶炼的脱硫过程
除TiO2含量很低的炉渣外,含钛五元系炉渣的脱硫能力一般都比普通四元系炉渣脱硫能力要低。
其脱硫能力的变化特点是,随渣中TiO2含量增加,脱硫能力降低。
3.4.1含钛炉渣脱硫性能的影响因素
含钛炉渣的脱硫能力主要是受含钛五元渣系的性质及其冶炼的特殊性影响,与普通炉渣有明显的差别。
1.渣中TiO2含量的影响
高钛型炉渣脱硫能力远比普通炉渣低。
含钛炉渣随TiO2含量增加LS下降。
在碱度0.90~1.20范围内,不同TiO2的炉渣随碱度升高LS都有所升高。
2.碱度的影响
在TiO2含量不变的情况下,碱度在0.80~1.20范围内,高钛型炉渣的脱硫能力随碱度增加而提高。
各种碱度下的脱硫能力随TiO2含量增加而下降。
不同TiO2含量的炉渣随碱度升高,Ls提高幅度并不大。
3.温度的影响
随温度升高,LS显著提高,生铁含硫降低,但是,由于温度升高而引起含钛炉渣变稠时,其脱硫能力反而下降。
含钛炉渣开始变稠的温度与渣中的TiO2含量有关,随TiO2含量增加,变稠的开始温度越低,且开始变稠的反应时间越短。
4.MgO含量的影响
在MgO<10%的炉渣中,增加MgO含量,LS升高,可提高炉渣脱硫能力,但当渣中MgO>10%时,增加MgO含量,Ls反而下降,因此高钛型炉渣冶炼的适宜MgO含量为10%左右,CaO/SiO2约1.10。
3.4.2改善含钛炉渣脱硫能力的措施
1.MnO:
随添加量增加,炉渣粘度降低,Ls升高。
2.CaF2:
渣中CaF2约1%左右,并适当提高碱度,CaO/SiO2比值由1.06提高到1.10,LS由5.22提高到5.77,生铁含硫有所降低,因此添加CaF2可使含钛炉渣的脱硫能力得到一定程度的改善。
4.含钛炉渣的冶炼特性
高炉冶炼的操作技术,一般是根据冶炼条件(原燃料、装备水平)来合理选择并确定高炉冶炼的基本操作制度(送风制度、装料制度、造渣制度、热制度)以及为及时调剂由于冶炼过程中错综复杂的变动因素而引起冶炼行程的失常,如煤气流分布失常、造渣制度或热制度失常等,以使高炉冶炼行程稳定顺行,实现高炉冶炼的“优质、低耗、高产、长寿”的综合冶炼效果。
4.1煤气流合理分布的调控
对含钛炉渣的冶炼而言,合理煤气流分布的调控,除高炉冶炼的共性外,针对其冶炼特性抑制含钛炉渣的变稠是至关重要的。
4.1.1煤气流合理分布的标志
对含钛炉渣冶炼,要从高钛型钒钛烧结矿软化温度高、滴落温度范围宽的特点出发,必须保证软熔带根部具有较好熔化能力而过热度要高于普通矿冶炼的特点,以及炉缸工作活跃,是高钛型炉渣冶炼调节煤气流合理分布的关键。
实践认为,高钛型炉渣冶炼的合理煤气流分布,其曲线如图1。
特点是边缘CO2含量高于中心,其差值约3%左右,最高点CO2含量位置在取样位置的第二点处,既不靠近炉喉边缘,也不远离炉墙。
图1煤气分布曲线
4.1.2基本操作制度的选择与确定
含钛炉渣冶炼,煤气流分布的调节与普通矿冶炼相同,其方法仍是“以下部调剂为基础,上下部调剂相结合”。
但因含钛炉渣冶炼的特性,调控煤气流合理分布既要适合于冶炼的共性,又要适合于冶炼的特殊性,这是高炉冶炼含钛炉渣防稠的基础。
