建设每小时生产1万5千方甲裂制氢装置可行性研究报告.docx
《建设每小时生产1万5千方甲裂制氢装置可行性研究报告.docx》由会员分享,可在线阅读,更多相关《建设每小时生产1万5千方甲裂制氢装置可行性研究报告.docx(77页珍藏版)》请在冰豆网上搜索。
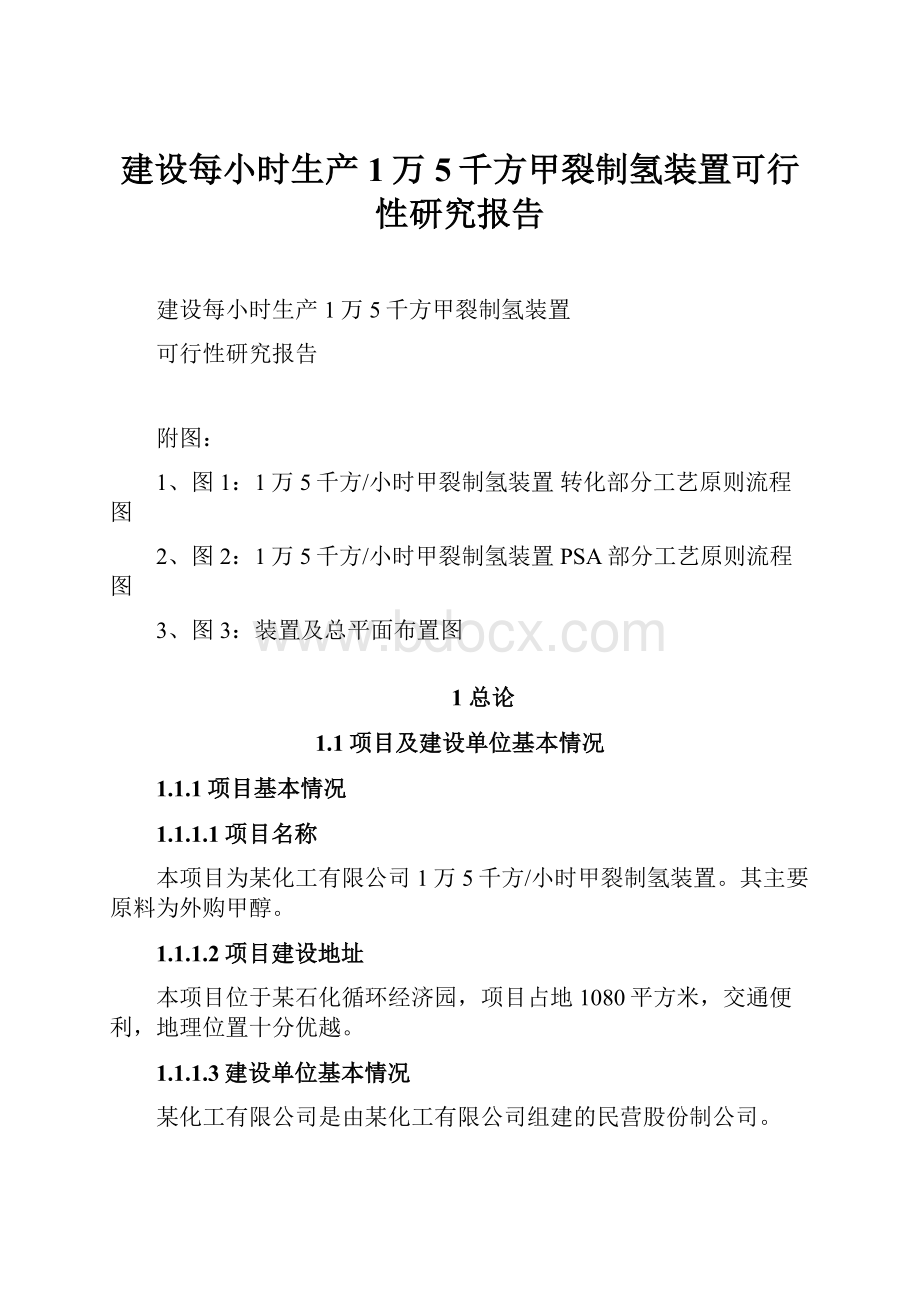
建设每小时生产1万5千方甲裂制氢装置可行性研究报告
建设每小时生产1万5千方甲裂制氢装置
可行性研究报告
附图:
1、图1:
1万5千方/小时甲裂制氢装置转化部分工艺原则流程图
2、图2:
1万5千方/小时甲裂制氢装置PSA部分工艺原则流程图
3、图3:
装置及总平面布置图
1总论
1.1项目及建设单位基本情况
1.1.1项目基本情况
1.1.1.1项目名称
本项目为某化工有限公司1万5千方/小时甲裂制氢装置。
其主要原料为外购甲醇。
1.1.1.2项目建设地址
本项目位于某石化循环经济园,项目占地1080平方米,交通便利,地理位置十分优越。
1.1.1.3建设单位基本情况
某化工有限公司是由某化工有限公司组建的民营股份制公司。
某化工有限公司始建于一九九五年,注册资本3000万元,是一家以常减压蜡油为原料,以生产石蜡产品为主导,及副产化工溶剂油等产品的民营企业。
公司位于某县境内,沈盘公路127公里处,厂区占地10万平方米,交通便利,地理位置十分优越。
公司现有固定资产9000万元,公司拥有员工227人,其中高中级技术管理人员占15%。
公司下设生产技术部、市场部、质检部以及燃料油车间、沥青车间和石蜡制品车间等机构。
公司年加工常减压蜡油10万吨,年产值12亿元人民币。
公司采用无溶剂制蜡工艺,经压榨脱蜡、发汗脱油、白土精制等一系列过程生产出高纯度工业用蜡,广泛用于制造合成脂肪酸和高级醇及制造火柴、蜡烛、蜡笔、防水剂、软管、纤维板、橡胶等。
随着国民生活水平的提高,石蜡的二次开发也逐步有所增加。
在食品、药品、化妆品、电线、电缆、电池等行业的应用日益增加。
公司1997年被中华人民共和国农业部评为“二档乡镇企业”;2003年被某县政府列为“县民营企业重点保护单位”;同时也是市重点扶持的民营企业,2003年被某市政府评为“先进集体”;2005年被某市人民政府授予“经济社会发展贡献奖”;2007年被某市人民政府评为“纳税贡献企业”;2008年被某县人民政府评为“文明企业”;连续五年被市、县工商局评为“守合同、重信用”单位。
1.1.2编制依据
1.1.2.1《某化工有限公司1万5千方/小时甲裂制氢装置》项目建议书;
1.1.2.2《某化工有限公司1万5千方/小时甲裂制氢装置》可行性研究报告技术服务合同;
1.1.2.3建设单位提供的地质资料、气象水文资料及其他相关资料;
1.1.2.4《某化工有限公司1万5千方/小时甲裂制氢装置》可行性研究报告编制委托书;
1.1.2.5建设单位提供的其他资料。
1.1.3编制原则
1.1.3.1按照“整体规划、分步实施”的原则编制可行性研究报告;
