薄板轧制过程中检测与质量控制技术及新发展.docx
《薄板轧制过程中检测与质量控制技术及新发展.docx》由会员分享,可在线阅读,更多相关《薄板轧制过程中检测与质量控制技术及新发展.docx(11页珍藏版)》请在冰豆网上搜索。
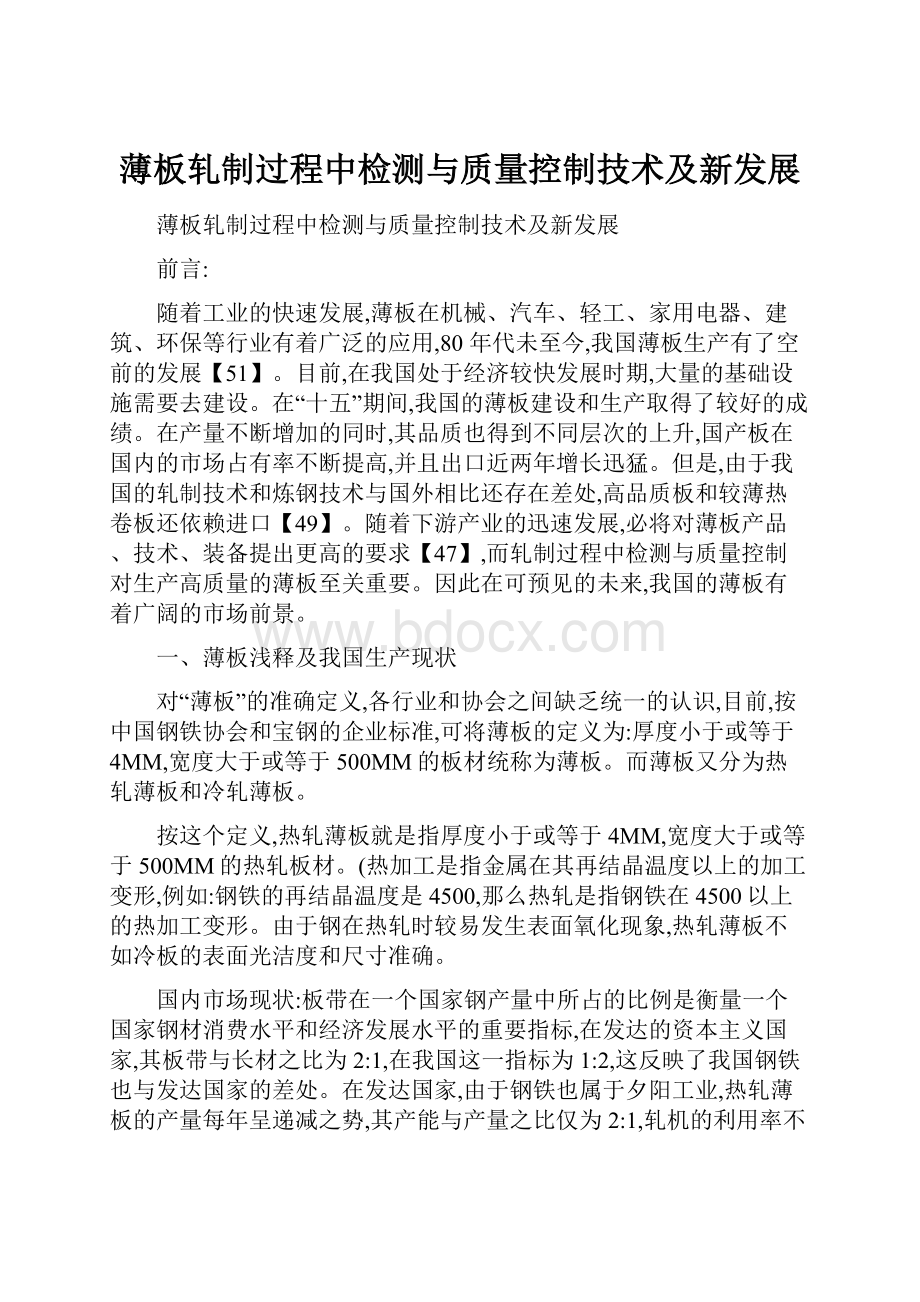
薄板轧制过程中检测与质量控制技术及新发展
薄板轧制过程中检测与质量控制技术及新发展
前言:
随着工业的快速发展,薄板在机械、汽车、轻工、家用电器、建筑、环保等行业有着广泛的应用,80年代未至今,我国薄板生产有了空前的发展【51】。
目前,在我国处于经济较快发展时期,大量的基础设施需要去建设。
在“十五”期间,我国的薄板建设和生产取得了较好的成绩。
在产量不断增加的同时,其品质也得到不同层次的上升,国产板在国内的市场占有率不断提高,并且出口近两年增长迅猛。
但是,由于我国的轧制技术和炼钢技术与国外相比还存在差处,高品质板和较薄热卷板还依赖进口【49】。
随着下游产业的迅速发展,必将对薄板产品、技术、装备提出更高的要求【47】,而轧制过程中检测与质量控制对生产高质量的薄板至关重要。
因此在可预见的未来,我国的薄板有着广阔的市场前景。
一、薄板浅释及我国生产现状
对“薄板”的准确定义,各行业和协会之间缺乏统一的认识,目前,按中国钢铁协会和宝钢的企业标准,可将薄板的定义为:
厚度小于或等于4MM,宽度大于或等于500MM的板材统称为薄板。
而薄板又分为热轧薄板和冷轧薄板。
按这个定义,热轧薄板就是指厚度小于或等于4MM,宽度大于或等于500MM的热轧板材。
(热加工是指金属在其再结晶温度以上的加工变形,例如:
钢铁的再结晶温度是4500,那么热轧是指钢铁在4500以上的热加工变形。
由于钢在热轧时较易发生表面氧化现象,热轧薄板不如冷板的表面光洁度和尺寸准确。
国内市场现状:
板带在一个国家钢产量中所占的比例是衡量一个国家钢材消费水平和经济发展水平的重要指标,在发达的资本主义国家,其板带与长材之比为2:
1,在我国这一指标为1:
2,这反映了我国钢铁也与发达国家的差处。
在发达国家,由于钢铁也属于夕阳工业,热轧薄板的产量每年呈递减之势,其产能与产量之比仅为2:
1,轧机的利用率不足50%,发达的资本主义国家现在主要是利用技术和资本的优势,生产高品质,高附加值的产品。
【49】
由于冷轧薄板比热轧薄板具有强度高,抗凹能力强,表面光洁度好,尺寸精确等优点。
它广泛应用于汽车,家电、轻工、电子、化工等方面。
随着国民经济的快速发展,产品的换代升级和产业结构的不断调整,冷轧薄板的市场需求具有广阔的前景。
我国冷轧薄板发展的市场现状:
由于我国现阶段冷轧卷板质量与发达的资本主义国家相比还存在较大的差处,特别是在生产高档轿车面板,电冰箱面板等方面。
例如:
宝钢的电冰箱冷轧面板的质量稳定性、表面光洁度方面还难达到国内用户的满意,相反,日本的新日铁和南韩的浦项这方面作的不错。
我国现阶段每年生产冷轧薄板约600多万吨,进口约500多万吨,进口主要集中在高档材和较薄材。