含钛炉渣冶炼主要原料是以钒钛烧结矿为主,钒钛烧结矿平均粒度组成比普通烧结矿平均粒度小,但入炉烧结矿小于5mm粉末小于20%时,布料无反常现象。
高钛型钒钛烧结矿经入炉前筛分后,入炉时小于5mm粉末一般小于10%。
通过实践及研究,钒钛烧结矿的布料规律,无论钟式炉顶或是无钟炉顶布料都和普通矿炉顶布料的一般规律一致。
1.送风制度的选择原则
对于含钛炉渣的冶炼,选择送风制度的基本原则与普通炉渣的冶炼基本相似,即根据高炉冶炼的具体条件,按不同冶炼强度确定适宜的鼓风动能,以使初始煤气流合理分布,保证炉缸工作的活跃。
普通矿冶炼中冶炼强度与适宜鼓风动能E的关系如图2所示,高钛型炉渣冶炼时鼓风动能、实际风速与冶炼强度的关系如图3所示。
图2冶炼强度与适宜鼓风动能E的关系
2.装料制度的确定原则
一般按装料制度的变动影响布料的一般规律与送风制度相结合确定装料制度(装入顺序、批重、料线),以达到煤气流合理分布的目的。
1)料线:
改变料线主要是改变焦炭堆角。
当批重一定时,随料线降低,焦炭和烧结矿的堆角差越来越小。
当料线高于临界料线(约1.58m)时,布料就会造成反常,而低于临界料线时,布料规律符合传统的概念。
2)批重:
随烧结矿批重增大,堆角逐渐下降,当批重增加到一定数值后变化减缓。
焦炭批重也呈现同样的规律。
3)径向矿焦比:
在一定批重下,矿石与焦炭的堆角差愈大,则中心的矿焦比愈小,而边缘矿焦比愈大。
在一定批重下,料线愈低,矿石与焦炭的堆角差值由负到正,故愈加重边缘而发展中心气流。
随批重增加,烧结矿堆角和焦角均降低。
因此可采用烧结矿分装制,焦炭一次装入制。
4)装料顺序对布料规律的影响
OKOKOKKOKKOOOOKKKOOKKOKO
OKKO
边缘由重到轻
OOKKKKOOKOOKOKOKOKKOKOKO
KOKO
中心由重到轻
实践表明,倒同装或正同装的装料顺序,无论单独使用或组合成综合装料顺序,如mOOKK+nKKOO,往往都会造成煤气流分布不良,故一般不使用。
而KOKO倒分装顺序,因强烈发展边缘又发展中心,只用于处理炉况失常时使用。
为控制炉顶布料以达到煤气流合理分布的目的,实际生产中采用综合装料顺序并配合料线和批重。
4.2含钛炉渣冶炼的热制度选择
炉温是高炉顺行的基础,实践中通常以铁中[Si]来表示炉温。
含钛炉渣冶炼的是五元渣系,其中TiO2与SiO2在高炉冶炼的炉渣中CaO/SiO2的比值下,其性质相似,故含钛炉渣冶炼可以用∑(Si+Ti)%相对代表炉温,但由于含钛炉渣中TiO2含量范围差别较大,可视[Si]%和[Ti]%随炉温变化的灵敏程度,分别按
[Si]%或[Ti]%来代表炉温。
含钛炉渣由于其冶炼的特殊性,热制度的选择与普通炉渣冶炼有明显区别。
选择热制度的原则是:
首先按炉渣中TiO2含量选择适宜的炉温,其次是在保证冶炼顺行的前提下,选择的炉温应利于抑制钛的过还原,防止钛渣变稠,有好的脱硫能力和较低铁损。
对于高钛渣,还要抑制“泡沫渣”的形成。
因此,含钛炉渣的冶炼都要在煤气流合理分布、炉缸工作活跃的基础上,按渣中TiO2含量范围所划分的低钛渣、中钛渣、高钛型炉渣,分别选择适宜的炉温,这是冶炼含钛炉渣的关键。
