设施布置设计概述.docx
《设施布置设计概述.docx》由会员分享,可在线阅读,更多相关《设施布置设计概述.docx(22页珍藏版)》请在冰豆网上搜索。
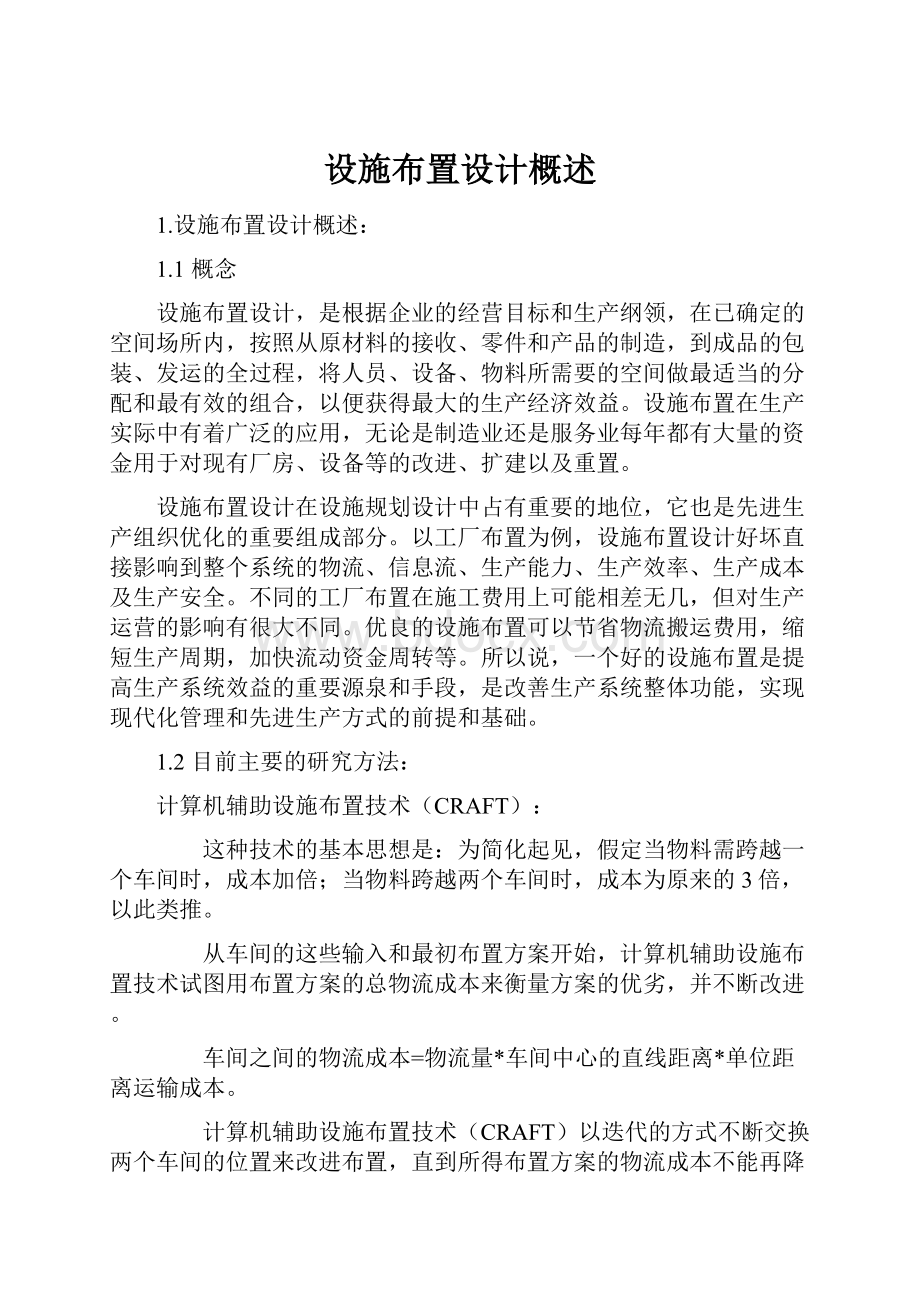
设施布置设计概述
1.设施布置设计概述:
1.1概念
设施布置设计,是根据企业的经营目标和生产纲领,在已确定的空间场所内,按照从原材料的接收、零件和产品的制造,到成品的包装、发运的全过程,将人员、设备、物料所需要的空间做最适当的分配和最有效的组合,以便获得最大的生产经济效益。
设施布置在生产实际中有着广泛的应用,无论是制造业还是服务业每年都有大量的资金用于对现有厂房、设备等的改进、扩建以及重置。
设施布置设计在设施规划设计中占有重要的地位,它也是先进生产组织优化的重要组成部分。
以工厂布置为例,设施布置设计好坏直接影响到整个系统的物流、信息流、生产能力、生产效率、生产成本及生产安全。
不同的工厂布置在施工费用上可能相差无几,但对生产运营的影响有很大不同。
优良的设施布置可以节省物流搬运费用,缩短生产周期,加快流动资金周转等。
所以说,一个好的设施布置是提高生产系统效益的重要源泉和手段,是改善生产系统整体功能,实现现代化管理和先进生产方式的前提和基础。
1.2目前主要的研究方法:
计算机辅助设施布置技术(CRAFT):
这种技术的基本思想是:
为简化起见,假定当物料需跨越一个车间时,成本加倍;当物料跨越两个车间时,成本为原来的3倍,以此类推。
从车间的这些输入和最初布置方案开始,计算机辅助设施布置技术试图用布置方案的总物流成本来衡量方案的优劣,并不断改进。
车间之间的物流成本=物流量*车间中心的直线距离*单位距离运输成本。
计算机辅助设施布置技术(CRAFT)以迭代的方式不断交换两个车间的位置来改进布置,直到所得布置方案的物流成本不能再降低为止。
也就是说,计算机辅助设施布置技术要不断计算两个车间位置交换后对总成本的影响;如果总成本降低,则交换位置。
是通过相应的CRAFT软件来进行的。
主要缺陷:
虽然以搬运费用最小或相互关系密切度最大为目标,以产生一个好的布局方案,但是它在达到满意方案之前的选择过程未充分考虑其他方案,并对初始布置敏感。
1.3生产系统设施布置设计的目标:
(1)最有效地利用空间。
要使场地利用达到适当的建筑占地系数(建筑物、构筑物占地面积与场地总面积的比率),使建筑物内部设备的占有空间和单位制品的占有空间较小。
(2)物料搬运费用最小。
要便于物料的输入,使产品、废料等物料的运输线尽量短捷,并尽量避免运输的往返和交叉。
(3)适应组织结构的合理化和管理的方便,使有密切关系或性质相近的作业单位布置在一个区域并就近布置,甚至合并在同一个建筑物内。
(4)为职工提供方便、安全、舒适的作业环境。
使之合乎生理、心理的要求,为提高生产效率和保证职工身心健康创造条件。
这些目标实际上不可能都达到最佳,有时甚至相互矛盾,要用恰当的指标对每一个方案进行综合评价,达到总体目标最佳。
