过程控制课程设计.docx
《过程控制课程设计.docx》由会员分享,可在线阅读,更多相关《过程控制课程设计.docx(17页珍藏版)》请在冰豆网上搜索。
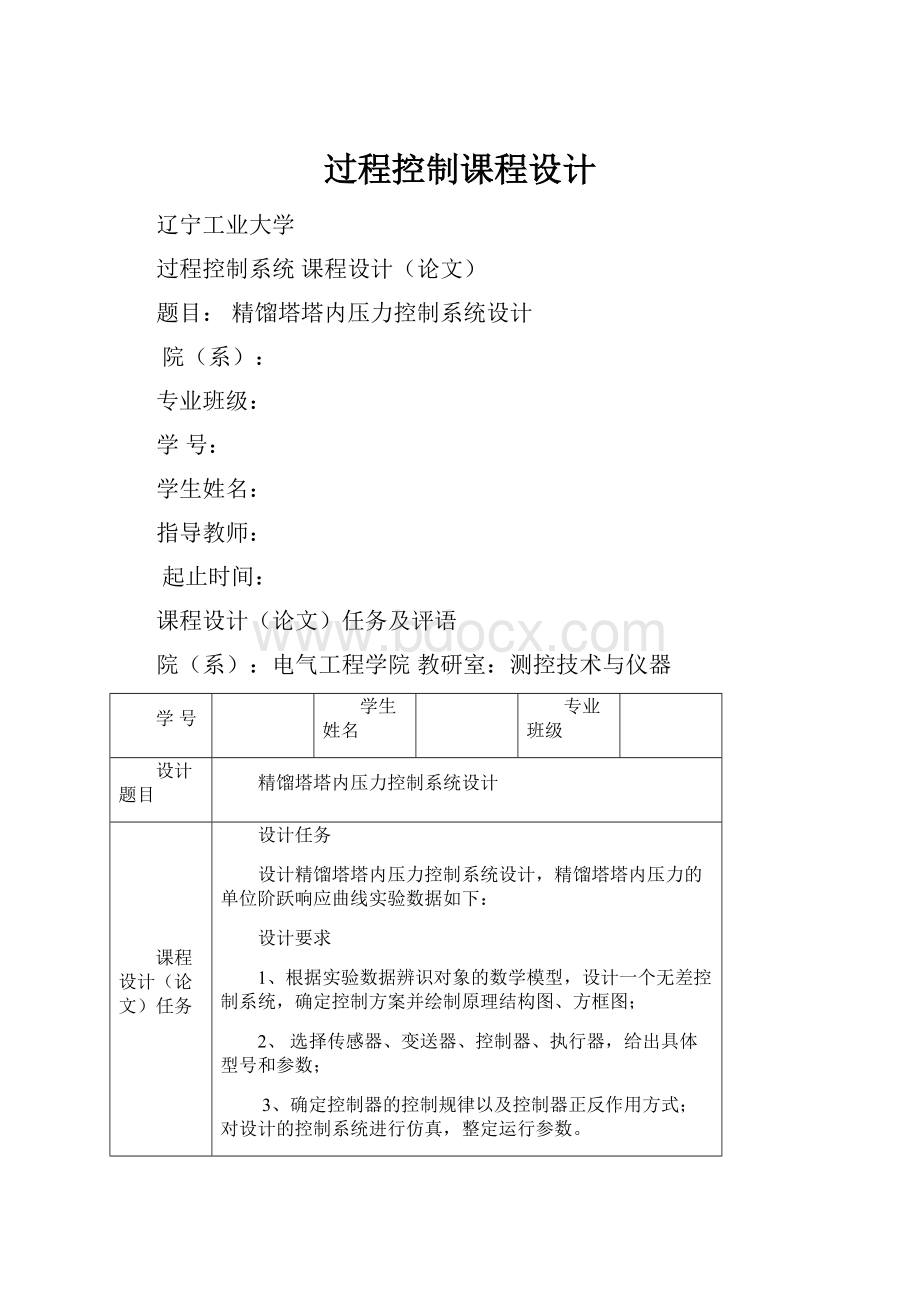
过程控制课程设计
辽宁工业大学
过程控制系统课程设计(论文)
题目:
精馏塔塔内压力控制系统设计
院(系):
专业班级:
学号:
学生姓名:
指导教师:
起止时间:
课程设计(论文)任务及评语
院(系):
电气工程学院教研室:
测控技术与仪器
学号
学生姓名
专业班级
设计题目
精馏塔塔内压力控制系统设计
课程设计(论文)任务
设计任务
设计精馏塔塔内压力控制系统设计,精馏塔塔内压力的单位阶跃响应曲线实验数据如下:
设计要求
1、根据实验数据辨识对象的数学模型,设计一个无差控制系统,确定控制方案并绘制原理结构图、方框图;
2、选择传感器、变送器、控制器、执行器,给出具体型号和参数;
3、确定控制器的控制规律以及控制器正反作用方式;对设计的控制系统进行仿真,整定运行参数。
4、若设计由数字控制系统实现应给出系统硬件电气连接图及程序流程图;
5、按规定的书写格式,撰写、打印设计说明书一份;设计说明书应在4000字以上。
技术参数
测量范围:
0-5大气压,控制压力:
1±大气压,超调量小于等于25%;
工作计划
1、布置任务,查阅资料,理解掌握系统的控制要求。
(2天)
2、确定系统的控制方案,绘制原理结构图、方框图。
(1天)
3、选择传感器、变送器、控制器、执行器,给出具体型号和参数。
(2天)
4、确定控制器的控制规律以及控制器正反作用方式(1天),调节阀的气开气关形式以及流量特性选择。
(1天)
5、上机实现系统的模拟运行或仿真、答辩。
(2天)
6、撰写、打印设计说明书(1天)
指导教师评语及成绩
平时:
论文质量:
答辩:
指导教师签字:
总成绩:
年月日
注:
成绩:
平时20%论文质量60%答辩20%以百分制计算
摘要
精馏塔是石油、化学加工工业(CPI)中使用量最大、能耗最高、应用面极广的分离单元操作设备。
本设计采用单回路控制系统对塔内压力进行实时控制,采用PID算法的DTZ—2100控制器对HK-613系列通用型压力变送器采集到的塔内压力值进行处理,并将控制信号传递给ZXS型新系列气动薄膜角形单座调节阀,令其对冷却量进行控制,从而达到对塔内压力的控制。
精馏塔的控制最终目标是:
在保证产品质量的前提下,使回收率最高,能耗最小,或使总收益最大生产设备自动化程度的提高,有利于降低工厂成本、促进生产线的柔性化和集成化,有利于提高产品的产量、质量以及产品的竞争力。
从某种意义上说,高效的精馏塔控制技术为我们创造了不可忽视的经济效益和社会效益。
关键词:
精馏塔;分离单元;PID算法
第1章绪论
研究背景及意义
精馏是化工、石油化工、炼油生产过程中应用极为广泛的传质传热过程。
而石油化工是基础性产业,它为农业、能源、交通、机械、电子、纺织、轻工、建筑、建材等工农业和人民日常生活提供配套和服务,在国民经济中占有举足轻重的地位,在现代生活中,几乎随时随地都离不开化工产品,从衣、食、住、行等物质生活到文化艺术、娱乐等精神生活,都需要化工产品为之服务。
