门铰链镀枪色镍工艺与设计终稿.docx
《门铰链镀枪色镍工艺与设计终稿.docx》由会员分享,可在线阅读,更多相关《门铰链镀枪色镍工艺与设计终稿.docx(42页珍藏版)》请在冰豆网上搜索。
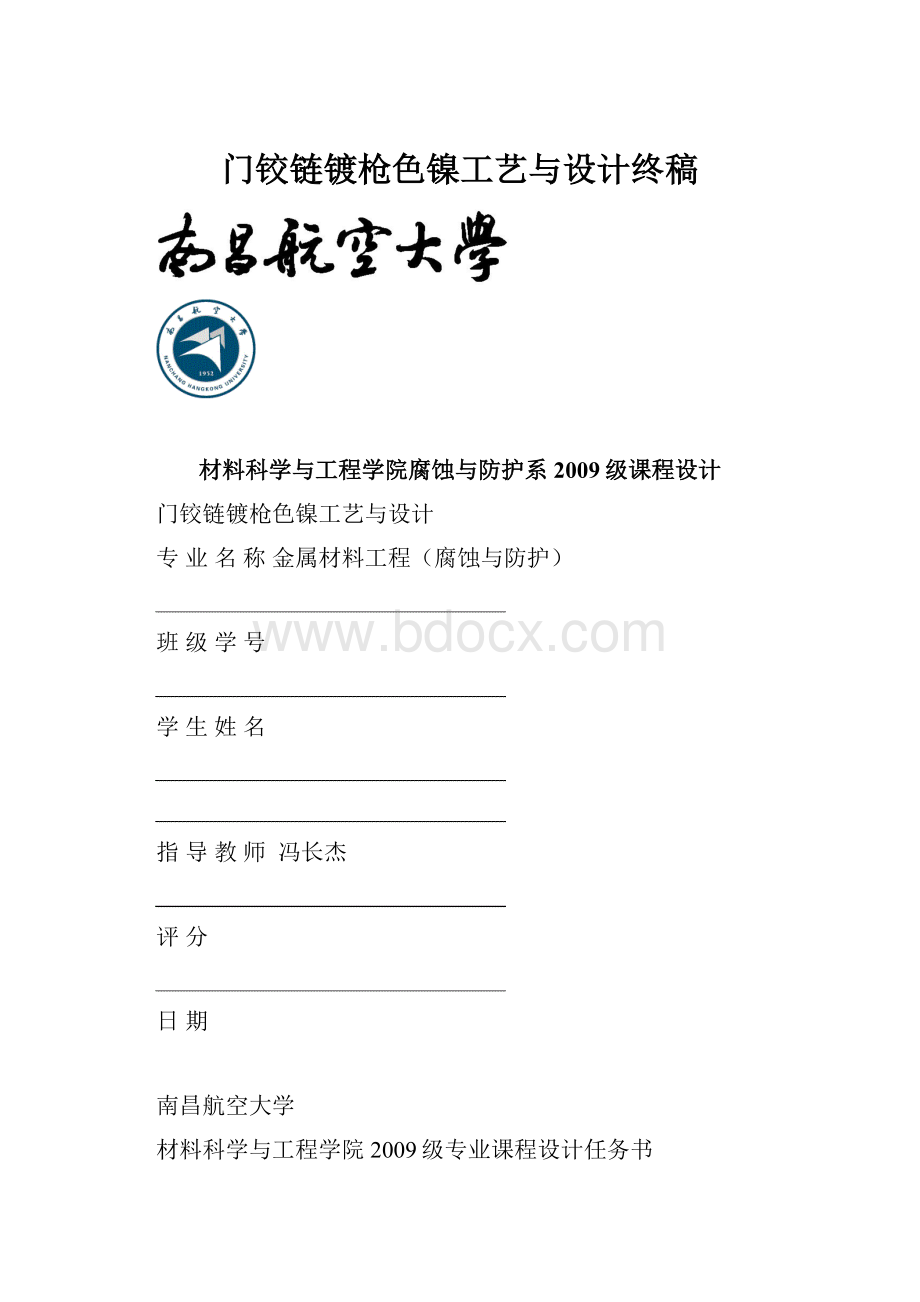
门铰链镀枪色镍工艺与设计终稿
材料科学与工程学院腐蚀与防护系2009级课程设计
门铰链镀枪色镍工艺与设计
专业名称金属材料工程(腐蚀与防护)
班级学号
学生姓名
指导教师冯长杰
评分
日期
南昌航空大学
材料科学与工程学院2009级专业课程设计任务书
I、专业课程设计题目:
门铰链镀枪色镍工艺与设计
II、专业课程设计任务及设计技术要求:
零件为低碳钢门铰链,对其进行预镀铜后,电镀枪色镍,年产量300万个,要求:
1.完成生产线设计说明书的编写;
2.完成工艺设计说明书的编写,并编写生产操作规程;
3.在A3纸上绘制零件挂具图。
III、专业课程设计进度:
1.2.5周查资料并完成以上设计工作内容
2.第4周周二上午交初稿,周五交正式稿
班腐蚀与防护系金属材料工程专业类
学生:
日期:
自2012.12.3至2012.12.31
指导教师:
冯长杰系主任:
刘光明
一生产线设计说明书
1前言
锡镍合金、电镀工艺之镀层含锡65%、镍35%、硬度达600VH以上,有良好耐磨性、防腐蚀性能极佳,色泽柔和、持久不变,有良好的覆盖能力,可得到色泽均匀一致的镀层,广泛用于首饰、汽车、钟表灯饰、五金工具等镀件。
但是因其与基体结合力较弱,应先预镀铜,再镀枪色镍。
2设计依据
(1)工件零件和材质:
门铰链、低碳钢
(2)表面积:
76.12×88.88-6×3.14×(0.688/2)2=6763.8mm2=67.64cm2
(3)检查零件→喷沙→上挂具→碱性化学除油→热水洗→冷水洗→酸浸蚀→冷水洗→预镀铜→冷水洗→镀光亮铜→冷水洗→活化→冷水洗→镀光亮镍→冷水洗→活化(H2SO45%)→冷水洗→镀枪色镍→冷水洗→热水洗→钝化→冷水洗→热水洗→烘干→下挂具→包装入库。
3车间任务和生产纲领
(1)车间任务
本车间负责对低碳钢制门铰链进行预镀铜再电镀枪色镍。
(2)生产纲领
年产量:
每年300万件。
考虑零件报废率,按5%计算,则实际年产量为315.8万件。
3工作制度和年时基数
(1)工作制度:
三班制生产,每班8小时
(2)工作天数:
251天(除去双休日)
(3)工人年时基数为全年时间和扣除病、产、事假及探亲等时间损失后的有效工作时间:
251×8×3-(251×8×3)×11%=5361h(11%为工人年时基数损失率)
(4)设备年时基数(两班制)为全年工作时间扣除设备检修及其他原因引起的停工时间:
251×8×3-(251×8×3)×4%=5783h(4%为设备年时基数损失率)
(5)年产量:
315.8万件
日产量:
3158000/251=12582件
每小时:
12582/(8×2)=525件
4生产节拍
t=FK×60/A
式中:
t—生产节拍时间(min/件)
F—设备年时基数(h)
K—设备利用系数(0.8~0.9)
