模具CADCAM理论基础.docx
《模具CADCAM理论基础.docx》由会员分享,可在线阅读,更多相关《模具CADCAM理论基础.docx(16页珍藏版)》请在冰豆网上搜索。
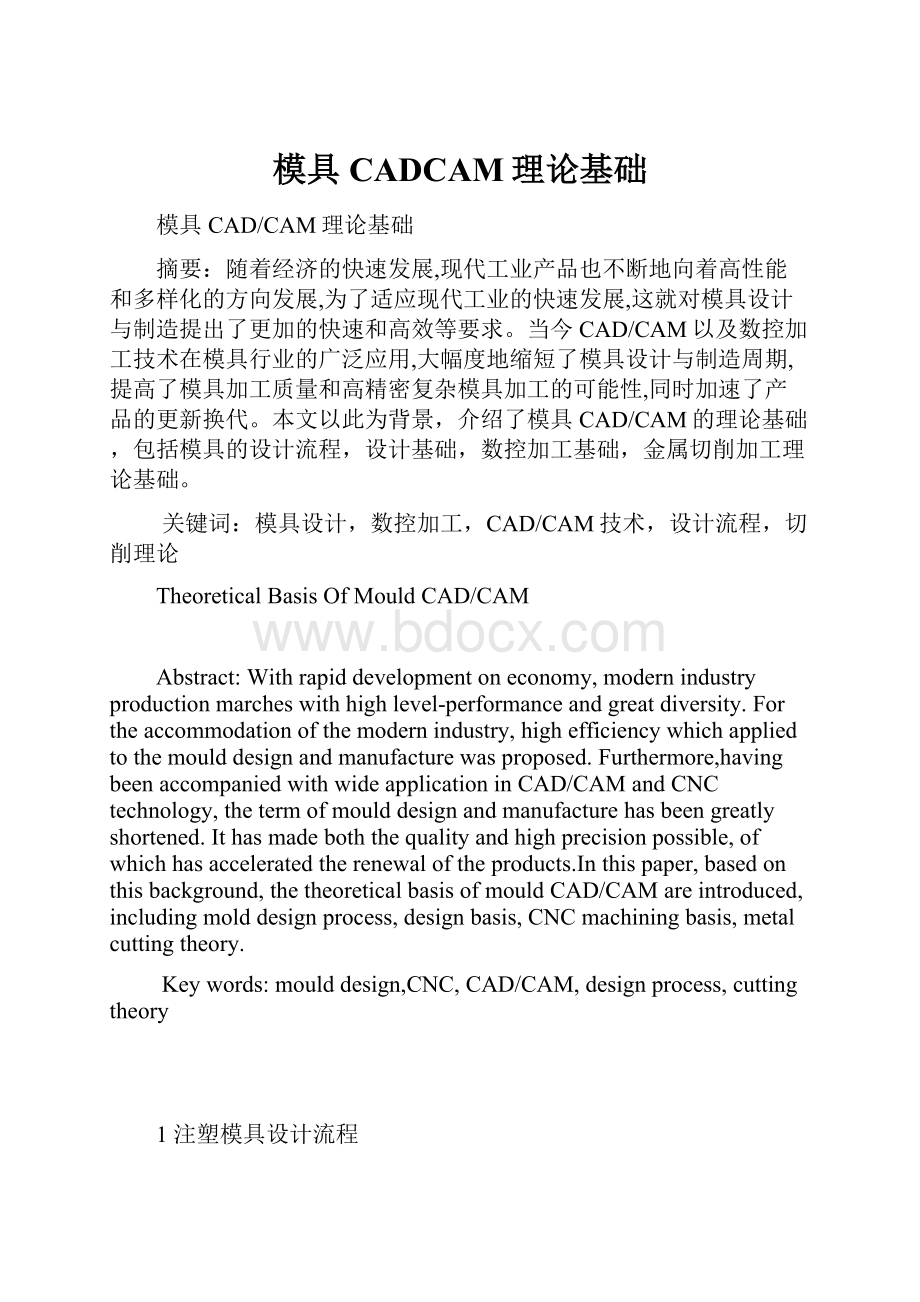
模具CADCAM理论基础
模具CAD/CAM理论基础
摘要:
随着经济的快速发展,现代工业产品也不断地向着高性能和多样化的方向发展,为了适应现代工业的快速发展,这就对模具设计与制造提出了更加的快速和高效等要求。
当今CAD/CAM以及数控加工技术在模具行业的广泛应用,大幅度地缩短了模具设计与制造周期,提高了模具加工质量和高精密复杂模具加工的可能性,同时加速了产品的更新换代。
本文以此为背景,介绍了模具CAD/CAM的理论基础,包括模具的设计流程,设计基础,数控加工基础,金属切削加工理论基础。
关键词:
模具设计,数控加工,CAD/CAM技术,设计流程,切削理论
TheoreticalBasisOfMouldCAD/CAM
Abstract:
Withrapiddevelopmentoneconomy,modernindustryproductionmarcheswithhighlevel-performanceandgreatdiversity.Fortheaccommodationofthemodernindustry,highefficiencywhichappliedtothemoulddesignandmanufacturewasproposed.Furthermore,havingbeenaccompaniedwithwideapplicationinCAD/CAMandCNCtechnology,thetermofmoulddesignandmanufacturehasbeengreatlyshortened.Ithasmadeboththequalityandhighprecisionpossible,ofwhichhasacceleratedtherenewaloftheproducts.Inthispaper,basedonthisbackground,thetheoreticalbasisofmouldCAD/CAMareintroduced,includingmolddesignprocess,designbasis,CNCmachiningbasis,metalcuttingtheory.
Keywords:
moulddesign,CNC,CAD/CAM,designprocess,cuttingtheory
1注塑模具设计流程
随着模具CAD/CAM/CAE技术的广泛的应用与高速发展,很大程度地提高了模具的制造精度、减少了试模的次数以及缩短了设计周期,由此提高了模具的设计和制造效率。
并行设计是相对串行设计的设计方法,它是现在应用最为广泛的模具设计方法,模具的并行设计方法是以提高模具设计与制造质量和效益、缩短产品的幵发周期为目标,采用并行设计方法来设计产品的基本思路是将产品开发周期中各阶段和产品的各个部分的设计同时进行。
并行设计强调的是过程上和功能上的集成,在产品的设计和优化过程中,实现各阶段和各部分不同任务的协同工作,同时进行。
图1注塑模具设计周期
