A3000试验台管道压力和流量接偶控制系统设计毕业设计.docx
《A3000试验台管道压力和流量接偶控制系统设计毕业设计.docx》由会员分享,可在线阅读,更多相关《A3000试验台管道压力和流量接偶控制系统设计毕业设计.docx(96页珍藏版)》请在冰豆网上搜索。
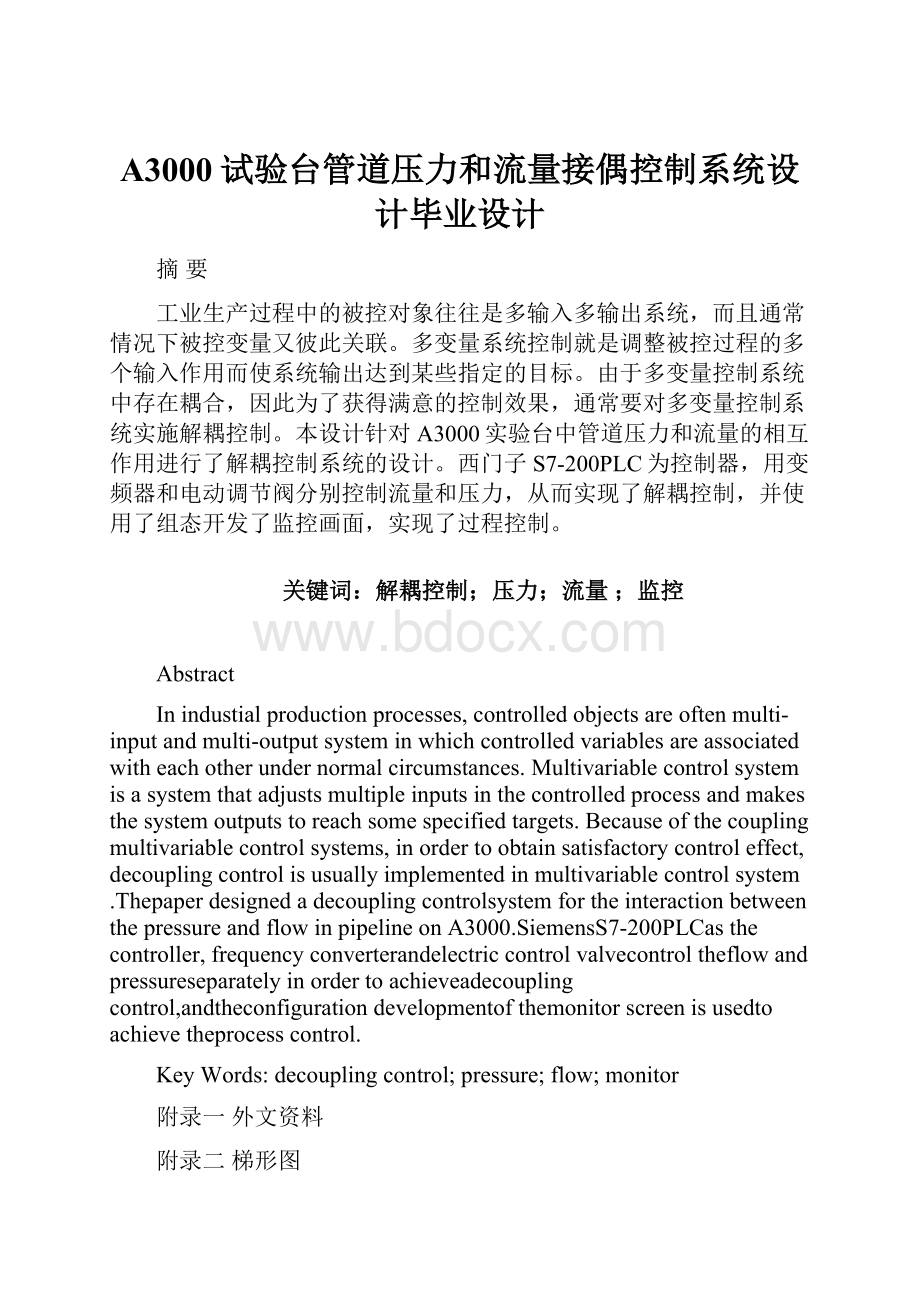
A3000试验台管道压力和流量接偶控制系统设计毕业设计
摘要
工业生产过程中的被控对象往往是多输入多输出系统,而且通常情况下被控变量又彼此关联。
多变量系统控制就是调整被控过程的多个输入作用而使系统输出达到某些指定的目标。
由于多变量控制系统中存在耦合,因此为了获得满意的控制效果,通常要对多变量控制系统实施解耦控制。
本设计针对A3000实验台中管道压力和流量的相互作用进行了解耦控制系统的设计。
西门子S7-200PLC为控制器,用变频器和电动调节阀分别控制流量和压力,从而实现了解耦控制,并使用了组态开发了监控画面,实现了过程控制。
关键词:
解耦控制;压力;流量;监控
Abstract
Inindustialproductionprocesses,controlledobjectsareoftenmulti-inputandmulti-outputsysteminwhichcontrolledvariablesareassociatedwitheachotherundernormalcircumstances.Multivariablecontrolsystemisasystemthatadjustsmultipleinputsinthecontrolledprocessandmakesthesystemoutputstoreachsomespecifiedtargets.Becauseofthecouplingmultivariablecontrolsystems,inordertoobtainsatisfactorycontroleffect,decouplingcontrolisusuallyimplementedinmultivariablecontrolsystem.ThepaperdesignedadecouplingcontrolsystemfortheinteractionbetweenthepressureandflowinpipelineonA3000.SiemensS7-200PLCasthecontroller,frequencyconverterandelectriccontrolvalvecontroltheflowandpressureseparatelyinordertoachieveadecouplingcontrol,andtheconfigurationdevelopmentofthemonitorscreenisusedtoachievetheprocesscontrol.
KeyWords:
decouplingcontrol;pressure;flow;monitor
附录一外文资料
附录二梯形图
第一章绪论
1.1选题背景及A3000实验台介绍
过程控制是生产过程自动控制的简称,这是自动化技术的一个重要组成部分。
通常是指石油、化工、电力、冶金、轻工、建材、核能等工业生产中连续的或按一定周期与程序进行的生产过程自动控制。
