承钢烧结矿优化研究内容.docx
《承钢烧结矿优化研究内容.docx》由会员分享,可在线阅读,更多相关《承钢烧结矿优化研究内容.docx(13页珍藏版)》请在冰豆网上搜索。
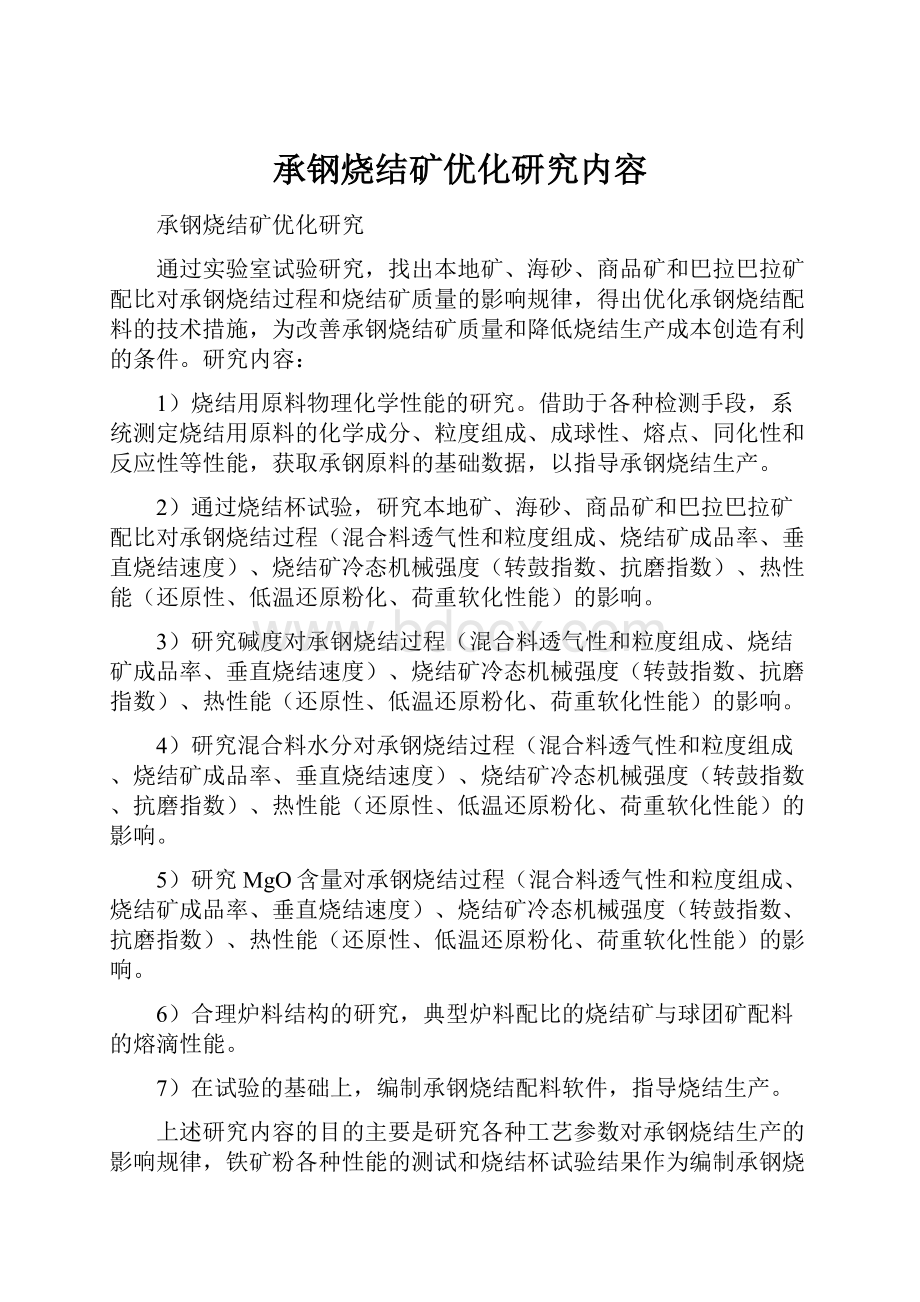
承钢烧结矿优化研究内容
承钢烧结矿优化研究
通过实验室试验研究,找出本地矿、海砂、商品矿和巴拉巴拉矿配比对承钢烧结过程和烧结矿质量的影响规律,得出优化承钢烧结配料的技术措施,为改善承钢烧结矿质量和降低烧结生产成本创造有利的条件。
研究内容:
1)烧结用原料物理化学性能的研究。
借助于各种检测手段,系统测定烧结用原料的化学成分、粒度组成、成球性、熔点、同化性和反应性等性能,获取承钢原料的基础数据,以指导承钢烧结生产。
2)通过烧结杯试验,研究本地矿、海砂、商品矿和巴拉巴拉矿配比对承钢烧结过程(混合料透气性和粒度组成、烧结矿成品率、垂直烧结速度)、烧结矿冷态机械强度(转鼓指数、抗磨指数)、热性能(还原性、低温还原粉化、荷重软化性能)的影响。
3)研究碱度对承钢烧结过程(混合料透气性和粒度组成、烧结矿成品率、垂直烧结速度)、烧结矿冷态机械强度(转鼓指数、抗磨指数)、热性能(还原性、低温还原粉化、荷重软化性能)的影响。
4)研究混合料水分对承钢烧结过程(混合料透气性和粒度组成、烧结矿成品率、垂直烧结速度)、烧结矿冷态机械强度(转鼓指数、抗磨指数)、热性能(还原性、低温还原粉化、荷重软化性能)的影响。
5)研究MgO含量对承钢烧结过程(混合料透气性和粒度组成、烧结矿成品率、垂直烧结速度)、烧结矿冷态机械强度(转鼓指数、抗磨指数)、热性能(还原性、低温还原粉化、荷重软化性能)的影响。
6)合理炉料结构的研究,典型炉料配比的烧结矿与球团矿配料的熔滴性能。
7)在试验的基础上,编制承钢烧结配料软件,指导烧结生产。
上述研究内容的目的主要是研究各种工艺参数对承钢烧结生产的影响规律,铁矿粉各种性能的测试和烧结杯试验结果作为编制承钢烧结配料软件,指导烧结生产的基础,为此合理选择测定参数,进而得出影响规律是课题成败的关键。
课题突出的是理论性研究,但也要考虑生产实际情况,应尽快查找有关资料,熟悉烧结生产的有关知识和各种测试的内容、设备及方法。
一、承钢原料的物化性能分析
1、烧结用原燃料的化学成分
承钢目前采用或将来准备采用的原燃料的化学分析。
2、烧结用含铁原料的粒度组成
利用LS激光粒度分析仪对铁精矿粉进行粒度分析。
3、烧结用含铁原料的矿物组成和矿物结构
利用环氧树酯粘结和磨片技术分别将铁矿粉制成光片和薄片,借助于光学显微镜测定承钢烧结用铁矿粉的矿物组成。
4、烧结用含铁原料中铁矿物和脉石矿物的粒度、孔隙度
利用环氧树酯粘结和磨片技术分别将铁矿粉制成光片和薄片,借助于光学显微镜测定承钢烧结用铁矿粉中铁矿物和脉石矿物的粒度范围、平均粒度和孔隙度。
5、烧结用含铁原料的熔点
烧结用含铁原料的熔点采用RD-04型全自动熔点测定仪进行测定。