如图1所示,注塑模的设计周期一般包括了注塑件的结构设计、模具设计、模具加工制造和产品生产这四个阶段,所有阶段都相互影响、相互关联,每个阶段都对产品成本、质量、开发周期等产生间接或直接的影响。
模具设计部分是最重要的一个环节,向上它决定了注塑件的设计可否实现,向下制约了模具制造和产品成型能否成功。
根据注塑模并行设计思想,一副完整的注塑模具设计及其加工过程如图2所示。
工作流程各阶段说明如下:
图2精密注塑模具并行设计与加工制作流程图
1注塑件的造型设计,可采用CAD、UG等软件的三维造型功能来设计。
2根据产品需求进行模具的概念设计,其包括绕口类型、型腔数目、模架类型、抽芯方式和脱模方式等。
3在模具方案初步确定之后,采用CAE相关软件进行流动、冷却、保压以及翅曲等分析,来确定适合的冷却系统、绕注系统等。
如果CAE的分析结果不能满足生产要求实现产品的生产,那么可以修改设计方案或者根据用户和产品的使用要求修改产品的结构。
通过多次额模拟制造,制定出合理的注塑工艺。
4在完成通过CAE分析以及方案评价以后,再进行模具结构的详细设计,这包括冷却系统和饶注系统的尺寸及布置,导向脱模机构的设计、镶块、滑块的设计以及标准件的选择等,然后进行模拟幵模、合模与脱模的过程分析,并进行模具组装和运动过程的干涉检查。
这个阶段可以利用CAD等相关软件注塑模具设计模块来进行。
5通过CAM相关软件进行模拟数控加工和自动生成型芯、形腔的数控加工代码。
最后再进行实际制造与装配,并利用先前得到的工艺参数进行试模与生产。
2模具设计基础
2.1注塑件的建模
注塑件的建模指的是在CAD平台上创建注塑件的完整模型。
包括注塑件结构特征和尺寸特征,有时还应包括材料属性特征、物理属性特征和工艺特征等信息。
建模的基本过程包括输入塑料种类的选择、塑件的性能要求、产品外形和结构设计以及确定对模具结构性能和注塑工艺的要求等。
注塑件的建模目的不仅在于设计出满足用户要求的产品,而且还在于为后续设计和制造出这种塑料产品的模具。
塑件模型,应为后续CAD模具设计提供相关信息,为能自动生成模具型腔等提供条件。
通常塑件建模有两种情况:
其一是对已经有现成塑件的建模,在现有塑件结构和尺寸的基础上(或者对尺寸、结构作一定的修改)创建模型;另一种是以及客户的需求来设计新的塑件并创建其模型。
以参数化技术、复合建模技术和特征建模技术为主要特点的CAD技术的发展,为注塑产品的设计建模提供了可靠的保证。
现有的CAD系统对上述两种建模类型都有了较为成熟的技术,而产品模型向信息模型、产品信息向模
具信息的转换将成为今后国内外研究的重点。
2.2模具计算机辅助设计系统
模具CAD设计是在塑件三维实体建模完成的基础上进行模具的结构设计。
设计内容主要包括以下几个方面:
1确定模具的整体设计方案。
包括:
型腔数量及布置,分型面的位置、绕注系统选用何种绕口及是否采用分流道,是否需要有侧向抽芯机构,冷却系统的设计方案,模架类型和规格的选取等等。
由于精密注塑模成型过程中要求较高,在设计时应该注意:
冷却系统是否能将注塑件均勻地冷却、绕注系统(特别是分流道)是否平衡、侧抽芯机构是否有干涉等问题。
2成形零件设计。
成形零件是模具的关键部分,成形零件的表面质量、尺寸精度直接影响到产品的表面质量和精度,在设计成形零件的时候要充分考虑到塑料的收缩率等因素,保证产品的精度和质量。