在现代工业生产过程中,过程控制技术正在为实现各种最优的技术经济指标、提高经济效益和劳动生产率、改善劳动条件、保护生态环境等方面起着越来越大的作用。
A3000过程控制实验系统是以工业现场工艺设备为背景,以自动化教学要求和自动化工程师认证技能测试要求为依据推出的实验、培训和测试平台。
1.1.1A3000总体架构
A3000测试平台总体物理系统如图1-1所示。
(控制系统有30多种,现场系统可能具有现场总线。
)
图1-1A3000测试平台总体物理系统图
逻辑结构如图1-2所示。
图1-2逻辑结构图
A3000现场系统特性:
1.尺寸:
1450(毫米宽度)X700(毫米深度)X1950(毫米高度)。
全不
锈钢框架。
2.电力:
三相接地四线制380V±10%,单相三线制,220V±10%,
3.能耗:
最大额定用电6kw/h。
自来水120L,可重复使用。
A3000控制系统特性:
1.尺寸:
800(宽度)X60(深度)X1950(高度)。
标准工业机柜。
2.电力:
单相三线制,220V±10%,
3.能耗:
最大额定用电1kw/h
1.1.2测试平台现场系统
物理受控系统包括了测试对象单元、供电系统、传感器、执行器(包括变频器及移相调压器),从而组成了一个只需接受外部标准控制信号的完整、独立的现场环境。
下面使用示意图和流程图方式介绍现场系统的结构、原理、操作和维护。
为了防止动力设备静电积累而触电或者损坏设备,所以系统必须可靠接地现场系统包括三个水箱,一个大储水箱,一台锅炉,一个工业用板式换热器,两个水泵,大功率加热管,滞后时间可以调整的滞后系统。
现场系统工艺流程图如图1-3所示。
图1-3现场系统工艺流程图
1.2解耦的概念
耦合是指两个或两个以上的体系或两种运动形式间通过相互作用而彼此影响以至联合起来的现象。
解耦就是用数学方法将两种运动分离开来处理问题,常用解耦方法就是忽略或简化对所研究问题影响较小的一种运动,只分析主要的运动。
数学中解耦是指使含有多个变量的数学方程变成能够用单个变量表示的方程组,即变量不再同时共同直接影响一个方程的结果,从而简化分析计算。
通过适当的控制量的选取,坐标变换等手段将一个多变量系统化为多个独立的单变量系统的数学模型,即解除各个变量之间的耦合。
最常见的有发电机控制,锅炉调节等系统。
软件开发中的耦合偏向于两者或多者的彼此影响,解耦就是要解除这种影响,增强各自的独立存在能力,可以无限降低存在的耦合度,但不能根除,否则就失去了彼此的关联,失去了存在意义。
在现代化的工业生产中,不断出现一些较复杂的设备或装置,这些设备或装置的本身所要求的被控制参数往往较多,因此,必须设置多个控制回路对该种设备进行控制。
由于控制回路的增加,往往会在它们之间造成相互影响的耦合作用,也即系统中每一个控制回路的输入信号对所有回路的输出都会有影响,而每一个回路的输出又会受到所有输入的作用。
要想一个输入只去控制一个输出几乎不可能,这就构成了“耦合”系统。
由于耦合关系,往往使系统难于控制、性能很差。
三种解耦理论分别是:
基于Morgan问题的解耦控制,基于特征结构配置的解耦控制和基于H_∞的解耦控制理论。
在过去的几十年中,有两大系列的解耦方法占据了主导地位。
其一是围绕Morgan问题的一系列状态空间方法,这种方法属于全解耦方法。