A—年纲领(挂具/a)
t=5783×85%×60/3158000=0.093(min/件)
由于生产量较大,所以采用自动生产线进行生产。
5线速度
v=Ad/FK×60
式中:
v—输送机的计算速度(线速度)(m/min)
A—年纲领挂具数(挂/年)
d—挂钩之间的间距(mm)
F—设备年时基数(h)
K—设备利用系数(0.8~0.9)
每挂零件数取(48个)
v=(3158000/72)×60×10-3/(5783×85%)=0.535(m/min)
6主要工序时间计算
t=(60×ρ×d)/(c×Jk×ηk)(min)
式中:
t——电镀时间(min);
ρ——镀层金属密度(g/cm2);
d——镀层厚度(μm);
c——电化当量(g/A•h);
Jk——阴极电流密度(A/dm2);
ηk——阴极电流效率(%)。
已知镀层要求厚度为:
预镀铜2μm;枪色镍2μm。
根据公式以及镀层厚度要求计算得到主要工序的电镀时间为:
氰化镀预铜:
t=(60×8.9×2)/(1.186×2×95)=4.74min
镀枪色镍:
t=(60×8.9×2)/(1.095×2×95)=5.13min
镀枪色镍时间符合工艺要求的5-10分钟。
由计算可知,工艺流程中,时间最长的工序为5.13分钟,采用每10分钟电镀一批零件,一小时电镀六批,每一批2挂,每挂48个零件。
6×2×48=576个>525个,所以可以完成任务。
7挂具的设计
挂具是固定零件,连接电极,使电流均匀地传递到零件上而进行电镀的工具。
因此合理地选用挂具对保证镀层质量、提高生产效率、降低劳动强度有重要意义。
设计挂具的基本原则是:
有足够的机械强度和良好的导电性能;零件与挂具要接触牢固,装卸方便;此外还要力求质量小、体积小、坚固耐用、装载量适当。
7.1挂具的尺寸设计
镀件的表面积:
一块镀件表面积为67.64cm2;
根据每挂生产48个零件和零件的最大装挂尺寸可以算出:
零件在长宽高方向的最大尺寸分别为:
88.88mm(按90mm计算)10.90mm(按11mm计算),76.12mm(按80mm计算)
挂具的长度:
L=7×90+30×7+2×45=930mm;
挂具的宽度:
K=2×11+100=122mm
挂具的高度:
H=5×80+5×40+100+80=780mm;
(此处尺寸为挂有零件时的整体尺寸)
7.2挂具的材料选择
挂具应选择资源丰富、成本较低、有足够的机械强度、导电性能好、不易腐蚀的材料。
常用的有钢、铜、黄铜、磷青铜、钛、不锈钢、铝及其合金等。
7.3挂具的结构
挂具的结构一般都由吊钩、提杆、主杆、支杆和挂钩五个部分组成。
7.3.1吊钩
吊钩是挂具与极棒的连接结构,电镀时由它传递电流到挂具和零件上,因此,必须采用导电性能好的材料制作,本车间采用黄铜。
吊钩和极棒应保持较大的接触面和良好的接触状态,以保证电流顺利通过。
7.3.2提杆、主杆和支杆
提杆:
位于主杆的上部并和主杆垂直,用焊接的方法与主杆相连接。
当挂具悬挂于镀槽时,提杆的位置应高出液面80mm左右。
主杆:
支撑整个挂具和所挂零件的质量,并通过主杆传递电流到各支杆和零件上。
