MFMEA操作标准.docx
《MFMEA操作标准.docx》由会员分享,可在线阅读,更多相关《MFMEA操作标准.docx(14页珍藏版)》请在冰豆网上搜索。
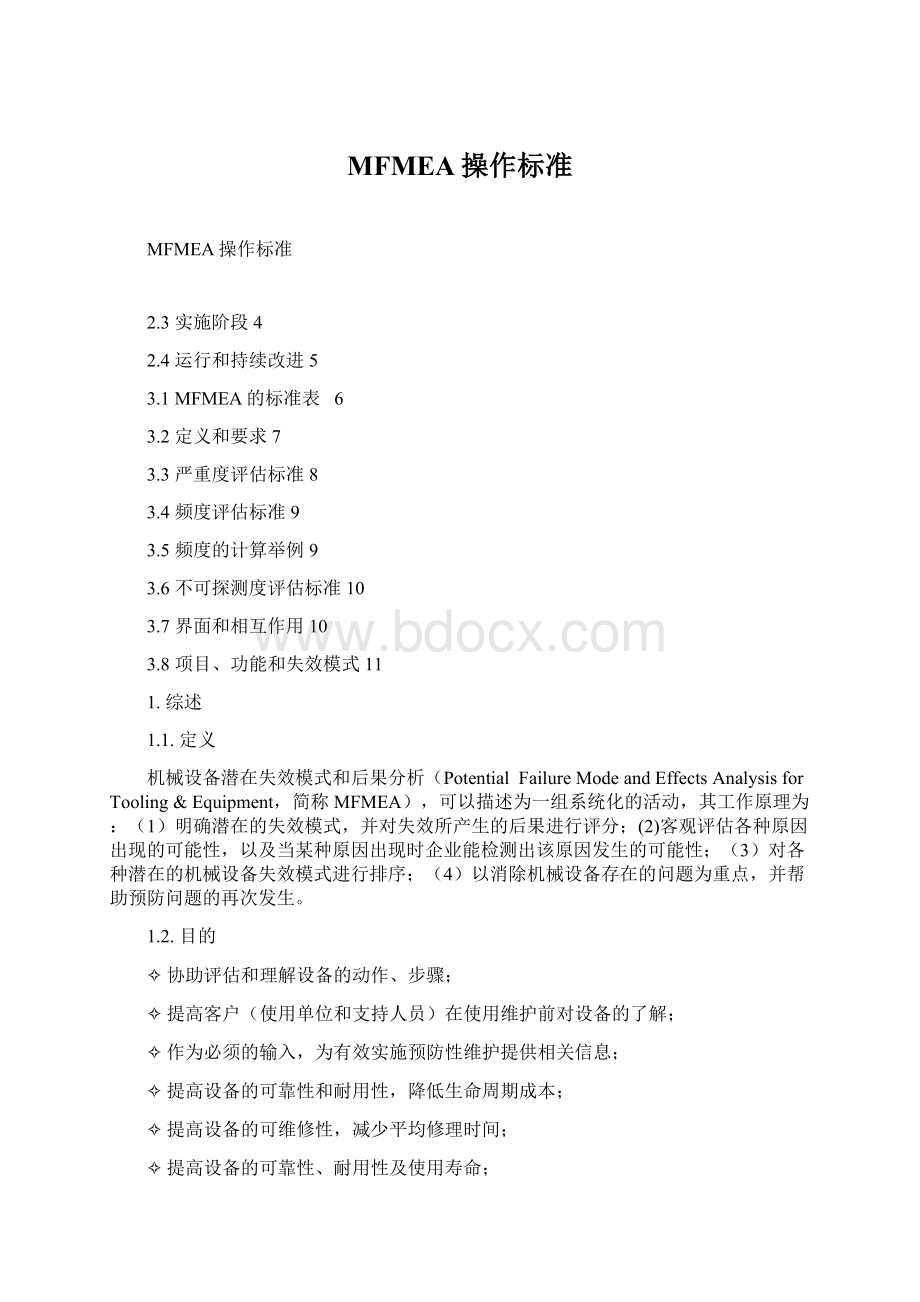
MFMEA操作标准
MFMEA操作标准
2.3实施阶段4
2.4运行和持续改进5
3.1MFMEA的标准表6
3.2定义和要求7
3.3严重度评估标准8
3.4频度评估标准9
3.5频度的计算举例9
3.6不可探测度评估标准10
3.7界面和相互作用10
3.8项目、功能和失效模式11
1.综述
1.1.定义
机械设备潜在失效模式和后果分析(PotentialFailureModeandEffectsAnalysisforTooling&Equipment,简称MFMEA),可以描述为一组系统化的活动,其工作原理为:
(1)明确潜在的失效模式,并对失效所产生的后果进行评分;
(2)客观评估各种原因出现的可能性,以及当某种原因出现时企业能检测出该原因发生的可能性;(3)对各种潜在的机械设备失效模式进行排序;(4)以消除机械设备存在的问题为重点,并帮助预防问题的再次发生。
1.2.目的
✧协助评估和理解设备的动作、步骤;
✧提高客户(使用单位和支持人员)在使用维护前对设备的了解;
✧作为必须的输入,为有效实施预防性维护提供相关信息;
✧提高设备的可靠性和耐用性,降低生命周期成本;
✧提高设备的可维修性,减少平均修理时间;
✧提高设备的可靠性、耐用性及使用寿命;
✧建立潜在失效模式的分级表,建立预防/纠正措施的优先系统。
1.3.适用范围
本操作标准适用于内饰制造工厂,有较多制造设备或检测设备或动力设备的工厂。
2.MFMEA实施步骤
2.1.启动阶段
2.1.1.成立MFMEA推进小组
各子公司选择需做MFMEA的设备,由设备经理牵头,主管工程师、设备维修人员参加,成立该设备MFMEA推进小组。
推进小组要求:
Ø一个系统化的行动团队;
Ø充分考虑生产环境对设备的影响;
Ø以设备的整体操作表现的优化为目标;
Ø基于故障树分析FTA;
Ø动态的文件(当机械设备开发和操作阶段中发生变化或获得新信息时,MFMEA应不断更新)。
2.1.2.制订MFMEA实施计划
Ø各子公司根据需做MFMEA的设备,制订本公司MFMEA实施计划。
Ø填写MFMEA实施汇总表,样表如下:
公司
MFMEA编号
设备编号
设备名称
设计责任
编制人
核心小组成员
起始日期
修订日期
修订内容
2.2.准备阶段
在开始MFMEA之前,推进小组应该准备如下可供参考的资料:
Ø设备的故障树FTA分析
Ø关键配件清单
Ø由于设备原因造成的缺陷记录,维修保养记录(如PM、EM工单等)
2.3.实施阶段
2.3.1MFMEA系统图
2.3.2MFMEA的编制