利用专用模型将所测定的矿粉制成Φ5mm×5mm的园柱形试样,在大气条件下升温加热,升温速度控制为:
600℃以下,15℃/min;600℃以上,10℃/min,将试样在加热时高度减至原试样50%时的温度,即半球点的温度定义为该铁矿石的熔点。
6、烧结用含铁原料的同化性能
烧结用含铁原料同化性能的检测采用RD-04型全自动熔点测定仪进行,利用专用模型分别将CaO和铁矿粉压制成Φ5×5mm的园柱形试样,然后将铁矿粉试样置于CaO试样之上,放入RD-04型全自动熔点测定仪中,在空气气氛下升温加热,升温速度控制为:
600℃以下,15℃/min;600℃以上,10℃/min。
将铁矿粉试样开始熔化的温度定义为最低同化温度,测定不同铁矿粉达到这一同化特征的温度,由此评价不同矿粉的同化性能。
7、烧结用含铁原料的液相流动特性
将铁矿粉与CaO按二元碱度的要求进行配料,根据高碱度烧结矿对粘附粉的碱度要求以及考虑到物料偏析的影响,二元碱度选取为3.0。
铁矿粉与CaO混匀后利用专用模型压制成Φ5×5mm的圆柱形试样,然后在模拟烧结温度曲线和气氛的条件下在RD-04型全自动熔点测定仪中进行焙烧,考虑到低温烧结的原则,试验温度控制在1280℃。
通过测定每个圆柱形试样焙烧前后的投影面积,并利用以下公式计算出铁矿粉的液相流动性指数。
流动性指数=(试样流动后面积-试样原始面积)/试样原始面积
8、烧结用含铁原料差热分析
采用仪器的型号
9、烧结用含铁原料的成球性(这部分比较乱,需参考相关教科书重新确定检测指标)
9.1制粒效果的评价
烧结混合料混匀制粒效果的评价目前主要有以下几种方法。
1)制粒后烧结混合料的平均粒度
取制粒料500g,用液氮速冻后振动筛分,按+5mm,5~3mm,3~1mm,-lmm分级,其平均粒度d的计算方法见公式
(2)所示:
(2)
式中:
Pi—制粒料中i粒级百分含量,%
di—制粒料中i粒级的平均粒径,mm
(>5mm取5×1.414mm,5~3mm取4mm,3~1mm取2mm,-1mm取0.5mm进行计算)
2)制粒效率η:
以制粒后+3mm的增量来表示制粒效率η,η越大,制粒效果越好。
计算方法见公式(3)所示:
η=
(3)
式中:
E1—制粒前烧结混合料中+3mm的含量,%;
E2—制粒后烧结混合料中+3mm的含量,%;
3)制粒性指数GI0.5,GI0.5越大,表明细粒级(<0.5mm)物料粘附成球越高,制粒效果越好。
计算方法见公式(4)所示:
GI0.5=
(4)
式中:
A1—制粒前烧结混合料中-0.5mm含量,%
A2—制粒后烧结混合料中-0.5mm含量,%
4)抗机械冲击指数
取制粒后料足量,从1m高处落下10次,取落下样500g用液氮速冻后筛分,计算其抗机械冲击指数B,计算方法见公式(5)所示:
B=
(5)
式中
M(0.5)—制粒前干烧结混合料中<0.5mm粒级含量,%;
P(0.5)—制粒后二混料中<0.5mm粒级含量,%;
S(0.5)—二混料落下实验后<0.5mm粒级含量,%。