在精密注塑模具的设计过程中,应考虑如何使成形零件的尺寸变化最小。
这时,不能采用一般注塑模具设计时的计算方法,不能简单地按塑件成形尺寸精度的1/5或1/3来确定成型零件的尺寸精度。
其中日本学者村上宗雄提出的“塑件的尺寸精度和模具的尺寸精度关系”理论被广泛应用。
该理论先用塑件的图面尺寸来得出模具的图面尺寸,再从模具的图面尺寸求出模具的实际尺寸,然后使用制造的模具来注塑得到产品,进而得到产品的实际尺寸。
塑件最终的实际尺寸应在产品所需尺寸的公差范围之内。
同时,该理论认为模具磨损、制造误差、收缩率的偏移、实际收缩率与预计收缩率之差等因素将影响产品尺寸。
3结构零件的设计以及模架等标准件的选择。
在承受注塑压力的过程中,模具各部分的刚度和强度不足会产生变形,进而影响注产品的精度。
虽然模具的结构零件不直接参与塑件成形,但能影响到模腔的精度,从而影响产品的精度。
所以,无论是在设计普通的注塑模,还是在设计精密注塑模具时,都应该对模具的结构零件进行受力校核等,并提出合理尺寸、精度材料等要求。
2.3计算机辅助注塑工艺设计
注塑模具CAE技术是采用计算机对塑料产品成形过程的各个阶段进行定量与或定性的描述,在模具制造之前发现并及时改正设计问题。
依据塑料传热学和流变学的基础理论,建立液态塑料在型腔中的传热、流动等的数学模型,利用计算机数值计算,并将其结果转化为图形,直观、形象地模拟出温度场、压力场、冷却过程及其随时间的变化。
利用CAE技术可以在模具制造之前,评估模具的设计方案,分析和预测成型
缺陷,为方案的修改提供依据,以提高模具制造的可靠性与成功率。
目前所使用的CAE软件都可以模拟塑件的温度场、充模过程、压力场、翅曲变形、应力场等结果。
这些参数的模拟结果不仅可以有助于设计者发现设计方案中存在的缺陷与问题,还有助于获得合适的注塑工艺,这不仅提高了模具设计效率,还提高了模具设计与制造的成功率。
注塑CAE技术的发展主要经历了中性层模拟、三维真实感模拟以及三维模拟三个阶段,每个阶段都有其不同的特点
1早期的注塑CAE软件基本上是基于塑件的中心层流动模拟,也就是中性层模拟。
该技术先将薄壁注塑件抽象成为近似的曲面和平面,即中性面,然后在中性层面上生成二维的平面三角形网格,再对平面三角形网格进行有限元计算。
最终得出的分析结果(每个时间段的压力场、温度场等)在中心层上釆用不同的颜色显示出来。
该技术虽然能够分析形状较为复杂的塑件,但也存在着较大的局限性:
将形状复杂的三维塑件抽象成中心层是一个非常复杂的过程,并且操作过程比较繁琐;分析的结果也缺乏真实感;该方法难以实现CAE与CAD的集成。
2三维真实感模拟是现阶段应用最广泛的注塑模成型过程模拟技术。
该技术不需要中心层,可在三维实体模型上直接进行分析,并且该技术实现了CAE与CAD的集成。
该技术的核心是应用一维有限差分与二维有限元的耦合,首先读取三维塑件实体的有关信息,利用实体的表面信息产生表面的二维平面三角形网格。
对较薄的塑件来说,可以对所有的三角网格节点进行配对,得到节点的配对信息和厚度信息。
再采用得到的节点厚度信息和配对信息以及三角网格数据进行有限元计算,得到的成型过程分析结果能在三维实体表面通过不同的颜色显示出来。
3三维真实感流动模拟技术虽然具有很多优势,但是也存在一些缺陷。
由于采用一维有限差分和二维有限元的稱合,不能兼顾到液态塑料在厚度方向上流动的速度,因此不能分析成型过程中的微观表现,比如液态塑料前沿的推进方式和流动形态。
