塑料提桶模具设计方案及其型腔仿真加工.docx
《塑料提桶模具设计方案及其型腔仿真加工.docx》由会员分享,可在线阅读,更多相关《塑料提桶模具设计方案及其型腔仿真加工.docx(15页珍藏版)》请在冰豆网上搜索。
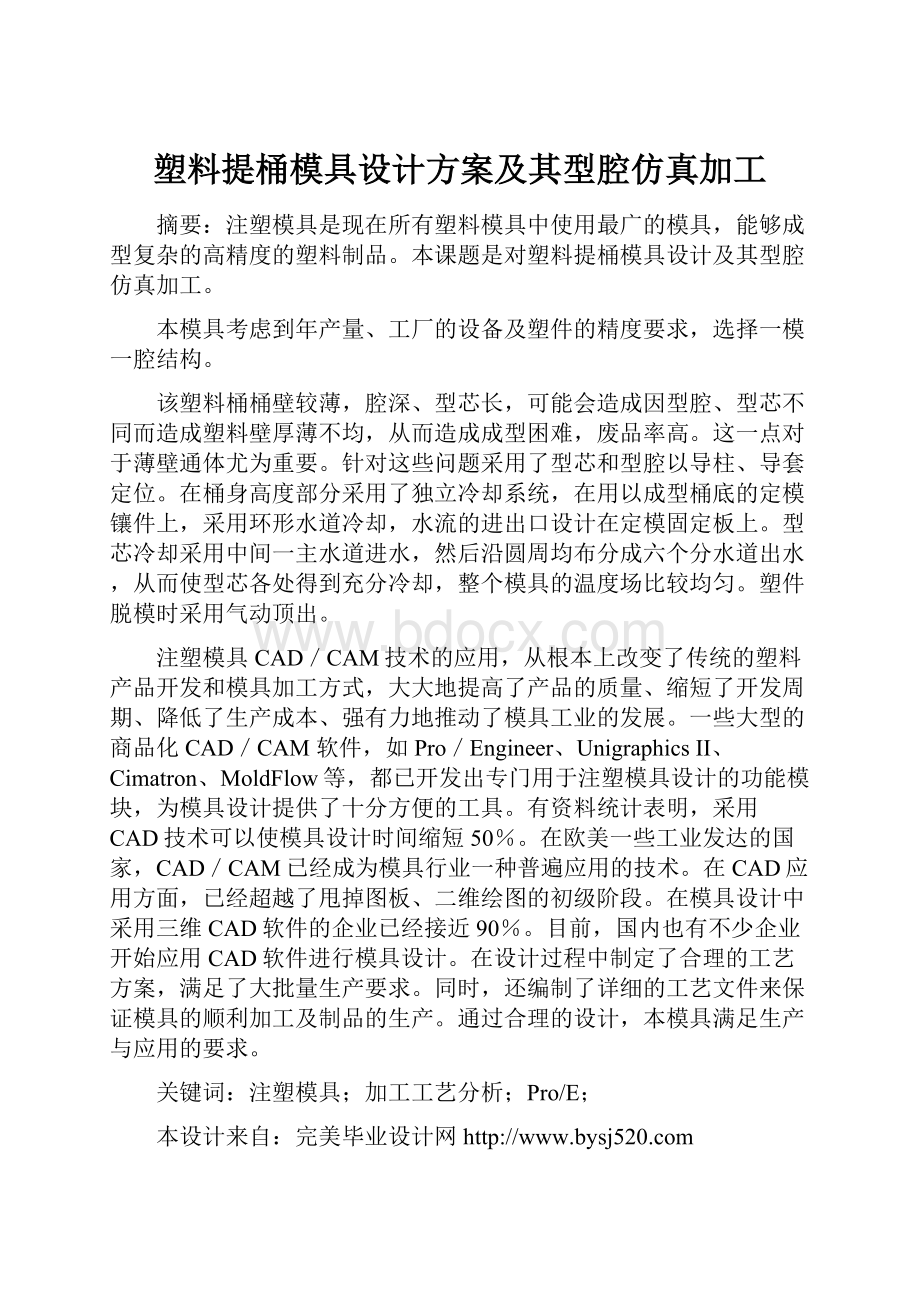
塑料提桶模具设计方案及其型腔仿真加工
摘要:
注塑模具是现在所有塑料模具中使用最广的模具,能够成型复杂的高精度的塑料制品。
本课题是对塑料提桶模具设计及其型腔仿真加工。
本模具考虑到年产量、工厂的设备及塑件的精度要求,选择一模一腔结构。
该塑料桶桶壁较薄,腔深、型芯长,可能会造成因型腔、型芯不同而造成塑料壁厚薄不均,从而造成成型困难,废品率高。
这一点对于薄壁通体尤为重要。
针对这些问题采用了型芯和型腔以导柱、导套定位。
在桶身高度部分采用了独立冷却系统,在用以成型桶底的定模镶件上,采用环形水道冷却,水流的进出口设计在定模固定板上。
型芯冷却采用中间一主水道进水,然后沿圆周均布分成六个分水道出水,从而使型芯各处得到充分冷却,整个模具的温度场比较均匀。
塑件脱模时采用气动顶出。
注塑模具CAD/CAM技术的应用,从根本上改变了传统的塑料产品开发和模具加工方式,大大地提高了产品的质量、缩短了开发周期、降低了生产成本、强有力地推动了模具工业的发展。
一些大型的商品化CAD/CAM软件,如Pro/Engineer、UnigraphicsII、Cimatron、MoldFlow等,都已开发出专门用于注塑模具设计的功能模块,为模具设计提供了十分方便的工具。
有资料统计表明,采用CAD技术可以使模具设计时间缩短50%。
在欧美一些工业发达的国家,CAD/CAM已经成为模具行业一种普遍应用的技术。
在CAD应用方面,已经超越了甩掉图板、二维绘图的初级阶段。
在模具设计中采用三维CAD软件的企业已经接近90%。
目前,国内也有不少企业开始应用CAD软件进行模具设计。
在设计过程中制定了合理的工艺方案,满足了大批量生产要求。
同时,还编制了详细的工艺文件来保证模具的顺利加工及制品的生产。
通过合理的设计,本模具满足生产与应用的要求。
关键词:
注塑模具;加工工艺分析;Pro/E;
本设计来自:
完美毕业设计网
登陆网站联系客服远程截图或者远程控观看完整全套论文图纸设计
客服QQ:
8191040
Plasticbucketmoldcavitydesignandsimulationprocessing
Abstract:
Atpresent,injectionmoldingistheplasticsmouldthathasbeingusedmostextensively,itcanmoldthecomplexandhighaccurateplasticproduct.TheSubjectisaboutthedesignoftheplasticbucketprocessanalysis.
Thismoldconsideredtheannualoutput,thefactoryequipmentandmodelstheaccuracyrequirement,choosesamoldcavitystructure.TheplasticbucketTongbithin,deepcavity,thecorelong,maybecausedbymold,andthecoreofdifferentthicknessofthinplasticuneven,resultingindifficultiesinforming,thehighrejectionrate.Thisisparticularlyimportantforthethin-walledplasticbucket.Inlightoftheseproblemsusingadynamic,scheduledtodie-guided,guidedsetsofpositioning.Inthebarrelsarehighpartlybasedonanindependentcoolingsystem,forformingabarrelattheendofthemoduleinserts,acircularcoolingwater,theflowofimportsandexportsinthedesignofthefixed-board.CoreCoolingbythemiddleofawatermainwaterway,andthenalongthecircumferencearedividedintosixsub-clotheffluentwater,sothattheentirecoreisfullycooled,thewholemoldofrelativelyuniformtemperaturefield.Strippingplasticpartsusedinairtothetop.
InjectionMouldCAD/CAMtechnologyapplications,tofundamentallychangethetraditionalmoldplasticproductdevelopmentandprocessing,greatlyenhancethequalityoftheproductsandshortenthedevelopmentcycleandreducethecostofproduction,astrongimpetustothemoldindustry.Somelarge-scalecommercializationoftheCAD/CAMsoftware,suchasPro/Engineer,UnigraphicsII,Cimatron,MoldFlow,havebeendevelopedspecificallyfortheinjectionmolddesignfunctionmodulesforthemolddesignprovidesaveryconvenienttool.Statisticsshowthattherearedata,theuseofCADtechnologycanshortenthetimetodiedesign50percent.EuropeandtheUnitedStatesinsomeindustrializedcountries,CAD/CAMdieindustryhasbecomeauniversalapplicationofthetechnology.InCADapplications,hassurpassedgetriddrawingboard,two-dimensionaldrawingsoftheinitialstage.DieDesignintheuseof3DCADsoftwareenterpriseshavebeencloseto90percent.Atpresent,therearemanydomesticenterprisesbegantodieofCADsoftwaredesign.Inthedesignprocessofformulatingareasonableprogrammetomeettherequirementsofmassproduction.Atthesametime,hasalsopreparedadetaileddocumentoftheprocesstoensurethesmoothprocessingandmouldproductsproduction.Throughrationaldesign,productionandapplicationofmoldstomeettherequirements.