Ø根据已制订的设备故障树FTA制订相对应的MFMEA,编制《机械设备潜在失效模式和后果分析》表。
(见附录3.1)
Ø建议FTA中的部件功能做为MFMEA表中“项目/功能”的输入,“基本事件”、“省略事件”、“开关事件”、“转移事件”、“条件事件”等事件做为表中“潜在失效模式”的输入。
Ø《机械设备潜在失效模式和后果分析》表中有关定义和要求(见附录3.2)
Ø严重度评估标准(见附录3.3)
Ø频度评估标准(见附录3.4)
Ø频度的计算举例(见附录3.5)
Ø不可探测度评估标准(见附录3.6)
2.3.3措施所产生结果RPN的重估
明确纠正措施后,估计并记录纠正后的频度、严重度和不易探测度数,计算并记录纠正后的RPN值。
如果有必要考虑进一步的措施,还应重复分析过程,并应该一直关注持续改进。
根据纠正后的RPN值,测算出部件功能总的RPN,提交FTA推进小组输入FTA报告。
2.3.4建议措施的落实
必须及时对故障树分析的结果进行评价、总结,提出改进建议,并注重综合利用各种故障分析的资料,提出预防故障与消除故障的对策。
根据MFMEA表中的建议措施在MAXIMO系统中编制EM、PM工单,同时在MAXIMO系统中输出“故障代码”(FailureCode)。
2.4.运行和持续改进
设备维护工程师负责确保所有建议措施完成施行或充分提出。
MFMEA是一种动态文档,它总能反映最新设备设计水平与维修水平,应该定期对工单执行效果进行分析论证,不断完善MFMEA。
当对已有MFMEA内容进行更新时,应填写实施汇总表对更新内容予以简单描述。
以保证MFMEA实施的连续性和可追溯性。
装备中心根据MFMEA形成设备技术标准。
3.附录
3.1MFMEA的标准表
3.2定义和要求:
序号
定义和要求
1.FMEA编号
跟踪用的MFMEA文件编号
2.项目
填入所分析的系统,子系统或组件的名称,如机器人是底盘焊接系统的分系统,焊枪、密封枪、机械爪则是具体的组件
3.设计责任
设备供应商名称
4.编制者
姓名,部门,电话号码
5.工序/工厂
该项目使用范围和影响区域
6.关键日期
MFMEA中所有项目预定完成的日期
7.FMEA日期
初始MFMEA日期和当前版本日期
8.核心小组
有权确定和/或执行任务的责任部门和个人姓名、部门、电话
9.项目/功能
简单描述被分析的过程或功能,小组应考虑动作、材料、过程、环境、安全。
每一步的要求、目的、功能。
当某一步包括有不同的功能和不同的潜在失效模式时,应尽可能分开,例如:
ü按每分钟X立方米的速度抽密封剂到面板
ü按每分钟不小于X加仑的速度抽冷冻剂
ü在Y秒内达到XN-m的扭矩
ü在Y秒内温度上升X度并保持Z秒
ü在Y秒内移动产品X米
……
10.潜在失效模式
过程可能发生的不满足过程要求和/或设计的功能,可能对本道或后道产生的影响列出每一个潜在失效模式—以部件、分系统、主系统为主线.
