6A文硅片事业部MES系统研发及实施项目总结报告.docx
《6A文硅片事业部MES系统研发及实施项目总结报告.docx》由会员分享,可在线阅读,更多相关《6A文硅片事业部MES系统研发及实施项目总结报告.docx(40页珍藏版)》请在冰豆网上搜索。
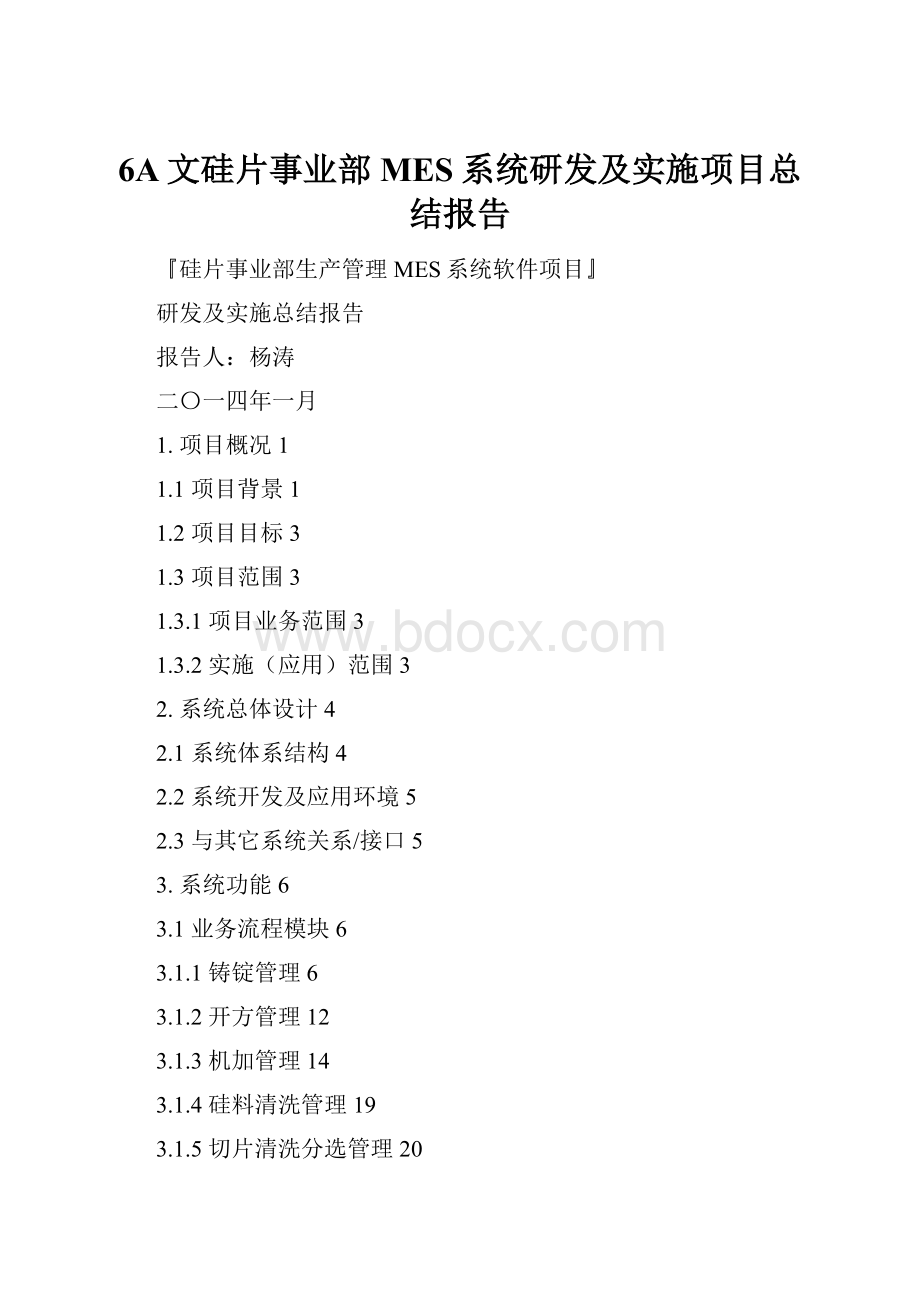
6A文硅片事业部MES系统研发及实施项目总结报告
『硅片事业部生产管理MES系统软件项目』
研发及实施总结报告
报告人:
杨涛
二〇一四年一月
1.项目概况1
1.1项目背景1
1.2项目目标3
1.3项目范围3
1.3.1项目业务范围3
1.3.2实施(应用)范围3
2.系统总体设计4
2.1系统体系结构4
2.2系统开发及应用环境5
2.3与其它系统关系/接口5
3.系统功能6
3.1业务流程模块6
3.1.1铸锭管理6
3.1.2开方管理12
3.1.3机加管理14
3.1.4硅料清洗管理19
3.1.5切片清洗分选管理20
3.2业务管理模块27
3.2.1生产计划模块27
3.2.2产量管理模块28
3.2.3质量及过程管理模块31
3.2.4锭块片集成管理模块33
3.2.5在制品存货管理34
3.2.6铸锭投料监测管理36
3.3系统管理模块37
3.3.1系统运行条件及参数管理37
3.3.2操作日志管理38
3.3.3用户及密码管理39
3.3.4内网在线信息沟通40
4.实施应用效果41
5.结论42
1.项目概况
硅片事业部MES系统完全自我研发并独立实施,充分结合大全硅片实
际生产业务,满足从硅料导入至硅片发货的整个生产过程,量身定制,实现全过程无缝衔接与数据共享集成,整合人、机、料及业务规则,确保各工序在统一生产体系环境中规范业务操作,并实时监测生产进度,质量达成以及主要物资消耗,实现硅片生产过程的量化管理,有力打造生产管理的数据支撑平台。
同时,兼具良好的用户交互性与功能延展性,软件所有界面均支持数据导出功能,便于不同部门实时采集生产过程中人、机、料信息并进行不同需求的分析,提高生产应变能力。
硅片事业部MES生产管理系统经历8个月的应用,实践证明具有良好的适宜性、集成性和交互性,这也是任何一款系统应用软件是否具备实际应用价值的三大判定要素。
1.1项目背景
在决定自主研发MES系统之前,我们曾经打算引进上海上扬软件公司的MES系统,但在调研阶段,因困于某些外部因素导致项目暂停,在此阶段,硅片事业部生产管理信息采集以手工录入为主,除原已运行的ERP外,没有其它可用于生产过程管理的软件,但ERP只能为我们解决对物料的计划及供应、库存管理,生产过程则好比暗箱,各车间、各工序均有不同数据统计模式,相互不存在数据共享和集成,因为是手工统计,不免出现录入错误和时间滞后,导致车间与部门管理者不能及进获取准确生产数据,极大地限制了对生产过程的实进有效管理,生产中普遍出现的状况是:
1、生产进度跟踪滞后,为了解生产情况,往往需要花较多的时间去
现场统计数据,当产量提升后,现场流转速度加快,管理者很难及时跟进实际生产变化的节奏。
2、生产过程中上下工序衔接困难,下道工序不清楚前道工序产出节拍,很难提前应对异常,并有效作出本工序生产作业计划。
3、生产在制品流转易出现混乱,尤其突出的是硅块加工工序,在手工统计时期,无法随时掌握机加在制硅块的准确数量、重量及存放位置。