Keywords:
injectionmolding;processingtechnologyanalysis;Pro/E;
目录
1前言.............................................................1
2总体设计方案.....................................................3
3具体设计说明.....................................................4
3.1塑件的测绘.....................................................4
3.2塑件的造型.....................................................4
3.3塑件材料性能分析...............................................6
3.4塑件的结构分析.................................................6
3.5型腔数的确定...................................................6
3.6浇口位置选择...................................................7
3.7浇口结构形式的选择.............................................8
3.8浇口尺寸的确定.................................................8
3.9浇注系统的平衡.................................................8
3.10分型面的设计..................................................8
3.11主流道的设计..................................................9
3.12冷却系统设计..................................................10
3.13导向装置......................................................12
3.14顶出系统设计..................................................12
3.15侧抽芯的设计..................................................12
3.16确定各模板尺寸................................................13
3.17凸凹模结构形式................................................14
3.18加工零件工艺审查..............................................15
3.19基准选择......................................................16
4Cimatron仿真加工................................................17
4.1设计步骤.......................................................17
5结论.............................................................24
参考文献...........................................................25
致谢...............................................................26
附录...............................................................27
1前言
随着塑料行业的不断发展,对塑料模具提出越来越高的要求,因此,精密、大型、复杂、长寿命塑料模具的发展将高于总量发展速度。
同时,由于近年来进口模具中,精密、大型、复杂、长寿命模具占多数,所以,从减少进口、提高国产化率角度出发,这类高档模具在市场上的份额也将逐步增大。
采用模具生产制件具有生产效率高,质量好,切削少,节约能源和原材料,成本低等一系列优点,模具成型已经成为当代工业生产的重要手段,成为多种成型工艺中最具有潜力的发展方向。
模具是机械、电子等工业的基础工业,它对国民经济和社会发展起着越来越大的作用。
模具行业是制造业的重要组成部分,具有广阔的市场前景。
注塑模具分为热塑性塑料注塑成型模具和热固性塑料注塑成型模具两大类。
注塑模具的结构是由塑件结构和注塑机的形式决定的。
凡注塑模具,均可分为动模和定模两大部分。
要真确地、高水平地使用注塑模具计算机辅助设计的各种软件,也必须对模具设计的原则和方法有透彻的了解。
注射成型是塑料制品的主要成型方法,约半数以上的塑料制品是通过注射成型的。