精馏的目的是利用混合液中各组分具有不同挥发度,将各组分分离并达到规定的纯度要求。
精馏过程的实质是利用混合物中各组分具有不同的挥发度,即同一温度下各组分的蒸汽分压不同,使液相中轻组分转移到气相,气相中的重组分转移到液相,实现组分的分离。
1.精馏过程的核心在于回流,而回流必须消耗大量能量。
降低能耗是精馏过程发展的重大课题。
除了选择经济上合理的回流比外,主要的节能措施有:
热泵精馏。
将塔顶蒸气绝热压缩(见热力学过程)升温后,重新作为再沸器的热源(见热泵蒸发);
2.多效精馏:
精馏装置由压力依次降低的若干个精馏塔组成,前一精馏塔塔顶蒸气用作后一精馏塔再沸器的加热蒸气(见多效蒸发);
3.采用高效精馏塔,可用较小的回流比;采用高效换热器,可降低传热温度差,这样就可以减少有效能损失。
4.采用电子计算机对过程进行有效控制,减小操作裕度,确保过程在最低能耗下进行。
精馏操作分为连续精馏和间歇精馏,本设计的研究对象是连续精馏的过程。
其操作过程是:
原料液经预热加热到一定温度后,进入精馏塔中的进料板,料液在进料板上与自塔上部下降的回流液体汇合后,在逐板下流,最后流入塔底再沸器中,液体在逐板下降的同时,它与上升的蒸汽在每层塔板上相互接触,同时进行部分汽化和部分冷凝的质量和能量的传递过程。
操作时,连续从再沸器中取出的部分液体作为塔底产品,部分液体汽化产生上升蒸汽,从塔底回流入塔内出塔顶蒸汽进入冷凝器中被冷凝成液体,并将部分冷凝液用泵送回塔顶作为回流液体,其余部分经冷却器后被送出作为塔顶产品。
精馏塔是石油、化学加工工业(CPI)中使用量最大、能耗最高、应用面极广的分离单元操作设备。
从精馏设备的历史发展来看,精馏技术与石油、化学加工工业的发展是相辅相成、相互刺激、共同进步的发展关系。
精馏技术的任何进步,都会极大刺激化学加工工业的技术发展,同样在石油、化学加工工业发展的每一个历史阶段都会对精馏设备技术提出更高要求。
当前填料塔技术已经基本可以满足不远未来的需求,板式塔技术依然是未来发展的主流。
现有新型板式塔技术的发展主要是传统简单技术的深化和传统简单技术的复杂化,前者可以很好地满足现有生产局面对塔内件的要求,而后者将发展成未来板式塔的主流。
精馏塔是化工生产中分离互溶液体混合物的典型分离设备。
它是依据精馏原理对液体进行分离,即在一定压力下,利用互溶液体混合物各组分的沸点或饱和蒸汽压不同,使轻组份(即沸点较低或饱和蒸汽压较高的组分)汽化。
经多次部分液相汽化和部分气相冷凝,使气相中的轻组分和液相中的重组分浓度逐渐升高,从而实现分离的目的,满足化工连续化生产的需要。
精馏塔塔釜温度控制的稳定与否直接决定了精馏塔的分离质量和分离效果,控制精馏塔的塔釜温度是保证产品高效分离,进一步得到高纯度产品的重要手段。
维持正常的塔釜温度,可以避免轻组分流失,提高物料的回收率,也可减少残余物料的污染作用。
随着现代化工的飞速发展,生产规模的不断扩大,工艺过程越趋复杂,对工艺流程前后工序相互关联紧密,充分利用能源等提出的要求,精馏塔在工业过程控制领域发挥了越来越重要的作用,广泛应用于各种行业的生产过程中。
