数控机床的分类及典型轴类零件的加工.docx
《数控机床的分类及典型轴类零件的加工.docx》由会员分享,可在线阅读,更多相关《数控机床的分类及典型轴类零件的加工.docx(30页珍藏版)》请在冰豆网上搜索。
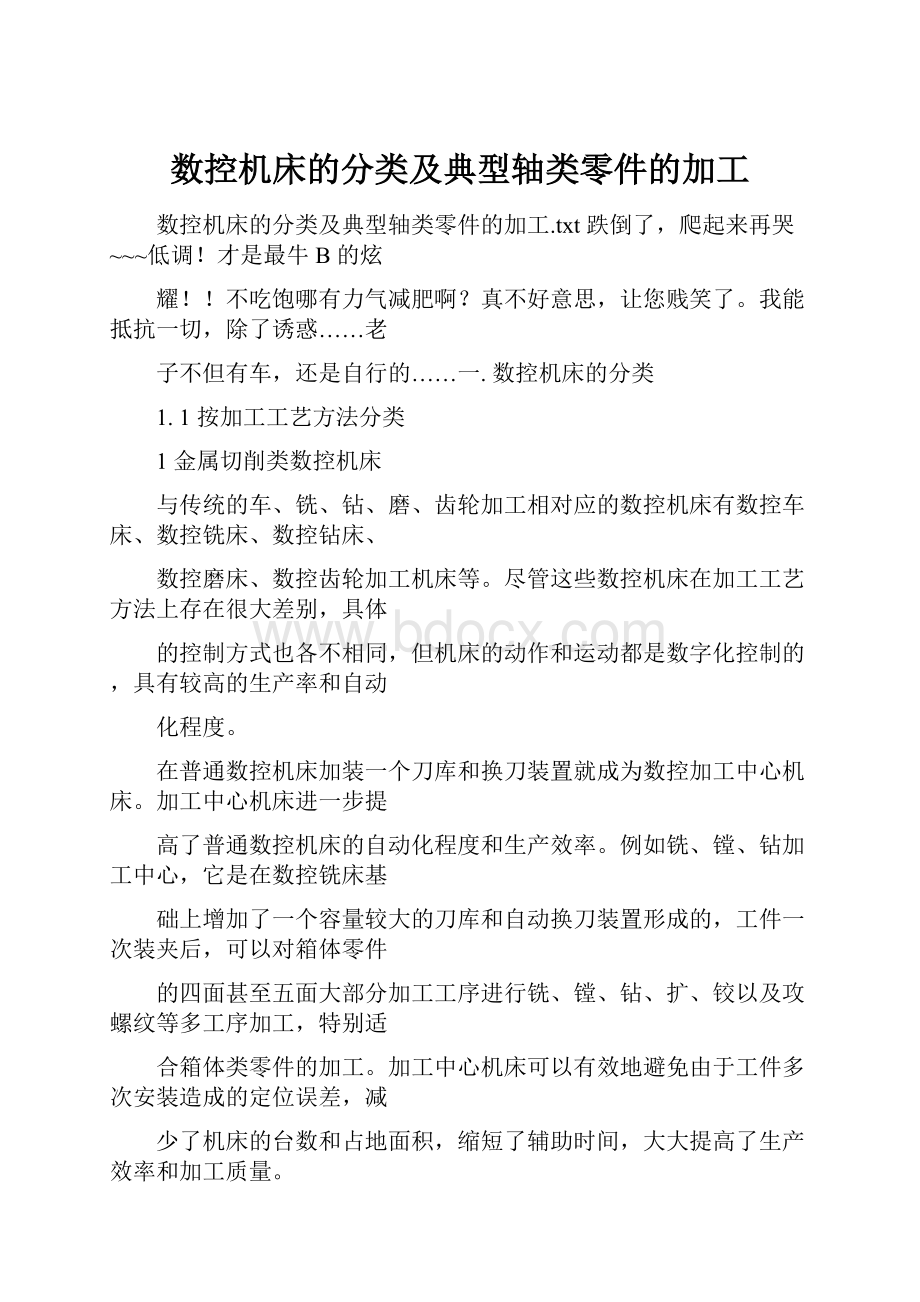
数控机床的分类及典型轴类零件的加工
数控机床的分类及典型轴类零件的加工.txt 跌倒了,爬起来再哭~~~低调!