这种基于精确对消的解耦方法,遇到被控对象的任何一点摄动,都会导致解耦性的破坏,这是上述方法的主要缺陷。
其二是以Rosenbrock为代表的现代频域法,其设计目标是被控对象的对角优势化而非对角化,从而可以在很大程度上避免全解耦方法的缺陷,这是一种近似解耦方法。
选择适当的控制规律将一个多变量系统化为多个独立的单变量系统的控制问题。
在解耦控制问题中,基本目标是设计一个控制装置,使构成的多变量控制系统的每个输出变量仅由一个输入变量完全控制,且不同的输出由不同的输入控制。
在实现解耦以后,一个多输入多输出控制系统就解除了输入、输出变量间的交叉耦合,从而实现自治控制,即互不影响的控制。
互不影响的控制方式,已经应用在发动机控制、锅炉调节等工业控制系统中。
多变量系统的解耦控制问题,早在30年代末就已提出,但直到1969年才由E.G.吉尔伯特比较深入和系统地加以解决。
解耦的方法有三种:
完全解耦控制,静态解耦控制和软件解耦
完全解耦控制,对于输出和输入变量个数相同的系统,如果引入适当的控制规律,使控制系统的传递函数矩阵为非奇异对角矩阵,就称系统实现了完全解耦。
使多变量系统实现完全解耦的控制器,既可采用状态反馈结合输入变换的形式,也可采用输出反馈结合补偿装置的形式
静态解耦控制,一个多变量系统在单位阶跃函数(见过渡过程)输入作用下能通过引入控制装置实现稳态解耦时,就称实现了静态解耦控制。
对于线性定常系统(A,B,C),如果系统可用状态反馈来稳定,且系数矩阵A、B、C满足关于秩的关系式,则系统可通过引入状态反馈和输入变换来实现静态解耦。
多变量系统在实现了静态解耦后,其闭环控制系统的传递函数矩阵G(s)当s=0时为非奇异对角矩阵;但当s≠0时,G(s)不是对角矩阵。
对于满足解耦条件的系统,使其实现静态解耦的状态反馈矩阵K和输入变换矩阵L可按如下方式选择:
首先,选择K使闭环系统矩阵(A-BK)的特征值均具有负实部。
随后,选取输入变换矩阵,式中D为非奇异对角矩阵,其各对角线上元的值可根据其他性能指标来选取。
由这样选取的K和L所构成的控制系统必定是稳定的,并且它的闭环传递函数矩阵G(s)当s=0时即等于D。
在对系统参数变动的敏感方面,静态解耦控制要比完全解耦控制优越,因而更适宜于工程应用。
软件解耦,说起软件的解耦必然需要谈论耦合度,降低耦合度即可以理解为解耦,模块间有依赖关系必然存在耦合,理论上的绝对零耦合是做不到的,但可以通过一些现有的方法将耦合度降至最低。
做事情要想事半功倍,就要高处着眼,触摸到事情的脉络。
当今流行着各种眼花缭乱的软件框架,不管是struts,还是spring,hibernate,还是.net,还是各种前端UI框架,其设计的核心思想是:
尽可能减少代码耦合,如果发现代码耦合,就要采取解耦技术;
解耦方法有但不限有如下几种:
(a)采用现有设计模式实现解耦,如事件驱动模式、观察者模式、责任链模式等都可以达到解耦的目的;
(b)采用面向接口的方式编程,而不是用直接的类型引用,除非在最小内聚单元内部。
但使用该方法解耦需要注意不要滥用接口。
(c)高内聚,往往会带来一定程度的低耦合度。
高内聚决定了内部自行依赖,对外只提供必须的接口或消息对象,那么由此即可达成较低的耦合度。
解耦控制是多变量系统控制的有效手段。