精馏塔的控制最终目标是:
在保证产品质量的前提下,使回收率最高,能耗最小,或使总收益最大生产设备自动化程度的提高,有利于降低工厂成本、促进生产线的柔性化和集成化,有利于提高产品的产量、质量以及产品的竞争力。
从某种意义上说,高效的精馏塔控制技术为我们创造了不可忽视的经济效益和社会效益。
当前发展状况
图精馏塔历史发展
阶段I:
(20~50年代):
1920年,有溢流的泡罩塔板开始应用于炼油工业,开创了一个新的炼油时代。
泡罩塔板对设计水平要求不高、对各类操作的适应能力强、对操作控制要求低等特性在当时被认为是无可替代的板型。
Rachig环填料塔主要应用于较小直径的无机分离塔设备中,同时也开发了Pall环,标志着现代乱堆填料的诞生。
阶段II:
(50~70年代)∶
消除放大效应的研究:
AIChE研究,浮阀塔板的开发,FRI的成立,系统化的设计方法:
1955年,Monsanto公司的Bolles发表了着名的“泡罩塔板设计手册”,首先提出了科学的、规范化塔板设计技术,该方法到目前为止仍然广泛流行,大孔筛板的研究。
阶段III:
(70~90年代):
大型液体分布器的基础研究,使得填料塔的放大研究成功,并在减压塔中应用获得极大的经济效益和社会效益,通过计算机对辅助精馏塔放大效应的研究,计算塔板效率和精馏过程设计,新型高性能浮阀塔板的开发及应用。
阶段IV(80末-至今)∶
新型高性能塔板的开发及工业应用,塔板设计、开发更趋于科学化的方向。
鉴于精馏塔塔设备在炼油和石化工业中的作用、重要地位和当今我国石化工业面临的形势,按照塔内件研究的历史发展规律,结合我国精馏塔塔设备操作现状和现有塔内件的技术水平,提出现阶段和未来的塔内件开发方向可以从三个主要方面拓展:
1.精馏塔塔内件实用技术是指针对当前的常规生产实际和特殊体系,以扩能、增效、降耗为目的,以实现“安、稳、长、满、优”为目标,在现有塔板新技术基础上进行的更优性能精馏塔塔内件开发和拓展,以使当前企业尽快摆脱困境,更好地适应即将面临的激烈国际石化市场的竞争。
2.精馏塔塔内件实用技术是未来生产发展赶超国外的必要准备之一。
过去我国精馏塔塔内件大多数是国外2O世纪50~70年代塔板技术的消化吸收、国产化和改进深化研究。
真正自主开发的塔内件技术极少。
为了适应未来国际石化市场的竞争,赶超国际水平,Sina—pac应该开展一些超前的高性能技术,例如CSI超大型处理能力塔板,形成自己的特色。
3.精馏设备是规模经济,精馏塔塔设备大型化已经受到重视。
尽管当前的原油减压塔已经实现9m塔径的超大型规模,但由于减压塔放大效应最低而采用常规技术放大的成功率较高。
对于常压、加压体系,超大型塔设备的建立必须先期进行超大型塔设备的应用基础研究。
精馏塔塔设备科学化设计是未来塔设备的发展方向,现有经验设计技术难以适应未来塔设备科学化设计的要求,因此需要开展科学化塔内件设计技术的技术储备。
第2章系统方案设计
概述
本设计为单回路控制系统。
通过压力传感器对精馏塔塔内压力进行实时测量,同时将对应的电信号传递给PID控制器进行处理,并由控制器输出控制信号控制执行器的阀门开度,实现对精馏塔塔内压力的动态控制。