【51】
二、轧制过程检测方法研究
近年来,随着制造工业的快速发展,用户对成品带钢的板形精度要求越来越苛刻。
在轧制过程中,为了控制成品的板形,一般在成品机架的出口配置一套板形仪,然后根据板形仪的测量结果反馈到轧机并通过倾辊、弯辊、点冷却等板形控制手段对实物板形进行反馈控制,形成板形闭环控制系统,最终达到改善实物板形的目的。
这就是说,对于板形闭
环控制系统而言,板形检测是前提与基础,所有的板形控制手段如倾辊、弯辊、点冷却等都是以板形检测设备的检测结果作为依据的【1】。
目前,国际上许多著名的公司都有其各自的板形检测设备,而在国内,由于尚无完善的板形检测仪,因此都是从国外成套引进的板形自动控制系统。
【3】
在工业薄板生产线上.薄板冷压成型后,往往不可避免的要有一些疵庇,诸如压痕、漏眼、夹渣等,给后续成型加工带来一定的影响。
如缺陷没有被发现,则制罐厂用该薄板成型后就会出现废品,影响产品质量并产生负效应。
因此,有必要在薄板下线之前发现薄板上的疵庇,打上一定的印记。
从而避免次品进入下一道工序。
这样,如何及时、准确地发现薄板上的疵庇就成为急待解决的问题。
传统方法,查找疵庇是采用人工的办法。
在薄板的一侧用强光照射,在另一侧设专人观察;采用此种办法,浪费一定的人工,而且人眼长期注视着快速移动的薄板,很容易疲倦。
因此.效果可想而知,很难适应目前工业化生产发展的需要。
在当前全面质量管理过程中,更需要先进的智能化的检测手段。
这样,需要研制一种自动检测系统,在无人参与的情况下自动、有效的查找薄板上的疵庇,解决生产上的急需,对保证产品质量,降低原材料消耗,提高成品率。
【5】
(一、基于Web的薄板连轧生产线远程监测系统
随着计算机技术的迅猛发展与普及,网络技术已经开始在各个领域中被广泛应用,在工业检测系统中,应用Web技术实现远程检测以及故障诊断的研究和应用也越来越广泛。
利用计算机技术将必要监测信息送到企业内任意的PC机或移动计算机的屏幕上。
企业有关人员利用Web浏览器可在通用的接口下显示来自监控、数据采集系统和其它管理系统的信息。
这样,企业的中上层管理人员维修人员可以在任意远程或局域网上查看到实时的监控信息,并实现网上远程诊断。
【9】
本系统集成了大数据量传输、特征参数提取、智能诊断、油液状态与磨损影射等高新技术,实现了从动力到每个轧制机架、输送装置、乃至成品等全部生产环节的监测。
其特点包括如下6个部分:
1、针对大型薄板连轧机组整条生产线展开全方位的在线连续监测,能以彩色图形、多种曲线、数字和文字动态反映全部设备的状态。
2、建立起了较为完善的知识库数据库,并使其具有了一定的自学习功能。
3、采用双向推理、神经元网络、模糊专家系统相融合的人工智能方法对大型热连轧机组的各种故障进行诊断和预测。
4、对张力控制装置进行系统辨识,并建立其动态模型,通过仿真进行故障分类,并建立故障树。
5、将分形维数,小波变换等分析技术应用故障特征提取,提高了诊断的精确度。