在现代化的工业生产中,不断出现一些较复杂的设备或装置,这些设备或装置的本身所要求的被控制参数往往较多,因此,必须设置多个控制回路对该种设备进行控制。
由于控制回路的增加,往往会在它们之间造成相互影响的耦合作用,这就构成了“耦合”系统。
由于耦合关系,往往使系统难于控制、性能很差。
在解耦控制问题中,基本目标是设计一个控制装置,使构成的多变量控制系统的每个输出变量仅由一个输入变量完全控制,且不同的输出由不同的输入控制。
在实现解耦以后,一个多输入多输出控制系统就解除了输入、输出变量间的交叉耦合,从而实现自治控制。
对于输出和输入变量个数相同的系统,如果引入适当的控制规律,使控制系统的传递函数矩阵为非奇异对角矩阵系统就实现了完全解耦。
使多变量系统实现完全解耦的控制器,既可采用状态反馈结合输入变换的形式,也可采用输出反馈结合补偿装置的形式。
1.3管道压力和流量的解耦控制
管道流量压力控制系统就是一个耦合的系统,如图1-4,系统阀1和系统阀2对管道压力的影响同样强烈,对流量的影响程度也相同。
因此当压力偏低是开大控制阀1,流量也将增加,此时通过流量控制器而关小阀2,结果又使管道中的压力上升,阀1和阀2相互作用相互影响着,这是一个典型的关联系统,关联系数与温度等其他因素无关,具有一致性。
流量也有类似的情况
图1-4管道压力和流量耦合系统图
1.4设计内容
1.4.1设计要求
熟悉控制工艺流程、串级控制的原理,了解串级控制的特点,查阅相关科技文献,掌握控制、检测、通讯等技术要求;对控制系统进行建模(包括机理建模和实验建模);掌握液位和流量系统对控制的要求,提出控制方案(包括方案论证与确定、技术经济分析等内容),完成硬件设计(其中还包括理论分析、设计计算、实验及数据处理、设备及元器件选择等),根据工艺要求合理优化,完成软件需求的系统分析和编制;撰写设计说明书,绘制图纸;指定内容的外文资料翻译。
1.4.2设计思想
本文讨论的是A3000实验台管道压力和流量的解耦控制,当流量增大时,调小变频器,同时管道压力也变小,增大调节阀,压力变小,但流量又会增大。
为了解决这种耦合带来的不便,通过解耦,采用某种结构,寻找合适的控制规律来消除系统中各控制回路之间的相互耦合关系,使每一个输入只控制相应的一个输出,每一个输出又只受到一个控制的作用。
即让电动调节阀只控制压力,变频器只控制流量。
如图1-5所示:
图1-5管道压力与流量解耦控制示意图
A3000实验台管道压力与流量系统主要包括的对象有:
下水箱,储水箱,电动调节阀,变频器,增压泵和送水管道以及管道中用到的旋塞阀。
这些设备由实验台上两个支路并联构成:
涉及的支路1由增压泵,储水箱,涡轮流量计,部分供水管道以及管道中用到的旋塞阀;涉及的支路2由涡轮流量计,压力变送器,电动调节阀下水箱,部分管道以及管道中用到的旋塞阀。
由变频器控制增压泵的出水量来调整管道中的压力与流量;由电动调节阀控制阀门的开度也能调整管道中的压力与流量
如图2,水介质由泵P101(变频器U-101驱动)从水箱V104中加压获得压头,经手阀QV-103(用于两个支路连接)、流量计FT-101、压力传感器PT101、电动阀FV-101、水箱V103、手阀QV-116回流至水箱V104而形成水循环,水箱只作为一连通器,其中,给水压力由压力变送器PT-101测得,给水流量由FT-101测得。