5)烧结混合料透气性指数
取制粒后的烧结混合料装入Φ100mm×295mm的圆柱形容器内,控制通过料层的气体流量Q为35m3/h,测定料层的压降(P),料层透气性指数可由Voice公式计算[21],计算方法见公式(6)所示:
Tq=
(6)
式中:
Q—通过料层的风量,m3/h
h—料层的高度,mm
A—容器的面积,mm2
P—通过料层的压降mmH2O,×9.8Pa
9.2原料成球性测试
1.原料性能测试
1)铁矿粉最大分子水
采用压滤法测定铁矿粉的最大分子水。
在试样表面上施加一定的压力,使试样中的自由水、毛细水被压出并被滤纸所吸收,保留在试样中的水就是最大分子水。
测试步骤:
①将20g左右试样以蒸馏水充分湿润至饱和状态,静置2h。
②先把20张滤纸放在压塞上,经过润湿的试样放在滤纸上,再在试样上放好20张滤纸,放入上压塞。
③然后施加压力(65.5kg/cm2),加压5min后,取出试样称量为G1,放入烘箱110±5℃进行烘干至恒重G2,根据公式(6)计算出最大分子水W水。
W水=
(6)
2)铁矿粉最大毛细水
利用毛细水只能靠毛细力的作用在颗粒之间形成的毛细孔迁移,重力并不能使其发生运动的原理,采用涂蜡容量法测定,当微颗粒间的孔隙为毛细水所充满时,所填充的水就是最大毛细水。
测试步骤:
①首先将装料器、筛板涂上一薄层蜡,把筛板放入装料器中,在筛板上铺两层滤纸。
②称好的干燥试样(50~100g)以松散的状态装入装料器中,料面要平整,并测出料层高度H。
应该注意,测定前进水管的水位与筛板底保持在同一水平线上。
③记下装料时间即开始吸水初始时间t1。
当毛细水沿毛细孔上升时,进水管的水位逐渐下降,此时打开滴定管阀门,放出蒸馏水,使进水管的水位保持稳定,直到料面已湿润,试样不再吸水为止,记下吸水终止时间t2,注意:
滴定管的放水速度应与毛细水上升速度一致。
④称量吸水之后试样的重量。
⑤按照公式(7)计算铁矿粉的最大毛细水。
W毛=
(7)
式中:
W毛——试样最大毛细水,%;
m1——试样吸水量,g;
m2——干样重量,g。
V=
(8)
式中:
V——毛细水平均上升速度,mm/s;
H——试样高度,mm;
t1——试样初始吸水时间,s;
t2——试样中止吸水时间,s。
3)铁矿粉成球性能
造球原料的自然性质中,以颗粒表面的亲水性、颗粒形状,对其成球性影响最大。
颗粒表面亲水性越高,固相与液相界面的接触角越小,颗粒容易被水浸湿,薄膜水和毛细水含量越高,毛细水的迁移速度也高,从而成球性好。
利用铁矿粉最大分子水、最大毛细水,用公式(9)可以计算出各种铁矿粉静态成球性指数K。
(9)
式中:
W水—
W水—
根据K值大小来衡量铁矿粉的静态成球性能,K值越大,说明其越容易成球。
K=0.20~0.35物料属弱成球性;K=0.35~0.60物料属中成球性;
K=0.60~0.80物料属良成球性;K>0.80物料属优成球性。
二、烧结配矿试验
2.1烧结杯实验