主杆的材料一般选用φ6mm~φ8mm的黄铜棒。
支杆:
通常用焊接的方法固定在主杆上,工作时承受悬挂零件的质量,支杆的材料一般用φ4mm~φ6mm的黄铜棒。
7.3.3挂钩
挂钩在挂具上的分布密度要适当。
应使挂具上的零件绝大部分表面或重要表面能朝向阳极,并避免压叠现象。
本车间挂钩选用钢丝做挂钩。
一般中小型镀件之间间隔l5mm~30mm,杯状镀件的间隔一般为直径的1.5倍。
8镀槽种类的选择
1)热、冷水清洗槽
冷水清洗槽通常是由硬聚氯乙烯塑料板、聚丙烯硬板或碳钢板制成的,但酸浸蚀工序后的冷水槽因有酸液带入,宜采用硬聚氯乙烯塑料或其他耐酸材料制作。
热水清洗槽通常由钢槽体及蒸汽加热管组成,由于热水槽容易沉积水垢,设计时应把排水、溢水管径适当加大。
2)化学除油槽
化学除油槽由钢槽、蒸汽加热管及导电装置组成,溶液为碱性工作温度70~90℃。
3)酸浸蚀槽和酸性镀槽
由于浸蚀及抛光液使用硫酸,它的腐蚀性很强,必须要用耐腐蚀的材料制作槽体或衬里。
酸性槽采用小型的硬聚氯乙烯槽。
4)碱性镀槽(氰化镀铜)
碱性溶液对钢铁无腐蚀作用,氰化镀铜和本次镀枪色镍所选用工艺电镀液都是碱性。
可以直接用钢板做槽体,但为了不污染镀液,保持镀液的清洁,常用聚氯乙烯板衬里槽。
需加热的镀液要安装蒸汽加热管。
5)光亮镀铜槽
此槽根据溶液配方组成及工艺条件,为常温酸性镀槽,槽体可用聚氯乙烯塑料板。
6)镀镍槽
此槽根据溶液配方组成及工艺条件,可选用酸性镀槽,槽体可用聚氯乙烯塑料板,温度50±4℃。
7)钝化槽
钝化槽根据溶液配方组成及工艺条件,选用酸性镀槽,槽体采用聚氯乙烯塑料板,温度为室温。
9槽体尺寸及个数的确定
9.1中心槽的选择
由生产工艺可知中心槽为枪色镍电镀槽。
9.2中心槽的尺寸计算
中心槽长度公式为L=nL1+(n-1)L2+2L3
式中L—槽子的长度(mm)
n—沿槽长方向的挂具数
L1—沿槽长方向挂具的宽度
L2—沿槽长方向挂具间的距离(30mm~100mm)
L3—挂具边缘至槽壁的距离(80mm~100mm)
如果再采用阴极移动,再加阴极移动的行程40mm~140mm
n=2L1=930mmL2=30mmL3=80mm
根据公式得到L=2090mm
中心槽宽度公式为b=nk×b1+2nk×b2+(nk+1)δ+2b3
式中b—槽子宽度(mm)
nk—挂具或阴极列数
b1—沿槽宽方向的挂具宽度(mm)
b2—挂具边缘至阳极表面的距离(150mm~250mm)
b3—阳极背面至槽壁的距离(30mm~50mm)
δ—阳极或阳极篮的厚度(mm)
nk=1b1=122mmb2=200mmb3=40mmδ=10mm
根据公式得b=1×122+2×1×200+(1+1)×10+2×40=622mm
中心槽高度公式为h=h1+h2+h3+h4
式中h—槽子高度(mm)
h1—挂具工作部位的高度(mm)
h2—挂具下端距槽底的高度(100mm~200mm)
h3—挂具上端距液面的高度(80mm~150mm)
h4—液面至槽沿的距离(100mm~150mm)
根据公式得到h=780+100+100+120=1100mm
