主生产计划有关数值的计算mps的编制过程信院作业上课讲义.docx
《主生产计划有关数值的计算mps的编制过程信院作业上课讲义.docx》由会员分享,可在线阅读,更多相关《主生产计划有关数值的计算mps的编制过程信院作业上课讲义.docx(14页珍藏版)》请在冰豆网上搜索。
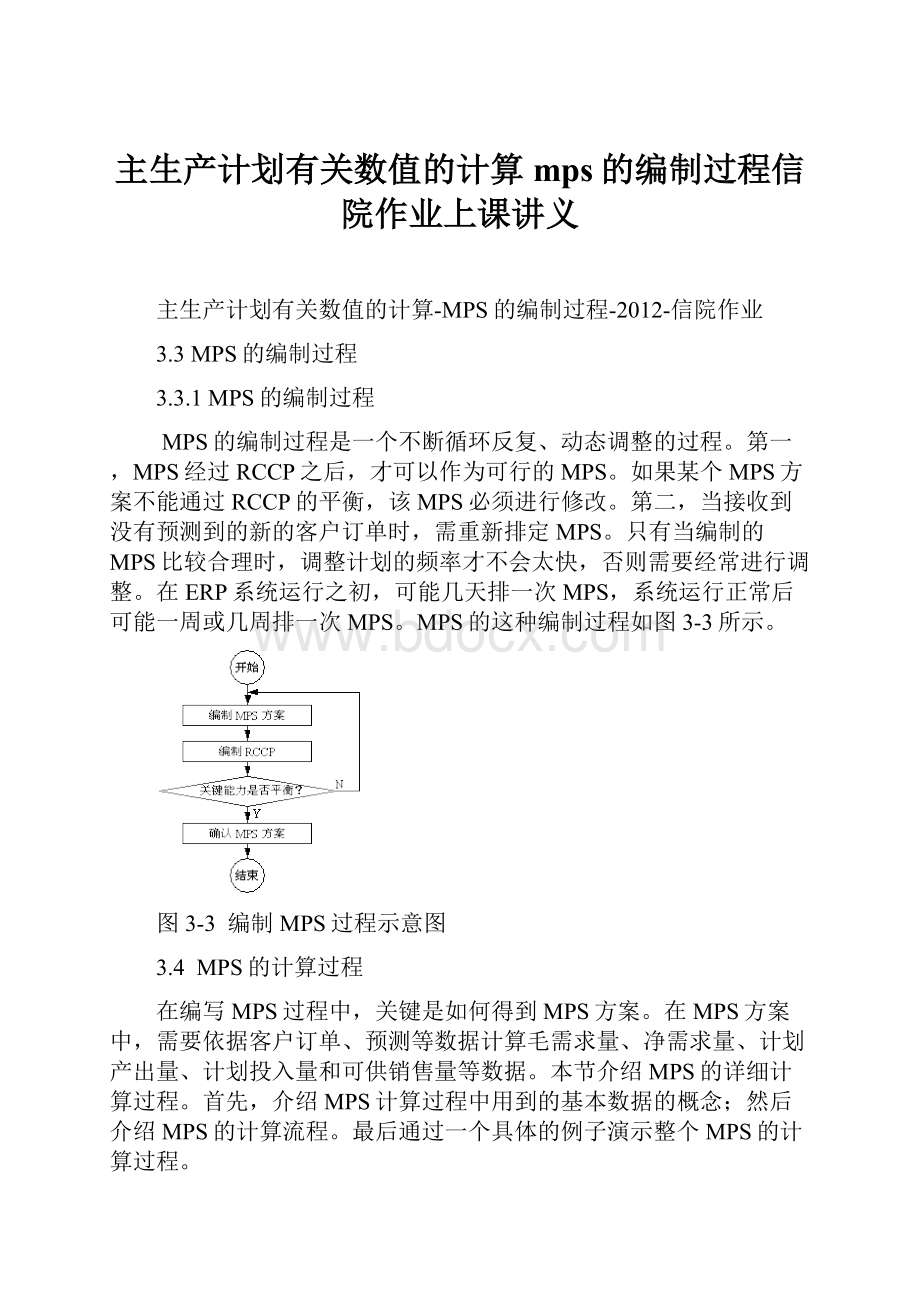
主生产计划有关数值的计算mps的编制过程信院作业上课讲义
主生产计划有关数值的计算-MPS的编制过程-2012-信院作业
3.3MPS的编制过程
3.3.1 MPS的编制过程
MPS的编制过程是一个不断循环反复、动态调整的过程。
第一,MPS经过RCCP之后,才可以作为可行的MPS。
如果某个MPS方案不能通过RCCP的平衡,该MPS必须进行修改。
第二,当接收到没有预测到的新的客户订单时,需重新排定MPS。
只有当编制的MPS比较合理时,调整计划的频率才不会太快,否则需要经常进行调整。
在ERP系统运行之初,可能几天排一次MPS,系统运行正常后可能一周或几周排一次MPS。
MPS的这种编制过程如图3-3所示。
图3-3 编制MPS过程示意图
3.4 MPS的计算过程
在编写MPS过程中,关键是如何得到MPS方案。
在MPS方案中,需要依据客户订单、预测等数据计算毛需求量、净需求量、计划产出量、计划投入量和可供销售量等数据。
本节介绍MPS的详细计算过程。
首先,介绍MPS计算过程中用到的基本数据的概念;然后介绍MPS的计算流程。
最后通过一个具体的例子演示整个MPS的计算过程。
3.4.1基本数量概念
在MPS计算过程中,经常用到9大基本数量的概念。
这些数量概念分别是:
预测量、订单量、毛需求量、计划接收量、预计可用库存量(PAB)、净需求量、计划产出量、计划投入量和可供销售量(ATP)。
预测量是企业生产计划部门根据企业的经营计划或销售计划,采用合适的预测方法预测的最终产品项目将要生产的数量。
订单量是企业已经明确得到的、将要为客户提供的最终产品的数量,是企业明确的生产目标。
预测量和订单量是企业组织生产管理活动的核心目标。
在不同类型的企业中,预测量和订单量所起的作用也不尽相同。
毛需求量(grossrequirement)是根据预测量和订单量计算得到的初步需求量。
可以根据表3-8的数据计算毛需求量。
毛需求量的计算与时区的确定、企业的生产政策有关。
在MPS中,毛需求量是除了预测量和订单量之外的其他量的计算基础。
计划接收量(scheduledreceipts)是指正在执行的订单量。
在制定MPS计划时,往往把制定计划日期之前的已经发出的、将要在本计划期内到达的订单数量作为计划接收量来处理。
如果希望手工修改MPS,也可以把手工添加的接收量作为计划接收量处理。
预计可用库存量(projectedavailablebalance,PAB)是指现有库存中扣除了预留给其他用途的已分配量之后,可以用于需求计算的那部分库存量。
PAB的计算公式如下:
PAB=前一时段末的PAB+本时段计划接收量-本时段毛需求量+本时段计划产出量
在PAB的计算公式中,如果前3项的计算结果是负值,表示如果不为库存补充,将会出现缺料。
因此需要借助第4项,即本时段计划产出量,用于库存的补充。
净需求量(netrequirement,NR)是根据毛需求量、安全库存量、本期计划产出量和期初结余计算得到的数量。
净需求量的计算公式如下:
净需求量=本时段毛需求量-前一时段末的PAB-本时段的计划接收量+安全库存量
计划产出量(plannedorderreceipts)是指在计算PAB时,如果出现负值,表示需求不能被满足,需要根据批量政策计算得到的供应数量。
计划产出量只是一个计算过程中的数据,并不是真正的计划投入数据。