本例为解耦调节系统,调节阀FV-101为被控变量压力PT-101的操纵变量,变频器U-101为被控变量流量FT-101的操纵变量,两条支路各自的调节器的运算输出通过解耦器的函数解耦运算,分别去控制各自调节回路的操纵变量。
管道中流量、压力控制系统就是相互耦合的系统。
变频器和调节阀都对系统的压力和流量造成影响,因此,当压力偏大而开大调节阀时,流量也将增加,如果此时通过流量控制器作用而调小变频器,结果又使管路的压力下降,变频器和调节阀互相影响,这是一个典型的关联系统。
关联的系数与温度等参数无关。
由于系统变频器调节I支路流量,调节阀调节II支路流量,为了实现解耦实验,需要并联两个支路。
并管之后还可以选择使用II支路的电磁流量计来进行流量测量。
在解耦设计方面,我们可以通过前馈补偿解耦法或者对角阵解耦法,使得一个被调节量仅与一个调节器输出量之间有关系,而与另一个独立。
从而达到解耦目的
而设计中要解决的设计难题是,一个PID控制只有一个过程值输入一个输出,要解决两输入两输出的问题,需要设计解耦器,使用两个PID控制器;并且解耦器的设计是比较困难的,而两个输入和输出组合一个PID调解器也是设计中的难题。
控制阀和变频器对系统压力的影响程度同样强烈,对流量的影响程度也相同。
解决这些难题需要通过数学建模来解决,这一点我会在第二章第二节会讨论到。
第二章系统方案选择
2.1常见控制规律的类型
比例积分微分调节(PID调节):
PID调节器的动作规律是
(2.1)
或
(2.2)
式中δ、TI和TD参数意义与PI、PD调节器相同。
2.2控制方案的比较选择
单回路控制系统是过程控制中结构最简单的一种形式,它只用一个调节器,调节器也只有一个输入信号,从系统方框图看,只有一个闭环。
在大多数情况下,这种简单系统已经能够满足工艺生产的要求,因此,它是一种最基本的、使用最广泛的控制系统。
但是也有另外一些情况,譬如输入输出对象是多变量,别且之前还存在耦合,这往往要用到多个控制回路,这时单回路控制系统就无能为力了。
另外,随着生产过程向着大型、连续和强化方向发展,对操作条件要求更加严格,参数间相互关系更加复杂,对控制系统的精度和功能提出许多新的要求,对能源消耗和环境污染也有明确的限制。
为此,需要在单回路的基础上,采取其它措施,组成复杂控制系统,而解耦控制系统就是解决多变量耦合,改善控制精度和控制质量极为有效的控制系统。
压力和流量是工业生产过程中常用的两个参数,对压力和流量进行控制的装置在工业生产中应用的十分普遍。
而两者之间又使典型的耦合关系,所以必须采取解耦控制才能取得较好的控制效果
2.3解耦控制系统数学模型的建立
2.3.1机理建模和实验建模的运用
对于管道中流量、压力控制系统这个相互耦合的系统,变频器和调节阀都对系统的压力和流量造成影响。
因此,当压力偏大而开大调节阀时,流量也将增加,此时通过流量控制器作用而调小变频器,结果又使管路的压力下降,变频器和调节阀互间互相影响,这是一个典型的关联系统。
关联的系数与温度等参数无关。
如图2-1所示
图2-1管道压力与流量解耦控制
我们固定P1在小范围内,由于不涉及温度等问题,所以该过程基本上只与压力和开度有关,是时不变的。
如果把P1定义成未知数,则可以列出一个方程。
使用对角矩阵法进行解耦算法。
如图2-2所示。