9.3镀槽尺寸及个数的确定
镀枪色镍槽尺寸的确定:
根据年产量要求及工作制度确定等知道每槽应能镀72件,由于零件的性质确定每挂放36个零件,所以一槽要能容纳2挂,由此可确定槽子尺寸见表9.3。
9.3槽体尺寸
槽体名称
尺寸
个数
冷水槽
热水槽
浸蚀槽
化学除油槽
预镀铜槽
镀亮铜槽
镀亮镍槽
活化槽
镀枪色槽
钝化槽
浸涂槽
2100×800×1100
2100×800×1100
2100×800×1100
2100×800×1100
2100×800×1100
2100×800×1100
2100×800×1100
2100×800×1100
2100×800×1100
2100×800×1100
2100×800×1100
8
3
1
1
1
1
1
2
1
1
1
10材料动力(水、电、蒸汽、压缩空气等)消耗
10.1水耗量的计算
10.1.1给水的要求
工艺用水,包括配制镀液、调整槽液及溶液蒸发补充水,水质要求较高,有时应用去离子水(纯水)。
清洗零件用水,可用自来水和质量较好的井水。
设备冷却用水,可用井水或净化回收的水。
10.1.2排水
根据废水的特征按质分流排水、便于回收或单独处理。
不进行回收和单独处理的,可混合排放。
应注意节约用水,自动线上浸、淋、漂、喷洗尽量采用逆流清洗方法;设备冷却水或加热用水尽量回用。
10.1.3生产用水量的计算
1)清洗槽用水量的计算
小时用水量和最大小时用量可按下面简单方法计算:
小时用水量=槽体有效容积×小时换水次数(m3/h)
最大小时用水量=槽体有效容积×(小时换水次数+1)(m3/h)。
即冷水槽小时用水量=1050×10-3×1=1.05m3/h
最大小时用水量=1050×10-3×(1+1)=2.1m3/h
平均小时用水量=(1×2.1+7×1.05)/8=1.18m3/h
热水槽小时用水量=1050×10-3×0.5=0.525m3/h
最大小时用水量=1050×10-3×(0.5+1)=1.575m3/h
平均小时用水量=(1×1.575+7×0.525)/8=0.656m3/h
2)车间用水总量计算
水量的总消耗量按下式计算:
Qavg=Q1K1(m3/h)
Qmax=Q2K2(m3/h)
式中Qavg——车间小时用水平均总量(m3/h);
Qmax——车间小时用水最大总量(m3/h);
Q1,Q2分别为各用水设备的小时用水平均之和及最大量之和(m3/h);
K1——设备同时使用系数,采用0.7~0.9
K2——设备同时换水系数,采用0.8~0.9
Qavg=1.18×5+0.656=6.556(m3/h)
Qmax=2.1×5+1.575=12.075(m3/h)
10.2电的消耗
车间除照明用电和设备动力用电外,还有电加热装置用电。
照明用电按车间各工作间照明的最低照度估算。
标准设备用电量,按产品说明书表明的电容量计算,非标准设备按设备设计图纸上表明的电容量计算。
电加热装置用电,可根据热量计算结果换算。
电镀车间所用的直流电源大部分属于低压电源设备。
常用的直流发电机组、硅整流器及可控硅整流器等。