才是最牛 B 的炫
耀!
!
不吃饱哪有力气减肥啊?
真不好意思,让您贱笑了。
我能抵抗一切,除了诱惑……老
子不但有车,还是自行的……一. 数控机床的分类
1. 1 按加工工艺方法分类
1 金属切削类数控机床
与传统的车、铣、钻、磨、齿轮加工相对应的数控机床有数控车床、数控铣床、数控钻床、
数控磨床、数控齿轮加工机床等。
尽管这些数控机床在加工工艺方法上存在很大差别,具体
的控制方式也各不相同,但机床的动作和运动都是数字化控制的,具有较高的生产率和自动
化程度。
在普通数控机床加装一个刀库和换刀装置就成为数控加工中心机床。
加工中心机床进一步提
高了普通数控机床的自动化程度和生产效率。
例如铣、镗、钻加工中心,它是在数控铣床基
础上增加了一个容量较大的刀库和自动换刀装置形成的,工件一次装夹后,可以对箱体零件
的四面甚至五面大部分加工工序进行铣、镗、钻、扩、铰以及攻螺纹等多工序加工,特别适
合箱体类零件的加工。
加工中心机床可以有效地避免由于工件多次安装造成的定位误差,减
少了机床的台数和占地面积,缩短了辅助时间,大大提高了生产效率和加工质量。
2 特种加工类数控机床
除了切削加工数控机床以外,数控技术也大量用于数控电火花线切割机床、数控电火花成型
机床、数控等离子弧切割机床、数控火焰切割机床以及数控激光加工机床等。
3 板材加工数控机床
常见的应用于金属板材加工的数控机床有数控压力机、数控剪板机和数控折弯机等。
近年来,其它机械设备中也大量采用了数控技术,如数控多坐标测量机、自动绘图机及工业
机器人等
1. 2 按控制控制运动轨迹分类
1 点位控制数控机床
位置的精确定位,在移动和定位过程中不进行任何加工。
机床数控系统只控制行程终点的坐
标值,不控制点与点之间的运动轨迹,因此几个坐标轴之间的运动无任何联系。
可以几个坐
标同时向目标点运动,也可以各个坐标单独依次运动。
这类数控机床主要有数控坐标镗床、数控钻床、数控冲床、数控点焊机等。
点位控制数控机
床的数控装置称为点位数控装置。
2 直线控制数控机床
直线控制数控机床可控制刀具或工作台以适当的进给速度,沿着平行于坐标轴的方向进行直
线移动和切削加工,进给速度根据切削条件可在一定范围内变化。
直线控制的简易数控车床,只有两个坐标轴,可加工阶梯轴。
直线控制的数控铣床,有三个
坐标轴,可用于平面的铣削加工。
现代组合机床采用数控进给伺服系统,驱动动力头带有多
轴箱的轴向进给进行钻镗加工,它也可算是一种直线控制数控机床。
数控镗铣床、加工中心等机床,它的各个坐标方向的进给运动的速度能在一定范围内进行调
整,兼有点位和直线控制加工的功能,这类机床应该称为点位/直线控制的数控机床。
3 轮廓控制数控机床
轮廓控制数控机床能够对两个或两个以上运动的位移及速度进行连续相关的控制,使合成的
平面或空间的运动轨迹能满足零件轮廓的要求。
它不仅能控制机床移动部件的起点与终点坐
标,而且能控制整个加工轮廓每一点的速度和位移,将工件加工成要求的轮廓形状。
常用的数控车床、数控铣床、数控磨床就是典型的轮廓控制数控机床。
数控火焰切割机、电
火花加工机床以及数控绘图机等也采用了轮廓控制系统。
轮廓控制系统的结构要比点位/直
线控系统更为复杂,在加工过程中需要不断进行插补运算,然后进行相应的速度与位移控制。
现在计算机数控装置的控制功能均由软件实现,增加轮廓控制功能不会带来成本的增加。
因
此,除少数专用控制系统外,现代计算机数控装置都具有轮廓控制功能。
1. 3 按驱动装置的特点分
1 开环控制数控机床