然而直接利用塑了件三维实体的基本信息来生成立体的三维流动模拟技术,用生成的三维立体网格直接进行有限元计算,并且分析的结果能直接在三维实体上显示出来。
这种技术可以解决上述两种技术所遇到的问题,所以三维流动模拟技术应该是注塑模CAE的发展方向。
3模具数控加工基础
3.1数控加工原理
在零件的加工过程中,把零件的形状、尺寸、加工步骤、工艺参数等编写成数字形式的代码,将这些代码输入数控机床的控制系统中,这些代码经过控制系统运算处理后驱动伺服系统来控制机床工作,自动对零件进行加工。
3.2数控加工特点
相对于普通机床加工而言,数控加工有两个最大的特征:
一个是能大大地提高加工误差精度以及加工质量;另一个是能极大地稳定加工质量,提高加工重复精度,保持加工零件的一致性。
一般来说,数控加工拥有下列优点:
1生产效率高;
2对机床的操作人员要求不高;
3大大地提高加工精度,零件加工的一致性好;
4加工过程管理比较容易;
5能减少工装夹具及装夹时间;
6可以降低次品和废品率;
7设计变更方便,实现柔性加工;
8可以减少检验的工作量;
9自动化程度比较高,一人可以同事操控多台机床;
10操作者的劳动强度低。
[1]
3.3数控加工技术在模具加工中的重要性
随着工业产品不断地向高性能化和多样化的方向发展,客户往往要求模具制造商能在短时间内为其新产品的开发和及生产提供所需的模具。
为了客户的需求,数控加工技术已被模具制造行业广泛应用。
随着电子技术的不断发展,数控技术由以前的硬件数控发展到了计算机控制。
采用计算机控制,不仅提高了数控机床的加工精度,而且拓展了数控技术的应用范围。
随着对数控加工技术不断的研究与完善,各种通用及专用的CAD/CAM系统不断被研发出来,目前数控技术以及CAD/CAM系统在模具设计与加工领域中起着不可替代作用。
在模具加工过程中,利用数加工控技术可明显缩短模具制造周期,提高模具制造加工精度以及降低成本。
数控铣是在模具数控加工中最常用的加工方法。
4数控加工理论基础
数控编程是指从零件形状和尺寸到得到加工程序的整个过程。
数控编程的的任务主要是计算加工走刀过程中的刀位点。
一般来说,取刀具表面的交点与刀具轴线作为刀位点,如果是在多轴加工中需要给出刀轴矢量。
数控编程过程是目前CAD/CAPP/CAM系统中最能体现效益的环节之一,它在实现提高加工质量和加工精度、加工自动化、缩短产品研发周期等这些方面发挥着非常重要的作用。
在汽车工业、航空工业等诸多领域都有着广泛的应用。
[2-4]
4.1NC刀具轨迹生成
数控编程核心主要工作就是生成刀具轨迹,之后将刀具轨迹离散成刀位点,经过处理后产生数控加工程序。
[5]刀具轨迹产生的方法主要有:
1基于点、线、面和体的NC刀具轨迹生成方法
实体加工一般分为实体区域加工和实体轮廓加工两种。
层切法为实体加工的实现方法,该方法是用一族水平面来切被加工的实体,然后对获得的交线产生等距线来作为走刀轨迹。
2基于特征的NC刀具轨迹生成方法
特征加工方法使得数控编程人员不需要对点、线、面和实体进行操作,而直接对特征进行数控编程,这样极大地提高了编程效率。
参数化特征造型已经发展了一段时间,但基于特征的刀具轨迹的生成方法才开始研究不久[6-8]。
实体加工的基础是特征加工,但是特征加工并不等同于实体加工。