根据承钢生产和未来原料结构进行烧结杯实验。
烧结杯尺寸为Φ300mm×600mm。
各次试验用料按试验设计方案配料。
每次试验的总原料量为100kg,人工加水拌匀,混合料水分控制为8%左右,然后加入Φ600mm×1000mm的小型圆筒混料机内进行混匀造球,混匀造球的时间控制为7min。
烧结杯底层放置4.0kg大于10mm的成品烧结矿作为铺底料,烧结料层厚度控制为600mm。
风机风量为14.4m3/min,烧结负压控制为15000Pa。
采用石油液化气进行烧结点火,烧结点火温度控制为1150℃,烧结点火时间为1min,烧结点火负压控制为8000Pa,将烧结废气温度开始下降时定为烧结终点,当废气温度达到230℃时倒出、破碎(达到终点以后风机的风量不变)。
2.2烧结指标测定
2.2.1混合料粒度组成
混合料的粒度组成:
经配料、焖料、混料机混料后,取混合料2kg,在-10℃下冷冻1h后,检测混合料粒度组成。
2.2.2混合料透气性指数
透气性指数根据日本标准进行测定,试验装置如图2.1所示。
透气性指数的表达式为:
式中:
JPU—日本透气性单位;
Q—通过风量,7.5m3/min;
A—料面端面积,0.0184m2;
H—料层厚度,0.4m;
—压力损失,Pa。
1、装料桶;2、U形压力计;3、浮子流量计;4、截流盖板;5、烧结杯。
图2.1透气性指数测试装置
2.2.3烧结透气性
根据混合料透气性的定义,混合料装入烧结杯点火后,控制此时的风量,得到的负压即可表示混合料的透气性。
烧结过程中在相同点火条件、抽风负压下,记录废气温度曲线,测定垂直烧结速度。
2.2.4烧结矿冷强度
烧结矿的冷强度和粒度组成测定参照国家标准(YB/T5166-1993),烧结矿从烧结杯倒出后,烧结饼置于2m高自由落下至铁板3次,取大于10mm的百分比作为烧结成品率。
有关指标计算方法:
成品率=
式中:
G1——大于5mm粒级的烧结矿重量,kg;
W2——烧结矿总重,kg。
垂直烧结速度=
式中:
H1——装料前料面至杯口的高度,mm;
H2——装料后料面至杯口的高度,mm;
t——烧结时间,min。
所用转鼓为Φ1000mm×250mm的1/2ISO转鼓,试样为大于10mm的成品烧结矿7.5kg,以25r/min的转速转动8min,取大于6.3mm的百分比作为烧结矿的转鼓指数,取小于0.5mm的百分比作为烧结矿的耐磨指数。
转鼓指数:
抗磨指数:
式中:
m0——入鼓试样重量,kg;
m1——转鼓后+6.3mm粒级部分重量,kg;
m2——转鼓后-6.3mm~+0.5mm粒级部分重量,kg。
2.3烧结矿冶金性能测试
2.3.1还原性能
采用国家标准(GB/T13241-1991)进行测定。
在固定床中用CO和N2的混合气体进行等温还原,试样粒度10.0~12.5mm,试样重量500±1g,还原温度900℃,还原气体成分CO:
N2=30:
70,还原气体流量为15L/min,还原时间3h。