这类控制的数控机床是其控制系统没有位置检测元件,伺服驱动部件通常为反应式步进电动
机或混合式伺服步进电动机。
数控系统每发出一个进给指令,经驱动电路功率放大后,驱动
步进电机旋转一个角度,再经过齿轮减速装置带动丝杠旋转,通过丝杠螺母机构转换为移动
部件的直线位移。
移动部件的移动速度与位移量是由输入脉冲的频率与脉冲数所决定的。
此
类数控机床的信息流是单向的,即进给脉冲发出去后,实际移动值不再反馈回来,所以称为
开环控制数控机床。
开环控制系统的数控机床结构简单,成本较低。
但是,系统对移动部件的实际位移量不进行
监测,也不能进行误差校正。
因此,步进电动机的失步、步距角误差、齿轮与丝杠等传动误
差都将影响被加工零件的精度。
开环控制系统仅适用于加工精度要求不很高的中小型数控机
床,特别是简易经济型数控机床。
2 闭环控制数控机床
接对工作台的实际位移进行检测,将测量的实际位移值反馈到数控装置中,与输入的指令位
移值进行比较,用差值对机床进行控制,使移动部件按照实际需要的位移量运动,最终实现
移动部件的精确运动和定位。
从理论上讲,闭环系统的运动精度主要取决于检测装置的检测
精度,也与传动链的误差无关,因此其控制精度高。
图 1-3 所示的为闭环控制数控机床的系
统框图。
图中 A 为速度传感器、C 为直线位移传感器。
当位移指令值发送到位置比较电路时,
若工作台没有移动,则没有反馈量,指令值使得伺服电动机转动,通过 A 将速度反馈信号送
到速度控制电路,通过 C 将工作台实际位移量反馈回去,在位置比较电路中与位移指令值相
比较,用比较后得到的差值进行位置控制,直至差值为零时为止。
这类控制的数控机床,因
把机床工作台纳入了控制环节,故称为闭环控制数控机床。
闭环控制数控机床的定位精度高,但调试和维修都较困难,系统复杂,成本高。
3 半闭环控制数控机床
半闭环控制数控机床是在伺服电动机的轴或数控机床的传动丝杠上装有角位移电流检测装置
(如光电编码器等),通过检测丝杠的转角间接地检测移动部件的实际位移,然后反馈到数
控装置中去,并对误差进行修正。
通过测速元件 A 和光电编码盘 B 可间接检测出伺服电动机
的转速,从而推算出工作台的实际位移量,将此值与指令值进行比较,用差值来实现控制。
由于工作台没有包括在控制回路中,因而称为半闭环控制数控机床。
半闭环控制数控系统的调试比较方便,并且具有很好的稳定性。
目前大多将角度检测装置和
伺服电动机设计成一体,这样,使结构更加紧凑。
4 混合控制数控机床
将以上三类数控机床的特点结合起来,就形成了混合控制数控机床。
混合控制数控机床特别
适用于大型或重型数控机床,因为大型或重型数控机床需要较高的进给速度与相当高的精度,
其传动链惯量与力矩大,如果只采用全闭环控制,机床传动链和工作台全部置于控制闭环中,
闭环调试比较复杂。
混合控制系统又分为两种形式:
(1)开环补偿型。
它的基本控制选用步进电动机的开环伺服机构,另外附加一个校正电路。
用装在工作台的直线位移测量元件的反馈信号校正机械系统的误差。
(2)半闭环补偿型。
它是用半闭环控制方式取得高精度控制,再用装在工作台上的直线位
移测量元件实现全闭环修正,以获得高速度与高精度的统一。
其中 A 是速度测量元件(如测
速发电机),B 是角度测量元件,C 是直线位移测量元件。
二. 典型轴类零件的加工
1 零件图工艺分析
该零件表面由圆柱、圆锥、顺圆弧、逆圆弧及螺纹等表面组成。
其中多个直径尺寸有较严的
尺寸精度和表面粗糙度等要求,机器人;球面 Sφ50?