实体加工与特征加工的不同之处主要有如下几点:
从概念上来说,特征作为构成零件的基本功能要素,为工程人员熟知,也是非常符合工程人员的操作习惯和思路;而实体是一种低层次的几何对象,是通过布尔运算来获得的一个几何体,它没有功能语义信息。
并且实体加工通常是对零件或实体的一次性加工。
但是在实际生产中每个零件需要多把刀多次加工来完,通常需要有粗加工、半精加工以及精加工等众多的工步来完成,对于零件的各个部位一般需要使用不同的刀具来进行切削等加工;有些时候某个零件既要车削加工,又要使用铣削加工。
通常实体加工主要是用来对零件进行粗加工和半精加工。
但是特征加工能从其本质上解决这些问题,具有较好的智能。
对于某些特定的特征则可以规定一些固定不变的加工方法,尤其是在STEP标准中规定了的那些特征。
假如对全部标准特征都设定好固定的加工方法,这样对由标准特征组成的零件加工就非常的方便了。
如果CAPP系统可以提供这些特定工艺特征,这样以来NCP系统就可以大幅度降低交互输入量,整个系统就更智能。
上述所说的这些是实体加工不可能实现的,而特征加工可实现以CAD、NCP、CNC及CAPP系统的综合集成,以实现彼此之间信息的双向流动,这样就为CMS以及CE(并行工程)的实现打下了基础;而这些导师实体加工做不
到的。
3对CAD/CAM系统中NC刀具轨迹生成方法的分析
目前主要有两种方式实现CAD/CAM系统来集成的CAM系统是比较成熟的:
相对较独立的CAM系统(例如:
Surfcam、Mastercam等)和一体化程度较高的CAD/CAM系统(例如:
Pro/E、UG等)。
前者是从其它CAD系统或文件提取产品的几何模型,而后者采用其内部的数据格式从CAD系统中提取产品的几何模型。
虽然方式有所不同,但无论哪种CAM系统,都是由五个不同的模块组成的,即刀具轨迹生成、交互工艺参数输入、三维加工动态仿真、刀具轨迹编辑以及后置处理这五个模块。
UG是我国模具行业使用较广的CAD/CAM系统之一,它最显著的特点是强大的刀轨生成功能,它包括铣削、车削以及线切割等较为完善的加工方法。
其它的相关软件,例如Cimitron,Euclid,CATIA,CV等的NC刀具轨迹功能各有各的特点,但是基本内容和方法没有本质的区别。
4.2数控加工过程仿真系统(NGEdit)
零件在数控机床上的加工是通过数控指令程序来控制的。
为了确保其程序的准确性,防止在零件加工过程中发生碰撞和干涉,在生产实际中,往往采用试切进行检验。
这种方法不仅费工费料,增加生产成本,而且增加了产品得生产周期。
后来一段时间又采用轨迹显示法,用纸或着色板来代替工件仿真刀具切削轨迹,这种方法也有很大的局限性。
也有用木料、石蜡、塑料和改性树脂等软材料来替代工件进行三维和多维加工来检验切削的轨迹。
但是,这种试切需要占用加工现场和数控机床等资源。
因此,研究人员一直在试验计算机仿真代替试切的方法,并且在图形显示、仿真计算和试切环境模型化等诸多方面都取得了较大的进展。
目前该方法正向着提高模型精度、改善图形显示的真实感以及仿真计算实时化等的方面发展。
根据试切环境的模型特点,现阶段NC切削仿真分为力学仿真和几何仿真这两个方面。
其中几何仿真不需要考虑切削力、切削参数以及其它的因素影响,只仿真刀具相对于工件的运动,来检验NC程序是否正确。