4.2.1含钛炉渣冶炼时,铁中[Si]和[Ti]的变化特点
为选择冶炼含钛炉渣的热制度,必须掌握各种含钛炉渣冶炼时,铁中[Si]和[Ti]以及两者之间关系随炉温变化的规律及特点。
1.低钛渣(8~10%TiO2)冶炼:
铁中[Si]和[Ti]都随炉温升高而增加,且[Si]>[Ti],其关系为[Ti]=0.700[Si]-0.025。
低钛渣冶炼时,铁中[Si]随炉温变化较[Ti]灵敏,故可以[Si]相对表示炉温。
为防止低钛渣变稠并能控制低的铁损和良好的脱硫能力,实践认为适宜的炉温范围是:
∑(Si+Ti)=0.63~0.75%,相应的[Si]=0.38~0.45%,[Ti]=0.25~0.30%,[Ti]的上限是考虑铁损,不是变稠的限界。
2.中钛渣(13~15%TiO2)冶炼:
铁中[Si]和[Ti]都随炉温升高而增加,而铁中[Si]仍大于[Ti],其关系为[Ti]=0.841[Si]-0.007。
实践认为中钛渣冶炼的适宜炉温范围是:
∑(Si+Ti)=0.45~0.56%,相应的[Si]=0.25~0.31%,[Ti]=0.20~0.25%,若[Ti]达到0.30%,中钛渣开始变稠,虽对炉况尚未产生不良影响,但铁损明显增加。
如[Ti]大于0.30%以上,炉渣明显变稠,不仅铁损高,若调剂不及时会产生粘渣,导致冶炼行程失常。
3.高钛渣(23~25%TiO2)冶炼:
铁中[Si]和[Ti]都随炉温升高而增加,但铁中[Ti]>[Si],其关系为[Ti]=1.353[Si]+0.012,因此高钛型炉渣冶炼时可以[Ti]相对表示炉温。
当冶炼凉行时,铁中[Ti]逐渐接近于[Si]。
如当渣中TiO2含量提高到26~29%时,铁中[Si]和[Ti]随炉温下降有个交点,形成明显的炉凉或由凉转热的分界点。
如果铁中[Ti]<[Si],则是高钛型炉渣冶炼时炉缸中心堆积的重要标志之一。
4.2.2高钛型炉渣冶炼适宜炉温的选择
高钛渣(23~25%TiO2)冶炼,随炉温升高[Ti]随之升高,且渣中Ti(C,N)含量亦随之增加,因此,控制铁中[Ti]就控制了渣中Ti(C,N)的生成量,从而抑制了泡沫渣的形成并减缓炉渣变稠。
高钛型炉渣冶炼实际冶炼过程中,炉温与渣铁行为关系如图4所示。
图4炉温与fT的关系
1.Ⅱ区炉温范围是高钛型炉渣冶炼的适宜炉温范围,fT=0.70~0.90(fT为TiO2酸性系数,指终渣中以TiO2形态存在的金属钛占总金属钛量的比例,Ti(低)/Ti(高)=0.20~0.10。
此炉温范围无泡沫渣形成,渣铁分离好,可实现较佳的综合冶炼效果。
2.Ⅰ区范围炉温系炉凉行程。
此情况下,fT>0.90,Ti(低)/Ti(高)≤0.10。
3.Ⅲ区范围炉温系偏高炉温。
fT=0.60~0.70,Ti(低)/Ti(高)=0.20~0.25。
有时形成泡沫渣,虽未对冶炼行程有什么不良影响,但炉渣有些稠化而铁损增加。
4.Ⅳ区范围炉温是炉渣变稠的炉热行程。
fT<0.60~0.50,Ti(低)/Ti(高)>0.25~0.35。
虽然炉渣尚能流动,但放渣困难带铁多,渣口破损