对化工、石油化工、炼油生产的精馏具有重要作用。
本设计要求设计一个精馏塔塔内压力的无差控制系统,要求测量范围为0-5MPa,控制压力为:
1±大气压,超调量为小于等于25%。
系统对象特性分析
1.被控参数的选择
被控参数的选择是控制系统设计的核心问题。
直接关系到生产的稳定操作、产品产量和质量的提高以及生产安全与劳动条件的改善。
所以应尽量选择能直接反应控制目的的参数为被控参数。
根据生产工艺要求设计是控制精馏塔塔内压力的单回路控制系统,所以塔内压力为被控参数。
2.操纵变量的选择
被控参数确定之后,还需要选择一个合适的操作变量。
以便被控参数在外界干扰作用下发生变化时,能够通过对操纵变量的调整,使得被控参数迅速地返回到原来的给定值上,以保持产品质量的不变。
本设计是以进入精馏塔内的物料为操纵变量。
系统方案论证
压力是为建立塔稳定操作提供条件。
压力恒定阻止了气体积累。
对于一个连续系统,若不阻止积累就不可能取得稳态操作,也就不可能稳定。
压力是精馏塔操作的主要控制参数,压力除影响气体积累外,还影响冷凝、蒸发、温度、组成、相对挥发度等塔内发生的几乎所有过程。
精馏塔对压力的平衡要求很严格。
一旦压力大幅度波动,塔釜液位、回流液位紧跟着波动,进而影响到物料平衡、热量平衡、相平衡三大平衡,从而使整个操作系统处于不平稳状态,影响到产品质量及产量。
例如从提高产品质量来说,压力越高,沸点越接近,气液两相越难分离,显然降低压力可以提高产品质量。
但降低操作压力是以增加冷却介质的用量或降低冷却介质温度为前提的,因此降低操作压力是有限度的。
由此可见,压力控制对精馏塔的操纵有主导作用。
方案一:
采用分程控制:
首先通过改变冷却量来调节精馏塔塔内压力,而当冷却量达到最大后,如果塔内压力仍不能下降达到设定值,说明精馏塔内已含有过多的物料,光通过增大冷却量以无法完成控制,因此就要通过打开另一个阀门,通过排放物料的方法降低塔内压力。
控制方案示意图如图。
图方案一控制方案示意图
方案二:
采用单回路控制:
单回路控制系统又称简单控制系统,是指由一个控制对象、一个检测元件及变送器、一个调节器和一个执行器所构成的闭合系统。
单回路控制系统结构简单、易于分析设计,投资少、便于施工,并能满足一般生产过程的控制要求,因此在生产中得到广泛应用。
本设计是精馏塔塔内压力控制系统,精馏塔塔内压力是被控参数,塔内物料量是操纵变量,压力变送器将精馏塔内的压力值转换为电信号送入温度控制器中,控制器通过控制调节阀开度,调节进入塔内的冷却水流量,从而达到控制精馏塔内压力的目的。
由于与方案一相比,方案二在同样能达到控制要求的前提下,结构更简单、成本更低、更便于施工,因此最后选择方案二。
系统组成总体结构
设本系统为液相采出,流出物含微量不凝物,所以采用单回路控制系统,单回路控制系统结构简单、易于分析设计,投资少、便于施工,并能满足一般生产过程的控制要求,在生产中得到广泛应用。
单回路控制系统具有以下特点:
1.它由一个测量变送装置、一个控制器、一个控制阀和相应的被控对象所组成。