因此,塑料注射模的数量为其它各类塑料模具之首,约占整个塑料模具总产量的50%以上。
同时塑料注射模具的设计制造和加工精度,均比其它各类塑料模具难度要大一些。
一般来说,若能掌握塑料注射模具的制造技术,则对掌握其它各类塑料模具的制造技术,显然会容易多了。
注塑模设计的主要内容归纳起来大致有以下几个方面:
A、根据塑料熔体的流变行为和流道、型腔内各处的流动主力通过分析得出充模顺序,同时考虑塑料熔体在模具型腔内被分流及重新熔合的问题和模腔内原有空气导出的问题,分析熔接痕的位置、决定浇口的数量和方位。
B、根据塑料熔体的热学性能数据、型腔形状和冷却水道的布置,分析得出保压和冷却过程中塑件温度场的变化情况,解决塑件收缩及补缩问题,尽量减少由于温度和压力不均、结晶和取向不一致而造成的残余内应力和翘曲变形。
C、塑件脱模和横向分型抽芯的问题可通过经验和理论分析来解决这方面的问题,目前还正在大力研究建立在经验和理论计算基础上的计算机专家系统软件,以期这方面的工作能更快、更准确无误的在计算机上实现。
D、决定塑件的分型面,决定型腔的镶拼组合。
模具的总体结构和零件形状不单要满足充模和冷却等工艺方面的要求,同时成型零件还要具有适当的精度、粗糙度、强度和刚度、易于装配和制造,制造成本低。
以上这些问题,并非孤立存在,而是相互影响的,应综合加以考虑。
本课题是对塑料提桶进行测绘、模具设计、模具型腔仿真加工。
课题来源于盐城市羽佳塑料制品厂。
基于生产实践之上的对塑料提桶的模具设计以及仿真加工。
在设计过程中要解决塑料提桶制品测绘、模具设计、在模具设计时对分型面的选择、浇口形式与位置的确定、型腔的安排、型腔和型芯冷却水道的设置、工艺分析及加工仿真等问题。
塑料提桶制品的几何尺寸进行测量后要进行合理的后处理。
模具分型面处在同一平面时不需要一定的角度,所以选择底面为分型面。
本模具设计采用直接浇口。
为使流道平衡,应使各型腔距主流道距离均等。
由于所成型的制品形状简单且几何尺寸较大,因此可采用冷却水道围绕型腔、定模镶件、型芯主体的冷却方式。
模具方案设计完成后对型腔进行仿真加工。
据此方案可以达到设计的预期效果。
并且大大提高了注塑模的质量和效率。
2总体方案论证
本课题的设计目的是对塑料提桶三维造型及优化、塑料注射模具设计和模具加工仿真。
其中:
1、制品的厚度方向小于2.0;2、制品材料为ABS;3、制品表面粗糙度不低于实物表面;4、制品生产批量为5万件;5、制品的其他要求要符合设计规范。
在进行零件的三维造型之前,首先要对塑件进行测绘,绘制塑件二维工程图,然后根据工程图进行塑件的三维造型,再进行型腔的设计,主要是分型面的设计,接着就是把分型后的型腔装配组件调入Pro/EWildfire4.0进行整个模架的设计,然后进行仿真加工。
首先是对塑件进行测绘。
由于该塑件大都为曲面实际测量有一定困难所以采用多次取断面进行测量的方法。
测绘好后使用Pro/EWildfire4.0进行三维造型。
主要采用拉伸、除料、旋转等步骤造型。
根据工厂现有设备的注射量、锁模力等方面进行考虑,还有塑件的精度等级确定采用一模一腔。
同时确保塑件及浇注系统所需的注射量不超过注射机最大容量的80%。
接着确定模具总体模具结构形式。
根据所选用的模具结构形式,确定其定模、动模结构。
此制品外形简单,尺寸较大,应考虑既节省材料,减轻模具重量,又使模具结实,故作如下分析:
A、模具呈圆形,动、定模直接由导柱连接,用锥面配合保证同轴度。
此模具在三个角上为导柱空出位置,结构合理。
B、该模具采用多段水冷却,型腔四周虽在冷却水孔处应力集中,但孔径小。
再者,动模受力均匀,不易应注射压力而变形,模具结构合理。
C.对各个系统进行设计,首先是浇注系统。
根据所选用定模及动模模块及定模板尺寸、模具的类型、型腔的类型、型腔的数目、布置、成型零件型腔尺寸、形状及塑料型号等因素,确定浇注系统形式。
模具设计完成后,进行型腔的加工工艺分析,在确定加工工艺步骤后,在Cimatron中进行刀具路径设定完成仿真加工,而后输出数控程序。
3具体设计说明
3.1塑件的测绘
塑件为塑料提桶,材料为ABS,用游标卡尺对零件进行测绘。
我们最终所需要加工得到的是制造此零件的模具型腔,由于制造的原因,塑件在出模后不可避免的会产生一定的变形,因此对该零件的测量数值需要进行分析处理。
如对塑件较大尺寸误差的进行修正,对相同形状处所测不同尺寸的取均值进行圆整,然后绘出零件的草图。
由于条件限制所以采用多次取断面进行测量的办法。
用游标卡尺(0~300、0.02),曲线测量仪等测量。
测绘过程中必须把被测物体放在工作平面上,采用多次测量求平均值,正确地读取数据。
测量的主要尺寸如下图:
图3-1塑件制品图
3.2塑件的造型
零件测绘草图出来以后,应该根据零件的测绘图,对零件的进行三维造型。
三维造型可以选用Pro/E软件,三维造型的所有参数与测绘的数据一致。
首先打开三维软件Pro/E,进入零件设计界面,点击草绘拉伸命令,然后在竖直面内画塑料提桶的中间截面的断面图,点击
旋转命令绘制三维图形,由于该塑件大都是曲面都是圆滑过渡所以在三维造型中要使用倒圆角
命令。
该塑件大都是曲面所以三维造型有一定的困难。
要正确的绘制出该塑件的造型图必须熟练掌握Pro/E的绘图命令。
由Pro/E软件的计算功能得塑件尺寸为:
该塑件口径为270mm,高度为240mm,壁厚为2mm.