1.1.3.2以市场为导向,以经济效益为中心,做到少投入、多产出、快速产出;
1.1.3.3优化工艺流程,充分利用厂区已建的公用工程及辅助设施和园区基础设施,最大限度压缩工程投资,加快工程建设进度;
1.1.3.4新建装置采用先进、成熟、可靠的工艺技术和设备,大力推进技术进步,确保产品质量,降低装置能耗。
优先选用国内自行开发的工艺新技术和质量可靠的设备、材料,尽可能节约外汇,必须引进的设备应先进可靠;
1.1.3.5采用集散型控制系统(DCS),实现集中监视和先进过程控制、协调操作参数,提高工艺装置和辅助设施的自动化水平和综合管理水平,提高经济效益;
1.1.3.6严格执行国家和地方关于环境保护、消防和职业安全卫生等有关法律、法规,做到“三废”治理、安全卫生等保障措施与工程建设同时进行。
1.2建设的必要性
某化工有限公司根据公司进一步向石油化工领域纵深发展的战略布局需要,结合某石油化工的地缘等优势,并根据市场对高端油品需求的不断上升,公司拟在某生物质能化工产业园区得胜分园区新建一套1万5千方/小时甲裂制氢装置,用于某公司30万吨/年加氢精制项目加氢,补充原制氢装置制氢能力不足的缺口,以提高产品质量,提升市场竞争力。
1.3研究结果
1.3.1结论
1.3.1.1甲醇制氢装置采用国内成熟、先进的技术,确保产品质量。
1.3.1.2装置产品达到99.99%的纯度,氢气量可供多套加氢装置使用,完全满足加氢工艺的要求。
1.3.1.3装置建成后,将过去由产品带入社会环境的硫、氮、杂质(未燃烧烃),集中在装置内转化为硫化氢和氨加以回收和处理,具有显著的社会环保效果。
1.3.1.4装置的各项技术经济指标较好,具有良好的经济和社会效益。
总之,建设1万5千方/小时甲裂制氢装置,对促进公司的长远发展,合理利用资源,提高企业经济效益,保护环境、促进社会就业和保持社会安定是十分必要的,具有深刻的现实意义和长远的历史意义。
2市场分析与预测
本制氢装置,作为《新建年产XXXXXXX、XXXXXX、XXXXXX项目》中的一个子项,目的是向公司的加氢装置提供氢气,故产品氢气自产自用不进入市场。
氢气价格参考当地供氢价格,本可研报告氢气暂定为2.00元/Nm3
3生产规模及生产技术方案
3.1生产规模及生产方案
3.1.1生产规模
设计规模:
15000m3n/h,
操作弹性:
30%~110%,
年运行时数:
8400小时。
3.2工艺技术方案选择
3.2.1制氢工艺技术方案选择
目前国内生产H2的生产方法主要有以下三种:
一是水电解法生产:
此方法比较简便,但能耗很大,高达5~6kwh/Nm3,且纯度不够理想。
二是石油、天然气、煤制氢:
传统的以石油、天然气为原料制氢,这类制氢装置投资较大,生产成本较低,适用于石油气、天然气丰富的地区使用。
三是以煤为原料,经过造气后提氢,这类装置需要庞大的投资,生产环境不友好,已经逐步被国家限制使用。
四是甲醇裂解制氢:
这种方法是甲醇和水在催化剂作用下裂解生成氢气、二氧化碳及少量一氧化碳的混合气体,再经变压吸附提纯氢气,这类装置投资不大,建设周期短,开停车方便快捷,现在甲醇市场供大于求,甲醇价格便宜,是投资最省,成本最低的一种制氢方法。
本项目选择甲醇裂解制氢的生产方法,本方法不仅原料来源方便、工艺成熟、装置简单、易于操作,且产品氢气纯度高,生产成本低,具有广泛的发展市场。
3.3制氢的主要操作条件
制氢主要操作条件
3.3.1反应器
入口温度℃230
出口温度℃235
入口压力MPa(a)2.6
出口压力MPa(a)2.5
制氢催化剂装量m344.8
3.3.2PSA单元操作条件
入口温度℃40
入口压力MPa(G)2.5
3.4工艺流程特点
3.5.1.1本装置换热器采用我公司专利产品--高效节能换热新工艺,采用此种工艺,转化气出口温度可降低至80度以下,回收了更多的热量,减少了导热油供热量,装置能量消耗达到最低。
3.5.1.2变压吸附装置采用二段法抽真空再生流程,先脱碳,再提氢,可以回收部分氢气作燃料气,同时氢气回收率高,甲醇单耗低。
3.5.1.3本装置的采用产品气量自动调节控制系统,根据所需要的产品气量自动调节进料量的大小,装置自动化程度显著提高。
3.5.1.4两段变压分别采用十个吸附塔、七次均压,提高了氢气回收率;当某个塔的管路或阀门出现故障的时候,可以切掉其中一个塔,程序自动调整到9个塔运行,保证了装置的长期稳定运行。
3.5.1.5本装置的吸附剂采用密相装填技术,可进一步减小床层内的死空间,提高有效组分回收率。
3.5.1.6采用专用吸附剂,氢气选择高,吸附剂用量少,配比合理、投资更省,运行费用更低,指标更先进。
3.5.1.7本装置采用先进、可靠的气动系统作为程控阀的驱动源,具有运行稳定、长周期、程控阀动作快、使用寿命长等优点;在与某一吸附塔有关的程控阀(或它的控制部件)出现故障后,可以进行自适应PSA专家诊断系统无扰动切换,以保证装置长期稳定运行和便于维修。
4工艺装置
4.1项目范围
本项目设计范围为制氢装置边界线以内部分,由转化部分、脱碳部分、提氢部分及导热油部分,其余制氮系统、仪表空气系统、循环冷却水系统等由厂区统一提供。
4.2原料来源及产品去向
4.2.1原料来源
制氢装置原料主要是外购,原料所需的脱盐水由锅炉房软水系统提供。
4.2.2产品去向
氢气:
管道输送到用氢装置。
4.3装置组成
该装置由转化、脱碳、提氢三大部分组成。
4.4原料性质及产品组成
4.4.1甲醇的性质
甲醇是一种无色、透明、易燃、易挥发的有毒液体,常温下对金属无腐蚀性(铅、铝除外),略有酒精气味。
分子量32.04,相对密度0.792(20/4℃),熔点-97.8℃,沸点64.5℃,闪点12.22℃,自燃点463.89℃,蒸气密度1.11,蒸气压13.33KPa(100mmHg21.2℃),蒸气与空气混合物爆炸极限6~36.5%(体积比),能与水、乙醇、乙醚、苯、酮、卤代烃和许多其他有机溶剂相混溶,遇热、明火或氧化剂易燃烧。
燃烧反应式为:
CH3OH+O2→CO2+H2O
4.5装置物料平衡