1.4设施布置基本类型
按设施的作用布置:
(1)存储:
新仓库、储藏室按其存储作用布置。
(2)销售布置:
从销售的作用去布置,如商场、商店。
(3)生产布置:
按工厂产品需要布置。
(4)住宅布置:
按人居住的需要布置。
按企业流程布置:
(1)工艺原则布置(ProcessLayout)
工艺原则布置也称机群式布置。
这种布置形式的特点就是把同种类型的设备和人员集中布置在一个地方,便于调整设备和人员,容易适应产品的变化,从而使生产系统的柔性大大增加,但是当工件需要经过多种设备进行加工时,工件就不得不往返于各工序之间,增加了产品搬运次数与搬运距离,常常带来物料交叉搬运与逆向流动的问题,这种布置形式通常适用于单件生产及多品种小批量生产模式。
(2)产品原则布置(ProductLayout)。
产品原则布置也称流水线布置或对象原则布置。
当产品品种很少而生产数量又很大时,应按产品的加工工艺过程顺序配置设备,形成流水线,这是大量生产中典型的设备布置方式。
由于产品原则布置是按产品的加工、装配工艺过程顺序配置各道工序所需设备、人员及物料的,因此能最大限度地满足固定品种的产品的生产过程对空间和时间的客观要求,生产效率非常高,单件产品生产成本低,但成本适应性即柔性差,适用于少品种大量生产。
(3)成组原则布置(GroupLayout)。
成组原则布置又称混合原则布置。
在产品品种较多,每种产品的产量又是中等程度的情况下,将工件按其外形与加工工艺的相似性进行编码分组,同组零件用相似的工艺过程进行加工,同时将设备成组布置,即把适用频率高的机器群按工艺过程顺序布置组合成成组制造单元,整个生产系统由数个成组制造单元构成,这种布置方式既有流水线的生产效率又有机群式布置的柔性,可以提高设备开工率、减少物流量及加工时间,成组布置适用于多品种、小批量的生产类型。
现代成组原则布置包括柔性制造单元(FMC)和柔性制造系统(FMS)两种形式。
(4)固定式布置(FixedProductionLayout)。
产品固定式布置适用于大型设备如飞机、轮船的制造过程,产品固定在一个固定位置上,所需设备、人员、物料均围绕产品布置,这种布置方式在一般场合很少应用。
综合布置:
(1)按作用和流程组合在一起布置。
比如一个工厂,它的车间按产品原则布置,而销售部门按销售原则布置。
(2)工程项目布置:
根据一个工程做一次性布置,但一次性布置中也是综合性的。
由上可知,产品品种的多少、产量的高低直接决定了设备布置的形式,因此,只有对产品——产量关系进行深入分析,才能产生恰当的设备布置形式。
1.5设施布置类型选择的影响因素
在设施布置中,到底选用哪一种布置类型(工艺对象专业化布置、产品对象专业化布置、混合布置、固定布置),除了生产组织方式战略以及产品加工特性以外(这是显而易见的),还应该考虑其它一些因素。
也就是说,一个好的设施布置方案,应该能够使设备、人员的效益和效率尽可能好。
为此,还应该考虑以下一些因素:
(1)所需投资。