的尺寸公差还兼有控制该球面形状(线
轮廓)误差的作用。
尺寸标注完整,轮廓描述清楚。
零件材料为 45 钢,无热处理和硬度要
求。
通过上述分析,可采用以下几点工艺措施。
①对图样上给定的几个精度要求较高的尺寸,因其公差数值较小,故编程时不必取平均值,
而全部取其基本尺寸即可。
②在轮廓曲线上,有三处为圆弧,其中两处为既过象限又改变进给方向的轮廓曲线,因此在
加工时应进行机械间隙补偿,以保证轮廓曲线的准确性。
③为便于装夹,坯件左端应预先车出夹持部分(双点画线部分),右端面也应先粗车出并钻
好中心孔。
毛坯选 φ60?
棒料。
2 选择设备
根据被加工零件的外形和材料等条件,选用 TND360 数控车床。
3 确定零件的定位基准和
①定位基准 确定坯料轴线和左端大端面(设计基准)为定位基准。
②装夹方法 左端采用三爪自定心卡盘定心夹紧,右端采用活动顶尖支承的装夹方式。
4 确定加工顺序及进给路线
加工顺序按由粗到精、由近到远(由右到左)的原则确定。
即先从右到左进行粗车(留
0.25?
精车余量),然后从右到左进行精车,最后车削螺纹。
TND360 数控车床具有粗车循环和车螺纹循环功能,只要正确使用编程指令,机床数控系统
就会自动确定其进给路线,因此,该零件的粗车循环和车螺纹循环不需要人为确定其进给路
线(但精车的进给路线需要人为确定)。
该零件从右到左沿零件表面轮廓精车进给,如图 2
所示。
图 2 精车轮廓进给路线
5 刀具选择
①选用 φ5?
中心钻钻削中心孔。
②粗车及平端面选用 900 硬质合金右偏刀,为防止副后刀面与工件轮廓干涉(可用作图法检
验),副偏角不宜太小,选 κ=350。
③精车选用 900 硬质合金右偏刀,车螺纹选用硬质合金 600 外螺纹车刀,刀尖圆弧半径应小
于轮廓最小圆角半径,取 rε=0.15~0.2?
。
将所选定的刀具参数填入数控加工刀具卡片中(见表 1),以便编程和操作管理。
表 1 数控加工刀具卡片
产品名称或代号
×××
零件名称
典型轴
零件图号
×××
序号
刀具号
刀具规格名称
数量
加工表面
备注
1
T01
φ5 中心钻
1
钻 φ5 mm 中心孔
2
T02
硬质合金 900 外圆车刀
1
车端面及粗车轮廓
右偏刀
2
T03
硬质合金 900 外圆车刀
1
精车轮廓
右偏刀
3
T04
硬质合金 600 外螺纹车刀
1
车螺纹
编制
×××
审核
×××
批准
×××
共 页
第 页
6 切削用量选择
①背吃刀量的选择 轮廓粗车循环时选 ap=3 ?
,精车 ap=0.25?
;螺纹粗车时选 ap= 0.4 ?
,
逐刀减少,精车 ap=0.1?
。
②主轴转速的选择车直线和圆弧时,选粗车切削速度 vc=90m/min、精车切削速度
vc=120m/min,然后利用公式 vc=πdn/1000 计算主轴转速 n(粗车直径 D=60 ?
,精车工件直
径取平均值):
粗车 500r/min、精车 1200 r/min。
车螺纹时,参照式(5-1)计算主轴转速
n =320 r/min.
③进给速度的选择 选择粗车、精车每转进给量,再根据加工的实际情况确定粗车每转进给
量为 0.4?
/r,micro motor,精车每转进给量为 0.15?
/r,最后根据公式 vf = nf 计算粗车、
精车进给速度分别为 200 ?
/min 和 180 ?