表4.5-制氢装置物料平衡表
物料名称
t/a
kg/h
备注
入
方
甲醇
62400
7800
水
36000
4500
合计
98400
12300
出
方
产品氢气
10716
1339.5
燃料气
940
0.1175
放空气
86744
10960
合计
98400
12300
4.6甲裂制氢工艺流程简述
4.6.1转化部分
甲醇催化转化制氢工艺过程包括:
原料汽化、过热过程、催化转化反应、转化气冷却冷凝、净化以及提纯等。
一、原料汽化过程
原料汽化、过热是指在加压条件下,将甲醇和脱盐水按规定比例用泵加压送入系统进行预热、汽化过热至转化温度的过程。
完成此过程需:
原料液储槽、原料液泵、汽化器、过热器等设备及其配套仪表和阀门。
该工序目的是为催化转化反应提供规定的原料配比、温度等条件。
二、催化转化反应
在规定温度和压力下,原料混合气在转化器中进行气相催化反应,同时完成催化裂解和转化两个反应。
完成此反应过程需转化器、导热油供热系统及其配套仪表和阀门。
该工序的目的是完成化学反应,得到主要含有氢气和二氧化碳的转化气。
三、转化气冷却冷凝
将转化器下部出来的高温转化气经冷却、冷凝降到常温。
完成该过程的设备有:
两台换热器、冷凝器三台设备及其配套仪表和阀门。
该工序目的是降低转化气温度,冷凝并回收部分甲醇、水等物质。
四、转化气净化
含有氢气、二氧化碳和少量甲醇、水的低温转化气,进入净化塔用脱盐水洗涤吸收其中未反应的甲醇的过程。
完成该过程的设备有:
净化塔、脱盐水泵(一开一备)三台设备及其配套仪表和阀门。
该工序目的是用脱盐水与转化气在净化塔填料上传热、传质吸收甲醇等有机物,塔釜收集未转化完的甲醇和水循环使用,塔顶制得转化气送PSA工段。
4.6.2PSA部分
PSA部分分为脱碳过程和提氢过程,脱碳以过程主要脱除掉转化气中二氧化碳,提氢过程则脱掉脱碳气中一氧化碳和少量二氧化碳及副反应产物甲烷,提纯氢气。
主要过程如下:
1、脱碳单元
来自转化部分的转化气压力2.5Mpa(G)、温度40℃,进入界区后,自塔底进入吸附塔中正处于吸附工况的塔,在其中多种吸附剂的依次选择吸附下,除去转化气中大部分的水分及二氧化碳,获得纯度大于90的粗氢气,经压力调节系统稳压后送出界区。
粗氢气进入提氢工段后,由塔底进入提氢塔中正处于吸附工况的塔,在其中多种吸附剂的依次选择吸附下,一次性除掉除氢气以外的其它杂质,获得纯度大于99.99%的产品氢气,经压力调节系统稳压后送出界区。
当吸附剂吸附饱和后,通过程控阀门切换至其它塔吸附,吸附饱和的塔则转入再生过程。
在再生过程中,吸附塔首先经过连续七次均压降压过程尽量回收塔内死空间氢气,然后通过逆放和抽真空两个步序使被吸附杂质解吸出来。
脱碳部分的解吸气直接放空,提氢部分的逆放解吸气进入解吸气缓冲罐,抽真空的解吸气进入解吸气缓冲罐,然后经调节阀调节混合后稳定地送往锅炉房,用作转化炉的燃料。
PSA部分的具体工作过程如下:
4.6.2.1吸附过程