6、通过铁谱,光谱等分析方法,经模糊评判和预测,全面系统地监测轧机液压润滑系统油品质量和装置的磨损状态。
【9】
(二、表面质量自动检测系统
冷轧带钢的表面质量问题已经被越来越多钢铁企业和最终用户所的关注。
传统上的检测冷已不能满足企业对表面质量控制和表面质量评估的要求,特别是对表面质量有着严格要求的汽车外板,使用表面质量自动检测系统已成为企业的发展趋势。
该系统由检测装置、相机计算机系统、服务器和质量显示终端组成。
检测装置对称安装在生产线上,由表面质量传感器和光源组成。
【4】
1、传感器
传感器系统使用的是相机数字CCD相机,上下表面各两排,每排12个,一排相机同时记录整个表面的图像,一旦相机看到板带的新的部份,新一排的图像就被自动记录下来了。
板带速度越快,则每秒中记录的数量就越多。
面扫描相机根据板带速度,只要需要时随时由外部进行触发拍照。
传感器系统使用的光源为标准泛光光源红外LED,具有寿命长.耗电少等特点。
每个传感器单元都配备了自动照明控制,根据对记录的图像的照明结果的评估,照明控制自动优化光照总量。
2、光源
系统选用LED面光源.发射的光是平行光,相机放置的位置是在入射光的反射光路上。
系统记录下来的图像里.图像是否包括可疑目标,侦测软件要在非常有限的时间内作出决定。
3、服务器
检测服务器由parsytec公司提供,处理器为3.0Hz,2G内存,80GB磁盘阵列RAIDI系统,供操作系统和检测数据库,外置USB硬盘用来给系统备份和进行自动缺陷数据和图像储存。
4、工作原理
通过以上的检测装置,质量自动检测系统做到了板带缺陷100%检测,通过相机记录图像,在线表面传感器(检测梁通过相机计算机进行(相机PC图像分析(缺陷识别,位于生产线服务器进行缺陷存档,数据库保存10天月左右,缺陷包括缺陷图像,容量取决于材质和生产工艺,数据库目录和缺陷图像是自动存档并删除的,若想增加存储时间,可以增设大容量移动硬盘。
检测终端在板卷缺陷分布图显示所有缺陷。
【4】表面检测系统的优势:
【8】
(1精度高,能发现小的缺陷。
(2改进轧辊的更换工作。
(3减少带钢尾端开卷检查次数。
(4降低成本。
(三、基于和差补偿的薄板凸度检测系统
板带材厚度的测量是板带钢轧制生产工艺中的重要环节,对指导操作控制、保证产品质量等起到重要的作用.随着AGG系统在板带轧机上的普遍应用,板带材的纵向厚度精度得到了显著提高,板带材的凸度问题显得日益突出.板带材的凸度问题不仅取决于热轧,冷轧板来料的成品厚度、局部高点、凸度等几何参数也直接影响着冷轧产品最终质量。
1、“和差补偿”原理
和差补偿”原理就是利用一组传感器(传感器A和传感器B垂直放置于被测物体厚度两面的同一轴线上,传感器A和传感器B沿平行于被测物体表面横向移动,在移动中采集大量被测物体厚度变化数据,再把这些数据进行“和差补偿”运算处理,以消除测量误差。
2、测量原理的实现
为了能够离线、快速地进行板厚、板凸度的准确测量,首钢技术研究院提出研究课题,商丘计量测控有限公司和湖北工业大学计算机学院合作,利用上述“和差补偿”原理,共同研制开发了“BH-I型离线薄板凸度测量仪”。