/min。
综合前面分析的各项内容,并将其填入表 2 所示的数控加工工艺卡片。
此表是编制加工程序
的主要依据和操作人员配合数控程序进行数控加工的指导性文件。
主要内容包括:
工步顺序、
工步内容、各工步所用的刀具及切削用量等。
表 2 典型轴类零件数控加工工艺卡片
单位名称
×××
产品名称或代号
零件名称
零件图号
×××
典型轴
×××
工序号
程序编号
夹具名称
使用设备
车间
001
×××
三爪卡盘和活动顶尖
TND360 数控车床
工步号
工步内容
刀具号
刀具规格
/ mm
主轴转速
/r.m-1
进给速度
/mm.m-1
背吃刀量/ mm
备注
1
平端面
T02
25×25
500
手动
2
钻中心孔
T01
φ5
950
手动
3
粗车轮廓
T02
25×25
500
200
7 零件精加工工序
N0010 G50 X150.0 Z200.0;
N0020 G00 X60.0 Z1.0 S320 T0202 M08 M03;
N0030 G71 P0040 Q0050 U1.0 W0.5 D4.0 ;
N0040 G00 X24.0 S320;
G00 X24.0 S320;
G01 X29.85 W─2.925 F0.15;
W─16.15;
X26.0. W─1.925;
W─5;
X36.0 W─10.0;
W─10.0;
G02 X30.0 Z─9.0 I12.0 K─9.0;
G02 X40.0 Z─69.0 I20.0 K─15.0;
G03 X40.0 Z─99.0 I─20.0 K─15.0;
G02 X34.0 Z─108.0 I12.0 K─9.0;
G01 W─5.0;
X56.0 W─41.0;
N0050 W─11.0;
N0055 G00 X150.0 Z200.0 M05 T0200 M09;
N0056 T0303 M08 M03;
N0060 G70 P0040 Q0050;
N0070 G00 X150.0 Z200.0 M05 T0300 M09;
N0080 T0404 S320 M03 M08;
N0090 G00 X36.0 Z3.0;
N0100 G92 X29.05 Z─22.0 F3.0;
N0110 X29.05;
N0120 X28.75;
N0130 X28.45;
N0140 X28.25;
N0150 X28.05;
N0155 X28.05;
N0160 G00 X36.0 Z4.5;
N0170 G92 X29.45 Z─22.0 F3.0;
N0180 X29.05;
N0190 X28.75;
N0200 X28.45;
N0210 X28.25;
N0210 X28.05;
N0220 X28.05;
N0230 G00 X150.0 Z200.0 T0400 M05 M09;
N0240 M30;
我们不仅要学会做,机械传动系统,而且还要做得更好,注意和改正工作中的问题:
三.数控机床零件加工前的准备
近年来,为了适应市场需要,不少职业技术学校相继开设了数控技术方面的专业。
我校也于
去年购置了两台经济型数控车床和一台数控床身铣床并配置华兴数控仿真软件(机床数控系
统是南京华兴数控操作系统)以满足数控教学的要求。
通过几个学期的教学实践,深感要做
好数控机床操作,零件加工前的准备工作相当重要。
1、零件的加工程序编写及校验
在数控机床上加工零件,不管数控机床使用的是何种操作系统,必须要有与数控机床相适应
的数控加工程序。
首先,学生根据教师给出的零件图自行编制加工程序。
在编写加工程序的
时候先分析零件图,根据零件图的技术要求来分析加工工艺路线,确定加工步骤,合理选择
加工中每一道工序中要使用的刀具以及加工中的切削用量参数,并进行与数控加工程序相关
的数学处理。
在数学处理时会出现一些繁琐的坐标计算问题,为简化计算和缩短计算时间,
我们让学生在计算机模拟房内利用 AutoCAD 软件先绘制零件图,再利用 AutoCAD 软件的查询
命令予以解决并记下数据。
通过工艺分析与数学计算,再根据所确定的工艺路线与零件加工
步骤来编写程序。
在编写完数控加工程序之后,利用数控机床制造商提供的配套数控仿真教
学软件在计算机模拟室进行反复校验和仿真模拟,以检查程序的正确性,同时,对坐标数值、
进给量、刀补值等参数进一步处理,以适应实际加工需要。
为什么要这样做呢?