4、缺乏对主要生产设备的运行时间监控,统计分析设备停机、运行、切换时间没有准确数据支撑,无法有效获取计算设备利用率、稼动率的基础数据。
5、生产过程控制缺乏有效管理和追溯机制,无法及时获取从硅料投入至硅片产出的全面跟踪数据,在不同的手工录入表单中建立链接实现困难程度较高。
6、设立专门的统计员完成数据流程卡录入,因统计员个人对生产情况的认知度不同再加上手工填写的可识别性差异,导致数据录入准确性差,同时,在数据量极大的情况下,手工输入的EGCEL表单运行非常困难。
7、生产车间各个班组绩效考评量化困难,不能及时获取及时的分到不同班组或个人的产量、质量、效率数据,往往到月底时才进行统计,日常班组、个人工作进展情况难以公示,从而很难做到事中激励。
8、事业部生产综合管理信息不能及时共享和输出,事业部管理者获取生产信息的条件有限。
1.2项目目标
通过MES的研发及实施,实现硅片生产过程人、机、料数据全面集成与共享,确保生产信息准确性,达到从硅料至硅片的全过程实时追溯,建立事业部生产业务数据平台,支撑所有部门利用平台数据开展各项业务数据分析和量化工作激励,为改善硅片事业部的生产运作效率和质量提供辅助。
1.3项目范围
1.3.1项目业务范围
MES系统主要对硅片生产过程产生的业务流进行管理,包含配料、铸锭、开方、机加、切片、硅片清洗、分选及包装、硅锭边皮料清洗、业务综合管理等功能模块。
1.3.2实施(应用)范围
MES系统实施应用于硅片事业部铸锭车间、开方机加车间、切片车间(也包括硅片清洗和分选包装)、硅料清洗车间、生产部、质量部,同时为事业管理层、综合管理部、公司财务部等提供生产综合管理数据查询。
2.系统总体设计
2.1系统体系结构
硅片事业部MES系统总体设计流程图
2.2系统开发及应用环境
硅片事业部MES系统采用服务器与客户端并行架构,服务器存储数据库文件和负载企业应用逻辑,客户端采用绿色版可执行文件,容量较小,可通过邮件发布,不需要安装,对客户终端电脑配置无最低要求。
服务器硬件:
DELLR810-双CPU-至强E7-2803,物理12核24逻辑线程,4个600G硬盘(1热备,3存储)。
数据库:
MicrosoftSQLServer20GG。
客户端:
使用Delphi集成开发环境开发编辑可执行EGE绿版文件。
应用操作系统:
Windows20GG\GP\WIN7\WIN8,不适用于Linus\Android\Mac操作系统。
2.3与其它系统关系/接口
与公司目前运行的ERP暂无设计接口,ERP属于清软平台开发产品,
考虑客户端衔接没有可能,只能通过ERP开放数据库接口,MES向ERP采集物料计划、采购订单、库存数据,同时硅片从MES产出入库接入ERP。
3.系统功能
3.1业务流程模块
3.1.1铸锭管理
3.1.1.1配料管理
实现功能:
根据原生硅料批次、重量及边皮料在线中间库数据(右侧表)及其它硅料创建硅锭配料单,一锭一单,单号由系统根据既定规则自动生成,目前是“年+月+日+当天配料流水号”,比如14011501,即14年1月15日配的第1埚料,配好的硅锭料单将在配料单明细表中显示。
实现功能:
对已配好的锭料单数据进行维护,包括:
查询、修改,删除,可双击左侧配料单表查看具体某一份配料单的配料明细(右侧表),当该埚料在后续补装炉后,配料单号表中会自动出现硅锭号,无硅锭号的说明尚未装炉,同时,可在右侧表中根据原生硅料批次号、投用边皮料锭号和硅料类型追溯到使用的所有硅锭。
实现功能:
根据已知硅锭号循环追溯投入边皮料的锭号,追溯层级为向前追溯30次,上图中我们设定的目标硅锭号是HMP14012506,查询到投用的边皮料锭号是HMP14012803,而投用至HMP14012803边皮料锭号是HMP13122511,以此向前类推,右侧可显示对应硅锭的电性能(电阻率、少子寿命)变化趋势(自动关联集成后道工序检测结果)。
另外,双击表中任一硅锭可查看历史配料明细清单(右侧表下)。
3.1.1.2铸锭运行管理
实现功能:
1、完成铸锭装炉工作:
根据配料单号(选择项,前面已创建),选择炉号及其它相关信息(班组、班次、使用工艺、时间等)进行装炉,系统会自动判断所选炉号是否被占用,若被占用则不能完成装炉工作。
2、铸锭在线运行监测:
在装炉时即计算出此次运行与本炉上次出锭间隔切换时间(便于监测铸锭炉运行效率),同时,自动更新运行时间,与实现铸锭炉运行进度保持一致,铸锭完成后勾选出炉即可。
3、如装炉数据有误,允许具有高级管理权限的用户返回装炉前状态进行修改。
4、铸锭运行过程中发生的相关情况填入对应硅锭表项中。
3.1.1.3出锭管理
实现功能:
1、完成铸锭后转铸锭在线库存,并开始自动计算冷锭时间,质量部授权专员对锭等级进行判定。
2、当下道工序开方领锭后,铸锭在线库存被领的锭会自动去除。
3、出锭管理表中记录在线库存锭的相关数据。
3.1.1.4铸锭数据管理
实现功能:
记录所有铸锭历史数据,并设定按条件查询(硅锭号、锭等级、铸锭工艺、锭状态-自动关联锭后期运行状态),及双条件高级查询(所有锭相关信息均可作为查询关索引键字)。
3.1.2开方管理
实现功能:
1、根据铸锭在线库存选择已达到冷锭期标准的硅锭进行开方(点击选择红色按纽会弹出选锭表,其中冷锭时间是自动计算的),选择开锭规则(锭至块编号规则,在系统条件设置中确定),完成后会自动生成25个硅块进入下道工序,开方后的硅锭会出现在已开方表中(下表)。
2、支持对误操作导致的数据错误进行修改(特定授权专员)。
3.1.3机加管理
3.1.3.1机加一次检测
实现功能:
对开方后的25个硅块进行一次检测,确定少子寿命、电阻率、划出一次有效长度,根据检测结果,判定工序转移路径(进入机加工、报废处理或集中待处理),记录人员及处理意见数据。
同时,对于外发或委外加工退回的硅块也从一次检测添加硅块进入处理流程。
3.1.3.2机加二次检测
实现功能:
完成一次检测后经过带锯、倒角、平磨加工的硅块进入机加二次检测工序,系统会自动引入相应硅块的一次检测结果,同时,在此检测员将二次检测数据在线实时录入系统(包括:
机加设备、操作员、加工尺寸数据及各种加工异常等),完成后根据二次检测结果确定硅块流转路径(在线合格库,报废处理或二次集中待处理)。
3.1.3.3在线合格库
实现功能:
经过机加二次检测的合格硅块转入在线合格库,在此集中了硅块所有相关信息(硅块本身的电性能、效率类型、尺寸、损耗值、人员、设备及加工异常数据等),如果要选择外发,则可以从这选择需发出的硅块,被选中的硅块会进入硅块发货管理流程,转切片工序的无需发出,通过在切片工序中配棒领料功能实现硅块向切片工序的转移。