主要考核的还原度指数(RI)是指铁矿石还原3h时的还原度。
用下列公式计算时间tmin后的还原度Rt,计算RI时,t为3h,以三价铁为基准,用质量百分数表示:
式中:
m0——试样的质量,g;
m1——还原开始前试样质量,g;
mt——还原tmin后试样质量,g;
W1——试验前试样中FeO的含量,%;
W2——试验前试样的全铁含量,%。
2.3.2低温还原粉化性能
根据《铁矿石低温粉化试验静态还原后使用冷转鼓的方法》(GB/T13242—1991)进行烧结矿的低温还原粉化试验。
烧结矿的低温还原粉化试验分为定温还原试验和转鼓试验两部分,还原反应管的内径为Φ75mm,试验用试样为500g粒度为10.0~12.5mm成品烧结矿,还原温度控制为500℃,还原气体的成分控制为CO:
CO2:
N2=20:
20:
60,还原气体的流量控制为15L/min,定温还原的时间控制为1h。
还原后的试样在纯N2保护下冷却至室温,称重后装入尺寸为Φ130mm×200mm的转鼓,转鼓以10r/min的速度转300r,取出后分别用6.3mm、3.15mm、0.5mm的方孔筛进行筛分分离,分别将试样中大于6.3mm的百分比、大于3.15mm的百分比、小于0.5mm的百分比以RDI+6.3、RDI+3.15和RDI-0.5表示。
RDI+3.15为考核指标,RDI+6.3和RDI-0.5为参考指标。
1空气压缩机;2氮气瓶;3CO转化炉;4混合器;5洗涤瓶(吸收O2);6洗涤瓶(吸收CO2);7洗涤瓶(干燥气体);8流量计;10还原炉;11反应管;12电子天平;13废气燃烧器;14运算器;15记录仪;16红外气体分析仪(分析记录CO量);17红外气体分析仪(分析记录CO2量);18温控仪。
图2.2还原装置示意图
2.3.3荷重软化性能
在升温过程中,当料柱高度收缩10%时的温度为软化开始温度(T10%),收缩40%时的温度为软化终了温度(T40%),△T=T40%-T10%为软化温度区间。
试样粒度为2.5~3.2mm,荷重为1kg/cm2,料柱高度为20mm。
荷重软化试验装置示意图见图2.3。
1硅碳棒;2电炉;3坩埚底座;4试样;5硅碳棒压杆;6紧固螺丝;7配重;
8百分表;9钢棒压杆;10支架;11石墨坩埚;12热电偶;13温控仪
图2.3荷重软化试验装置示意图
需承钢提供的条件
1.承钢目前采用或将来准备采用烧结配料方案:
表1承钢烧结配料方案
混匀料配比
方案-1
方案-2
方案-3
方案-4
方案-5
普矿
本地矿
商品矿
巴拉巴拉矿
钢渣
返矿
石灰石粉
合计
100
100
100
100
100
注:
1、所有原燃料都以承钢提供为准;
2、烧结矿FeO含量按%控制;
3、烧结矿的水份按%控制;
4、烧结矿MgO含量按控制;
5、烧结矿的品位按%控制。
2.采集具有代表性的承钢目前采用或将来准备采用的原燃料,并送至河北理工大学。
3.承钢目前采用或将来准备采用的原燃料的化学分析,最好由承钢提供。