因为一般职业技术学校受经费等原因限制,数控机床数量较少,学生要
同时上数控机床校验不太可能,况且时间拖得长不利于教学。
另一方面,通过校验还可以使
学生在数控机床操作之前熟悉数控加工软件的使用方法以及熟悉数控机床的操作面板,为下
一步的数控机床操作打好基础。
最后,教师对每个学生编制的加工程序做全面细致的审核,
确定最终加工程序。
教师审核的内容主要是程序结构的合理性、走刀线路、主轴转速、进给
量、吃刀深度以及刀具的选择等,在审核的同时为学生提出建设性的修改意见,使学生知道
为什么要这样修改,不改会造成什么后果,程序确定之后,及时将程序记下以备操作。
2、加工材料及刀具、夹具的准备
程序准备仅仅是第一步,程序校验通过以后,接下来就是加工材料及刀具和夹具的准备。
这
一步工作做得如何,将直接影响到数控操作的最终效果和学生的学习兴趣,因此要认真做好。
目前,职业技术学校供数控机床操作教学用的材料主要是铝材、尼龙棒、钢材、石蜡、硬木
砧板等,选用的材料要能最大限度地满足数控操作教学的要求,同时要考虑经济性。
根据我
校的实际情况,我们选择铝和石蜡作为车床和铣床的加工材料。
刀具的选择则要根据被加工
材料的表面形状、材质等来选择,由于我们所选用的这些材料没有很高的硬度,故对刀具无
特别要求,选用普通刀具即可。
但在加工时由于零件的形状和技术要求不同,要选择不同类
型的刀具来加工,例如加工三角形螺纹要选择三角螺纹车刀,加工圆弧则要选择圆弧到或者
是尖刀来进行加工等,合理的选择加工刀具是加工好零件的基本保证。
夹具的选择比较简单,
如在数控车床上加工铝棒和石蜡棒,铝棒和石蜡棒直接由三爪自定心卡盘夹紧即可;而在铣
床上加工时,只要按普通铣床的要求,用压板将铝或石蜡板固定在工作台上或机用平口钳夹
紧就可以了,夹紧力的控制以在加工过程中工件不发生移动为宜。
但是在实际数控机床加工应用中,要综合考虑数控机床的技术要求、夹具的特点、工件材料
的性能、加工工序、切削用量以及其他相关因素来正确选用刀具和夹具,而在学习过程中要
求学生把石蜡材料看成是金属材料来进行加工,用加工金属材料的切削参数来加工石蜡材料,
在加工过程中合理分配加工余量,将粗加工和精加工进行区分。
通过以上做法,加工出的工
件符合图纸要求,效果良好,达到了数控机床操作的目的。
3、数控机床的调整与对刀
数控加工程序编写完和零件材料准备好以及选择了恰当的刀具后,要对数控机床进行调整、
润滑、检查等工作,确保数控机床的性能。
然后再进行对刀,使数控机床上每一把刀具的刀
位点在刀架转位后或换刀后,每把刀的刀位点的位置都重合在同一点。
在对刀完成后即进行
零件的试加工,以检验程序与对刀的精确性,如果试加工的零件的尺寸精度与形位公差不符
合图纸要求,则要进行刀具偏差的微量修调,然后再进行试加工,一直到所加工的零件符合
图纸要求。
通过试加工以后,就可以对该零件进行批量加工了。
一个数控加工的零件是否合
格,数控机床的对刀起到关键的作用,也就是说所加工的零件是否合格的基本保证是对刀要
准确。
4、安全教育工作
时时不忘安全,牢记安全第一的宗旨。
针对机械加工的特点,在操作前进行安全教育是重要
的。
要求学生严格遵守数控实验室管理制度、数控机床安全操作规程。
同时我们还以一些因
违反操作规程而造成伤亡的典型案例来教育学生,要求学生在操作过程中要严肃、认真和细
心,从而增强了学生的安全意识。
在上机前我们还将数控机床操作步骤以讲义的形式分发给
学生,要求学生细心领会和掌握,学生在数控机床操作过程中一定要按操作规程要求去做,
确保不发生过安全事故。
四. 我国数控系统的发展史
1.我国从 1958 年起,由一批科研院所,高等学校和少数机床厂起步进行数控系统的研制和
开发。
由于受到当时国产 mini gear box 元器件水平低,部门经济等的制约,未能取得较大
的发展。
2.在改革开放后,我国数控技术才逐步取得实质性的发展。
经过“六五"(81----85 年)的引