直流发电机组能供给稳定的直流电流,过载能力比整流装置大,输出电压稳定,电流波形平直,输出功率大;但由于直流电机组需要安装在单独的电源室,造成直流输电线路较长,线路上电量消耗较大,所以效率较低。
硅整流装置比直流发电机组轻便灵活,而且可以采用不同的线路和结构得到几种波形的直流电源,以满足不同镀种的要求。
防腐型硅整流装置可以放在镀槽槽边,便于采用单机单槽供电,直流输出线路短,损耗小,效率较高,但其过载能力差。
可控硅整流装置的体积比硅整流装置小,调压也比较方便,便于自动远距离调压。
1)额定电压
选用整流器的额定电压,切勿过高。
应略高于槽端最高电压与线路压降之和。
否则整流器效率不高,浪费电力。
2)额定电流
整流器的额定电流,应稍大于镀槽最大负荷时所需的电流。
如在产品系列中未能找到额定电流和电压都合适的产品,只能选较高额定电压的产品,而使额定电流应有相应余量。
否则对可控硅整流器元件会由于过载发热而损坏。
3)电流波形
可控硅整流器的电流波形随电压的调节而变化。
目前,生产量较大的镀锌、光亮铜、光亮镍、电解除油等都采用单相全波可控硅整流器,该设备用于焦磷酸盐镀铜,效果也很好。
10.3蒸汽消耗
10.3.1加热过程蒸汽消耗量计算
Q=[V·ρ·c·﹙t2-t1﹚/t﹢V·q]β
所用蒸汽量为:
G=Q/γ(kg/h)
式中Q——镀液升温所需要的热量(4.168kJ/h)
V——槽液容积(L)
ρ——溶液密度(kg/L)
c——溶液比热容(4.168kJ/kg·℃),(水及水溶液ρc=1)
t1——镀液初始温度(室温)
t2——镀液工作温度(℃)
q——单位体积水溶液加热过程中平均消耗量(4.168kJ/L·h)
t——升温时间(h)
β——热量损失系数,槽子有保温层时β=1.1~1.15,无保温层时β=1.15~1.3。
G——蒸汽消耗量(kg/h)
Q——镀液加热或热水槽工作时所需的热量(kJ/h)
γ——蒸汽的潜热,
当电镀车间蒸汽压力p=0.3MPa时,γ=2164kJ/kg
p=0.2MPa时,γ=2135kJ/kg
化学除油:
Q=[1050×(80-25)/1.5+1050×10.5]×1.15=56953.75kJ/h
G=56953.75/2164=28.32kg/h
热水槽Q=[1050×(80-25)/1.5+1050×10.5]×1.15=56953.75kJ/h
G=56953.75/2164=28.32kg/h
酸浸蚀:
Q=[1050×(60-25)/1.5+1050×5.5]×1.15=34816.25kJ/h
G=34816.25/2164=16.09kg/h
氰化镀铜:
Q=[1050×(30-25)/1.5+1050×1]×1.15=5232.5kJ/h
G=5232.5/2164=2.42kg/h
镀光亮镍:
Q=[1050×(55-25)/1.5+1050×4.5]×1.15=25725kJ/h
G=25725/2164=11.89kg/h
总蒸汽消耗量:
G=28.32+28.32+16.09+2.42+11.89=87.04kg/h