该测量仪器主要用于冷、热轧板绝对厚度和相对厚度的高精度测量,可满足冷热轧板离线、轻便、快速、高精度测量板厚及板凸度的需要.该仪器主要由移动测量架体、嵌入式处理系统和数据库管理系统组成。
为了检测基于“和差补偿”原理设计的板凸度测量仪的精度,将用该仪器测量得到的数据与逐点用高精度千分尺测得的数据进行比较,结果误差小于0.003mm,完全达到板凸度测量系统要求的精度。
因此,该系统可以作为板凸度曲线测量的专用工具使用。
【10】
三、薄板质量控制技术研究
薄板在航空、航天、汽车、船舶及许多民用工业中部占有相当重的比例,因此,提高相应的成形技术和制造水平是一个具有普遍意义的大课题.其核心集中体现在简化设计、提高质量、缩短周期、降低成本。
也就是说,如何充分利用和发挥材料的成形性能、发掘新的成形工艺与方法.并借助当今飞速发展的计算机技术来优化零件的结构及工艺【37】。
随着工业的发展,薄板用户要求生产商提供质量稳定的产品,为了满足用户要求,国外公司从产品质量和过程控制出发开发了轧材质量自动无损捡测系统(NDT。
【33】
(一、热轧薄板质量控制
热轧超薄带钢(厚度≤1.2mm不仅在做为冷轧原料时可以减少冷轧轧制道次,降低生产成本;而且可以替代冷轧带钢直接应用于建筑、汽车和饮料等行业。
生产热轧超薄带钢可使企业每吨带钢的利润增加,从而增强企业的竞争能力。
然而,热轧超薄带钢表面质量要求高,尺寸精度、板形和性能较难控制,以现有的热轧板带技术装备难以生产高质量的热轧超薄带钢。
唐钢超薄带钢生产线是国家国债贴息重点技改项目,采用薄板坯连铸连轧型式,运用了H2结晶器、动态液芯压下、半无头轧制、动态Pc控制、铁索体轧制等新技术,可以生产高质量的0.8~1.2mm热轧超薄带钢。
【32】
目前热轧带钢产品规格范围可降到0.8mm~1.2mm。
随着无头轧制技术、铁索体区轧制、薄板坯连铸连轧、轧后紧凑式卷取工艺等生产工艺及设备的日趋完善和成熟,热轧带钢的生产极限厚度将降至0.6~0.8mm。
【24】
与传统热轧带钢工艺比较在轧钢工艺中最基本的工艺控制因素是温度、变形控制和速度控制,这三个工艺参数的最佳配合最终决定产品的产量、质量。
(1温度控制
根据轧钢工艺中质量控制观点,产品的力学性能很大程度上取决于轧制过程的温度控制。
如能实现恒温轧制,就可以排除温度因素对产品质量的影响,保证产品具有均一的尺寸、板形、金相组织和性能,所以生产中的保温和调温技术非常重要。
(2变形控制
传统热连轧机组的压下规程设定主要是合理的分配各道次的压下量,确定各机架的实际轧出厚度。
薄板坯连铸连轧过程中的变形制定原则与传统的热连轧工艺相同,但在坯料、温度控制、轧机布置与传统的热轧机组有较大差别,在量值方面有较大的变化,表现在变形量和负荷都远大于传统热连轧机。
(3速度控制
传统的热轧带钢生产,为避免温降造成坯料头尾温差而产生的厚度精度差、板形不好和性能不均匀一致等问题,在轧制过程中必须要升速轧制。