原料气自塔底进入吸附塔A,在吸附压力(2.5MPa.G)下,选择吸附所有杂质,不被吸附的氢气作为产品从塔顶排出。
当吸附前沿(传质区前沿)到达吸附剂预留段的下部时停止吸附。
4.6.2.2一均降压过程。
吸附结束后,A塔停止进原料,然后通过程控阀与刚完成二均升步骤的E塔相连进行均压,这时A塔死空间内的高压氢气就均入E塔得以回收,直到两塔的压力基本相等时,结束一均降过程。
4.6.2.3二均降压过程。
一均降压结束后,A塔又通过程控阀与刚完成三均升步骤的F塔相连进行均压,这时A塔死空间内的高压氢气就接着均入F塔,得以继续回收。
直到两塔的压力基本相等时,结束二均降压过程。
4.6.2.4三均降压过程。
二均降压结束后,A塔又通过程控阀与三均罐相连进行均压,这时A塔死空间内的高压氢气就接着均入三均罐,得以继续回收。
直到两塔的压力基本相等时,结束三均降压过程。
4.6.2.5四均降压过程。
结束后,A塔又通过程控阀与刚完成五均升的G塔相连进行均压,这时A塔死空间内的高压氢气就接着均入G塔,得以继续回收。
直到两塔的压力基本相等时,结束四均降压过程。
4.6.2.6五均降压过程。
四均降压结束后,A塔又通过程控阀与刚完成六均升的H塔相连进行均压,这时A塔死空间内的高压氢气就接着均入H塔,得以继续回收。
直到两塔的压力基本相等时,结束五均降压过程。
4.6.2.7六均降压过程。
五均降压结束后,A塔又通过程控阀与六均罐相连进行均压,这时A塔死空间内的高压氢气就接着均入六均罐,得以继续回收。
直到两塔的压力基本相等时,结束六均降压过程。
4.6.2.8七均降压过程。
六均降压结束后,A塔又通过程控阀与刚抽完真空,解析完全等用的I塔相连进行均压,这时A塔死空间内的高压氢气就接着均入I塔,得以继续回收。
直到两塔的压力基本相等时,结束七均降压过程。
4.6.2.9逆放过程
七均降过程结束后,A塔压力已降至0.23MPa(G)左右,这时,杂质已开始从吸附剂中解吸出来,于是打开逆放程控阀,逆着吸附方向将吸附塔压力降至0.03MPa(G)左右。
逆放出的解吸气被送入解吸气缓冲罐。
4.6.2.10抽真空过程
逆着吸附方向,用真空泵经程控阀对吸附塔抽真空,降低塔内吸附剂表面的真空度,让杂质组分从吸附剂中完全解吸出来,A塔得到彻底再生。
4.6.2.11七均升压过程。
抽真空过程结束后,A塔通过程控阀与刚完成六均降压步骤的C塔相连进行均压升压,这时C塔死空间内的高压氢气就流入A塔被回收,同时A塔压力得以上升,直到两塔压力基本相等。
4.6.2.12六均升压过程。
七均升结束后,A塔通过程控阀与六均罐相连进行均压升压,这时六均罐内的高压氢气就流入A塔被回收,同时A塔压力得以上升,直到两塔压力基本相等。
4.6.2.13五均升压过程。
六均升结束后,A塔通过程控阀与刚完成四均降压步骤的D塔相连进行均压升压,这时D塔死空间内的高压氢气就流入A塔被回收,同时A塔压力得以上升,直到两塔压力基本相等。
4.6.2.14四升压过程。