2.控制器是根据被控变量与给定值的偏差来进行控制的。
3.系统结构简单,所需自动化技术工具少(仪表少),投资比较低,操作维护也比较方便。
单回路控制系统是由一个控制对象、一个检测元件及变送器、一个调节器和一个执行器所构成的闭合系统,如图所示,x为设定值,y为输出的控制量。
图工艺流程图
图控制系统框图
第3章仪表选型
压力变送器选择
在工业生产过程中,为了正确指导生产操作、保证生产安全运行、提高产品质量和实现生产过程自动化,一项必不可少的工作是准确而及时地检测出生产过程中的各个有关参数,例如压力、流量、物位及温度等。
用来检测这些参数的技术工具称为检测仪表。
用来将这些参数转化为一定的便于传送的信号(例如电信号或气压信号)的仪表通常称为传感器。
当传感器的输出为单元组合仪表中规定的标准信号时,通常称为变送器。
而变送器对参数的测量则是过程控制中不可缺少的一个环节。
由于设计要求的控制变量为精馏塔塔内压力,并且规定了测量范围为0~5标准大气压,因此本设计选择HK-613系列通用型压力变送器,该变送器选用国际着名公司高精度,高稳定性压力传感器组件,经过高可靠性的放大电路及精密温度补偿,将被测介质的压力转换成4~20mADC、0~5VDC,0~10VDC及1~5VDC等标准电信号,高质量的传感器、精湛的封装技术以及完善的装配工艺确保了该产品的优异质量和最佳性能,并且该变送器适用于液压及气动控制系统。
实物图如图所示。
相关参数:
测量范围:
0~至0~250MPa
准确度:
级、级、级
介质温度-30~+85℃
环境温度-20~+85℃
储存温度-40~+90℃
图压力变送器实物图
执行器的选择
执行机构是自动控制系统中的一个重要组成部分。
它的作用是接受控制器送来的控制信号,改变被控介质的流量,从而将被控变量维持在所要求的数值上或一定的范围内。
执行器按其能源形式可分为气动、电动、液动三大类。
气动执行器用压缩空气作能源,其特点是结构简单、动作可靠、平稳、输出推力大、维修方便、放火防爆,而且价格较低,因此广泛地应用于化工、炼油等生产过程中。
它可以方便地与气动仪表配套使用。
气动执行器有时还配有的辅助装置,常用的有法盲、阀门定位器,阀门定位器的作用是利用反馈原理来改善执行器的性能,使执行器能按控制器的控制信号,实现准确定位。
考虑到一旦系统出现故障或进物料中断时,无控制信号输出,调节阀自动关闭,以免物料全部流走,因此本设计中执行器选用气开式调节阀。
根据设计的流量特性为液体,本设计采用ZXS型新系列气动薄膜角形单座调节阀。
ZXS型新系列气动薄膜角形单座调节阀采用顶导向结构,具有结构紧凑、重量轻、动作灵敏、阀容量大、流体通道呈S流线型、压降损失小、阀容量大、流量特性精确、拆装方便等优点。
可调范围大,固有可调比50,流量特性有直线和等百分比。
广泛应用于精确控制气体、液体等介质,特别适用于允许泄漏量小阀前事压差不大的高粘度,含有悬浮物和颗粒状物质流体的调节,可避免结焦、堵塞,便于自净与清洗的场合。
阀体口径范围DN20~200。
适用流体温度由-200℃~+560℃,并且执行机构采用多弹簧结构,高度及重量均减小30%。
控制器的选择