【31】
随着热轧薄板成形性能研究及轧制工艺的优化,钢板的力学性能会更加稳定,产品的延伸率也得到了提高【28】。
(二、冷轧薄板质量控制
在冷轧生产过程中,质量控制是非常重要的方面,有时甚至是决定性的方面。
冷轧的生产过程主要包括开卷、轧制变形和卷取三部分,而其中轧制变形是影响和控制冷轧产品表面质量最关键的过程。
冷轧质量的控制根据缺陷产生的部位主要分为两部份。
一是辊缝内轧件表面质量控制,构成现代高速冷轧机辊缝轧件变形的三个基本组元是轧件、轧辊和润滑,在辊缝内这三个基本组元相互作用相互影响,共同影响与制约产品质量,根据缺陷的产生原因,辊缝内轧件表面缺陷分为三类:
与润滑有关的缺陷、轧辊自身缺陷在板面上的反映和机械装配不当产生的损伤。
二是辊缝外轧件表面质量控制,影响辊缝外轧件表面质量的主要因素有与带材接触的导辊与带材间运行的同步性,开卷和卷取张力给定及操作方法。
【25】冷轧薄板质量控制应注意以下几个方面:
【52】
(1轧制压下率与轧制速度控制。
(2开卷张力与喂料高度控制。
(3轧制张力控制。
(三、薄板坯连铸连轧的产品质量控制
薄板坯连铸连轧技术的开发和广泛应用使钢铁工业的工艺技术和设备组成发生了突破性变革,被认为是当前板材发展的方向之一。
薄板坯连铸连轧技术与常规流程比;具有节能、投资省、生产周期短、劳动成本低及适应性强等优点,因此赢得了世界各国的青睐【23】。
由于薄板坯连铸连轧工艺与传统工艺在钢铁冶金过程中的热历史不同,加上在连铸、均热、连轧及层流冷却过程中采取了液芯压下、电磁制动、充分长且灵活的隧道式加热、均热、高压除磷、高精度连轧控制及灵活的层流冷却等一系列新的工艺控制技术,因此在新产品开发、扩大品种规格范围等方面需要充分认识这些新的工艺特点、充分发挥其技术优势【19】。
薄板坯连铸连轧技术除其短流程、近终形、节约能源、成本低的优势外,另一重要的优点是质量好。
由于薄板坯在结晶器内的冷却强度远大于传统的板坯,其二次和三次枝晶更短,铸态组织晶粒比传统板坯更细、更均匀。
原始组织精细为最终组织的细化创造了条件。
同时因冷却强度大,板坯的微观偏析也得到较大的改善,分布也更均匀,产品的性能更加稳定【18】。
薄板坯连铸连轧的研究及产品开发实践表明,热轧薄板最终产品的组织性能不仅取决于冶金成分,而且与各工艺过程环节的控制方法及参数密切相关,需要在各工艺过程中对其组织性能进行综合的优化控制才能达到最佳效果。
同时,在冶金成分一定的条件下,根据产品订货要求,可以在一定范围内采取灵活的柔性工艺控制方法得到不同强度性能级别的板带产品【19】。
四、薄板生产技术的新发展
装备制造业是为国民经济发展和国防建设提供技术装备的基础性产业。
钢铁业与装备制造业产业链关系非常紧密。
国务院提出的《关于加快振兴装备制造业的若干意见》,对钢铁行业来说,显然具有一定的政策利好因素。
由于行业用钢的特点,装备制造业加快发展,将大大推动板材的需求增长,同时对板材的质量也提出了更高的要求。
【47】
(一、薄板检测技术新发展