3.1.3.4硅块外发管理
实现功能:
当在硅块合格库中选择外发后,相应硅块会进入发出管理模块,在外发管理表中,分别按客户和发出时间可查询对应硅块发出明细,系统会自动汇总统计被选中硅块的总量数据(总数量、总重量、总异常长度和重量等)。
3.1.3.5回收硅料管理
实现功能:
机加车间加工硅块附属的边皮头尾料及因质量异常导致报废的硅块或其它零星硅料,通过回收料管理子模块向硅料清洗工序转移并统计数据,实现三种管理方式:
1、按锭归集的边皮头尾料,专锭专料管理并跟踪,2、报废硅块按块记录跟踪,3、零星报废硅料按日汇总记录跟踪。
3.1.4硅料清洗管理
实现功能:
按锭归集边皮料清洗和不按锭归集混合料清洗,完成后发至铸锭车间边皮料在线库存。
3.1.5切片清洗分选管理
3.1.5.1配棒管理
实现功能:
1、自动配棒:
根据表1左侧硅块实时动态中间库存,满足用户设置条件的单棒最长组合配棒,实现条件需要硅块合格库现场存放硅块尽量细分,便于根据配棒清单及时找到对应硅块。
2、手动配棒:
由切片配棒人员先到现场根据选择硅块组合配棒,完成后将数据在手配表中查询到硅块数据并生成配棒清单。
3、配棒编辑:
确认已配棒数据并正式提交配棒领用申请(可打印领用硅块表单)。
3.1.5.2领棒管理
实现功能:
由机加核算员根据切片提交的配棒需求申请,确认对应硅块信息,并确认发出硅块转移至切片车间。
3.1.5.3粘棒管理
实现功能:
将已配好的硅棒按用户要求进行组刀(切片前先将各个硅棒按每两根棒一组合成一刀硅棒,单刀组棒数可人为设定),并产生粘胶中间刀组在线库,待切片。
3.1.5.4切片上棒管理
实现功能:
从组刀在线库选择对应刀组选择切片机上机运行,右侧表中显示在线运行的切片机台及切割相应数据,运行时间自动计算,与实际切片保持一致。
3.1.5.5切割记录管理
实现功能:
记录切片历史切割信息,并可根据各项定制条件查询。
3.1.5.6切片工艺管理
实现功能:
定制切片不同工艺参数,提供对不常用工艺的封装,便于切片人员选择当前工艺,切片出片数、砂、线、液单耗均根据所选切片工艺自动关联运算。
3.1.5.7清洗分选管理
实现功能:
根据已完成的切片信息,按刀或按块录入清洗、分选人、机、料数据,系统自动计算质量及汇总数据。
在分选生产管理模块中,可根据时间和不同选项查询切片数据,并追溯包装箱单号,以确保以后客户返回信息的追溯管理。
3.1.5.8块至片&刀至片流程数据整合
实现功能:
实时自动整合按块分布的切片产量、质量数据,按刀分布的产量、质量和砂、线、液单耗数据,同时包括所有人、机、料相关数据,完全支持用户导出数据,以进行各项需求的分析。
3.2业务管理模块
将硅片全生产链信息进行整合,实时输出各项生产管理指标,向生产
管理人员提供综合生产管理信息,利于及时掌握硅片各个工序生产运行状况,对控制生产提供必要信息支撑。
3.2.1生产计划模块
实现功能:
按月度编制硅片事业部生产计划,制定各项指标,包括铸锭、硅块、切片产量、质量、加工成本以及损耗等指标,编制的计划值将作为在综合管理模块中系统自动监测实际完成情况偏差的判定依据。
3.2.2产量管理模块
分别提供:
铸锭、开方、切片运行、硅片每日产量及月度累计完成数据,实时监测各工序实际完成情况与计划偏差,每项日报数据均支持查看具体明细。
3.2.3质量及过程管理模块
实现功能:
按日及月度累计汇总监测铸锭的质量等级,运算一级锭合格率及一、二级锭合格率,并可查看历史数据。
实现功能:
实时监测硅料一次利用率,并可按时间段查询,双击当日可查看明细。
实再功能:
按不同铸锭炉查看出炉的硅料利用率、少子寿命、平均电阻率综合表现情况,同时可根据单台铸锭炉查看历史数据。
实现功能:
根据锭等级综合监测不同等级的硅锭电性能表现情况,并可查看历史记录。
3.2.4锭块片集成管理模块
实现功能:
对锭-块-片实现全面实时集成,展示某锭直到硅片的所生产、质量及产出进程。
3.2.5在制品存货管理
实现功能:
实时统计在线硅块存量及可用合格块的按不同长度区分的数量及重量。
3.2.6铸锭投料监测管理
实现功能:
实时监控铸锭配料和出炉锭的使用原生硅料、回收硅料及提纯硅料的比重,提供管理者对投料方向的控制信息。
3.3系统管理模块
3.3.1系统运行条件及参数管理
实现功能:
分别可以定义:
硅锭等级标准、开方机台信息、开方班组信息、开方生成硅块编号规则,产品质量类型、在线库位设置及综合参数设置,所有参数将在流程管理运行过程中作为条件使用。
3.3.2操作日志管理
实现功能:
实时详细记录所有用户操作系统的内容和时间,便于在系统操作异常时侦查操作对象和原因。
3.3.3用户及密码管理
实现功能:
创建新用户、修改用户信息、设置权限,记录用户登录IP地址,登录次数等,用户设置的密码作为用户隐私不公开(本模块仅限拥有系统超级权限的管理员可操作)。
同时,提供让用户可任意修改原有登录密码的界面。
3.3.4内网在线信息沟通
实现功能:
1、在线用户显示,自动加载、卸载;
2、选择用户主动沟通;
3、接受未加入在线交通对象的呼叫接入和应答模式沟通;
4、当接受到信息时,沟通界面会主动弹出,以提醒用户。
5、仅适宜于内网沟通,主要以因工作业务及时通信为目标,可监管通讯内容;
(须在装入系统客户端文件时,解除类似360防火墙的阻止网络通信设置,防火墙软件会有提示让用户选择)。
4.实施应用效果
1、MES系统在硅片事业部已全面推广实施,并已成为生产车间和部门日常生产辅助管理工具。
2、MES系统充分集成从硅料至硅片生产的全过程数据,可以查询、监测生产运行状态及其各项生产指标完成状态。
3、实时性强,生产流程数据在线基本由当班班长导入,与实际生产业务流程基本同步,减少专门设置系统数据统计员的数量。
4、量身定制,系统功能冗余度小,适用性高,日常模块及软件界面用户使用率达95%以上。
5、软件交互性良好,非常便于支持批量数据导入和导出,操作性及与EGCEL表格兼容性强。
6、企业智能管家应用,在自动化数据分析和快速运算等功能方面实现良好,向管理者提供简明扼要的综合生产运行数据,便于管理人员进行及时、有效的生产管控,系统内数据透明度高。
7、系统延展性强,产权及技术完全自主,可往更深层管理需求功能的实现进行二次或多次开发,可塑性大,可挖掘的潜力空间巨大。
5.
结论
MES系统适用于硅片事业部生产过程管理,通过8个月左右的运行实践,实现了项目总体设计方案,达到项目目标,基本满足硅片生产实际管理运行的需求。