设施布置将在很大程度上决定所要占用的空间、所需设备以及库存水平,从而决定投资规模。
如果产品的产量不大,设施布置人员可能愿意采用工艺对象专业化布置,这样可节省空间,提高设备的利用率,但可能会带来较高的库存水平,因此这其中有一个平衡的问题。
如果是对现有的设施布置进行改造,更要考虑所需投资与可能获得的效益相比是否合算。
(2)物料搬运。
在考虑各个经济活动单元之间的相对位置时,物流的合理性是一个主要考虑因素,即应该使量比较大的物流的距离尽可能短,使相互之间搬运量较大的单元尽量靠近,以便使搬运费用尽可能小,搬运时间尽可能短。
曾经有人做过统计,在一个企业中,从原材料投入直至产品产出的整个生产周期中,物料只有15%左右的时间是处在加工工位上,其余都处于搬运过程中或库存中,搬运成本可达总生产成本25%-50%。
由此可见,物料搬运是生产运作管理中相当重要的一个问题。
而一个好的设施布置,可使搬运成本大为减少。
(3)柔性。
设施布置的柔性一方面是指对生产的变化有一定的适应性,即使变化发生后也仍然能达到令人满意的效果;另一方面是指能够容易地改变设施布置,以适应变化了的情况。
因此在一开始设计布置方案时,就需要对未来进行充分预测;再一方面是,从一开始就应该考虑到以后的可改造性。
(4)其它。
其它还需要着重考虑的因素有:
劳动生产率,为此在进行设施布置时要注意不同单元操作的难易程度悬殊不宜过大;设备维修,注意不要使空间太狭小,这样会导致设备之间的相对位置不好;工作环境,如温度、噪音水平、安全性等,均受设施布置的影响;人的情绪,要考虑到是否可使工作人员相互之间能有所交流,是否给予不同单元的人员相同的责任与机会,使他们感到公平等。
1.6生产系统设施布置的基本要素
为了完成生产系统设施布置中的区域布置和生产设备布置,我们需从产品及产量出发,首先对产品组成进行分析,确定各零部件生产类型,制定出各个零部件的加工、装配工艺流程,根据工艺流程的各阶段的特点,划分出生产车间,并根据生产需要,设置必要的职能管理部门及附属的生产与生活服务部门,然后由设施布置设计人员来完成生产系统设施布置。
一般情况下把产品、产量、生产路线、辅助服务部门及生产时间安排作为设施布置给定的基本要素。
(1)产品P:
指待布置工厂将生产的商品、原材料或者加工的零件和成品等。
这些资料由生产纲领和产品设计提供,包括项目、品种类型、材料、产品特征等。
它影响着生产系统的组成及其各作业单位间相互关系、生产设备的类型、物料搬运方式等方面。
(2)产量Q:
指所生产的产品的数量,由生产纲领和产品设计方案决定,可以用件数、重量、体积等来表示。
它影响着生产系统的规模、设备的数量、运输量、建筑物面积大小等方面。
(3)生产路线R:
为了完成产品的加工,必须制定加工工艺流程,形成生产路线,可以用工艺过程表(卡)、工艺过程图、设备表等表示。
它影响着各作业单位之间的联系、物料搬运路线、仓库及堆放地的位置等方面。
(4)辅助服务部门S:
在实施系统布置工作以前,必须就生产系统的组成情况有一个总体的规划,可以大体上分为生产车间、职能管理部门、辅助生产部门、生活服务部门及仓储部门等。
我们可以把除生产车间以外的所有作业单位统称为辅助服务部门S,包括工具、维修、动力、收货、发运、铁路专用路线、办公室、食堂等。
由这些作业单位构成生产系统的生产支持系统部分,在某种意义上加强了生产能力。
有时辅助服务部门的占地总面积接近甚至大于生产车间所占面积,所以布置设计时应给予足够的重视。
(5)时间T:
指在什么时候、用多少时间生产出产品,包括各工序的操作时间、更换批量的次数。
本例是用工艺原则实现车间设备的详细布置,以车间之间总的物流费用最小为目标函数,建立车间设备布置的数学模型,并计算出最优方案。
2.问题描述
试对某液压元件厂的七个车间进行规划,使其各部门之间的物料搬运费最少。
各厂房、车间之间的布置见下图所示。
各车间和厂房之间的距离均视为相等,车间大小认为相同。
假设:
各车间之间用场内自制标准尺寸的料箱装物料,用电瓶车在各车间之间运输,电瓶车每次运输一箱物料(这样构成了一个“单位货物”)。
相邻车间之间单位货物的运输成本为1元,每隔一个车间增加1元。
第一年所需的运输量在表1中列出。
对角线之间允许移动,所以车间A和D,B和C可以被视为相邻车间。
表1:
各车间之间的年搬运量
进行工厂总平面布置需考虑的因素有:
1各作业区域的形状为矩形,且彼此大小认为相同。
2综合考虑物流因素和非物流因素。
3位置有特殊要求的作业区域的布置等。
3.建立目标函数
设:
为车间位置x与车间位置y之间单位货物的运输成本。
本题中各车间之间的物流运输费用矩阵表:
为车间
与车间
之间一年所需的物料运输量(如果车间之间有不同的运输路径,则选择最短的一条路径)。
本题中各车间间一年所需的物流运输量矩阵表:
设:
为车间被布置到车间布置图中的对应位置。
例如:
表示车间i被分配到车间布置图中的A位置。
即
表示为车间
与车间
之间单位货物的运输成本。
例如:
车间1被分配到车间布置图中的A位置,车间2被分配到车间布置图中的B位置,即
,则
=1,也就是说此时车间1与车间2之间单位货物的运输成本为1元;车间1,2之间的一年的物流量为10000次,即
;所需物流费用:
元。
物流运输费用等于每两车间之间的运量与其基本运费相乘所得结果的总和。
所以目标函数
可以写成:
显然目标函数就是要求使车间间总物料搬运费用最小的最优车间排列方案。
4.用目标函数计算初始方案
方案1:
车间布置如下图示:
即定义:
L
(1)=A,L
(2)=B,L(3)=C,L(4)=D,L(5)=E,L(6)=F,L(7)=G;
各车间之间物流的成本矩阵为(单位:
元)为:
1
2
3
4
5
6
7
1材料及成品库
10000
6250
18750
5000
12500
3000
2机加工缸件车间
100
1200
0
165000
9375
3机加工阀件车间
1850
250
1500
35000
4总装配车间
2500
120
376
5机加工泵件车间
160
17500