随着汽车、电器制造等工业部门的发展,对板形平直度的要求愈来愈高。
解决板形问题主要涉及两方面的技术:
一是板形信息的检测、传输和处理;二是控制手段以及相应的控制系统。
下面介绍薄板检测技术的最新发展。
按照与板带之间的空间关系,板形检测装置可分为接触式和非接触式两大类。
由于接触式板形检测装置易于划伤带钢表露,而且造债昂贵,维修困难,因而非接触式板形检测方法受到了人们越来越多的重视。
非接触式板形检测技术以激光三角法(位移法、光切法(截光法和莫尔法为代表这些测量方法具有结构简单、无损带钢表面、易于维护等优点。
【45】随着热轧板带钢短流程轧制工艺技术的日趋成熟,热轧板带向厚度更薄的方向发展,在更多领域可以用“热轧产品”代替“冷轧产品”。
因此,热轧板带的在线板形检测显得尤为重要。
目前,以激光三角法(位移法、光切法(截光法和莫尔法为代表的热轧带钢板形检测技术在实际应用中还存在着一些局限性,影响板形检测装置的适应性、精确度和稳定性。
今后热轧带钢板形检测的研究方向应结合板形自动控制数学模型技术等方面,使热轧板形检测技术向高精度、高速度、数字化的方向发展。
【50】
(二)、薄板质量控制技术新发展板带材的质量很大程度上取决于对轧制工艺过程的控制。
常规方法有许多不足之处,原始凸度的设定无法对不同规格、不同材质的轧件进行跟踪控制;不均匀冷却方法具有响应太慢的缺点。
戴维麦基公司对板形自动控制系统及冷却液的喷射装置进行了独特的设计.其中彼此分隔开的冷却和润滑系统(SLC和动态轧制工艺系统(DSS收到了很好的效果。
戴维.麦基公司利用计算机预测了全带材轧制的主要过程。
充分利用计算机来建立轧制过程中的数学模型,本质上就是在线的模型参数估计。
其中最为典型的例子是动态轧制工艺系统。
该系统主要安装在热轧机组上,用于板形和断面形状的控制。
由建立的数学模型和程序,根据预测的结果,连续地由轧机自适应功能进行控制。
与通常的反馈式AGC系统不同之处,在于这个系统采用两个基本自适应等级。
第一级为轧机控制的自适应,即包括轧辊的弯辊力、压下量的方式、运行速度和轧辊冷却液的分布等,使产品质量达到始终稳定一致。
实践证明,采用质量控制轧制工艺技术是生产强度高、韧性好、可焊性优良且成本低的钢板的最好办法。
将应变诱导轧制技术与常规控轧工艺相结合可获得更为理想的超细晶组织。
【42】结束语:
从长期看,目前我国的工业化程度还不是很高,大量基础设施需要建设;而随着我国装备制造业和建筑技术发展,加上对产品质量要求较高的专用板需求的快速增长,必将推动薄板生产技术的进步,拉动薄板市场的进一步发展。
参考文献:
【1【2【3【4【5】周莲莲,郑志刚,白振华.板带轧机板形检测设备系统误差综合补偿技术的开发.2009.05.】周鑫,马海良,王超.包钢集团冷轧机组板形检测.2008.08.】黄元辉.宝钢DCR机组板形检测与控制.2008.02.】王晓光,崔勇,庄权华.表面质量自动检测系统在连退线的应用.2008.05.】于正林,姜涛,王燕飞.薄板疵庇检测方法的研究.2001.06.