五均升结束后,A塔通过程控阀与刚完成三均降压步骤的E塔相连进行均压升压,这时E塔死空间内的高压氢气就流入A塔被回收,同时A塔压力得以上升,直到两塔压力基本相等。
4.6.2.15三均升压过程。
四均升压过程结束后,A塔通过程控阀与三均罐相连进行均压升压,这时三均罐内的高压氢气就流入A塔被回收,同时A塔压力得以继续上升,直到两塔压力基本相等。
4.7.5.16二均升压过程。
三均升压过程结束后,A塔通过程控阀与刚完成一均降压步骤的F塔相连进行均压升压,回收F塔死空间内的高压氢气,同时A塔压力得以继续上升,直到两塔压力基本相等。
4.7.5.17一均升压过程。
二均升压过程结束后,A塔通过程控阀与刚完成吸附步骤的G塔相连进行均压升压回收G塔死空间内的高压氢气,同时A塔压力得以继续上升,直到两塔压力基本相等。
七次均压升的过程,不仅可以回收其他吸附塔内死空间氢气,提高氢气的回收率,而且也是逐渐降低或提高吸附塔压力,使吸附塔在压力波动较小的情况下切换到吸附状态,可以有效地防止塔内吸附剂的粉碎现象。
4.7.5.13产品气升压过程
经连续四次均压升压过程后,A塔压力已升至2.006Mpa(G)左右,这时用产品氢对吸附塔进行最后的升压,直到使其达到吸附压力。
经过以上步骤后,A塔的吸附剂得到了完全再生,同时又重新达到了吸附压力,因而已可无扰动地转入下一次吸附。
二、提氢单元(与脱碳单元同,此外略)。
4.7主要设备选择
4.7.1主要设备操作条件
1)原料液泵、脱盐水泵
选用国产的多级离心泵。
2)反应器
采用列管式结构,管程装填催化剂,壳程走导热油。
3)真空泵
脱碳真空泵采用水环式真空泵;提氢部分考虑解吸气回锅炉燃烧,故真空泵采用无油润滑真空泵。
4.7.2装置主要设备
本装置共有主要设备约47台,其中:
转化器3台
水洗塔1台
冷换器4台
容器27台
导热油炉1套
真空泵5台
离心泵4台
管道混合器1台
4.7.3主要设备规格
1)转化器
设备名称
转化器
转化器型式
列管式
介质名称
H2、H2O、CO2、CO、CH4
平均反应温度,℃
230/270(初期/末期)
反应器入口压力,MPa(G)
2.6
堆比,g/cm3
~1.30
实际装入量,m3
14.93
反应器尺寸,mm
Φ2200×11469
2)洗涤塔
序号
设备名称
介质
操作温度
操作压力
填料类型
填料层高度
备注
1
洗涤塔
H、CO、CO2、CH4、水
20~60
~2.6
波纹填料
4米
3)、吸附塔类
序号
设备名称
介质
操作温度(℃)
操作压力(MPa)
填料装填量(m3)
材质
数量
备注
1
脱碳塔
氢气、二氧化碳、一氧化碳、甲烷
40~60
2.6
24.8
Q345R
10
2
提氢塔
氢气、二氧化碳、一氧化碳、甲烷
40~60
2.5
13.9
Q345R
10
4)换热器类汇总表
序号
设备名称
介质
操作温度℃
操作压力(a)MPa
流量
热负荷
对数平均温差
传热面积
折流板
数量
进口
出口
进口
出口
kg/h
kW
℃
m2
间距mm
台
1
2
3
4
5
6
7
8
9
10
11
12