这样能消除或减少因程序有误导致的零件报废、刀具折断或夹具破坏、机床损伤等问题;同时还能縮短从产品的设计到产品制造的时间。
而力学仿真是一种物理仿真,它应用仿真切削过程中的动态力学特征来预测刀具振动、刀具破损以及切削参数,进而实现优化切削过程。
根据仿真过程采用的驱动数据是NC代码还是CL(CutterLocation,即刀位)数据,可将数控加工仿真分作两类:
其一是基于自动编程所得到的的NC程序来进行加工过程仿真;另一类是采用后置处理之前的CL数据进行的加工过程仿真。
因为基于CL数据的加工过程仿真不考虑数控加工中的受力等影响因素,而只能检验刀具轨迹的正确与否,存在较大的局限性。
基于NC程序加工仿真不但能检验加工过程中的干涉以及碰撞,而且能测量加工过程需要的工时,还能根据机床的主轴速度、进给速度等参数模拟加工过程中工件和刀具的温度等多种复杂因素,比较而言,这是一种更加优秀的仿真方法。
5金属切削加工基础理论
5.1切削加工的历史与发展
人们对金属切削基础理论的研究始于17世纪,1679年Hooke的《论刀具切削》出版就是杰出的代表。
[9]但真正对金属切削原理进行深入的研究到19世纪中期才开始。
1851年法国Cocquilhat.M是最早测量了钻头在切削铸铁等金属材料时的扭矩,并且列出了切除单位体积的材料需要功的表格;法国若塞耳于1864年研究了刀具几何形状和参数对切削加工过程中所需力的影响;俄国季梅考于1870年提出了切割过程中被切金属在刀具的前方不但受到挤压,而且会受到剪切力的观点[10];俄国布里克斯于1896年将材料的塑性变形这一概念引入到金属切削的理论中;这时,才比较完整的解释和定义了切屑加工。
英国的Coker于1922年首先采用光学法来研究了切削过程中切屑的形成。
1938到1940年美国M.E.麦钱特和H,厄恩斯特通过显微镜釆用高速摄影机拍下了切屑的形成过程,并进一步用摩擦理论解释和分析了连续切屑和断续切屑的形成原理。
5.2数控加工的切削用量
切削用量的选择原则一般是:
粗加工往往以提高生产效率和加工成本为主,而精加工和半精加工时,首先应该在保证设计所需要达到的加工质量的前提下,同时兼顾加工成本、切削效率以及经济性。
具体数值的选择和制定应根据切削用量手册、机床说明书以及结合实际生产经验来确定[11]。
为了尽可能地提高生产率,并保证切削刀具的耐用度,应使切削速度、进给速度和吃刀量(切削宽度L、切削深度t)三个参数的乘积最大,也就是材料的去除率最大。
上述切削用量的三要素中,任何一个增加都会降低刀具的耐用度,但它们对此的影响程度不一样,切削速度对刀具耐用度的影响最大,进给速度次之,吃刀量影响最小为了提高生产率而使刀具耐用度降低量最小,通常首先应选定尽可能大的吃刀量(切削宽度L、切削深度t),然后选择合适进给速度Vt,最后综合考虑刀具的耐用度来确选定定切削速度V。
1切削深度t
当工艺系统允许以及机床动力足够的情况下,选择的切削深度t基本就等于加工余量,这能显著地提高生产效率。
但是为了保证加工零件的表面粗糖度和尺寸精度,一般情况下都留一定的加工余量来进行后续的精加工。
数控机床比普通机床的精加工余量要小。
2切削宽度L
切削宽度L与刀具直径d—般是成正比的,而跟切削深度成反比。
选用经济型的数控机床进行加工时中,L的取值一般为:
L=(0.6-0.9)d。
3切削速度V