控制器是系统的大脑和指挥中心,是整个控制系统的核心所在,输入信号进
入控制器,并且按照控制器的控制规律进行计算,即进行信号处理,运算处理的结果作为输出信号控制执行机构的动作,完成指挥控制系统的任务。
根据设计的控制系统分析,当精馏塔储液槽液位上升、被控参数出现偏差时,应增加调节阀的开度,使液位下降,调节器LC应为“正作用”方式,才能在储液槽液位升高时,调节器LC输出信号增大,调节阀开度增大,物料流出量增加,液位下降。
在实际工业生产应用中,调节器是构成自动控制系统的核心仪表,它将来自变送器的测量信号VI与调节器的内给定或外给定信号VS进行比较,得到其偏差e,有e=VI-VS,然后调节器对该偏差信号按某一规律进行运算,输出调节信号控制执行机构的动作,以实现对被控变量如温度、液位、压力和流量等的自动控制作用。
调节器的分类方法很多,按使用的能源来分,有气动调节器和电动调节器;按结构形式分有基地式调节器、单元组合调节器和组装式调节器。
单元组合调节器有气动单元组合调节器和电动单元组合调节器。
共有I型、II型和III型调节器。
由于DDZ-III型调节器性能优越,易于与计算机联用。
因此,本设计的调节器选择使用PID算法的DDZ-III型调节器。
根据设计要求,本设计选用DTZ—2100为控制系统PID控制器,通过对被控值与给定值之差进行比例、微分、积分运算输出,并将输出的4~20mA直流信号送至执行机构,实现对工艺参数的自动调节。
输入信号:
1~
内给定信号:
1~
外给定信号:
4~
调节作用:
比例+积分+微分
比例带:
2~500%
积分时间:
~分或~25分
微分时间:
~10分(可切除)
输入、给定指示表:
指示范围:
0~100%,误差:
±1%
输出信号:
4~
负载电阻:
250~750Ω
最大工作电流:
约200mA
工作条件:
环境温度:
0~45℃相对湿度:
≤85%
工作振动:
频率≤25Hz全振幅≤
电源电压:
功耗:
6W
重量:
6kg
前馈信号:
1~4~(适用于前馈调节器)
前馈系数:
~(适用于前馈调节器)
刻度误差:
±%(适用于前馈调节器)
限制范围:
高限:
75~105%(适用于抗积分饱和调节器)
低限:
-5~25%(适用于抗积分饱和调节器)
刻度误差:
±%(适用于抗积分饱和调节器)
控制规律的选择
在工程实际中,应用最为广泛的调节器控制规律为比例、积分、微分控制,简称PID控制,又称PID调节。
PID控制器问世至今已有近70年历史,它以其结构简单、稳定性好、工作可靠、调整方便而成为工业控制的主要技术之一。
当被控对象的结构和参数不能完全掌握,或得不到精确的数学模型时,控制理论的其它技术难以采用时,系统控制器的结构和参数必须依靠经验和现场调试来确定,这时应用PID控制技术最为方便。
即当我们不完全了解一个系统和被控对象,或不能通过有效的测量手段来获得系统参数时,最适合用PID控制技术。
PID控制,实际中也有PI和PD控制。
PID控制器就是根据系统的误差,利用比例、积分、微分计算出控制量进行控制的。
由于本系统不存在有较大惯性组件(环节)或有滞后(delay)组件,计采用PI调节就可满足控制要求。