计划投入量(plannedorderreleases)是根据计划产出量、提前期等数据计算得到的计划投入数量。
可供销售量(availabletopromise,ATP)是指销售部门可以销售的产品数量。
ATP的计算公式如下:
ATP=本时段计划产出量+本时段计划接收量-下一次出现计划产出量之前各时段订单量之和
3.4.2MPS的计算过程
MPS的详细计算过程如图3-4所示。
在该计算过程中,首先需要确定系统设置的内容。
系统设置包括整个MPS计算需要的数据环境。
例如,需要明确编制MPS的日期,划分时段、时区,确定需求时界、计划时界、生产批量、批量增量、安全库存量和提前期等。
图3-4 计算MPS过程示意图
系统设置之后,可以计算毛需求量。
计算毛需求量的基础数据是预测量和订单量。
如何根据预测量和订单量得到毛需求量,取决于企业的类型、时区和生产政策。
例如,可以制定这样的政策:
在时区1,毛需求量等于订单量;在时区2,毛需求量等于订单量和预测量中的较大者;在时区3,毛需求量等于预测量。
计算计划接收量需要确认在编制计划日期之前已经下达的订单数量。
在ERP系统中可以由系统自动确认。
计算当期PAB往往也是当前数据的一种确认。
当期PAB是指编制计划日期时可用的库存量。
接着逐个时段进行计算。
计算本时段PAB初值表示,在一个时段中,PAB有两个值,一个是PAB初值,一个是PAB值。
这是因为在计算PAB值时,如果计算结果是负值,需要借助计划产出量进行调整。
计算本时段的净需求量。
如果PAB初值大于或等于安全库存量,表示不需要补充,因此净需求量为0;如果PAB初值小于安全库存量,则需要补充库存,这时净需求量为安全库存量减去PAB初值。
如果净需求量为0,表示不需要补充物料,因此,PAB等于PAB初值。
如果净需求量不为0,则需要计算计划产出量。
计算计划产出量需要依据企业的批量政策。
计划产出量的计算公式如下:
计划产出量=N生产批量
N生产批量≥净需求量(N-1) 生产批量
N为大于或等于1的整数
计算计划产出量之后,需要计算PAB值。
这时,计算PAB值要考虑计划产出量的影响。
计算PAB值之后,需要判断计划期中的各个时段是否已全部计算完毕。
如果没有全部计算完毕,需要计算下一个时段的数据。
计划期循环完毕之后,可以计算计划投入量和可供销售量。
3.4.3一个MPS示例
本节通过一个具体的示例来介绍MPS的计算过程。
假设将要编写自行车ZXCA-F的MPS,编写MPS的日期是2006年6月1日,现有库存量为120,安全库存量为20,生产批量为160,批量增量为160,提前期是1个时段。
第一步,计算毛需求量。
在需求时区,毛需求量等于订单量。
在计划时区,毛需求量等于预测量和订单量中的较大值。
在预测时区,毛需求量等于预测量。
毛需求量的计算结果MPS横式报表所示。
MPS横式报表
时区
当期
需 求 时 区
计 划 时 区
预 测 时 区
时段
1
2
3
4
5
6
7
8
9
10
预测量
70
70
70
70
70
80
80
80
80
80
订单量
100
90
80
60
70
90
50
100
90
70
毛需求量
100
90
80
70
70
90
80
80
80
80
PAB初值
120
20
-70
10
100
30
-60
20
-60
20
-60
净需求量
90
10
80
80
80
计划产出量
160
160
160
160
160
PAB
20
90
170
100
30
100
20
100
20
100
计划投入量
160
160
160
160
160
ATP
20
70
-50
20
-30
90
第二步,计算第1时段数据。
PAB初值=上期末预计可用库存量+计划接收量-毛需求量
PAB初值=120+0-100=20=安全库存量
当PAB初值>=安全库存,净需求=0。