10.3.2保温时蒸汽消耗量计算
Q1=V·q1+Wc1(t2-t1)β(kJ/h)
G1=Q1/γ(kg/h)
式中Q1——溶液槽保温时的耗热量;
G1——溶液槽保温时的蒸汽消耗量;
q1——单位体积溶液及水保温时耗热量;
W——单位时间内放进槽内的零件质量(kg/h);
c1——零件的比热容;
t1——放进槽内之前零件的温度;
t2——槽子工作温度;
β——加热损失系数。
化学除油:
Q1=1050×10.5+31.968×0.115(80-25)×1.2=11267.64kJ/h
G1=11267.64/2164=5.21kg/h
热水槽:
Q1=1050×10.5﹢31.986×0.115(80-25)×1.2=11267.64kJ/h
G1=11267.64/2164=5.21kg/h
酸浸蚀:
Q1=1050×5.5﹢31.986×0.115(60-25)×1.2=5929.49kJ/h
G1=5929.49/2164=2.74kg/h
氰化镀铜:
Q1=1050×1﹢31.986×0.115(30-25)×1.2=1072.07kJ/h
G1=1072.07/2164=0.495kg/h
镀枪色镍:
Q1=1050×4.5﹢31.986×0.115(55-25)×1.2=4857.42kJ/h
G1=4857.42/2164=2.25kg/h
总蒸汽消耗量:
G1=5.21+5.21+2.74+0.495+2.25=15.905kg/h
(3)蒸汽消耗总量
Gevg=G1K1;
Gmax=G2K2
Gevg,Gmax——分别为车间蒸汽平均及最大总消耗量(kg/h);
G1,G2——各用蒸汽设备的平均及最大消耗量之和(kg/h);
K1——设备使用系数,采用0.7~0.9;
K2——设备同时加热系数,采用0.8~1.0。
Gevg=21.82×0.8=12.729kg/h
Gmax=87.04×0.9=78.336kg/h
11主要工艺设备的采用及计算
11.1可控硅整流器
选择依据:
一槽一次镀零件72个,每个零件表面积为0.68dm2,电镀总电流密度为:
(1.5~3)×0.68×96=97.92~195.84A。
选用规格为500A、12V的整流器。
生产量较大的电解除油生产线都用单相全波可控硅整流器。
11.2蒸汽加热管
电镀车间蒸汽压一般为0.2~0.3Mpa,用聚四氟乙烯塑料做加热管在我国已经成熟,本车间也采用,蒸汽压选0.3Mpa。
因槽体较大,加热量大,选择蒸汽加热较好。
蒸汽加热所需的传热面积为S:
S=Q/k∆t
S——加热管所需的传热面积(m2)
Q——镀液升温或热水槽工作时所需的热量(kJ/h)
K——加热管的传热系数(kJ/h·m2·℃),对聚四氟乙烯塑料,加热水溶液时为1000~1460这里取1200。
∆t—饱和蒸汽温度与溶液平均温度差(℃);∆t=tz―(t1+t2)/2
tz——在指定表压下的饱和蒸汽温度:
当表压为p=0,2Mpa时,tz=132℃;
当表压为p=0.3Mpa时,tx=142℃;
S=56953.75/1200×89.5=0.53(m2).