而积分控制中,控制器的输出与输入误差信号的积分成正比关系。
对一个自动控制系统,如果在进入稳态后存在稳态误差,则称这个控制系统是有稳态误差的或简称有差系统(SystemwithSteady-stateError)。
为了消除稳态误差,在控制器中必须引入“积分项”,所以本设计选择PI调节。
PI调节器的输入输出关系为
第4章系统仿真
控制系统参数计算
由下表的数据,采用两点法确定一阶滞后环节的T、τ的值,从而得到对应的传递函数。
表塔内压力实验数据
由于阶跃响应曲线的拐点不易找准,切线的方向也有较大的随意性,通过作图求得的T、τ值因人而异,误差较大。
所以采用两点计算法确定被控过程时间T与滞后时间τ。
两点计算法是利用阶跃响应
上两个点的数据计算T和τ。
为了计算方便,首先将
转换成无量纲形式
。
由于采用两点法计算传递函数,因此在作图中选取两个不同时刻
和
对应的
和
,其中
,由于两点法比较常用,因此可以根据经验选取
两点,代入上式可得
的值,之后将该值代入下式。
通过计算后,可得:
代入可得传递函数为:
控制系统matlab仿真
无干扰单回路控制系统图如图所示。
图单回路系统图
无干扰单回路PI算法控制系统仿真曲线图如图。
图仿真曲线图
加入微分环节后重新整定PID各环节参数得到单回路无干扰仿真曲线图如图所示。
图调整后曲线图
图加干扰后仿真图
如图所示,该图为在100s时加入干扰后的单回路控制系统图。
施加干扰后控制系统的仿真曲线图如图所示。
图施加干扰后曲线图
由图可知,该系统产生干扰后可以较快的进行修正,使系统重新稳定。
第5章课程设计总结
本次设计是采用过程控制的方法对精馏塔塔内压力进行控制,首先是控制方案的确定,由于单回路控制系统具有结构简单、易于分析设计,投资少、便于施工等优点,其中结构简单代表了系统比其它复杂控制系统更稳定,而成本减少则代表了不浪费,因此在满足生产过程需要的前提下,选择了单回路控制系统作为本次设计的控制系统;之后是对控制算法的确定,根据精馏塔的工作过程,以及确定的控制方案,采用PID控制器作为系统控制器,其具有结构简单、稳定性好、工作可靠、调整方便的优点,而这些优点恰恰是精馏塔控制所需要的;最后是对变送器、执行器的选择,根据设计要求和精馏塔的防爆安全要求,对各个仪器进行了选择,完成了硬件部分的设计。
然后,是对控制方案的仿真,只有通过仿真才能确定设计的正确性,本设计采用MATLAB中的Simulink功能,构建单回路控制系统,并对PID参数进行整定,根据曲线确定各参数,达到了预期的效果,完成了对精馏塔塔内压力的控制。
参考文献
[1]潘永湘,杨延西,赵跃.过程控制与自动化仪表.北京:
机械工业出版社,2007
[2]俞金寿,蒋慰孙.过程控制工程.北京:
电子工业出版社,2007
[3]王正林.过程控制与Simulink应用.北京:
电子工业出版社,2007
[4]关守平.计算机控制理论与设计.沈阳:
东北大学出版社,2011
[5]林德杰.过程控制仪表及控制系统.北京:
机械工业出版社,2009
[6]胡华.石油控制理论.杭州:
浙江大学,2008.