图2-2解耦控制系统框
Gc1为流量-变频器的调节器,反作用;Gc2为压力-调节阀的调节器,正作用。
对于对象,被调量与调节量具有y=Pμ关系,这里换一个变量符号。
公式(2-1)
(2-1)
加入控制系统,那么调节量来源于解耦器,调节器(可以是一个PID调节器,等等)输出就是解耦器输入。
(2-2)
对于采用了解耦器的系统传递函数
(2-3)
综合上面的关系,如果G矩阵的逆存在,则我们可以设计D就等于它的逆乘以一个对角阵(可以是单位矩阵),这样可以使得一个被调节量仅与一个调节器输出量之间有关系,而与另一个独立。
从而达到解耦目的。
根据我们实验测得P0=80,P2=5,P1设为未知数x。
实际数值P0=150kPa*80%
水柱,P2=150kPa*5%水柱。
那么增益矩阵为
(2-4)
解耦矩阵
(2-5)
注意压力与流量有一个限制关系。
简单的,在变频器为35Hz,调节阀开度50%时,这个压力和流量将作为系统稳定时的给定值,然后在这个值附近变动。
不能变化太大,否则无法稳定。
如果量程范围不一样,或者水泵特性改了,则整个矩阵不同。
为了统一,设置如下:
(2-5)
2.3.2PID参数的整定方法
1)衰减振荡法PID控制器参数整定
由于工业生产安全稳定性要求,在不允许进行等幅振荡试验,或者对象特性无法达到等幅振荡的场合,可以采用衰减振荡法进行PID控制器参数整定。
与临界比例度法比较而言,参数整定步骤完全相同,唯一的区别是采用纯比例作用得到4:
1衰减振荡时的纯比例增益,Ks4:
1衰减的阶跃干扰的响应曲线为参数整定计算依据。
令Ts为4:
1衰减振荡周期,PID参数估算方法参见表2-1。
衰减振荡法控制器参数整定的优点是,整定质量较好、对工艺过程干扰较小、安全可靠。
缺点是,对于时间常数小的系统不易测取衰减振荡周期TS,干扰频繁的系统也不宜使用。
表2-1衰减振荡法PID控制器参数整定计算表
控制规律
P(Kc)
I(Ti)秒
D(Td)秒
P
KS
PI
0.83KS
O.5TS
PID
1.25KS
0.3TS
0.1TS
2)用经验法整定调节器的参数
经验法是依据阶跃响应曲线的形状,调整控制器参数,具有简单方便,适用于记录曲线不规则,外界干扰频繁的控制系统等优点。
缺点是参数整定花费时间长、整定结果因人而异,没有明确的标准。
经验法的步骤如下:
1.首先进行纯比例凑试。
置积分时间最大Ti=∞,微分时间为零Td=0。
参考表2-1大致选择控制器的比例增益Kc(或比例度PB)的初值。
将控制器投自动,对设定值施加一个偏移,记录响应曲线并观察曲线形状,尽量得到4:
1的衰减响应曲线。
通常,加大增益Kc响应曲线振荡加强,减小Kc响应曲线振荡减弱。
每改变一次Kc都要对设定值施加一个偏移,并记录响应曲线,观察曲线形状,直到满足要求。
2.第二步进行积分作用凑试。
先选择一个初始积分时间值,减小积分时间,积分作用增强;加大积分时间,积分作用减弱。
同比例凑试,每改变一次积分时间,都要施加阶跃干扰,并观察响应曲线。
由于加入积分作用后系统稳定性有所降低,应将比例增益Kc减小10~20%左右,以便补偿加入积分作用后导致的系统稳定性下降。
3.如果需要,最后加入微分作用。
微分时间越大,微分作用越强。
微分时间Td大约是积分时间Ti的1/3~1/4。
加入微分作用后,可适当加大Kc,减小Ti。