净需求量=0
计划产出量=0
PAB初值=上期末预计可用库存量+计划接收量-毛需求量
PAB=1200+0-100=20
ATP=本时段计划产出量+本时段计划接收量-下一次出现计划产出量之前各时段订单量之和
ATP=0+20-0=20160+
第三步,计算第2时段数据。
PAB初值=上期末预计可用库存量+计划接收量-毛需求量
PAB初值=20+0-90=-70<20
当PAB初值<安全库存,净需求=安全库存-PAB初值
净需求量=20-(-70)=90
计划产出量=1160=160
PAB初值=上期末预计可用库存量+计划接收量-毛需求量
PAB=20+160-90=90
ATP=本时段计划产出量+本时段计划接收量-下一次出现计划产出量之前各时段订单量之和
ATP=160+0-90=70
第四步,计算第3时段数据。
PAB初值=上期末预计可用库存量+计划接收量-毛需求量
PAB初值=-70+160-80=10<20
当PAB初值<安全库存,净需求=安全库存-PAB初值
净需求量=20-10=10
计划产出量=1160=160
PAB初值=上期末预计可用库存量+计划接收量-毛需求量
PAB=90+160-80=170
ATP=本时段计划产出量+本时段计划接收量-下一次出现计划产出量之前各时段订单量之和
ATP=160+0-80-60-70=-50
第五步,计算第4时段数据。
PAB初值=上期末预计可用库存量+计划接收量-毛需求量
PAB初值=10+160-70=100>20
当PAB初值>=安全库存,净需求=0。
计划产出量=0
PAB初值=上期末预计可用库存量+计划接收量-毛需求量
PAB=170+0-70=100
ATP=本时段计划产出量+本时段计划接收量-下一次出现计划产出量之前各时段订单量之和
ATP=0+0-0=0
第六步,计算第5时段数据。
PAB初值=上期末预计可用库存量+计划接收量-毛需求量
PAB初值=100+0-70=30>20
当PAB初值>=安全库存,净需求=0。
计划产出量=0
PAB初值=上期末预计可用库存量+计划接收量-毛需求量
PAB=100+0-70=30
ATP=本时段计划产出量+本时段计划接收量-下一次出现计划产出量之前各时段订单量之和
ATP=0+0-0=0
第七步,计算第6时段数据。
PAB初值=上期末预计可用库存量+计划接收量-毛需求量
PAB初值=30+0-90=-60<20
当PAB初值<安全库存,净需求=安全库存-PAB初值
净需求量=20-(-60)=80
计划产出量=1160=160
PAB初值=上期末预计可用库存量+计划接收量-毛需求量
PAB=30+160-90=100
ATP=本时段计划产出量+本时段计划接收量-下一次出现计划产出量之前各时段订单量之和
ATP=160+0-90-50=20
第八步,计算第7时段数据。
PAB初值=上期末预计可用库存量+计划接收量-毛需求量
PAB初值=-60+160-80=20=安全库存量
当PAB初值>=安全库存,净需求=0。
净需求量=0
计划产出量=0
PAB初值=上期末预计可用库存量+计划接收量-毛需求量
PAB=100+0-80=20
ATP=本时段计划产出量+本时段计划接收量-下一次出现计划产出量之前各时段订单量之和
ATP=0+0-0=0
第九步,计算第8时段数据。
PAB初值=上期末预计可用库存量+计划接收量-毛需求量
PAB初值=20+0-80=-60<20
当PAB初值<安全库存,净需求=安全库存-PAB初值
净需求量=20-(-60)=80
计划产出量=1160=160
PAB初值=上期末预计可用库存量+计划接收量-毛需求量
PAB=20+160-80=100
ATP=本时段计划产出量+本时段计划接收量-下一次出现计划产出量之前各时段订单量之和
ATP=160+0-100-90=-30