6热处理车间
60
7铸造车间
目标函数为:
=
=160491元
即按图示方案排列车间的总物流成本为160491元
方案2:
车间布置如下图所示:
即定义L
(1)=G,L
(2)=B,L(3)=C,L(4)=D,L(5)=E,L(6)=F,L(7)=A;
各车间之间物流的成本矩阵为(单位:
元)为:
1
2
3
4
5
6
7
1材料及成品库
3000
12500
37500
5000
12500
3000
2机加工缸件车间
1000
1200
0
17500
3125
3机加工阀件车间
1850
250
1500
17500
4总装配车间
2500
120
376
5机加工泵件车间
160
35500
6热处理车间
120
7铸造车间
它为我们提供了以下信息:
车间1和车间2之间的年物流运输管理费用是30000元(3元x10000次搬运),对角线上的车间1与车间4之间的年物流运输管理费用是37500元(2元x18750次搬运),车间1和车间7之间的年物流运输管理费用是3000元(3元x1000次搬运)。
目标函数为:
=
=181673元
即按图示方案排列车间的总物流成本为181673元
可以看出,第二种方案的成本高于第一种方案的成本,即这两个方案中按照第一个方案为较优方案。
但是,这仅仅交换了两个车间的位置。
实际上对于一个有7个车间需要布置的工厂来说,有7!
(即5040)种可能的布置。
5.程序实现
根据数学模型的目标函数,采用MicrosoftVisualC#.NET程序语言进行编程。
Visual C#.NET程序设计语言是一种类型安全且面向对象的现代编程语言,它由C和C++演变而来,为生成运行在.NET框架上的、广泛的企业级应用程序而设计。
程序代码如下:
usingSystem;
usingSystem.Drawing;
usingSystem.Collections;
usingSystem.ComponentModel;
usingSystem.Windows.Forms;
usingSystem.Data;
usingSystem.Text;
namespaceWindowsApplication2
{
///
///Form1的摘要说明。
///
publicclassForm1:
System.Windows.Forms.Form
{
///
///必需的设计器变量。
///
privateSystem.ComponentModel.Containercomponents=null;
publicForm1()
{//Windows窗体设计器支持所必需的
InitializeComponent();
//TODO:
在InitializeComponent调用后添加任何构造函数代码
}
///
///清理所有正在使用的资源。
///
protectedoverridevoidDispose(booldisposing)
{
if(disposing)
{
if(components!