*什么原因导致设备超出工程规范?
*什么原因导致不满足顾客(内、外部)的要求?
典型的失效模式有:
弯/断/磨损/破/翘/短路/污/粘/开路/接地……
11.潜在失效后果
指失效模式对设备系统、分系统或部件的影响,任何对上、下道工序的影响都应考虑到。
典型的失效后果:
机器损坏;节拍时间增加;产出减少;性能降低;扭矩过小;工作不连贯;额外操作;噪声;功能部分/全部失效;震动;重复性差;危及操作人员……
12.严重度(S)
对失效模式导致的后果的严重程度评价指标,只有改变机器设备的设计才能降低严重度。
严重度评估分为1~10级----对1级严重度不必再分析
13.分级
本栏目是用来标示那些高严重度或其他的顾客要求(或对产品的KPC、KCC有影响)
14.潜在失效起因/机理
指失效是如何发生的,以可以纠正或控制的原则来描述。
应避免使用含糊不清的词语(如:
操作者错误,机器工作不正常)
没有充分润滑、腐蚀、定位磨损/损坏、材料疲劳失效、工具磨损、污染……
15.频度(O)
指具体的失效起因/机理发生的频率。
通过设计更改来降低“O”是首选的方法。
可以分1级和10级来估计频度的大小。
16.当前设备控制
是对尽可能防止失效模式的发生,或者探测将发生的失效模式的控制的描述。
两类控制方法:
1)预防----防止潜在的失效原因/机理的发生,或减小其发生率。
2)探测----通过分析或物理的方法探测潜在的失效原因/机理。
较好的做法是第1)种控制方法,例如:
对于“皮带断”这种失效模式,有两种方法可以进行控制
探测:
用传感器探测到断裂并声、光报警。
预防:
用带反馈系统的传感器,能通过自动调节滑轮系统来不断调节松紧,防止皮带断掉或减少断裂的可能。
18.风险顺序数(RPN)
严重度数(S)=,频度数(O)=,不易探测度数(D)=
RPN=(S)×(O)×(D)=1~1000
19.建议措施
对高“S”,高“RPN”项目要采取措施降低,
高严重度(9或10)项目,不管RPN值多大,必须予以特别关注,
建议措施要简单明了、有效,
只有设计更改才能降低“S”,通过设计来减少、控制失效原因。
建议按S-O-D的顺序来采取行动。
推荐采取的行动是降低风险、
增加顾客满意度、提高设备的可靠性、可维护性、耐久性。
通过控制/检查来降低“D”不是最好的方法,因为这些措施对S和O没有影响
20.职责和计划完成日期
负责建议措施的组织和个人和计划完成日期
21.采取的措施
当实施一项措施后,简要记载具体的执行情况,并记下生效日期
22.纠正后的RPN
当明确纠正措施后,估算并记录纠正后的严重度、频度和不易探测度数,计算并记录纠正后的RPN值。
如果没有措施,则不记录。
3.3严重度评估标准(推荐)
后果
标准:
后果的严重性
级别
危险—没有报警
后果非常严重—会影响到操作工、生产或维修人员的安全,或违反政府的法律法规,并没有报警
10
危险—有报警
后果非常严重—会影响到操作工、生产或维修人员的安全,或违反政府的法律法规,但有报警
9
非常严重
停工超过8小时或者生产有缺陷的零件超过4小时
8
严重
停工在4到8小时之间或者生产有缺陷的零件在2到4小时之间
7
中等
停工在1到4小时之间或生产有缺陷的零件在1到2小时之间
6
轻
停工在半小时到1小时之间或生产有缺陷的零件在1小时之内
5
非常轻
停工在到10到30分钟之间但是没有生产有缺陷的零件
4
轻微
停工在到10分钟之内,但是没有生产有缺陷的零件
3
非常轻微
过程参数的变化幅度超过了规定区间,需要在生产期间进行调整或通过其它过程控制。
但是没有停工,也没有生产有缺陷的零件。
2
没有后果
过程参数的变化幅度在规定区间,调整或其它过程控制可以在正常的保养期间进行。
1
3.4频度评估标准(推荐)
标准:
按时间
或
者
标准:
按操作周期
或
者
标准:
基于用户需求时间的可靠性
级别
1个/1小时
1个/90周期
R(t)<1%:
MTBF大约是用户需求时间的10%
10
1个/8小时
1个/900个周期
R(t)<5%:
MTBF大约是用户需求时间的30%
9
1个/24小时
1个/36000周期
R(t)<20%:
MTBF大约是用户需求时间的60%
8
1个/80小时
1个/90000周期
R(t)<37%:
MTBF等于用户的需求时间
7
1个/350小时
1个/180000周期
R(t)<78%:
MTBF是用户需求时间的2倍以上
6
1个/1000小时
1个270000周期
R(t)<78%:
MTBF是用户需求时间的4倍以上
5
1个/2500小时
1个/360000周期
R(t)<85%:
MTBF是用户需求时间的6倍以上
4
1个/5000小时
1个/540000周期
R(t)<90%:
MTBF是用户需求时间的10倍以上
3
1个/10000小时
1个/900000周期
R(t)<95%:
MTBF是用户需求时间的20倍以上
2
1个/25000小时
1个/(大于900000)周期
R(t)<98%:
MTBF是用户需求时间的50倍以上
1
备注:
以上可靠性计算基于如下假设:
设备有恒定故障率且故障可被修复。
参见:
关于样本发生概率的计算表
3.5频度的计算举例
失效率
MTBF
t(用户时间)
R(t)(t)
说明
1/1
1
8
0.03%
MTBF大约为用户需求时间的10%
1/8
8
24
4.98%
MTBF大约为用户需求时间的30%
1/24
24
40
18.89%
MTBF大约为用户需求时间的60%
1/80
80
80
36.79%
MTBF等于用户需求时间
1/350
350
200
60.65%
MTBF两倍于用户需求时间
1/1000
1000
250
77.88%
MTBF四倍于用户需求时间
1/2500
2500
400
85.21%
MTBF六倍于用户需求时间
1/5000
5000
500
90.48%
MTBF十倍于用户需求时间
1/10000
10000
500
95.12%
MTBF二十倍于用户需求时间
1/25000
25000
500
98.02%
MTBF五十倍于用户需求时间
R(t)=e-t/mtbf
用户需求时间:
用户根据实际情况制订的两次计划性维修之间的无故障的设备使用时间
3.6不可探测度评估标准
探测度
标准:
通过设计控制进行检测的可能性
级别
几乎不可能
设计或设备控制不能检测到潜在的(缺陷)源和由此发生的失效,或者没有设计或设备控制。
10
非常不可能
设计或设备控制检测到潜在的(缺陷)源和由此发生的失效的可能性非常小。
9
很不可能
设计或设备控制检测到潜在的(缺陷)源和由此发生的缺陷的可能性很小,设备控制可能会提示发生失效。
8
很低
设计和设备控制不能防止失效的发生。
失效发生后,设备控制能将失效隔离。
7
低
设计或设备控制检测到潜在的(缺陷)源和由此发生的失效的可能性小,设备控制会提示即将发生失效。
6
中等
设计控制检测到潜在的(缺陷)源和由此发生的失效的可能性中等,设备控制会防止即将发生的失效。
5
较高
设计控制检测到潜在的(缺陷)源和由此发生的失效的可能性较高,设备控制会防止即将发生的失效。
4
高
设计控制检测到潜在的(缺陷)源和由此发生的失效的可能性高,设备控制会防止即将发生的失效并隔离失效原因。
3
非常高
设计控制检测到潜在的(缺陷)源和由此发生的失效的可能性非常高,不一定需要设备控制。
2
几乎肯定
设计控制几乎肯定会检测到潜在的(缺陷)源和由此发生的缺陷,不需要设备控制。
1
3.7界面和相互作用
3.8项目、功能和失效模式