【6】张旭,小幺.不锈钢轧制过程板面缺陷分析及对策.2010.04.【7】周俊峰.高精度薄板带板凸度激光检测的误差分析与精度控制研究.2006.12.【8】路艳平,王宇,胡文强.邯钢CSP生产线应用在线表面质量检测系统的可行性研究2005.06.【9】任勇,吴百海,毛宁.基于Web的大型薄板连轧生产线远程监测系统.2007.03.【10】马轩,刘迪.基于和差补偿的板带钢薄板凸度检测系统.2010.04.【11】郭豫荣,张修义.金属薄板分层缺陷无损检测技术研究.2010.02.【12】冯雅观.提高薄板轧制过程分析的可靠性.1994.09.【13】江虎.涡流检测技术在重钢冷轧厂轧辊管理中的应用.2009.03.【14】李海艳.中碳钢薄板轧制的表面缺陷.2001.01.【15】陈兆能,佟德纯,朱继梅.状态监测与故障诊断技术在薄板轧制系统上的应用.2003.07.【16】曹亚丹,李惊鸿,杨福新.鞍钢中薄板坯连铸钢水质量控制实践.2000.08.【17】李慎国,吴晓军,黎雪芬.薄板冲压成形中的压边力控制模拟与应用.2004.07.【18】唐荻,蔡庆伍,米振莉.薄板坯连铸连轧的产品质量控制.1998.07.【19】康永林,傅杰.薄板坯连铸连轧组织性能综合控制理论及应用.2007.【20】时旭,刘相华,王国栋.板轧制的接触摩擦及其对轧制力的影响.2005.06.【21】许健勇.薄板轧制厚度与板形高精度控制技术.2000.【22】徐俊,崔晨光,程其华.薄带高速冷连轧轧制规程的优化.2007.06.【23】闰绍维,张彩军,何东颖.超薄热带连铸连轧生产线钢水质量控制.2007.02.【24】黄徐晶.超薄热轧带钢生产技术.2007.【25】王华春,李吉彬.冷轧表面质量控制的影响因素.2004.04.【26】闫志波.冷轧薄板冲压性能的影响因素.2006.04.【27】丘宏扬,黄亚娟.摩擦对薄板冲压件成形性能的影响.2005.01.【28】任海鹏,李欣波.热轧薄板冲压成形性能研究及轧制工艺优化.2006.【29】刘小川.唐钢1810mm生产线质量控制系统分析.2006.04.【30】陈礼斌,张庆国,王维东.唐钢薄板坯连铸连轧生产线质量控制系统分析.2003.02.【31】林绍峰.唐钢薄板坯热轧带钢轧制工艺特点及质量控制分析.2006.02.【32】韩旭光,杨杰.唐钢超薄带钢生产线质量控制技术.2007.【33】利比茨克.轧钢产品在线质量控制.2009.【34】冯玉光,丛海鹏.主成分分析法在薄板坯连铸连轧生产线质量控制问题中的应用.2005.【35】朱兴元,邹洋.稀土对冷轧深冲薄板成形性能的影响.2006.【36】冯士超,王艳红.连铸薄板坯的质量控制措施.2008.【37】朱丽萍,李新军.薄板成形技术研究现状.2009.【38】唐获.薄板坯连铸连轧技术的现状和新发展.2008.【39】热轧超薄带钢生产的新发展.2009.【40】李频.薄板坯连铸连轧技术特点浅析.2005.07.【41】张如斌.薄板坯连铸连轧在中国的迅猛发展2004.09.【42】夏佃秀,李兴芳,李建沛.控制轧制和控制冷却技术的新发展.2005.【43】郭伟刚,吴晓峰,陈磊.电磁成形技术在薄板成形中应用的研究进展.2007.06.【44】康永林.近两年我国薄板坯连铸连轧生产技术发展情况分析.2007.【45】王快社,张兵.板形检测控制新方法.2006.09.【46】董瑞峰.我国薄板坯连铸连轧生产技术发展现状分析.2009.【47】我国板带材生产状况及发展趋势.2009.【48】冷轧板带钢生产现状及新技术发展研究.2010.10.【49】冷、热薄板浅释及我国生产现状.2009.05.【50】王训宏,张兵.热轧板带板形检测发展分析.2005.02.【51】中国冷轧薄板市场分析研究.2009.【52】齐克敏.轧制理论与工艺.2008.05.