12车间组成、面积和人员
12.1车间组成
电镀车间按工作性质和设备布置分为生产部分和辅助部分。
生产部分包括喷砂、磨光、酸洗、除油、电镀以及其他表面处理、检验等。
辅助部分包括电源、电工、通风、维修、分析、挂具制造、化学药品库、零件库和成品库。
12.2车间的区划、厂房形式
大型电镀车间宜采用钢筋混凝土结构并涂覆耐腐蚀涂料;小型电镀车间可以用廉价的砖木结构,木材涂漆。
1)跨度(厂房宽度)
跨度常为(9、12、15、18、21、24、36、48……)M,即厂房跨度18M以上时,采用3M的倍数。
根据工艺设计的要求选择。
厂房的柱距为4或6M,视砖石结构或钢结构而定。
2)高度
跨度较大(12M以上)的大、中型电镀车间的高度(屋架下弦),一般不应低于7M,同时还应设置天窗;跨度较小的小型车间的高度可酌情降低,但不宜低于5M。
辅助间和生活间的净高,可以根据不同的情况予以确定。
一般采用3-3.5M。
3) 地面、墙裙
地面:
表面处理车间,地面应具有较好的综合性能,能适应酸碱交替、耐热耐油、耐水防滑、耐压抗冲等要求。
地面结构复杂,一般由面层、隔离层、找平层、垫层及地基组成。
墙裙(即腰墙):
电镀、酸洗车间腐蚀严重;涂装车间墙壁容易被污染,一般都设有墙群。
墙群高度一般取1200-1500mm。
4)门、窗
门的宽度在(800-1000)mm(单扇门)、1200mm、1500mm、1800mm、2100mm(1200+300n)(双扇门);
门的高度自2100mm开始,即(2100+300n)mm;窗的宽、高尺寸都以300mm为模数。
12.3车间面积
车间各部分面积见表3.3
表3.3面积分部
部门名称
工艺名称
面积(m2)
备注
生产部门
钳工间
22
电镀生产区
298
小计
320
生产辅助部门
分析间
34
材料间
22
零件库
34
小计
90
生活办公部门
生活区
22
小计
22
车间总面积
432
12.4工作人员组成
1)生产工人
可按工作岗位配备,生产工人人数为30人;
2)辅助工人
一般为生产工人的30%~50%,即12人;
3)检验人员
一般为生产工人的4%~5%,即1人;
4)行政管理人员及工程技术人员
一般为生产工人的18%~20%,即6人;
5)勤杂人员
一般为工人总数的2%~3%,即1人;
考虑到替换、请假的额外的缺勤情况,所以要加上20%的替补人员。
所以车间总人数为:
50×(1+20%)=60人。
13安全卫生及三废处理
13.1电镀废水
电镀废水或废液是电镀行业环境污染的重要方面,其废水不仅含污染物的种类不同,而且主要污染物的溶度、其他金属杂质离子的浓度以及溶液介质也都往往有较大差异。
电镀废水主要来源于:
镀前工件表面除油和酸洗后的清水洗;镀后零件的冷、热水清洗水;定期更换与过滤镀液时排出的废液;车间地坪的冲洗废水等。
13.2废水处理方法
1)化学法
化学还原法:
主要用于含铬废水的处理。
最常用的方法是亚硫酸法。
电化学腐蚀法:
主要利用微电池的腐蚀原理,采用铁屑处理电镀含铬废水。
铁氧体法:
应用于多种金属离子电镀混合废水的处理,采用铁氧体法处理电镀废水一般有三个过程,即还原反应、共沉积和生成铁氧体。
碱性氯化法:
采用氯系氧化剂将氰化物氧化破坏而去除的方法,适用于含氰废水的处理。
2)物理化学法
离子交换法:
既可以净化废水,又可回收利用废水中的有害成分。
活性炭吸附法:
主要用于含铬、含氰废水。
3)物理法
晶析法:
主要利用盐类物质在其过饱和溶液中可以析出较纯的结晶盐这一特征,使一些金属盐以晶体的形式得以回收,一般用于氰化镀锌和镀镍液等电镀液的回收处理。
膜分离法:
包括液膜分离法和采用固膜分离的反渗透法。
主要用于镀镍漂洗水的回收处理,与镀铜、镀锌等漂洗液的处理。
13.3电镀废气
废气主要来源于电镀车间前处理过程产生的酸、碱废气;以及电镀前工