=null)
{
components.Dispose();
}
}
base.Dispose(disposing);
}
staticvoidMain(string[]args)
{
///cost[7,7]为7个位置的费用矩阵
int[,]cost=newint[,]{{0,1,1,1,2,2,3},
{1,0,1,1,2,2,3},
{1,1,0,1,1,1,2},
{1,1,1,0,1,1,2},
{2,2,1,1,0,1,1},
{3,2,1,1,1,0,1},
{3,3,2,2,1,1,0},
};//amout[7,7]表示车间之间运输量矩阵
double[,]amout=newdouble[,]{{0,10000,6250,18750,5000,12500,1000},
{0,0,100,1200,0,8750,3125},
{0,0,0,1850,250,1500,17500},
{0,0,0,0,2500,120,188},
{0,0,0,0,0,160,17500},
{0,0,0,0,0,0,60},
{0,0,0,0,0,0,0}
};//Solution[5040]用于存储7!
个排布方法
string[]Solution=newstring[5040];
inti=0;intt=0;
doubletotalCost=double.MaxValue;
intbestSolution=0;
int[]temp=newint[7];
for(inti1=0;i1<7;i1++)
{temp[i1]=0;
for(inti2=0;i2<7;i2++)
{if(i2!
=i1)
{temp[i2]=1;
for(inti3=0;i3<7;i3++)
if(i3!
=i2&&i3!
=i1)
{temp[i3]=2;
for(inti4=0;i4<7;i4++)
if(i4!
=i3&&i4!
=i2&&i4!
=i1)
{temp[i4]=3;
for(inti5=0;i5<7;i5++)
if(i5!
=i4&&i5!
=i3&&i5!
=i2&&i5!
=i1)
{temp[i5]=4;
for(inti6=0;i6<7;i6++)
if(i6!
=i5&&i6!
=i4&&i6!
=i3&&i6!
=i2&&i6!
=i1)
{temp[i6]=5;
for(inti7=0;i7<7;i7++)
if(i7!
=i6&&i7!
=i5&&i7!
=i4&&i7!
=i3&&i7!
=i2&&i7!
=i1)
{temp[i7]=6;
doublesolutionCost=0;
int[]path=newint[]{i1,i2,i3,i4,i5,i6,i7};
for(intpathI=0;pathI<7;pathI++)
{for(intnext=path[pathI]+1;next<7;next++)
{
solutionCost+=cost[pathI,temp[next]]*amout[path[pathI],next];
}
}
t=i;
Solution[t]=(i1+1)+""+(i2+1)+""+(i3+1)+""+(i4+1)+""+(i5+1)+""+(i6+1)+""+(i7+1);
Console.Write("排列方案:
");
Console.Write(Solution[t]);Console.Write("费用:
");Console.WriteLine(solutionCost);if(solutionCost=0){totalCost=solutionCost;bestSolution=i;}
Solution[i]=(i1+1)+""+(i2+1)+""+(i3+1)+""+(i4+1)+""+(i5+1)+""+(i6+1)+""+(i7+1);
i++;
}
}
}
}
}
}
}
}
Console.WriteLine("最优排布方法为:
");
Console.WriteLine(Solution[bestSolution]);
Console.WriteLine("对应的最低消费为:
");
Console.WriteLine(totalCost);
Console.ReadLine();
}
}
}
程序运行结果:
全部5040种排布方案及其费用。
部分排布方案及其费用:
排布方案
费用(元)
排布方案
费用(元)
排布方案
费用(元)
排布方案
费用(元)
2614357
117621
7235416
140971
6547132
150878
2357416
158323
2614537
117621
7253416
140971
6574132
150878
2375416
158323
2641357
117621
2635174
140978
6417235
150923
2346715
158338
2641537
117621
2653174
140978
6471235
150923
2364715
158338
6214357
117781
5367412
140978
2635714
150978
5267341
158353
6241357
117781
5376412
140978
26