13
1
釜式汽化器
管程
导热油
280
265
0.6
0.6
650000
6800
64
285
1062
1
壳程
甲醇、水
160
210
2.7
2.7
18000
2
原料气换热器
管程
转化气
235
132
2.6
2.6
15800
1600
51
229
360
1
壳程
甲醇、水
85
162
2.7
2.7
18000
3
甲醇预热器
管程
转化气
135
70
2.6
2.6
15800
990
35
229
290
1
壳程
甲醇、水
40
105
2.7
2.7
18000
4
冷凝器
管程
冷却水
30
40
0.4
0.4
120000
750
27
268
320
1
壳程
转化气
105
40
2.6
2.6
13200
5
过热器
管程
导热油
280
274
0.6
0.6
650000
500
24
118
286
1
壳程
甲醇、水蒸汽
5)容器类汇总表
序号
设备名称
台数
型式
介质
操作
操作
流量
主要尺寸
容积m3
装满系数
备注
温度℃
压力(a)MPa
kg/h
m3/h
内径×长度(切线距)mm
1
2
3
4
5
6
7
8
9
10
11
12
13
1
脱盐水高位槽
1
立式
脱盐水
50
常压
4640
4640
Φ1200×2430
2.6
0.5
利旧
2
冷凝液罐
1
卧式
甲醇、水
90
2.6
4360
4360
Φ1000×1450
1.25
0.5
3
洗涤塔
1
立式
脱盐水、氢气、二氧化碳、一氧化碳
50
2.6
Φ1000×9335
6.41
0.5
4
气液分离缓冲罐
1
立式
氢气、二氧化碳、一氧化碳
40
2.55
Φ1600×9232
15.4
1.0
5
三均罐
1
立式
氢气、一氧化碳
40
1.68
Φ2400×11641
45
1.0
脱碳
6
五均罐
1
立式
氢气、一氧化碳
40
1.1
Φ2400×11641
45
1.0
脱碳
7
粗氢气缓冲罐
1
立式
氢气、氧化碳
40
2.45
Φ1800×9887
15.4
1.0
脱碳
8
三均罐
1
立式
氢气、一氧化碳
40
1.65
Φ1800×9887
21
1.0
提氢
9
六均罐
1
氢气、一氧化碳
40
0.58
Φ1800×9887
21
1.0
提氢
10
氢气缓冲罐
1
立式
氢气
40
2.4
Φ1600×8916
15.4
1.0
提氢
11
逆放气缓冲罐
1
立式
氢气
40
0.15
Φ2200×10534
35
1.0
提氢
12
解析气混合罐
1
立式
氢气
40
0.12
Φ2600×11057
50
1.0
提氢
6)泵类
序号
泵名称
流量(kg/h)
进口压力(MPa)
出口压力(MPa)
数量
备注
1
甲醇加压泵
12m3/h
常压
2.8
2
一开一备
2
脱盐水加压泵
5.5m3/h
常压
2.8
2
一开一备
3
循环液增压泵
12m3/h
2.5
2.6
2
一开一备
4
脱碳真空泵
抽气量≥4000m3/h