根据上述的方法绘制的制品的三维造型如图3-1所示:
图3-2塑件三维造型
3.3塑件材料性能分析
塑料模具结构比较复杂,组成一套模具的零件数目较多,而且由于各零件在工作中所处的地位、作用不同,对材料的性能要求也不同。
总的说来,用于制作塑料模具的材料,在质量上首先要求具有一定的硬度和耐磨性,其次是有一定的强度和韧性,再次是易于加工。
因此,应根据模具的结构、性能要求和使用条件、模具的制造方法,合理地选用模具材料。
根据文献[5]中的P546,模具中各个零件的材料选择如下:
A.导向零件的材料选择包括导套和导柱,由于在开、合模时有相对运动,成型过程中要承受一定的压力,或偏载负荷,如导柱、导套与斜导柱等部件,根据一软一硬的原则,保证硬度。
因此要求表面耐磨性好,心部具有一定的韧性,本设计中的导向零件选用T8A,经过渗碳淬火后表面硬度应达到50-55HRC;
B.浇注系统零件的材料选择本设计中的浇注系统零件选用T8A,经过渗碳淬火后表面硬度应达到50-55HRC;塑件材料ABS,密度取1.01g/cm3,脱模斜度取1°,ABS收缩率(0.3~0.8)%,取0.5%。
C.模体零件的材料选择包括各种动、定模板、型腔、型芯等,这些零件要求具有足够的机械强度,在本设计中选用45钢,经淬火处理后表面硬度达到40-45HRC,可满足上述要求;
D.定位零件的材料选择包括定位圈和螺钉,要求其具有足够的机械强度,耐磨性好,考虑上述要求,定位圈选用T8A,并表面淬火使硬度达到50-55HRC;螺钉选用45钢。
3.4塑件的结构分析
该塑件口径为270mm,高度为240mm,壁厚为2mm。
对于这种大型薄壁塑件模具,设计之前对塑件图纸进行分析,认为在生产过程中可能会产生下列问题:
A.由于腔深、型芯长,可能会因型腔、型芯不同心而造成塑件壁厚薄不均,从而造成成型困难,废品率高。
这一点对于薄壁桶体尤为重要。
B.该模具仅型腔、型芯装配后尺寸约为
560X413mm,属于大型模具,因此必须有良好的冷却系统,以保证塑件不变形,提高生产率。
C.型芯表面积2092cm2,根据公式计算,初始包紧力约为18.3吨,顶出时很可能使塑件产生裂纹或变形。
D.脱模时型芯外可能形成真空,增大脱模力。
由于模具尺寸较大,设计时动、定模以导柱定位,以确保型芯、型腔的同轴度。
3.5型腔数的确定
型腔的数量是由给定的注塑机型号XS—ZY—500来确定的,并且从塑件的尺寸精度考虑,由于该制品精度等级6所以型腔数控制在一腔,并且零件是塑料提桶,体积大,大批量生产,从注塑经济效益出发来确定。
热塑性塑料注射机型号:
XS—ZY—500
具体参数如下表:
表3-1注塑机参数
型号
XS—ZY—500
螺杆(柱塞)直径/mm
65
注射容量/cm3
665
注射压力/(105Pa)
104
锁模力/(kN)
3500
最大注射面积/cm2
1000
模具厚度
最大/mm
450
最小/mm
450
模板行程/mm
300
喷嘴
孔直径/mm
6
球半径/mm
18
定位孔直径/mm
100
注射时间s
1.6
动,定模固定板尺寸mm
630
以机床的注塑能力为基础,每次注射量不超过注射机最大注射量的80%。
该塑件外形简单,尺寸较大,故采用一模一腔的形式。
3.6浇口位置选择
模具设计时,浇口的位置及尺寸要求比较严格,初步试模后还需进一步修改浇口尺寸,无论采用何种浇口,其开设位置对塑件成型性能及质量影响很大,因此合理选择浇口的开设位置是提高质量的重要环节,同时浇口位置的不同还影响模具结构。
总之要使塑件具有良好的性能与外表,一定要认真考虑浇口位置的选择,通常要考虑以下几项原则:
A.避免制件上产生喷射等缺陷浇口应开设在塑件截面最厚处,当塑件壁厚相差较大时,在避免喷射的前提下,浇口开设在塑件截面的最厚处,以利于熔体流动、排气和补料,避免产生缩孔或表面凹陷。
B.有利于型腔排气在浇口位置确定以后,应在型腔最后充填处或远离浇口的部位,开设排气槽;或利用分型面、推杆间隙等模内的活动部分排气。
C.考虑塑件使用时的载荷状况通常浇口位置不能设置在