表2-2经验法P.I.D.参数范围
系统
P.I.D参数
Kc
PB(%)
Ti(秒)
Td(秒)
流量
1-2.5
40-100
6-60
2-10
压力
1.4-2.3
30-70
20-180
2-20
温度
1.6-5
20-60
180-600
10-100
液位
1.25-25
4-80
按照以上三个步骤,经过反复凑试直到满意。
经验法P.I.D.参数范围如表2-2所示。
通常,对于数字式控制器而言,P.I.D.的调整范围如下:
KC=0.1~200(PB=999~0.5%)、Ti=1~9999s、Td=0~9999s
3)响应曲线法PID控制器参数整定
前面三种方法都不需测试对象的动态特性,并且是在闭环系统中进行参数整定。
而响应曲线法是在开环情况下,测试广义对象动态特性的控制器参数整定方法。
本方法步骤如下:
1.首先测取广义对象在阶跃输入下的响应曲线。
2.在响应曲线的拐点处作切线,通过切线与初始值和新稳态值的交点,可以测得广义对象的时间常数TP和纯滞后时间τ。
于是可以得到一阶惯性加纯滞后通道传递函数简化模型,表达了广义对象动态特性。
按照表2-3提供的计算公式,计算得到控制器的最佳参数值。
表2-3响应曲线法PID控制器参数整定计算表
控制规律
P(Kc)
I(Ti)秒
D(Td)秒
P
Tp/Kpτ
PI
0.9Tp
2.3τ
PID
1.2Tp
2τ
0.5τ
闭环加阶跃干扰试验整定参数的效果,由于可能出现测试误差,可适当修改相关参数,直到响应曲线满意为止。
响应曲线法应用普遍,具有较高的准确度,测试时对生产过程的干扰不大。
然而,当广义对象是非自衡过程时无法应用本方法。
2.4控制器的选择
2.4.1PLC的基本结构
PLC,即可编程逻辑控制器,它采用一类可编程的存储器,用于其内部存储程序,执行逻辑运算、顺序控制、定时、计数与算术操作等面向用户的指令,并通过数字或模拟式输入/输出控制各种类型的机械或生产过程
可编程逻辑控制器实质是一种专用于工业控制的计算机,其硬件结构基本上与微型计算机相同,基本构成为:
1)电源
可编程逻辑控制器的电源在整个系统中起着十分重要的作用。
如果没有一个良好的、可靠的电源系统是无法正常工作的,因此,可编程逻辑控制器的制造商对电源的设计和制造也十分重视。
一般交流电压波动在+10%(+15%)范围内,可以不采取其它措施而将PLC直接连接到交流电网上去
2)中央处理单元(CPU)
中央处理单元(CPU)是可编程逻辑控制器的控制中枢。
它按照可编程逻辑控制器系统程序赋予的功能接收并存储从编程器键入的用户程序和数据;检查电源、存储器、I/O以及警戒定时器的状态,并能诊断用户程序中的语法错误。
当可编程逻辑控制器投入运行时,首先它以扫描的方式接收现场各输入装置的状态和数据,并分别存入I/O映象区,然后从用户程序存储器中逐条读取用户程序,经过命令解释后按指令的规定执行逻辑或算数运算的结果送入I/O映象区或数据寄存器内。
等所有的用户程序执行完毕之后,最后将I/O映象区的各输出状态或输出寄存器内的数据传送到相应的输出装置,如此循环运行,直到停止运行。
为了进一步提高可编程逻辑控制器的可靠性,对大型可编程逻辑控制器还采用双CPU构成冗余系统,或采用三CPU的表决式系统。
这样,即使某个CPU出现故障,整个系统仍能正