进国外技术,“七五”(86------90 年)的消化吸收和“八五”(91~一-95 年)国家组织的科技
攻关,才使得我国的数控技术有了质的飞跃,当时通过国家攻关验收和鉴定的产品包括北京
珠峰公司的中华 I 型,华中数控公司的华中 I 型和沈阳高档数控国家工程研究中心的蓝天 I
型,以及其他通过“国家机床质量监督测试中心”测试合格的国产数控系统如南京四开公司
的产品。
3.我国数控机床制造业在 80 年代曾有过高速发展的阶段,许多机床厂从传统产品实现向数
控化产品的转型。
但总的来说,技术水平不高,质量不佳,所以在 90 年代初期面临国家经
济由计划性经济向市场经济转移调整,经历了几年最困难的萧条时期,那时生产能力降到
50%,库存超过 4 个月。
从 1 9 9 5 年“九五”以后国家从扩大内需启动机床市场,加强限
制进口数控设备的审批,投资重点支持关键数控系统、设备、技术攻关,对数控设备生产起
到了很大的促进作用,尤其是在 1 9 9 9 年以后,国家向国防工业及关键民用工业部门投入
大量技改资金,使数控设备制造市场一派繁荣。
四
(2). 数控车的工艺和工装削
数控车床加工的工艺与普通车床的加工工艺类似,但由于数控车床是一次装夹,连续自动加
工完成所有车削工序,因而应注意以下几个方面。
1. 合理选择切削用量
对于高效率的金属切削加工来说,被加工材料、切削工具、切削条件是三大要素。
这些决定
着加工时间、刀具寿命和加工质量。
经济有效的加工方式必然是合理的选择了切削条件。
切削条件的三要素:
切削速度、进给量和切深直接引起刀具的损伤。
伴随着切削速度的提高,
刀尖温度会上升,会产生机械的、化学的、热的磨损。
切削速度提高 20%,刀具寿命会减少
1/2。
进给条件与刀具后面磨损关系在极小的范围内产生。
但进给量大,切削温度上升,后面磨损
大。
它比切削速度对刀具的影响小。
切深对刀具的影响虽然没有切削速度和进给量大,但在
微小切深切削时,被切削材料产生硬化层,同样会影响刀具的寿命。
用户要根据被加工的材料、硬度、切削状态、材料种类、进给量、切深等选择使用的切削速
度。
最适合的加工条件的选定是在这些因素的基础上选定的。
有规则的、稳定的磨损达到寿命才
是理想的条件。
然而,在实际作业中,刀具寿命的选择与刀具磨损、被加工尺寸变化、表面质量、切削噪声、
加工热量等有关。
在确定加工条件时,需要根据实际情况进行研究。
对于不锈钢和耐热合金
等难加工材料来说,可以采用冷却剂或选用刚性好的刀刃。
2. 合理选择刀具
1) 粗车时,要选强度高、耐用度好的刀具,以便满足粗车时大背吃刀量、大进给量的要求。
2) 精车时,要选精度高、耐用度好的刀具,以保证加工精度的要求。
3) 为减少换刀时间和方便对刀,应尽量采用机夹刀和机夹刀片。
3. 合理选择夹具
1) 尽量选用通用夹具装夹工件,避免采用专用夹具;
2) 零件定位基准重合,以减少定位误差。
4. 确定加工路线
加工路线是指数控机床加工过程中,刀具相对零件的运动轨迹和方向。
1) 应能保证加工精度和表面粗糙要求;
2) 应尽量缩短加工路线,减少刀具空行程时间。
5. 加工路线与加工余量的联系
目前,在数控车床还未达到普及使用的条件下,一般应把毛坯上过多的余量,特别是含有锻、
铸硬皮层的余量安排在普通车床上加工。
如必须用数控车床加工时,则需注意程序的灵活安
排。
6. 夹具安装要点
目前液压卡盘和液压夹紧油缸的连接是靠拉杆实现的,如图 1。
液压卡盘夹紧要点如下:
首
先用搬手卸下液压油缸上的螺帽,卸下拉管,并从主轴后端抽出,再用搬手卸下卡盘固定螺
钉,即可卸下卡盘。
四(3). 进行有效合理的车削加工
有效节省加工时间
Index 公司的 G200 车削中心集成化加工单元具有模块化、大功率双主轴、四轴联动的功能,
从而使加工时间进一步缩短。
与其他借助于工作轴进行装夹的概念相反,该产品运用集成智
能加工单元可以使工件自动装夹到位并进行加工。
换言之,自动装夹时,不会影响另一主轴
的加工,这一特点可以缩短大