第十步,计算第9时段数据。
PAB初值=上期末预计可用库存量+计划接收量-毛需求量
PAB初值=-60+160-80=20=安全库存量
当PAB初值>=安全库存,净需求=0。
净需求量=0
计划产出量=0
PAB初值=上期末预计可用库存量+计划接收量-毛需求量
PAB=100+0-80=20
ATP=本时段计划产出量+本时段计划接收量-下一次出现计划产出量之前各时段订单量之和
ATP=0+0-0=0
第十一步,计算第10时段数据。
PAB初值=上期末预计可用库存量+计划接收量-毛需求量
PAB初值=20+0-80=-60<20
当PAB初值<安全库存,净需求=安全库存-PAB初值
净需求量=20-(-60)=80
计划产出量=1160=160
PAB初值=上期末预计可用库存量+计划接收量-毛需求量
PAB=20+160-80=100
ATP=本时段计划产出量+本时段计划接收量-下一次出现计划产出量之前各时段订单量之和
ATP=160+0-70=30
1.假设某车厂期初库存为200台,安全库存量为60台,生产批量为150台,提前期为1周,需求时界为2,计划时界为6,见表2-16。
试编制MPS计划报表。
要求:
按照前述讲述的MPS计算方法,把每一步的计算步骤都写出来,最后将计算结果数值填入表中。
表2-16
时区
需求时区
计划时区
预测时区
时段(周)
1
2
3
4
5
6
7
8
9
10
11
12
预测量
80
80
80
80
80
80
80
80
80
80
80
80
合同量
72
100
92
40
64
112
0
8
0
60
0
0
毛需求
PAB初值
净需求
计划产出量
预计PAB
2.答案:
时区
需求时区
计划时区
预测时区
时段
1
2
3
4
5
6
7
8
9
10
11
12
预测量
80
80
80
80
80
80
80
80
80
80
合同量
72
100
92
40
64
112
0
8
0
60
0
0
毛需求
72
100
92
80
80
112
80
80
80
80
80
80
PAB初值
128
28
86
6
76
-36
34
104
24
94
14
84
净需求
32
54
96
26
36
46
计划产出量
150
150
150
150
150
150
预计PAB
128
178
86
156
76
114
184
104
174
94
164
84
续表
2.某制造业企业PDM的实施过程如图所示,简述PDM成功实施的8个步骤。
制造业企业PDM的实施过程
一般说来实施不可能一蹴而就,比较合理的方式是分步、分阶段实施。
(1)确定PDM项目的范围和目标:
从企业级或全盘目标开始,越具体、越明确越好。
(2)搞清企业现状:
研究并评估企业的业务系统现状,即前面提到的三要素。
这一工作的完成会引进一些改进机会,即找到实施的切入点,这些切入点正如俗语所说:
“低处的水果”。
这样的“水果”可以是降低费用、节约工时、改进质量等。
(3)建立将要“做什么”的定义:
研究并取一致意见,决定公司将来如何运作,即决定PDM系统的管理结构。
(4)初定阶段移植计划:
这是一个计划或路线图,它将阶段性地表示如何把PDM系统的每个模块植入企业并最后使其协调工作。
(5)选定实施应遵循:
“低处的水果好摘”原则。
总之,应是最易入手、最快见效的一块试点。
(6)完成样板项目:
在试点上开发、试验、演示这个PDM样板,取得初步经验。
(7)完善并“成品化”这个试点:
总结完成样板过程中的经验教训,完善并扩充样板,使其具备完整的生产级的能力。
(8)完善“做什么”的定义和移植计划;在试点经验基础上,考虑对原来PDM目标和移植计划做相应调整与完善。
至此,可以考虑在其他试点上实施第(6)~(8)步,直到全部PDM系统实施完毕。