提高切削速度V也是提高加工率的一个有效措施,但切削速度V对刀具耐用度的影响较大。
当切削速度V增大时,刀具的耐用度急剧降低,所以V的选定主要还是要综合考虑刀具的耐用度。
除此之外,V与所加工材料得种类也有比较大的关系,例如立统刀统30CrNi2MoVA合金钢时,v可一般选用8m/min左右;而同样条件下铁削锦合金时,切削速度可以达到200m/min以上[13-14]。
4主轴转速n(r/min)
机床主轴的转速一般需要根据切削速度V来选择。
其计算公式为:
n=1000v/
(1)
式中:
d——工件或刀具的直径(mm)
一般数控机床的控制面板上都有主轴转速倍率开关,可以在事前选定或加工过程中进行主轴转速调整。
5进给速度Vr
进给速度Vr—般是根据所加工工件的表面粗糖度和加工精度要求以及工件材料和刀具来选择,进给速度Vr的提高也有助于生产效率的提高[15]。
进给速度Vr的大小与每齿进给量成正比。
当粗加工时,的选择取决于铣刀类型、刀具材料以及零件所用材料的力学性能。
零件所用材料硬度和强度越高,值选取越小,反之就越大;高速钢洗刀的应小于硬质合金统刀。
而精加工的时候,的选选择需要考虑工件表面质量要求,表面粗糖度越低,Vr越小。
转速n、每齿进给量fz进给速度Vr之间的关系为:
Vr=fzZn
(2)
5.3铣削力、机床动力校核以及铣削功率
1铣削力[16-17]
在统削加工的过程中,统削力是影响加工质量和刀具耐用度的主要因素之一,又是测算切削功率以及校核机床功率的重要依据。
铣削过程中,把一个刀齿上受到的总铁削力Fr分解得到3个相互垂直的分力,即背向力Fp、垂直切削力Fn和切削力Fc。
背向力Fp作用于沿统刀的轴线方向。
对螺旋齿圆柱铁刀来说,Fp是由螺旋齿所产生的,Fn和Fp的大小受铣刀螺旋角影响,而直齿圆柱统刀的Fp为零。
垂直切削力Fn是在工作平面上,是总的统削力在垂直于主运动方向上的分力。
它作用在垂直于统刀轴线方向上,使铣刀刀杆有产生弯曲的趋势。
切削力Fc是统削力在主运动方向上的分力,作用与统刀外圆的切线上,消耗了机床大部分的功率,因此又称作主切削力。
一般在计算铣削力时只需计算主切削力Fc,在一个刀齿上所承受的平均铣削力的简便实用的公式如下所示:
(3)
(4)
式中:
HBS——被加工材料的布氏硬度。
A平均——多刃刀具切削面积的平均值,单位
。
若有Z个刀齿同时工作,那么该统刀总切削力
:
为:
(5)
2铣削功率
铣削加工过程中主切削力所消耗的功率Pc(单位:
KW)的计算公式为:
(6)
进给运动所消耗的功率Pf—般情况下为0.15Pc,因此总的统削功率Pm可记为:
(7)
同时,考虑到机床的机械损耗,那么选用的机床必须具备功率大于
的电动机:
(8)
式中:
——机床效率,其值一般在0.75到0.85之间。
5.4数控加工所用刀具的选择原则
刀具的选择通常是在数控编程过程中的人机交互状态下完成的。
刀具的选择应根据工件材料的性能、机床的加工能力、切削用量、加工工序等因素来选用合适的刀柄和刀具。
刀具选用的基本原则是:
精度和耐用度高,刚性好,安装以及调整方便。
在满足使用要求的情况下,尽可能地选用较短的刀柄来提高刀具的刚性。
数控机床上所用的刀具跟普通机床使用的刀具相比,有较大的区别,其热点主要有:
1互换性好,方便快速换刀;
2刚性好,热变形小,精度